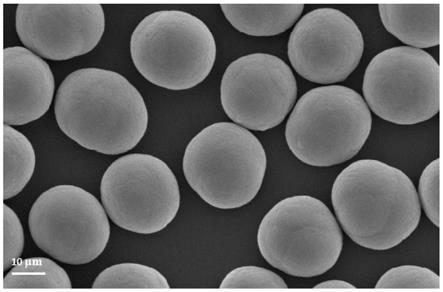
1.本发明属于锂离子电池正极材料钴酸锂的前驱体领域,涉及一种粒度均匀分布大颗粒球形掺杂碳酸钴的制备方法。
背景技术:2.钴酸锂(lco)是目前最成熟的正极材料,广泛应用于3c消费类电子产品领域。近年来,随着5g手机的兴起,消费者对电池的容量提出了更高的要求。研究表明,提高充电截止电压,能有效提高电池容量。例如,将电压从4.45v提高至4.48v,相应lco电池的能量密度能提高约3.5%。但是,提高电压会造成材料的晶体结构坍塌,导致容量衰减很快。元素掺杂能有效解决材料晶体结构的稳定性问题。al、mg、ni、mn等元素掺杂能有效改善lco在高电压下的循环性能。获得掺铝钴酸锂的传统方法是将掺杂金属盐、四氧化三钴以及碳酸锂三者混合物同时煅烧得到掺杂型钴酸锂,此方法采用固相掺杂,元素掺杂均匀性较差。目前大部分掺杂四氧化三钴是通过湿法共沉淀合成掺杂碳酸钴,然后经煅烧分解获得。但采用液相沉淀法制备掺杂碳酸钴过程中,存在以下难题:
3.采用液相沉淀法制备掺杂碳酸钴过程中,存在以下难题:
4.(1)采用间歇法合成制备掺铝大颗粒碳酸钴时,分釜(分出一半物料)后投料易产生粘连,影响碳酸钴球形度。
5.(2)由于各掺杂离子与钴离子浓度积存在较大差异,导致离子沉淀不同步。当粒度长大到一定程度时掺杂离子易单独产生新核成为新的生长位点导致产生小颗粒,影响粒度分布。
技术实现要素:6.为克服上述现有掺杂碳酸钴制备过程中存在的难题,本发明提供一种粒度均匀分布大颗粒球形掺杂碳酸钴的制备方法,以钴盐为原料、碳酸盐为沉淀剂,可溶性铝、镁、镍、锰盐为掺杂源,通过精准设置不同投料阶段的转速、流速和ph等参数,控制控制碳酸钴粒度稳定增长,避免小颗粒产生。
7.本发明采用的技术方案如下:一种粒度均匀分布大颗粒球形掺杂碳酸钴的制备方法,其包括步骤:
8.一、原辅料准备
9.将可溶性钴盐和可溶性掺杂盐混合均匀配制成溶液a,接着配制碳酸盐溶液b,供后面的步骤二和三使用;
10.二、制备碳酸钴晶种
11.将碳酸盐溶液b,加入反应釜中作为底液,在100
‑
350rpm搅拌条件下,溶液a、碳酸盐溶液b同时匀速加入反应釜,使体系ph逐步降低至7.0
‑
8.0,得到d50为5.5
‑
7.5μm碳酸钴;沉降、抽上清液,循环投料,直至d50达到8.0
‑
12.0μm,碳酸钴晶种制备完成;
12.三、碳酸钴生长
13.将步骤二中的晶种浆料均分为两份至两个反应釜中进行生长,经多次循环投料,当碳酸钴d50达到12.0
‑
15.0μm,第一阶段生长结束;第一阶段生长结束后,将每个反应釜中的浆料均分为两份至两个反应釜中进行第二阶段生长,经多次循环投料使碳酸钴15.0
‑
18.0μm,第二阶段生长结束;第二阶段生长结束后,将每个反应釜中的浆料均分为两份至两个反应釜中进行第三阶段生长,多次循环投料直至达到碳酸钴d50达到20.0
‑
25.0μm,第三阶段生长结束;整个生长过程中控制各阶段钴液流速、转速和ph值,使碳酸钴稳步生长,避免小颗粒的产生;
14.将合成的碳酸钴晶种洗涤、干燥和过筛,得到一种粒度均匀分布大颗粒球形掺杂碳酸钴。
15.所得碳酸钴d50为20.0
‑
25.0μm,qd((d90
‑
d10)/d50)小于0.4,粒度分布均匀,电镜显示无小颗粒,碳酸钴中元素掺杂含量在0.05%
‑
0.6%。
16.本发明的原理如下:
17.(1)为了防止分釜后投料产生粘连,钴液流量减小,同时转速提高,控制碳酸钴粒度增长速度,保证球形度。
18.(2)为了防止产生小颗粒,粒度增长至一定程度后控制合成体系ph值并进一步降低钴液流量,降低掺杂离子沉淀速率,避免生成新核导致小颗粒产生。
19.进一步地,步骤一中,所述可溶性钴盐为氯化钴、硫酸钴、硝酸钴中的一种或几种的混合物。
20.进一步地,步骤一中,所述可溶性掺杂盐为可溶性铝、镁、镍、锰对应的硫酸盐、硝酸盐、氯盐的一种或几种混合物。
21.进一步地,所述步骤一中,所述溶液a中,钴溶液的浓度为80~160g/l,掺杂元素与钴质量浓度比为(0.0010
‑
0.0125):1;所述的碳酸盐溶液b为碳酸铵或碳酸氢铵溶液,浓度为180~230g/l。
22.进一步地,所述步骤三中,第一阶段流量为15
‑
45ml/min,循环投料为8
‑
12次,ph为6.5
‑
7.8,转速为100
‑
250r/min第一阶段流量为15
‑
45ml/min,循环投料为8
‑
12次,ph为6.5
‑
7.8,转速为100
‑
250r/min;第二阶段流量为第一阶段流量的70
‑
80%,循环投料为7
‑
12次,ph比第一阶段低0.2
‑
0.5,转速为第一阶段的1.2
‑
1.5倍;第三阶段流量为第二阶段的30
‑
50%,循环投料为5
‑
9次,ph比第二阶段低0.2
‑
0.4,转速为第二阶段的1.2
‑
1.5倍。
23.本发明具有的有益效果如下:本发明能控制碳酸钴粒度增长速度,保证了球形度;本发明能有效控制合成过程中掺杂离子的沉淀速率,避免了小颗粒产生,得到一种粒度均匀分布大颗粒球形掺杂碳酸钴。
附图说明
24.图1为本发明实施例1制备得到的产品扫描电镜图;
25.图2为本发明实施例1制备得到的产品粒度分布图。
具体实施方式
26.以下通过实施例描述本发明的详细过程,提供实施例是为了理解的方便,绝不是为了限制本发明。
27.实施例1
28.一、原辅料准备
29.配制铝/钴质量浓度比为(0.0098
‑
0.0102):1的混合均匀溶液a,钴浓度为117g/l,铝浓度为1.17g/l,配置226g/l的碳酸氢铵溶液b,供后面的步骤二和三使用。
30.二、制备碳酸钴晶种
31.将碳酸盐溶液b加入反应釜作为底液,在250rpm搅拌条件下,溶液a和碳酸盐溶液b同时匀速加入反应釜,使体系ph逐步降低至7.5
‑
7.8,得到d50为6.1μm的碳酸钴。沉降、抽上清液,循环投料,直至d50达到10.5μm,晶种制备完成。
32.三、碳酸钴生长
33.将步骤二中的晶种浆料均分为两份至两个反应釜中进行生长;第一阶段流量为35ml/min,ph为7.4
‑
7.7,转速为130r/min。经10次循环投料使碳酸钴长大至d50为13.2μm时,第一阶段结束。第一阶段生长结束后,将每个反应釜中的浆料均分为两份至两个反应釜中进行第二阶段生长,流量为第一阶段的70%,即25ml/min,ph比第一阶段低0.2,即7.2
‑
7.5,转速为第一阶段1.25倍,即150r/min。经8次循环投料使碳酸钴17.0μm,第二阶段生长结束。第二阶段结束后,将每个反应釜中的浆料均分为两份至两个反应釜中进行第三阶段生长,第三阶段流量为第二阶段流量的50%,即12ml/min,循环投料为7次,ph比第二阶段低0.4,即6.8
‑
7.3,转速为第二阶段转速的1.2倍,即180r/min。直至达到碳酸钴d50达到20.8μm,第三阶段生长结束。
34.将合成的掺铝碳酸钴物料洗涤干燥、过筛得到掺铝球形碳酸钴。经检测d50为20.8μm,径距qd,即(d90
‑
d10)/d50=0.38,粒度分布均匀,电镜显示无小颗粒,碳酸钴中铝含量为0.45%。
35.实施例2
36.一、原辅料准备
37.将硫酸钴和十八水硫酸铝、硫酸镁、硫酸镍、硫酸锰溶液配制成铝、镁、镍、锰与钴质量浓度比分别为(0.0080
‑
0.090):1,(0.0015
‑
0.0025):1,(0.0015
‑
0.0020):1,(0.0020
‑
0.0030):1的混合均匀溶液a,钴浓度为118g/l,配置223g/l的碳酸氢铵溶液b,供后面的步骤二和三使用。
38.二、制备碳酸钴晶种
39.将碳酸盐溶液b加入反应釜作为底液,在200rpm搅拌条件下,溶液a和碳酸盐溶液b同时匀速加入反应釜,使体系ph逐步降低至7.6
‑
7.8,得到d50为6.8μm的碳酸钴。沉降、抽上清液,循环投料,直至d50达到10.5μm,晶种制备完成;
40.三、碳酸钴生长
41.将步骤二中的晶种浆料均分为两份至两个反应釜中进行生长;第一阶段流量为40ml/min,ph为7.3
‑
7.6,转速为110r/min。经10次循环投料使碳酸钴长大至d50为14.3μm时,第一阶段结束。第一阶段生长结束后,将每个反应釜中的浆料均分为两份至两个反应釜中进行第二阶段生长,流量为第一阶段的80%,即32ml/min,ph为比第一阶段低0.3,即7.0
‑
7.5,转速为第一阶段1.3倍,即145r/min。经8次循环投料使碳酸钴18.0μm,第二阶段生长结束。第二阶段结束后,将每个反应釜中的浆料均分为两份至两个反应釜中进行第三阶段生长。第三阶段流量为第二阶段流量的30%,即10ml/min,ph比第二阶段低0.2,即6.8
‑
7.3,转
速为第二阶段转速的1.4倍,即200r/min。循环投料为7次,直至碳酸钴d50达到21.5μm,第三阶段生长结束。
42.将合成的掺铝碳酸钴物料洗涤干燥、过筛得到掺铝球形碳酸钴。经检测d50为21.8μm,径距qd,即(d90
‑
d10)/d50=0.32,粒度均匀分布,电镜显示无小颗粒,碳酸钴中铝、镁、镍、锰含量分别为0.38%、0.08%、0.08%、0.17%。