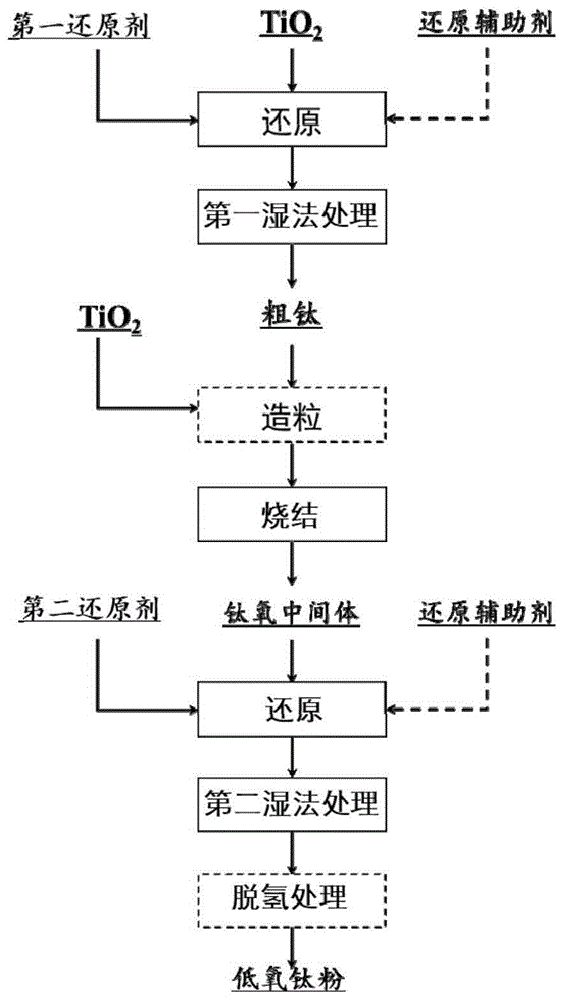
本发明涉及化工冶金
技术领域:
,尤其涉及一种制备低氧钛粉的方法。
背景技术:
:钛及钛合金是重要的功能与结构材料,具有密度小、比强度高、无磁性、耐蚀性强、生物相容性好等优点,在航空航天、海洋船舶、化工能源、生物医疗等领域应用广泛。钛是典型的化学活泼金属,其强化学活泼性使得氧化钛中钛与氧经直接还原充分解离困难,金属钛制备较常见金属难度大、代价高,其强化学活泼性也使得钛及钛合金在加工过程中易被氧污染。金属钛加工成锻件/制件的主流方法为锻造法,不仅流程长,且因钛化学活性高、热传导差、硬度和强度高,钛合金材切削困难,由轧制品制成制件的买飞比高达12:1~20:1,因此锻造法材料利用率很低。以需高品质的钛及钛合金粉末为原料的近终成形法为一些形状复杂、特殊定制的钛制件替代加工方法,流程短、材料利用率高。金属钛/钛合金粉末的制备方法有多种。目前主流的钛粉生产方法为氢化-脱氢法(hdh),是将海绵钛/钛锭/钛屑等先吸氢氢化变脆、再破碎至需要的尺寸范围、最后真空脱氢的生产过程。hdh法可生产纯钛粉及钛合金粉,产品形貌一般为无规则,粒度控制通过筛分来实现。但hdh法不具备纯化的功能,粉末纯度取决于原料纯度;且一般情况下所得粉末的o/n含量增加过多、控制困难。纯度和球形度高的高品质钛合金粉基本是采用雾化法制得的,包括气雾化、等离子体雾化、离心雾化等。各种雾化方法均大体包括三步骤,即熔化、雾化和冷却。熔化的方式可为真空电感应熔化、等离子体电弧熔化、感应滴熔。熔化后液态金属被高压气雾化成金属液滴、或经高速旋转产生的离心力制造金属液滴,并在保护气氛中快速冷却而成为球形金属颗粒。雾化法除存在细粉率低外,昂贵的棒材/丝材的使用、大量的电耗及气耗等,使得雾化法制粉成本较高,一般每公斤售价高达数百-数千元。为降低高品质金属钛/钛合金粉的生产成本,研究者提出了诸多新技术,包括基于kroll法改进的adma法、连续钠还原的armstrong法、电化学还原的ffc-剑桥法、犹他大学-gsd法、hamr法等。adma法的技术关键在于将氢气引入至还原、相分离、冷却等各个工序,以将镁热还原和氢化过程整合,直接制备氢化钛粉,有望降低钛粉的生产成本和能耗。armstrong法是基于连续钠还原ticl4(或ticl4及合金元素氯化物)来制备金属钛粉或钛合金粉。ffc法是基于电化学还原tio2(或tio2与合金元素氧化物的混合物)阴极来制备金属钛或钛合金的方法,但该法尚未突破电流效率低和惰性阳极替换碳阳极以避免碳污染的难题。adma法、armstrong法及ffc法是制备不规则钛/钛合金粉末的典型代表。gsd法是造粒-烧结-脱氧的简称,是美国犹他大学研发的一种制备球形钛/钛合金粉的新方法,该法以钛屑或者高氧的钛粉为原料,经氢化破碎、喷雾造粒、脱脂烧结、低温脱氧等工序制得近球形的钛/钛合金粉,主要服务于3d打印行业。hamr法是一种低成本金属钛粉制备技术的突破与创新,包括还原、浸出、热处理、脱氧、浸出等关键步骤,但脱氧阶段还原剂利用效率还有进一步提高的空间。因此,本发明即拟对hamr流程进行优化。技术实现要素:鉴于现有技术中存在的问题,本发明提供一种制备低氧钛粉的方法,所述方法通过将二氧化钛分为两部分处理,能充分利用第二次还原过程中过量的还原剂,降低还原剂和能量消耗,且提高钛氧中间体的氧含量有利于抑制造粒用的粘接剂对钛粉产品的影响,提高了最终钛粉的产品质量,应用前景广阔。为达此目的,本发明采用以下技术方案:第一方面,本发明提供一种制备低氧钛粉的方法,所述方法包括如下步骤:(1)第一部分二氧化钛依次经第一还原剂还原和第一湿法处理,得到粗钛;(2)混合所述粗钛与第二部分二氧化钛,得到混合物料,所述混合物料依次经烧结和破碎,得到钛氧中间体;(3)所述钛氧中间体依次经第二还原剂还原和第二湿法处理,得到低氧钛粉。本发明提供的制备低氧钛粉的方法,先将一部分tio2原料用活泼金属还原剂还原,还原产物经第一湿法处理后获得粗钛;该方法还将另一部分tio2原料与粗钛混合、烧结、破碎,得到钛氧中间体,该钛氧中间体再次经活泼金属作还原剂经深度还原,并进行第二湿法处理后,得到低氧金属钛粉。本发明中为保证钛氧中间体深度还原的充分,深度还原时活泼金属还原剂将会过量使用,以保证活泼金属与钛氧中间体的充分物理接触,导致一部分活泼金属的无效损失,因此往粗钛中混入一部分原料tio2,能充分利用过量的这部分还原剂,降低钛粉制备过程中的还原剂消耗。此外,因还原和深度还原、两段湿法处理用的装备通用,往粗钛中混入一部分原料tio2可以提高深度还原及其相应湿法处理阶段的设备空间利用率,降低钛粉制备的过程能耗。本发明所述低氧钛粉是指氧含量≤0.5wt%的钛粉。本发明对混合的形式没有特殊限制,可采用本领域技术人员熟知的任何可用于将粉末混合的方式,例如可以是行星磨混合、滚磨混合、三维混合或v型混合等方式中的任意一种。本发明对烧结的形式没有特殊限制,可采用本领域技术人员熟知的任烧结方式,例如可以是真空烧结、气氛烧结或热等静压烧结等。优选地,所述破碎包括机械破碎和/或研磨等方式,对此不做特殊限制。优选地,所述第二部分二氧化钛和第一部分二氧化钛的质量比为1:(1~65),例如可以是1:1、1:2、1:5、1:10、1:15、1:20、1:25、1:30、1:35、1:40、1:45、1:50、1:55、1:60或1:65等,优选为1:(3~65)。优选地,所述第一还原剂和第二还原剂各自独立地包括mg、ca、mg-li合金或mg-ca合金中的一种或至少两种的组合。优选地,所述第一还原剂和第二还原剂各自独立地为粉状、屑状或颗粒状中的一种或至少两种的组合。优选地,所述第一还原剂和第二还原剂中典型但非限制性的组合各自独立地为:mg粉和mg屑的组合,mg粉和ca颗粒的组合,mg屑和ca颗粒的组合,mg粉和mg-ca合金粉的组合,mg粉、mg屑和ca颗粒的组合。优选地,所述第一还原剂与第一部分二氧化钛的质量比为(0.6~1.5):1,例如可以是0.6:1、0.7:1、0.8:1、0.9:1、1.0:1、1.1:1、1.2:1、1.3:1、1.4:1或1.5:1等。优选地,所述第二还原剂与钛氧中间体的质量比为(0.05~5):1,例如可以是0.05:1、0.1:1、0.5:1、1:1、1.5:1、2:1、2.5:1、3:1、3.5:1、4:1、4.5:1或5:1等。优选地,步骤(1)和步骤(3)中还原的温度各自独立地为600~1200℃,例如可以是600℃、667℃、734℃、800℃、867℃、934℃、1000℃、1067℃、1134℃或1200℃等,但不限于所列举的数值,该范围内其他未列举的数值同样适用。优选地,步骤(1)和步骤(3)中还原的气氛各自独立地为真空或保护气氛。优选地,所述保护气氛包括氢气、氩气或氦气中的任意一种或至少两种的组合,其中典型但非限制性的组合为:氩气和氢气的组合,氩气和氦气的组合,氢气和氦气的组合,氩气、氢气和氦气三者的组合,优选为氢气。氢对ti-o固溶体热力学稳定性具有调控作用,优选采用氢气辅助热还原法制备钛粉,ti-o固溶体中的氧在间隙元素氢的帮助下经金属镁作还原剂进行高效脱除,提高了钛粉中氧的去除率,进一步降低了钛粉中的氧含量。优选地,步骤(1)和步骤(3)中还原时各自独立地加入还原辅助剂。优选地,步骤(1)和步骤(3)中所述还原辅助剂各自独立地包括包括mgcl2、cacl2、nacl、kcl、licl、mgcl2-cacl2共熔盐、mgcl2-nacl共熔盐、mgcl2-kcl共熔盐、mgcl2-licl共熔盐、cacl2-nacl共熔盐、cacl2-kcl共熔盐、cacl2-licl共熔盐、nacl-kcl共熔盐、nacl-licl共熔盐、kcl-licl共熔盐或nacl-kcl-licl共熔盐中的任意一种或至少两种的组合,其中典型但非限制性的组合为:mgcl2和cacl2的组合,mgcl2和nacl的组合,mgcl2和licl的组合,mgcl2和mgcl2-kcl共熔盐的组合,cacl2和nacl的组合,cacl2和licl的组合,nacl和licl的组合,licl和mgcl2-kcl共熔盐的组合,licl和kcl-licl共熔盐的组合,mgcl2-kcl共熔盐和kcl的组合,mgcl2-kcl共熔盐和kcl-licl共熔盐的组合。优选地,所述还原辅助剂与第一部分二氧化钛的质量比为(0.05~3):1,例如可以是0.05:1、0.1:1、0.15:1、0.2:1、0.5:1、1.0:1、1.5:1、2.0:1、2.5:1、2.8:1或3.0:1等。优选地,所述还原辅助剂与钛氧中间体的质量比为(0.05~3):1,例如可以是0.05:1、0.1:1、0.15:1、0.2:1、0.5:1、1.0:1、1.5:1、2.0:1、2.5:1、2.8:1或3.0:1等。优选地,步骤(1)中所述第一湿法处理包括:还原产物经水和/或酸液浆化,得到浆料。所述浆料依次经ph调节、固液分离、洗涤和干燥,得到粗钛。优选地,所述酸液的ph≥0.5,例如可以是0.5、0.7、0.9、1、1.2、1.4、1.5、1.7、1.9或2等,但不限于所列举的数值,该范围内其他未列举的数值同样适用。优选地,所述浆化的液固比为(1~100):1ml/g,例如可以是1:1ml/g、12:1ml/g、23:1ml/g、34:1ml/g、45:1ml/g、56:1ml/g、67:1ml/g、78:1ml/g、89:1ml/g或100:1ml/g等,但不限于所列举的数值,该范围内其他未列举的数值同样适用。优选地,所述ph调节过程中控制浆料的ph≥0.8,例如可以是0.8、1.1、1.3、1.6、1.8、2.1、2.3、2.6、2.8或3等,但不限于所列举的数值,该范围内其他未列举的数值同样适用。优选地,所述ph调节后浆料的ph为1.5~3.0,例如可以是1.5、1.7、1.9、2、2.2、2.4、2.5、2.7、2.9或3.0等,但不限于所列举的数值,该范围内其他未列举的数值同样适用。本发明中为防止钛粉在ph调节过程中与酸发生溶解反应,所述ph调节过程的浆料控制在ph值0.8以上,当ph值稳定在1.5~3.0之间并不再变化视为ph调节结束。优选地,所述洗涤的温度为0~60℃,例如可以是0℃、7℃、14℃、20℃、27℃、34℃、40℃、47℃、54℃或60℃等,但不限于所列举的数值,该范围内其他未列举的数值同样适用。优选地,所述洗涤包括水洗。优选地,所述干燥的温度为≤60℃,例如可以是40℃、43℃、45℃、47℃、49℃、52℃、54℃、56℃、58℃或60℃等,但不限于所列举的数值,该范围内其他未列举的数值同样适用。所述干燥的方式为不超过60℃的常压或真空干燥、或冷冻干燥中的一种,本发明中控制干燥的温度能够有效防止钛粉表面的过度氧化。优选地,步骤(2)中所述烧结的温度为700~1400℃,例如可以是700℃、778℃、856℃、934℃、1012℃、1089℃、1167℃、1245℃、1323℃或1400℃等,但不限于所列举的数值,该范围内其他未列举的数值同样适用。优选地,所述烧结的时间为0.1~24h,例如可以是0.1h、2.8h、5.5h、8.1h、10.8h、13.4h、16.1h、18.7h、21.4h或24h等,但不限于所列举的数值,该范围内其他未列举的数值同样适用。优选地,所述烧结的气氛为真空或保护气氛。优选地,所述保护气氛包括氢气、氩气或氦气中的任意一种或至少两种的组合,其中典型但非限制性的组合为:氩气和氢气的组合,氩气和氦气的组合,氢气和氦气的组合,氩气、氢气和氦气三者的组合。优选地,在步骤(2)中所述烧结前,将混合物料进行造粒。本发明中若为控制粉体形貌,在烧结前引入造粒,通过往粗钛中混入一部分原料tio2以提高钛氧中间体的氧含量,有利于抑制造粒用的粘结剂对钛金属的碳污染。优选地,所述造粒的方法包括喷雾造粒或滚筒造粒。本发明中造粒的作用在于将混合料团聚成颗粒尺寸可调的球形粉体,该球形粉体入炉烧结后可得到球形钛氧中间体,有利于本发明低氧金属钛粉的形貌球形化。优选地,步骤(3)中所述第二湿法处理包括:还原产物经水和/或酸液浆化,得到浆料;所述浆料依次经ph调节、固液分离、洗涤和干燥,得到低氧钛粉。优选地,所述酸液的ph≥0.5,例如可以是0.5、0.7、0.9、1、1.2、1.4、1.5、1.7、1.9或2等,但不限于所列举的数值,该范围内其他未列举的数值同样适用。本发明中为防止钛粉在ph调节过程中与酸发生溶解反应,所述ph调节过程的浆料控制在ph值0.8以上,当ph值稳定在1.5~3.0之间并不再变化视为ph调节结束。优选地,所述浆化的液固比为(1~100):1ml/g,例如可以是1:1ml/g、12:1ml/g、23:1ml/g、34:1ml/g、45:1ml/g、56:1ml/g、67:1ml/g、78:1ml/g、89:1ml/g或100:1ml/g等,但不限于所列举的数值,该范围内其他未列举的数值同样适用。优选地,所述ph调节过程中控制浆料的ph≥0.8,例如可以是0.8、1.1、1.3、1.6、1.8、2.1、2.3、2.6、2.8或3等,但不限于所列举的数值,该范围内其他未列举的数值同样适用。优选地,所述ph调节后浆料的ph为1.5~3.0,例如可以是1.5、1.7、1.9、2、2.2、2.4、2.5、2.7、2.9或3.0等,但不限于所列举的数值,该范围内其他未列举的数值同样适用。优选地,所述洗涤的温度为0~60℃,例如可以是0℃、7℃、14℃、20℃、27℃、34℃、40℃、47℃、54℃或60℃等,但不限于所列举的数值,该范围内其他未列举的数值同样适用。优选地,所述干燥的温度为≤60℃,例如可以是40℃、43℃、45℃、47℃、49℃、52℃、54℃、56℃、58℃或60℃等,但不限于所列举的数值,该范围内其他未列举的数值同样适用。所述干燥的方式为不超过60℃的常压或真空干燥、或冷冻干燥中的一种,本发明中控制干燥的温度能够有效防止钛粉表面的过度氧化,更有利于控制最终金属钛粉体的氧含量水平。优选地,步骤(3)中所述低氧钛粉经脱氢处理后产出。优选地,所述脱氢处理的温度为500~1000℃,例如可以是500℃、556℃、612℃、667℃、723℃、778℃、834℃、889℃、945℃或1000℃等,但不限于所列举的数值,该范围内其他未列举的数值同样适用。当脱氧工艺引入氢气气氛时,会使得低氧金属钛粉中含氢,当低氧钛粉产品的应用场景对产品中氢含量有所限定时,则进行脱氢处理。作为本发明优选的技术方案,所述方法包括如下步骤:(1)第一部分二氧化钛依次经第一还原剂于600~1200℃在真空或保护气氛中进行还原和第一湿法处理,所述第一湿法处理包括:还原产物经水和/或酸液浆化,酸液的ph≥0.5,得到浆料,浆化的液固比为(1~100):1ml/g,所述浆料依次经ph调节,ph调节过程中控制浆料的ph≥0.8,ph调节后浆料的ph为1.5~3.0,固液分离、温度为0~60℃的洗涤和温度为≤60℃的干燥,得到粗钛;(2)混合所述粗钛与第二部分二氧化钛,得到混合物料,所述混合物料依次经造粒、真空或保护气氛中700~1400℃烧结0.1~24h和破碎,得到钛氧中间体;(3)所述钛氧中间体依次经第二还原剂于600~1200℃在真空或保护气氛中进行还原和第二湿法处理,所述第二湿法处理包括:还原产物经水和/或酸液浆化,酸液的ph≥0.5,得到浆料,浆化的液固比为(1~100):1ml/g,所述浆料依次经ph调节,ph调节过程中控制浆料的ph≥0.8,ph调节后浆料的ph为1.5~3.0,固液分离、温度为0~60℃的洗涤和温度为≤60℃的干燥,得到低氧钛粉;所述第二部分二氧化钛和第一部分二氧化钛的质量比为1:(1~65),所述第一还原剂和第二还原剂各自独立地包括mg、ca、mg-li合金或mg-ca合金中的一种或至少两种的组合,所述还原辅助剂各自独立地包括包括mgcl2、cacl2、nacl、kcl、licl、mgcl2-cacl2共熔盐、mgcl2-nacl共熔盐、mgcl2-kcl共熔盐、mgcl2-licl共熔盐、cacl2-nacl共熔盐、cacl2-kcl共熔盐、cacl2-licl共熔盐、nacl-kcl共熔盐、nacl-licl共熔盐、kcl-licl共熔盐或nacl-kcl-licl共熔盐中的任意一种或至少两种的组合。第二方面,本发明提供一种低氧钛粉,所述钛粉由第一方面所述的制备低氧钛粉的方法制得。本发明提供的低氧金属钛粉采用第一方面所述的方法制得,氧含量低,还原剂使用量低,为一种低成本的金属钛粉制备方法。与现有技术相比,本发明至少具有以下有益效果:(1)本发明提供的制备低氧钛粉的方法将一部分原料tio2混入粗钛,能提高深度还原阶段过量活泼金属的利用率,降低还原剂消耗,相较于一次性将全部二氧化钛进行处理而言,还原剂的消耗能够降低1.5%以上,在较优条件下能够降低5%以上;而且该方法能提高钛氧中间体的氧含量,抑制造粒用的粘结剂对钛金属的碳污染;(2)本发明提供的制备低氧钛粉的方法包括还原处理,能保障制得的钛粉中氧含量低,氧含量低于0.5wt%,在较佳条件下氧含量<0.20wt%。附图说明图1是本发明提供的制备低氧钛粉的方法的流程示意图。具体实施方式下面结合附图并通过具体实施方式来进一步说明本发明的技术方案。下面对本发明进一步详细说明。但下述的实例仅仅是本发明的简易例子,并不代表或限制本发明的权利保护范围,本发明的保护范围以权利要求书为准。如图1所示,本发明提供的制备低氧钛粉的方法包括如下步骤:(1)第一部分二氧化钛依次经第一还原剂600~1200℃在真空或保护气氛中进行还原和第一湿法处理,所述第一湿法处理包括:还原产物经水和/或酸液浆化,酸液的ph≥0.5,得到浆料,浆化的液固比为(1~100):1ml/g,所述浆料依次经ph调节,ph调节过程中控制浆料的ph≥0.8,ph调节后浆料的ph为1.5~3.0,固液分离、温度为0~60℃的洗涤和温度为≤60℃的干燥,得到粗钛;(2)混合所述粗钛与第二部分二氧化钛,得到混合物料,所述混合物料依次经造粒、真空或保护气氛中700~1400℃烧结0.1~24h和破碎,得到钛氧中间体;所述造粒为虚线框,表示可根据实际工艺情况进行造粒或者不进行造粒;(3)所述钛氧中间体依次经第二还原剂600~1200℃在真空或保护气氛中进行还原和第二湿法处理,所述第二湿法处理包括:还原产物经水和/或酸液浆化,酸液的ph≥0.5,得到浆料,浆化的液固比为(1~100):1ml/g,所述浆料依次经ph调节,ph调节过程中控制浆料的ph≥0.8,ph调节后浆料的ph为1.5~3.0,固液分离、温度为0~60℃的洗涤和温度为≤60℃的干燥,得到低氧钛粉。一、实施例实施例1本实施例提供一种制备低氧钛粉的方法,所述方法包括如下步骤:(1)第一部分二氧化钛依次经mg作第一还原剂750℃在氢气气氛中进行还原,还原过程中加入mgcl2作还原辅助剂,mg与第一部分二氧化钛的质量比为0.65:1,mgcl2与第一部分二氧化钛的质量比为0.2:1,还原产物经盐酸酸液浆化,酸液的ph为2.0,得到浆料,浆化的液固比为50:1ml/g,所述浆料依次经ph调节,ph调节过程中控制浆料的ph≥1.2,ph调节后浆料的ph为2.0,过滤,固相经温度为20℃的水洗涤和温度为30℃的真空干燥,得到粗钛;(2)混合所述粗钛与第二部分二氧化钛,得到混合物料,所述混合物料依次经喷雾造粒、真空环境中1000℃烧结4h和破碎研磨,得到钛氧中间体;(3)所述钛氧中间体依次经mg作为第二还原剂770℃在氢气气氛中进行还原,还原过程中加入mgcl2作还原辅助剂,mg与钛氧中间体的质量比为0.2:1,mgcl2与钛氧中间体的质量比为0.6:1,还原产物经盐酸酸液浆化,酸液的ph为2.1,得到浆料,浆化的液固比为50:1ml/g,所述浆料依次经ph调节,ph调节过程中控制浆料的ph≥1.3,ph调节后浆料的ph为2.0,过滤,固相经温度为20℃的水洗涤和温度为30℃的真空干燥,得到低氧钛粉;所述第二部分二氧化钛和第一部分二氧化钛的质量比为1:9;所述低氧钛粉经800℃脱氢处理后产出。实施例2本实施例提供一种制备低氧钛粉的方法,所述方法包括如下步骤:(1)第一部分二氧化钛依次经ca作第一还原剂950℃在真空中进行还原,还原过程中加入cacl2-nacl共熔盐作还原辅助剂,ca与第一部分二氧化钛的质量比为1:1,cacl2-nacl共熔盐与第一部分二氧化钛的质量比为1:1,还原产物经盐酸酸液浆化,酸液的ph为0.5,得到浆料,浆化的液固比为100:1ml/g,所述浆料依次经ph调节,ph调节过程中控制浆料的ph≥0.8,ph调节后浆料的ph为1.5,过滤,固相经温度为60℃的水洗涤和温度为60℃的常压干燥,得到粗钛;(2)混合所述粗钛与第二部分二氧化钛,得到混合物料,所述混合物料依次经滚筒造粒、氩气气氛中1400℃烧结2h和破碎研磨,得到钛氧中间体;(3)所述钛氧中间体依次经mg-li合金作为第二还原剂800℃在氢气气氛中进行还原,还原过程中加入mgcl2-licl共熔盐作还原辅助剂,mg-li合金与钛氧中间体的质量比为0.4:1,mgcl2-licl共熔盐与钛氧中间体的质量比为2:1,还原产物经盐酸酸液浆化,酸液的ph为0.5,得到浆料,浆化的液固比为5:1ml/g,所述浆料依次经ph调节,ph调节过程中控制浆料的ph≥0.8,ph调节后浆料的ph为1.5,过滤,固相经温度为10℃的水洗涤和温度为-10℃的冷冻干燥,得到低氧钛粉;所述第二部分二氧化钛和第一部分二氧化钛的质量比为1:3;所述低氧钛粉经1000℃脱氢处理后产出。实施例3本实施例提供一种制备低氧钛粉的方法,所述方法包括如下步骤:(1)第一部分二氧化钛依次经mg作第一还原剂900℃在氩气气氛中进行还原,不添加还原辅助剂,mg与第一部分二氧化钛的质量比为0.6:1,还原产物经盐酸酸液浆化,酸液的ph为1.0,得到浆料,浆化的液固比为2:1ml/g,所述浆料依次经ph调节,ph调节过程中控制浆料的ph≥1.0,ph调节后浆料的ph为3.0,离心分离,固相经温度为4℃的水洗涤和温度为-5℃的冷冻干燥,得到粗钛;(2)混合所述粗钛与第二部分二氧化钛,得到混合物料,所述混合物料依次经喷雾造粒、真空环境中700℃烧结24h和破碎研磨,得到钛氧中间体;(3)所述钛氧中间体依次经ca作为第二还原剂1000℃在氩气气氛中进行还原,还原过程中加入cacl2作还原辅助剂,ca与钛氧中间体的质量比为0.06:1,cacl2与钛氧中间体的质量比为3:1,还原产物经盐酸酸液浆化,酸液的ph为0.8,得到浆料,浆化的液固比为100:1ml/g,所述浆料依次经ph调节,ph调节过程中控制浆料的ph≥0.9,ph调节后浆料的ph为3.0,过滤,固相经温度为60℃的水洗涤和温度为60℃的常压干燥,得到低氧钛粉;所述第二部分二氧化钛和第一部分二氧化钛的质量比为1:65。实施例4本实施例提供一种制备低氧钛粉的方法,所述方法除步骤(1)中不加入还原辅助剂外,其余均与实施例1相同。实施例5本实施例提供一种制备低氧钛粉的方法,所述方法除步骤(3)中mgcl2与钛氧中间体的质量比为0.02:1外,其余均与实施例1相同。实施例6本实施例提供一种制备低氧钛粉的方法,所述方法除步骤(3)中mgcl2与钛氧中间体的质量比为4:1外,其余均与实施例1相同。实施例7本实施例提供一种制备低氧钛粉的方法,所述方法除步骤(2)中不进行喷雾造粒,直接烧结外,其余均与实施例1相同。实施例8本实施例提供一种制备低氧钛粉的方法,所述方法除步骤(3)中不加入还原辅助剂外,其余均与实施例1相同。实施例9本实施例提供一种制备低氧钛粉的方法,所述方法除步骤(3)中干燥的温度为75℃外,其余均与实施例1相同。实施例10本实施例提供一种制备低氧钛粉的方法,所述方法除所述第二部分二氧化钛和第一部分二氧化钛的质量比为1:5外,其余均与实施例1相同。实施例11本实施例提供一种制备低氧钛粉的方法,所述方法除所述第二部分二氧化钛和第一部分二氧化钛的质量比为1:65外,其余均与实施例1相同。二、对比例对比例1本对比例提供一种制备低氧钛粉的方法,所述方法不将二氧化钛分为两部分,具体的方法包括如下步骤:(1)全部二氧化钛依次经mg作第一还原剂750℃在氢气气氛中进行还原,还原过程中加入mgcl2作还原辅助剂,mg与二氧化钛的质量比为0.65:1,mgcl2与二氧化钛的质量比为0.2:1,还原产物经盐酸酸液浆化,酸液的ph为2.0,得到浆料,浆化的液固比为50:1ml/g,所述浆料依次经ph调节,ph调节过程中控制浆料的ph≥1.2,ph调节后浆料的ph为2.0,过滤,固相经温度为20℃的水洗涤和温度为30℃的真空干燥,得到粗钛;(2)所述粗钛依次经喷雾造粒、真空环境中1000℃烧结4h和破碎研磨,得到钛氧中间体;(3)所述钛氧中间体依次经mg作为第二还原剂770℃在氢气气氛中进行还原,还原过程中加入mgcl2作还原辅助剂,mg与钛氧中间体的质量比为0.2:1,mgcl2与钛氧中间体的质量比为0.6:1,还原产物经盐酸酸液浆化,酸液的ph为2.1,得到浆料,浆化的液固比为50:1ml/g,所述浆料依次经ph调节,ph调节过程中控制浆料的ph≥1.3,ph调节后浆料的ph为2.0,过滤,固相经温度为20℃的水洗涤和温度为30℃的真空干燥,得到低氧钛粉。对比例2本对比例提供一种制备低氧钛粉的方法,所述方法除不进行步骤(2)中的烧结外,其余均与实施例1相同。三、测试及结果测试方法:采用onh分析仪检测上述实施例和对比例中低氧钛粉中的氧含量,其结果如表1所示。表1氧含量(wt%)实施例10.099实施例20.095实施例30.103实施例40.091实施例50.237实施例60.089实施例70.145实施例80.401实施例90.112实施例100.131实施例110.089对比例10.090对比例20.259从表1可以看出以下几点:(1)综合实施例1~11可以看出,本发明提供的制备低氧钛粉的方法,通过将二氧化钛分为两部分处理,能充分利用第二次还原过程中过量的还原剂,制备得到的低氧钛粉中氧含量≤0.5wt%,在较优条件下,低氧钛粉中氧含量≤0.2wt%,应用前景广阔。(2)综合实施例1和对比例1相比,实施例1中将二氧化钛分为两部分处理,相较于对比例1一次性将全部二氧化钛进行处理而言,在配比相同的情况下,实施例1中还原剂的使用量比对比例1中的使用量减少了7.42%,且氧含量与对比例1中的氧含量基本相当,由此表明,本发明通过将二氧化钛分为两部分处理,减少了还原剂的使用量;(3)综合实施例1和对比例2相比,实施例1中进行烧结,而对比例2中不进行烧结而言,实施例1中低氧钛粉的氧含量仅为0.099wt%,而对比例2中低氧钛粉的氧含量高达0.259wt%,由此表明,本发明通过采用烧结步骤,显著降低了低氧钛粉中的氧含量;(3)综合实施例1和实施例8可以看出,实施例1中加入还原辅助剂,相较于实施例8中未加入还原辅助剂而言,实施例1中低氧钛粉的氧含量仅为0.099wt%,而实施例8中低氧钛粉的氧含量为0.401wt%,由此表明,本发明通过加入还原辅助剂,进一步降低了低氧钛粉中的氧含量;(4)综合实施例1和实施例5~6可以看出,实施例1步骤(3)中氯化镁与钛氧中间体的质量比为0.6:1,相较于实施例5~6中质量比分别为0.02:1和4:1而言,实施例1中低氧钛粉的氧含量仅为0.099wt%,而实施例5中低氧钛粉的氧含量分别为0.237wt%,实施例6中氧含量下降并不明显,由此表明,本发明通过将还原辅助剂的含量控制在特定范围内,进一步降低了低氧钛粉中的氧含量,并且节约了还原辅助剂的使用量;(5)综合实施例1和实施例7可以看出,实施例1中经喷雾造粒后再烧结,相较于实施例7中不进行喷雾造粒而言,实施例1中低氧钛粉的氧含量仅为0.099wt%,且能够控制低氧钛粉的形貌,而实施例7中低氧钛粉的氧含量为0.145wt%,由此表明,本发明通过进行喷雾造粒,进一步降低了低氧钛粉中的氧含量,且能够控制低氧钛粉的形貌。综上所述,本发明提供的制备低氧钛粉的方法通过将二氧化钛分为两部分处理,能充分利用第二次还原过程中过量的还原剂,降低钛粉制备过程中的还原剂消耗;其还原剂的消耗能够降低1.5%以上,在较优条件下能够降低5%以上,而且提高钛氧中间体的氧含量,可有效抑制造粒用的粘结剂对钛金属的碳污染;并且该方法能够提高第二次还原及其湿法处理的设备空间利用率,降低钛粉制备的过程能耗,且制备得到的低氧钛粉中氧含量≤0.5wt%,在较优条件下,低氧钛粉中氧含量≤0.2wt%,应用前景广阔。申请人声明,本发明通过上述实施例来说明本发明的详细结构特征,但本发明并不局限于上述详细结构特征,即不意味着本发明必须依赖上述详细结构特征才能实施。所属
技术领域:
的技术人员应该明了,对本发明的任何改进,对本发明所选用部件的等效替换以及辅助部件的增加、具体方式的选择等,均落在本发明的保护范围和公开范围之内。当前第1页12