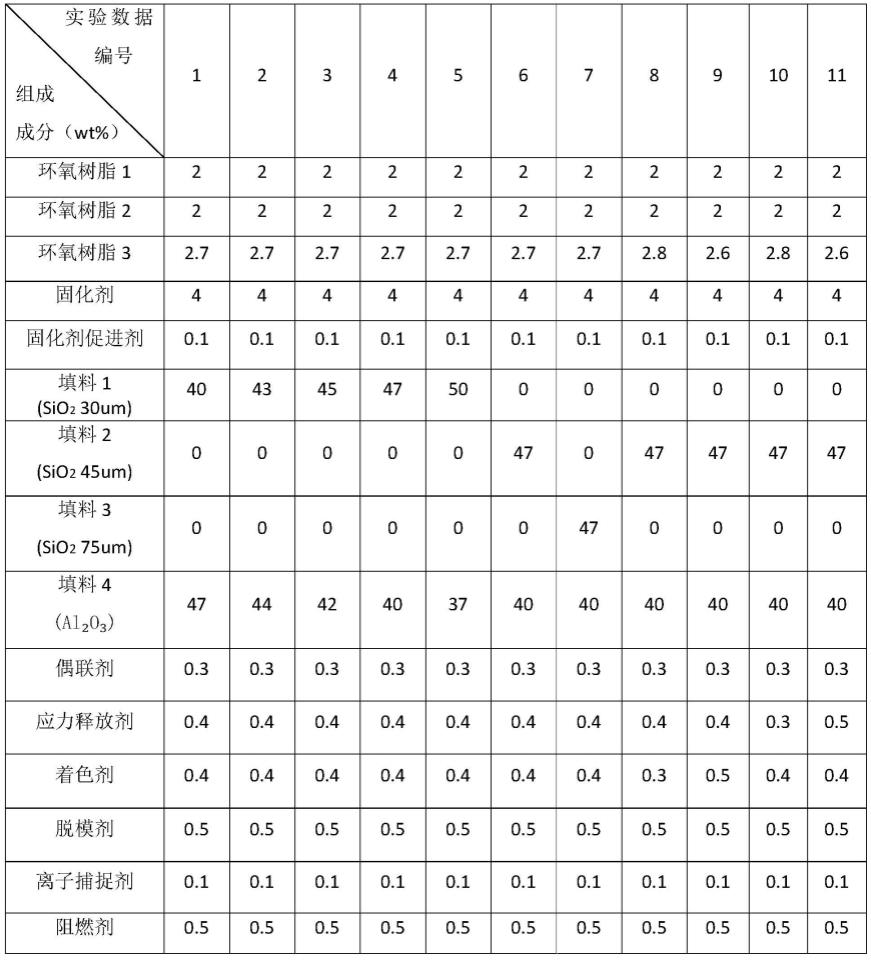
1.本发明涉及电子封装材料技术领域,具体为一种环氧塑封料组合物、制备方法及应用。
背景技术:2.环氧树脂是一种热固性树脂,优异的作业性和稳定的可靠性使其在电子制造业的应用越来越广,尤其是电子封装领域,如粘接银胶、印刷电路板、塑封料饼等。其中,以多官能团型环氧树脂、杂环型环氧树脂及酯环型环氧树脂作为主要的树脂成分,酚醛树脂作为固化剂、二氧化硅作为填充剂、金属氢氧化物和磷系化合物作为阻燃剂,以及适量的偶联剂、脱模剂、应力释放剂等各种其他添加剂构成的环氧树脂塑封料饼,在当今的集成电路封装领域处于不可或缺的地位。
3.随着芯片制程的摩尔定律逐渐消失,提高芯片算力需要增加芯片的运算频率,使得单位功耗不断增加,伴随而来的局部区域发热将导致芯片失效,这一痛点一直困扰着当今的微电子应用领域。传统商业芯片为避免局部发热,一般都会在器件表面黏附散热措施,如覆盖散热石墨、贴合铜质散热片等,但是这些手法会增加产品厚度,影响商业电子产品的实际使用感受。
4.而随着消费电子轻量化、芯片算力的提升,为了给电池留下空间,常规封装的厚度必将趋向轻薄化以及具备高散热能力,且随着封装厚度的降低,常规封装料饼存在着散热能力不足、堵塞bump、芯片表面胶体开裂、胶体黑度不足造成泛白及透光等风险,因此为适应当今消费电子轻薄化的发展趋势,保证内置芯片性能的完美体现,亟需开发一种应用于超薄封装的高散热技术,其中需要注意的是,在封装技术领域,按厚度条件分类,封装结构分为超薄封装结构、薄封装结构、常规封装结构,其中,超薄封装结构的厚度范围为:厚度≤0.37mm,薄封装结构的厚度范围为:0.37mm<厚度<0.45mm,常规封装结构的厚度范围为:厚度≥0.45mm。
技术实现要素:5.本发明的目的在于克服现有环氧塑封料组合物存在着散热能力不足、堵塞bump、芯片表面胶体开裂、胶体黑度不足造成泛白及透光等风险,提供了一种环氧塑封料组合物、制备方法及应用。
6.为了实现上述目的,本发明提供一种环氧塑封料组合物,包含填料、应力释放剂、着色剂,所述填料包括氧化铝和氧化硅,所述氧化硅的质量分数为45wt%-50wt%,所述氧化铝的质量分数为37wt%-42wt%,所述应力释放剂的质量分数范围为0.3wt%-0.5wt%,所述着色剂的质量分数范围为0.3wt%-0.5wt%。
7.作为一种可实施方式,所述应力释放剂的质量分数为0.4wt%,所述着色剂的质量分数为0.4wt%。
8.作为一种可实施方式,所述填料中填料粒子的最大尺寸根据后续进行封装的芯片
上凸点之间的间距确定,从而防止当根据制备得到的胶体进行塑封时,填料粒子造成凸点之间堵塞使得胶体不能注入;所述填料中填料粒子的最小尺寸根据后续进行封装时使用的胶体排气槽的口径确定,从而防止所述胶体排气槽边缘出现溢胶。
9.作为一种可实施方式,当芯片上凸点之间的间距为135μm时,设定所述填料中填料粒子的最大尺寸为45μm,设定所述填料中填料粒子的最小尺寸为38μm。
10.作为一种可实施方式,还包含环氧树脂、固化剂、固化促进剂、偶联剂和辅助添加剂,其中,所述环氧树脂的质量分数范围为4wt%-9wt%,所述固化剂的质量分数范围为:4wt%-9wt%;所述固化促进剂的质量范围为0.02wt%-0.5wt%,所述偶联剂的质量分数范围为0.05wt%-0.5wt%,所述辅助添加剂的质量分数范围为1wt%-2wt%。
11.作为一种可实施方式,所述应力释放剂选自液体硅油、聚硅氧烷橡胶粉末、有机硅改性环氧树脂中的任意一种或几种;所述着色剂选自炭黑、钛白粉、油溶苯胺黑、氧化锌中的任意一种或几种。
12.作为一种可实施方式,所述环氧树脂选自邻甲酚醛环氧树脂、脂肪族缩水甘油醚环氧树脂、多酚型缩水甘油醚环氧树脂、缩水甘油酯型环氧树脂、缩水甘油胺型环氧树脂、双联苯型环氧树脂、双酚a型环氧树脂、双酚f型环氧树脂、脂环族环氧树脂、杂环型环氧树脂中的任意一种或几种。
13.作为一种可实施方式,所述固化剂选自苯酚线性酚醛树脂及其衍生物、苯甲酚线性酚醛树脂及其衍生物、单羟基或二羟基萘酚醛树脂、联苯型酚醛树脂、芳烷基苯酚型环氧树脂及其衍生物中的任意一种或几种;所述固化促进剂选自咪唑化合物及其盐类化合物。
14.作为一种可实施方式,所述偶联剂选自环氧硅烷偶联剂、氨基硅烷偶联剂、巯基硅烷偶联剂中的任意一种或几种。
15.作为一种可实施方式,所述应力释放剂选自液体硅油、聚硅氧烷橡胶粉末、有机硅改性环氧树脂中的任意一种或几种;所述着色剂选自炭黑、钛白粉、油溶苯胺黑、氧化锌中的任意一种或几种。
16.作为一种可实施方式,所述辅助添加剂包含脱模剂、阻燃剂及离子捕捉剂;脱模剂选自硬酯酸、氧化型或非氧化型聚乙烯蜡、蒙旦蜡、费托蜡中的任意一种或几种;阻燃剂选自硼酸盐、钼酸盐、水合金属氢氧化物中的任意一种或几种;离子捕捉剂选自酸性金属盐,铝镁的化合物等含水氧化物中的一种或几种。
17.相应的,本发明还提供一种环氧塑封料组合物的制造方法,包括以下步骤:
18.将环氧树脂、填料、着色剂、阻燃剂、离子捕捉剂、应力释放剂进行混合得到混合物a,其中,所述填料包括氧化铝和氧化硅,所述氧化硅的质量分数为45wt%-50wt%,所述氧化铝的质量分数为37wt%-42wt%,所述应力释放剂的质量分数范围为0.3wt%-0.5wt%,所述着色剂的质量分数范围为0.3wt%-0.5wt%;
19.向所述混合物a中添加固化促进剂、固化剂、偶联剂、脱模剂获得混合物b;
20.将所述混合物b加入至预设温度的注塑机中挤出,挤出后冷却,再进行粉碎打饼,得到所述环氧塑封料组合物。
21.相应的,本发明还提供一种环氧塑封料组合物在半导体元器件封装中的应用。
22.本发明的有益效果:本发明实施例提供了一种环氧塑封料组合物、制备方法及应用,通过使用高散热环氧塑封料组合物封装芯片,替代传统的器件表面黏附散热措施,使得
倒装qfn产品具有更薄的封装尺寸和更好的散热性能;通过调节合理的填料比例获得了具有高散热料饼,并通过调整填料颗粒尺寸,使其满足倒装qfn的完全填充要求和防止溢胶要求;此外,设计合理的应力释放剂及着色剂含量,保证了器件整体的可靠性和保密性要求。
附图说明
23.图1为本发明实施例实验数据4得到的塑封料组合物对应的溢胶效果图;
24.图2为本发明实施例实验数据6得到的塑封料组合物对应的不溢胶效果图;
25.图3为本发明实施例实验数据8得到的塑封料组合物对应的泛白效果图;
26.图4为本发明实施例实验数据6对应的芯片区域的不分层效果图;
27.图5为本发明实施例实验数据6对应的引脚区域的不分层效果图;
28.图6为本发明实施例实验数据7对应的出现空腔时的效果图;
29.图7为本发明实施例实验数据10对应的分层效果图;
30.图8为本发明实施例实验数据11对应的粘膜效果图。
具体实施方式
31.下面将结合本发明实施例中的附图,对本发明实施例中的技术方案进行清楚、完整地描述,显然,所描述的实施例仅仅是本发明一部分实施例,而不是全部的实施例。基于本发明中的实施例,本领域普通技术人员在没有做出创造性劳动前提下所获得的所有其他实施例,都属于本发明保护的范围。
32.本实施例提供一种技术方案:一种环氧塑封料组合物,包含填料、应力释放剂、着色剂,所述填料包括氧化铝和氧化硅,所述氧化硅的质量分数为45wt%-50wt%,所述氧化铝的质量分数为37wt%-42wt%,所述应力释放剂的质量分数范围为0.3wt%-0.5wt%,所述着色剂的质量分数范围为0.3wt%-0.5wt%。
33.其中,需要注意的是,本发明实施例是对现有环氧塑封料组合物中的部分成分做出了改进,从而在使用组合形成的塑封料进行塑封后有更好的效果,其中,所述应力释放剂的质量分数范围为0.3wt%-0.5wt%和所述着色剂的质量分数范围为0.3wt%-0.5wt%中的0.3wt%-0.5wt%都表示大于0.3wt%小于0.5wt%的一个范围,即可以为0.35wt%、0.4wt%、0.45wt%等,但并不包括0.3wt%和0.5wt%。
34.所述氧化硅的质量分数45wt%-50wt%表示大于45wt%小于50wt%的一个范围,即该范围不包含45wt%和50wt%;所述氧化铝的质量分数为37wt%-42wt%表示大于37wt%小于42wt%的一个范围,即该范围不包含37wt%和42wt%。
35.在本实施例中,首先,针对超薄封装散热系数太低,不能满足内部器件的高散热需求,本实施例通过调整氧化铝和二氧化硅填料的比例,保证翘曲合理的情况下,实现高散热的需求,因此最终通过实验将填料中的氧化硅和氧化铝的质量分数范围分别配置为了45wt%-50wt%和37wt%-42wt%以实现效果;其次,针对超薄封装导致的胶体表面有透光、泛白的风险,本实施例通过调整着色剂的比例,实现对胶体泛白、透光以及导电异常的改善,因此最终通过实验将着色剂的质量分数范围配置为0.3wt%-0.5wt%;再者,针对超薄封装存在分层风险,本实施例通过调整应力释放剂的比例,改善对内部分层和脱模的影响,因此最终通过实验将应力释放剂的质量分数范围配置为0.3wt%-0.5wt%;然后,针对超薄
封装内部未全部填充导致出现内部气孔的问题,以及进行封装时使用的胶体排气槽附近出现溢胶的问题,本实施例根据实验将所述填料中填料粒子的最大尺寸根据后续进行封装的芯片上凸点之间的间距进行确定,从而防止当根据制备得到的胶体进行塑封时,填料粒子造成凸点之间堵塞使得胶体不能注入;所述填料中填料粒子的最小尺寸根据后续进行封装时使用的胶体排气槽的口径进行确定,从而防止所述胶体排气槽边缘出现溢胶,其中例如当芯片凸点之间的间距为135μm时,设定所述填料中填料粒子的最大尺寸为45μm,设定所述填料中填料粒子的最小尺寸为38μm,也就是说,填料粒子的尺寸要小于等于45μm大于等于38μm。
36.可选的,本实施例提供的环氧塑封料组合物还包含环氧树脂、固化剂、固化促进剂、偶联剂和辅助添加剂,其中,所述环氧树脂的质量分数范围为4wt%-9wt%,所述固化剂的质量分数范围为:4wt%-9wt%;所述固化促进剂的质量范围为0.02wt%-0.5wt%,所述偶联剂的质量分数范围为0.05wt%-0.5wt%,所述辅助添加剂的质量分数范围为1wt%-2wt%。
37.可选的,所述环氧树脂选自邻甲酚醛环氧树脂、脂肪族缩水甘油醚环氧树脂、多酚型缩水甘油醚环氧树脂、缩水甘油酯型环氧树脂、缩水甘油胺型环氧树脂、双联苯型环氧树脂、双酚a型环氧树脂、双酚f型环氧树脂、脂环族环氧树脂、杂环型环氧树脂中的任意一种或几种。
38.可选的,所述固化剂选自苯酚线性酚醛树脂及其衍生物、苯甲酚线性酚醛树脂及其衍生物、单羟基或二羟基萘酚醛树脂、联苯型酚醛树脂、芳烷基苯酚型环氧树脂及其衍生物中的任意一种或几种;所述固化促进剂选自咪唑化合物及其盐类化合物。
39.可选的,所述偶联剂选自环氧硅烷偶联剂、氨基硅烷偶联剂、巯基硅烷偶联剂中的任意一种或几种。
40.可选的,所述应力释放剂选自液体硅油、聚硅氧烷橡胶粉末、有机硅改性环氧树脂中的任意一种或几种;所述着色剂选自炭黑、钛白粉、油溶苯胺黑、氧化锌中的任意一种或几种。
41.可选的,所述辅助添加剂包含脱模剂、阻燃剂及离子捕捉剂;脱模剂选自硬酯酸、氧化型或非氧化型聚乙烯蜡、蒙旦蜡、费托蜡中的任意一种或几种;阻燃剂选自硼酸盐、钼酸盐、水合金属氢氧化物中的任意一种或几种;离子捕捉剂选自酸性金属盐,铝镁的化合物等含水氧化物中的一种或几种。
42.在本实施例中,为了解决常规环氧塑封料组合物散热能力不足、堵塞bump、芯片表面胶体开裂、胶体黑度不足造成泛白及透光等风险,本实施例根据多种实验数据,从而发现可以通过调整常规环氧塑封料组合物中氧化硅、氧化铝、应力释放剂、着色剂的相应质量分数以及填料粒子的尺寸,来解决相应的不同问题。
43.如表1所示,为作为例子的11组实验数据,其中每组实验数据都包含有以质量分数wt%为单位的环氧塑封料组合物中的不同成分;其中,环氧树脂1、环氧树脂2、环氧树脂3分别表示在环氧塑封料组合物中的不同环氧树脂种类,由于是现有材料,本实施例不详细列明;而填料1、填料2、填料3分别为最大尺寸分别为30μm、45μm、75μm的sio2,填料4为al2o3。
[0044][0045]
表1
[0046]
如表2所示为根据对应11组实验数据得到的环氧塑封料组合物进行可靠性验证、翘曲度验证和导入率验证的实验结果。其中,可靠性的验证方式可以为:使用towa的机台包封尺寸为3x3mm的倒装qfn产品,封装厚度0.37mm,温度条件为175℃,脱模后对产品进行后固化处理,175℃的条件保温4个小时,随后按ipc j-std-020c-2004要求,进行msl-1级别进行考核并使用超声波扫描内部分层情况。翘曲度的验证方式可以为:使用towa机台包封258x78的铜框架产品,包封厚度0.37mm,待后固化结束后,胶体朝上,测量胶体最高点与最低点的高度差异。导热率的验证方式可以为:将环氧树脂塑封料按照标准模具制备成相应样块,将样块放置在冷热板之间,经过一定时间后,测量两个板的温差,代入样块的厚度,计算出样品的热导率。
[0047][0048]
表2
[0049]
首先使用根据表1中编号为1、2、3、4、5的实验数据得到的环氧塑封料组合物进行塑封,验证的是氧化硅和氧化铝的在填料中的不同占比对封装结构的散热能力和翘曲的影响,根据表2所示,可以看出,当采用不同质量分数的氧化硅和氧化铝时,对塑封形成的封装结构的翘曲和导热率都存在较大影响;其中,实验数据编号为1、2、3的翘曲数值表示翘曲大,实验数据编号为4、5的翘曲数值表示翘曲小,实验数据编号为1、2、3、4的导热率数值表示导热率大即散热能力好,实验数据编号为5的导热率数值表示导热率小即散热能力差。
[0050]
因此,为了同时获取翘曲小而且散热能力好的效果,在多次实验验证后的最终实验结果中,本实施例得到了当氧化硅和氧化铝的质量分数范围分别为45wt%-50wt%和37wt%-42wt%时,其中,45wt%-50wt%表示大于45wt%小于50wt%的一个范围,37wt%-42wt%表示大于37wt%小于42wt%的一个范围;能够使得当根据制备得到的塑封料组合物进行封装后,翘曲小而且散热能力好。
[0051]
其次,使用根据表1实验编号为4、6、7的实验数据得到的环氧塑封料组合物进行塑封,验证的是对内部填充的影响,当芯片凸点之间的间距为135μm,根据表2可以看出,通过选用最大尺寸分别为30μm、45μm、75μm的填料粒子时,30μm会产生溢胶的效果,75μm会产生bump堵塞即芯片凸点堵塞的效果,即当根据制备得到的胶体进行塑封时,大颗填料粒子堵塞胶体流通通道使得胶体不能注入,导致产品内部未填充,出现空腔,而45μm不会产生溢胶也不会出现空腔;如图1所示即实验数据4的溢胶效果图,可以看出胶体排气槽边缘电镀后还存在很多的溢胶,而溢胶的原因是填料粒子的尺寸小于胶体排气槽的口径导致胶体溢出,溢胶的存在会导致包封模具的堵塞,影响连续作业性,如图2所示为实验数据6对应的效
果图,可以看出胶体边缘没有出现溢胶,而且胶体表面平整,没有出现过大的翘曲;如图6所示为对应实验数据7的出现空腔的效果图,而出现空腔的原因是填料粒子太大堵塞胶体流通通道导致。
[0052]
因此,为了同时得到不溢胶和不堵塞的效果,在多次实验验证后的最终实验结果中,得到可以根据进行封装的芯片上凸点之间的间距确定所述填料中填料粒子的最大尺寸从而解决内部未全部填充,导致出现内部气孔的问题,根据后续进行封装时使用的胶体排气槽的口径确定填料中填料粒子的最小尺寸,从而防止所述胶体排气槽边缘出现溢胶;其中由于本实施例中使用的芯片凸点之间的间距为135μm,因此得出了将填料粒子的最大尺寸设定为45μm的结论,同时为了防止溢胶,设定填料粒子的最小尺寸为38μm,也就是说,填料粒子的尺寸要小于等于45μm
×
45μm大于等于38μm
×
38μm。
[0053]
再者,使用根据表1实验编号为6、8、9的实验数据得到的环氧塑封料组合物进行塑封,验证的是着色剂对胶体泛白、透光以及导电异常的改善,根据表2可以看出,通过选用着色剂的质量分数分别为0.3wt%、0.4wt%、0.5wt%时,得到的是当着色剂为0.3wt%时,出现了泛白和透光的效果,而当着色剂为0.4wt%或者0.5wt%时,得到的是不泛白的效果,但是当着色剂为0.5wt%时出现的是导电异常的问题;如图3所示即为实验数据8的泛白效果图,可以看出胶体表面泛白,反射率过强,影响marking即做标记的作业。
[0054]
因此为了解决泛白、透光及导电异常的问题,在多次实验验证后的最终实验结果中,得到可以将着色剂的质量分数范围配置为0.3wt%-0.5wt%,其中,0.3wt%-0.5wt%范围不包括0.3wt%和0.5wt%,但可以包含0.35wt%、0.45wt%等。
[0055]
接着使用根据表1实验编号为6、10、11的实验数据得到的环氧塑封料组合物进行塑封,验证的是应力释放剂对内部分层和脱模的影响,可以看出,通过选用应力释放剂的质量分数分别为0.4wt%、0.3wt%、0.5wt%时,得到的是当着色剂为0.3wt%时,出现了分层的效果,当应力释放剂为0.4wt%得到的是不分层、不粘膜的效果,当应力释放剂为0.5wt%时,得到的是粘膜的效果,如图4和图5所示即为实验数据6对应的芯片和引脚区域的不分层的效果图,如图7所示即为实验数据10对应的分层的效果图,如图8所示即为实验数据11对应的粘膜的效果图,可以看出胶体黏附模具上表面,导致脱模困难和胶体表面破损。
[0056]
因此为了解决内部分层和脱模的问题,在多次实验验证后的在最终实验结果中,得到可以将应力释放剂的质量分数范围配置为0.3wt%-0.5wt%,其中,0.3wt%-0.5wt%范围不包括0.3wt%和0.5wt%,但可以包含0.35wt%、0.45wt%等。
[0057]
本发明实施例提供了一种高散热环氧塑封料组合物,使用高散热环氧塑封料组合物封装芯片,替代传统的器件表面黏附散热措施,使得倒装qfn产品具有更薄的封装尺寸和更好的散热性能。
[0058]
本发明实施例通过调节合理的填料比例获得了具有高散热料饼,并通过调整填料颗粒尺寸,使其满足倒装qfn的完全填充要求和防止溢胶要求;此外,设计合理的应力释放剂及着色剂含量,保证了器件整体的可靠性和保密性要求。
[0059]
基于同一发明构思,本发明实施例还提供一种环氧塑封料组合物的制造方法,包括以下步骤:
[0060]
将环氧树脂、填料、着色剂、阻燃剂、离子捕捉剂、应力释放剂进行混合得到混合物a,其中,所述填料包括氧化铝和氧化硅,所述氧化硅的质量分数为45wt%-50wt%,所述氧
化铝的质量分数为37wt%-42wt%,所述应力释放剂的质量分数范围为0.3wt%-0.5wt%,所述着色剂的质量分数范围为0.3wt%-0.5wt%;
[0061]
向所述混合物a中添加固化促进剂、固化剂、偶联剂、脱模剂获得混合物b;
[0062]
将所述混合物b加入至预设温度的注塑机中挤出,挤出后冷却,再进行粉碎打饼,得到所述环氧塑封料组合物。
[0063]
基于同一发明构思,本发明实施例还提供一种环氧塑封料组合物在半导体元器件封装中的应用。
[0064]
本发明虽然己以较佳实施例公开如上,但其并不是用来限定本发明,任何本领域技术人员在不脱离本发明的精神和范围内,都可以利用上述揭示的方法和技术内容对本发明技术方案做出可能的变动和修改,因此,凡是未脱离本发明技术方案的内容,依据本发明的技术实质对以上实施例所作的任何简单修改、等同变化及修饰,均属于本发明技术方案的保护范围。