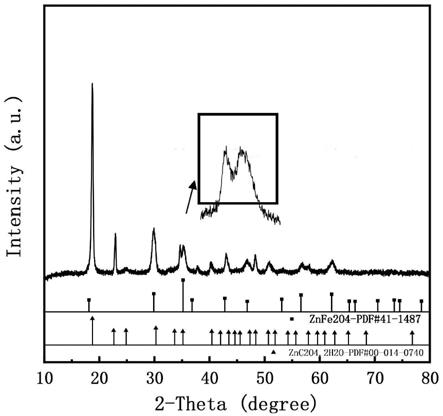
1.本发明属于湿法冶金渣综合回收技术领域,具体涉及一种铁酸锌资源化处理方法。
背景技术:2.湿法炼锌是我国大多锌冶炼企业选择的冶炼工艺,主要步骤为“焙烧-浸出-净化-电积”等工艺。锌精矿经焙烧后得到锌焙砂,锌焙砂主要成分包括铁酸锌(znfe2o4)、zno,其中zno易溶于酸,在较低的酸浓度下就可以浸出,因而湿法炼锌过程中,铁酸锌的存在是造成锌浸出率低的主要原因。铁酸锌为尖晶石结构,性质稳定并不溶于稀酸和碱。研究表明,硫酸浓度120g/l,浸出时间为150~180min,浸出温度达到75℃时铁酸锌才开始溶解,但是在高酸浓度下铁也被浸出进入到溶液中,引入了杂质,增加了后续提炼锌的步骤。同时溶液中fe
3+
的增加导致溶液电位增加,进而抑制了铁酸锌分解。在湿法炼锌工艺中,将锌焙砂中浸之后得到的锌中浸渣经热酸浸得到酸浸液,酸浸液再经过预中和得到的预中和液利用铁钒法除铁后会得到一种危险废物——铁钒渣。铁钒渣中不仅含有大量的ga、ge、in、ag和fe等有价金属,由于锌焙砂未得到有效处理,铁酸锌为铁矾渣中的难资源化分离处理的物相,加之铁矾渣本身沉渣量大,不仅浪费大量的ga、ge、in、ag和fe等有价金属资源,同时产生的锌浸渣会占用大量的土地,而且对环境也有着严重的威胁,。
3.火法炼锌工艺中,铁酸锌可以在高温下被c、so2以及co等还原成fe3o4和zno,但是该法易过还原成zno和feo或zno和fe。中国专利cn103276197a公开了一种锌焙砂闪速还原焙烧的方法,该发明虽然改进了能效高的问题,能实现锌焙砂中铁酸锌快速彻底分解还原(1~3s),但是仍存在过还原问题,如何开发一种新方法对铁酸锌进行可控高效资源化分离已成为湿法炼锌沉铁渣处理需要迫切解决的问题。
技术实现要素:4.为解决铁酸锌性质温度,资源化利用难度大的问题,本发明目的在于提供一种温和的铁酸锌转型并资源化联产fe3o4和zno的处理方法。
5.一种铁酸锌处理方法,将包含铁酸锌、草酸和还原剂的浆料进行一锅转型(也称为一锅反应),随后进行固液分离,得到草酸锌和草酸亚铁的转型产物;
6.其中,草酸与铁酸锌的重量比大于或等于0.5;还原剂与铁酸锌的重量比大于或等于0.25。
7.铁酸锌具有尖晶石结构,性质稳定,难于转型转化,另外,其酸浸难度大,浸出率很低,例如,在草酸体系中基本上没有浸出效果。为解决该行业性难题,本发明早先尝试将其进行液相一锅转型,然而早先的效果并不理想,主要在于转型效果不理想,且转型的固相产物负载在原料表面堵塞反应通道,进一步影响转型处理效果。针对该技术问题,本发明创新地发现,将铁酸锌置于包含草酸和还原剂的体系内,在草酸和还原剂的同步处理下,可以实现协同,可以一锅、温和地液相转型形成草酸锌和草酸亚铁;如此,有助于实现铁酸锌的资
源化处理。
8.研究发现,所述的草酸和还原剂的一锅同步(起始同步)以及条件的联合控制是协同实现铁酸锌一锅温和转型的关键。
9.本发明中,为了实现草酸和还原剂的协同,改善一锅转型效果,可以向铁酸锌及其浑浊液(浆液)中添加溶解有草酸和还原剂的混合溶液,或者将铁酸锌及其溶液(浆液)添加在溶解有草酸和还原剂的底液中,混合获得所述的浆料。如此有助于更利于实现铁酸锌和草酸、还原剂的一锅同步协同处理。
10.本发明中,所述的矿浆的溶剂为水。
11.优选地,所述的浆料中,溶剂的用量没有特别要求,例如,溶剂和铁酸锌的质量比为30:1~50:1。
12.作为优选,所述的还原剂为水溶性还原化合物,优选为抗环血酸及其水溶性盐。所述的还原剂可以以固体或者水溶液形式使用。
13.本发明中,在所述的草酸和还原剂一锅协同下,进一步配合成分比例的控制,有助于进一步改善协同,改善铁酸锌的温和转型效果。
14.作为优选,草酸与铁酸锌(以干重计)的质量比大于或等于0.7;优选为0.7~1.5:1,更进一步优选为1~1.5:1。
15.作为优选,所述的还原剂与铁酸锌(以干重计)的质量比大于或等于0.25;优选为0.25~2:1;更进一步优选为1~1.5:1。
16.本发明中,一锅反应在敞口条件下反应;
17.优选地,一锅反应在搅拌下进行,优选的搅拌转速为100~300r/min。
18.本发明中,得益于所述的草酸和还原剂以及比例的协同,可以在温和的条件下实现铁酸锌的转型。所述的处理温度没有特别要求,出于操作简便性考量,一锅反应的温度例如可以大于或等于10℃,进一步优选为40~60℃。
19.本发明中,一锅反应的时间可根据转化情况进行调整,例如,一锅反应的时间大于或等于1h;进一步优选为1~2h。
20.本发明中,一锅反应后,进行固液分离,随后再经过水洗、醇洗、干燥处理,即可获得草酸锌和草酸亚铁的转型产物。
21.本发明中,对转型产物在保护性气氛下进行焙烧处理,获得fe3o4和zno;
22.优选地,所述的保护性气氛为氮气、惰性气体中的至少一种;
23.优选地,所述的焙烧的温度为400-600℃,进一步优选为400~500℃。
24.本发明研究发现,将转型的产物在保护性气氛以及所述的温度下,能够意外地成功实现转型得到的复合草酸盐的协同转型,有利于可控地获得fe3o4和zno物相产物。
25.优选地,对焙烧的产物进行磁选分离,获得fe3o4和zno。
26.本发明中,所述的铁酸锌的来源于纯物质、矿物、渣中的至少一种。
27.本发明一种优选的铁酸锌处理方法,将铁酸锌和草酸、还原剂用水浆化,获得浆料;将浆料进行一锅转型处理,随后分离获得包含草酸锌和草酸亚铁的转型产物。优选再将该转型产物在保护气氛、400~600℃下焙烧处理,获得包含四氧化三铁、氧化锌的焙烧产物。
28.本发明以铁酸锌为原料制备四氧化三铁和氧化锌,制备过程简单,生产的产品纯
度大,既能充分地利用铁酸锌,又能实现氧化锌和四氧化三铁的低成本工业化生产。
29.本发明一种更优选的方法,包括以下步骤:
30.(1):将铁酸锌物料加入水中,溶剂与铁酸锌的质量比为30:1~50:1;搅拌5~10min;
31.(2):向铁酸锌-溶剂体系同步加入还原剂和浸出剂,还原剂(抗坏血酸)、浸出剂与铁酸锌的质量比为0.25~1.5:0.7~1.5:1;将上述混合后得到的体系混合搅拌均匀后,40~60℃的温度下反应1~2h即可得到反应产物;所述的反应条件均为常压空气气氛。
32.(3):将步骤(2)反应后获得的产物采用蒸馏水或者无水乙醇洗涤3~5次,将洗涤后的产物采用冷冻真空干燥或者采用真空烘箱干燥的方法获得干燥后产物即草酸锌和草酸亚铁的混合物;
33.(4):将步骤(3)获得的草酸锌和草酸亚铁的混合物在惰性气氛(如氮气或者氩气)下进行热解反应(热解升温至400-600℃),即可获得四氧化三铁和氧化锌,通过磁选即可将四氧化三铁和氧化锌分离。
34.本发明所述的方法,还可以延伸至其他类似物料的制备应用中。例如,可采用含有铁酸锌的其他沉铁渣物料替换所述的铁酸锌。
35.与现有技术相比,本发明的特点和有益效果是:
36.为解决铁酸锌难以可控高效资源化分离利用的问题,本发明通过草酸和还原剂一锅同步协同,进一步配合反应温度以及物料比例的联合控制,能够意外地使铁酸锌温和转型成草酸盐混合物;进一步将转型产物在惰性气氛、低温热解下可使转型的产物定向转化为磁性fe3o4和zno,最后可通过磁选分离方式分别获得fe3o4和zno。通过上述手段的联合,本发明可以实现铁酸锌的温和转化与资源化可控高效分离。
37.本发明整个反应条件温和,操作简单,实现了铁酸锌的可控资源化高效处理和增值利用,同时也为湿法炼锌过程中沉铁渣问题的根本解决提供了方法和技术借鉴,该发明工业化应用前景广泛。
附图说明
38.图1和图2分别是铁酸锌的xrd与sem图;
39.图3和图4分别是实施例1制得的产物的xrd与sem图;
40.图5为实施例1所得产物的惰性热解产物的xrd图;
41.图6为实施例2(重量比为7:10)a组案例的xrd和sem图;
42.图7为实施例2(重量比为1.5:1)b组案例的xrd和sem图;
43.图8和9分别为实施例3所得的sem和xrd图;
44.图10和11分别为实施例4所得(60℃条件下)产物的sem图和xrd图;
45.图12为对比例1所得产物的xrd图;
46.图13和14分别是对比例1(抗坏血酸添加量为0.1g时)所得产物的sem图与热重产物的xrd图;
47.图15和16分别是对比例2得到产物的sem与xrd图;
48.图17是对比例3得到产物的xrd图;
49.图18是对比例4得到产物的xrd图;
50.图19和20分别是对比例5所得产物的sem和xrd图;
51.图21是对比例6空气氛围下热解所得产物的xrd图;
52.图22是对比例7热解所得产物的xrd图;
53.图23是对比例8热解所得产物的xrd图;
具体实施方式
54.下面结合实施例对本发明作进一步详细说明。
55.本发明实施例中的铁酸锌主要为试剂级别和铁矾渣一次浸出所获得的铁酸锌。
56.实施例1
57.本实施例采用的为试剂级铁酸锌(分析纯,xrd见图1,sem见图2)通过草酸和抗坏血酸协同使得铁酸锌还原溶解重结晶得到草酸锌和草酸亚铁,再通过惰性气氛热解获得氧化锌和四氧化三铁,最后可通过磁选方式实现铁锌分离,具体操作程序按照以下步骤进行:
58.(1)取铁酸锌2.75g加入到溶剂水当中搅拌均匀得到浆料,溶剂水与铁酸锌的质量比为30:1;
59.(2)在步骤(1)的浆料中同步加入浸出剂草酸与还原剂抗坏血酸(添加草酸和抗坏血酸的混合溶液);浸出剂、还原剂与铁酸锌的质量比为1:1:1,混合均匀,得到前驱物体系;
60.(3)前驱物体系在40℃下搅拌(搅拌转速为250r/min)反应,反应过程在敞口容器中进行,反应时间为2h,反应后采用蒸馏水或者无水乙醇洗涤,倒掉上清液,重复3次,获得反应产物,反应产物的xrd和sem图谱见附图3和附图4,由附图3和4可知:铁酸锌溶解重结晶产物的xrd图谱可知,铁酸锌物相的xrd衍射峰消失,原铁酸锌的形貌和物相结构发生了明显转变。
61.(4)在惰性气氛下(氩气氛围),将步骤(3)获得的粉体产物升温至600℃,并保温2h,获得热解产物。热解产物的xrd图谱见附图5。研究发现,通过惰性气氛热解,铁酸锌溶解重结晶产物可转化为四氧化三铁和氧化锌,从而实现了铁酸锌中铁锌的分离和资源化,该发明方案具有优异的产业应用价值。
62.实施例2
63.和实施例1相比,区别仅在于,改变草酸的比例,其中,草酸和铁酸锌的重量比例分别为(a)7:10;(b)1.5:1;其他条件同实施例1。
64.通过测定发现,处理后的产物均具有和实施例1相似结构形貌的产物。其sem图和xrd图分别见图6和7(图6为a组案例;图7为b组案例)。
65.实施例3
66.和实施例1相比,区别仅在于,改变抗坏血酸的比例,其中,抗坏血酸和铁酸锌的重量比例分别为:(a)1:4;(b)1.5:1;其他条件同实施例1;
67.通过测定发现,处理后的产物均具有和实施例1相似结构形貌的产物。例如,实施例所得产物的xrd和sem图分别见附图8和9,由图可知,相较于铁酸锌物料,原铁酸锌物相消失,反应后产物的形貌和结构均发生了明显变化。
68.实施例4
69.和实施例1相比,区别仅在于,改变步骤(3)的反应温度(一锅反应温度),分别为15℃、50℃、60℃,;其他条件同实施例1。
70.通过测定发现,处理后的产物均具有和实施例1相似形貌的产物。例如,60℃产物的sem和xrd图分别见附图10和11(15℃反应产物见右图),相较于原始铁酸锌物料,原铁酸锌物相消失,其形貌和结构均发生了明显的变化。
71.对比例1
72.和实施例1相比,区别仅在于,降低抗坏血酸的含量,也即是,将抗坏血酸的添加量分别为0.1、0.3和0.5g;其他条件同实施例1。
73.与所加抗坏血酸为0.7g的结果对比,该案例的xrd图如图12所示,抗坏血酸添加量为0.1g时产物的sem图如图13所示。结果表明当抗坏血酸添加量较少时,反应的主要产物为铁酸锌和草酸锌,说明还原剂添加量较少,难以促进铁酸锌自身结构转化,同时热重产物的xrd(附图14)结果表明,其惰性气氛下热解产物为氧化锌和铁酸锌。可见,未控制在本发明要求的范围内,铁酸锌无法转化和热解分离得到四氧化三铁和氧化锌。
74.对比例2
75.和实施例1相比,区别仅在于,降低草酸的的含量,也即是,将草酸和铁酸锌的比例控制在1:5;其他条件同实施例1。
76.该案例的sem图与xrd分别如图15和16所示,分析结果表明,由于草酸量较少,其未与抗坏血酸产生协同促进铁酸锌溶解重结晶的作用,xrd图谱结果表明,铁酸锌转化产物为znfe2o4和zn(c2o4)2h2o。可见,未控制在本发明要求的范围内,铁酸锌转化产物无法通过惰性气氛热解得到四氧化三铁和氧化锌。
77.对比例3
78.和实施例1相比,区别仅在于,步骤(2)中,仅添加抗坏血酸,添加量分别为0.5、1.0、1.5和2.5g,不添加草酸。
79.与铁酸锌的xrd图谱相比,该案例所获产物的xrd见图17,其主要物相仍为znfe2o4,因此可知,在抗坏血酸单独存在条件下,铁酸锌结构难以被破坏。
80.对比例4
81.和实施例1相比,区别仅在于,步骤(2)中,仅添加草酸,添加量分别为0.5、1.0、1.5和2.5g,不添加抗坏血酸。
82.与铁酸锌的xrd图谱相比,该案例所获产物的xrd见图18,其主要物相为znfe2o4和zn(c2o4)2h2o,由此可知,在草酸单独存在条件下,只能使得铁酸锌实现部分转化。
83.对比例5
84.和实施例1相比,区别仅在于,步骤(3)中,一锅反应时间缩短至0.5h。与实施例1一锅反应产物的sem和xrd图相比,该案例所获产物的sem图和xrd图谱分别见附图19和20,其主要物相为znfe2o4、zn(c2o4)2h2o。
85.对比例6
86.和实施例1相比,区别仅在于,步骤(4)中,热解的气氛为空气。对热解产物xrd图谱(附图21)分析结果发现,其物相组成主要为铁酸锌和氧化锌。
87.对比例7
88.和实施例1相比,区别主要在于,将含铁酸锌的渣样品(包含草酸亚铁、草酸锌、草酸铅的混合物相)在ar气氛、800℃下热解2h。结果发现(附图22),草酸亚铁转化为氧化亚铁,未得到四氧化三铁物相产物。
89.对比例8
90.和实施例1相比,区别主要在于,将含铁酸锌的渣样品(包含草酸亚铁、草酸锌、草酸铅的混合物相)在ar气氛、300℃下热解2h。结果发现(附图23),草酸盐混合物只是失去了结晶水,并没有向四氧化三铁以及氧化锌转化。故在此温度条件下热解无法使得其分离转化。