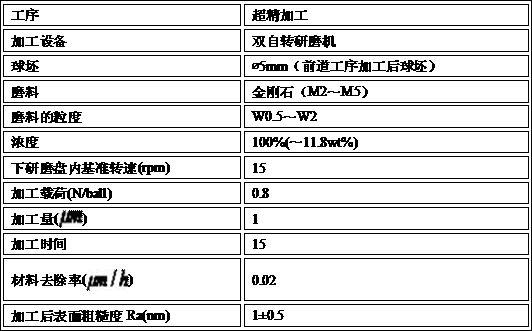
1.本发明涉及到一种精密球珠的研磨加工,特别是针对圆珠笔的笔尖的陶瓷圆珠的高精度的研磨加工工艺,属于高精度球形零件的加工工艺。
背景技术:2.精密球无论是在现代工业领域还是在精密工程领域都占有十分重要的地位。且高精度球珠具有广泛的应用,如轴承珠,阀芯,笔珠等,特别是笔珠作为圆珠笔的重要部件,其加工精度直接影响到圆珠笔的质量。近二十年来,我国的圆珠笔制造行业取得举世瞩目的发展,生产规模和出口量已跃居世界第一。制笔行业在发展笔类产品的同时,也十分渴望相关零部件的发展提高。笔珠作为圆珠笔的重要组成部分,早在上个世纪70年代,我国制笔行业科技人员就对用材进行了攻关。但是由于当时的高科技陶瓷制备工艺和加工技术相对比较落后,所以开发的氧化铝陶瓷球珠表面光洁度差,成品率低,不能满足商业化的要求。近年来高科技技术的迅猛发展,高精度的陶瓷微珠的制备技术已经取得突破。陶瓷笔珠在日本、瑞士、德国等制笔业发达的国家,作为高档笔的用球已经十分普及。陶瓷笔珠以其书写手感良好、耐腐蚀、耐磨损,对球座体磨损小、出墨均匀、划线长久等优点备受青睐。我国在“七五”到“十五”连续四个“863”计划的大力支持下,高技术陶瓷的原料、成型、加工技术也取得了显著的进展。目前,国内有部分厂家制造加工的1.0~0.38mm的陶瓷笔珠已经通过国家相关部门的技术测试,已经在国内外笔类行业推广运用。随着陶瓷微珠的应用日益广泛,但是高精度的陶瓷球珠的加工难度大,经济附加值高。所以急需一种既能降低加工成本又能提高加工精度的,球珠加工工艺。
技术实现要素:3.为了克服现有的球形零件研磨加工工艺所存在的球度低,效率低,加工一致性查,表面粗糙度高,加工成本较高,加工装置复杂等问题,本发明提高一种高效率高精度且加工成本较低的球珠研磨加工工艺。
4.本发明提供的一种球珠的研磨加工工艺,包括如下步骤:(1) 铸造完成后,冲洗铸造模具,测量待研磨件的尺寸,确定待研磨余量和粗研磨的研磨材料尺寸。
5.(2) 粗研磨加工工艺:磨料:m10~m15碳化硼;磨料的粒度:w20~w40;磨料在研磨盘中的质量百分比:20%~80%;载荷压力:8~15n;研磨液:水。
6.(3) 半精研磨加工工艺:磨料:m8~m10碳化硼;磨料的粒度:w10~w20;磨料在研磨盘中的质量百分比:20%~80%;载荷压力:6~10n;研磨液:水。
7.(4) 精研磨加工工艺:磨料:m5~m8碳化硼;磨料的粒度:w5~w10;磨料在研磨盘中的质量百分比:10%~30%;载荷压力:2~5n;研磨液:煤油+润滑油,其中煤油在基液中的质量百分百是60%~80%,润滑油的质量百分百是:6%~8%。
8.(5) 超精研磨加工工艺:磨料:m2~m5金刚石;磨料的粒度:w0.5~w2;磨料的质量
百分比:8%~20%;载荷压力:0.5~2.5n;基液:煤油;基液的质量百分比是:65%~85%,添加润滑油和分散剂;其中润滑油的质量百分比是:4%~8%;分散剂的质量百分比为:3%~6%。
9.(6) 抛光加工工艺:磨料:m3~m5 ceo2;磨料的粒度:w3~w6;磨料的质量百分比:8%~10%;载荷压力:0.5~1n;基液:煤油;基液的质量百分比是:65%~85%,添加润滑油和分散剂;其中润滑油的质量百分比是:4%~6%;分散剂的质量百分比为:3%~6%。
10.在本发明中的球珠研磨加工工艺中,所述步骤(1)中铸造完成后,采用卜海苏豫电子有限公司的双频超声波清洗机 sk2210lh进行5 min的清洗,然后在于燥皿中进行干燥处理。干燥处理结束后对工件采用德国mahr s2型接触式粗糙度测试仪测试粗糙度,由日本岛津公司的毫克级(0.1mg)auy220型天平测量质量,确定出待研磨余量。
11.进一步的所述步骤(2)~(3)中采用双面且下盘自带v型槽的研磨机,其中两个研磨盘采用上下布置,所述的下磨盘表面开有3条v型槽,其中三条v型槽为同心圆,同心圆圆心与研磨盘圆心重合。其中上研磨盘与下研磨盘相互偏心,偏心角度可调范围:5~30度。载荷压力通过上磨盘施加给工件,所述的上磨盘和下磨盘分别由电机驱动,其中上研磨盘速度是:30~60rpm,下研磨盘与上研磨盘速度同步。
12.进一步所述步骤(4)~(5)中采用双自转研磨盘研磨机,其研磨盘上研磨盘下侧为外锥形,下磨盘上侧为内锥形,两个磨盘结合形成了一个v字型,上磨盘与下磨盘有相同的转动轴,有相同的转动圆心,分别由电机驱动。上磨盘速度:20~40rpm,其中下磨盘的速度是上磨盘的2~3倍。
13.进一步的所使用的双面且下盘自带v型从的研磨机,研磨盘的材料是铸铁研磨盘。
14.再进一步的所使用的双自转研磨机,其研磨盘材料是选用金刚石研磨盘。
15.陶瓷球的研磨过程就是利用游离磨料对球坯进行刮削和挤压去除材料的过程,达到减小球径,提高球度,降低表面粗糙度的目的,这些去除作用要通过球珠与研磨盘之间相对运动来完成。但是由于陶瓷球属于脆性材料,在去除作用过程中很容易产生裂纹,所以在对陶瓷球珠要进行分布研磨,由粗到细的工序进行。在进行研磨加工前需要对球坯的加工余量,球度进行测量,分出不同批次。根据加工余量和球度进行分批研磨加工,一方面提高了研磨效率,另一方面提高了研磨的合格率。所以工序的合理划分在大批量的球珠研磨加工中会提高整体的研磨效率。
16.因此,本发明采用的合理研磨工艺:测量球坯数据;粗研磨;半精研磨;精研磨;超精研磨。为了提高研磨效率,应该根据球坯的加工余量以及球坯球度等进行合理的分批,再由粗到细进行研磨,根据研磨后的球坯状态逐步调整研磨压力,研磨盘的运动速度。为使得球坯在研磨盘中研磨均匀充分,需要采取措施使研磨液悬浮且均匀循环。
17.与现有的球珠研磨加工工艺相比,本发明的优点在于;1.通过加工余量和球度的方式对研磨球坯进行分批次研磨,有效的提高了陶瓷球的这类球形零件的研磨精度和研磨效率,合理的工序安排又降低了生产成本,实现了批量生产,且在研磨精度,效率以及机械设备结构上具有综合优势;2.对整个球类零件的研磨技术发展起到了积极推进的作用,可以提供高质量的圆珠笔臂珠,推动圆珠笔的质量发展,出口国外,逐步形成高精度的陶瓷球高科技企业,推动经济增长。
具体实施方式
18.下面为本发明做进一步的描述:一种高精度的球珠研磨加工工艺包括,粗研磨,半精研磨,精研磨,超精研磨,具体有:(1)粗研磨设备:双面且下盘自带v型槽的研磨机;研磨盘:铸铁研磨盘;磨料:m10~m15碳化硼;磨料的粒度:w20~w40;磨料在研磨盘中的质量百分比:20%~80%;载荷压力:8~15n;研磨液:水。
19.(2)半精研磨设备:双面且下盘自带v型槽的研磨机;研磨盘:铸铁研磨盘;磨料:m8~m10碳化硼;磨料的粒度:w10~w20;磨料在研磨盘中的质量百分比:20%~80%;载荷压力:6~10n;研磨液:水。
20.(3)精研磨设备:双自转研磨机;研磨盘:金刚石研磨盘;磨料:m5~m8碳化硼;磨料的粒度:w5~w10;磨料在研磨盘中的质量百分比:10%~30%;载荷压力:2~5n;研磨液:煤油+润滑油,其中煤油在基液中的质量百分百是60%~80%,润滑油的质量百分百是:6%~8%。
21.(4)超精研磨设备:双自转研磨机;研磨盘:金刚石研磨盘;磨料:m2~m5金刚石;磨料的粒度:w0.5~w2;磨料的质量百分比:8%~20%;载荷压力:0.5~2.5n;基液:煤油;基液的质量百分比是:80%,添加润滑油和分散剂;其中润滑油的质量百分比是:4%~8%;分散剂的质量百分比为:3%~6%。
22.(5)抛光工艺设备:双自转研磨机;研磨盘:金刚石研磨盘;磨料:m3~m5 ceo2;磨料的粒度:w3~w6;磨料的质量百分比:8%~10%;载荷压力:0.5~1n;基液:煤油;基液的质量百分比是:10%,添加润滑油和分散剂;其中润滑油的质量百分比是:6%;分散剂的质量百分比为:4%。
23.粗研磨加工时的研磨加工的工艺条件:在对陶瓷球进行研磨加工前,对球珠进行冲洗,测量,然后进行分组,然后再进行2个小时的预研,用于确保陶瓷球与磨料之间接触良好。经过4个小时加工后,达到加工要求。、半精研磨和精研磨的加工工艺条件:
在经过半精加工和精加工后,需要对工件进行冲洗,圆度。粗糙度的测量,目的是确定超精加工的参数调整。超精研磨加工工艺条件如下: 由于抛光采用的是化学机械抛光,材料的去除主要依靠化学,而非磨料的硬度这样在抛光过程中,虽然在磨料与工件之间存在化学机械作用,但磨料的机械去除作用可能会占主导地位,从而破坏化学机械抛光所能形成的优质表面,并不能使工件表面的缺陷减少。所以选择了磨料ceo2,下表给出抛光工艺条件:
一个球珠在通过上述的几种研磨加工后,基本上能够达到研磨要求,粗研磨加工是为了缩小尺寸和圆度误差,半精研磨和精研磨是为超精研磨做准备,进一步缩小粗研磨后产生的各种层次不齐的表面,以及尺寸误差。在超精研磨下,基本上尺寸圆度已经达到加工要求,但是最后进行抛光工艺是为了进一步提高球坯表面的质量。