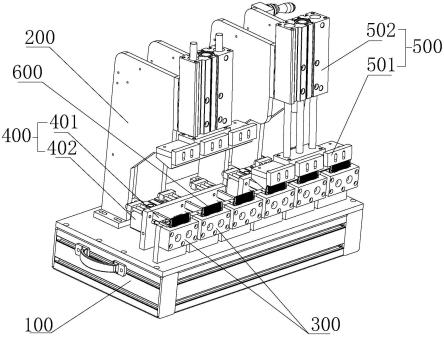
1.本实用新型涉及毛发修剪设备技术领域,特别涉及一种用于电推剪刀头组件组装的工装设备。
背景技术:2.电推剪是一种常用于修理头发或动物毛发的器具,一般是由电机驱动动刀片在定刀片上作横向往复运动以配合实现毛发的修剪;其中刀头组件为电推剪的核心部件,现有的刀头组件一般由定刀片、动刀片、压簧片、螺钉固定片和胶条五个散件组成,压簧片、螺钉固定片和定刀片之间通过螺钉穿设固定相连,压簧片的前端部套接胶条并抵压在动刀片上横向水平延伸的上嵌槽内;但是由于定刀片与动刀片之间没有卡位或者其他的相互定位的结构,为了保证动刀头及定刀头之间齿距的深度以及齿尖的平行度,一般由熟练工凭借经验目测判定、缓慢组装,这样导致刀组件的组装效率极其低下,返工率高,同时受疲劳度以及生产环境的光线等不可控因素影响,同一批次生产出来的刀头在尺寸一致性上存在一定的差异,产品品质难以保证,具有改进的空间。
技术实现要素:3.本实用新型是为了克服上述现有技术中缺陷,提供一种用于电推剪刀头组件组装的工装设备,通过型模能够保证刀片组件五个散件的相对位置,不受外部因素影响,同时通过平推动力机构和下压动力机构抵消螺丝锁附释放过程中产生的外力,以确保在组装过程位置都保持在同一位置不会发生位移,产品一致性得到保证,有效的提高了生产效率、提高了产品品质。
4.为实现上述目的,本实用新型提供一种用于电推剪刀头组件组装的工装设备,包括:
5.型模,其具有开口朝上的型腔,用于嵌装刀片组件以限定刀片、动刀片、压簧片、螺钉固定片和胶条之间的相对位置;
6.所述型腔包括供定刀片依靠的纵向第一侧壁、以及与第一侧壁相对的第二侧壁,所述型腔的第一侧壁上设置有与刀片组件的螺钉安装位对应导通的安装孔位;
7.平推动力机构,其对应安装在型模第二侧壁的一侧,包括用于抵压螺钉固定片的第一抵压模块、以及用于驱动第一抵压模块朝向或者背离螺钉固定板运动的第一驱动模块;
8.所述型腔的第二侧壁上设置有供第一抵压模块伸入型腔内的让位结构;
9.下压动力机构,其对应安装在型模的上方,包括用于同时抵压动刀片和定刀片的第二抵压模块、以及用于驱动第二抵压模块朝向或者背离刀头组件运动的第二驱动模块。
10.进一步设置为:所述型模的型腔开口为“凸”字形结构,所述型腔包括宽口径的第一腔室、以及窄口径的第二腔室,所述第一腔室用于嵌装定刀片以限定定刀片的水平横向位置和竖向位置,所述第二腔室用于嵌装动刀片以限定动刀片的水平横向位置。
11.进一步设置为:所述第二腔室的开口宽度与动刀片的宽度相适配,所述第二腔室的第二侧壁上设置有两个呈水平间隔布置的第一凸起,所述动刀片的下端部搁置在两个第一凸起的上端部上以限定动刀片的竖向位置;
12.所述第二腔室的第二侧壁上对应两个第一凸起之间水平间隔设置有两个第二凸起,所述螺钉固定片被限位夹持于两个第二凸起之间以限定螺钉固定片的水平横向位置;
13.所述第二腔室的第二侧壁上对应第一凸起的下方设置有第三凸起,所述螺钉固定片搁置在第三凸起上以限位螺钉固定片的竖向位置;
14.所述压簧片被限位夹持于两个第一凸起之间以限位压簧片的水平横向位置;
15.所述第二腔室的第二侧壁上还设置有可水平伸缩的弹簧柱,所述弹簧柱用于抵接在压簧片上以限定压簧片的竖向位置,同时与第一侧壁配合以夹持限定刀头组件的水平纵向位置。
16.进一步设置为:所述型模包括对合形成型腔的定模板和靠模板,其中所述定模板为平板结构,所述靠模板为簸箕结构,所述型模对应定模板侧的两个拐角处还设置有限位块,两个限位块之间限定出第二腔室的开口,所述第一凸起、第二凸起、第三凸起和弹簧柱均设置在定模板上,所述定模板上设置有供第一抵压模块穿过的让位缺口。
17.进一步设置为:所述弹簧柱包括堵块、顶推柱和弹簧;
18.所述定模板上设置有与型腔相连通的阶梯孔,所述阶梯孔包括大孔部、以及连通大孔部和型腔且与口径与顶推柱相适配的小孔部,所述堵块对应固定安装在定模板以封堵大孔部,所述堵块上设置有与顶推柱相适配的过孔;
19.所述顶推柱插装在阶梯孔内且所述顶推柱对应位于大孔部内的部分上设置有限位环,所述弹簧套接在顶推柱上且抵触连接于限位环与堵块之间。
20.进一步设置为:还包括基座和固定架,所述型模固定安装在基座的纵向前部,所述平推动力机构安装在型模的后侧,所述固定架安装在平推动力机构的后侧且所述下压动力机构固定安装在固定架上以位于型模的上方。
21.与现有技术相比,本实用新型结构简单、合理,通过型模能够保证刀片组件五个散件的相对位置,不受外部因素影响,同时通过平推动力机构和下压动力机构抵消螺丝锁附释放过程中产生的外力,以确保在组装过程位置都保持在同一位置不会发生位移,产品一致性得到保证,有效的提高了生产效率、提高了产品品质。
附图说明
22.图1是本实用新型一种用于电推剪刀头组件组装的工装设备的立体结构示意图;
23.图2是型模的立体结构示意图;
24.图3是型模对应弹簧柱处的竖向剖面示意图;
25.图4是定模板的立体结构示意图;
26.图5是刀头组件的立体结构示意图。
27.结合附图在其上标记以下附图标记:
28.100、基座;200、固定架;300、型模;301、型腔;302、第一腔室;303、第二腔室;1、定模板;11、让位缺口;12、第一凸起;13、第二凸起;14、第三凸起;15、阶梯孔;2、靠模板;21、安装孔位;3、限位块;4、弹簧柱;41、堵块;42、顶推柱;421、限位环;43、弹簧;400、平推动力机
构;401、第一抵压模块;402、第一驱动模块;500、下压动力机构;501、第二抵压模块;502、第二驱动模块;600、刀头组件;5、定刀片;6、动刀片;7、压簧片;8、螺钉固定片;9、胶条。
具体实施方式
29.下面结合附图,对本实用新型的一个具体实施方式进行详细描述,但应当理解本实用新型的保护范围并不受具体实施方式的限制。
30.本实用新型一种用于电推件刀头组件组装的工装设备如图1至图5所示,包括基座100、固定架200、型模300、平推动力机构400和下压动力机构500;型模300固定安装在基座100的纵向前部,用于嵌装刀头组件600以限位定刀片5、动刀片6、压簧片7、螺钉固定片8和胶条9的相对位置;平推动力机构400对应安装在型模300的纵向后侧以用于抵消螺钉旋紧过程中刀头组件600所受到的向后作用力,包括用于抵压螺钉固定片8的第一抵压模块401、以及用于驱动第一抵压模块401朝向或者背离螺钉固定板运动的第一驱动模块402;固定架200对应安装在平推动力机构400的后侧,下压动力机构500固定安装在固定架200上以位于型模300的上方,下压动力机构500用于抵消螺钉旋紧过程中刀头组件600所受到的向上作用力,用于同时抵压动刀片6和定刀片5的第二抵压模块501、以及用于驱动第二抵压模块501朝向或者背离刀头组件600运动的第二驱动模块502。
31.在本实施例中,如图1所示,型模300共有六副且呈横向间隔的布置的基座100上;平推动力机构400为两组且每组平推动力机构400均包括与型模300一一对应的三个第一抵压模块401、以及驱动三个第一抵压模块401同步运动的一个第一驱动模块402;固定架200为两个且每个驱动架上均设置有一个下压动力机构500,每个下压动力机构500均包括与型模300一一对应的三个第二抵压模块501、以及用于同步驱动三个第二抵压模块501的一个第二驱动模块502;本实施例中,第一驱动模块402和第二驱动模块502均为气缸结构。
32.在上述方案中,如图2、图3、图4和图5所示,型模300包括定模板1、靠模板2、限位块3和弹簧柱44,其中定模板1为平板结构且定模板1上对应开设有供平推机构的第一抵压模块401穿过的让位缺口11结构,靠模板2为簸箕结构,定模板1和靠板模固定对合形成开口朝上的型腔301,该型腔301用于西限位安装刀头组件600,弹簧柱44可伸缩的安装在定模板1上以用于限定刀头组件600的水平纵向位置(前后方向),限位块3为两块且对应安装在定模板1一侧的两个拐角处以缩小定型腔301开口,以构造形成“凸”字型结构的型腔301开口,如此将型腔301分隔为位于靠模板2一侧且为宽口径的第一腔室302、以及位于定模板1一侧且为窄口径的第二腔室303;其中,第一腔室302用于嵌装定刀片5以限定定刀片5的水平横向位置(左右方向)和竖向位置(上下方向),具体的,靠模板2的竖向底板限定定刀片5的竖向位置,第一腔室302的开口限定定刀片5的水平横向位置;第二腔室303用于嵌装动刀片6以限定动刀片6的水平横向位置。
33.具体的,如图3和图4所示,第二腔室303的开口的口径(横向宽度)与动刀片6的横向宽度相适配;定模板1的内侧壁按照刀头组件600各部件的位置参数对应设置有用于限位的第一凸起12、第二凸起13和第三凸起14;具体的,该第一凸起12为两个且呈水平间隔布置,动刀片6嵌装在第二腔室303的开口内且其下端部搁置在两个第一凸起12上以实现对动刀片6水平横向位置和竖向位置的限定;第二凸起13为两个且呈水平间隔的布置于两个第一凸起12之间,该第二凸起13的凸起高度低于第一凸起12的凸起高度,螺钉固定片8限位夹
持安装于两个第二凸起13之间以限定螺钉固定片8的水平横向位置,第三凸起14对应设置在第二凸起13的下方,螺钉固定片8的下端部搁置在第三凸起14上以限定螺钉固定片8的竖向位置;压簧片7对应安装在第二凸起13的内侧且被限位夹持安装于两个第一凸起12之间以限定压簧片7的水平横向位置,同时通过弹簧柱44抵压在压簧片7上,该压簧片7上对应构造形成有与弹簧柱44相配合的结构,通过配合弹簧柱44能够限制压簧片7下滑移以限定压簧片7的竖向位置;再者,通过弹簧柱44顶推压簧片7以作用于整个刀片组件向前运动与靠模板2的内壁相配合以整体限定刀头组件600的水平纵向位置;如此型腔301实现对刀头组件600的各个部件的准确、可靠的限位,保证了每次螺钉锁附的一致性;靠模板2上对应开设有与刀头组件600的螺钉安装位置相对应的安装孔位21。
34.具体的,如图3所示,弹簧柱44包括堵块41、顶推柱42和弹簧43;定模板1的对应位置上开设有阶梯孔15,该阶梯孔15包括大孔部、以及连通大孔部和型腔301且与口径与顶推柱42相适配的小孔部,堵头对应固定安装在定模板1上以封堵度大孔部的开口,堵头上开设有与顶推柱42相适配的过孔;顶推柱42插装在阶梯孔15内且其后端部穿过过孔延伸至堵头外、其前端部穿过小孔部延伸至型腔301内,顶推柱42对应位于大孔部的部分上设置有限位环421,弹簧43套接在顶推柱42上且抵接连接于堵头与限位环421之间以使得顶推柱42始终具有向前运动伸入型腔301的作用力,同时通过过孔与小孔部的约束能够使得顶推柱42的运动更加可靠稳定。
35.工装设备的具体使用流程;
36.首先将组装好的刀头组件600装入型模300的型腔301内与实现对各个部件的限位;接着,通过控制器控制平推动力机构400和下压动力机构500工作,以使得平推动力机构400的第一抵压模块401抵压在刀头组件600的后端部,下压动力机构500的第二抵压模块501抵压在刀头组件600的上端部;最后,螺钉通过安装孔位21旋入刀头组件600的螺钉安装位置,此时第一抵压模块401和第二抵压模块501能够分别抵消螺钉锁附过程中作用于刀头组件600的作用力,如此保证了组装过程中刀头组件600的位置以避免其发生位移,保证了产品生产的效率和质量。
37.与现有技术相比,本实用新型结构简单、合理,通过型模能够保证刀片组件五个散件的相对位置,不受外部因素影响,同时通过平推动力机构和下压动力机构抵消螺丝锁附释放过程中产生的外力,以确保在组装过程位置都保持在同一位置不会发生位移,产品一致性得到保证,有效的提高了生产效率、提高了产品品质。
38.以上公开的仅为本实用新型的实施例,但是,本实用新型并非局限于此,任何本领域的技术人员能思之的变化都应落入本实用新型的保护范围。