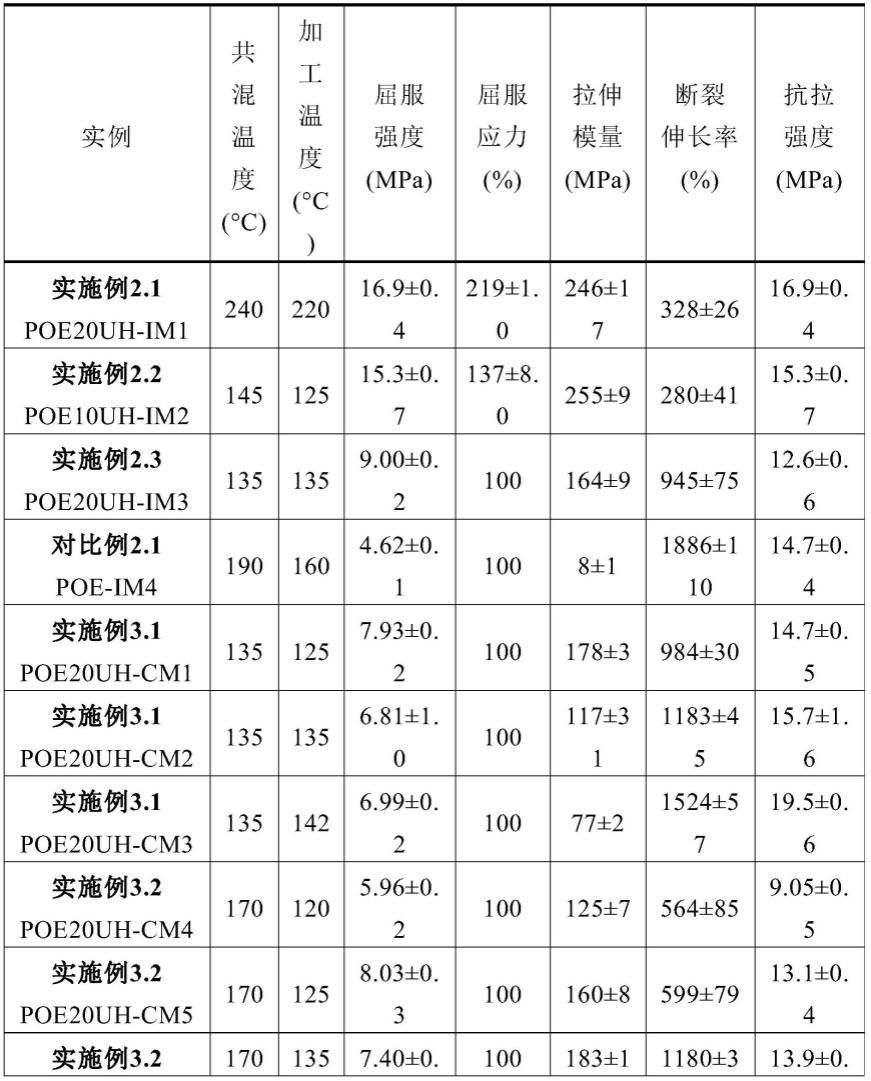
1.本发明属于高分子材料改性和加工成型技术领域,具体地,本发明涉及一种原位形成低支化超高分量聚乙烯微纳纤维增强聚烯烃弹性体组合物及制备方法。
背景技术:2.聚烯烃弹性体(poe)是使用耐高温(非)茂金属催化剂通过高温高压溶液共聚技术制造的乙烯/a-烯烃共聚物。通过改变共聚单体的含量和类型、“剪裁”共单体在分子链中的分布、分子量和长支链含量,能调控poe的聚集态结构及其相应的热、力学和流变性能。poe是由无定形软链段和可结晶硬链段化学键合的共聚物。不同链段的热力学不相容性导致形成非均相聚集态结构。在使用温度下,无定形软链段提供橡胶的弹性,以具有可逆热熔化和冷固化的晶体作为物理交联点提供力学强度。高温下,晶体熔融而具有热塑性,从而使用塑料的注塑、挤出和发泡等加工工艺设备加工。与传统硫化橡胶相比,poe呈颗粒形态,容易跟其他聚合物共混,加工成型能耗低,污染少,产品无毒、可回收再利用。poe除了汽车轮胎以外,广泛应用于汽车内外饰件、电线电缆护套、建筑防水卷材、生物医用材料、家电、光伏封装、鞋底和自行车轮胎等。然而,由于耐高温(非)茂金属催化剂和高温高压溶液共聚技术的限制,用于发泡、热成型和吹塑成型的高分子量高熔体强度聚烯烃弹性体只能通过气相流化床反应器技术制造。
3.超高分子量聚乙烯(uhmwpe)的分子量在1
–9×
106g/mol之间,链缠结含量较高,具有自润滑、耐磨损、耐切割、耐低温冲击、耐环境应力开裂性、抗积垢和抗污染和优良的生物相容性。因此,通过溶液凝胶纺丝制造的高强高模uhmwpe纤维广泛应用于耐切割防护手套、防弹背心和船只绳缆等,通过模压成型和挤出制造的材料通过一次成型或二次加工应用于人工关节和特殊板材,通过单螺杆挤出方法制造的管材应用于耐磨和耐高温领域,通过热至相分离和单向拉伸的uhmwpe微孔膜应用于锂电池隔膜。uhmwpe作为高性能工程塑料,也应用于聚丙烯的增韧增强改性和橡胶的耐磨改性。
4.uhmwpe纤维强度高、模量高、耐切割和耐腐蚀等特点,广泛应用于增强橡胶材料。复合材料制造主要通过两种方式,第一种是橡胶混炼过程中添加短切uhmwpe纤维,能明显改善橡胶的耐磨擦性能(cn1454928a)。然而,硫化或成型温度高于纤维熔点时,纤维熔化,增强效果降低。另外,短切纤维表面光滑,不易粘附异物,纤维与基体的粘结强度低。另外,纤维与基体的相容性较差,难于与基体粘结,纤维增强橡胶的效果不明显。第二种是采用界面改性方法提高uhmwpe纤维与纤维基体的粘结程度。中国专利cn 104292510a公开了一种通过界面改性技术制备1-10份uhmwpe纤维/橡胶复合材料的方法,虽然复合材料的撕裂强度和纤维的剥离强度均提高,但是复合材料的拉伸模量较低。aizezi m.等(acs appl.polym.mater.2019,1,7,1735-1748)把聚烯烃弹性体颗粒与聚丙烯树脂熔体共混形成双连续相结构,通过辐射交联改善聚烯烃弹性体与聚丙烯的相界面,再二次模压使聚丙烯分散相发生取向,与未交联共混物相比,所制备薄膜的100%定伸强度和抗拉强度显著提
60
‑‑
30℃。
24.本发明的第二方面,提供了一种如本发明第一方面所述的树脂组合物的制备方法,所述方法包括步骤:
25.任选的(1)预混:将聚烯烃弹性体颗粒和低支化超高分子量聚乙烯粉末混合均匀;
26.(2)熔体共混:在熔体共混设备中,对所述的聚烯烃弹性体颗粒和低支化超高分子量聚乙烯粉末进行熔体共混,其中,所述的共混在聚烯烃弹性体熔点以上,且聚乙烯分解温度以下的温度下进行,且所述熔体共混设备的转速为50-500rpm;优选地,共混完成后,对所述的树脂组合物进行造粒。
27.在另一优选例中,所述的预混步骤使用高速混合机或其他混合设备进行。
28.在另一优选例中,所述的熔体共混设备选自下组:反向双螺杆挤出机、同相双螺杆挤出机、单螺杆挤出机。
29.在另一优选例中,所述的共混的温度80-250℃。
30.在另一优选例中,所述的熔体共混设备的转速为200-500rpm。
31.本发明的第三方面,提供了一种制品,所述的制品是用如本发明第一方面所述的树脂组合物制备的,或所述的制品含有如本发明第一方面所述的树脂组合物。
32.本发明的第四方面,提供了一种如本发明第三方面所述的制品的制备方法,所述的制品采用选自下组(i)、(ii)或(iii)的方法进行成型:
33.(i)注塑成型:使用微注塑机或注塑机,对如本发明第一方面所述的树脂组合物进行注塑成型;其中,所述的注塑在温度为100-250℃下进行,且所述注塑过程中,模具温度为0-80℃;
34.(ii)模压成型:在聚烯烃弹性体熔点以上和190℃以下的模压温度下,对如本发明第一方面所述的树脂组合物进行模压成型;
35.(iii)挤出成型:在120-250℃下,对如本发明第一方面所述的树脂组合物进行挤出成型;且所述挤出成型过程中,模具温度为聚烯烃弹性体熔点-220℃。
36.在另一优选例中,注塑、模压和挤出成型制品中超高分子量聚乙烯呈现微纳纤维状和类球形微纳颗粒。
37.在另一优选例中,当采用注塑成型工艺时,与纯聚烯烃弹性体相比,所述树脂组合物的拉伸模量提高2-40倍。
38.在另一优选例中,当采用注塑成型工艺时,与纯聚烯烃弹性体相比,所述树脂组合物的100%定伸强度提高1-5倍。
39.在另一优选例中,当采用模压成型工艺时,与纯聚烯烃弹性体相比,所述树脂组合物的拉伸模量提高2-35倍。
40.在另一优选例中,当采用模压成型工艺时,与纯聚烯烃弹性体相比,所述树脂组合物的100%定伸强度提高1-4倍。
41.在另一优选例中,所述的制品用于制备选自下组的橡塑制品:耐磨鞋底、抗穿刺薄膜、减震器、发泡材料、传送带、聚丙烯或尼龙的增韧改性。
42.应理解,在本发明范围内中,本发明的上述各技术特征和在下文(如实施例)中具体描述的各技术特征之间都可以互相组合,从而构成新的或优选的技术方案。限于篇幅,在此不再一一累述。
附图说明
43.图1为本发明所使用的低支化超高分子量聚乙烯粉末的形貌图;
44.图2为本发明实施例2.1-3和3.1-3.4的微注塑和模压复合材料的拉伸应力-应变曲线;
45.图3为本发明实施例2.1,3.2和3.4的注塑和模压片材中低支化超高分子量聚乙烯微纳纤维的形貌图。
具体实施方式
46.本发明人经过长期而深入的研究,开发了一种含有聚烯烃弹性体和低支化超高分子量聚乙烯分散相增强体的树脂组合物。通过调整低支化超高分子量聚乙烯分散相增强体的含量,制备得到了刚性和强度同时改善的熔体共混树脂组合物。基于上述发现,发明人完成了本发明。
47.树脂组合物的制备
48.为了克服传统超高分子量聚乙烯短切纤维增强橡胶复合材料及其加工方法的缺点,本发明提供了一种原位形成低支化超高分子量聚乙烯微纳纤维增强聚烯烃弹性体组合物及制备方法,所述方法包括以下步骤:
49.(1)预混:使用高速混合机或其他混合设备把按比例称重的聚烯烃弹性体颗粒和超高分子量聚乙烯粉末混合均匀。也可以通过双螺杆挤出机分批加料免去预混工序段。
50.(2)熔体共混:使用双螺杆挤出机熔体共混,共混温度为100-250℃,转速为100-500rpm,造粒。
51.(3)成型:所述的成型采用以下任意一种方法进行:
52.注塑成型:使用微注塑机或注塑机,注塑温度为100-250℃,模具温度为0-80℃,组合物的拉伸模量和100%定伸强度比纯聚烯烃弹性体分别提高40倍和5倍。
53.模压成型:在聚烯烃弹性体熔点以上和190℃以下的模压温度下模压成型,组合物的拉伸模量和100%定伸强度比纯聚烯烃弹性体分别提高35倍和4倍。
54.在步骤1所述的超高分子量聚乙烯粉末为无规则或类球形疏松性多孔粉体,含有纳米纤维连接的类球形次级颗粒(附图1),支化度小于1/100000c,粘均分子量为1.5
–9×
106g/mol,颗粒大小为40
–
300um,粉体熔点为140-145℃,结晶度为65-80wt%。
55.在步骤1所述的聚烯烃弹性体颗粒为至多含50wt%a-烯烃的乙烯/a-烯烃共聚物,a-烯烃选用丙烯、1-丁烯、1-己烯、1-辛烯和4-甲基-1-戊烯等,优先选用乙烯/1-丁烯共聚物和乙烯/1-辛烯共聚物,熔体流动指数为0.2-30g/10min(2.16kg@190℃),重均分子量为50-300kg/mol,分子量分布为1.5-3,密度为0.85-0.92g/cm3,熔点为30-120℃,玻璃化转变温度为-60
‑‑
30℃。聚烯烃弹性体产品可以选用dow公司的engage
tm
系列牌号、mitsui chemical公司的tafmer
tm
系列牌号、exxonmobile公司的vistamaxx
tm
系列牌号、lg公司的lucene
tm
系列牌号和sabic公司的fortify
tm
系列牌号产品及其组合物。
56.在步骤2和3中所述的工艺可以在双螺杆挤出机中进行,优选地,所述的双螺杆挤出机可以为为反向双螺杆挤出机、同相双螺杆挤出机,或单螺杆挤出机。
57.通过步骤2制备的组合物跟其他添加剂共混,然后进行成型以制备相关产品,例如耐磨鞋底、抗穿刺薄膜、减震器、发泡材料和传送带等领域,也可以应用于聚丙烯和尼龙的
增韧改性。
58.作为增强体的低支化超高分子量聚乙烯
59.本发明中,所使用的低支化超高分子量聚乙烯可以通过本领域中已知的方法制备,在一个优选的实施方式中,采用以下方法制备:
60.以催化剂和烷基铝化合物为助催化剂组成的非均相催化体系与乙烯接触,在乙烯分压为0.2至10mpa、0至100℃范围内反应1-18小时获得。催化剂与助催化剂的摩尔比是1:1-5000,一般可在1:10-2000时聚合2-6小时以便使催化活性、聚合物性质与生产成本均维持在较好的范围,优选1:20~500。
61.其中,所述的催化剂可以采用本领域已知的相应催化剂,但一个优选的实施方式下,催化剂通过步骤(a)-(d),和任选的步骤(e)进行制备:
62.(a)惰性气体保护条件下,将无水氯化镁加入到惰性烃类溶剂中,搅拌条件下加入≥2当量氯化镁的c1-c10的醇进行接触,体系保持至60-120℃形成均一溶液,然后,降温至-30℃以下,控制搅拌转速和超重力反应器转速得到前体浆液p-i;其中,所述的降温速度优选1-10℃/min;所述的惰性气体优选氮气;优选2-6当量的c1-c10的醇;更优选2-4当量;
63.(b)步骤(a)得到的前体浆液i在低于-30℃的条件下与烷基铝接触1-2h,随后在60-120℃保持2-6h得到前体浆液p-ii;
64.(c)步骤(b)得到的前体浆液ii在-30℃以下与钛化合物的烃类溶液接触0.5-1h后升温并在60-120℃保持2-6h,得到催化剂浆液c-iii;升温速度优选1-10℃/min;
65.(d)将步骤(c)得到的催化剂浆液c-iii过滤;
66.(e)将步骤(d)得到的催化剂浆液干燥;
67.其中,所述的钛化合物是能够溶解于烃类溶剂中的,例如ticl4或ti(r)4,其中r是c1-c6的烷基、烯丙基、苄基或nme2,或者其他能够溶解于烃类溶剂中的钛化合物。
68.钛配合物与氯化镁的摩尔比可以为0.3-0.8:1,优选0.4-0.6:1,最优选0.5:1;在第四副族金属钛的烷基配合物络合载钛反应的过程中,需要控制反应升温的速度,升温速度为1-10℃/min,优选1-5℃/min,最优选1℃/min;最后载钛接触反应的温度控制在60-120℃,优选80-100℃,在优选温度下反应时间控制在2-6h,优选4-5h。
69.聚合一般在惰性有机溶剂中进行,例如烃类、环烃类或芳烃类,也可以在卤代溶剂中进行,如二氯乙烷、氯苯,为有利于反应器操作,惰性有机溶剂可使用小于12个碳的烃类。举例如下但并不仅限于此,丙烷、异丁烷、正戊烷、2-甲基丁烷、正己烷、环己烷、甲苯、氯苯、二氯乙烷及其混合物。
70.聚合温度维持在0至100℃,为达到好的催化活性与生产能力,可维持在40至80℃。
71.聚合乙烯分压为0.2至1.5mpa或聚合乙烯分压为0.2至1.5mpa/氢气分压为0.01-0.1mpa内操作可获得较好的反应器操作参数与聚合物。
72.助催化剂是烷基铝化合物,烷基铝氧烷或弱配位阴离子;所述的烷基铝化合物优选于alet3,alme3或al(i-bu)3,alet2cl,烷基铝氧烷优选甲基铝氧烷,mmao(修饰的甲基铝氧烷)等;弱配位阴离子优选于[b(3,5-(cf3)2c6h3)4]-、-oso2cf3或((3,5-(cf3)2)c6h3)4b-。催化剂与助催化剂可以任何顺序加入体系使聚合进行,优选alet3。聚合所使用的催化剂与助催化剂的比例可变,通常所述的聚合时间为1-18小时,催化剂与助催化剂的摩尔比是1:1-5000,一般可在1:10-2000时聚合2-6小时以便使催化活性、聚合物性质与生产成本均维持
在较好的范围,优选1:20-500。
[0073]
在本发明的优选实施方式中,所述的催化剂在40-80℃、0.2-0.8mpa乙烯压力下催化乙烯聚合得到超高分子量聚乙烯微粒,且聚合活性高于100kg pe/g cat.,聚合得到的粉料重量比至少95%以上通过150微米的网状筛,以激光衍射散射法测定的中径(d
50
)为50μm≤d
50
≤80μm,更优的,为50μm≤d
50
≤70μm,聚乙烯粘均分子量150-1000万;更优的,聚乙烯粘均分子量150-800万。利用熔融
13
c nmr分析其支化结构,证实聚合物中每100,000个骨架碳原子中含有支链数目小于1个。
[0074]
与现有技术相比,本发明的主要优点包括:
[0075]
1.本发明使用普通双螺杆挤出机通过聚烯烃弹性体与低支化超高分子量聚乙烯粉末直接熔体共混,原位形成超高分子量聚乙烯微纳纤维化结构,通过调节注塑和模压工艺,保留其微纳纤维结构并发生取向,大幅度提高聚烯烃弹性体的拉伸模量和定伸强度,从而使橡胶的刚性和强度同时增加。
[0076]
2.本发明提供的低支化超高分子量聚乙烯增强聚烯烃弹性体组合物可以在普通塑料加工设备制造,具有通用性,加工成本低,对超高分子量聚乙烯微纳纤维不需表面处理。
[0077]
下面结合具体实施例,进一步阐述本发明。应理解,这些实施例仅用于说明本发明而不用于限制本发明的范围。下列实施例中未注明具体条件的实验方法,通常按照常规条件,或按照制造厂商所建议的条件。除非另外说明,否则百分比和份数按重量计算。
[0078]
具体实施方式
[0079]
具体实例用于说明本发明的新型低支化超高分子量聚乙烯原位微纳纤维增强聚烯烃弹性体组合物及制备方法的优越性以及制品性能的可控性。本发明范围不限于实例中的工艺操作条件和制品性能及应用。
[0080]
通用测试方法
[0081]
粉末形貌及其在组合物中的形态测试:在hitachi mci000真空镀铂后,使用hitachi regulus 8100扫描电子显微镜在10kv和10ua条件下表征粉末形貌和组合物的低温脆断断面形貌;
[0082]
粉末的熔点和结晶度测试:使用dsc2000测试,条件为将3-8mg粉末切片装入铝制干锅,在氮气气氛下以10℃/min加热速率升温至160℃,恒温3min后,以10℃/min冷却速率降温至40℃,恒温3min。以10℃/min加热速率升温至160℃。结晶度为熔融焓*100%/290(kj/mol)。
[0083]
力学性能测试:注塑样品按实施实例制备注塑成iso20573-typecp多用途样条。模压片材使用冲片机和裁刀切iso20573-typecp多用途样条。在wdw-20电子万能试验机进行测试,拉伸速率为50mm/min,环境温度为23℃,力学性能数据取5-6个样品的平均值。
[0084]
复合粘度测试:低温模压样品切成直径为25mm的圆片,在ta instrument ares-g2旋转流变仪中在160℃测定0.01-100rad/s范围的复合粘度。
[0085]
本发明使用的双螺杆挤出机和微注塑为thermo scientific公司的haake polylab os rheodrive 4双螺杆挤出机(l/d为40)和haake minijet ii注塑机。模压机为锡华精密检测仪器公司生产的xh-406型通用压片机,具有两层独立的加热和加压单元,模压在下层单元中进行,冷却结晶在上层进行。力学性能测试使用iso20573-typecp多用途样
条。
[0086]
本发明使用的原料为低支化超高分子量聚乙烯,中试产品,编号为uh,粘均分子量为3.89
×
106g/mol,熔点为142.5℃,结晶度为81.7%,支化度<1/100000,其粉末形态如附图1所示。该低支化超高分子量聚乙烯可以通过现有技术中合适的方法制备,例如中国专利201010554473.8中所述的低支化超高分子量聚乙烯。
[0087]
在一个优选例中,该低支化超高分子量聚乙烯通过以下方法制备:
[0088]
将30l不锈钢搅拌聚合釜先后用n2置换,0.4mpa氮气下利用8kg己烷把alet3(10ml)加入釜内,控制搅拌转速250rpm,釜内温度预热到60℃左右,然后使用0.4mpa氮气压力条件下利用2kg己烷把30mg cat冲进聚合釜内,活化10min,然后卸去釜内氮气压力,再通入乙烯气体,使釜内压力达到0.4mpa,控制釜内温度为70℃,聚合2h后停止通入乙烯,用循环恒温油浴使釜内温度降至50℃以下,放空体系中的气体并出料,干燥后得到颗粒状聚合物。其中,催化剂是通过以下方法制备的:
[0089]
(a)惰性气体保护条件下,将无水氯化镁加入到惰性烃类溶剂中,搅拌条件下加入≥2当量氯化镁的c1-c10的醇进行接触,体系保持至60-120℃形成均一溶液,然后,降温至-30℃以下,控制搅拌转速和超重力反应器转速得到前体浆液p-i;所述的降温速度为1-10℃/min;
[0090]
(b)步骤(a)得到的前体浆液i在低于-30℃的条件下与烷基铝接触1-2h,随后在60-120℃保持2-6h得到前体浆液p-ii;
[0091]
(c)步骤(b)得到的前体浆液ii在-30℃以下与钛化合物的烃类溶液接触0.5-1h后升温并在60-120℃保持2-6h,得到催化剂浆液c-iii;升温速度优选1-10℃/min;
[0092]
(d)将步骤(c)得到的催化剂浆液c-iii过滤;
[0093]
(e)将步骤(d)得到的催化剂浆液干燥,得到所述的催化剂。
[0094]
本发明所使用的聚烯烃弹性体颗粒为陶氏化学公司的engage
tm
产品,分子量为71.7kg/mol,分子量分布为2.27,支化度为35.1ch3/1000c,1-辛烯含量为8.7mol%,熔点为78℃。
[0095]
实施例1.1共混实例e1
[0096]
称取800g聚烯烃弹性体、200g超高分子量聚乙烯粉体和5g抗氧剂(1010),均匀预混合后,倒入双螺杆挤出机喂料口,共混温度为190-200-210-220-220-240-220-220-210-200℃,转速为200rpm,扭矩为74nm,喂料速率为15%,挤出后水浴冷却,造粒,在60℃真空干燥24h。在相同条件下,再共混造粒,干燥。
[0097]
实施例1.2共混实例e2
[0098]
称取800g聚烯烃弹性体、200g超高分子量聚乙烯粉体和5g抗氧剂(1010),均匀预混合后,倒入双螺杆挤出机喂料口,共混温度为110-120-130-130-130-135-130-130-125-120℃,转速为100rpm,扭矩为90-100nm,喂料速率位6%,挤出后水浴冷却,造粒,在60℃真空干燥24h。在相同条件下,再共混造粒,干燥。
[0099]
实施例1.3共混实例e3
[0100]
称取800g聚烯烃弹性体、200g超高分子量聚乙烯粉体和5g抗氧剂(1010),均匀预混合后,倒入双螺杆挤出机喂料口,共混温度为140-150-150-160-160-170-160-160-160-150℃,转速为100rpm,扭矩为90-100nm,喂料速率位10%,挤出后水浴冷却,造粒,在60℃真
空干燥24h。在相同条件下,再共混造粒,干燥。
[0101]
实施例1.4共混实例e4
[0102]
称取900g聚烯烃弹性体、100g超高分子量聚乙烯粉体和5g抗氧剂(1010),均匀预混合后,倒入双螺杆挤出机喂料口,共混温度为110-120-130-130-140-145-140-140-135-130℃,转速为100rpm,扭矩为95nm,喂料速率位8%,挤出后水浴冷却,造粒,在60℃真空干燥24h。在相同条件下,再共混造粒,干燥。
[0103]
实施例1.5共混实例e5
[0104]
称取900g聚烯烃弹性体、100g超高分子量聚乙烯粉体和5g抗氧剂(1010),均匀预混合后,倒入双螺杆挤出机喂料口。挤出机喂料段到模口温度为110-120-130-130-130-135-130-130-125-120℃,转速为100rpm,扭矩为80-100nm,喂料速率为6-8%,挤出后水浴冷却,造粒,在60℃真空干燥24h。
[0105]
对比例1.1共混对比实例e6
[0106]
称取1000g聚烯烃弹性体和5g抗氧剂(1010),均匀预混合后,倒入双螺杆挤出机喂料口,挤出温度为140-150-160-170-180-190-190-180-180-170℃,转速为150rpm,扭矩为75nm,喂料速率为15%,挤出后水浴冷却,造粒,在60℃真空干燥24h。在相同条件下,再共混造粒,干燥。
[0107]
实施例2.1注塑实例im1
[0108]
使用e1造粒的组合物在thermo scientific haake minijet ii中进行注塑,制备iso20573-typecp多用途样条,注塑温度为220℃,注塑压力为90mpa,注塑时间为30s,保压压力为60mpa,保压时间为1min,模具温度为40℃,结晶时间为5min。
[0109]
实施例2.2注塑实例im2
[0110]
使用e4造粒的组合物在thermo scientific haake minijet ii中进行注塑,制备iso20573-typecp多用途样条,注塑温度为125℃,注塑压力为90mpa,注塑时间为30s,保压压力为60mpa,保压时间为1min,模具温度为40℃,结晶时间为5min。
[0111]
实施例2.3注塑实例im3
[0112]
使用e2造粒的组合物在thermo scientific haake minijet ii中进行注塑,制备iso20573-typecp多用途样条,注塑温度为135℃,注塑压力为90mpa,注塑时间为30s,保压压力为60mpa,保压时间为1min,模具温度为40℃,结晶时间为5min。
[0113]
对比例2.1注塑对比实例im4
[0114]
使用e6造粒的聚烯烃弹性体在thermo scientific haake minijet ii中进行注塑,制备iso20573-typecp多用途样条,注塑温度为160℃,注塑压力为90mpa,注塑时间为30s,保压压力为60mpa,保压时间为1min,模具温度为40℃,结晶时间为5min。
[0115]
实施例3.1模压实例cm1-3
[0116]
使用e2造粒的组合物分别在125、135、142℃和相同2.5mpa下,预压10min,再在10mpa下,压制5min,40-60℃冷却结晶5-10min,制备厚度为2mm的片材。使用冲片机和iso20573-typecp裁刀制备标准样条5-6个。
[0117]
实施例3.2模压实例cm4-6
[0118]
使用e3造粒的组合物在120、125、135℃和相同2.5mpa下,在模压机中预压10min,再在10mpa下,压制5min,40-60℃冷却结晶5-10min,制备厚度为2mm的片材,10rad/s和120
℃的复合粘度为13.5kpa.s。使用冲片机和iso20573-typecp裁刀制备标准样条5-6个。
[0119]
实施例3.3模压实例cm7
[0120]
使用e1造粒的组合物在120℃和2.5mpa下,在模压机中预压10min,再在10mpa下,压制5min,60℃冷却结晶5-10min,制备厚度为2mm的片材。使用冲片机和iso20573-typecp裁刀制备标准样条5-6个。
[0121]
实施例3.4模压实例cm8-9
[0122]
使用e4和e5造粒的组合物在123℃和2.5mpa下,在模压机中预压10min,再在10mpa下,压制5min,40-60℃冷却结晶5-10min,制备厚度为2mm的片材。10rad/s和120℃的复合粘度为7.42kpa.s。使用冲片机和iso20573-typecp裁刀制备标准样条5-6个。
[0123]
对比例3.1模压对比实例cm10
[0124]
使用e6造粒的聚烯烃弹性体在125℃和2.5mpa下,在模压机中预压10min,再在10mpa下,压制5min,40℃冷却结晶10min,制备厚度为2mm的片材,10rad/s和120℃的复合粘度为4.54kpa.s。使用冲片机和iso20573-typecp裁刀制备标准样条5-6个。
[0125]
上述各个实施例中制备得到的试样的测试结果如下表1中所示:
[0126]
表1
[0127]
[0128][0129]
上述共混实施例1.1-6和微注塑实施例2.1-3结果表明,聚烯烃弹性体跟低支化高分子量聚乙烯高温共混时,双螺杆扭矩不大(实施例1.1),而按原位微纳纤维化技术低温共混时,扭矩很大(实施例1.2和1.5),需要降低挤出机转速,以便降低组合物的熔体粘度和挤出摩擦生热,会导致降低生产效率,不适合规模生产,更重要的是降低挤出机转速会降低剪切速率,使超高分子量聚乙烯粉体的分散性变差。然而,有意义的是,这种低温共混颗粒,低温注塑时,复合材料保持硬弹性,没有表现明显屈服行为(实施例2.3-im3和附图2-im3曲线)。在超高分子量聚乙烯熔点以上共混并低温注塑时,只需要添加10wt%的超高分子量聚乙烯,能使复合材料的性能大幅度提高(实施例2.2和附图2-im2)。因此,聚烯烃弹性体跟低支化超高分子量聚乙烯共混并加工时,需要平衡其加工性能和制品性能。
[0130]
如表1所示,当成型温度(模具温度)降低至超高分子量聚乙烯熔点附近的温度(125-145℃)时,链松弛速率降低,有助于微纳纤维的取向和保留(附图3),从而显著增强复合材料的性能:
[0131]
(1)微注塑实施2.1-2.3结果(表1)表明,当聚烯烃弹性体基体中的低支化超高分子量聚乙烯含量超过10wt%时,注塑复合材料皮层容易形成三维链缠结的物理网络,微纳纤维发生取向(附图3,poe20uh-im),即使高温注塑时,复合材料仍表现屈服行为(实施例2.1-3和附图2-im)。因此,兼顾加工性能和复合材料的弹性性能以及耐磨损性能,低支化超高分子量聚乙烯的含量应少于20wt%,更优选地少于10wt%。
[0132]
(2)模压实施例3.1-3.4结果(表1)表明,模压温度高于聚烯烃弹性体熔点以上和接近低支化超高分子量聚乙烯粉体熔点时,低支化超高分子量聚乙烯保留纳米纤维结构(附图3,poe10uh-cm和poeuh-cm),显著增强复合材料中的力学性能,并且复合材料保持硬弹性体性能;随着超高分子量聚乙烯含量的增加和模压温度的提高,复合材料定伸强度变化不大,但拉伸模量和断裂伸长率提高,说明模压温度的提高有利于颗粒之间的粘接。当聚烯烃弹性体基体中的低支化超高分子量聚乙烯含量超过20wt%时,模压复合材料的力学性能大幅增加,但是三维链缠结网络大幅度增加组合物的复合粘度,影响其熔体流动性能。为此,兼顾加工性能和复合材料的弹性性能以及耐磨损等性能,低支化超高分子量聚乙烯的含量应少于20wt%。模压材料使用ares-g2流变仪测试流变性能得出,poe20uh、poe10uh和poe在0.1rad/s的复合粘度分别为49、9.3和4.8kp.s,表明超高分子量聚乙烯的加入大幅度增加聚烯烃弹性体的熔体粘度,因此,这种组合物在可重复加工高熔体强度弹性体及其发
泡材料领域显示潜在的应用价值。
[0133]
综合上述,组合物应用于工业生产时,优化共混和加工成型工艺,可以明显降低低支化超高分子量聚乙烯的用量,从而降低生产成本。根据复合材料的性能需求(弹性性能、刚性和耐磨损性能特殊性能),可以选用含不同组分超高分子量聚乙烯的组合树脂,满足生产和制品要求。
[0134]
在本发明提及的所有文献都在本技术中引用作为参考,就如同每一篇文献被单独引用作为参考那样。此外应理解,在阅读了本发明的上述讲授内容之后,本领域技术人员可以对本发明作各种改动或修改,这些等价形式同样落于本技术所附权利要求书所限定的范围。