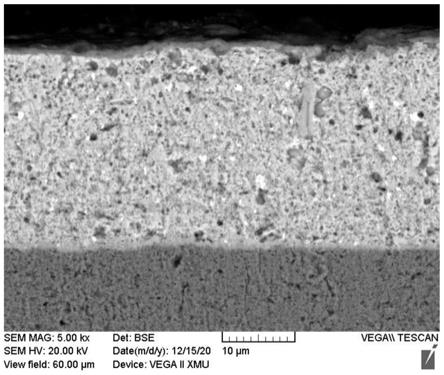
1.本发明属于金属合金材料技术领域,涉及一种铜合金轴瓦材料表面铅锡合金镀层的制备方法。
背景技术:2.轴瓦合金材料是金属材料的机械、物理、化学性质以及材料轴承特性的折衷产物,所以没有最好的轴瓦合金材料,只有在一定使用条件下较好的轴瓦合金材料。轴瓦由三部分组成,分别为钢背、减摩合金层和软镀层,滑动轴承工作时,轴瓦与转轴之间要求有一层很薄的油膜起润滑作用。如果润滑不良,轴瓦与转轴之间就存在直接的摩擦,摩擦会产生很高的温度,虽然轴瓦是由特殊的耐高温合金材料制成,但发生直接摩擦产生的高温仍然足以将其烧坏,轴瓦还可能由于负荷过大、温度过高、润滑油存在杂质或黏度异常等因素造成烧瓦,烧瓦后滑动轴承就损坏了。
3.目前重型动力机械,如汽轮机等大型机器的高速轴瓦;压缩机等轴承和轴瓦;轧钢机等轴承、轴瓦;磨床支架滑块使用的基本都是铜基轴承合金,即以铜为基体加入铅、锡等合金元素,制备出既有硬质相作为轴瓦材料的支撑,又有软质相在轴承工作过程中起润滑作用的轴承材料,但是这种材料屈服强度低,在实际工况中由于高速重载使用环境,减摩合金层易磨损,轴瓦材料的寿命普遍不高,且目前重型机械中使用的轴瓦大多依赖进口,轴瓦材料的寿命不高导致机械使用过程中产生巨大成本。
技术实现要素:4.本发明的目的是提供一种铜合金轴瓦材料表面铅锡合金镀层的制备方法,解决了现有技术中存在的现有铜合金轴瓦材料使用过程中寿命过低,成本高的问题。
5.本发明所采用的技术方案是,一种铜合金轴瓦材料表面铅锡合金镀层的制备方法,具体按照以下步骤实施:
6.步骤1、称取锡块和铅块,加热融化得到锡铅合金a;
7.步骤2、对铜合金轴瓦材料表面进行预处理;
8.步骤3、将经过步骤2预处理的铜合金轴瓦材料置于熔融态的锡铅合金a中进行热浸镀,冷却后得到铜合金轴瓦材料表面铅锡合金镀层。
9.本发明的特点还在于:
10.步骤1中加热熔融锡块和铅块时加入稀土。
11.步骤1中融化温度为320
‑
350℃,升温速率6
‑
10℃/min,融化时间50
‑
80min。
12.步骤2具体按照以下步骤实施:
13.步骤2.1、用砂纸打磨铜合金轴瓦材料表面直至光滑,得到铜合金b;
14.步骤2.2、将步骤2.1中得到的铜合金b放入配置好的碱溶液进行去油污处理,随后放入超声波清洗仪清洗10
‑
20min,得到铜合金c;
15.步骤2.3、将步骤2.2得到的铜合金c放入配置好的助镀液中进行助镀处理,然后使
用烘干箱在40
‑
60℃的温度下进行烘干处理,得到铜合金d。
16.步骤2.1中使用500#
‑
2000#的水砂纸进行打磨。
17.步骤2.2中碱洗溶液的溶质包括质量比为3
‑
5:1
‑
3:1的naoh、na2co3和na2sio3,其中h2o占溶液总质量的60
‑
80%,碱洗溶液温度为70
‑
90℃,碱洗时间为30
‑
60min。
18.步骤2.3中助镀液的配比为0.5
‑
1.0mlhcl、5
‑
15gzncl2、1.0
‑
2.0gnh4cl、1.0
‑
5.0gnacl和30
‑
50mlh2o,助镀液温度为70
‑
90℃,保温时间为10
‑
30min。
19.步骤3中热浸镀温度为200
‑
350℃,热时间为10
‑
70s。
20.本发明的有益效果是:通过本发明的制备方法在铜合金轴瓦材料表面热浸镀了一层铅锡合金镀层,镀层与铜合金基体之间具有良好的界面结合强度,得到的这种铅锡合金镀层和基体的界面临界载荷可以达到20
‑
30n,并且临界载荷相当稳定,扩散层厚度合适;这种在现有铜合金轴瓦材料表面热浸镀一层铅锡合金镀层的方法,在很大程度上减少了轴瓦材料合金层的磨损,可以大幅度的提高现有铜合金轴瓦的使用寿命,从而达到节约成本的目的,产生巨大的经济效益。
附图说明
21.图1是本发明实施例1所获得铅锡合金镀层的5000倍显微组织图;
22.图2是本发明实施例2所获得铅锡合金镀层的5000倍显微组织图;
23.图3是本发明实施例3所获得铅锡合金镀层的5000倍显微组织图;
24.图4是本发明实施例4所获得铅锡合金镀层的5000倍显微组织图。
具体实施方式
25.下面结合附图和具体实施方式对本发明进行详细说明。
26.本发明一种铜合金轴瓦材料表面铅锡合金镀层的制备方法,具体按照以下步骤实施:
27.步骤1,按照质量比80
‑
95:5
‑
20的比例称取纯度不小于99.9%的sn块和pb块,将装有称量好sn块的坩埚放入坩埚式电阻炉中,电阻炉温度设置为320
‑
350℃,升温速率为6
‑
10℃/min,保温时间50
‑
80min;待sn块熔化为液体后加入pb块,并且加入微量的稀土,这可以有效的防止铅锡合金中铅的偏聚现象,使游离的铅单质可以较均匀的分布在铅锡合金中,在保温过程中对金属液持续进行搅拌,保温完成后从电阻炉中取出坩埚,空冷至室温,得到铅锡合金a;
28.步骤2:铜合金轴瓦材料表面预处理
29.使用500#
‑
2000#的水砂纸将铜合金轴瓦材料金属块表面打磨光滑,得到铜合金b,随后对打磨光滑的铜合金b放入碱洗溶液中进行碱洗,去除其表面的油污等有机污染物,碱洗溶液的溶质为naoh、na2co3、na2sio3,其质量比为3
‑
5:1
‑
3:1,其中h2o占溶液总质量的60
‑
80%,溶液温度为70
‑
90℃,碱洗时间为30
‑
60min;碱洗完成后,取出铜合金b,用蒸馏水冲洗干净,最后将其放入烧杯,往烧杯中倒入酒精放入超声波清洗仪中清洗10
‑
20min,得到铜合金c;接着又对碱洗后的铜合金c进行助镀处理,助镀溶液的配比为0.5
‑
1.0mlhcl、5
‑
15gzncl2、1.0
‑
2.0gnh4cl、1.0
‑
5.0gnacl和30
‑
50mlh2o,溶液温度为70
‑
90℃,保温时间为10
‑
30min,保温结束后,使用烘干箱在40
‑
60℃的温度下对其进行烘干处理,最后得到铜合
金d;
30.步骤3,将步骤2中得到的铜合金d放入熔融态的铅锡合金a中进行热浸镀处理,在放入铜合金d之前用金属棒将镀液表面的氧化物等杂质清理干净,热浸镀温度为200
‑
350℃,热浸镀时间为10
‑
70s,热浸镀完成后,将试样取出进行空冷,得到铜合金铅锡合金镀层,至此制备完成。
31.实施例1
32.本发明提供一种铜合金轴瓦材料表面铅锡合金镀层的制备方法,具体包括以下几个步骤:
33.步骤1,按照质量比95:5的比例称取纯度不小于99.9%的sn块和pb块,将装有称量好sn块的坩埚放入坩埚式电阻炉中,电阻炉温度设置为320℃,升温速率为8℃/min,保温时间60min;待sn块熔化为液体后加入pb块,并且加入微量稀土,这可以有效防止铅锡合金中铅的偏聚现象,使游离的铅单质可以较均匀的分布在铅锡合金中,在保温过程中对金属液持续进行搅拌,保温完成后从电阻炉中取出坩埚,空冷至室温,得到铅锡合金a;
34.步骤2:铜合金轴瓦材料表面预处理
35.使用500#
‑
2000#的水砂纸将铜合金轴瓦材料金属块表面打磨光滑,得到铜合金b,随后对打磨光滑的铜合金b放入碱洗溶液中进行碱洗,去除其表面的油污等有机污染物,碱洗溶液的溶质为naoh、na2co3、na2sio3,其质量比为4:2:1,其中h2o占溶液总质量的65%,溶液温度为85℃,碱洗时间为60min;碱洗完成后,取出铜合金b,用蒸馏水冲洗干净,最后将其放入烧杯,往烧杯中倒入酒精放入超声波清洗仪中清洗10min,得到铜合金c;接着又对碱洗后的铜合金c进行助镀处理,助镀溶液的配比为0.6mlhcl、11gzncl2、1.4gnh4cl、3gnacl和45mlh2o,溶液温度为85℃,保温时间为10min,保温结束后,使用烘干箱在50℃的温度下对其进行烘干处理,最后得到铜合金d;
36.步骤3,将步骤2中得到的铜合金d放入熔融态的铅锡合金a中进行热浸镀处理,在放入铜合金d之前用金属棒将镀液表面的氧化物等杂质清理干净,热浸镀温度为210℃,热浸镀时间为30s,热浸镀完成后,将试样取出进行空冷,得到铜合金铅锡合金镀层,至此制备完成。
37.本发明实施例1制备的铅锡合金镀层的显微组织如图1所示,热浸镀的温度为210℃,可以看出其镀层为“三层结构”,分别是图片上方亮灰色的铅锡合金层、中间部分灰色的扩散层和下方深灰色的铜合金层,并且其扩散层是典型的“锯齿状”,“锯齿状”扩散层可以使镀层具有良好的界面结合强度;使用ws
‑
2005自动划痕仪得到临界载荷,施加载荷为0
‑
50n,载荷施加的速度为50n/min,划痕长度为10mm;利用nano measurer软件,测量得到扩散层的厚度;通过上述方法对本发明实施例1制备的铅锡合金镀层的界面强度和扩散层厚度进行测试计算,得到其临界载荷为23.3n、扩散层厚度为1.52μm。
38.实施例2
39.本发明提供一种铜合金轴瓦材料表面铅锡合金镀层的制备方法,具体包括以下几个步骤:
40.步骤1,按照质量比95:5的比例称取纯度不小于99.9%的sn块和pb块,将装有称量好sn块的坩埚放入坩埚式电阻炉中,电阻炉温度设置为320℃,升温速率为8℃/min,保温时间60min;待sn块熔化为液体后加入pb块,并且加入微量稀土,这可以有效防止铅锡合金中
铅的偏聚现象,使游离的铅单质可以较均匀的分布在铅锡合金中,在保温过程中对金属液持续进行搅拌,保温完成后从电阻炉中取出坩埚,空冷至室温,得到铅锡合金a;
41.步骤2:铜合金轴瓦材料表面预处理
42.使用500#
‑
2000#的水砂纸将铜合金轴瓦材料金属块表面打磨光滑,得到铜合金b,随后对打磨光滑的铜合金b放入碱洗溶液中进行碱洗,去除其表面的油污等有机污染物,碱洗溶液的溶质为naoh、na2co3、na2sio3,其质量比为4:2:1,其中h2o占溶液总质量的65%,溶液温度为85℃,碱洗时间为60min;碱洗完成后,取出铜合金b,用蒸馏水冲洗干净,最后将其放入烧杯,往烧杯中倒入酒精放入超声波清洗仪中清洗10min,得到铜合金c;接着又对碱洗后的铜合金c进行助镀处理,助镀溶液的配比为0.6mlhcl、11gzncl2、1.4gnh4cl、3gnacl和45mlh2o,溶液温度为85℃,保温时间为10min,保温结束后,使用烘干箱在50℃的温度下对其进行烘干处理,最后得到铜合金d;
43.步骤3,将步骤2中得到的铜合金d放入熔融态的铅锡合金a中进行热浸镀处理,在放入铜合金d之前用金属棒将镀液表面的氧化物等杂质清理干净,热浸镀温度为250℃,热浸镀时间为30s,热浸镀完成后,将试样取出进行空冷,得到铜合金铅锡合金镀层,至此制备完成。
44.本发明实施例2制备的铅锡合金镀层的显微组织如图2所示,热浸镀的温度为250℃,可以看出其镀层为“三层结构”,分别是图片上方亮灰色的铅锡合金层、中间部分灰色的扩散层和下方深灰色的铜合金层,并且其扩散层是典型的“锯齿状”,“锯齿状”扩散层可以使镀层具有良好的界面结合强度;使用ws
‑
2005自动划痕仪得到临界载荷,施加载荷为0
‑
50n,载荷施加的速度为50n/min,划痕长度为10mm;利用nano measurer软件,测量得到扩散层的厚度;通过上述方法对本发明实施例2制备的铅锡合金镀层的界面强度和扩散层厚度进行测试计算,得到其临界载荷为23.5n、扩散层厚度为2.03μm。
45.实施例3
46.本发明提供一种铜合金轴瓦材料表面铅锡合金镀层的制备方法,具体包括以下几个步骤:
47.步骤1,按照质量比95:5的比例称取纯度不小于99.9%的sn块和pb块,将装有称量好sn块的坩埚放入坩埚式电阻炉中,电阻炉温度设置为320℃,升温速率为8℃/min,保温时间60min;待sn块熔化为液体后加入pb块,并且加入微量稀土,这可以有效防止铅锡合金中铅的偏聚现象,使游离的铅单质可以较均匀的分布在铅锡合金中,在保温过程中对金属液持续进行搅拌,保温完成后从电阻炉中取出坩埚,空冷至室温,得到铅锡合金a;
48.步骤2:铜合金轴瓦材料表面预处理
49.使用500#
‑
2000#的水砂纸将铜合金轴瓦材料金属块表面打磨光滑,得到铜合金b,随后对打磨光滑的铜合金b放入碱洗溶液中进行碱洗,去除其表面的油污等有机污染物,碱洗溶液的溶质为naoh、na2co3、na2sio3,其质量比为4:2:1,其中h2o占溶液总质量的65%,溶液温度为85℃,碱洗时间为60min;碱洗完成后,取出铜合金b,用蒸馏水冲洗干净,最后将其放入烧杯,往烧杯中倒入酒精放入超声波清洗仪中清洗10min,得到铜合金c;接着又对碱洗后的铜合金c进行助镀处理,助镀溶液的配比为0.6mlhcl、11gzncl2、1.4gnh4cl、3gnacl和45mlh2o,溶液温度为85℃,保温时间为10min,保温结束后,使用烘干箱在50℃的温度下对其进行烘干处理,最后得到铜合金d;
50.步骤3,将步骤2中得到的铜合金d放入熔融态的铅锡合金a中进行热浸镀处理,在放入铜合金d之前用金属棒将镀液表面的氧化物等杂质清理干净,热浸镀温度为290℃,热浸镀时间为30s,热浸镀完成后,将试样取出进行空冷,得到铜合金铅锡合金镀层,至此制备完成。
51.本发明实施例3制备的铅锡合金镀层的显微组织如图3所示,热浸镀的温度为290℃,可以看出其镀层为“三层结构”,分别是图片上方亮灰色的铅锡合金层、中间部分灰色的扩散层和下方深灰色的铜合金层,并且其扩散层是典型的“锯齿状”,“锯齿状”扩散层可以使镀层具有良好的界面结合强度;使用ws
‑
2005自动划痕仪得到临界载荷,施加载荷为0
‑
50n,载荷施加的速度为50n/min,划痕长度为10mm;利用nano measurer软件,测量得到扩散层的厚度;通过上述方法对本发明实施例3制备的铅锡合金镀层的界面强度和扩散层厚度进行测试计算,得到其临界载荷为21.1n、扩散层厚度为2.45μm。
52.实施例4
53.本发明提供一种铜合金轴瓦材料表面铅锡合金镀层的制备方法,具体包括以下几个步骤:
54.步骤1,按照质量比95:5的比例称取纯度不小于99.9%的sn块和pb块,将装有称量好sn块的坩埚放入坩埚式电阻炉中,电阻炉温度设置为320℃,升温速率为8℃/min,保温时间60min;待sn块熔化为液体后加入pb块,并且加入微量稀土,这可以有效防止铅锡合金中铅的偏聚现象,使游离的铅单质可以较均匀的分布在铅锡合金中,在保温过程中对金属液持续进行搅拌,保温完成后从电阻炉中取出坩埚,空冷至室温,得到铅锡合金a;
55.步骤2:铜合金轴瓦材料表面预处理
56.使用500#
‑
2000#的水砂纸将铜合金轴瓦材料金属块表面打磨光滑,得到铜合金b,随后对打磨光滑的铜合金b放入碱洗溶液中进行碱洗,去除其表面的油污等有机污染物,碱洗溶液的溶质为naoh、na2co3、na2sio3,其质量比为4:2:1,其中h2o占溶液总质量的65%,溶液温度为85℃,碱洗时间为60min;碱洗完成后,取出铜合金b,用蒸馏水冲洗干净,最后将其放入烧杯,往烧杯中倒入酒精放入超声波清洗仪中清洗10min,得到铜合金c;接着又对碱洗后的铜合金c进行助镀处理,助镀溶液的配比为0.6mlhcl、11gzncl2、1.4gnh4cl、3gnacl和45mlh2o,溶液温度为85℃,保温时间为10min,保温结束后,使用烘干箱在50℃的温度下对其进行烘干处理,最后得到铜合金d;
57.步骤3,将步骤2中得到的铜合金d放入熔融态的铅锡合金a中进行热浸镀处理,在放入铜合金d之前用金属棒将镀液表面的氧化物等杂质清理干净,热浸镀温度为330℃,热浸镀时间为30s,热浸镀完成后,将试样取出进行空冷,得到铜合金铅锡合金镀层,至此制备完成。
58.本发明实施例4制备的铅锡合金镀层的显微组织如图4所示,热浸镀的温度为330℃,可以看出其镀层为“三层结构”,分别是图片上方亮灰色的铅锡合金层、中间部分灰色的扩散层和下方深灰色的铜合金层,并且其扩散层是典型的“锯齿状”,“锯齿状”扩散层可以使镀层具有良好的界面结合强度;使用ws
‑
2005自动划痕仪得到临界载荷,施加载荷为0
‑
50n,载荷施加的速度为50n/min,划痕长度为10mm;利用nano measurer软件,测量得到扩散层的厚度;通过上述方法对本发明实施例4制备的铅锡合金镀层的界面强度和扩散层厚度进行测试计算,得到其临界载荷为22.3n、扩散层厚度为2.62μm。