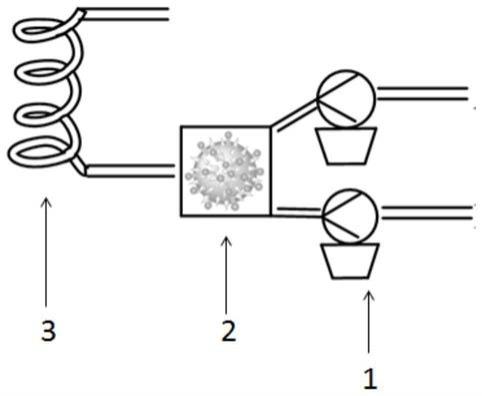
1.本发明具体涉及一种有机硅助剂的制备方法。
背景技术:2.有机硅材料已经成为航空、高新技术、国防军工和国民经济领域内不可缺少的关键材料,并被列为国家重点鼓励发展产业之一。目前,有机硅下游高附加值产品的开发是有机硅行业发展的重点之一。高分子有机硅消泡剂、流平剂及分散剂是有机硅高附加值产品的典型代表,目前该系列的有机硅助剂的生产均采用间歇釜进行生产,反应时间约为2~5小时,另外考虑到加料、滴定及洗釜的时间,整个生产过程可能长达6~8小时。于一家生产各种有机硅助剂的厂家来说,每个产品的产量不大,如果生产每一个产品都使用一个专用的釜会造成巨大的资源浪费,而如果使用同一釜生产不同有机硅助剂,那么在洗釜过程中也会造成巨大溶剂浪费和污染。此外,传统的釜式反应器换热面积小,在高温下反应会存在较大的安全隐患。间歇釜生产过程中物料的跑冒滴漏及人员操作的误差,也会对产品质量的稳定和人体健康造成不利影响。最后由于反应釜传热传质条件较为复杂,造成了不能很好地控制产品质量的问题,很多在小试情况下容易实现良好性能的产品在工业化过程中难以实现或性能较差。
技术实现要素:3.本发明的目的是提供一种反应时间短、转化效率高的有机硅助剂的制备方法。
4.为了达到上述目的,本发明采用如下技术方案:
5.本发明提供一种有机硅助剂的制备方法,将含氢硅油与催化剂的混合物,以及含双键的脂肪烃、醚、醇中的一种或多种分别通入管式连续流反应器中进行硅氢加成反应制得所述的有机硅助剂,其中,所述催化剂为过渡金属的盐,控制所述的管式连续流反应器中的温度为50~300℃,物料在所述的管式连续流反应器中的停留时间为1~600s。
6.本发明通过使用管式连续流反应器制备有机硅助剂,可以解决传统制备方法中存在的步骤繁琐、效率低、成本高、污染大和危险性大等问题。
7.优选地,所述的含氢硅油的活性氢和所述的含双键的脂肪烃、醚、醇中的一种或多种的双键的投料摩尔比为1:1~1:2,进一步优选为1:1~1:1.2。
8.本发明中,所述的含氢硅油可以是低含氢硅油,也可以是高含氢硅油。
9.优选地,所述的含氢硅油的重均分子量为100~500000,活性氢含量为0.01~1.7wt%。
10.进一步优选地,所述含氢硅油的重均分子量为100~5000,活性氢含量为0.01~0.5wt%。
11.根据一些实施方式,所述的催化剂为pt、rh、ir、ru、fe等过渡金属的盐,其中pt系催化剂活性较高。优选地,所述的催化剂包括但不限于氯铂酸水合物、卡斯特铂金催化剂中的一种或多种,该类催化剂的催化效率较高,使用前需与醇或醚或酮或异丙醇形成络合物。
12.优选地,所述催化剂的质量为所述含氢硅油与催化剂的混合物总质量的0.01~25%。
13.进一步优选地,所述催化剂的质量为所述含氢硅油与催化剂的混合物总质量的0.01~0.5%。
14.优选地,所述的含双键的脂肪烃为r
‑
r’,其中,r为含有一个或多个双键的烃类,进一步优选为烯丙基或乙烯基;r’为碳原子数为5~15的烷基,所述的r’为直链烷基或含有支链的烷基。
15.根据一些实施方式,所述的含双键的脂肪烃为1
‑
辛烯、1
‑
十二碳烯、1
‑
十八碳烯中的一种或多种。
16.优选地,所述的含双键的醚为r
‑
(r’)
n
‑
or”,其中,r为含有一个或多个双键的烃类,进一步优选为烯丙基或乙烯基;r’为含氧或不含氧亚烷基,进一步优选为不含氧亚烷基、乙氧亚基、丙氧亚基中的一种或多种;n为自然数;r”为氢、烷基或亚烷基醇,进一步优选为乙基、丙基、丁基、异丙基、亚戊基醇、亚己基醇中的一种。
17.根据一些实施方式,所述的含双键的醚为烯丙基单乙二醇醚、烯丙基聚乙二醇400单甲醚、烯丙基聚丙二醇500单甲醚中一种或多种。
18.优选地,所述的含双键的醇为r
‑
r’,其中,r为含有一个或多个双键的烃类;r’为碳原子数为1~10的亚烷基醇,所述的r’为直链亚烷基醇或含有支链的亚烷基醇。
19.所述的含双键的醇为一元醇或多元醇,优选为一元醇。根据一些实施方式,所述的含双键的醇为3
‑
丁烯
‑1‑
醇、3
‑
戊烯
‑1‑
醇、5
‑
己烯
‑3‑
乙基
‑1‑
醇中的一种或多种。
20.优选地,所述的含氢硅油与催化剂的混合物在所述管式连续流反应器中的流速为0.01~1000ml/min,所述的含双键的脂肪烃、醚、醇中的一种或多种在所述管式连续流反应器中的流速为0.01~1000ml/min。本发明中,根据管式连续流反应器的规格及反应所需的时间来调整流速。
21.优选地,所述管式连续流反应器的内径为1/16~8mm,选择内径合适的管式连续流反应器,可以使物料受热均匀,反应充分,从而提高产品转化率。所述管式连续流反应器的长度可根据需要选择。
22.优选地,将所述的含氢硅油与催化剂的混合物,以及所述的含双键的脂肪烃、醚、醇中的一种或多种先通入混合器中,然后再通入所述的管式连续流反应器中进行反应。
23.根据一些实施方式,所述的混合器的类型可以根据物料的特性进行更换,可以选择的类型有w型、e型、t型、p型、v型、s型、f型、ex型混合器。
24.优选地,所述的制备方法还包括将所述的含氢硅油与催化剂的混合物加入溶剂中制得稀释液,再将所述的稀释液通入所述的管式连续流反应器中进行反应,再将所述的管式连续流反应器中的出料进行减压蒸馏脱除溶剂得到所述的有机硅助剂。当含氢硅油粘度较高而无法直接进样时,可使用溶剂对其进行稀释,相应的出料需通过减压蒸馏脱除溶剂。
25.进一步优选地,所述溶剂为醇,所述溶剂的加入量为所述的含氢硅油、所述的催化剂和所述的溶剂总质量的0.01
‑
99%,更优选为1
‑
5%。所述的醇包括但不限于丁醇、戊醇、己醇中的一种或多种。
26.本发明中,若需要生产其他类型的产品,可根据需求对混合器前管中、混合器中及混合器后管中的物料进行回收,回收后可用于下一次生产。其中混合器前的可当原料使用,
混合器中及混合器后的样品可根据物料互溶状况判断是否直接通入连续流反应中进行反应,若互溶程度好则直接通入连续流反应器中,若互溶差可添加一定比例的溶剂混合后通入连续流反应器中。
27.本发明的制备方法可以获取不同停留时间的产品,然后通过与传统间歇釜生产的产品进行比较来确定性能最优的产品的生产条件。
28.本发明的有机硅助剂的制备方法的具体操作步骤如下:a)将一定分子量的含氢硅油(预先与催化剂混合),与含双键的脂肪烃和/或含双键的醚和/或含双键的醇同时通入管式连续流反应器,或经混合器混合后通入管式连续流反应器;b)反应温度设定为50~300℃,流速设定为0.01~1000ml/min,两股物料经过管式连续流反应器后出料即可得到产品。
29.本发明较传统间歇反应釜生产方法相比,整个反应过程连续化,生产不同类型的产品时只需更换的原料和操作参数,不仅大大简化了不同门类产品的生产流程,而且获得的产品与采用间歇釜生产的产品相比性能更加优异,有效保证了产品质量;本发明的反应时间短,原料转化稳定高效,有效提高了生产效率、降低了生产成本;本发明的生产过程不会造成环境污染,并且避免了资源浪费。
30.由于采用上述技术方案,本发明与现有技术相比具有如下优点:
31.本发明的制备方法可实现不同类别有机硅高分子助剂的连续化生产,大大简化了不同门类产品的生产流程;本发明的原料的转化率在短时间内可达到90%以上,且原料转化率稳定;本发明的制备方法能够有效保证产品质量、提高生产效率、降低生产成本。
附图说明
32.附图1:具体实施例中使用的连续流反应器的结构示意图;
33.附图2:实施例1的连续流反应器与传统间歇釜式反应器的转化率对比;
34.附图3:实施例2的连续流反应器与传统间歇釜式反应器的转化率对比;
35.附图4:实施例3的连续流反应器与传统间歇釜式反应器的转化率对比;
36.附图5:实施例4的连续流反应器与传统间歇釜式反应器的转化率对比;
37.附图6:实施例1与对比例1的产品在128环氧树脂中的抑泡性能和消泡性能测试;
38.附图7:实施例1与对比例1的产品在601环氧树脂中的抑泡性能和消泡性能测试;
39.附图8:实施例1与对比例1的产品在1753羟基丙烯酸树脂中的抑泡性能和消泡性能测试;
40.附图9:实施例1与对比例1的产品在yk304低羟丙烯酸树脂中的抑泡性能和消泡性能测试,
41.其中,附图1中:1、供料泵模块;2、混合器模块;3、换热反应模块。
具体实施方式
42.下面结合具体的实施案例对本发明的技术方案进一步描述,但本发明不只限于下面的实施例。实施例中采用的实施条件可以根据具体要求做进一步调整,未注明的实施条件通常为常规实验中的条件。
43.本发明中,使用的仪器、原料和试剂均可通过市售获得。
44.实施例1
45.(1)将连续流管式反应器的供料泵模块1、混合器模块2、换热反应模块3按照图1所示结构依次连接,本实施例的连续流反应器的内径为1mm。设置换热反应模块3的循环系统温度为240℃,预热时间为30min,使换热反应模块3处于温度平衡状态。
46.(2)设定供料泵的流量,控制含氢硅油与催化剂的混合物(含氢硅油分子量约为1200,活性氢含量约为0.17wt%;催化剂为氯铂酸水合物,用量为混合物总质量的0.01%)的流量为1.1ml/min,烯丙基单乙二醇醚的流量为0.2ml/min,可以根据停留时间的需要按照这一比例进行调整。
47.(3)两股物料经混合器模块2混合后,进入换热反应模块3进行反应,控制反应温度为240℃,物料在换热反应模块3中停留1
‑
600s,反应完成后的反应液即为产品,取不同反应时间的产品,经滴定分析,转化率均高于90%,并与传统间歇釜式反应器中的产品进行转化率比较,比较结果见图2。
48.由图2可知,本实施例可在极短的时间(40.7s)内取得相当高的转化率,与传统间歇釜反应器相比,效率大大提高。间歇釜反应器后期转化率较高的主要原因之一是高温下原料挥发,导致分析结果偏高,而连续流反应器不存在该问题。
49.实施例2
50.(1)本实例中使用的连续流反应器同实施例1,设置换热反应模块3的循环系统温度为230℃,预热时间为30min,使换热反应模块3处于温度平衡状态。
51.(2)设定供料泵的流量,控制含氢硅油与催化剂的混合物(含氢硅油分子量约为1200,活性氢含量约为0.17wt%;催化剂为氯铂酸水合物,用量为混合物总质量的0.01%)的流量为2.0ml/min,3
‑
丁烯
‑1‑
醇的流量为0.3ml/min,可以根据停留时间的需要按照这一比例进行调整。
52.(3)两股物料经混合器模块2混合后,进入换热反应模块3进行反应,控制反应温度为230℃,物料在换热反应模块3中停留1
‑
600s,反应完成后的反应液即为产品,取不同反应时间的产品,经滴定分析,转化率均高于90%,并与传统间歇釜式反应器中的产品进行转化率比较,比较结果见图3。
53.同样由图3可知,本实施例与传统间歇釜反应器相比,效率大大提高。间歇釜反应器中存在高温下原料挥发的问题,从而导致后期转化率分析结果偏高。
54.实施例3
55.(1)本实例中使用的连续流反应器同实施例1,并设置换热反应模块3的循环系统温度为200℃,预热时间为30min,使换热反应模块3处于温度平衡状态。
56.(2)设定供料泵的流量,控制含氢硅油与催化剂的混合物(含氢硅油分子量约为1200,活性氢含量约为0.17wt%;催化剂为卡斯特铂金催化剂,用量为混合物总质量的0.02%)的流量为2.0ml/min,十二碳烯的流量为0.8ml/min,可以根据停留时间的需要按照这一比例进行调整。
57.(3)两股物料经混合器模块2混合后,进入换热反应模块3进行反应,控制反应温度为200℃,物料在换热反应模块3中停留1
‑
600s,反应完成后的反应液即为产品,取不同反应时间的产品,经滴定分析,转化率均高于90%,并与传统间歇釜式反应器中的产品进行转化率比较,比较结果见图4。
58.同样由图4可知,本实施例与传统间歇釜反应器相比,效率大大提高。间歇釜反应
器中存在高温下原料挥发的问题,从而导致后期转化率分析结果偏高。
59.实施例4
60.(1)本实例中使用的连续流反应器同实施例1,设置换热反应模块3的循环系统温度为240℃,预热时间为30min,使换热反应模块3处于温度平衡状态。
61.(2)设定供料泵的流量,控制含氢硅油与催化剂的混合物(含氢硅油分子量约为1200,活性氢含量约为0.17wt%;催化剂为卡斯特铂金催化剂,用量为混合物总质量的0.02%)的流量为2.4ml/min,烯丙基聚乙二醇400单甲醚的流量为2ml/min,可以根据停留时间的需要按照这一比例进行调整。
62.(3)两股物料经混合器模块2混合后,进入换热反应模块3进行反应,控制反应温度为240℃,物料在换热反应模块3中停留1
‑
600s,反应完成后的反应液即为产品,取不同反应时间的产品,经滴定分析,转化率均高于90%,并与传统间歇釜式反应器中的产品进行转化率比较,比较结果见图5。
63.由图5可知,本实施例的转化率明显高于传统间歇釜反应器,并且本实施例可在极短的时间(40.7s)内取得相当高的转化率,与传统间歇釜反应器相比,效率大大提高。由于本实施例使用的原料沸点较高,不存在挥发的问题,因此可明显看出本实施例的优越性。
64.对比例1
65.往250ml三口烧瓶中加入烯丙基单乙二醇醚10.2g,含氢硅油与催化剂的混合物(含氢硅油分子量约为1200,活性氢含量约为0.17wt%;催化剂为氯铂酸水合物,用量为混合物总质量的0.01%)129.6g,搅拌下加热升温至240℃,恒温反应10min后,取出冷却即得到对比例1的产品lqh
‑
1200。
66.选取实施例1中停留时间为276.9s(p4)、138.5s(p7)、60.2s(p12)、40.7s(p14)的样品与对比例1制得的产品lqh
‑
1200进行消泡、抑泡性能测试,测试方法如下:
67.在不同树脂体系下,分别添加0.2%的不同样品、lqh
‑
1200、或空白样,密封好后,一同进行震荡机震荡10min后取出。
68.抑泡性能:震荡前液面高度记为h0,震荡后气泡高度不再增加时记录液面高度h1,液面高度变化率(%)=(h1‑
h0)/h0*100,根据液面高度变化率划分抑泡能力。
69.抑泡能力等级划分标准:1:0
‑
1%;2:1
‑
5%;3:5
‑
15%;4:15
‑
30%;5:>30%;+:更好;
‑
:更差;其中,数值越小代表抑泡作用越好,数值越大代表抑泡作用越差,同一数值下,“+”越多代表抑泡作用越好,
“‑”
越多代表抑泡作用越差,例如,按抑泡作用从好至差:2>3++>3+>3>3
‑
>3
‑‑
>4。。
70.消泡性能:将上述震荡后的测试样静置1h后观察气泡状况并划分等级,划分标准为:a:完全没有气泡;b:几乎没有气泡;c:气泡较少,仅上半液层中有一些气泡;d:气泡很多且不是很紧密;e:气泡很多,没有液体可见;+:更好;
‑
:更差。
71.抑泡性能及消泡性能结果见表1~4。
72.p4、p7、p12、p14、lqh
‑
1200在128树脂中的抑泡、消泡性能比较结果见表1和图6,图6从左至右依次为128树脂中加入空白样、p12、p14、lqh
‑
1200、p4、p7。由于消泡剂与128树脂存在一定的不相容性,故气泡消失后体系浑浊、不透明,但液面高度基本没有差别。
73.表1
[0074] 空白lqh
‑
1200p4p7p12p14
抑泡性5
‑‑
2++2++2++2++2++消泡性ecccc+c+
[0075]
p4、p7、p12、p14、lqh
‑
1200在601树脂中的消泡、抑泡性能比较结果见表2和图7,图7从左至右依次为601树脂中加入空白样、p7、p4、lqh
‑
1200、p12、p14。由于消泡剂与601树脂存在一定的不相容性,故气泡消失后体系浑浊、不透明,但液面高度基本没有差别。
[0076]
表2
[0077] 空白lqh
‑
1200p4p7p12p14抑泡性42222+2+消泡性cc+c+c+c++c+
[0078]
p4、p7、p12、p14、lqh
‑
1200在1753树脂中的消泡、抑泡性能比较结果见表3和图8,图8从左至右依次为1753树脂中加入空白样、lqh
‑
1200、p12、p7、p14、p4。
[0079]
表3
[0080] 空白lqh
‑
1200p4p7p12p14抑泡性3
‑‑
3+3+3+3+3+消泡性cccccc
[0081]
p4、p7、p12、p14、lqh
‑
1200在yk304树脂中的消泡、抑泡性能比较结果见表4和图9,图9从左至右依次为yk304树脂中加入空白样、lqh
‑
1200、p7、p14、p4、p12。
[0082]
表4
[0083] 空白lqh
‑
1200p4p7p12p14抑泡性3
‑
3+3+3+3+3+消泡性c+ccccc
[0084]
通过以上实验结果可知,使用较短停留时间制备的有机硅消泡剂具有与lqh
‑
1200相当甚至更好的消泡和抑泡性能,其中,抑泡性能更加优越,在很多测试条件下60.2s(p12)具有更为优异的消泡和抑泡特性。
[0085]
以上对本发明做了详尽的描述,目的在于让本领域内的技术人员了解本发明的内容并加以实施,并不能以此限制本发明的保护范围,且本发明不限于上述的实施例,凡根据本发明的精神实质所做的等效变化或修饰,都应涵盖在本发明的保护范围之内。