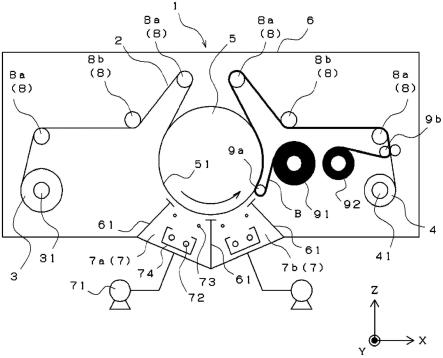
1.本发明涉及一种成膜装置,其用于利用真空成膜法在带状的基材上形成具有规定功能的功能膜。
背景技术:2.近年来,通过在塑料膜等产品的表面上涂布作为薄膜的功能膜而提高产品的功能的方法被应用于多领域中。在塑料膜上形成以抗氧化、防止水分渗入等为目的的阻隔膜而成的阻挡膜是其中一例,也可以将其他透明导电膜、防反射膜等在基材上成膜。
3.这样的成膜基材例如利用下述专利文献1所示的成膜装置来形成。专利文献1记载的成膜装置的示意图示于图9。该成膜装置100中,利用作为真空成膜法之一的等离子体cvd法在基材101上形成作为功能膜之一的阻隔膜。具体地说,供给至成膜室102内的阻隔膜的原料气体被等离子体所分解,该分解后的原料气体沉积在基材101上,由此在基材101上形成作为阻隔膜的薄膜。
4.另外,图9的成膜装置100中,从卷出辊105卷出并被卷取辊106卷取的长条带状基材101沿着由主辊103和引导辊104形成的输送路径进行输送。特别是,在沿着主辊103输送基材101时,利用与主辊103相向设置的成膜室102在基材101上形成薄膜。
5.现有技术文献
6.专利文献
7.专利文献1:日本特开2016-060942号公报
技术实现要素:8.发明所要解决的课题
9.但是,上述成膜装置100中,形成于基材101上的功能膜的性能可能降低。具体地说,上述成膜装置100中,在形成基材101的输送路径的引导辊104上具有与基材101的膜形成面侧接触的膜形成面侧辊104a和与基材101的膜形成面的相反侧的面接触的背面侧辊104b,但在通过成膜室102而形成了功能膜的薄膜的基材101与具有坚硬表面的膜形成面侧辊104a接触时,存在功能膜产生损伤、其性能降低的问题。并且,在假设以不存在与形成有功能膜的薄膜的基材接触的膜形成面侧辊的方式构成成膜装置的情况下,存在基材的输送路径受限、其结果装置大型化的问题。
10.本发明是鉴于上述问题而进行的,其目的在于提供能够不降低功能膜的性能而在基材上形成功能膜的成膜装置和成膜方法。
11.用于解决课题的手段
12.为了解决上述课题,本发明的成膜装置的特征在于,其具备:成膜室,在以卷对卷方式输送的基材的膜形成面侧形成薄膜;引导部件,通过与基材的膜形成面侧或其相反侧接触而引导基材的输送方向,从而形成基材的输送路径;保护部件贴合部,位于基材的输送路径中的上述成膜室的下游侧且设置于最先与基材的膜形成面侧接触的上述引导部件与
上述成膜室之间,将具有挠性的保护部件贴合在基材的膜形成面侧。
13.根据本发明的成膜装置,能够不降低功能膜的性能而在基材上形成功能膜。具体地说,通过具备位于基材的输送路径中的成膜室的下游侧且设置于最先与基材的膜形成面侧接触的引导部件与成膜室之间的、将具有挠性的保护部件贴合在基材的膜形成面侧的保护部件贴合部,能够避免形成于基材上的薄膜与引导辊发生物理接触,因此能够防止由于与引导辊的表面的接触而损伤薄膜的情况。
14.另外,上述保护部件的与基材对置的一侧的面中,在基材的宽度方向上与基材的两端部对置的部分的粘合力可以比两端部之间的部分的粘合力高。
15.由此,在将保护部件从基材剥离时,能够减少连薄膜也从基材剥离的情况。
16.另外,上述保护部件在基材的宽度方向上可以仅与基材的一部分对置。
17.由此,在基材的未贴合保护部件的部分与引导辊之间产生间隙,能够避免薄膜与引导辊发生物理接触。
18.另外,基材的输送方向可以反转,上述保护部件贴合部可以隔着上述成膜室设置在基材的输送路径的两侧。
19.由此,即使在成膜装置内使基材反转输送而进行成膜的情况下,也能够避免形成于基材上的薄膜与引导辊发生物理接触。
20.另外,可以在上述保护部件贴合于基材上的状态下卷取基材。
21.由此,能够在基材被卷取的状态下防止薄膜与基材的背面接触。
22.另外,可以进一步具有在卷取基材前将上述保护部件从基材剥离的保护部件剥离部。
23.由此,可防止由于在贴合有保护部件的状态下卷取而导致的卷绕偏移,仅将基材进行卷取。
24.另外,由上述保护部件剥离部剥离的上述保护部件可以被送至上述保护部件贴合部,形成保护部件的循环路径。
25.由此,能够使应准备的保护部件的长度较短。
26.发明的效果
27.根据本发明的成膜装置,能够不降低功能膜的性能而在基材上形成功能膜。
附图说明
28.图1是表示本发明的一个实施方式中的成膜装置的示意图。
29.图2是表示本发明的一个实施方式中的保护部件的示意图。
30.图3是表示本发明的另一实施方式中的保护部件的示意图。
31.图4是表示本发明的又一实施方式中的保护部件的示意图。
32.图5是表示本发明的另一实施方式中的成膜装置的示意图。
33.图6是表示本发明的又一实施方式中的成膜装置的示意图。
34.图7是表示本发明的又一实施方式中的成膜装置的示意图。
35.图8是表示本发明的又一实施方式中的成膜装置的示意图。
36.图9是表示现有的成膜装置的示意图。
具体实施方式
37.使用附图对本发明的实施方式进行说明。
38.图1是本发明的一个实施方式中的成膜装置1的示意图,为主视图。
39.成膜装置1为用于在基材上进行表面处理而形成薄膜的装置,例如,在具有挠性的塑料膜上形成作为以抗氧化、防止水分渗入为目的的功能膜的阻隔膜,用于食品用的保护膜、柔性太阳能电池等。具体地说,在柔性太阳能电池的情况下,在塑料膜等带状基材上形成由各电极层和光电转换层等构成的太阳能电池单元后,利用成膜装置1在太阳能电池单元上形成2层以上薄膜从而形成阻隔膜。由此,能够有效地防止水分渗入到太阳能电池单元中,能够形成氧化耐久特性优异的柔性太阳能电池。
40.该成膜装置1具有:束保持辊3、束保持辊4,它们是用于保持具有挠性的基材的束的2个束保持辊;配置于束保持辊3与束保持辊4之间的主辊5;容纳主辊5的主辊室6;和形成薄膜的成膜室7,使从一个束保持辊(束保持辊3)送出的基材2在沿着主辊5的外周面51输送的同时通过各成膜室7,由此在基材2上形成薄膜,并由另一个束保持辊(束保持辊4)进行卷取。
41.另外,主辊5的旋转方向如图1中箭头所示,该箭头的方向(逆时针方向)为此时的基材2的输送方向。
42.另外,成膜装置1具有保护部件贴合部9a,通过将保护部件b贴合在形成有薄膜的基材2的膜形成面侧,避免了作为形成基材2的输送路径的辊体的、与基材2的膜形成面侧接触的引导辊104a与形成于基材2上的薄膜发生物理接触。
43.束保持辊3和束保持辊4各自具有大致圆筒形状的芯部31和芯部41,基材2被卷绕在这些芯部31和芯部41上,形成了基材2的束。
44.通过旋转驱动这些芯部31和芯部41,能够将基材2送出或卷取。即,利用束保持辊3和束保持辊4进行所谓卷对卷输送,通过利用未图示的控制装置控制芯部31和芯部41的旋转,能够增加和减少基材2的送出速度或卷取速度。具体地说,图1的方式中,束保持辊3比主辊5更靠基材的输送路径的上游侧,因此,束保持辊3成为送出基材2的辊,相反地束保持辊4成为卷取基材2的辊。并且,在基材2受到来自位于下游侧的芯部41的牵拉力的状态下,通过使位于上游侧的芯部31旋转,基材2向下游侧被送出,通过适当地对芯部31施加制动,基材2在不会挠曲的情况下以一定的速度被送出。另外,通过调节芯部41的旋转,既能够抑制送出的基材2发生挠曲,同时相反地也能够以不对基材2施加必要程度以上的张力的方式进行卷取。
45.此处,基材2是沿一个方向延伸的具有挠性的薄板状的长条体,可应用具有厚度0.01mm~0.2mm、宽度5mm~1600mm的平板形状的长条体。另外,作为材质,没有特别限定,例如可以适当使用pet(polyethylene terephthalate,聚对苯二甲酸乙二醇酯)等树脂膜。
46.这样,上述束保持辊3与束保持辊4成为对辊,一个将基材2送出,另一个以与上述送出速度相同的卷取速度将基材2卷取,由此能够一边将施加于基材2的张力维持在规定的值一边输送基材2。
47.主辊5在基材2的输送路径中设置于束保持辊3与束保持辊4之间,形成为直径比上述束保持辊各自的芯部31和芯部41大的大致圆筒形状。主辊5的外周面51在周向上形成为曲率一定的曲面,由未图示的控制装置进行驱动控制而旋转。束保持辊3和束保持辊4随着
该主辊5的旋转工作而被控制旋转,由此,从束保持辊3送出的基材2在负荷有规定张力的状态下沿着主辊5的外周面51被输送。即,在基材2沿着主辊5的外周面51的状态下,束保持辊3和束保持辊4随着主辊5的旋转而以与基材2的输送连动的方式进行旋转,由此基材2在基材2整体张紧的状态下以其表面与各成膜室7对置的姿态从束保持辊3向束保持辊4被输送。
48.通过像这样在张紧的状态下输送基材2,并在输送基材2的同时利用成膜室7进行成膜,能够防止成膜时的基材2的抖动,能够提高层积于基材2上的薄膜的膜厚精度,并且能够防止由基材2的抖动所致的颗粒的产生。另外,通过增大主辊5的曲率半径,可在基材2以更接近平坦的状态被支承的同时进行成膜,因此能够防止成膜后的基材2产生翘曲,同时,基材2与成膜室7内的等离子体电极72的距离大致均一,易于形成膜厚均匀的薄膜。需要说明的是,成膜时的基材2的输送速度达到40~50m/分钟。
49.另外,通过将从主辊5到作为卷取辊的束保持辊4的张力设定得比从作为送出辊的束保持辊3到主辊5的张力稍高,能够使基材2进一步紧密贴附在主辊5上。
50.主辊室6是为了容纳主辊5并将室内的压力保持恒定而将周围用罩包围而成的空间。除了形成成膜装置1的外装的罩以外,主辊室6还具有间隔部61,利用该间隔部61在成膜装置1内分隔出主辊室6和后述的成膜室7。通过该间隔部61,形成沿着主辊5的外周部51输送的基材2仅一部分暴露于成膜室7的方式。
51.另外,本实施方式中采取了下述方式:仅在成膜室7侧设置真空泵71,通过真空泵71的工作,主辊室6也与成膜室7一起被减压,但也可以在主辊室6侧也设置有真空泵。
52.需要说明的是,在主辊室6也设置真空泵的情况下,为了防止在成膜室7内产生的颗粒被卷到成膜室7外,主辊室6内的压力优选将设定得比成膜室7内的压力高。
53.需要说明的是,本实施方式中,束保持辊3和束保持辊4被容纳在主辊室6内,但也可以具有将它们设置在主辊室6的外部的构成。但是,通过像本实施方式这样将它们设置在主辊室6内,能够保护基材2和成膜后的基材2(成膜基材)免于暴露于大气中。
54.成膜室7是利用真空成膜法之一的等离子体cvd(chemical vapor deposition,化学气相沉积)法在基材2上形成薄膜的机构。该成膜室7具有:将室内减压的真空泵71、施加用于产生等离子体的高电压的等离子体电极72、将作为形成于基材2上的薄膜的原料的原料气体供给至室内的原料气体供给部73。另外,本实施方式中,作为等离子体的原料的等离子体形成气体也从原料气体供给部73供给。
55.该成膜室7中,在利用真空泵71将成膜室7内减压并从原料气体供给部73供给等离子体形成气体的状态下对等离子体电极72施加电压,由此在等离子体电极72的附近产生等离子体,成膜室7内成为等离子体气氛。在像这样成为等离子体气氛的状态下,从原料气体供给部73供给原料气体,由此原料气体被该等离子体分解(活化),在与成膜室7对置的基材2的膜形成面上形成薄膜。
56.另外,本实施方式中,进一步设置有通过减压来控制成膜室7内的压力的未图示的压力控制机构,在原料气体的供给之前,利用真空泵71将成膜室7内减压,直至达到规定的压力。需要说明的是,本实施方式中,在成膜室7的内部被减压至达到10-2
pa以下后供给原料气体。并且,在通过供给原料气体而使成膜室7的内部达到0.5pa~3.0pa左右的状态下进行成膜。
57.另外,本实施方式中,以与主辊5的外周面51中的基材2所接触的区域对置的方式
沿着外周面51并排设置有2个成膜室7(成膜室7a、7b),通过束保持辊3、束保持辊4、主辊5等的旋转,一边输送基材2一边利用各成膜室7进行成膜,由此在基材2上利用成膜室7a、成膜室7b依次进行薄膜的形成。需要说明的是,2个成膜室7均具有上述真空泵71、等离子体电极72和原料气体供给部73,但为了作图的方便,图1中仅对成膜室7a所具有的真空泵71、等离子体电极72和原料气体供给部73标注了符号。
58.等离子体电极72具有沿主辊5的宽度方向(y轴方向)延伸的大致u字形状,图1中仅示出了大致u字形状的等离子体电极72的大致直线状部分的截面。另外,在等离子体电极72的端部连接有未图示的高频电源。
59.另外,等离子体电极72的折返部分形成为位于成膜室7的外侧,仅等离子体电极72的大致直线状的部分与主辊5上的基材2对置。
60.另外,等离子体电极72被在与主辊5对置的方向具有开口的电极罩74所包围。成膜中成膜室7为减压状态,但利用该电极罩74,可抑制供给至等离子体电极72附近的等离子体形成气体的扩散,使等离子体的形成和维持变得容易。
61.原料气体供给部73是设置于成膜室7内的主辊5附近的、沿主辊5的宽度方向(y轴方向)延伸的管状部件,其经由配管与成膜装置1外的未图示的原料气体供给机构连接。另外,原料气体供给部73中,沿y轴方向设置有2个以上的开口,对于主辊5上的基材2的膜形成面附近,在基材2的整个宽度方向(y轴方向)上大致均匀地供给原料气体。
62.另外,本实施方式中,原料气体供给部73也经由配管与成膜装置1外的未图示的等离子体形成气体供给机构连接,如上所述等离子体形成气体也从原料气体供给部73被供给至成膜室7内的等离子体电极72附近。
63.此处,本实施方式中,原料气体例如为hmds(六甲基二硅氮烷)气体。hmds气体含有硅和碳,通过供给氩气、氮气等作为等离子体形成气体,形成密合性高的碳化硅(sic)系薄膜,另外,通过供给氧气作为等离子体形成气体,形成致密且阻隔性高的sio2膜。
64.此处,本实施方式中,sio2膜如上所述阻隔性高,是与作为功能膜的阻隔膜的阻隔性这一功能有很大关系的膜。
65.与此相对,碳化硅系薄膜的密度比sio2膜低,因此阻隔性比sio2膜低,几乎与阻隔膜的阻隔性无关,因此与sio2膜相比,对组成没有严格的限制。取而代之,碳化硅系薄膜如上所述密合性高,通过在基材2与sio2膜之间、以及sio2膜与sio2膜之间形成该碳化硅系薄膜,可形成不仅阻隔性高、而且柔性也高的阻隔膜。
66.此处,本说明中,从阻隔膜的角度出发,将具有阻隔性的sio2膜称为阻隔层、将具有密合性的碳化硅系薄膜称为缓冲层,在图1的实施方式中,成膜室7a形成缓冲层,成膜室7b形成阻隔层。即,薄膜的表层为阻隔层。
67.引导辊8在本发明中称为引导部件,是形成基材2的输送路径的部件的一种方式,是相对于束保持辊3、束保持辊4和主辊5配置于规定的相对位置的圆柱状的辊体。各个引导辊8以其中心轴为旋转轴,其旋转轴的方向与束保持辊3、束保持辊4和主辊5的旋转轴的方向相同。从束保持辊3卷出的基材2通过与各个引导辊8的外周面的一部分接触,在沿着引导辊8的外周面被引导输送方向的同时前进,并被卷取到束保持辊4上。此时,基材2的输送路径由引导辊8的配置所决定,各引导辊8通过与基材2的摩擦力一边旋转一边将基材2向下游侧送出。另外,通过设置于主辊5附近的引导辊8来调整基材2相对于主辊5的包角,确保充分
的包角,以使基材2在主辊5上无滑动地输送。
68.需要说明的是,本说明中,将这些引导辊8之中与基材2的待形成薄膜的面(膜形成面)接触的引导辊称为膜形成面侧辊8a,将与膜形成面的相反侧的面接触的辊称为背面侧辊8b。
69.保护部件贴合部9a在基材2的输送路径中位于成膜室7的下游侧,且位于最先与基材2的膜形成面侧接触的膜形成面侧辊8a与成膜室7之间,是将保护部件b贴合在形成了薄膜的基材2上的部件,在本实施方式中为与主辊5的外周面51对置的夹辊。通过利用该保护部件贴合部9a和主辊5将基材2和保护部件b一起夹入,将保护部件b向基材2按压,由此将保护部件b贴合在基材2上。
70.图2示出了本发明的一个实施方式中的保护部件b,图2(a)是表示保护部件b与基材2的位置关系的图,图2(b)是表示贴合了保护部件b的基材2与膜形成面侧辊8a的位置关系的图。
71.保护部件b是具有挠性的长条的带状体,材质为树脂、纸等,在与基材2对置的一侧的整个面上具有粘合性。如图2(a)所示,保护部件b与基材2的膜形成面侧对置而被贴合。
72.此处,如上所述,保护部件b通过位于成膜室7下游侧的保护部件贴合部9a被贴合,因此在基材2上形成有薄膜m的状态下将保护部件b与基材2贴合。即,薄膜m位于基材2与保护部件b之间,如图2(b)所示,在基材2和保护部件b被膜形成面侧辊8a引导时,不是薄膜m而是保护部件b与膜形成面侧辊8a的表面接触。因此,能够避免形成在基材2上的薄膜m与膜形成面侧辊8a发生物理接触,因此即使假设在膜形成面侧辊8a的外周面的一部分形成有因颗粒的附着等所致的微小的凹凸,也能够防止该微小的凹凸对薄膜m造成损伤。
73.另外,由于保护部件贴合部9a位于成膜室7的下游侧,因此在利用成膜室7形成薄膜时,保护部件b未贴合在基材2上,因此保护部件b不会妨碍利用成膜室7在基材2上形成薄膜。
74.回到图1,本实施方式的成膜装置1中,在保护部件贴合部9a的附近设置有束保持辊91。从束保持辊91卷出的保护部件b被引导至保护部件贴合部9a,沿着保护部件贴合部9a的外周面的一部分,保护部件b被送至利用保护部件贴合部9a和主辊5将基材2和保护部件b夹入的位置。
75.束保持辊91是卷绕有用于贴合在基材2上的保护部件b的圆柱状的辊体,通过从该束保持辊91卷出保护部件b,将保护部件b向保护部件贴合部9a供给。
76.需要说明的是,卷绕在束保持辊91上的保护部件b的前端部被手动引导至保护部件贴合部9a,并贴合在基材2上。从该状态开始利用束保持辊3、束保持辊4和主辊5实施基材2的输送,由此,从束保持辊91卷出保护部件b的推进力是通过贴合有保护部件b的基材2被主辊5和束保持辊4沿输送方向牵拉而产生的。因此,束保持辊91即使没有马达等驱动源也无妨。
77.另外,本实施方式中,成膜装置1还设置有在基材2即将被束保持辊4卷取之前将保护部件b从基材2剥离的保护部件剥离部9b。该保护部件剥离部9b是由在束保持辊4的跟前的位置夹着基材2的一对圆柱状的辊体构成的夹辊。保护部件b沿着形成保护部件剥离部9b的一对辊体中的一个辊体的外周面将保护部件b与基材2分离。
78.另外,在保护部件剥离部9b附近具有束保持辊92,从基材2剥离的保护部件b被引
导至束保持辊92并被卷取。
79.束保持辊92为圆柱状的辊体,安装于未图示的马达等驱动源上,以自身的中心轴为旋转轴进行旋转驱动。保护部件b最初在保护部件剥离部9b的位置通过手动从基材2剥离,并被该束保持辊92卷取。之后,通过束保持辊92的旋转驱动,保护部件b自动连续地在保护部件回收部9b的位置从基材2剥离,并被束保持辊92卷取。此处,束保持辊92对保护部件b的回收速度与束保持辊4对基材2的回收速度相同。
80.另外,在完成向基材2整体上形成薄膜、保护部件b全部被束保持辊92卷取后,通过将该束保持辊92更换到束保持辊91的位置,能够将保护部件b再利用。
81.此处,图1中以粗线表示的部分表示保护部件b被输送的部分。这在之后的附图中也同样。图1中可知,基材2的输送路径之中,在保护部件贴合部9a与保护部件剥离部9b之间的部分,保护部件b的输送路径与基材2的输送路径一致,保护部件b仅在该部分贴合在基材2上。成膜室7的下游的膜形成面侧辊8a全部位于该粗线所表示的路径上,由此在被束保持辊4卷取之前的期间,能够完全避免基材2上的薄膜与膜形成面侧辊8a接触,因此能够防止膜形成面侧辊8a的表面导致薄膜损伤。因此,本发明的成膜装置1能够在不降低薄膜的性能的情况下在基材2上形成薄膜。
82.另外,在基材2即将被束保持辊4卷取之前,保护部件剥离部9b将保护部件b剥离,由此,利用保护部件贴合部9a在基材2上贴合保护部件b之前附着在薄膜上的颗粒等被转印至保护部件b的粘合面,束保持辊4能够在基材2上不附着有颗粒的状态下将基材2卷取。
83.另外,可防止束保持辊4将基材2连同保护部件b一起卷取的情况下可能发生的卷绕偏移,仅卷取基材2。
84.需要说明的是,本实施方式中,为了防止在保护部件剥离部9b将保护部件b剥离时薄膜与保护部件b一起剥离,保护部件b的粘合力优选在与基材2一起输送的期间不发生偏移的条件范围内相对较弱。
85.接着,将另一实施方式中的保护部件b示于图3。该实施方式中,保护部件b在与基材2对置的一侧的面的宽度方向两端部具有强粘合部b1,在其之间具有弱粘合部b2。弱粘合部b2的粘合力与强粘合部b1相比较弱,有时也可以无粘合力。
86.如上所述,保护部件b的粘合力强的情况下,薄膜可能与保护部件b一起剥离。此处,形成在基材2上的薄膜大多在特别是宽度方向内侧的部分要求作为薄膜的性能,与此相对,形成在宽度方向两端部的薄膜有时在之后的工序中被切割、废弃等,对性能的期待小;或者本来就未在宽度方向端部形成有薄膜。这种情况下,在与基材2的宽度方向两端部对置的强粘合部b1,以强粘接力与基材2的膜形成面侧贴合,另一方面,在基材2的两端部之间的部分,基材2与保护部件b的粘接力为弱的状态,由此能够在将保护部件b从基材2剥离时防止薄膜的重要部分与保护部件b一起剥离。
87.接着,将又一实施方式中的保护部件b示于图4。图4(a)是表示保护部件b与基材2的位置关系的图,图4(b)是表示贴合有保护部件b的基材2与膜形成面侧辊8a的位置关系的图。该实施方式中,保护部件b在基材2的宽度方向上仅与基材2的一部分对置并贴合。图4(a)的方式中,保护部件b仅贴合在基材2的宽度方向两端部。
88.像这样仅在一部分贴合有保护部件b的基材2与膜形成面侧辊8a接触时,在基材2的未贴合有保护部件b的部分与膜形成面侧辊8a之间形成图4(b)所示的间隙s,因此能够防
止形成在基材2上的薄膜m与膜形成面侧辊8a的外周面接触。
89.该实施方式中,贴合保护部件b的部分优选选择基材2的宽度方向两端部等由于在之后的工序中被切割、废弃而对薄膜的性能的期待小的部分、或者本来就未形成薄膜的部分,由此,在将保护部件b从基材2剥离时,能够防止薄膜的重要部分与保护部件b一起剥离。在基材2的宽度方向的尺寸比较小、不易产生挠曲的情况下,使用这样的保护部件b是有用的。
90.图5是本发明中的另一方式中的成膜装置1。
91.该成膜装置1中,束保持辊3与束保持辊4的旋转方向可以反转,由此,基材2的输送方向可以反转。图1中采取了从束保持辊3卷出基材2、向束保持辊4上卷取基材2的方式,但通过使束保持辊3、束保持辊4和主辊的旋转方向反转,与上述相反地,束保持辊4成为送出侧,束保持辊3成为卷取侧。并且,通过在每隔规定的时间使基材2的输送方向反转的同时进行成膜,基材2在成膜装置1内一边往返一边进行成膜。
92.此处,该实施方式中,为了在基材2的输送方向反转的情况下也能够在成膜室7的下游侧将保护部件b贴合在基材2上,隔着成膜室7在基材2的输送路径的两侧设置有保护部件贴合部9a和保护部件剥离部9b。由此,即使在成膜装置1内使基材2反转而输送、成膜的情况下,也能够防止形成在基材2上的薄膜与膜形成面侧辊8a发生物理接触。
93.需要说明的是,该成膜装置1中,如图5中粗线所示,也可以使用在基材2的输送方向上位于成膜室7的上游侧的保护部件贴合部9a和保护部件剥离部9b,在直到即将利用成膜室7进行成膜之前的期间将保护部件b贴合在基材2的膜形成面上。由此,能够防止颗粒等附着到基材2的膜形成面上。
94.图6是本发明中的又一实施方式中的成膜装置1。
95.该成膜装置1中,在保护部件剥离部9b从基材2剥离的保护部件b经由2个以上的引导辊的引导而被引导向保护部件贴合部9a,并再次贴合至基材2上。即,形成了保护部件b的循环路径,以使保护部件b被再利用。此处,各引导辊95可以是不与驱动源连接的自由辊,另外,也可以将一部分引导辊95与驱动源连接而辅助使保护部件b循环的力。
96.图1所示的实施方式的成膜装置1的情况下,需要预先准备与基材2同等长度的保护部件b,与此相对,该实施方式的成膜装置1中,可形成循环路径的长度的保护部件b就足够了,能够使应准备的保护部件b的长度较短。
97.另外,通过像图7那样将保护部件b的循环路径设置在成膜室7的上游侧和下游侧这两侧,在基材2的输送方向可以反转的情况下,不论是向哪个输送方向输送基材2,保护部件b都可保护形成在基材2上的薄膜,能够防止薄膜与膜形成面侧辊8a接触。另外,通过使用在基材2的输送方向上位于成膜室7的上游侧的保护部件贴合部9a和保护部件剥离部9b,在直到即将利用成膜室7进行成膜之前的期间将保护部件b贴合在基材2的膜形成面上,能够防颗粒等附着到基材2的膜形成面上。
98.图8是本发明中的又一实施方式中的成膜装置1。
99.该成膜装置1中,基材2以在保护部件贴合部9a被贴合了保护部件b的状态在束保持辊4上被卷取。通过像这样将基材2与保护部件b一起卷取,能够在基材2被卷取的状态下防止薄膜与基材2的背面接触。
100.另外,该实施方式的成膜装置1中,如图8所示,在从束保持辊3卷出的基材2上也预
先贴合有保护部件b的情况下,可以通过设置在成膜室7的上游侧的保护部件剥离部9b在利用成膜室7进行成膜前将保护部件b从基材2剥离。
101.利用以上的成膜装置,能够不降低功能膜的性能而在基材上形成功能膜。
102.此处,本发明的成膜装置不限于图示的方式,也可以为本发明的范围内的其他方式。例如,本说明中示出了阻隔膜相当于功能膜的实施方式,但不限于此,也可以为了形成透明导电膜、防反射膜等其他功能膜而使用本发明的成膜装置。
103.另外,形成基材的输送路径的引导部件不限于上述说明中的引导辊8那样的辊体,例如也可以为带等方式。
104.另外,本说明中,薄膜的形成使用了等离子体cvd法,但不限于此,例如也可以为催化化学气相沉积法(cat cvd)那样的其他cvd法、或者溅射法、蒸镀法之类的其他真空成膜法。
105.另外,上述说明中,成膜室为2个,但不限于此,也可以为1个或3个以上。
106.另外,上述说明中,基材为pet膜,但不限于此,也可以为pen膜等其他树脂膜。另外,不限于树脂膜,例如也可以为金属膜等。
107.另外,关于基材与保护部件贴合方式,在上述说明中利用粘合力,但不限于此,例如也可以利用静电。
108.符号说明
109.1 成膜装置
110.2 基材
111.3 束保持辊
112.4 束保持辊
113.5 主辊
114.6 主辊室
115.7 成膜室
116.7a 成膜室
117.7b 成膜室
118.8 引导辊(引导部件)
119.8a 膜形成面侧辊
120.8b 背面侧辊
121.9a 保护部件贴合部
122.9b 保护部件剥离部
123.31 芯部
124.41 芯部
125.51 外周面
126.61 间隔部
127.71 真空泵
128.72 等离子体电极
129.73 原料气体供给部
130.74 电极罩
131.91 束保持辊
132.92 束保持辊
133.95 引导辊
134.100 成膜装置
135.101 基材
136.102 成膜室
137.103 主辊
138.104 引导辊
139.104a 膜形成面侧辊
140.104b 背面侧辊
141.b 保护部件
142.b1 强粘合部
143.b2 弱粘合部
144.m 薄膜
145.s 间隙