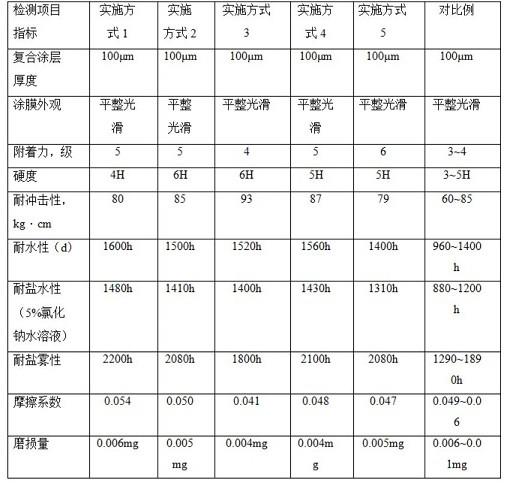
1.本发明涉及防腐耐磨涂层技术领域,尤其涉及一种碳纳米管改性耐磨耐腐复合涂层及制作方法。
背景技术:2.目前,地球表面海洋约占71%的面积,航海业和海洋开发已成为全世界很多国家经济发展不可或缺的重要支柱。
3.海洋环境是十分严酷的腐蚀环境,舰船在海洋行驶过程中,船体受海水侵蚀冲刷和日照紫外线辐射的作用,处于富氧状态干湿交替的环境,同时,又有海洋垃圾和污染物的侵蚀碰撞,所以,船体腐蚀情况最为严重不但能够降低船舶钢结构的强度,缩短船舶寿命,还会增加航行阻力,降低航速,影响船舶性能和航行安全,对防腐涂料的性能要求更高。
4.现有技术中,常用的涂层如环氧树脂、有机硅树脂、聚氨酷树脂、醇酸树脂和聚醋树脂等可用来制备不同功能的涂层,实现防护和装饰等功能。
5.但是现有技术中,简单防腐层的防腐性能差,现在的涂层多为单层或双层,在海洋环境下防腐能力较差,在高频摩擦使用条件下需要经常涂覆涂料才可降低金属制品的腐蚀速率,导致工作强度大,防腐效率较低。
技术实现要素:6.本发明的目的在于提供一种碳纳米管改性耐磨耐腐复合涂层及制作方法,旨在解决现有技术中的简单防腐层的防腐性能差,现在的涂层多为单层或双层,在海洋环境下防腐能力较差,在高频摩擦使用条件下需要经常涂覆涂料才可降低金属制品的腐蚀速率,导致工作强度大,防腐效率较低的技术问题。
7.为实现上述目的,本发明采用的一种碳纳米管改性耐磨耐腐复合涂层及制作方法,包括碳纳米管改性锌铁合金层、底漆层、碳纳米管改性锌粉层和面漆层,所述碳纳米管改性锌铁合金层、所述底漆层、所述碳纳米管改性锌粉层和所述面漆层依次设置;所述碳纳米管改性锌铁合金层由以下重量百分比的组分组成:fe2~5%、cnts02~05%和zn945~978%;所述底漆层由以下重量百分比的组分组成:环氧树脂40~50%、高岭土5~10%、碳化硅与氧化铁填料10~15%、柔性树脂5~10%、聚氨酯10~15%、氧化锌-氮化铝-碳纳米管5~10%和水10~15%;所述碳纳米管改性锌粉层由以下重量百分比的组分组成:固化剂5~20%、碳纳米管改性锌粉20~30%、环氧树脂20~30%、酚醛树脂10~20%、填料5~10%、催化剂1~5%和添加剂1~5%;所述面漆层由以下重量百分比的组分组成:环氧树脂30~50%、酚醛树脂10~20%、颜料3~8%、碳化硅与氮化铝填料10~20%、纳米助剂1~3%和水15~30%。
8.其中,所述碳纳米管改性锌铁合金层的厚度为5~15μm,所述底漆层的厚度为30~50
μm,所述碳纳米管改性锌粉层的厚度为5~15μm,所述面漆层的厚度为30~50μm。
9.本发明还提供一种碳纳米管改性耐磨耐腐复合涂层的制作方法,制备上述所述的碳纳米管改性耐磨耐腐复合涂层,包括如下步骤:采用对应百分比组分制备所述碳纳米管改性锌铁合金层;采用对应百分比组分制备所述底漆层;采用对应百分比组分制备所述碳纳米管改性锌粉层;采用对应百分比组分制备所述面漆层;最终将所述碳纳米管改性锌铁合金层、所述底漆层、所述碳纳米管改性锌粉层和所述面漆层依次涂覆于工件外表壁,以此制备出所述碳纳米管改性耐磨耐腐复合涂层。
10.其中,制备上述所述的碳纳米管改性锌铁合金层,包括如下步骤:将所述fe和所述zn和所述cnts在乙醇中球磨48~72小时;在惰性气氛中干燥8~24小时得混合粉末a;采用连续挤压的方式将所述混合粉末a挤压形成直径为2~3mm的丝材备用;将工件表面进行喷砂清理并形成麻面,采用火焰热喷涂工艺在工件的表面进行所述丝材的喷涂,即形成所述碳纳米管改性耐磨耐腐复合涂层。
11.其中,制备上述所述的底漆层,包括如下步骤:将所述聚氨酯、所述柔性树脂和所述水混合搅拌10~30min,制得聚氨酯复合乳液;向所述聚氨酯复合乳液中加入氧化锌-氮化铝-碳纳米管,并搅拌120~360min;加入所述环氧树脂、所述高岭土和所述氮化硅与氮化铝填料,并搅拌120~360min,制得所述底漆层。
12.其中,制备上述所述的碳纳米管改性锌粉层,包括如下步骤:将所述固化剂熔化并加入所述碳纳米管改性锌粉,搅拌均匀后,制得混合粉末a;将所述环氧树脂、所述酚醛树脂、所述填料、所述催化剂和所述添加剂添加并混合熔炼,制得混合粉末b;将所述混合粉末a与所述混合粉末b均匀混合后制得所述碳纳米管改性锌粉层。
13.其中,制备上述所述的面漆层,包括如下步骤:将碳纳米管溶解于聚氨酯溶液中,所述碳纳米管在所述聚氨酯溶液中的质量分数为5~20%,将含氢氯氟烃,并加热至100~120℃,保温3~5h,脱水烘干;加入碳化硅与氮化铝填料研磨48~72h,并脱水烘干,制得所述纳米助剂;将所述环氧树脂、所述酚醛树脂、所述颜料、所述碳化硅与氮化铝填料、纳米助剂和水混合搅拌10~60min,以此制得所述面漆层。
14.本发明的一种碳纳米管改性耐磨耐腐复合涂层及制作方法的有益效果为:1、从物理化学角度来说,晶体结构相同、原子结构相似的物质更容易形成一个整体,即润湿性好,结合时会结合的更牢固。
15.船体都是采用钢铁材料制成的,若直接喷涂锌层,由于锌与铁之间存在结构差异,即润湿性不好,会导致锌与铁之间的结合较差。
16.本发明在碳纳米管改性锌铁合金层中加入铁成分,在锌中通过共熔冶炼的方式加入铁,则在喷涂锌铁合金时,合金中的铁会起到促进锌铁合金(涂层)与铁(船体)之间的结合,可增加锌与工件表面的润湿程度,从而使碳纳米管改性锌铁合金层与工件表面结合的
更加牢固。
17.2、在碳纳米管改性锌铁合金层的制备过程中,采用火焰热喷涂工艺在船体表面进行丝材的喷涂,在喷涂过程中,锌铁合金丝被火焰熔化,在压缩空气的作用下,熔化后的合金被雾化成熔滴,并飞向船体表面。
18.在熔滴飞行和沉积在船体表面的过程中,熔滴冷却,碳纳米管改性锌铁合金层中的液态zn与δ相(fezn
10
) 包晶生成耐磨性较好的ξ相(fezn
13
) (在803k时),从而增加耐磨性,其中δ相是一种高温铁素体,由液态铁冷却到1538摄氏度发生结晶,液态铁转变为δ-fe所得,ξ相具有单斜结构,其结晶的对称性差,性能较硬且脆性大。
19.3、本发明中的碳纳米管改性锌铁合金层中掺杂碳纳米管cnts, cnts具有优异的耐磨、耐腐蚀和导电性能,在增加耐磨性的同时,联通zn和fe形成原电池,zn 比fe活泼,通过牺牲zn保护fe,从而达到防腐的目的。
20.4、本发明中的底漆层中含有氧化锌氮化铝_碳纳米管,在氧化锌氮化铝碳纳米管的制备过程中,首先制备管内掺杂铁的多壁碳纳米管,然后将管内掺杂铁的多壁碳纳米管加入到浓硫酸与苯磺酸混合溶液中,加热至40-60℃保温60~120min得到改性碳纳米管,通过这样的改性处理一方面是将铁氧化变成铁离子,以便在后期研磨过程中被锌还原,让锌离子掺杂进入碳纳米管内;另一-方面能够使碳纳米管羧基化,有利于在混料时均匀分散。
21.5、本发明底漆层中加入了改性的碳纳米管,一是与改性锌铁合金层中的碳纳米管形成了一个连续分布的特点,为电子的传输提供畅通的通道,当有电子进入涂层时,能够直接被锌所捕获,通过腐蚀锌来保护铁,起到更好保护船体的作用;二是利用碳纳米管自身的耐磨性提高底漆层的耐磨性。
22.6、本发明中的碳纳米管改性锌粉层的制备方法中,首先制备管内掺杂铁的多壁碳纳米管,然后将管内掺杂铁的多壁碳纳米管加入到浓硫酸、浓硝酸和浓盐酸的混合溶液中氧化,将铁氧化变成铁离子,以便在后期研磨过程中被锌还原;然后经水洗、烘干后加入锌熔体,450~480℃保温30~60min,锌熔体能够与碳纳米管更好地结合,锌离子容易被掺杂进入碳纳米管内;最后经雾化制粉、筛选后得所述碳纳米管改性锌粉。
23.7、本发明中的碳纳米管改性锌粉层,一是可以联通改性锌铁合金层和底漆层之间的连贯性,使碳纳米管连续分布,为电子的传输提供畅通的通道,当有电子进入涂层时,能够直接被锌所捕获,通过腐蚀锌来保护铁,起到更好保护船体的作用;二是利用碳纳米管自身的耐磨性提高碳纳米管改性锌粉层的耐磨性;三是通过给底漆层喷涂一层低熔点的锌层,保护底漆层不被腐蚀,当有电子进入涂层时,首先应腐蚀锌含量较高的碳纳米管改性锌粉层。
24.8、本发明中的碳纳米管改性锌粉层是通过固体粉末的形式喷涂的,粉末制备过程中,各成分能够得到更加均匀的混合,避免了碳纳米管偏聚的问题。
25.且在施工过程中,能够更好地控制喷涂的涂层厚度和均匀性。
26.9、本发明中的面漆层中也加入了改性的碳纳米管,是整个复合涂层中碳纳米管具有连续性,一方面较好地阻止了电化学腐蚀,另一面起到很好的耐磨作用。
附图说明
27.为了更清楚地说明本发明实施例或现有技术中的技术方案,下面将对实施例或现
有技术描述中所需要使用的附图作简单地介绍,显而易见地,下面描述中的附图仅仅是本发明的一些实施例,对于本领域普通技术人员来讲,在不付出创造性劳动的前提下,还可以根据这些附图获得其他的附图。
28.图1是本发明的第一实施例的制作方法1-4项工艺步骤流程图。
29.图2是本发明的第一实施例的制作方法5-8项工艺步骤流程图。
30.图3是本发明的第二实施例的制作方法1-4项工艺步骤流程图。
31.图4是本发明的第二实施例的制作方法5-8项工艺步骤流程图。
32.图5是本发明的第三实施例的制作方法1-4项工艺步骤流程图。
33.图6是本发明的第三实施例的制作方法5-8项工艺步骤流程图。
34.图7是本发明的第四实施例的制作方法1-4项工艺步骤流程图。
35.图8是本发明的第四实施例的制作方法5-8项工艺步骤流程图。
36.图9是本发明的第四实施例的制作方法9项工艺步骤流程图。
37.图10是本发明的第五实施例的制作方法1-4项工艺步骤流程图。
38.图11是本发明的第五实施例的制作方法5-8项工艺步骤流程图。
39.图12是本发明的第五实施例的制作方法9项工艺步骤流程图。
40.图13是本发明的对比例的对比数据图。
具体实施方式
41.一种碳纳米管改性耐磨耐腐复合涂层,包括碳纳米管改性锌铁合金层、底漆层、碳纳米管改性锌粉层和面漆层,所述碳纳米管改性锌铁合金层、所述底漆层、所述碳纳米管改性锌粉层和所述面漆层依次设置;所述碳纳米管改性锌铁合金层由以下重量百分比的组分组成:fe2~5%、cnts02~05%和zn945~978%;所述底漆层由以下重量百分比的组分组成:环氧树脂40~50%、高岭土5~10%、碳化硅与氧化铁填料10~15%、柔性树脂5~10%、聚氨酯10~15%、氧化锌-氮化铝-碳纳米管5~10%和水10~15%;所述碳纳米管改性锌粉层由以下重量百分比的组分组成:固化剂5~20%、碳纳米管改性锌粉20~30%、环氧树脂20~30%、酚醛树脂10~20%、填料5~10%、催化剂1~5%和添加剂1~5%;所述面漆层由以下重量百分比的组分组成:环氧树脂30~50%、酚醛树脂10~20%、颜料3~8%、碳化硅与氮化铝填料10~20%、纳米助剂1~3%和水15~30%。
42.所述碳纳米管改性锌铁合金层的厚度为5~15μm,所述底漆层的厚度为30~50μm,所述碳纳米管改性锌粉层的厚度为5~15μm,所述面漆层的厚度为30~50μm。
43.在对工件表面进行喷砂清理的步骤中,喷涂时使用的氧气的纯度2》995%,z 炔气的纯度≥975%;和/或,喷涂时使用的氧气的压力为04~07mpa, 乙炔气的压力为007~013mpa,压缩空气的压力为05~07mpa;喷涂时喷枪的喷涂角度为65~80
°
,喷涂距离为100~200mm,喷枪移动速度为5~20m/min,送丝速度为3
‑ꢀ
5m/min;喷束宽为3~8cm。
44.所述氧化锌-氮化铝-碳纳米管的制备方法如下:碳纳米管的制备:在流动氢气环境下,通过chsoh、fe(c:h)和s(c4hs)在1050~1180
℃发生催化化学反应,生成管内掺杂铁的多壁碳纳米管;碳纳米管的改性处理:将管内掺杂铁的多壁碳纳米管加入到浓硫酸与05mol/l的苯磺酸混合溶液中,加热至40-60℃,保温60~120min,然后经水洗,干燥,得到改性碳纳米管;球磨填料:对氧化锌粉、锌粉、氮化铝、二氧化硅粉以及改性碳纳米管混合后的混合粉末进行超声清洗烘干,然后在乙醇中对所述混合粉末进行球磨,通高纯氮气球磨48~72小时,得所述氧化锌-氮化铝-碳纳米管;其中,所述混合粉末的粒径为300-3000目,所述混合粉末与磨球的质量比为1:20~30,球磨转速为10000
‑ꢀ
20000转小时。
45.所述氧化锌-氮化铝-碳纳米管由以下重量百分比的组分组成:氧化锌粉20~ 40%、锌粉10-30%、氮化铝30-45%、二氧化硅粉5~10%和碳纳米管02%-1 2%。
46.所述碳纳米管改性锌粉的制备方法如下:碳纳米管的制备:在流动氢气环境下,通过c2hsoh、fe(cshs)和 s(c4h)在1050~1180℃发生催化化学反应,生成管内掺杂铁的多壁碳纳米管;碳纳米管的改性处理:将管内掺杂铁的多壁碳纳米管加入到浓硫酸、浓硝酸和浓盐酸的混合溶液中氧化,然后经水洗、烘干后加入锌熔体,450~480℃保温30
‑ꢀ‑
60min;最后经雾化制粉、筛选后得所述碳纳米管改性锌粉。
47.请参阅图1和图2,实施例1,本发明还提供一种碳纳米管改性耐磨耐腐复合涂层的制作方法,包括如下步骤:s1:将3%所述fe和96.8%所述zn的粉末与0.2%所述cnts在乙醇中球磨60小时,然后在惰性气氛下干燥15小时得混合粉末,接着采用连续挤压的方式将混合粉末挤压形成直径为2
‑ꢀ
3mm的丝材,对丝材进行碱洗,然后盘卷后备用;s2:将船体表面喷砂清理,除去沙、泥、锈、油污等杂物,并在船体表面形成麻面;采用火焰热喷涂工艺在船体的表面进行丝材的喷涂,即形成碳纳米管改性锌铁合金层;s3:将12%所述聚氨酯、6%所述柔性树脂和15%所述水混合搅拌20min,制得聚氨酯复合乳液,向聚氨酯复合乳液中添加8%所述氧化锌-氮化铝-碳纳米管,并搅拌240min后,加入43%所述环氧树脂、5%所述高岭土和11%所述碳化硅与氧化铁填料,并搅拌240min,喷涂至所述碳纳米管改性锌铁合金层表面得到所述底漆层;s4:碳纳米管的制备:在流动氢气,环境下,通过c2h5oh、fe(c5h5)和s(c4h5)在1050~1180℃发生催化化学反应,生成管内掺杂铁的多壁碳纳米管;s5:球磨填料:对25%所述氧化锌粉、25%所述锌粉、40%所述氮化铝、9%所述二氧化硅粉以及1%所述改性碳纳米管混合后的混合粉末进行超声清洗烘干,然后在乙醇中对混合粉末进行球磨,通高纯氮气球磨60小时,得所述氧化锌氮化铝-碳纳米管;其中,混合粉末的粒径为300-3000目,混合粉末与磨球的质量比为1:25,球磨转速为15000 转小时;s6:碳纳米管的制备:在流动氢气环境下,通过c2h5oh、fe(c5h5)和s(c4h5)在1050
‑ꢀ
1180℃发生催化化学反应,生成管内掺杂铁的多壁碳纳米管;将管内掺杂铁的多壁碳纳米管加入到浓硫酸、浓硝酸和浓盐酸的混合溶液中氧化,然后经水洗、烘干后加入锌熔体, 450~480℃保温50min;最后经雾化制粉、筛选后得碳纳米管改性锌粉;s7:接着将15%所述固化剂熔化,加入25%所述碳纳米管改性锌粉,搅拌均匀后,造粒得共混粉末1;将25%所述环氧树脂、18%所述酚醛树脂、9%所述填料、4%所述催化剂以及4%
所述添加剂熔融混炼,造粒得共混粉末2;将所述共混粉末1与所述共混粉末2混合后,喷徐到所述底漆层表面即得所述碳纳米管改性锌粉层;s8:先将所述碳纳米管溶解于所述聚氨酯中,所述碳纳米管在所述聚氨酯中的质量分数为10%;然后加入所述含氢氯氟烃,加热至100~120℃,保温4小时,脱水烘干;加入所述碳化硅与氮化铝填料研磨60小时,脱水烘干,制得所述纳米助剂,然后将40%所述环氧树脂、15%所述酚醛树脂、5%所述颜料、15%所述碳化硅与氮化铝填料、2%所述纳米助剂以及23%所述水混合搅拌40min,喷徐到所述碳纳米管改性锌粉层表面既得所述面漆层。
48.请参阅图3和图4,实施例2,本发明还提供一种碳纳米管改性耐磨耐腐复合涂层的制作方法,包括如下步骤:s1:将5%所述fe和94.8%所述zn的粉末与0.2%cnts在乙醇中球磨60小时,然后在惰性气氛下干燥15小时得混合粉末,接着采用连续挤压的方式将混合粉末挤压形成直径为2
‑ꢀ
3mm的丝材,对丝材进行碱洗,然后盘卷后备用;s2:将船体表面喷砂清理,除去沙、泥、锈、油污等杂物,并在船体表面形成麻面;采用火焰热喷涂工艺在船体的表面进行丝材的喷涂,即形成碳纳米管改性锌铁合金层;s3:将12%所述聚氨酯、6%所述柔性树脂和15%所述水混合搅拌20min,制得聚氨酯复合乳液,向聚氨酯复合乳液中添加8%所述氧化锌-氮化铝-碳纳米管,并搅拌240min后,加入43%所述环氧树脂、5%所述高岭土和11%所述碳化硅与氧化铁填料,并搅拌240min,喷涂至所述碳纳米管改性锌铁合金层表面得到所述底漆层;s4:碳纳米管的制备:在流动氢气,环境下,通过c2h5oh、fe(c5h5)和s(c4h5)在1050~1180℃发生催化化学反应,生成管内掺杂铁的多壁碳纳米管;s5:球磨填料:对25%所述氧化锌粉、25%所述锌粉、40%所述氮化铝、9%所述二氧化硅粉以及1%所述改性碳纳米管混合后的混合粉末进行超声清洗烘干,然后在乙醇中对混合粉末进行球磨,通高纯氮气球磨60小时,得所述氧化锌氮化铝-碳纳米管;其中,混合粉末的粒径为300-3000目,混合粉末与磨球的质量比为1:25,球磨转速为15000 转小时;s6:碳纳米管的制备:在流动氢气环境下,通过c2h5oh、fe(c5h5)和s(c4h5)在1050
‑ꢀ
1180℃发生催化化学反应,生成管内掺杂铁的多壁碳纳米管;将管内掺杂铁的多壁碳纳米管加入到浓硫酸、浓硝酸和浓盐酸的混合溶液中氧化,然后经水洗、烘干后加入锌熔体, 450~480℃保温50min;最后经雾化制粉、筛选后得碳纳米管改性锌粉;s7:接着将15%所述固化剂熔化,加入25%所述碳纳米管改性锌粉,搅拌均匀后,造粒得共混粉末1;将25%所述环氧树脂、18%所述酚醛树脂、9%所述填料、4%所述催化剂以及4%所述添加剂熔融混炼,造粒得共混粉末2;将所述共混粉末1与所述共混粉末2混合后,喷徐到所述底漆层表面即得所述碳纳米管改性锌粉层;s8:先将所述碳纳米管溶解于所述聚氨酯中,所述碳纳米管在所述聚氨酯中的质量分数为10%;然后加入所述含氢氯氟烃,加热至100~120℃,保温4小时,脱水烘干;加入所述碳化硅与氮化铝填料研磨60小时,脱水烘干,制得所述纳米助剂,然后将40%所述环氧树脂、15%所述酚醛树脂、5%所述颜料、15%所述碳化硅与氮化铝填料、2%所述纳米助剂以及23%所述水混合搅拌40min,喷徐到所述碳纳米管改性锌粉层表面既得所述面漆层。
49.请参阅图5和图6,实施例3,本发明还提供一种碳纳米管改性耐磨耐腐复合涂层的制作方法,包括如下步骤:
s1:将2%所述fe和97.8%所述zn的粉末与0.2%所述cnts在乙醇中球磨60小时,然后在惰性气氛下干燥15小时得混合粉末,接着采用连续挤压的方式将混合粉末挤压形成直径为2
‑ꢀ
3mm的丝材,对丝材进行碱洗,然后盘卷后备用;s2:将船体表面喷砂清理,除去沙、泥、锈、油污等杂物,并在船体表面形成麻面;采用火焰热喷涂工艺在船体的表面进行丝材的喷涂,即形成碳纳米管改性锌铁合金层;s3:将12%所述聚氨酯、6%所述柔性树脂和15%所述水混合搅拌20min,制得聚氨酯复合乳液,向聚氨酯复合乳液中添加8%所述氧化锌-氮化铝-碳纳米管,并搅拌240min后,加入43%所述环氧树脂、5%所述高岭土和11%所述碳化硅与氧化铁填料,并搅拌240min,喷涂至所述碳纳米管改性锌铁合金层表面得到所述底漆层;s4:碳纳米管的制备:在流动氢气,环境下,通过c2h5oh、fe(c5h5)和s(c4h5)在1050~1180℃发生催化化学反应,生成管内掺杂铁的多壁碳纳米管;s5:球磨填料:对25%所述氧化锌粉、25%所述锌粉、40%所述氮化铝、9%所述二氧化硅粉以及1%所述改性碳纳米管混合后的混合粉末进行超声清洗烘干,然后在乙醇中对混合粉末进行球磨,通高纯氮气球磨60小时,得所述氧化锌氮化铝-碳纳米管;其中,混合粉末的粒径为300-3000目,混合粉末与磨球的质量比为1:25,球磨转速为15000 转小时;s6:碳纳米管的制备:在流动氢气环境下,通过c2h5oh、fe(c5h5)和s(c4h5)在1050
‑ꢀ
1180℃发生催化化学反应,生成管内掺杂铁的多壁碳纳米管;将管内掺杂铁的多壁碳纳米管加入到浓硫酸、浓硝酸和浓盐酸的混合溶液中氧化,然后经水洗、烘干后加入锌熔体, 450~480℃保温50min;最后经雾化制粉、筛选后得碳纳米管改性锌粉;s7:接着将15%所述固化剂熔化,加入25%所述碳纳米管改性锌粉,搅拌均匀后,造粒得共混粉末1;将25%所述环氧树脂、18%所述酚醛树脂、9%所述填料、4%所述催化剂以及4%所述添加剂熔融混炼,造粒得共混粉末2;将所述共混粉末1与所述共混粉末2混合后,喷徐到所述底漆层表面即得所述碳纳米管改性锌粉层;s8:先将所述碳纳米管溶解于所述聚氨酯中,所述碳纳米管在所述聚氨酯中的质量分数为10%;然后加入所述含氢氯氟烃,加热至100~120℃,保温4小时,脱水烘干;加入所述碳化硅与氮化铝填料研磨60小时,脱水烘干,制得所述纳米助剂,然后将40%所述环氧树脂、15%所述酚醛树脂、5%所述颜料、15%所述碳化硅与氮化铝填料、2%所述纳米助剂以及23%所述水混合搅拌40min,喷徐到所述碳纳米管改性锌粉层表面既得所述面漆层。
50.请参阅图7至图9,实施例4,本发明还提供一种碳纳米管改性耐磨耐腐复合涂层的制作方法,包括如下步骤:s1:将3%所述fe和96.8%所述zn的粉末与0.2%所述cnts在乙醇中球磨60小时,然后在惰性气氛下干燥15小时得混合粉末,接着采用连续挤压的方式将混合粉末挤压形成直径为2
‑ꢀ
3mm的丝材,对丝材进行碱洗,然后盘卷后备用;s2:将船体表面喷砂清理,除去沙、泥、锈、油污等杂物,并在船体表面形成麻面;采用火焰热喷涂工艺在船体的表面进行丝材的喷涂,即形成碳纳米管改性锌铁合金层;s3:将12%所述聚氨酯、6%所述柔性树脂和15%所述水混合搅拌20min,制得聚氨酯复合乳液,向聚氨酯复合乳液中添加8%所述氧化锌-氮化铝-碳纳米管,并搅拌240min后,加入43%所述环氧树脂、5%所述高岭土和11%所述碳化硅与氧化铁填料,并搅拌240min,喷涂至所述碳纳米管改性锌铁合金层表面得到所述底漆层;
s4:碳纳米管的制备:在流动氢气,环境下,通过c2h5oh、fe(c5h5)和s(c4h5)在1050~1180℃发生催化化学反应,生成管内掺杂铁的多壁碳纳米管;s5:碳纳米管的改性处理:将管内掺杂铁的多壁碳纳米管加入到浓硫酸与0.5mol/l的苯磺酸混合溶液中,加热至40-60℃,保温90min,然后经水洗,干燥,得到改性碳纳米管;s6:球磨填料:对25%所述氧化锌粉、25%所述锌粉、40%所述氮化铝、9%所述二氧化硅粉以及1%所述改性碳纳米管混合后的混合粉末进行超声清洗烘干,然后在乙醇中对混合粉末进行球磨,通高纯氮气球磨60小时,得所述氧化锌氮化铝-碳纳米管;其中,混合粉末的粒径为300-3000目,混合粉末与磨球的质量比为1:25,球磨转速为15000 转小时;s7:碳纳米管的制备:在流动氢气环境下,通过c2h5oh、fe(c5h5)和s(c4h5)在1050
‑ꢀ
1180℃发生催化化学反应,生成管内掺杂铁的多壁碳纳米管;将管内掺杂铁的多壁碳纳米管加入到浓硫酸、浓硝酸和浓盐酸的混合溶液中氧化,然后经水洗、烘干后加入锌熔体, 450~480℃保温50min;最后经雾化制粉、筛选后得碳纳米管改性锌粉;s8:接着将15%所述固化剂熔化,加入25%所述碳纳米管改性锌粉,搅拌均匀后,造粒得共混粉末1;将25%所述环氧树脂、18%所述酚醛树脂、9%所述填料、4%所述催化剂以及4%所述添加剂熔融混炼,造粒得共混粉末2;将所述共混粉末1与所述共混粉末2混合后,喷徐到所述底漆层表面即得所述碳纳米管改性锌粉层;s9:先将所述碳纳米管溶解于所述聚氨酯中,所述碳纳米管在所述聚氨酯中的质量分数为10%;然后加入所述含氢氯氟烃,加热至100~120℃,保温4小时,脱水烘干;加入所述碳化硅与氮化铝填料研磨60小时,脱水烘干,制得所述纳米助剂,然后将40%所述环氧树脂、15%所述酚醛树脂、5%所述颜料、15%所述碳化硅与氮化铝填料、2%所述纳米助剂以及23%所述水混合搅拌40min,喷徐到所述碳纳米管改性锌粉层表面既得所述面漆层。
51.请参阅图10至图12,实施例5,本发明还提供一种碳纳米管改性耐磨耐腐复合涂层的制作方法,包括如下步骤:s1:将3%所述fe和96.8%所述zn的粉末与0.2%所述cnts在乙醇中球磨60小时,然后在惰性气氛下干燥15小时得混合粉末,接着采用连续挤压的方式将混合粉末挤压形成直径为2
‑ꢀ
3mm的丝材,对丝材进行碱洗,然后盘卷后备用;s2:将船体表面喷砂清理,除去沙、泥、锈、油污等杂物,并在船体表面形成麻面;采用火焰热喷涂工艺在船体的表面进行丝材的喷涂,即形成碳纳米管改性锌铁合金层;s3:将12%所述聚氨酯、6%所述柔性树脂和15%所述水混合搅拌20min,制得聚氨酯复合乳液,向聚氨酯复合乳液中添加8%所述氧化锌-氮化铝-碳纳米管,并搅拌240min后,加入43%所述环氧树脂、5%所述高岭土和11%所述碳化硅与氧化铁填料,并搅拌240min,喷涂至所述碳纳米管改性锌铁合金层表面得到所述底漆层;s4:碳纳米管的制备:在流动氢气,环境下,通过c2h5oh、fe(c5h5)和s(c4h5)在1050~1180℃发生催化化学反应,生成管内掺杂铁的多壁碳纳米管;s5:碳纳米管的改性处理:将管内掺杂铁的多壁碳纳米管加入到浓硫酸、浓硝酸和浓盐酸的混合溶液中,然后经水洗,干燥,得到改性碳纳米管;s6:球磨填料:对25%所述氧化锌粉、25%所述锌粉、40%所述氮化铝、9%所述二氧化硅粉以及1%所述改性碳纳米管混合后的混合粉末进行超声清洗烘干,然后在乙醇中对混合粉末进行球磨,通高纯氮气球磨60小时,得所述氧化锌氮化铝-碳纳米管;其中,混合粉末的
粒径为300-3000目,混合粉末与磨球的质量比为1:25,球磨转速为15000 转小时;s7:碳纳米管的制备:在流动氢气环境下,通过c2h5oh、fe(c5h5)和s(c4h5)在1050
‑ꢀ
1180℃发生催化化学反应,生成管内掺杂铁的多壁碳纳米管;将管内掺杂铁的多壁碳纳米管加入到浓硫酸、浓硝酸和浓盐酸的混合溶液中氧化,然后经水洗、烘干后加入锌熔体, 450~480℃保温50min;最后经雾化制粉、筛选后得碳纳米管改性锌粉;s8:接着将15%所述固化剂熔化,加入25%所述碳纳米管改性锌粉,搅拌均匀后,造粒得共混粉末1;将25%所述环氧树脂、18%所述酚醛树脂、9%所述填料、4%所述催化剂以及4%所述添加剂熔融混炼,造粒得共混粉末2;将所述共混粉末1与所述共混粉末2混合后,喷徐到所述底漆层表面即得所述碳纳米管改性锌粉层;s9:先将所述碳纳米管溶解于所述聚氨酯中,所述碳纳米管在所述聚氨酯中的质量分数为10%;然后加入所述含氢氯氟烃,加热至100~120℃,保温4小时,脱水烘干;加入所述碳化硅与氮化铝填料研磨60小时,脱水烘干,制得所述纳米助剂,然后将40%所述环氧树脂、15%所述酚醛树脂、5%所述颜料、15%所述碳化硅与氮化铝填料、2%所述纳米助剂以及23%所述水混合搅拌40min,喷徐到所述碳纳米管改性锌粉层表面既得所述面漆层。
52.对比例:使用申请号为201810946198.0 的专利制备的涂层。
53.针对上述实施方式1至5以及对比例得到的涂层性能指标进行检测,包括涂膜厚度、光泽度、附着力、硬度、抗冲击强度、耐水性、耐盐水性。
54.检测方法如下:1)涂膜厚度的测定根据gbt 13452 .2-92,以测厚仪测定漆膜厚度,在漆膜完全干燥并形成硬膜的前提下,将测厚仪放置在样板表面,确保测厚仪与仪器垂直,然后转动表盘以使测厚仪量程大于漆膜厚度,按下测量按钮,待表头不再转动时读数,同一个板测三次然后求平均值,误差不应超过+2um,且测试点距离不能太近。
55.2)涂膜光泽度的确定根据gb 9754-88,在对光泽度计进行先高光泽度后低光度的校准之后,然后对同一个板不同点读数,取3个点,误差不小于5个单位,然后求平均值。
56.3)漆膜附着力的测定( 漆膜的划格实验)按gbt 9286-1998,将板平放在桌面上以保证实验过程样板不会变形。
57.手握划格器,均匀施力匀速地在样板_上横着划一段距离的划痕,然后保持相同的力度与速度与之前的划痕成90再划一段相同的距离,得到格阵,观察漆膜脱落程度,若脱落得太厉害,用软毛刷沿着格阵线的方向刷一刷再观察效果。
58.同-块板在不同的部位至少测试三次,若三次结果差值超过一个单位等级,则作废。
59.4)涂膜硬度的测定按照gbt 6739-2006铅笔法测定漆膜硬度,参照gb/t 13452 .2-92在确保漆膜厚度误差不大的情况下,准备6b (软)到6h (硬)的铅笔各
‑ꢀ‑
支,利用小车按照铅笔从硬到软的顺序用铅笔在涂膜的表面上推进至少7mm,观察漆膜破损情况,可借助橡皮轻擦表面以方便观察,不能损伤涂膜表面的铅笔硬度即为漆膜硬度。
60.5)漆膜抗冲击性能的测定(快速变形实验)按照gbt 20624 .2-2006, 先将重锤提升到导管上最高高度固定,再将漆膜样板平贴放在实验装置底座的支撑面上,在确保每冲击点与边缘之间的距离不小于15 mm的前提下,释放重锤,使其自由下落到冲头上。
61.升高重锤,取出样板并用放大镜观察,若样板有明显的裂纹,降低重锤高度,重复前面的实验步骤,直至首次观察不到明显裂纹,记录此时的冲击强度。
62.6)漆膜耐水性的测定按照gbt 1733-93,采用浸水实验法,将样板浸泡在蒸馏水中,样板之间不应贴合,每天观察漆膜是否有失光、发白、起泡、起皱、生锈等现象,若出现,则记录时间,单位:天。
63.7)耐盐水性按照gbt 10834-1989,将样板浸泡于预先配制好的5%氯化钠水溶液中,每天观察是否出现失光、变色、生锈、起泡、脱落和裂纹等破坏现象,观察时,用自来水冲洗样板表面,并用软布轻轻擦拭样板表面,在观察到破坏现象的那天,记录时间,单位:天。
64.8)摩擦系数和磨损量将漆膜样板水平固定在摩擦磨损实验仪工作台,载荷20n、滑动速度1m/s、摩擦时间5min,测得平均摩擦系数和磨损量。
65.检测后的性能指标结果如下图6所示。
66.以上所揭露的仅为本发明一种较佳实施例而已,当然不能以此来限定本发明之权利范围,本领域普通技术人员可以理解实现上述实施例的全部或部分流程,并依本发明权利要求所作的等同变化,仍属于发明所涵盖的范围。