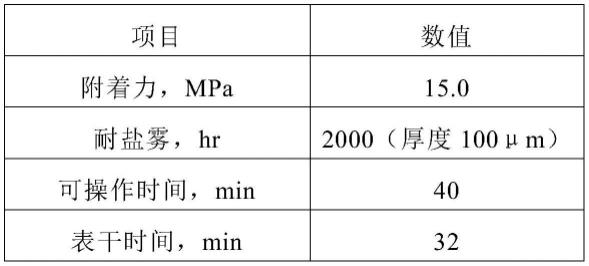
1.本发明涉及防腐涂料技术领域,具体涉及一种硅烷改性环氧基水性聚氨酯钢构防腐涂料。
背景技术:2.无论是风电塔筒还是建筑钢构,或者桥梁等,传统的防腐方案是用溶剂型环氧富锌底漆打底,再涂覆溶剂型环氧云铁中间漆,最后表面涂覆耐候的聚氨酯或者氟碳面漆,室内建筑钢构在中涂漆做完后表面再涂覆防火涂料。但这种防腐方法存在以下问题:涂料中溶剂的存在会污染环境,影响人体健康,而且后处理的代价也比较大。在节能减排的环保发展形势下,为了解决溶剂型材料的环境污染问题,科研工作者多了大量的工作,希望把溶剂型防腐材料改成环保的水性防腐材料或无溶剂防腐涂料,虽然取得了一定的成绩,但是水性防腐涂料的防腐效果还不是很理想,还是比不上溶剂型富锌底漆的防腐效果。其次,在现有的防腐方案中,防腐涂料的涂覆施工道数多,环氧富锌底漆一般2-3 道,然后环氧云铁中间漆2道,而且在气温低时还要加热处理,无论是在施工效率还是能源消耗上都有再优化的空间。
3.所以,现在非常需要一款防腐涂料取代产品,既能解决环保的问题,同时具有高防腐的性能,还要减少施工道数,降低综合成本。
技术实现要素:4.本发明要解决的技术问题是:克服现有技术的不足,提供一种硅烷改性环氧基水性聚氨酯钢构防腐涂料,具有无溶剂、水性环保、免烘烤、防腐性能优异等优点,可以代替环氧富锌底漆,可用于多种金属防腐场合。
5.本发明的技术方案为:
6.硅烷改性环氧基水性聚氨酯钢构防腐涂料,包括a组分和b组分,a组分与b组分的质量比为1:(1.5-2.0);其中a组分包括100%固含量的水性异氰酸酯固化剂;b组分包括有机硅改性环氧树脂、复合乳化剂、防锈颜料、流平剂、耐盐雾助剂、催化剂和稀释剂;有机硅改性环氧树脂占b组分总质量的65-85%,复合乳化剂占b组分总质量的 1-3%,防锈颜料占b组分总质量的5-20%,流平剂占b组分总质量的0.1-0.2%,耐盐雾助剂占b组分总质量的2-6%,催化剂占b组分总质量的0.1-0.2%,稀释剂占b组分总质量的5-10%。
7.优选地,所述水性异氰酸酯固化剂采用nco含量为20wt%以上、粘度为3000cps 以下的固化剂;优选地,所述水性异氰酸酯固化剂采用hdi固化剂、ipdi固化剂或mdi 固化剂。如bayhydur xp2547(粘度570-730cps,nco含量为22.5
±
0.5)、广东东旭化学工业制造有限公司的水性异氰酸酯固化剂wd-8200(固含量100%,粘度2500cps)。
8.为提高防腐涂料的防腐性能,同时提高和基材的结合力,涂料体系中引入可提高结合力的环氧树脂和氨基硅氧烷,通过氨基硅氧烷偶联剂和环氧树脂的聚合反应,消耗掉氨基硅氧烷中的氨基并产生更多的羟基,既确保了结合力的提高又避免偶联剂的单氨基和
环氧树脂的单羟基与异氰酸酯反应后对性能的不利影响。
9.优选地,所述有机硅改性环氧树脂由以下方法制得:于100-120℃下将环氧树脂减压脱水2-2.5h,除水以抑制-si-or水解的发生;添加氨基硅氧烷偶联剂,于100-120℃反应 4-5h,即得有机硅改性环氧树脂;优选地,所述有机硅改性环氧树脂的羟基官能度平均为2-2.5,环氧树脂与氨基硅氧烷偶联剂的质量比为1:(0.5-0.7),确保环氧树脂过量并使产物避免较多的交联而使粘度增加太多。
10.优选地,所述环氧树脂采用粘度为5000cps以下的无溶剂液体双酚a型环氧树脂、双酚f型环氧树脂及酚醛胺型环氧树脂。
11.优选地,所述氨基硅氧烷偶联剂采用含有单伯氨基结构的硅氧烷;优选地,所述氨基硅氧烷偶联剂采用γ-氨丙基三乙氧基硅烷、γ-氨丙基三甲氧基硅烷、n-β(氨乙基)
‑ꢀ
γ-氨丙基三甲氧基硅烷、n-β(氨乙基)-γ-氨丙基三乙氧基硅烷、3-氨丙基甲基二乙氧基硅烷或3-氨丙基三甲氧基硅烷。
12.优选地,所述复合乳化剂包括阳离子乳化剂和非离子乳化剂,阳离子乳化剂和非离子乳化剂分别占b组分总质量的0.5-1.5%;优选地,所述复合乳化剂包括十六烷基三甲基溴化铵(ctab)和壬酚聚氧乙烯醚(np-10)。添加复合乳化剂的目的是为施工时降低粘度而添加水稀释准备。
13.优选地,所述防锈颜料采用磷酸锌、磷钼酸锶中的一种或两种,并将其烘烤脱水。
14.优选地,所述流平剂为德国tego有机硅流平剂glide410、wet270、kl245、glide100 中的一种或两种。
15.优选地,所述稀释剂采用2,2,4三甲基1,3戊二醇二异丁酸酯或二异丙基萘。
16.优选地,所述催化剂采用有机锡或有机铋类催化剂。
17.耐盐雾助剂采用陕西费米新材料应用科技有限公司的spp-y100产品,是一种液体低粘度磺酸铵盐型耐盐雾助剂,粘度为100cps(20℃),比重为1.0g/cm3。这种助剂可以在金属基材表面形成“伞”状防护,具有强力的隔阻、提高附着力和耐腐蚀的三重功效,其效率极高,可以替代部分防锈颜料并可提升整体防锈性能。
18.本发明用含有氨基的硅氧烷和环氧树脂反应,产物为含有羟基的多元醇,而且是硅氧烷基团封端。多元醇和异氰酸酯反应,可以常温固化,不用加热,而且聚氨酯类涂料的反应速度比环氧类的反应速度更快,可提高施工效率。在分子链上封端的硅氧烷会水解成硅醇结构并进一步聚合成聚硅醇,可大幅提高结合力和防腐性能。纯水性体系一般体系中含有水,往往喷涂一道的厚度不大,否则会流挂或者长时间不干等缺陷,本发明体系可以添加水实现薄涂,也可以不加水而成为100%固含量的防腐材料体系。通过添加液体的耐盐雾助剂来减少粉末防锈颜料的量,确保粘度不太大;并且采用防锈效果好的磷钼酸锶防锈颜料,提高防锈效果。
19.本发明与现有技术相比,具有以下有益效果:
20.1.实现了无溶剂化。本发明的防腐涂料不含溶剂,为无溶剂体系。喷涂施工时可以添加适量的水作为稀释剂来降低粘度,调成水性涂料便于喷涂施工。也可以采用专用设备,通过给原料加热的办法来降低粘度,实现无溶剂化,厚涂施工。
21.2.结合力的要求。聚氨酯的结合力普遍低于环氧树脂,环氧树脂基本被认为是结合力最好的材料,在防腐材料中,结合力差就意味着防腐性能也不会好,所以需要确保新体
系有足够的结合力。本发明采用硅氧烷改性环氧树脂和聚氨酯反应的方式,满足结合力的要求,硅氧烷的烷氧基水解并聚合成聚硅醇,也可大幅提高结合力。
22.3.低粘度要求。溶剂型或水性涂料之所以添加溶剂或水,就是为了降低粘度,因为防腐涂料往往需要添加大量的锌粉以及防锈颜料才能起到好的防腐效果,这就必然导致粘度增加,不方便施工。本发明中不以添加大量锌粉牺牲阳极的方式来达到良好防腐的要求,而是用液体耐盐雾助剂这一“液体防锈颜料”代替部分粉末防锈颜料,防锈颜料采用防锈效果优异的可少量添加就具有良好防腐作用的磷酸钼锶,同时添加适量的磷酸锌,具有协同防腐效果,获得防腐效果优异并容易喷涂施工的材料。同时在原料中提前加入复合乳化剂,可以在使用时添加水来稀释,也可以通过原料加热的方式降低粘度来喷涂施工,尤其是薄涂要求时可使用这个办法。
23.4.环氧树脂、氨基硅氧烷偶联剂和聚氨酯的反应问题。由于低粘度低分子量的环氧树脂分子中羟基含量往往很低,基本每个环氧分子含有一个羟基,甚至平均不到一个羟基,成了单官能团多元醇。在和聚氨酯反应时以链终止剂的身份存在,对性能非常不利。氨基硅氧烷的加入是为了提高结合力、表面易清洁性、防腐性能等,但是含氨基的硅烷和聚氨酯的nco反应速度极快,不利于施工。再就是,氨基硅氧烷也是单官能团,添加太多对材料的性能也有极不利的影响。有些疏水性好的硅氧烷往往和聚氨酯的相容性不好。为解决这些问题,本发明采用氨基硅氧烷和环氧树脂的环氧基团先进行反应,氨基反应掉,同时环氧基开环产生羟基,生成了多羟基的硅烷改性环氧树脂,其作为多元醇可以和nco平稳反应,同时产物末端的烷氧基通过水解生成硅醇,并进一步自聚及和底材的羟基聚合,获得附着力的提高及防腐性能的提高。
24.5.综合成本的控制。一个新技术是否具有实用价值,还要看是否具有可操作性,其中成本也是一个关键影响因素。本发明的防腐涂料在喷涂后不必加热固化,可常温固化,有利于节约能源。同时不再用富锌底漆和云铁中间漆的多道涂覆的方案,而是采用一道成型的方式,提高了效率,进一步降低了成本。
25.6.本发明在原料合成时避免水的存在,主要是为了提高贮存稳定性,避免水解的产生,但是使用时可以添加水以降低粘度,同时产生水解利于烷氧基的水解和聚合。且本发明为了获得良好的水稀释性,采用复合乳化剂。
具体实施方式
26.为了使本技术领域的人员更好地理解本发明中的技术方案,下面对本发明实施例中的技术方案进行清楚、完整地描述,显然,所描述的实施例仅仅是本发明一部分实施例,而不是全部的实施例。基于本发明中的实施例,本领域普通技术人员在没有做出创造性劳动前提下所获得的所有其他实施例,都应当属于本发明保护的范围。
27.实施例1
28.a组分:选用covestro水性聚异氰酸酯固化剂bayhydur xp2547,粘度为570-730cps, nco质量比为22.5
±
0.5%。
29.b组分的制备:
30.将46份环氧树脂npef-170(南亚环氧树脂)投入反应釜中,于120℃减压脱水2h,添加24份γ-氨丙基三乙氧基硅烷,于120℃反应4h,得到有机硅改性的环氧树脂,出料降温。
31.将16.6份烘干脱水后的磷酸锌防锈颜料、1.5份乳化剂ctab、1.5份乳化剂壬酚聚氧乙烯醚(np-10)、0.2份流平剂kl245、5份耐盐雾助剂spp-y100、0.2份催化剂二月桂酸酯二丁基锡(t12)、5份稀释剂2,2,4-三甲基1,3戊二醇二异丁酸酯(txib)投入到有机硅改性的环氧树脂中,搅拌均匀后投入砂磨机研磨,测试细度达到15-20μm时出料。
32.本实施例的防腐涂料使用质量配比为a:b:水=1:1.6:0.4。
33.本实施例的防腐涂料涂层的性能如表1所示:
34.表1
35.项目数值附着力,mpa12.6耐盐雾,hr2400(厚度100μm)可操作时间,min40表干时间,min20耐冲击性,cm56一道可成膜厚度,μm40
[0036] 实施例2
[0037]
a组分:广东东旭化学工业制造有限公司的水性异氰酸酯固化剂wd-8200(固含量 100%,粘度2500cps,nco质量比为21%)。
[0038]
b组分的制备:
[0039]
将43份环氧树脂npef-175(南亚环氧树脂)投入反应釜中,于120℃减压脱水2h,添加22份γ-氨丙基三甲氧基硅烷,于120℃反应4h,得到有机硅改性的环氧树脂多元醇,出料降温。
[0040]
将10.8份烘干脱水后的磷酸锌防锈颜料、6份烘干脱水后磷钼酸锶防锈颜料、1份乳化剂ctab、1份乳化剂np-10、0.1份流平剂kl245、6份耐盐雾助剂spp-y100、0.1 份催化剂二月桂酸酯二丁基锡(t12)、10份稀释剂二异丙基萘投入到有机硅改性的环氧树脂中,搅拌均匀后投入砂磨机研磨,测试细度达到15-20μm时出料。
[0041]
本实施例的防腐涂料使用质量配比为a:b:水=1:1.6:0.4。
[0042]
本实施例的防腐涂料涂层的性能如表2所示:
[0043]
表2
[0044]
参数数值附着力,mpa10.8耐盐雾,hr2800(厚度100μm)可操作时间,min40表干时间,min21耐冲击性,cm60一道可成膜厚度,μm36
[0045]
实施例3
[0046]
a组分:选用covestro xp 2655,粘度3000cps,nco质量比为21%。
[0047]
b组分的制备:
[0048]
将40份环氧树脂npef-176(南亚环氧树脂)投入反应釜中,于120℃减压脱水2h,添
加26份n-β(氨乙基)-γ-氨丙基三甲氧基硅烷,于120℃反应4h,得到有机硅改性的环氧树脂多元醇,出料降温。
[0049]
将15份烘干脱水后的磷酸锌防锈颜料、5份烘干脱水后磷钼酸锶防锈颜料、1份乳化剂ctab、0.5份乳化剂np-10、0.1份流平剂kl245、5份耐盐雾助剂spp-y100、0.1 份催化剂二月桂酸酯二丁基锡(t12)、7.3份稀释剂二异丙基萘投入到有机硅改性的环氧树脂中,搅拌均匀后投入砂磨机研磨,测试细度达到15-20μm时出料。
[0050]
本实施例的防腐涂料使用质量配比为a:b=1:2,原料加热到40-50℃。
[0051]
本实施例的防腐涂料涂层的性能如表3所示:
[0052]
表3
[0053]
项目数值附着力,mpa14.8耐盐雾,hr2950(厚度100μm)可使用时间,min30表干时间,min30耐冲击性,cm50一道可成膜厚度,μm80
[0054]
实施例4
[0055]
a组分:选用covestro水性聚异氰酸酯固化剂bayhydur xp2547,粘度570-730cps, nco质量比为22.5
±
0.5%。
[0056]
b组分的制备:
[0057]
将52份环氧树脂npef-170(南亚环氧树脂)投入反应釜中,于110℃减压脱水2h,添加33份3-氨丙基甲基二乙氧基硅烷,于110℃反应4h,得到有机硅改性的环氧树脂多元醇,出料降温。
[0058]
将5份烘干脱水后的磷酸锌防锈颜料、0.5份乳化剂ctab、0.5份乳化剂np-10、0.1 份流平剂glide410、2份耐盐雾助剂spp-y100、0.1份有机铋催化剂bicat8118、6.8份稀释剂二异丙基萘投入到有机硅改性的环氧树脂中,搅拌均匀后投入砂磨机研磨,测试细度达到15-20μm时出料。
[0059]
本实施例的防腐涂料使用质量配比为a:b:水=1:1.6:0.3。
[0060]
本实施例的防腐涂料涂层的性能如表4所示:
[0061]
表4
[0062]
[0063][0064]
实施例5
[0065]
a组分:武汉仕全兴新材料科技股份有限公司s101水性异氰酸酯固化剂,粘度 2500cps,nco质量比为21.3%。
[0066]
b组分的制备:
[0067]
将40份环氧树脂htm5102(苏州圣杰特种树脂有限公司产品)投入反应釜中,于 110℃减压脱水2h,添加25份n-β(氨乙基)-γ-氨丙基三乙氧基硅烷,于120℃反应4h,得到有机硅改性的环氧树脂多元醇,出料降温。
[0068]
将13.5份烘干脱水后的磷酸锌防锈颜料、5份烘干脱水后磷钼酸锶防锈颜料、0.8份乳化剂ctab、0.7份乳化剂np-10、0.1份流平剂glide410、5份耐盐雾助剂spp-y100、 0.1份有机铋催化剂bicat8118、9.8份稀释剂二异丙基萘投入到有机硅改性的环氧树脂中,搅拌均匀后投入砂磨机研磨,测试细度达到15-20μm时出料。
[0069]
本实施例的防腐涂料使用质量配比为a:b=1:1.5,原料加热到40-60℃。
[0070]
本实施例的防腐涂料涂层的性能如表5所示:
[0071]
表5
[0072]
项目数值附着力,mpa14.3耐盐雾,hr2450(厚度100μm)可操作时间,min35表干时间,min36耐冲击性,cm52一道可成膜厚度,μm80
[0073]
根据jg/t224-2007建筑用钢结构防腐涂料的标准要求,建筑钢结构防腐涂料耐盐雾时间要求从200h到1000h不等(膜厚100微米)。而一般水性防腐涂料的耐盐雾时间要求会更短,如标准“hg/t4759-2014水性环氧树脂防腐涂料”中要求耐盐雾300h(膜厚 100微米),由实施例1-5的水性涂料耐盐雾时间测试结果可知,本发明的防腐涂料的耐盐雾时间已大大超出标准要求。
[0074]
对比例1
[0075]
与实施例3的区别在于:去掉实施例3中b组分的耐盐雾助剂。
[0076]
a组分:选用covestro xp 2655,粘度3000cps,nco质量比为21%。
[0077]
b组分的制备:
[0078]
将40份环氧树脂npef-176(南亚环氧树脂)投入反应釜中,于120℃减压脱水2h,添加26份n-β(氨乙基)-γ-氨丙基三甲氧基硅烷,于120℃反应4h,得到有机硅改性的环氧树脂多元醇,出料降温。
[0079]
将15份烘干脱水后的磷酸锌防锈颜料、5份烘干脱水后磷钼酸锶防锈颜料、1份乳化剂ctab、0.5份乳化剂np-10、0.1份流平剂kl245、0.1份催化剂二月桂酸酯二丁基锡
(t12)、7.3份稀释剂二异丙基萘投入到有机硅改性的环氧树脂中,搅拌均匀后投入砂磨机研磨,测试细度达到15-20μm时出料。
[0080]
本对比例的防腐涂料使用质量配比为a:b=1:1.9,原料加热到40-50℃。
[0081]
本对比例的防腐涂料涂层的性能如表6所示:
[0082]
表6
[0083]
项目数值附着力,mpa14.7耐盐雾,hr2600(厚度100μm)可使用时间,min28表干时间,min30耐冲击性,cm50一道可成膜厚度,μm100
[0084]
通过与实施例3的对比可见,如果不添加液体耐盐雾助剂,不但耐盐雾时间会下降,防腐效果降低;体系粘度较大,一道成膜厚度也会增加,不容易实现薄涂。
[0085]
本发明的防腐涂料与“hg/t3668-2009富锌底漆”的标准要求对比如表7所示:
[0086]
表7本发明产品与hg/t3668-2009富锌底漆产品性能对比
[0087][0088]
由表可知,本发明产品的耐盐雾性能远超过富锌底漆的相关标准规定,而且和基材的结合力也会大大提高,完全可以取代富锌底漆用于钢构防腐。
[0089]
另外,根据“jgj/t251-2011建筑钢结构防腐蚀技术规程”相关环氧富锌底漆的使用规定,规定环氧富锌底漆至少两道,然后再喷涂环氧云铁中间漆1-2道,最后涂覆面漆或者防火涂料。由于环氧富锌底漆中含有大量的锌粉,其致密性不太好,同时和防火涂料或者面漆的结合力也不理想,所以需要环氧云铁中间漆过渡,提高致密性,增加结合力。利用本发明的材料,其致密性良好,可以不用中间漆,直接涂覆防火涂料或者面漆,其结合力完全可以满足“jg/t224-2007建筑用钢结构防腐涂料”标准中规定的附着力要求,同时减少施工层数,提高了效率。
[0090]
尽管通过参考实施例的方式对本发明进行了详细描述,但本发明并不限于此。在不脱离本发明的精神和实质的前提下,本领域普通技术人员可以对本发明的实施例进行各种等效的修改或替换,而这些修改或替换都应在本发明的涵盖范围内/任何熟悉本技术领域的技术人员在本发明揭露的技术范围内,可轻易想到变化或替换,都应涵盖在本发明的保护范围之内。因此,本发明的保护范围应所述以权利要求的保护范围为准。