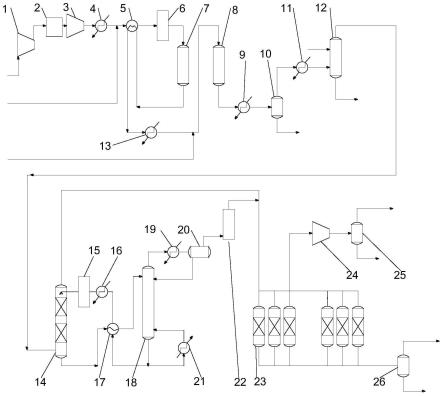
1.本发明涉及高炉煤气处理领域,具体为高炉煤气制氢用脱毒装置及高炉煤气制氢的生产工艺。
背景技术:2.我国钢铁行业主要以铁矿石和焦炭(或煤炭通过焦化后制备为焦炭使用)为原料,提炼出钢铁产品,因此钢铁行业排放的二氧化碳的碳源主要来自焦炭。钢铁行业中,焦炭主要使用在高炉或转炉工序,焦炭在使用过程中与氧气(或空气)反应被转化为高炉煤气与转炉煤气。
3.高炉煤气主要成分为co、co2、n2、h2、ch4等,其中可燃成分co含量约占15-30%,h2、ch4的含量很少,co2、n2的含量分别占15-30%、30-60%,热值仅为3500kj/m3左右。高炉煤气中的co2、n2既不参与燃烧产生热量,也不能助燃,相反,还吸收大量的燃烧过程中产生的热量,导致高炉煤气的理论燃烧温度偏低。高炉煤气的着火点并不高,似乎不存在着火的障碍,但在实际燃烧过程中,受各种因素的影响,混合气体的温度必须远大于着火点,才能确保燃烧的稳定性。高炉煤气的理论燃烧温度低,参与燃烧的高炉煤气的量很大,导致混合气体的升温速度很慢,温度不高,燃烧稳定性不好。
4.中国专利202210714585.8公开了高炉煤气制氢的生产工艺,本发明以高炉煤气为原料,经过变换、co2碳回收和变压吸附提氢等工序产出蓝色氢气和二氧化碳产品,同时副产出低硫燃料气共给全厂燃料气管网,满足全厂燃料气使用。进一步的,根据高炉煤气产氢的原理,合成出了一种贵金属负载的wmoox催化剂,其不仅能够较快速的催化高炉煤气中较低浓度的一氧化碳和水反应,还具有较长的寿命和制造成本;实现了高炉煤气燃烧前碳捕集和蓝色氢气联产,提升了高炉煤气的附加值。
5.因此,对高炉煤气进行进一步的净化及开发更高热值的产品是提高高炉煤气利用率的有效手段。由于高炉煤气中co+co2的含量约45%,可用作氢气的还原。若是能够有效利用高炉煤气制取高纯度高产量的氢气,将会大大提高高炉煤气的附加值。
6.但是,常用的氢气还原的脱毒装置中使用的脱毒剂需要定期人工更换,而脱毒后产物也无法进一步回收,脱毒效果差。
技术实现要素:7.针对现有技术存在的缺陷,本发明提供了一种高炉煤气制氢用脱毒装置及高炉煤气制氢的生产工艺以解决上述问题。
8.一种高炉煤气制氢用脱毒装置,包括脱毒腔,还包括传动腔,清洗腔和转动辊,所述脱毒腔后侧依次连接有所述传动腔和所述清洗腔,所述脱毒腔内设置有脱硫机构,所述脱硫机构用于延长高炉煤气在所述脱毒腔内经过的途径并对高炉煤气进行脱硫,所述传动腔内设置有多个所述转动辊,所述转动辊外侧包覆有脱硫剂,所述转动辊的两端分别伸入所述脱毒腔和所述清洗腔,所述传动腔用于切换所述转动辊的两端分别与所述脱毒腔和所
述清洗腔的对应位置。
9.进一步地,所述脱硫机构包括:折流板,转动槽,出气孔和进气孔,所述脱毒腔内部沿竖直方向设置有多个均匀分布的所述折流板,所述脱毒腔的侧壁与顶部的所述折流板之间设置有所述进气孔,所述脱毒腔相对折流板的侧壁底部与底部的所述折流板之间设置有所述出气孔,所述脱毒腔的顶壁与顶部的所述折流板之间、任意两个相邻的所述折流板之间和所述脱毒腔的底壁与底部的所述折流板之间均设置有所述转动槽,所述转动辊对应所述转动槽设置,且所述转动辊通过所述转动槽伸入所述脱毒腔内部,高炉煤气自进气孔进入所述脱毒腔内部,通过所述折流板依次经过多个所述转动辊,然后从所述出气孔排出。
10.进一步地,所述脱硫剂为氧化铁、氧化铝、碳酸钠、偏钒酸钠、栲胶、水中的一种或几种混合物。
11.进一步地,所述清洗腔内设置有进液孔,出液孔和清理槽,所述清洗腔顶部和底部分别设置有所述进液孔和所述出液孔,所述清洗腔内对应所述转动槽设置有多个所述清理槽,所述转动辊通过所述清理槽伸入所述清洗腔内部,所述清洗腔内设置有清理剂,所述清理剂设置为碱性溶液。
12.进一步地,所述转动辊外侧还设有密封组件,所述密封组件包括第一抵板和第二抵板,所述转动辊外侧中心对称连接有所述第一抵板和所述第二抵板,所述第二抵板与所述脱毒腔的内壁活动相抵,所述第一抵板与所述清洗腔的内壁活动相抵。
13.进一步地,所述传动腔内还设置有转动轴,所述转动轴的两端与所述传动腔的侧壁转动连接,所述转动轴外侧固定连接有所述转动辊,所述转动轴的两端伸出所述传动腔并连接有动力机构。
14.进一步地,所述动力机构包括传动齿轮,滑动座,传动齿,
15.所述转动轴伸出所述传动腔的两端均固定连接有所述传动齿轮,所述传动腔的两外侧壁对应所述传动齿轮均设置有所述滑动座,所述滑动座靠近对应所述传动齿轮的一侧设置有所述传动齿,所述传动齿通过齿轮啮合方式配合所述传动齿轮;两侧所述传动齿轮与所述清洗腔的两外侧壁之间还设有所述限位组件,两侧所述传动齿轮顶部与所述传动腔的外顶壁之间还设有所述同步组件。
16.进一步地,所述同步组件包括转动销,压板和u形座,两端所述滑动座顶部共同固定连接有所述u形座,所述u形座的底部与所述传动腔的顶部活动相抵,所述脱毒腔顶部转动连接有所述转动销,所述转动销外侧固定连接有所述压板,所述压板的末端与所述u形座的顶部活动相抵。
17.进一步地,所述限位组件包括限位槽,限位键和拉伸弹簧,所述清洗腔的两外侧壁均开设有所述限位槽,所述限位槽内滑动设置有所述限位键,两侧所述限位键均与对应所述滑动座固定连接,所述限位键的底部与所述限位槽底壁之间设置有所述拉伸弹簧,所述拉伸弹簧保持所述限位键有远离所述限位槽底部的趋势。
18.一种高炉煤气制氢的生产工艺,其特征在于,包括以下步骤:
19.(1)将高炉煤气原料气经压缩机压缩,再水洗/碱洗,得到预处理高炉煤气;
20.(2)将预处理高炉煤气再次压缩,再经过脱毒处理,得到净化后高炉煤气;
21.(3)将净化后的高炉煤气和水蒸汽混合,送入绝热变换炉,将部分co和水蒸气进行变化反应生产co和h,反应结束后进行热回收处理,再经过冷却器和分液器分液,去除大部
分水蒸气;
22.(4)将分液和洗涤处理后的高炉煤气通入吸收塔,并用二氧化碳吸收剂分离co,经冷却器和分液器处理,得到相对干燥的二氧化碳气体,最后通入脱毒装置进行脱硫处理后,捕集co;
23.(5)将剩下的气体导入变压吸附装置,提取出部分氢气并增压,作为高纯氢气储存在高纯氢气收集罐,将余下的气体作为无硫燃料气输出。
24.本发明的有益效果是:
25.1、设置在脱硫机构内部的折流板,高炉煤气在脱毒腔内经过路径较长,增加高炉煤气与脱毒剂的接触时间;然后通过转动辊表面的曲面设计,使得高炉煤气与脱毒剂的接触面积更大,使得高炉煤气脱硫效果更好。
26.2、通过转动辊的转动实现对于吸附在脱毒剂外侧的硫化物的清洗;转动辊的两侧始终保持一侧处于清洗腔内部,一侧处于脱毒腔内部,使得脱毒装置通入高炉煤气时,脱毒腔内进行脱硫处理,清洗腔内进行硫化物的清洗;通过转动转动辊即可实现转动辊的两侧切换;使得脱毒剂可以一直使用,无需人工更换,使用更加方便,同时更加节约资源。
27.3、通过设置密封组件,使得第一抵板与所述清洗腔的内壁活动相抵,所述第二抵板与所述脱毒腔的内壁活动相抵;此时通过第一抵板和第二抵板分隔脱毒腔和清洗腔,实现脱毒腔内的密封,使得高炉煤气脱硫效果好。
附图说明
28.图1:高炉煤气碳捕集联产氢气的工艺流程
29.图2是本发明脱毒装置的整体结构示意图;
30.图3是本发明的脱毒腔内部结构示意图;
31.图4是本发明的剖面结构示意图;
32.图5是本发明的清洗腔内部结构示意图;
33.图6是本发明的侧视结构示意图;
34.图7是本发明的传动腔内部结构示意图;
35.图8是本发明动力机构和密封组件的结构示意图;
36.图9是本发明图5中a处放大结构示意图;
37.图10是本发明密封组件与转动辊的位置示意图;
38.图中:1、第一原料压缩机;2、洗涤装置;3、第二原料压缩机;4、11、16、19、冷却器;5、预热器;6、15、脱毒装置;7、第一绝热变换炉;8、第二绝热变化炉;9、13、热回收装置;10、12、20、分液和洗涤装置;14、吸收塔;17、换热器;18、再生塔;21、再沸器;22
‑‑‑
脱硫装置;23、吸附罐;25、氢气收集罐;26、燃料气收集罐;31、脱毒腔;32、传动腔;33、清洗腔;41、折流板;42、转动槽;43、出气孔;44、进气孔;51、转动轴;52、转动辊;61、进液孔;62、出液孔;63、清理槽;71、转动销;72、压板;73、u形座;81、传动齿轮;82、滑动座;83、传动齿;91、限位槽;92、限位键;93、拉伸弹簧;94、第一抵板;95、第二抵板。
具体实施方式
39.实施例1
40.一种高炉煤气制氢的生产工艺,包括以下步骤:
41.(1)将高炉煤气原料气经第一原料压缩机1进行压缩,并压缩至1.03mpa压力,然后再导入水洗装置2进行洗涤,得到预处理高炉煤气;
42.(2)将预处理高炉煤气经第二原料压缩机3进行压缩并压缩至2.3mpa压力,再经过吸附脱毒罐6中进行脱毒处理,除去装置中的粉尘、氯离子、硫化物,得到净化后高炉煤气;
43.(3)将净化后的高炉煤气和水蒸汽混合,送入第一级绝热变换炉7,将部分co和水蒸气进行变化反应生产co2和h2,然后经过热回收装置13进行热回收处理,再导入第二级绝热变换炉8,将剩余的co与水蒸气变化反应生产co2和h2,反应结束后通入热回收装置9进行热回收处理,再经过分液器10进行一次分液,最后经过冷却器11和分液器12分液,去除大部分水蒸气;
44.(4)将分液和洗涤处理后的高炉煤气通入吸收塔14并补充二氧化碳吸收剂进行co2的分离和有机硫脱除,将经过吸收塔吸收二氧化碳后的溶液经过贫富溶剂换热器17进入再生塔18中进行解吸处理,得到二氧化碳,然后将经再生塔18处理后的二氧化碳吸收溶液经贫富溶剂换热器17或者再沸器21进一步升温,再次导入再生塔18释放出剩余二氧化碳和含硫化合物,将湿润的二氧化碳气体经冷却器19和分液器20处理,得到相对干燥的二氧化碳气体,最后通入脱毒装置22进行脱硫处理后,捕集co2;
45.(5)将剩下的气体导入变压吸附装置23,提取出部分氢气,通过压缩机24增压,然后将氢气储存于氢气收集罐25中,其中多个串联吸附罐中均装填有吸附剂;其中,两个或三个变压吸附塔组成一个变压吸附装置,高纯氢气增压后输出,其中回收了20-70%的h2;将余下的气体作为无硫燃料气进入收集罐26后对外输出。
46.步骤(1)中所述高炉煤气原料气的组成为:21%的co2、25%的co、3%的h2、50.39%的n2、0.002%的水蒸气、0.5%的o2、0.002%的h2s、0.006%的cos。
47.步骤(1)中所述水洗装置中装填有洗涤剂,所述洗涤剂为水。
48.步骤(2)中所述脱毒装置中含有脱硫剂/脱氯剂,所述脱硫剂/脱氯剂,按质量份剂,由以下组分组成:6份碳酸钠、1份偏钒酸钠、1.8份栲胶、991.2份水。
49.步骤(3)中所述高炉煤气与水蒸气的体积比为1:1.2,体积空速为7000m3/(m3·
h)。
50.步骤(3)中所述第一级绝热变换反应炉、第二级绝热变换反应炉中装填有催化剂,第一级绝热变换炉的反应条件:入口温度为300℃、压力为2.3mpa;第二级绝热变换炉的反应条件:反应温度为280℃、压力为2.2mpa。
51.步骤(4)中所述二氧化碳吸收剂为氢氧化钠水溶液。
52.步骤(5)所述吸附剂为活性炭。
53.所述催化剂的制备方法,包括以下步骤:
54.s1按质量份计,在室温下,将8份钨酸盐和1.5份六羰基钼添加到300份4.8m硝酸水溶液中,搅拌36h后,向其中加入0.1份贵金属阳离子盐,继续反应12h,以8000r/min转速离心分离出沉淀,用水洗涤3次,在60℃下干燥得到淡黄色固体粉末;
55.s2将步骤s1中得到的淡黄色固体粉末在真空环境下于300℃范围内加热处理10小时,降至室温,得到贵金属负载的wmoo
x
催化剂;
56.s3将贵金属负载的wmoo
x
催化剂和聚乙二醇按质量比1:10混合,用湿球磨法制成乳状浆液,并将上述乳状浆液喷涂到堇青石蜂窝陶瓷载体上,形成贵金属负载的wmoo
x
催化
剂过渡层;
57.s4对步骤s3喷涂乳状浆液后的堇青石蜂窝陶瓷载体进行室温通道吹扫、干燥,于600℃焙烧3小时,得到所述催化剂。
58.所述钨酸盐为钨酸钠。
59.所述贵金属阳离子盐为硝酸铂。
60.所述贵金属负载的wmoo
x
催化剂过渡层重量占蜂窝陶瓷载体总重量的40%。
61.实施例2
62.在实施例1的基础上,我们进一步改进了脱毒装置22,
63.一种高炉煤气制氢用脱毒装置,包括脱毒腔31,还包括传动腔32,清洗腔33和转动辊52,所述脱毒腔31后侧依次连接有所述传动腔32和所述清洗腔33,所述脱毒腔31内设置有脱硫机构,所述脱硫机构用于延长高炉煤气在所述脱毒腔31内经过的途径并对高炉煤气进行脱硫,
64.本实施例中,所述脱硫剂为氧化铁、氧化铝、碳酸钠、偏钒酸钠、栲胶、水中的一种或几种混合物。
65.本实施例中,所述脱硫机构包括:折流板41,转动槽42,出气孔43和进气孔44,所述脱毒腔31内部沿竖直方向设置有多个均匀分布的所述折流板41,所述脱毒腔31的侧壁与顶部的所述折流板41之间设置有所述进气孔44,所述脱毒腔31相对折流板41的侧壁底部与底部的所述折流板41之间设置有所述出气孔43,所述脱毒腔31的顶壁与顶部的所述折流板41之间、任意两个相邻的所述折流板41之间和所述脱毒腔31的底壁与底部的所述折流板41之间均设置有所述转动槽42。
66.通过设置在脱硫机构内部的折流板41,使得高炉煤气自进气孔44进入所述脱毒腔31内部,通过依次经过多个所述折流板41,然后从所述出气孔43排出,使得高炉煤气在脱毒腔31内经过路径较长,增加高炉煤气与脱毒剂的接触时间,使得脱毒效果好。
67.进一步地,我们希望进一步改变脱毒剂在脱毒腔31内的位置和分布,进一步增加高炉煤气与脱毒剂的接触面积。
68.所述传动腔32内设置有多个所述转动辊52,所述转动辊52外侧包覆有脱硫剂,所述转动辊52的两端分别伸入所述脱毒腔31和所述清洗腔33,所述传动腔32用于切换所述转动辊52的两端分别与所述脱毒腔31和所述清洗腔33的对应位置,
69.所述转动辊52对应所述转动槽42设置,且所述转动辊52通过所述转动槽42伸入所述脱毒腔31内部。
70.通过设置圆形的转动辊52,使得脱毒腔31内高炉煤气与半圆形的转动辊52接触,转动辊52表面的曲面设计,使得高炉煤气与脱毒剂的接触面积更大,使得脱毒效果更好。
71.综上,实施例2中,我们通过设置在脱硫机构内部的折流板41,高炉煤气在脱毒腔31内经过路径较长,增加高炉煤气与脱毒剂的接触时间;然后通过转动辊52表面的曲面设计,使得高炉煤气与脱毒剂的接触面积更大,使得高炉煤气脱硫效果更好。
72.实施例3
73.实施例1和2中,高炉煤气和脱毒剂反应后,硫化物吸附在脱毒剂外侧,者会影响脱毒剂进一步使用,因此在实施例2的基础上,我们设置了清理腔33;
74.所述清洗腔33内设置有进液孔61,出液孔62和清理槽63,所述清洗腔33顶部和底
部分别设置有所述进液孔61和所述出液孔62,所述清洗腔33内对应所述转动槽42设置有多个所述清理槽63,所述转动辊52通过所述清理槽63伸入所述清洗腔33内部,所述清洗腔33内设置有清理剂,所述清理剂设置为碱性溶液。
75.优选地,碱性溶液最优选设为氢氧化钙溶液,与硫化物反应生成硫化钙沉淀于清理腔33内部,且本反应中不产生其他有害反应物,而硫化钙工业需求极高,达到节能环保资源再利用的效果。
76.本实施例中,通过转动辊52的转动实现对于吸附在脱毒剂外侧的硫化物的清洗;转动辊52的两侧始终保持一侧处于清洗腔33内部,一侧处于脱毒腔31内部,使得脱毒装置22通入高炉煤气时,脱毒腔31内进行脱硫处理,清洗腔33内进行硫化物的清洗;通过转动转动辊52即可实现转动辊52的两侧切换;使得脱毒剂可以一直使用,无需人工更换,使用更加方便,同时更加节约资源。
77.进一步地,所述转动辊52外侧还设有密封组件,所述密封组件包括第一抵板94和第二抵板95,所述转动辊52外侧中心对称连接有所述第一抵板94和所述第二抵板95,所述第二抵板95与所述脱毒腔31的内壁活动相抵,所述第一抵板94与所述清洗腔33的内壁活动相抵。
78.自然状态下,第一抵板94与所述清洗腔33的内壁活动相抵,所述第二抵板95与所述脱毒腔31的内壁活动相抵;此时通过第一抵板94和第二抵板95分隔脱毒腔31和清洗腔33,实现脱毒腔31内的密封,使得高炉煤气脱硫效果好。
79.实施例4
80.在实施3的基础上,设置动力机构,使得实现转动辊52的状态切换。
81.所述传动腔32内还设置有转动轴51,所述转动轴51的两端与所述传动腔32的侧壁转动连接,所述转动轴51外侧固定连接有所述转动辊52,所述转动轴51的两端伸出所述传动腔32并连接有动力机构;所述动力机构包括传动齿轮81,滑动座82,传动齿83,所述转动轴51伸出所述传动腔32的两端均固定连接有所述传动齿轮81,所述传动腔32的两外侧壁对应所述传动齿轮81均设置有所述滑动座82,所述滑动座82靠近对应所述传动齿轮81的一侧设置有所述传动齿83,所述传动齿83通过齿轮啮合方式配合所述传动齿轮81;两侧所述传动齿轮81与所述清洗腔33的两外侧壁之间还设有所述限位组件,两侧所述传动齿轮81顶部与所述传动腔32的外顶壁之间还设有所述同步组件。
82.本实施例中,通过滑动座82上的传动齿83与多个传动齿轮81的齿轮啮合,可以实现多个转动辊52的同步运动,通过齿轮啮合对于转动辊52进行限位,锁紧效果好。
83.进一步地,所述同步组件包括转动销71,压板72和u形座73,两端所述滑动座82顶部共同固定连接有所述u形座73,所述u形座73的底部与所述传动腔32的顶部活动相抵,所述脱毒腔31顶部转动连接有所述转动销71,所述转动销71外侧固定连接有所述压板72,所述压板72的末端与所述u形座73的顶部活动相抵。
84.所述限位组件包括限位槽91,限位键92和拉伸弹簧93,所述清洗腔33的两外侧壁均开设有所述限位槽91,所述限位槽91内滑动设置有所述限位键92,两侧所述限位键92均与对应所述滑动座82固定连接,所述限位键92的底部与所述限位槽91底壁之间设置有所述拉伸弹簧93,所述拉伸弹簧93保持所述限位键92有远离所述限位槽91底部的趋势。
85.优选地,初始状态时,所述u形座73的底部与所述传动腔32的顶部相抵,所述压板
72的末端与所述u形座73的顶部相抵,所述拉伸弹簧93保持所述限位键92有远离所述限位槽91底部的趋势,此时,通过压板72和u形座73的相对位置设置,使得所述第二抵板95位于最顶部,且与所述脱毒腔31的内壁相抵,所述第一抵板94位于最底部,且与所述清洗腔33的内壁相抵,通过同步组件实现脱毒腔31内的密封。
86.本实施例中,通过u形座73实现两侧滑动座82同步运动,更加稳定,当需要转动转动辊52时,可以通过人工转动压板72,使得压板72不再压住u形座73,然后在拉伸弹簧93作用下,使得两端所述滑动座82带动u形座73向上,进而通过传动齿83与多个传动齿轮81的齿轮啮合,可以实现多个转动辊52的同步转动,实现对于转动辊52的清洗。
87.可优选的,本装置可以通过人工下压u形座73至与所述传动腔32的顶部相抵,然后转动压板72进行复位,操作简单。