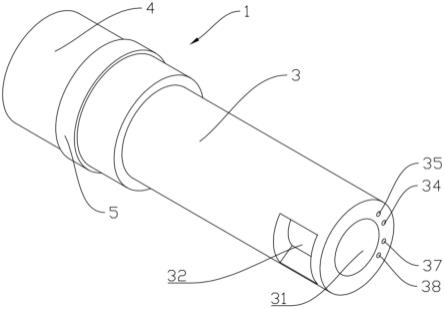
1.本实用新型涉及压铸技术领域,具体是涉及一种具有双头部冷却的压铸机料筒。
背景技术:2.目前压铸模具加工产品需要多道工序,其中定模与压铸机强板固定,模具分流锥与料缸的一端连接,料缸另一端连接入料筒,通过入料口将熔融金属倒入入料筒内,熔融金属可以为铝液等,通过压射头把熔融金属沿入料筒的孔腔推入料缸,使料缸充满熔融金属,在压射杆作用下,加大铸造压力,使熔融金属沿模具分流锥进入模具型腔,熔融金属充满模具型腔,完成产品压铸。
3.由于高温铝液在压射头的推动下,将入料筒的头部充满,而在高温高压、冷热交替的恶劣环境下,受拉应力和压应力影响,入料筒孔内表面极易产生龟裂现象,即产生铝液堆积后会使压射头磨损和拉毛,影响压射头使用寿命,同时也影响铝液从分流锥进入模具型腔的压射速度和压射力,因铝液温度不均,容易产生气泡卷入模具型腔,产品容易产生缺陷。而料缸处和入料筒的压射端是受热最集中的地方,目前多是采取对料缸进行冷却的方式,虽然解决了一定问题,但是入料筒进料时高温易造成入料筒热变形,影响使用寿命。
技术实现要素:4.本实用新型的目的是为了解决上述技术的不足而设计的一种具有双头部冷却的压铸机料筒,具有冷却效果好、延长料筒和压射头使用寿命的优点。
5.本实用新型所设计的一种具有双头部冷却的压铸机料筒,包括料筒本体,所述料筒本体两端分别为出料端和压射端,所述压射端用于连接压射组件,所述料筒本体上设置有用于倒入合金液的入料口,所述入料口靠近压射端设置,所述入料口的合金液通过压射组件流向出料端,所述出料端设置有第一冷却循环通道,所述第一冷却循环通道内设置有阻隔件,所述阻隔件使第一冷却循环通道内的冷却水流速减缓,冷却液与出料端表面充分接触,所述压射端设置有第二冷却循环通道,第二冷却循环通道对应位于入料口的下方。
6.本技术方案中,通过在料筒本体的出料端和压射端均设置冷却循环通道,冷却水通过冷却循环通道对料筒本体的两端进行冷却,以减小高温带来的影响,延长料筒本体和压射头的使用寿命;冷却水在流动过程中将料筒本体上的热量带走,可以对料筒表面进行冷却,但因水流停留时间短,带走的热量不够,因此,本技术方案通过在第一冷却循环通道内设置阻隔件,冷却水受到阻隔件的作用,在流动中具有短暂的停留,来吸收出料端的热量,达到更好的散热效果。另一方面,入料口主要用于倒入合金液,入料口下方的温度最高,通过在入料口下方设置第二冷却循环通道,能够平衡部分热量,提高料筒和压射组件的使用寿命。
7.进一步的,所述出料端套装有冷却套,所述第一冷却循环通道设置于冷却套内;所述第一冷却循环通道在冷却套表面形成有第一通道入口和第一通道出口,所述第一冷却循环通道为螺旋形。在冷却套内设置第一冷却循环通道,套装的安装方式更加方便,并且第一
冷却循环通道在冷却套内为螺旋形,冷却水流动的路径更长,与出料端表面的接触时间更长,散热效果更好。
8.更进一步的,所述阻隔件为钢珠。
9.更进一步的,所述第二冷却循环通道包括第二通道入口和第二通道出口,所述第二通道入口和第二通道出口设置于压射端底面;所述压射端还设置有第三冷却循环通道,所述第三冷却循环通道包括第三通道入口和第三通道出口,所述第三通道入口和第三通道出口设置于压射端底面;所述第二冷却循环通道和第三冷却循环通道为u形。
10.在本技术方案中,通过在压射端设置两个u形的冷却循环通道,冷却水通过压射端底面的通道入口和出口实现循环,使得压射端的热量减少,能够减少料筒本体压射端龟裂的现象,还能够保护压射头,延长料筒和压射头的使用寿命。
11.更进一步的,所述料筒本体包括入料筒和料缸,所述入料筒用于输送合金液,所述压射端设置于入料筒上,所述料缸用于连接压铸模具,所述出料端设置于料缸上,所述料筒本体由入料筒和料缸一体成型。
12.在实际使用过程中,料筒本体的结构可以为分体式或整体式,分体式料筒由入料筒与料缸组装而成,即料缸装在模具上,入料筒则安装在压铸机进料墙板上,二者分开安装形成料筒,使得料筒的整体同轴度较差,容易磨损压射头,频繁更换压射头则提高了制造成本。而本技术方案中,料筒为整体式结构,即通过设置料筒本体由入料筒和料缸一体成型,整体式料筒直接通过压铸机进料墙板和模具连接,有利于保证压射头运动时的同轴度,能够避免了分体式料筒因制造误差产生不同轴的影响,从而能有效地减少压射头的消耗量,来降低制造成本。
13.本实用新型所设计的一种具有双头部冷却的压铸机料筒,包括料筒本体,所述料筒本体两端分别为出料端和压射端,所述压射端用于连接压射组件,所述料筒本体上设置有用于倒入合金液的入料口,所述入料口靠近压射端设置,所述入料口的合金液通过压射组件流向出料端,所述出料端设置有第一冷却循环通道,所述第一冷却循环通道内设置有阻隔件,所述阻隔件使第一冷却循环通道内的冷却水流速减缓,冷却液与出料端的合金液充分接触,所述压射端设置有第二冷却循环通道;通过在料筒本体两端均设置冷却循环通道,延长料筒本体和压射头的使用寿命,通过在第一冷却循环通道内设置阻隔件,以减缓冷却水的流速,提高散热效率。
附图说明
14.图1是本公开一种具有双头部冷却的压铸机料筒的结构示意图;
15.图2是本公开一种具有双头部冷却的压铸机料筒另一角度的结构示意图;
16.图3是本公开一种具有双头部冷却的压铸机料筒的侧视示意图;
17.图4是本公开图3中a-a方向的剖视示意图;
18.图5是本公开一种具有双头部冷却的压铸机料筒的剖视示意图;
19.图6是本公开一种具有双头部冷却的压铸机料筒的主视示意图;
20.图7是本公开图6中b-b方向的剖视示意图。
21.图中:1、料筒本体;2、料缸;21、出料端;3、入料筒;31、压射端;32、入料口;33、第二冷却循环通道;34、第二通道入口;35、第二通道出口;36、第三冷却循环通道;37、第三通道
入口;38、第三通道出口;4、冷却套;41、第一冷却循环通道;42、第一通道入口;43、第一通道出口;44、阻隔件;5、圆环形凸起。
具体实施方式
22.下面将结合本实用新型实施例中的附图,对本实用新型实施例中的技术方案进行清楚、完整地描述,显然,所描述的实施例仅仅是本实用新型一部分实施例,而不是全部的实施例。基于本实用新型中的实施例,本领域普通技术人员所获得的所有其他实施例,都属于本实用新型保护的范围。
23.本领域技术人员应理解的是,在本实用新型中,术语“纵向、横向、上、下、前、后、左、右、竖直、水平、顶、底、内、外”等指示的方位或位置关系是基于附图所示的方位或位置关系,其仅是为了便于描述本实用新型和简化描述,而不是指示或暗示所指的装置或元件必须具有特定的方位、以特定的方位构造和操作,因此上述术语不能理解为对本实用新型的限制。
24.实施例1:
25.如图1至图7所示,本实施例所描述的一种具有双头部冷却的压铸机料筒,包括料筒本体1,料筒本体1两端分别为出料端21和压射端31,压射端31用于连接压射组件,料筒本体1由入料筒3和料缸2一体成型,入料筒3用于输送合金液,料缸2用于连接压铸模具,整体式料筒直接通过压铸机进料墙板和模具连接,提高压射头运动时的同轴度,有效减少压射头的消耗量,降低制造成本;压射端31设置于入料筒3上,出料端21设置于料缸2上,入料筒3上设置有入料口32,合金液通过入料口32倒入料筒3本体1内,通过压射头把合金液沿入料筒3的孔腔推入料缸2,即合金液通过压射组件流向出料端21;料筒本体1的表面还设置有圆环形凸起5,料筒本体1通过圆环形凸起5固定在压铸机墙板上。
26.出料端21和压射端31分别设置有第一冷却循环通道41和第二冷却循环通道33,第一冷却循环通道41和第二冷却循环通道33内循环有冷却水,第二冷却循环通道33对应位于入料口32的下方,通过两个冷却循环通道对料筒本体1两端散热,以减少料筒本体1表面龟裂的现象,延长料筒和压射头的使用寿命。
27.出料端21外表面套装有冷却套4,第一冷却循环通道41设置于冷却套4内,第一冷却循环通道41在冷却套4表面形成有第一通道入口42和第一通道出口43,冷却水经第一通道入口42进入第一冷却循环通道41,再由第一通道出口43出来,第一冷却循环通道41为螺旋形,冷却水流动的路径更长,与出料端21表面的接触时间更长,并且冷却面积也更大,散热效果更好,第一冷却循环通道41内设置有阻隔件44,冷却水在第一冷却循环通道41内流动,将出料端21表面的热量带走,阻隔件44使第一冷却循环通道41内的冷却水收到阻隔作用,在流动中具有短暂的停留,冷却液与出料端21表面充分接触,来吸收出料端21的热量,达到更好的散热效果,其中,本实施例中的阻隔件44为钢珠阻尼。
28.进一步的,压射端31设置有第二冷却循环通道33和第三冷却循环通道36,第二冷却循环通道33包括第二通道入口34和第二通道出口35,第二通道入口34和第二通道出口35设置于压射端31底面;第三冷却循环通道36包括第三通道入口37和第三通道出口38,第三通道入口37和第三通道出口38设置于压射端31底面;第二冷却循环通道33和第三冷却循环通道36为u形,冷却水经通道入口进入冷却循环通道,带走压射端31的部分热量,再由通道
出口流出,压射端31设置双通道循环冷却,平衡压射端31热量,保护压射组件即压射头,延长料筒和压射头的使用寿命。
29.本实施例所描述的一种具有双头部冷却的压铸机料筒,通过在料筒本体1两端均设置冷却循环通道,延长料筒本体1和压射头的使用寿命,通过在第一冷却循环通道41内设置阻隔件44,以减缓冷却水的流速,提高散热效率。
30.本实用新型不局限于上述最佳实施方式,任何人在本实用新型的启示下都可得出其他各种形式的产品,但不论在其形状或结构上作任何变化,凡是具有与本技术相同或相近似的技术方案,均落在本实用新型的保护范围之内。