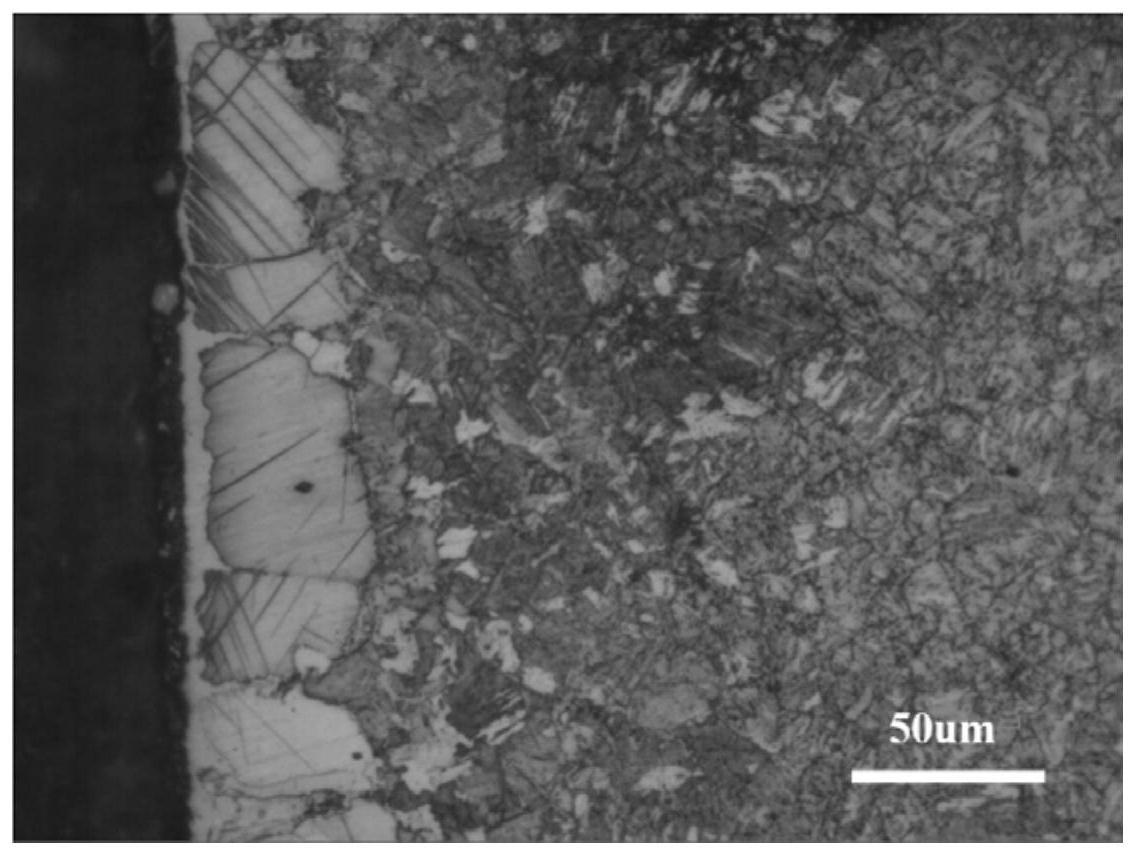
1.本发明属于金属表面处理技术领域,具体涉及一种低温高效离子氮铝共渗表面改性方法。
背景技术:2.离子渗氮在金属表面热处理中应用广泛,有着变形小,无污染及精度高的优势。然而单一离子渗氮存在如下不足:一方面是工艺效率不高,具体体现在要获得满足厚度要求的渗层通常需要70-80小时保温,极大浪费资源;另一方面是渗层硬度达不到某些严苛服役环境要求的极高表层硬度。
3.渗铝是向钢中渗入铝元素,并在工件表面形成高硬度铁铝金属间化合物,显著提升工件表面性能。与常规离子渗氮相比,渗铝的明显优势是:表层硬度提高30%以上,且耐高温氧化性、耐腐蚀性、耐磨损性等都进一步改善。然而,常规渗铝必须在高温下才能进行,渗铝温度通常在800-1000℃,如此高温条件无疑对零部件基体组织和性能不可避免带来负面影响。同时,因为铝的熔点较低,无法像其它合金元素一样通过直接放入离子渗氮炉里,实现离子氮铝共渗。基于此,开发一种低温高效离子氮铝共渗表面改性方法具有重要价值。
技术实现要素:4.基于背景技术部分指出的问题,本发明提供了一种低温高效离子氮铝共渗表面改性方法,解决铝熔点较低无法像其它合金元素一样通过直接放入离子渗氮炉里进行离子氮铝共渗的难题。并达到在低温条件下快速高效实现离子氮铝共渗,显著改善渗层综合性能的显著效果,表面硬度由常规离子渗氮的850hv提高至1250hv,提升近1.5倍,有效硬化层由175um提高至1050um,提升效率近6倍。且出现了新的强化相:fe
x
al、aln等物相。
5.本发明提供的低温高效离子氮铝共渗表面改性方法,包括以下步骤:
6.(1)将调质好的42crmo钢试样用型号为1500目砂纸打磨,使表面具有均匀细小的划痕,利于随后的絮状沉淀吸附。
7.(2)将试样接在直流电源阴极,阳极为纯铝。放入硝酸铝溶液中调节电流密度进行电解,使试样表面附着氢氧化铝沉淀。
8.直流电源器型号为itech-it6721,工作电压为1.5v-5v,工作电流为0.1a-0.5a。
9.硝酸铝溶液浓度为30g/l,电流密度为25-100ma/cm2,电解时间为10min。
10.(3)将电解沉积附着氢氧化铝的试样放入离子渗氮炉中,抽真空、调节电压、电流起辉通入氢气,进行氢气溅射40分钟,清洁试样表面;
11.将附着氢氧化铝沉淀的试样摆放在阴极盘上,并且最小间隔距离为10mm。
12.真空离子渗氮炉的型号为ldmc-8cl,极限真空度6.7pa,工作电流2-3a;工作电压为650-700v,通入氢气流量为600ml/min。
13.(4)溅射结束后,通入氮气,调节氮气氢气比例及压力,达到设定的温度后保温,进行离子氮铝共渗;
14.氮氢体积比为1:3,氮氢气体总流量为700ml/min。渗氮气氛压力为600pa,保温温度420℃-520℃,保温时间为4小时。
15.(5)待试样随炉冷却至室温后,取出附着氢氧化铝沉淀的试样,进行测试分析。
16.本发明的有益效果是:
17.(1)创造性的把铝电解成硝酸铝附着在试样表面,实现低温高效离子氮铝共渗表面改性,不仅极大的提高了工艺效率,而且显著改善渗层综合性能。
18.(2)本发明方法实现了在低温条件下形成aln、fe
x
al、fe4n等物相,对表面硬度提高有着显著效果。
19.(3)本发明方法显著提高了化合物层及有效渗层的厚度,有效硬化层提高近6倍,表面硬度提高近1.5倍。
附图说明:
20.图1是42crmo钢经过3v+0.2a+10min沉积氢氧化铝在低温高效离子氮铝共渗520℃+4h处理(即实例1)后渗层显微组织图;
21.图2是42crmo钢经过3v+0.2a+10min沉积氢氧化铝在低温高效离子氮铝共渗470℃+4h处理(即实例3)后的渗层显微组织图;
22.图3是42crmo钢经过3v+0.2a+10min沉积氢氧化铝在低温高效离子氮铝共渗420℃+4h处理(即实例2)后的渗层显微组织图;
23.图4是42crmo钢经过1.5v+0.1a+10min沉积氢氧化铝在低温高效离子氮铝共渗520℃+4h处理(即实例4)后渗层显微组织图;
24.图5是42crmo钢经过5v+0.4a+10min沉积氢氧化铝在低温高效离子氮铝共渗520℃+4h处理(即实例5)后的渗层显微组织图;
25.图6是42crmo钢经过常规离子渗氮520℃+4h处理(即对比例1)后的渗层显微组织图;
26.图7是42crmo钢常规离子渗氮和相同沉积氢氧化铝条件不同温度低温高效离子氮铝共渗处理(对应对比例1、实例1、2、3)后的物相分析图;
27.图8是42crmo钢常规离子渗氮和不同沉积氢氧化铝条件相同温度低温高效离子氮铝共渗处理(对应实例1、4、5)后的物相分析图;
28.图9是42crmo钢常规离子渗氮和不同温度低温高效离子氮铝共渗520℃+4h处理(对应对比例1、实例1、2、3)后的截面显微硬度分析图。
29.图10是42crmo钢常规离子渗氮和不同温度低温高效离子氮铝共渗520℃+4h处理(对应实例1、4、5)后的截面显微硬度分析图。
具体实施方式
30.现在结合具体实施例对本发明作进一步说明,以下实施例旨在说明本发明而不是对本发明的进一步限定。
31.实施例1
32.(1)将调质好的42crmo钢试样用1500目砂纸打磨,使表面具有均匀细小的划痕,利于随后的絮状沉淀吸附。
33.(2)将试样接在直流电源阴极,阳极为纯铝。放入硝酸铝溶液中调节电流密度进行电解,直流电源器型号为itech-it6721,工作电压为3v,工作电流为0.2a。硝酸铝溶液浓度为30g/l,电流密度为50ma/cm2,时间为10min。
34.(3)将附着氢氧化铝沉淀的试样摆放在阴极盘上,并且最小间隔距离为10mm。
35.(4)真空离子渗氮炉的型号为ldmc-8cl,极限真空度6.7pa,电流起辉2.5a;工作电压为670v,通入氢气流量为600ml/min。
36.(5)溅射结束后,通入氮气,氮氢体积比为1:3,氮氢气体总流量为700ml/min。渗氮气氛压力为600pa,在520℃保温时间为4小时。
37.(6)待试样随炉冷却至室温后,取出附着氢氧化铝沉淀的试样,进行测试分析。
38.(7)取出低温离子渗氮处理后的试样,采用光学金相显微镜观察截面显微组织见图1;
39.(8)采用hxd-1000tmc型维氏显微硬度计进行硬度分析。
40.(9)采用d/max-2500型x射线衍射仪进行物相分析。
41.实施例2
42.(1)将调质好的42crmo钢试样用1500目砂纸打磨,使表面具有均匀细小的划痕,利于随后的絮状沉淀吸附。
43.(2)将试样接在直流电源阴极,阳极为纯铝。放入硝酸铝溶液中调节电流密度进行电解,直流电源器型号为itech-it6721,工作电压为3v,工作电流为0.2a。硝酸铝溶液浓度为30g/l,电流密度为50ma/cm2,时间为10min。
44.(3)将附着氢氧化铝沉淀的试样摆放在阴极盘上,并且最小间隔距离为10mm。
45.(4)真空离子渗氮炉的型号为ldmc-8cl,极限真空度6.7pa,电流起辉2.5a;工作电压为670v,通入氢气流量为600ml/min。
46.(5)溅射结束后,通入氮气,氮氢体积比为1:3,氮氢气体总流量为700ml/min。渗氮气氛压力为600pa,在420℃保温时间为4小时。
47.(6)待试样随炉冷却至室温后,取出附着氢氧化铝沉淀的试样,进行测试分析。
48.(7)取出低温离子渗氮处理后的试样,采用光学金相显微镜观察截面显微组织见图1;
49.(8)采用hxd-1000tmc型维氏显微硬度计进行硬度分析。
50.(9)采用d/max-2500型x射线衍射仪进行物相分析。
51.实施例3
52.(1)将调质好的42crmo钢试样用1500目砂纸打磨,使表面具有均匀细小的划痕,利于随后的絮状沉淀吸附。
53.(2)将试样接在直流电源阴极,阳极为纯铝。放入硝酸铝溶液中调节电流密度进行电解,直流电源器型号为itech-it6721,工作电压为3v,工作电流为0.2a。硝酸铝溶液浓度为30g/l,电流密度为50ma/cm2,时间为10min。
54.(3)将附着氢氧化铝沉淀的试样摆放在阴极盘上,并且最小间隔距离为10mm。
55.(4)真空离子渗氮炉的型号为ldmc-8cl,极限真空度6.7pa,电流起辉2.5a;工作电压为670v,通入氢气流量为600ml/min。
56.(5)溅射结束后,通入氮气,氮氢体积比为1:3,氮氢气体总流量为700ml/min。渗氮
气氛压力为600pa,在470℃保温时间为4小时。
57.(6)待试样随炉冷却至室温后,取出附着氢氧化铝沉淀的试样,进行测试分析。
58.(7)取出低温离子渗氮处理后的试样,采用光学金相显微镜观察截面显微组织见图1;
59.(8)采用hxd-1000tmc型维氏显微硬度计进行硬度分析。
60.(9)采用d/max-2500型x射线衍射仪进行物相分析。
61.实施例4
62.(1)将调质好的42crmo钢试样用1500目砂纸打磨,使表面具有均匀细小的划痕,利于随后的絮状沉淀吸附。
63.(2)将试样接在直流电源阴极,阳极为纯铝。放入硝酸铝溶液中调节电流密度进行电解,直流电源器型号为itech-it6721,工作电压为1.5v,工作电流为0.1a。硝酸铝溶液浓度为30g/l,电流密度为25ma/cm2,时间为10min。
64.(3)将附着氢氧化铝沉淀的试样摆放在阴极盘上,并且最小间隔距离为10mm。
65.(4)真空离子渗氮炉的型号为ldmc-8cl,极限真空度6.7pa,电流起辉2.5a;工作电压为670v,通入氢气流量为600ml/min。
66.(5)溅射结束后,通入氮气,氮氢体积比为1:3,氮氢气体总流量为700ml/min。渗氮气氛压力为600pa,在520℃保温时间为4小时。
67.(6)待试样随炉冷却至室温后,取出附着氢氧化铝沉淀的试样,进行测试分析。
68.(7)取出低温离子渗氮处理后的试样,采用光学金相显微镜观察截面显微组织见图1;
69.(8)采用hxd-1000tmc型维氏显微硬度计进行硬度分析。
70.(9)采用d/max-2500型x射线衍射仪进行物相分析。
71.实施例5
72.(1)将调质好的42crmo钢试样用1500目砂纸打磨,使表面具有均匀细小的划痕,利于随后的絮状沉淀吸附。
73.(2)将试样接在直流电源阴极,阳极为纯铝。放入硝酸铝溶液中调节电流密度进行电解,直流电源器型号为itech-it6721,工作电压为5v,工作电流为0.4a。硝酸铝溶液浓度为30g/l,电流密度为100ma/cm2,时间为10min。
74.(3)将附着氢氧化铝沉淀的试样摆放在阴极盘上,并且最小间隔距离为10mm。
75.(4)真空离子渗氮炉的型号为ldmc-8cl极限真空度6.7pa电流起辉2.5a;工作电压为670v,通入氢气流量为600ml/min。
76.(5)溅射结束后,通入氮气,氮氢体积比为1:3,氮氢气体总流量为700ml/min。渗氮气氛压力为600pa,在520℃保温时间为4小时。
77.(6)待试样随炉冷却至室温后,取出附着氢氧化铝沉淀的试样,进行测试分析。
78.(7)取出低温离子渗氮处理后的试样,采用光学金相显微镜观察截面显微组织见图1;
79.(8)采用hxd-1000tmc型维氏显微硬度计进行硬度分析。
80.(9)采用d/max-2500型x射线衍射仪进行物相分析。
81.对比例1
82.(1)将42crmo钢放入型号为ldmc-8cl的真空渗氮炉内,并摆放在阴极盘。抽真空至真空度6.7pa后,调节电压为670v、电流起辉2.5a,通入600ml/min氢气,进行h2溅射,清洁试样表面。
83.(2)溅射完毕后,通入氮气,调节氮气和氢气体积比n2:h2=1:3,氮氢气体总流量为700ml/min。渗氮气氛压力为600pa,之后在给定的工艺参数(520℃+4h)下进行的离子渗氮处理。
84.(3)取出低温离子渗氮处理后的试样,采用光学金相显微镜观察截面显微组织见图2;
85.(4)采用hxd-1000tmc型维氏显微硬度计进行硬度分析。
86.(5)采用d/max-2500型x射线衍射仪进行物相分析。
87.对比图1和图6可以明显看出,在相同的温度时间条件下,低温高效离子氮铝共渗获得的化合物层明显高于常规离子渗氮,且出现明显的渗铝层,首次实现了在低温氮铝共渗。
88.对比图1、图2和图3可以明显看出,在不同的温度时间条件下,低温高效离子氮铝共渗获得的化合物层厚度随着时间的增加变厚,若温度高于520℃,导致化合物层粗化,所以在520℃效果达到最好。
89.从图7中可以看出,在相同的温度时间条件下,低温高效离子氮铝共渗与常规离子渗氮物相对比,发现附前者出现了新相fe
x
al、aln等多相组织,且fe
2-3
n及fe4n减少。在不同温度条件下,随着温度升高获得强化相aln及fe
x
al衍射峰变多。
90.从图8中可以看出,不同沉积氢氧化铝在相同低温高效离子氮铝共渗条件下,发现物相几乎相同。
91.从图9中可以看出,在相同的温度时间条件下,低温高效离子氮铝共渗与常规离子渗氮物相对比,发现前者截面硬度增加,且有效渗层大大增加。从175um提高至1050um,有效渗层提升近6倍。在不同温度时间下获得有效渗层随着温度升高而增加。
92.从图10中可以看出不同沉积氢氧化铝在相同低温高效离子氮铝共渗条件下,有效渗层及截面硬度都趋于一致,相差很小。
93.以上述依据本发明的理想实施例为启示,通过上述的说明内容,相关工作人员完全可以在不偏离本项发明技术思想的范围内,进行多样的变更以及修改。本项发明的技术性范围并不局限于说明书上的内容,必须要根据权利要求范围来确定其技术性范围。