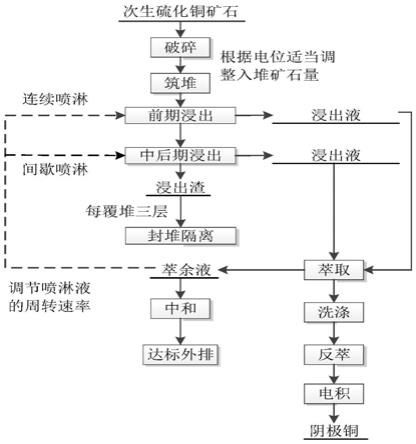
[0001]
本发明涉及一种生物堆浸系统调控电位的方法,适于矿冶行业应用。
背景技术:[0002]“生物堆浸-萃取-电积”工艺具有低成本、低能耗等显著优势,已成为低品位次生硫化铜矿的首选工艺。目前,全球有近20座矿山采用该工艺。我国首座万吨级生物提铜矿山于2005年底在紫金山铜矿投产,充分利用了传统工艺难以利用的低品位资源,获得良好的经济效益。但是,在铜浸出的实践过程中,矿石中的黄铁矿也会被氧化,而且由于黄铁矿含量比铜矿物含量高的多,生物堆浸过程的酸和铁产生量较大,环保成本较高。
[0003]
辉铜矿(cu2s)是次生硫化铜矿中铜的主要存在形态。辉铜矿在酸性高铁介质中的浸出分两阶段进行:第一阶段浸出动力学主要受氧化剂fe
3+
从溶液至矿物表面的扩散控制,其浸出速率与氧化剂fe
3+
浓度成正比,保持足够高的fe
3+
浓度即可快速浸出cu2s中的第一个铜;第二阶段浸出受化学反应控制,与温度强相关,与喷淋液中的fe
3+
浓度弱相关。黄铁矿的氧化动力受体系的氧化还原电位控制,氧化还原电位低时黄铁矿氧化速率缓慢,氧化还原电位高时黄铁矿氧化速度加快。
[0004]
如何将生物堆浸系统的氧化还原电位控制在较低的水平,是控制黄铁矿氧化的关键,是次生硫化铜矿生物堆浸过程要解决的关键技术问题。溶液中的氧化还原电位主要与fe
3+
和fe
2+
的摩尔浓度比值[fe
3+
]/[fe
2+
]有关,fe
3+
浓度越高,氧化还原电位越高。生物堆浸过程中,浸矿微生物(如氧化亚铁硫杆菌)会大大加快fe
2+
的氧化速率,提高生物堆浸系统的氧化还原电位。
[0005]
目前公开的生物堆浸过程控制氧化还原电位的方法主要有两种:一是中国专利cn 101984094 b公开的“一种生物堆浸过程中控制氧化还原电位的方法”,该专利提出了控制氧化还原电位的方法,即采取控制总的硫酸盐浓度220~260g/l,使硫氧化菌处于优势,抑制铁氧化菌活性,控制氧化还原电位650~720mv,从而抑制黄铁矿氧化,其存在控制总的硫酸盐浓度太高,在工业生产中使用的可行性不大等不足存在控制总的硫酸盐浓度太高,在工业生产中使用的可行性不大等不足;二是中国专利cn110527830a公开的“一种黄铜矿生物浸出的方法”,该专利提出了通过向黄铜矿生物浸出体系中加入表面活性剂和/或异噻唑啉酮类杀菌剂,抑制微生物活性,控制微生物对亚铁的氧化过程,从而调节浸出溶液的电位,其存在对微生物活性难以准确控制,对环境不友好等不足。
[0006]
为此研发一种生物堆浸系统调控电位的方法就显得尤为迫切且意义重大。
技术实现要素:[0007]
本发明的任务是为了克服现有技术的不足,提供一种次生硫化铜矿生物堆浸系统调控氧化还原电位的方法。既可将电位控制在相对标准氢电极电位(vs.she)600~700mv,又可有效抑制黄铁矿的氧化,无需添加任何药剂。
[0008]
本发明的任务是通过以下技术方案来完成的:
[0009]
1.生物堆浸系统调控电位的方法,它包括生物堆浸系统,其特征在于它还包括为控制电位在600~700mv采取调节入堆矿量、中后期间歇喷淋浸出、控制喷淋液周转速率和封堆措施,具体工艺步骤和条件如下:
[0010]
a.破碎-筑堆:先将次生硫化铜矿石破碎到-30mm~-50mm,筑堆,堆高10~12米,此后依据生物堆浸体系实测的电位高低,增加或减少入堆矿石量,以调节电位;
[0011]
b.前期浸出:喷淋管道布局后,用萃余液作为喷淋液向筑堆连续喷淋,进行前期浸出,喷淋强度为30~50l/h
·
m2,同时控制喷淋液的周转速率,直到铜浸出率达到40~50%,得到前期的铜浸出液;
[0012]
c.中后期浸出:用萃余液作为喷淋液向前期浸出后的矿堆进行间歇喷淋,同时控制喷淋液的周转速率,得到中后期的铜浸出液,两次浸出铜后的生物堆浸矿为老矿堆;
[0013]
d.封堆隔离:生物堆浸过程中,每覆堆三层且铜浸出结束后用膜对下层老矿堆进行封堆隔离。
[0014]
本发明与现有技术相比具有以下优点和效果:
[0015]
(1)工艺控制简单,根据生物堆浸系统的电位变化趋势,调整入堆矿石量、喷淋液的周转速率和喷淋制度,即可将生物堆浸系统的电位控制在目标范围内。
[0016]
(2)无需添加药剂,生产成本低。
[0017]
(3)环保效益好。在实现高效浸出铜的同时有效抑制了黄铁矿氧化,酸和铁的产生量少,大大降低了废水中和成本和中和渣量。
附图说明
[0018]
图1是根据本发明提出的一种生物堆浸系统调控电位的方法工艺流程图。
[0019]
以下结合附图对本发明作进一步详细描述。
具体实施方式
[0020]
2.如图1所示,本发明的生物堆浸系统调控电位的方法,它包括生物堆浸系统,其特征在于它还包括为控制电位在600~700mv采取调节入堆矿量、中后期间歇喷淋浸出、控制喷淋液周转速率和封堆措施,具体工艺步骤和条件如下:
[0021]
a.破碎-筑堆:先将次生硫化铜矿石破碎到-30mm~-50mm,筑堆,堆高10~12米,此后依据生物堆浸体系实测的电位高低,增加或减少入堆矿石量,以调节电位;
[0022]
b.前期浸出:喷淋管道布局后,用萃余液作为喷淋液向筑堆连续喷淋,进行前期浸出,喷淋强度为30~50l/h
·
m2,同时控制喷淋液的周转速率,直到铜浸出率达到40~50%,得到前期的铜浸出液;
[0023]
c.中后期浸出:用萃余液作为喷淋液向前期浸出后的矿堆进行间歇喷淋,同时控制喷淋液的周转速率,得到中后期的铜浸出液,两次浸出铜后的生物堆浸矿为老矿堆;
[0024]
d.封堆隔离:生物堆浸过程中,每覆堆三层且铜浸出结束后用膜对下层老矿堆进行封堆隔离。
[0025]
本发明的方法可以进一步是:
[0026]
所述步骤b、c铜浸出液入萃取-电积工序,得到产品阴极铜和萃余液。
[0027]
所述萃余液一部分返回步骤b前期浸出和步骤c中后期浸出作为喷淋液。
[0028]
所述萃余液剩余部分入中和工序,用石灰对中和至ph 6~9后外排。
[0029]
所述膜为土工膜或pe膜,可阻止老矿堆中的黄铁矿继续氧化。
[0030]
所述间歇喷淋为喷淋1天,停喷3~5天,可降低中后期浸出阶段的喷淋强度,抑制黄铁矿氧化,从而降低溶液中的铁离子浓度,减少浸矿微生物的数量。
[0031]
本申请文件所涉及的“覆堆”,是指矿石浸出结束后不清除底垫上的浸出渣,在其上方继续堆放矿石,进行喷淋浸出;“封堆隔离”,是利用土工膜或pe膜(聚乙烯膜)对下层铜浸出结束的老矿堆进行隔离,从根本上阻止老堆中的黄铁矿继续氧化;“控制入堆矿石量”,是控制一段时间范围内(如每天、每周)入堆并开始喷淋的矿石量,主要是利用其中的铜矿物与fe
3+
反应,降低生物堆浸系统的电位,在维持生产稳定的情况下,当电位偏高时,适当增加入堆矿石量,反之,适当减少入堆矿石量;“控制喷淋液的周转速率”,是控制喷淋液在矿堆外或溶液池的停留时间,喷淋液贮存在溶液池中时,由于其中存在大量的浸矿微生物,会加速fe
2+
氧化,使溶液电位升高,停留时间越长,溶液电位越高;“矿石的中后期浸出过程采用间歇喷淋制度”,是通过间歇喷淋,降低处于浸出后期的矿石的喷淋强度,抑制黄铁矿氧化,从而降低溶液中的铁离子浓度,减少浸矿微生物的数量,这是基于fe
2+
氧化成fe
3+
的过程可为浸矿微生物繁殖提供必要的能量。
[0032]
实施例1
[0033]
某次生硫化铜矿石中铜品位0.40%,铜矿物以辉铜矿和铜蓝为主,含少量难浸铜矿物硫砷铜矿等;黄铁矿含量较高(4-8%),铜矿物与黄铁矿紧密共生;脉石矿物以石英为主,耗酸脉石含量低。铜矿石破碎到-50mm≥85%后,筑堆,堆高10米。喷淋管道布局后,利用萃余液进行段连续喷淋,喷淋强度35l/h
·
m2。铜浸出率达到50%后,进入中后期浸出阶段,进行间歇喷淋,喷淋1天,休闲3天。铜浸出液进入萃取-电积工序生产阴极铜。萃余液的周转周期(在溶液池中的平均停留时间)为24h。采用覆堆浸出三层后,用土工膜对下层的老矿堆进行封堆隔离。根据堆浸系统的电位对一定时间范围内的入堆矿石量进行适当调整。堆浸系统的电位控制在670~690mv范围内。矿堆浸出7~8个月,浸出渣铜含量小于0.08%,铜浸出率大于80%,黄铁矿氧化率5%。年处理矿石1000万吨,开路萃余液中和费用3000万元/年。
[0034]
实施例2
[0035]
某次生硫化铜矿石中铜品位0.40%,铜矿物以辉铜矿和铜蓝为主,含少量难浸铜矿物硫砷铜矿等;黄铁矿含量较高(4-8%),铜矿物与黄铁矿紧密共生;脉石矿物以石英为主,耗酸脉石含量低。铜矿石破碎到-50mm≥85%后,筑堆,堆高10米。喷淋管道布局后,利用萃余液进行段连续喷淋,喷淋强度35l/h
·
m2。铜浸出率达到50%后,进入中后期浸出阶段,进行间歇喷淋,喷淋1天,休闲5天。铜浸出液进入萃取-电积工序生产阴极铜。萃余液的周转周期(在溶液池中的平均停留时间)为12h。采用覆堆浸出三层后,用pe膜对下层的老矿堆进行封堆隔离。根据堆浸系统的电位对一定时间范围内的入堆矿石量进行适当调整。堆浸系统的电位控制在640~660mv范围内。矿堆浸出7~8个月,浸出渣铜含量小于0.08%,铜浸出率大于80%,黄铁矿氧化率3%。年处理矿石1000万吨,开路萃余液中和费用1800万元/年。
[0036]
对比例
[0037]
某次生硫化铜矿石中铜品位0.40%,铜矿物以辉铜矿和铜蓝为主,含少量难浸铜矿物硫砷铜矿等;黄铁矿含量较高(4-8%),铜矿物与黄铁矿紧密共生;脉石矿物以石英为
主,耗酸脉石含量低。铜矿石破碎到-40mm≥85%后,筑堆,堆高12米。喷淋管道布局后,利用萃余液进行连续喷淋。浸出液进入萃取-电积工序生产阴极铜。未采取额外措施对堆浸系统的电位进行调控,堆浸系统的电位850~900mv。矿堆浸出7~8个月,浸出渣铜含量小于0.07%,铜浸出率大于82%,黄铁矿氧化率20%。年处理矿石1000万吨,开路萃余液中和费用1.2亿元/年。
[0038]
实施例与对比例的技术经济指标对比见表1。
[0039]
表1实施例与对比例的技术经济指标对比表
[0040][0041][0042]
如上所述,便可较好地实现本发明。上述实施例仅为本发明最佳的实施方式,但本发明的实施方式并不受上述实施例的限制,其他未背离本发明的精神实质与原理下所做的改变、修饰、替换、组合、简化,均应为等效的置换方式,都包含在本发明的保护范围内。