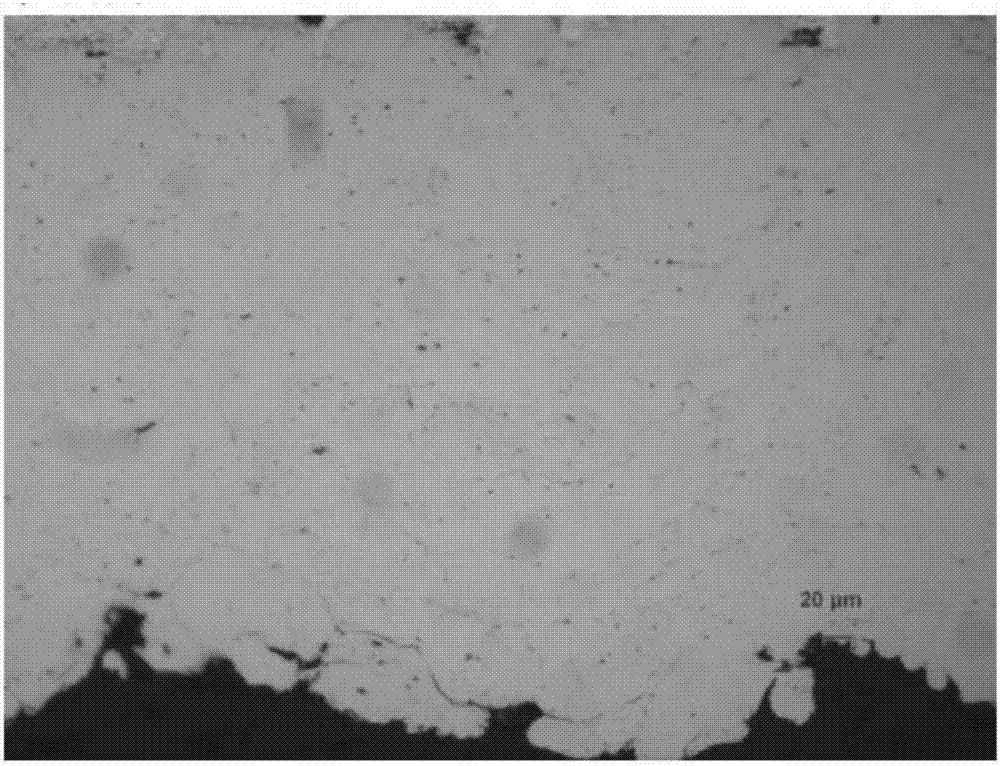
本实用新型涉及属于烹饪器具
技术领域:
,尤其涉及一种结构致密的导磁涂层及具有其的锅体、烹饪器具。
背景技术:
:铝合金、304不锈钢等材质在家用电器产品中应用非常广泛,但这些非磁性或弱导磁性材质的锅具具备的电磁加热功能不理想。例如,铝制IH加热压力锅或煎锅等,传统工艺部分采用热压钎焊或铆接的方式,在基体锅具底部制备一层导磁的430不锈钢薄板。但这两种工艺无法解决锅体高位复底不锈钢板的问题,其电磁加热功率较小。尤其是后者的铆接工艺,在铝锅底上进行铁板(或430不锈钢)复合工艺时,需要在铁板(或430不锈钢)上开多个孔,但这样会块体的致密性下降,其切割磁感线的密度下降,导致其电磁加热的涡流效应下降,加热功率相应下降。通过在锅底部制备一定致密的导磁涂层可有效解决该问题。技术实现要素:鉴于现有技术所存在的问题,本实用新型所要解决的技术问题是提供一种结构致密的导磁涂层及具有其的锅体、烹饪器具。该导磁涂层是通过严格控制冷喷涂技术的工艺参数而得到,具有致密性好、不易脱落、性能稳定、可批量稳定应用,实用新型所要解决的另一技术问题是提供上述结构致密的导磁涂层的制备方法,实用新型所要解决的再一技术问题是提供含有上述结构致密的导磁涂层的锅体和锅具,所述锅具良好的电磁加热效果。本实用新型解决上述技术问题的技术方案如下:一种结构致密的导磁涂层,其已作为层状涂层施涂在基材的表面上,所述导磁涂层由冷喷涂工艺制成,导磁涂层的孔隙率为0.05~0.5%。通过采用冷喷涂技术,在这些锅具底部制备一层高致密性的磁性导磁涂层,以实现其良好的电磁加热效果。以Fe、Ni、Co、Fe-Si合金、430不锈钢等细微粉末为原材料,通过控制冷喷涂的工艺参数,制备孔隙率低的结构致密的磁性导磁涂层(0.05~0.5%),可以显著提升非磁性或弱磁性锅具的电磁加热效率(最大输出功率达1600~2000W)。该冷喷涂技术在铝锅底部制备的导磁涂层性能明显优于热喷涂制备的导磁涂层,且有望部分取代目前的铝合金/复底不锈钢板,或铝合金/不锈钢复合板制备的锅具或炊具,显著降低IH加热小家电产品的制造成本,并达到快速高效电磁加热的目的。这里IH为InductionHeating的简写,指利用了电磁诱导引起的两次电流(旋涡电流)通过被加热材料时发生的焦耳热量。本实用新型解决上述技术问题的技术方案还可以为:一种结构致密的导磁涂层,其已作为层状涂层施涂在基材的表面上,所述导磁涂层由冷喷涂工艺制成,导磁涂层的孔隙率为0.05~0.25%。优选的,所述导磁涂层的厚度为0.1~0.6mm。冷喷涂(CS:ColdSpray),又称为气体动力喷涂技术,是指当具有一定塑性的高速固态粒子与基体碰撞后,经过强烈的塑性变形而发生沉积形成导磁涂层的方法。通常条件下,一般的概念是当固态粒子碰撞到某种基体后将产生固态粒子对基体的冲蚀作用。本实用新型的有益效果是:所述导磁涂层具有高致密、结合力强、不易脱落的特点,孔隙率为0.05~0.25%具有提高导磁涂层结合力和电磁加热功率的有益效果,低于这一范围,会导致工艺过程实施困难的问题;高于这一范围,会导致导磁涂层结合力和电磁加热功率下降的问题。进一步,所述导磁涂层为通过工作气体将导磁金属的粉末冷喷涂在待喷涂结构的表面所形成的涂层。进一步,所述工作气体为空气、氦气、氮气中的一种或几种。进一步,所述导磁金属选自Fe、Ni、Co、Fe-Si、不锈钢中一种或几种的混合。采用上述技术方案的有益效果是:Fe、Ni、Co、Fe-Si、不锈钢分别具有良好的导磁率的特点,这些粉末制备的导磁涂层,具有良好的电磁加热效果。进一步,所述导磁金属的粉末粒度为1~50μm。采用上述技术方案的有益效果是:采用较小粒度的导磁金属的粉末有利于提高导磁涂层的致密性和结合力,如果粉末粒度过高,容易导致导磁涂层表面粗糙,导磁涂层致密性较差等问题。本实用新型解决上述了另一技术问题的技术方案如下:一种结构致密的导磁涂层的制备方法,包括如下步骤:通过工作气体将导磁金属的粉末冷喷涂在待喷涂结构的表面。进一步,所述工作气体为空气、氦气、氮气中的一种或几种。采用上述技术方案的有益效果是空气、氦气和氮气分别具有保护气氛的特点,在导磁涂层制备过程中,具有保护导磁涂层的基材粉末不被大量氧化的效果。进一步,所述冷喷涂的喷射压力为1~3.5Mpa。采用上述技术方案的有益效果是:采用上述的压力,有利于保证导磁涂层具备良好的结合力,如果压力过高,会导致后期喷涂的粉末难以沉积,导磁涂层厚度无法增加的问题;如果压力过低,会导致金属粉末的速率低于其沉积的临界速率,始终难以在基体表面沉积的问题。进一步,所述冷喷涂的喷射温度为573~1273K。采用上述技术方案的有益效果是:采用上述的温度,有利于提升导磁涂层的致密性和结合力等,如果温度过高,会导致喷枪长期经受高温,零部件容易损伤的问题;如果温度过低,会导致导磁涂层结合力和致密性较差等问题。进一步,所述冷喷涂的气体速度为1~2.4m3/min。采用上述技术方案的有益效果是:采用上述的气体速度,有利于保证粉末粒子具有足够的速度(略高于其沉积的临界速度),粉末能有效沉积,如果气体速度过高,会导致粒子飞行速度过高,将原有导磁涂层冲蚀掉,后期导磁涂层难以沉积的问题;如果气体速度过低,会导致粉末粒子飞行速度低、粉末难以在锅体表面沉积的问题。进一步,所述冷喷涂的导磁粉末输送速度为5~15kg/h。采用上述技术方案的有益效果是:采用上述的输送速度,有利于提高粉末的有效沉积率,如果输送速度过高,会导致粉末的平均飞行速率下降,粉末的沉积率下降的问题;如果输送速度过低,会导致粉末的有效沉积速率下降的问题。进一步,所述冷喷涂的喷射距离为10~50mm。采用上述技术方案的有益效果是:采用上述的喷射距离,有利于提高导磁涂层的沉积效率,如果喷射距离过高,会导致粒子飞行至基体表面时的速度过低,难以沉积的问题;如果喷射距离过低,会导致粒子飞行至基体表面时的速度过高,将前期制备的导磁涂层冲蚀掉而后期的导磁涂层难以沉积增厚的问题。进一步,所述冷喷涂的消耗功率为15~55kW。采用上述技术方案的有益效果是:采用上述的消耗功率,有利于对保护气体进行有效加热,热的保护气体可对粉末进行良好的预热,使其达到合适的喷涂温度,如果消耗功率过高,会导致气体温度过高,容易对喷嘴的密封圈等造成损伤问题;如果消耗功率过低,会导致保护气体的加热温度较低,粉末预热温度不足,导磁涂层结合力较差等问题。进一步,所述导磁金属选自Fe、Ni、Co、Fe-Si、不锈钢中一种或几种的混合。采用上述技术方案的有益效果是:Fe、Ni、Co、Fe-Si、不锈钢分别具有良好的导磁率的特点,这些粉末制备的导磁涂层,具有良好的电磁加热效果。进一步,所述导磁金属的粉末粒度为1~50μm。采用上述技术方案的有益效果是:采用较小粒度的导磁金属的粉末有利于提高导磁涂层的致密性和结合力,如果粉末粒度过高,容易导致导磁涂层表面粗糙,导磁涂层致密性较差等问题。进一步,所述导磁涂层的厚度为0.1~0.6mm。采用上述技术方案的有益效果是:导磁涂层的厚度为0.1~0.6mm,有利于保证导磁涂层具备良好的电磁加热效果,并提高生产效率,如果厚度过高,会导致生产效率下降等问题;如果厚度过低,会导致导磁涂层的电磁加热功率较低的问题。一种锅体,包括锅本体和所述结构致密的导磁涂层,所述导磁涂层位于锅本体的外表面,且位于锅本体的侧壁的下部和/或底部上。进一步,所述锅本体的材质为铝合金、不锈钢、高强陶瓷、高强玻璃中的一种或几种。采用上述技术方案的有益效果是:铝合金、不锈钢、高强陶瓷、高强玻璃分别具有非导磁或弱导磁的特点,在其表面制备导磁涂层后,均具有良好的电磁加热效果。一种烹饪器具,包括电磁感应线圈和上述的锅体,所述电磁感应线圈和导磁涂层对应设置。烹饪器具可以为但不限于锅具。采用上述技术方案的有益效果是:锅具本身具有较高的强度,其表面可有效冷喷沉积导磁涂层,并根据导磁涂层的特征保证其良好的电磁加热效果。进一步,所述电磁感应线圈往所述锅体的投影为投影区,所述投影区位于所述导磁涂层内,且所述投影区的区域边缘距离所述导磁涂层的边缘1mm以上。采用上述方案的有益效果为:因为冷喷涂涂层的边缘通常致密度都不够的,通过这样的设计,可以保证冷喷涂层的感应充分发热。进一步,所述电磁感应线圈和所述导磁涂层外表面之间的间距小于10mm。采用上述方案的有益效果为:这样可以最大限度地利用磁场,特别是穿透0.1~0.6mm厚度范围的导磁涂层,使得整个导磁涂层都具有电流从而产生焦耳热发热。附图说明图1为本实用新型局部结构示意图。图2为实施例2的孔隙率的检测结果。附图中,各标号所代表的部件列表如下:1、锅本体,2、导磁涂层。具体实施方式以下结合具体实施例对本实用新型的原理和特征进行描述,所举实例只用于解释本实用新型,并非用于限定本实用新型的范围。本实用新型为一种结构致密的导磁涂层,其已作为层状涂层施涂在基材的表面上,所述导磁涂层由冷喷涂工艺制成,导磁涂层的孔隙率为0.05~0.25%。优选的,导磁涂层的厚度为0.1~0.6mm。本实用新型还公开了一种结构致密的导磁涂层的制备方法,包括如下步骤:通过工作气体将导磁金属的粉末冷喷涂在待喷涂结构的表面。所述工作气体为空气、氦气、氮气中的一种或几种。所述冷喷涂的喷射压力为1~3.5Mpa。所述冷喷涂的喷射温度为573~1273K。所述冷喷涂的气体速度为1~2.4m3/min。所述冷喷涂的导磁粉末输送速度为5~15kg/h。所述冷喷涂的喷射距离为10~50mm。所述冷喷涂的消耗功率为15~55kW。所述导磁金属选自Fe、Ni、Co、Fe-Si、不锈钢中一种或几种的混合。所述导磁金属的粉末粒度为1~50μm。所述导磁涂层的厚度为0.1~0.6mm。进一步,上述的工艺条件还可以为:所述工作气体为空气、氦气、氮气中的一种或几种。所述冷喷涂的喷射压力为1.8~2.5Mpa。所述冷喷涂的喷射温度为1173~1273K。所述冷喷涂的气体速度为1.6~2.4m3/min。所述冷喷涂的导磁粉末输送速度为7~10kg/h。所述冷喷涂的喷射距离为20~40mm。所述冷喷涂的消耗功率为20~50kW。所述导磁金属选自Fe、Ni、Co、Fe-Si、不锈钢中一种或几种的混合。所述导磁金属的粉末粒度为10~40μm。所述导磁涂层的厚度为0.15~0.4mm。导磁涂层的孔隙率为0.1~0.24%。一种锅体,包括锅本体和上述导磁涂层,所述导磁涂层位于锅本体的外表面,且位于锅本体的侧壁的下部及底部。所述锅本体的材质为铝合金、不锈钢、高强陶瓷、高强玻璃中的一种或几种。在锅体进行制备时,可以对锅本体的外表面进行基体预处理,所述基体预处理的方法为对锅本体的基材外表面杂质进行除油脱脂处理;可选择的,在基体预处理之前,对锅本体的基材待喷涂表面进行喷砂处理。一种烹饪器具,包括电磁感应线圈和上述的锅体,所述电磁感应线圈和导磁涂层对应设置。所述电磁感应线圈往所述锅体的投影为投影区,所述投影区位于所述导磁涂层内,且所述投影区的区域边缘距离所述导磁涂层的边缘1mm以上,以保证冷喷涂层的感应充分发热。所述电磁感应线圈和所述导磁涂层外表面之间的间距小于10mm,使得整个导磁涂层都具有电流从而产生焦耳热发热。下面通过一些具体的实施例来进行具体介绍。采用冷喷涂系统,压缩空气加速导磁金属粉末到零界速度,经喷嘴喷出,导磁金属粉末直击到锅体外表面后发生物理形变。导磁金属粉末撞扁在锅体外表面并牢固附着,形成一层致密性很好的导磁层,使锅具有导磁性能。说明书附图中附图1为摘要附图,如图1所示,图1是本实用新型含冷喷涂导磁涂层锅具的局部结构示意图。在锅本体1的底部、或底部+圆弧过渡处,喷涂导磁涂层2,锅本体1与导磁涂层2之间主要以机械结合的方式结合在一起,二者构成可电磁加热的锅具/炊具。实施例1一种锅体,包括锅本体和导磁涂层,所述导磁涂层位于锅本体的外表面。所述锅本体的材质为铝合金。利用冷喷涂工艺在锅本体上制备导磁涂层,包括以下步骤:1.对锅本体的外表面待喷涂表面进行除油脱脂处理;2.通过工作气体将导磁金属的粉末冷喷涂在锅本体的外表面,所述导磁金属的粉末在锅本体的表面形成导磁涂层,具体的工艺参数为:(1)导磁粉末选自采用纯度为99.0-99.8%的Fe粉末,粉末粒度为10~20μm;工作气体采用高纯氮气,氮气的纯度为99.99%,喷涂距离为25~30mm;喷涂温度(即气体加热温度)为1223~1273K;消耗功率为20~35kW;导磁粉末输送速度为7~8kg/h;喷射压力为1.8~2.0Mpa;气体速度为1.6~1.8m3/min;(2)制备的导磁涂层厚度为0.15~0.2mm,孔隙率为0.14~0.16%;安装有该锅体的锅具,锅具的电磁加热最大功率高达1800W。实施例2一种锅体,包括锅本体和导磁涂层,所述导磁涂层位于锅本体的外表面。所述锅本体的材质为304不锈钢。利用冷喷涂工艺在锅本体上制备导磁涂层,包括以下步骤:1.对锅本体的外表面待喷涂表面进行不需喷涂的位置用遮蔽治具进行遮挡处理;2.通过工作气体将导磁金属的粉末冷喷涂在锅本体的表面,所述导磁金属的粉末在锅本体的表面形成导磁涂层,具体的工艺参数为:(1)导磁粉末选自采用纯度为99.0-99.8%的Fe粉末,粉末粒度为10~20μm;工作气体采用高纯氮气,氮气的纯度为99.99%,喷涂距离为25~30mm;喷涂温度(即气体加热温度)为1173~1223K;消耗功率为25~30kW;导磁粉末输送速度为8~9kg/h;喷射压力为2~2.1Mpa;气体速度为1.8~2.0m3/min;(2)制备的导磁涂层厚度为0.3~0.4mm,孔隙率为0.10~0.12%;安装有该锅体的锅具,锅具的电磁加热最大功率高达1840W。实施例3一种锅体,包括锅本体和导磁涂层,所述导磁涂层位于锅本体的外表面。所述锅本体的材质为铝合金内锅。利用冷喷涂工艺在锅本体上制备导磁涂层,包括以下步骤:1.对锅本体的外表面不需喷涂的位置用遮蔽治具进行遮挡处理,所述锅本体为铝合金内锅;2.通过工作气体将导磁金属的粉末冷喷涂在锅本体的表面,所述导磁金属的粉末在锅本体的表面形成导磁涂层,具体的工艺参数为:(1)导磁粉末选自采用纯度为99.0-99.5%的Fe-Si合金粉末,粉末粒度为20~40μm;工作气体采用高纯氮气,氮气的纯度为99.99%,喷涂距离为25~40mm;喷涂温度(即气体加热温度)为1173~1223K;消耗功率为25~30kW;导磁粉末输送速度为7~9kg/h;喷射压力为1.8~2.1Mpa;气体速度为1.8~2.0m3/min;(2)制备的导磁涂层厚度为0.2~0.3mm,孔隙率为0.15~0.18%;安装有该锅体的锅具,锅具的电磁加热最大功率高达1780W。实施例4一种锅体,包括锅本体和导磁涂层,所述导磁涂层位于锅本体的外表面。所述锅本体的材质为铝合金内锅。利用冷喷涂工艺在锅本体上制备导磁涂层,包括以下步骤:1.对锅本体的外表面不需喷涂的位置用遮蔽治具进行遮挡处理,所述锅本体为铝合金内锅;2.通过工作气体将导磁金属的粉末冷喷涂在锅本体的表面,所述导磁金属的粉末在锅本体的表面形成导磁涂层,具体的工艺参数为:(1)导磁粉末选自采用纯度为99.0-99.5%的Ni粉末,粉末粒度为20~40μm;工作气体采用高纯氮气,氮气的纯度为99.99%,喷涂距离为30~40mm;喷涂温度(即气体加热温度)为1223~1273K;消耗功率为30~50kW;导磁粉末输送速度为8~10kg/h;喷射压力为2.3~2.5Mpa;气体速度为2.0~2.2m3/min;(2)制备的导磁涂层厚度为0.3~0.4mm,孔隙率为0.15~0.18%,安装有该锅体的锅具,锅具的电磁加热最大功率高达1750W。实施例5一种锅体,包括锅本体和导磁涂层,所述导磁涂层位于锅本体的外表面。所述锅本体的材质为高硼玻璃内锅。利用冷喷涂工艺在锅本体上制备导磁涂层,包括以下步骤:1.对锅本体的外表面不需喷涂的位置用遮蔽治具进行遮挡处理,所述锅本体为高硼玻璃内锅;2.通过工作气体将导磁金属的粉末冷喷涂在锅本体的表面,所述导磁金属的粉末在锅本体的表面形成导磁涂层,具体的工艺参数为:(1)导磁粉末选自采用纯度为99.0-99.5%的Fe合金粉末,粉末粒度为20~40μm;工作气体采用高纯氦气,氦气的纯度为99.9%,喷涂距离为25~40mm;喷涂温度(即气体加热温度)为1223~1273K;消耗功率为30~40kW;导磁粉末输送速度为7~9kg/h;喷射压力为2.1~2.4Mpa;气体速度为2.0~2.4m3/min;(2)制备的导磁涂层厚度为0.2~0.3mm,孔隙率为0.18~0.2%,安装有该锅体的锅具,锅具的电磁加热最大功率高达1850W。实施例6一种锅体,包括锅本体和导磁涂层,所述导磁涂层位于锅本体的外表面。所述锅本体的材质为高强氧化铝陶瓷内锅。利用冷喷涂工艺在锅本体上制备导磁涂层,包括以下步骤:1.对锅本体的外表面不需喷涂的位置用遮蔽治具进行遮挡处理,所述锅本体为高强氧化铝陶瓷内锅;2.通过工作气体将导磁金属的粉末冷喷涂在锅本体的外表面,所述导磁金属的粉末在锅本体的表面形成导磁涂层,具体的工艺参数为:(1)导磁粉末选自采用纯度为99.0-99.5%的430不锈钢粉末,粉末粒度为10~20μm;工作气体采用高纯氦气,氦气的纯度为99.9%,喷涂距离为25~40mm;喷涂温度(即气体加热温度)为1123~1173K;消耗功率为20~30kW;导磁粉末输送速度为7~9kg/h;喷射压力为1.8~2.0Mpa;气体速度为1.7~2.0m3/min;(2)制备的导磁涂层厚度为0.2~0.3mm,孔隙率为0.2~0.22%,安装有该锅体的锅具,锅具的电磁加热最大功率高达1760W。实施例7一种锅体,包括锅本体和导磁涂层,所述导磁涂层位于锅本体的外表面。所述锅本体的材质为304不锈钢内锅。利用冷喷涂工艺在锅本体上制备导磁涂层,包括以下步骤:1.对锅本体的外表面不需喷涂的位置用遮蔽治具进行遮挡处理,所述锅本体为304不锈钢内锅;2.通过工作气体将导磁金属的粉末冷喷涂在锅本体的表面,所述导磁金属的粉末在锅本体的表面形成导磁涂层,具体的工艺参数为:(1)导磁粉末选自采用纯度为99.0-99.5%的Ni粉末,粉末粒度为10~40μm;工作气体采用高纯氮气,氮气的纯度为99.99%,喷涂距离为20~40mm;喷涂温度(即气体加热温度)为1173~1223K;消耗功率为20~35kW;导磁粉末输送速度为8~9kg/h;喷射压力为2.1~2.4Mpa;气体速度为2.0~2.1m3/min;(2)制备的导磁涂层厚度为0.2~0.3mm,孔隙率为0.22~0.24%,安装有该锅体的锅具,锅具的电磁加热最大功率高达1780W。对比例1在实施例1的基础上调整了喷涂温度(即气体加热温度)为423~573K,其余均与实施例1相同。对比例2在实施例1的基础上调整了喷涂温度(即气体加热温度)为573~623K,其余均与实施例1相同。对比例3在实施例1的基础上调整了喷涂距离为40~50mm,其余均与实施例1相同。对比例4在实施例1的基础上调整了喷涂距离为50~60mm,其余均与实施例1相同。对比例5在实施例1的基础上调整了粉末粒度为50~80μm,其余均与实施例1相同。对比例6在实施例1的基础上调整了粉末粒度为80~100μm,其余均与实施例1相同。对比例7在实施例1的基础上调整了喷射压力为0.8~1.0Mpa,其余均与实施例1相同。下面分别将各实施例以及各对比例进行孔隙率、结合力和电磁加热功率的检测。图2为本实用新型实施例2的孔隙率测量结果。孔隙率的计算方法为:孔隙的面积与待测样品的面积的百分比。经检测,孔隙率为0.12%,说明涂层孔隙少、非常致密、致密性好。孔隙率、结合力和电磁加热功率的检测结果见表1。表1名称孔隙率结合力/MPa电磁加热功率/W实施例10.15%28.61800实施例20.12%32.31840实施例30.17%24.91780实施例40.15%26.51750实施例50.18%29.21850实施例60.20%30.51760实施例70.23%27.11780对比例10.29%21.61570对比例20.26%22.71630对比例30.32%20.41520对比例40.45%17.71460对比例50.41%18.51420对比例60.68%17.21370对比例70.81%15.61290根据表1中的数据可以看出,通过严格控制冷喷涂的工艺参数,可以在非导磁材质的锅具或炊具表面制备一层高致密的磁性导磁涂层。可有效实现非磁性材质锅具的导磁性能或提高弱导磁性材质锅具的电磁加热功能。且该导磁涂层的结合力强。导磁涂层的原材料为导磁性能优良的Fe、Ni、Co、Fe-Si、430不锈钢等细微粉末,优选导磁涂层的特征为:孔隙率为0.1~0.25%。在本实用新型的描述中,需要说明的是,术语“顶”、“底”、“内”、“外”等指示的方位或位置关系为基于附图所示的方位或位置关系,仅是为了便于描述本实用新型和简化描述,而不是指示或暗示所指的装置或元件必须具有特定的方位、以特定的方位构造和操作,因此不能理解为对本实用新型的限制。此外,术语“第一”、“第二”仅用于描述目的,而不能理解为指示或暗示相对重要性。以上所述仅为本实用新型的较佳实施例,并不用以限制本实用新型,凡在本实用新型的精神和原则之内,所作的任何修改、等同替换、改进等,均应包含在本实用新型的保护范围之内。当前第1页1 2 3