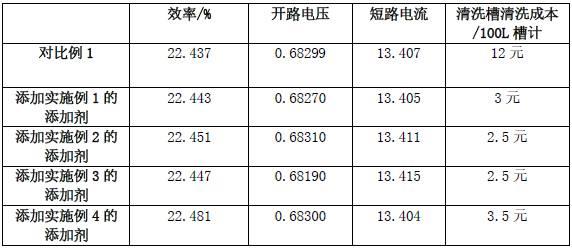
一种硅片清洗用添加剂、清洗液及硅片制绒后清洗方法
1.技术领域:本发明涉及硅片清洗技术领域,具体涉及一种用于硅片制绒后清洗的添加剂、清洗液以及硅片制绒后清洗方法。
2.
背景技术:在太阳能单晶电池的生产过程中,制绒是其中一道重要的工艺,在制绒工艺中需要使用制绒添加剂,若制绒添加剂在制绒工序完成后有残留,则会影响电池片的效率和良率,因此需要再制绒后再添加一步清洗工序。
3.在目前的制绒后清洗工序中,一般采用双氧水和碱的混合液来实现制绒液和脏污的去除,其中双氧水提供氧化作用分解硅片表面吸附的有机物,碱可以增强双氧水的氧化性,在制绒后清洗过程中需要不断补充碱和双氧水,以保证清洗的效果。因此需要用到大量的双氧水和碱进行清洗操作,具有以下缺点:(1)使得电池片生产成本较高;(2)碱和双氧水对自然环境都具备较大的危害性,在废水处理过程中需要特别处理,一旦有处理不当,极易产生环境问题,危害自然水体和土壤;(3)碱和双氧水的后清洗效果并不理想,制约了硅片做成电池后的效率提升。
4.
技术实现要素:本发明的目的是针对现有技术的缺陷,提供一种硅片清洗用添加剂、清洗液以及硅片制绒后清洗方法,可以减少碱和双氧水的用量,并提高单晶电池效率。
5.实现本发明目的的技术方案是:一种硅片清洗用添加剂,其各组分的质量百分含量为:3%-5%的软水剂、3%-6%的氧化剂、0.01%-0.05%的低泡耐碱渗透剂、1%-3%的缓冲剂,余量为水;其中,所述氧化剂选自于由次氯酸钠、亚氯酸钠、高氯酸钠以及过硼酸钠所组成的群组,所述低泡耐碱渗透剂为磺酸盐类表面活性剂。
6.在一些实施例中,所述氧化剂包括次氯酸钠和亚氯酸钠,所述次氯酸钠占所述添加剂的质量百分比为2%-3%,所述亚氯酸钠占所述添加剂的质量百分比为1%-3%。次氯酸钠和亚氯酸钠复配的氧化剂可提高清洗效率。
7.在一些实施例中,所述软水剂选自于由硬脂酸钠和乙二胺四乙酸二钠所组成的群组。
8.在一些实施例中,所述缓冲剂选自于由硫酸钠、硅酸钠以及乙酸钠所组成的群组。
9.本技术还提供了一种硅片清洗液,包括碱和双氧水的混合溶液以及如上所述的硅片清洗用添加剂,其中所述碱和双氧水的混合溶液和所述硅片清洗用添加剂的质量比为100:0.2-0.5。
10.在一些实施例中,所述碱和双氧水的混合溶液中,含有质量百分比为0.9%-1.5%的双氧水以及质量百分比为0.06%-0.1%的氢氧化钠或氢氧化钾。
11.本技术还提供了一种硅片制绒后清洗方法,包括以下步骤:s1、将质量百分比为3%-5%的软水剂、3%-6%的氧化剂、0.01%-0.05%的低泡耐碱渗透剂、1%-3%的缓冲剂加入到余量的水中;混合均匀配置成硅片清洗用添加剂;其中,所述氧化剂选自于由次氯酸钠、亚氯酸钠、高氯酸钠以及过硼酸钠所组成的群组,所述低泡耐碱渗
透剂为磺酸盐类表面活性剂;s2、将步骤s1中配制好的硅片清洗用添加剂加入到碱和双氧水的混合溶液中,混合均匀配置成硅片清洗液;其中,所述硅片清洗用添加剂与所述碱和双氧水的混合溶液的质量比为0.2-0.5:100;所述碱和双氧水的混合溶液中的碱采用氢氧化钠或氢氧化钾。
12.s3、将硅片放入到步骤s2配置好的所述硅片清洗液中,控制清洗温度为60-70℃,清洗时间为150s-200s;之后,在水中浸泡180s-200s,完成清洗。
13.在一些实施例中,所述步骤s1中,所述氧化剂包括次氯酸钠和亚氯酸钠,所述次氯酸钠占所述添加剂的质量百分比为2%-3%,所述亚氯酸钠占所述添加剂的质量百分比为1%-3%。
14.在一些实施例中,所述步骤s2中,所述碱和双氧水的混合溶液中含有质量百分比为0.9%-1.5%的双氧水以及质量百分比为0.06%-0.1%的碱。
15.在一些实施例中,所述步骤s3中,清洗温度为65-70℃,清洗时间为180s-200s。
16.本发明的有益效果在于:(1)本发明提供了一种硅片清洗用添加剂、清洗液以及硅片制绒后清洗方法,通过在清洗液中添加本发明的添加剂,达到减少碱和双氧水用量的目的。实际生产中,能够降低二者80%耗量,大幅度降低了成本,且清洁更彻底,能够提高单晶电池效率0.01%-0.05%。在降低生产成本的同时,也降低了污水处理的成本,避免了对自然水体、土壤的污染。(2)本发明中的软水剂,可以降低水的硬度,帮助控制清洗过程中泡沫的产生,并对清洗效果有促进作用。氧化剂为硅片清洗用添加剂提供氧化性,可以对硅片表面油脂氧化分解,有助于剥离硅片表面的有机脏污成分。缓冲剂为添加剂的碱性提供缓冲作用,可以增强清洗效果,同时缓冲剂也具有稳定泡沫的作用。低泡耐碱渗透剂可以在碱性条件下拥有较好润湿性和渗透性,并且清洗过程中泡沫少,在硅片表面无吸附,这使得硅片在后清洗工序中不但制绒液等有机物可以完全去除,硅片清洗用添加剂本身在硅片表面也完全零吸附,为单晶电池片的效率提升提供了可能。此外,添加剂整体呈碱性,但用量较传统碱加双氧水的清洗降低了约80%,后续的污水处理成本大大下降。
17.具体实施方式:下面对本发明的较佳实施例进行详细阐述,以使本发明的优点和特征能更易被本领域人员理解,从而对本发明的保护范围做出更为清楚明确的界定。
18.实施例1一种硅片清洗用添加剂,其各组分的质量百分含量为:3%的软水剂、4%的氧化剂、0.05%的低泡耐碱渗透剂、1%的缓冲剂,余量为水。
19.其中,所述软水剂为硬脂酸钠,所述氧化剂包括次氯酸钠和亚氯酸钠。所述次氯酸钠占所述添加剂的质量百分比为3%,所述亚氯酸钠占所述添加剂的质量百分比为1%,所述低泡耐碱渗透剂为磺酸盐类表面活性剂,所述缓冲剂为硫酸钠。
20.实施例2一种硅片清洗用添加剂,其各组分的质量百分含量为:4%的软水剂、5%的氧化剂、0.03%的低泡耐碱渗透剂、2%的缓冲剂,余量为水。
21.其中,所述软水剂为硬脂酸钠,所述氧化剂包括次氯酸钠和亚氯酸钠,所述次氯酸钠占所述添加剂的质量百分比为2%,所述亚氯酸钠占所述添加剂的质量百分比为3%,所述
低泡耐碱渗透剂为磺酸盐类表面活性剂,所述缓冲剂为硫酸钠。
22.实施例3一种硅片清洗用添加剂,其各组分的质量百分含量为:5%的软水剂、3%的氧化剂、0.01%的低泡耐碱渗透剂、3%的缓冲剂,余量为水。
23.其中,所述软水剂为乙二胺四乙酸二钠,所述氧化剂包括次氯酸钠和高氯酸钠,所述次氯酸钠占所述添加剂的质量百分比为2%,所述亚氯酸钠占所述添加剂的质量百分比为1%,所述低泡耐碱渗透剂为磺酸盐类表面活性剂,所述缓冲剂为硅酸钠。
24.实施例4一种硅片清洗用添加剂,其各组分的质量百分含量为:3.5%的软水剂、6%的氧化剂、0.02%的低泡耐碱渗透剂、3%的缓冲剂,余量为水。
25.其中,所述软水剂为硬脂酸钠和乙二胺四乙酸二钠的混合物,所述氧化剂包括亚氯酸钠和过硼酸钠,所述亚氯酸钠占所述添加剂的质量百分比为3%,所述过硼酸钠占所述添加剂的质量百分比为3%,所述低泡耐碱渗透剂为磺酸盐类表面活性剂,所述缓冲剂为乙酸钠。
26.实施例5一种硅片清洗液,包括碱和双氧水的混合溶液以及实施例1所述的硅片清洗用添加剂。其中所述碱和双氧水的混合溶液和所述硅片清洗用添加剂的质量比为100:0.2。
27.所述碱和双氧水的混合溶液中,含有质量百分比为0.9%-1.5%(比如0.9%、1%、1.3%、1.5%)的双氧水以及质量百分比为0.06%-0.1%(比如0.06%、0.07%、0.09%、0.1%)的碱,其中碱为氢氧化钠。
28.实施例6与实施例5不同的是,所述的添加剂为实施例2的硅片清洗用添加剂,所述碱和双氧水的混合溶液和所述硅片清洗用添加剂的质量比为100:0.3,碱为氢氧化钾。
29.实施例7与实施例5不同的是,所述的添加剂为实施例3的硅片清洗用添加剂,所述碱和双氧水的混合溶液和所述硅片清洗用添加剂的质量比为100:0.5,碱为氢氧化钾。
30.实施例8与实施例5不同的是,所述的添加剂为实施例4的硅片清洗用添加剂,所述碱和双氧水的混合溶液和所述硅片清洗用添加剂的质量比为100:0.5,碱为氢氧化钠。
31.实施例9一种硅片制绒后清洗方法,包括以下步骤:s1、将质量百分比为3%-5%的软水剂、3%-6%的氧化剂、0.01%-0.05%的低泡耐碱渗透剂、1%-3%的缓冲剂加入到余量的水中;混合均匀配置成硅片清洗用添加剂;其中,所述氧化剂选自于由次氯酸钠、亚氯酸钠、高氯酸钠以及过硼酸钠所组成的群组,所述低泡耐碱渗透剂为磺酸盐类表面活性剂;s2、将步骤s1中配制好的硅片清洗用添加剂加入到碱和双氧水的混合溶液中,混合均匀配置成硅片清洗液;其中,所述硅片清洗用添加剂与所述碱和双氧水的混合溶液的质量比为0.2-0.5:100;所述碱和双氧水的混合溶液中碱采用氢氧化钠或氢氧化钾。
32.s3、将硅片放入到步骤s2配置好的所述硅片清洗液中,控制清洗温度为60-70℃,
清洗时间为150s-200s;之后,再在水中浸泡180s-200s,完成清洗。
33.所述步骤s1中,所述氧化剂包括次氯酸钠和亚氯酸钠,所述次氯酸钠占所述添加剂的质量百分比为2%-3%,所述亚氯酸钠占所述添加剂的质量百分比为1%-3%。
34.所述步骤s2中,所述碱和双氧水的混合溶液中含有质量百分比为0.9%-1.5%的双氧水以及质量百分比为0.06%-0.1%的碱。
35.所述步骤s3中,清洗温度为65-70℃,清洗时间为180s-200s。
36.对比例1采用碱和双氧水的混合溶液对制绒后的硅片进行清洗,所述碱和双氧水的混合溶液中,含有质量百分比为0.9%-1.5%的双氧水以及质量百分比为0.06%-0.1%的碱,碱为氢氧化钠或氢氧化钾。
37.使用对比例1的清洗液以及添加实施例1-4的添加剂的清洗液分别对制绒后的硅片按本技术以同样的工序进行清洗,结果见表1。
38.表1通过性能测试结果显示,在制绒后清洗工序中采用本发明实施例1-4的添加剂后,相对于对比例,清洗效果并没有下降,甚至电池效率普遍有0.01%-0.05%的提升。同时能够降低碱和双氧水的80%耗量,大幅度降低了成本。
39.以上所述实施例仅表达了本发明的几种实施方式,其描述较为具体和详细,但并不能因此而理解为对发明专利范围的限制。应当指出的是,对于本领域的普通技术人员来说,在不脱离本发明构思的前提下,还可以做出若干变形和改进,这些都属于本发明的保护范围。