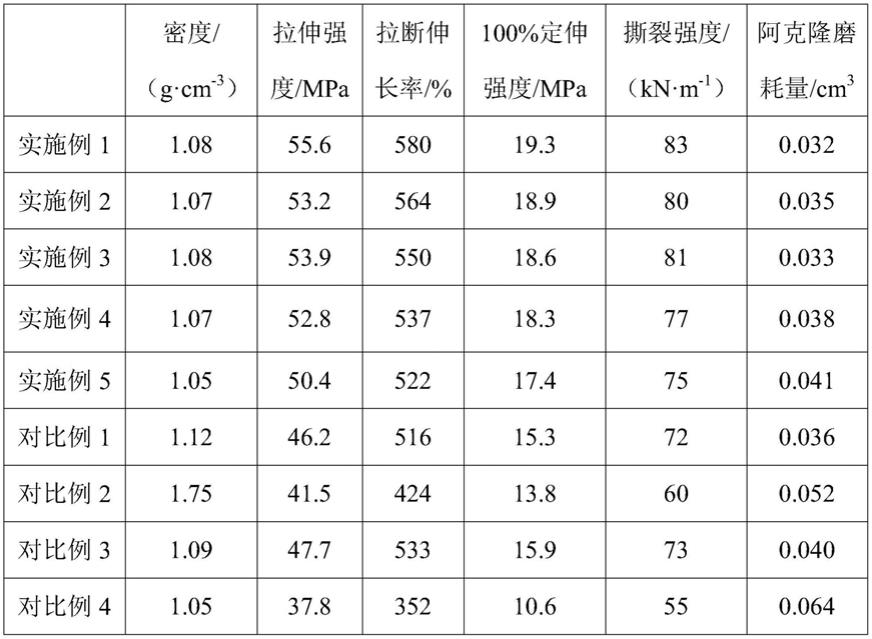
1.本发明涉及高分子材料领域,具体为一种船用耐盐雾腐蚀橡胶材料及其制备方法。
背景技术:2.盐雾腐蚀是一种常见和最有破坏性的大气腐蚀。盐雾是指大气中由含盐微小液滴所构成的弥散系统。其成因主要由于海洋中海水激烈扰动,风浪破碎,海浪拍岸等产生大量泡沫、气泡,气泡破裂时会生成微小的水滴,海水滴大部分因重力作用而降落,部分处于平衡的状态而分布于海面上,它们随气流升入空中,经裂解、蒸发、混并等过程演变成弥散系统。
3.船舶在海上航行过程中,长时间处于该盐雾弥散系统中,会导致船用橡胶件腐蚀、老化、甚至损坏,影响航行安全,氟橡胶是指主链或侧链的碳原子上接有氟原子的一种合成高分子弹性体,具有耐热、耐油、耐溶剂、耐强氧化剂等特性,并具有良好的物理机械性能,所以被广泛应用到远洋船舶上,但随着技术的发展,单纯氟橡胶的耐盐雾腐蚀性能已无法满足船用橡胶件的使用需求。
技术实现要素:4.发明目的:针对上述使用需求,本发明提供了一种船用耐盐雾腐蚀橡胶材料及其制备方法。
5.所采用的技术方案如下:
6.一种船用耐盐雾腐蚀橡胶材料,包括以下组成成分:
7.全氟橡胶、端羧基液体氟橡胶、甲基乙烯基硅橡胶、氢化丁腈橡胶、无机纳米填料、不饱和脂肪酸改性碳纳米管、炭黑、交联剂、其余助剂。
8.进一步地,包括以下重量份数的组成成分:
9.全氟橡胶20-25份、端羧基液体氟橡胶5-10份、甲基乙烯基硅橡胶40-45份、氢化丁腈橡胶1-3份、无机纳米填料10-16份、不饱和脂肪酸改性碳纳米管10-15份、炭黑3-5份、交联剂0.5-1份、其余助剂0-1份。
10.进一步地,所述甲基乙烯基硅橡胶中乙烯基含量为1.8-5%。
11.进一步地,所述无机纳米填料为纳米高岭土、纳米蛭石、纳米膨润土、纳米蒙脱土、纳米氧化铝、纳米氧化镁、纳米氧化锌中的任意一种或多种组合。
12.进一步地,所述无机纳米填料为纳米高岭土和纳米氧化锌的组合。
13.进一步地,所述不饱和脂肪酸为亚油酸或亚麻酸。
14.进一步地,所述不饱和脂肪酸改性碳纳米管的制备方法如下:
15.s1:将碳纳米管加入由浓硫酸和浓硝酸组成的混酸中,升温至80-90℃超声振荡1-3h,滤出水洗后烘干;
16.s2:惰性气体保护下,将碳纳米管与不饱和脂肪酸于80-90℃混合1-3h后,滤出后
烘干。
17.进一步地,所述交联剂为主交联剂dcp和助交联剂taic组成。
18.进一步地,所述其余助剂包括抗氧剂、抗臭氧剂、抗屈挠龟裂剂、光稳定剂、紫外线吸收剂、有害金属抑制剂、防老剂、防白蚁剂、防鼠咬剂、防啃咬剂,防霉剂中的任意一种或多种组合。
19.上述船用耐盐雾腐蚀橡胶材料的制备方法:
20.将全氟橡胶、甲基乙烯基硅橡胶、氢化丁腈橡胶混合后塑炼,再与端羧基液体氟橡胶、无机纳米填料、不饱和脂肪酸改性碳纳米管、炭黑混合进行混炼,接着将交联剂和其余助剂加入,混炼均匀后薄通、打三角包下片,最后硫化即可。
21.本发明的有益效果:
22.全氟橡胶的热稳定性强、耐酸碱盐腐蚀,但是加工性能较差,而端羧基液体氟橡胶与全氟橡胶主链结构组成相近,二者具有良好的相容性,加入后能提高全氟橡胶的力学性能和加工性能等,盐雾作为一种含盐微小水滴,水的存在侵入橡胶材料内部,加剧盐雾腐蚀,而甲基乙烯基硅橡胶的加入可以引入硅原子,改善橡胶材料的耐水性能,从而提升耐盐雾腐蚀的能力,氢化丁腈橡胶是丁腈橡胶经过选择性加氢后成为具有饱和结构的特种材料,将氢化丁腈橡胶用于改性氟橡胶的报道并不鲜见,发明人经过测试,将氢化丁腈橡胶用于本发明对全氟橡胶进行改性,相互间有良好的接枝交联反应,可以提升交联效率,而且,甲基乙烯基硅橡胶和亚油酸改性碳纳米管的加入引入了不饱和键,在主交联剂dcp和助交联剂taic,结构中的不饱和键参与了橡胶材料的硫化过程,提高了橡胶材料的交联密度,改善了橡胶材料的耐盐雾腐蚀性能,经过测试,本发明所制备的橡胶材料具有良好的力学性能和耐盐雾腐蚀性能,且密度与海水接近,可以用于制作船用橡胶件,具有广阔的应用前景。
具体实施方式
23.实施例中未注明具体条件者,按照常规条件或制造商建议的条件进行。所用试剂或仪器未注明生产厂商者,均为可以通过市售购买获得的常规产品。
24.实施例1:
25.一种船用耐盐雾腐蚀橡胶材料,包括以下重量份数的组成成分:
26.全氟橡胶20份、端羧基液体氟橡胶8份、甲基乙烯基硅橡胶40份、氢化丁腈橡胶2份、无机纳米填料12份、亚油酸改性碳纳米管10份、炭黑3份、交联剂0.5份、抗氧剂1010 0.2份、紫外线吸收剂uv-531 0.1份。
27.其中,甲基乙烯基硅橡胶中乙烯基含量为1.8-5%。
28.无机纳米填料为纳米高岭土和纳米氧化锌质量比1:1的组合。
29.交联剂为主交联剂dcp和助交联剂taic按质量比5:2的组合。
30.亚油酸改性碳纳米管的制备方法如下:
31.将碳纳米管加入由浓硫酸和浓硝酸按质量比3:1组成的混酸中,升温至90℃超声振荡3h,滤出水洗至中性后烘干,氮气保护下,将碳纳米管与亚油酸于85℃混合搅拌2h,滤出后烘干。
32.上述船用耐盐雾腐蚀橡胶材料的制备方法:
33.将全氟橡胶、甲基乙烯基硅橡胶、氢化丁腈橡胶混合后塑炼,再与端羧基液体氟橡胶、无机纳米填料、亚油酸改性碳纳米管、炭黑混合进行混炼,接着将交联剂、抗氧剂1010、紫外线吸收剂uv-531加入,混炼均匀后薄通8次、打三角包下片,再于液压平板硫化机上进行一段硫化,硫化温度为170℃,硫化压力为15mpa,硫化时间为8min,最后于常压下220℃二段硫化5h。
34.实施例2:
35.一种船用耐盐雾腐蚀橡胶材料,包括以下重量份数的组成成分:
36.全氟橡胶25份、端羧基液体氟橡胶5份、甲基乙烯基硅橡胶45份、氢化丁腈橡胶1份、无机纳米填料16份、亚油酸改性碳纳米管15份、炭黑3份、交联剂0.5份、抗氧剂1010 0.2份、紫外线吸收剂uv-531 0.1份。
37.其中,甲基乙烯基硅橡胶中乙烯基含量为1.8-5%。
38.无机纳米填料为纳米高岭土和纳米氧化锌质量比1:1的组合。
39.交联剂为主交联剂dcp和助交联剂taic按质量比5:2的组合。
40.亚油酸改性碳纳米管的制备方法如下:
41.将碳纳米管加入由浓硫酸和浓硝酸按质量比3:1组成的混酸中,升温至90℃超声振荡1h,滤出水洗至中性后烘干,氮气保护下,将碳纳米管与亚油酸于90℃混合1h后,滤出后烘干。
42.上述船用耐盐雾腐蚀橡胶材料的制备方法:
43.将全氟橡胶、甲基乙烯基硅橡胶、氢化丁腈橡胶混合后塑炼,再与端羧基液体氟橡胶、无机纳米填料、亚油酸改性碳纳米管、炭黑混合进行混炼,接着将交联剂、抗氧剂1010、紫外线吸收剂uv-531加入,混炼均匀后薄通10次、打三角包下片,再于液压平板硫化机上进行一段硫化,硫化温度为175℃,硫化压力为15mpa,硫化时间为10min,最后于常压下230℃二段硫化6h。
44.实施例3:
45.一种船用耐盐雾腐蚀橡胶材料,包括以下重量份数的组成成分:
46.全氟橡胶25份、端羧基液体氟橡胶5份、甲基乙烯基硅橡胶45份、氢化丁腈橡胶1份、无机纳米填料10份、亚油酸改性碳纳米管10份、炭黑3份、交联剂0.5份、抗氧剂1010 0.2份、紫外线吸收剂uv-531 0.1份。
47.其中,甲基乙烯基硅橡胶中乙烯基含量为1.8-5%。
48.无机纳米填料为纳米高岭土和纳米氧化锌质量比1:1的组合。
49.交联剂为主交联剂dcp和助交联剂taic按质量比5:2的组合。
50.亚油酸改性碳纳米管的制备方法如下:
51.将碳纳米管加入由浓硫酸和浓硝酸按质量比3:1组成的混酸中,升温至80℃超声振荡1h,滤出水洗至中性后烘干,氮气保护下,将碳纳米管与亚油酸于80℃混合1h后,滤出后烘干。
52.上述船用耐盐雾腐蚀橡胶材料的制备方法:
53.将全氟橡胶、甲基乙烯基硅橡胶、氢化丁腈橡胶混合后塑炼,再与端羧基液体氟橡胶、无机纳米填料、亚油酸改性碳纳米管、炭黑混合进行混炼,接着将交联剂、抗氧剂1010、紫外线吸收剂uv-531加入,混炼均匀后薄通6次、打三角包下片,再于液压平板硫化机上进
行一段硫化,硫化温度为170℃,硫化压力为10mpa,硫化时间为8min,最后于常压下200℃二段硫化4h。
54.实施例4:
55.一种船用耐盐雾腐蚀橡胶材料,包括以下重量份数的组成成分:
56.全氟橡胶20份、端羧基液体氟橡胶10份、甲基乙烯基硅橡胶45份、氢化丁腈橡胶3份、无机纳米填料16份、亚油酸改性碳纳米管15份、炭黑5份、交联剂1份、抗氧剂1010 0.2份、紫外线吸收剂uv-531 0.1份。
57.其中,甲基乙烯基硅橡胶中乙烯基含量为1.8-5%。
58.无机纳米填料为纳米高岭土和纳米氧化锌质量比1:1的组合。
59.交联剂为主交联剂dcp和助交联剂taic按质量比5:2的组合。
60.亚油酸改性碳纳米管的制备方法如下:
61.将碳纳米管加入由浓硫酸和浓硝酸按质量比3:1组成的混酸中,升温至90℃超声振荡3h,滤出水洗至中性后烘干,氮气保护下,将碳纳米管与亚油酸于90℃混合3h后,滤出后烘干。
62.上述船用耐盐雾腐蚀橡胶材料的制备方法:
63.将全氟橡胶、甲基乙烯基硅橡胶、氢化丁腈橡胶混合后塑炼,再与端羧基液体氟橡胶、无机纳米填料、亚油酸改性碳纳米管、炭黑混合进行混炼,接着将交联剂、抗氧剂1010、紫外线吸收剂uv-531加入,混炼均匀后薄通10次、打三角包下片,再于液压平板硫化机上进行一段硫化,硫化温度为175℃,硫化压力为15mpa,硫化时间为10min,最后于常压下230℃二段硫化6h。
64.实施例5:
65.一种船用耐盐雾腐蚀橡胶材料,包括以下重量份数的组成成分:
66.全氟橡胶20份、端羧基液体氟橡胶5份、甲基乙烯基硅橡胶45份、氢化丁腈橡胶1份、无机纳米填料16份、亚麻酸改性碳纳米管10份、炭黑5份、交联剂0.5份、抗氧剂1010 0.2份、紫外线吸收剂uv-531 0.1份。
67.其中,甲基乙烯基硅橡胶中乙烯基含量为1.8-5%。
68.无机纳米填料为纳米高岭土和纳米氧化锌质量比1:1的组合。
69.交联剂为主交联剂dcp和助交联剂taic按质量比5:2的组合。
70.亚麻酸改性碳纳米管的制备方法如下:
71.将碳纳米管加入由浓硫酸和浓硝酸按质量比3:1组成的混酸中,升温至90℃超声振荡1h,滤出水洗至中性后烘干,氮气保护下,将碳纳米管与亚麻酸于90℃混合1h后,滤出后烘干。
72.上述船用耐盐雾腐蚀橡胶材料的制备方法:
73.将全氟橡胶、甲基乙烯基硅橡胶、氢化丁腈橡胶混合后塑炼,再与端羧基液体氟橡胶、无机纳米填料、亚麻酸改性碳纳米管、炭黑混合进行混炼,接着将交联剂、抗氧剂1010、紫外线吸收剂uv-531加入,混炼均匀后薄通10次、打三角包下片,再于液压平板硫化机上进行一段硫化,硫化温度为170℃,硫化压力为15mpa,硫化时间为8min,最后于常压下230℃二段硫化4h。
74.对比例1:
75.与实施例1基本相同,区别在于,组成成分中不含端羧基液体氟橡胶。
76.对比例2:
77.与实施例1基本相同,区别在于,组成成分中不含甲基乙烯基硅橡胶。
78.对比例3:
79.与实施例1基本相同,区别在于,组成成分中不含氢化丁腈橡胶。
80.对比例4:
81.与实施例1基本相同,区别在于,将组成成分中的亚麻酸改性碳纳米管用碳纳米管代替。
82.性能测试:
83.将按照本发明实施例1-5及对比例1-4配方及方法所制备的橡胶材料作为试样进行性能测试。
84.拉伸强度与拉断伸长率:按照gb/t 528-2009进行测试。
85.耐磨性能:按照gb/t1689-1998进行测试。
86.撕裂强度:按照gb/t529-2008进行测试。
87.测试结果如下表1所示:
88.表1:
[0089][0090]
耐盐雾腐蚀性能:按照gb/t35858-2018进行测试,实验温度为35℃,盐雾溶液为5%浓度的氯化钠溶液,试验样品在盐雾中停放7d。
[0091]
测试结果如下表2所示:
[0092]
其中“+”代表增加,
“‑”
代表降低;
[0093]
表2:
[0094][0095]
由上表1可知,本发明所制备的橡胶材料具有良好的力学性能,且通过对比可知,端羧基液体氟橡胶、甲基乙烯基硅橡胶、氢化丁腈橡胶、不饱和脂肪酸改性碳纳米管的加入,对于提升橡胶材料的力学性能起到了积极作用;
[0096]
由上表2可知,本发明所制备的橡胶材料具有良好的耐盐雾腐蚀,且通过对比可知,端羧基液体氟橡胶、甲基乙烯基硅橡胶、氢化丁腈橡胶、不饱和脂肪酸改性碳纳米管的加入,对于提升橡胶材料的耐盐雾腐蚀性能起到了积极作用,尤其是甲基乙烯基硅橡胶和不饱和脂肪酸改性碳纳米管的加入,由于结构中的不饱和键参与了橡胶材料的硫化过程,提高了橡胶材料的交联密度,起到了改善耐盐雾腐蚀性能的作用。
[0097]
以上实施例仅用以说明本发明的技术方案,而非对其限制;尽管参照前述实施例对本发明进行了详细的说明,本领域的普通技术人员应当理解:其依然可以对前述各实施例所记载的技术方案进行修改,或者对其中部分技术特征进行等同替换;而这些修改或者替换,并不使相应技术方案的本质脱离本发明各实施例技术方案的精神和范围。