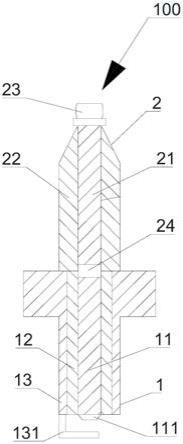
1.本发明涉及贵金属回收技术领域,具体涉及一种火花塞中贵金属的回收工艺。
背景技术:2.随着汽车技术的快速发展,火花塞的性能要求也不断提高,采用镍基合金电极的普通火花塞已无法适应大功率、高转速、大压缩比的现代发动机的需要,为了使火花塞具有更高的点火性能和使用寿命,将贵金属用于火花塞的电极中可以有效提高火花塞的性能;由于火花塞损坏后需要对内部的金属进行回收,传统的火花塞回收方式是将其破碎研磨后直接筛分其中的金属,但是,含有贵金属的火花塞损坏后采用传统的火花塞回收方法很难将贵金属单独回收,回收操作难度大,影响了贵金属的回收效益。
技术实现要素:3.有鉴于此,本发明提供了一种火花塞中贵金属的回收工艺以解决上述存在的问题。
4.本发明解决其技术问题所采用的技术方案是:
5.一种火花塞中贵金属的回收工艺,包括以下步骤:
6.(1)选取含贵金属的废旧火花塞,将废旧火花塞上的中心电极和侧电极切割分离后收集,得电极料;
7.(2)向步骤(1)的电极料中加入硝酸,加热保温,常温冷却,过滤,滤渣用去离子水洗涤至中性,得一次酸处理的电极料;
8.(3)向步骤(2)的一次酸处理的电极料中加入硫酸和水浸泡,过滤,滤渣用去离子水洗涤至中性,得二次酸处理的电极料;
9.(4)向步骤(3)的二次酸处理的电极料中加入盐酸,加热保温,常温冷却,过滤,滤渣用去离子水洗涤至中性,得三次酸处理的电极料;
10.(5)对步骤(4)的三次酸处理的电极料进行筛分,得贵金属料;
11.(6)向步骤(5)的贵金属料中加入王水,加热保温,常温冷却,过滤,滤渣用去离子水洗涤至中性,得渣料,滤液继续加热浓缩,再缓慢加入氯化铵,过滤,得氯铂酸铵沉淀,将氯铂酸铵沉淀浆化后加入水合肼进行还原处理,得海绵铂;
12.(7)将步骤(6)的渣料加入熔融状态的银中搅拌,常温冷却后加入硝酸,过滤,滤渣用去离子水洗涤至中性,得金属粉料;
13.(8)将步骤(7)的金属粉料加入王水中溶解,过滤,滤渣用去离子水洗涤至中性,得铱粉。
14.进一步地,所述步骤(1)的切割方式为采用切割模具对废旧火花塞上的中心电极和侧电极进行切割分离。
15.进一步地,所述步骤(2)中硝酸的质量分数为68%,加热温度为60
‑
80℃,保温3
‑
5min。
16.进一步地,所述步骤(3)中硫酸的质量分数为98%,硫酸与水的质量比为1:3,浸泡时间5
‑
7min。
17.进一步地,所述步骤(4)中盐酸的质量分数为15%,加热温度为75
‑
85℃,保温时间5
‑
7min。
18.进一步地,所述步骤(5)中的筛分采用的是150
‑
200目的筛网。
19.进一步地,所述步骤(6)中的加热温度为75
‑
85℃,保温5
‑
7min。
20.进一步地,所述火花塞中贵金属的回收工艺还包括以下步骤:
21.(1)将火花塞切除中心电极和侧电极后的剩余部分进行研磨,得研磨料;
22.(2)从步骤(1)的研磨料中筛选出剩余的金属;
23.进一步地,所述步骤(2)中筛选火花塞中剩余的金属采用的是重力选矿工艺,以水为介质,根据矿物密度不同将火花塞中剩余的金属筛选分离出来。
24.本发明的有益效果是:
25.本发明提供的火花塞中贵金属的回收工艺,废旧火花塞内的中心电极和侧电极中除了含有铂、铱等贵金属外,还含有铁、镍和铬等金属,因此本发明在回收废旧火花塞中的贵金属之前,先将中心电极和侧电极从废旧火花塞上切割下来,分离出的中心电极和侧电极收集得到的电极料依次采用硝酸、硫酸和盐酸进行酸洗,硝酸能将电极料中的铁溶解,并软化部分镍,从而避免金属铁对后续提取贵金属时造成影响,采用硫酸对电极料进行酸洗可以有效腐蚀电极料表面的铬,最后采用盐酸对电极料表面的镍进行完全的清洗,从而提取出火花塞中心电极和侧电机中的贵金属,电极料无需在高温高压环境下除去铁镍铬等金属,有效提高贵金属的回收速率,采用多种酸依次酸洗的步骤简单,方便操作,同时,本回收工艺还将切割后的火花塞通过球磨碾碎后采用重力选矿的方法在水中将火花塞中的金属与陶瓷分离,提高火花塞中金属的回收率。
附图说明
26.下面结合附图和实施例对本发明作进一步说明。
27.图1为火花塞的剖视图;
28.图中:100、火花塞,1、电极座,11、导电铜芯,111、中心电极,12、陶瓷电阻层,13、导电壳体,131、侧电极,2、手持段,21、金属杆,22、绝缘壳体,23、接线螺母,24、导电玻璃。
具体实施方式
29.现在结合附图对本发明作详细的说明。此图为简化的示意图,仅以示意方式说明本发明的基本结构,因此其仅显示与本发明有关的构成。
30.请参阅图1,火花塞100包括电极座1以及固定连接在电极座1一端的手持段2,电极座1包括导电铜芯11,包覆在导电铜芯11周围的陶瓷电阻层12,以及包覆在陶瓷电阻层12周围的导电壳体13,导电铜芯11的一端焊接有中心电极111,导电壳体13上焊接有与中心电极111相配合的侧电极131,侧电极131呈“l”形结构,侧电极131的弯折端延伸至中心电极的正下方,中心电极111与侧电极131之间留有间隙;手持段2包括金属杆21,包覆在金属杆21周围的绝缘壳体22,以及固定连接在金属杆21两端的接线螺母23和导电玻璃24,绝缘壳体22与导电壳体13固定连接,导电玻璃24设置在金属杆21与导电铜芯11之间且导电铜芯11的一
端与导电玻璃24固定连接;本实施例中,导电壳体13的材质为铁镍合金,中心电极111和侧电极131的材质包括铁、镍、铬导电金属以及铂、铱贵金属,金属杆21的材质为铁镍合金,绝缘壳体22的材质为陶瓷。
31.本发明提供了一种火花塞中贵金属的回收工艺,用于回收废旧火花塞中的贵金属,所述火花塞中贵金属的回收工艺包括以下步骤:
32.(1)选取含贵金属的废旧火花塞,采用切割模具对废旧火花塞上的中心电极111和侧电极131切割分离后收集得电极料。火花塞的中心电极111和侧电极131可将高压电引入燃烧室并产生火花,从而点燃气缸中的可燃混合气,因此,火花塞中的铂、铱等贵金属均存在于中心电极111和侧电极131中。
33.(2)向步骤(1)的电极料中加入质量分数68%的硝酸,加热至60
‑
80℃,保温3
‑
5min,常温冷却,过滤,滤渣用去离子水洗涤至中性,得一次酸处理的电极料。由于中心电极111和侧电极131中除了含有贵金属外,还含有铁、镍、铬等导电金属,因此,在回收贵金属之前,需要将导电金属通过酸洗溶解除去,采用硝酸能将电极料中的铁溶解,从而避免金属铁对后续提取贵金属时造成影响。
34.(3)向步骤(2)的一次酸处理的电极料中加入质量分数98%的硫酸和水,硫酸与水的质量比为1:3,浸泡5
‑
7min,过滤,滤渣用去离子水洗涤至中性,得二次酸处理的电极料。由于铬与硝酸反应时表面会生成紧密的氧化物薄膜而呈钝态,因此铬不溶于浓硝酸,采用硫酸对一次酸处理的电极料进行酸洗,铬能与硫酸反应生成硫酸铬,采用硫酸洗涤可以有效去除电极料表面的铬,从而避免金属铬对后续提取贵金属时造成影响。
35.(4)向步骤(3)的二次酸处理的电极料中加入质量分数15%的盐酸,加热至75
‑
85℃,保温5
‑
7min,常温冷却,过滤,滤渣用去离子水洗涤至中性,得三次酸处理的电极料。由于镍的表面能形成致密的氧化膜,不易与浓硝酸反应,且硫酸对镍的浸蚀极慢,因此采用稀盐酸对电极料表面的镍缓慢的进行清洗,从而避免金属镍对后续提取贵金属时造成影响。
36.(5)采用150
‑
200目的筛网对步骤(4)的三次酸处理的电极料进行筛分,得贵金属料。电极料中除了含有金属外,还含有少量的杂质,部分杂质无法溶解于酸内,通过筛网可以将未完全溶解的金属以及杂质从贵金属料中筛除,以便于后续的贵金属回收。
37.(6)向步骤(5)的贵金属料中加入王水,加热至75
‑
85℃,保温5
‑
7min,常温冷却,过滤,滤渣用去离子水洗涤至中性,得渣料,滤液继续加热浓缩,再缓慢加入氯化铵,过滤,得氯铂酸铵沉淀,将氯铂酸铵沉淀浆化后加入水合肼进行还原处理,得海绵铂;贵金属料中的主要成分为铂和铱,由于铱的化学性质稳定,是最耐腐蚀的金属,致密状态的铱无法溶解于沸腾的王水,因此将王水加热后迅速溶解贵金属料中的铂,可以有效提高贵金属的回收效率。
38.(7)将步骤(6)的渣料加入熔融状态的银中搅拌,加入硝酸,过滤,滤渣用去离子水洗涤至中性,得金属粉料。将渣料加入熔融状态的银中能使未溶解在王水中的铂族金属变为熔融状态,通过硝酸溶解后过滤可以去除渣料中的铂族金属。
39.(8)将步骤(7)的金属粉料加入王水中溶解,过滤,滤渣用去离子水洗涤至中性,得铱粉。致密状态的铱无法溶解于王水中,将金属粉料加入王水中,王水溶解金属粉料中附着的银,过滤后得到铱。
40.(9)将步骤(1)中火花塞切除中心电极111和侧电极131后的剩余部分进行研磨,使
火花塞中的陶瓷研磨成粉末,采用重力选矿工艺,以水为介质,根据矿物密度的不同从火花塞的剩余部分中筛选出剩余的金属。重力选矿是利用分选的矿物颗粒之间的相对密度、粒度、形状的差异,以及不同的矿物颗粒在介质(水、空气或其他相对密度较大的液体)中运动速率和方向的不同,使之彼此分离的选矿方法。
41.实施例1
42.本实施例的火花塞中贵金属的回收工艺包括以下步骤:
43.(1)选取含贵金属的废旧火花塞,采用切割模具对废旧火花塞上的中心电极和侧电极切割分离后收集,得电极料;
44.(2)向步骤(1)的电极料中加入质量分数68%的硝酸,加热至60℃,保温3min,常温冷却,过滤,滤渣用去离子水洗涤至中性,得一次酸处理的电极料;
45.(3)向步骤(2)的一次酸处理的电极料中加入质量分数98%的硫酸和水,硫酸与水的质量比为1:3,浸泡5min,过滤,滤渣用去离子水洗涤至中性,得二次酸处理的电极料;
46.(4)向步骤(3)的二次酸处理的电极料中加入质量分数15%的盐酸,加热至75℃,保温5min,常温冷却,过滤,滤渣用去离子水洗涤至中性,得三次酸处理的电极料;
47.(5)采用150目的筛网对步骤(4)的三次酸处理的电极料进行筛分,得贵金属料;通过筛网将未完全溶解的导电金属粉末从贵金属料中筛除,以便于后续的贵金属回收;
48.(6)向步骤(5)的贵金属料中加入王水,加热至75℃,保温5min,常温冷却,过滤,滤渣用去离子水洗涤至中性,得渣料,滤液继续加热浓缩,再缓慢加入氯化铵,过滤,得氯铂酸铵沉淀,将氯铂酸铵沉淀浆化后加入水合肼进行还原处理,得海绵铂;
49.(7)将步骤(6)的渣料加入熔融状态的银中搅拌,常温冷却后加入硝酸,过滤,滤渣用去离子水洗涤至中性,得金属粉料;
50.(8)将步骤(7)的金属粉料加入王水中溶解,过滤,滤渣用去离子水洗涤至中性,得铱粉;
51.(9)将步骤(1)中火花塞切除中心电极和侧电极后的剩余部分进行研磨,使火花塞中的陶瓷研磨成粉末,采用重力选矿工艺,以水为介质,根据矿物密度的不同从火花塞的剩余部分中筛选出剩余的金属。
52.实施例2
53.本实施例的火花塞中贵金属的回收工艺包括以下步骤:
54.(1)选取含贵金属的废旧火花塞,采用切割模具对废旧火花塞上的中心电极和侧电极切割分离后收集,得电极料;
55.(2)向步骤(1)的电极料中加入质量分数68%的硝酸,加热至70℃,保温4min,常温冷却,过滤,滤渣用去离子水洗涤至中性,得一次酸处理的电极料;
56.(3)向步骤(2)的一次酸处理的电极料中加入质量分数98%的硫酸和水,硫酸与水的质量比为1:3,浸泡6min,过滤,滤渣用去离子水洗涤至中性,得二次酸处理的电极料;
57.(4)向步骤(3)的二次酸处理的电极料中加入质量分数15%的盐酸,加热至80℃,保温6min,常温冷却,过滤,滤渣用去离子水洗涤至中性,得三次酸处理的电极料;
58.(5)采用180目的筛网对步骤(4)的三次酸处理的电极料进行筛分,得贵金属料;通过筛网将未完全溶解的导电金属粉末从贵金属料中筛除,以便于后续的贵金属回收;
59.(6)向步骤(5)的贵金属料中加入王水,加热至80℃,保温6min,常温冷却,过滤,滤
渣用去离子水洗涤至中性,得渣料,滤液继续加热浓缩,再缓慢加入氯化铵,过滤,得氯铂酸铵沉淀,将氯铂酸铵沉淀浆化后加入水合肼进行还原处理,得海绵铂;
60.(7)将步骤(6)的渣料加入熔融状态的银中搅拌,常温冷却后加入硝酸,过滤,滤渣用去离子水洗涤至中性,得金属粉料;
61.(8)将步骤(7)的金属粉料加入王水中溶解,过滤,滤渣用去离子水洗涤至中性,得铱粉。
62.(9)将步骤(1)中火花塞切除中心电极和侧电极后的剩余部分进行研磨,使火花塞中的陶瓷研磨成粉末,采用重力选矿工艺,以水为介质,根据矿物密度的不同从火花塞的剩余部分中筛选出剩余的金属。
63.实施例3
64.本实施例的火花塞中贵金属的回收工艺包括以下步骤:
65.(1)选取含贵金属的废旧火花塞,采用切割模具对废旧火花塞上的中心电极和侧电极切割分离后收集,得电极料;
66.(2)向步骤(1)的电极料中加入质量分数68%的硝酸,加热至80℃,保温5min,常温冷却,过滤,滤渣用去离子水洗涤至中性,得一次酸处理的电极料;
67.(3)向步骤(2)的一次酸处理的电极料中加入质量分数98%的硫酸和水,硫酸与水的质量比为1:3,浸泡7min,过滤,滤渣用去离子水洗涤至中性,得二次酸处理的电极料;
68.(4)向步骤(3)的二次酸处理的电极料中加入质量分数15%的盐酸,加热至85℃,保温7min,常温冷却,过滤,滤渣用去离子水洗涤至中性,得三次酸处理的电极料;
69.(5)采用200目的筛网对步骤(4)的三次酸处理的电极料进行筛分,得贵金属料;通过筛网将未完全溶解的导电金属粉末从贵金属料中筛除,以便于后续的贵金属回收;
70.(6)向步骤(5)的贵金属料中加入王水,加热至75
‑
85℃,保温5
‑
7min,常温冷却,过滤,滤渣用去离子水洗涤至中性,得渣料,滤液继续加热浓缩,再缓慢加入氯化铵,过滤,得氯铂酸铵沉淀,将氯铂酸铵沉淀浆化后加入水合肼进行还原处理,得海绵铂;
71.(7)将步骤(6)的渣料加入熔融状态的银中搅拌,常温冷却后加入硝酸,过滤,滤渣用去离子水洗涤至中性,得金属粉料;
72.(8)将步骤(7)的金属粉料加入王水中溶解,过滤,滤渣用去离子水洗涤至中性,得铱粉。
73.(9)将步骤(1)中火花塞切除中心电极和侧电极后的剩余部分进行研磨,使火花塞中的陶瓷研磨成粉末,采用重力选矿工艺,以水为介质,根据矿物密度的不同从火花塞的剩余部分中筛选出剩余的金属。
74.以上述依据本发明的理想实施例为启示,通过上述的说明内容,相关的工作人员完全可以在不偏离本发明的范围内,进行多样的变更以及修改。本项发明的技术范围并不局限于说明书上的内容,必须要根据权利要求范围来确定其技术性范围。