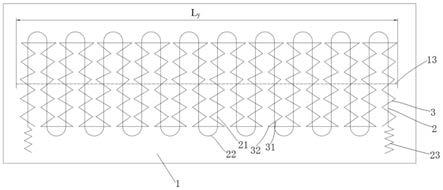
1.本发明涉及汽车配件技术领域,具体而言,涉及一种汽车内饰件基板、基板的制备方法及汽车内饰件。
背景技术:2.为了提高车辆安全性,在汽车方向盘、仪表盘、车门等部位会设置安全气囊,安全气囊安装在汽车内饰件中,由气囊门遮蔽,气囊点爆过程中,气囊门会绕着转轴打开并翻转。现有技术在气囊门的转轴部位设有网格布,汽车内饰件的基板上设有固定件,网格布固定在固定件上。气囊门打开时,网格布会用自身的强度将气囊门和汽车内饰件紧紧固定住,防止气囊门撕裂飞出。
3.但是采用网格布的固定结构存在一些不足,气囊门打开时网格布需要承受很大的撕裂力,因此对网格布延伸断裂等性能要求极高,需要采用特殊工艺编织,还需要经过特殊压缩工艺处理,其造价昂贵,生产成本高;另外汽车内饰件基板的材料受限,非纯注塑零件难以固定网格布,且基板上设置固定件,需要通过双料注塑工艺成型,这种工艺需要两幅模具进行两次注塑,降低了生产效率,增加了设备成本。
技术实现要素:4.本发明的目的是提供一种新的气囊门防撕裂结构,所要解决的技术问题上如何降低气囊门撕裂飞出风险,以及如何降低汽车内饰件的制造成本。
5.为解决上述问题,本发明第一方面提供一种汽车内饰件基板,包括基板本体和固定在所述基板本体上的受力线,所述受力线与所述基板本体缝合连接,所述基板本体包括气囊门,所述基板本体上设有弱化槽,所述弱化槽的延伸线构成所述气囊门的边缘,所述弱化槽两端之间的连线构成所述气囊门的转轴,所述受力线的设置位置与所述转轴对应。
6.相对于现有技术,本发明在基板本体上设置受力线,安全气囊打开时,气囊门沿弱化槽撕裂并沿转轴翻转,当转轴被会撕裂时受力线拉住气囊门,防止气囊门与基板本体完全分离,避免气囊门飞出损伤车内人员,与现有技术设置单独的网格布固定气囊门的结构相比,本发明将受力线直接固定在基板本体上,固定气囊门效果更好,生产工艺更加简单,可以提高生产效率,降低生产成本,具有很高的经济价值和推广前景。
7.在优选或可选的实施方式中,所述受力线包括多个拉伸部和多个弯折部,各所述拉伸部之间通过所述弯折部连接,各所述拉伸部穿过所述转轴,各所述弯折部设置在所述转轴的两侧。由此,多个拉伸部可以分摊安全气囊打开时的爆破力,降低对于受力线本身性能的要求,弯折部能够增加受力线与基板本体之间的摩擦力,分摊部分施加在拉伸部上的力。
8.在优选或可选的实施方式中,所述拉伸部为直线形。由此,拉伸部能发挥最大的性能,且便于拉伸部布置。
9.在优选或可选的实施方式中,各所述拉伸部之间相互平行。由此,利于各拉伸部之
间均匀分摊受力,提高受力线整体的承受能力。
10.在优选或可选的实施方式中,各所述拉伸部之间的间距相等。由此,均匀布置拉伸部,使各拉伸部之间受力更加均匀。
11.在优选或可选的实施方式中,所述拉伸部与所述转轴之间的夹角为α,90
°
≥α>0
°
。由此,限定拉伸部与转轴之间的夹角,转轴撕裂时拉伸部可以发挥其拉伸性能。
12.在优选或可选的实施方式中,所述拉伸部与所述转轴之间的夹角为α,90
°
≥α≥60
°
。由此,进一步限定拉伸部与转轴之间的夹角,使拉伸部更好地发挥其拉伸性能。
13.在优选或可选的实施方式中,各所述拉伸部的长度相等。由此,有利于各拉伸部均匀受力,且便于受力线布置。
14.在优选或可选的实施方式中,所述拉伸部的长度为l
s
,100mm≥2l
s*
sinα≥1mm。由此,限定拉伸部长度,保证每个拉伸部都能承受一定的拉力。
15.在优选或可选的实施方式中,所述转轴的长度为l
y
,所述拉伸部的数量为x,10cm≥l
y
/x≥0.5cm。由此,限定拉伸部的数量,保证受力线整体的承受冲击能力。
16.在优选或可选的实施方式中,所述受力线的延伸率为10%
‑
100%。由此,限定受力线的性能,保证受力线整体的承受冲击能力。
17.在优选或可选的实施方式中,所述受力线的断裂强度为500
‑
50000n/cm。由此,限定受力线的性能,保证受力线整体的承受冲击能力。
18.在优选或可选的实施方式中,所述弯折部为u形、v形或]形。由此,使弯折部能够增加受力线与基板本体之间的摩擦力,且便于受力线布置。
19.在优选或可选的实施方式中,各所述拉伸部的长度和与各所述弯折部的长度和的比例为1:10
‑
10:1。由此,可以根据需要承受的拉力设计拉伸部与弯折部的长度和比例,以此调整受力线能承受的总爆破力。
20.在优选或可选的实施方式中,所述受力线包括设置在两端的连接部,所述连接部与所述基板本体缝合连接。由此,将受力线的两端缝合在基板本体上,连接可靠,加工方便。
21.在优选或可选的实施方式中,所述连接部的形状为折线形。由此,制约了受力线的大幅度位移,避免受力线两端与基板本体脱离。
22.在优选或可选的实施方式中,所述连接部中相邻折线的夹角为1
°‑
89
°
。由此,进一步提高连接部的连接可靠度,避免其与基板本体脱离。
23.在优选或可选的实施方式中,所述连接部缝合的针脚密度为1
‑
10个/cm2。由此,保证连接部与基板本体连接可靠。
24.在优选或可选的实施方式中,所述受力线由一种或多种材料的纱线编织而成。由此,受力线对材料没有特殊要求,生产成本较低。
25.在优选或可选的实施方式中,所述受力线由一根或多根纱线编织而成。由此,受力线可以通过增加纱线数量来调整性能,不需要采用特殊工艺或材料,生产成本较低。
26.在优选或可选的实施方式中,还包括固定线,所述固定线与所述基板本体连接,并将所述受力线固定在所述基板本体上。由此,由固定线将受力线固定在基板本体上,加工简便,固定可靠,受力线不会与基板本体脱离。
27.在优选或可选的实施方式中,所述固定线为折线形,所述固定线包括固定部和转折部,各所述固定部之间通过所述转折部连接,各所述转折部分布在所示受力线两侧,各所
述固定部压住所述受力线。由此,爆破时受力线在固定线的挤压下可以获得更大摩擦力,分摊部分施加于受力线上的拉力,各固定部之间可以分摊受力。
28.在优选或可选的实施方式中,所述受力线的总长度为l
x
,所述固定部的数量为y,则10mm≥l
x
/y≥0.5mm。由此,固定部的数量可以根据所需承受的冲击力进行调整,保证固定部不会拉断。
29.在优选或可选的实施方式中,相邻所述固定部之间的夹角为1
°‑
89
°
。由此,提高固定部的固定效果,避免受力线与基板本体脱离。
30.在优选或可选的实施方式中,各相邻所述固定部之间的夹角相等。由此,使各固定部之间可以均匀分摊受力。
31.在优选或可选的实施方式中,各所述转折部与所述基板本体缝合连接。由此,将固定线多点缝合在基板本体上,连接可靠,加工方便。
32.在优选或可选的实施方式中,所述转折部缝合的针脚密度为1
‑
10个/cm2。由此,保证固定线与基板本体连接可靠,不会脱离。
33.在优选或可选的实施方式中,所述固定线由一种或多种材料的纱线编织而成。由此,固定线对材料没有特殊要求,生产成本较低。
34.在优选或可选的实施方式中,所述固定线由一根或多根纱线编织而成。由此,固定线可以通过增加纱线数量来调整性能,不需要采用特殊工艺或材料,生产成本较低。
35.在优选或可选的实施方式中,所述基板本体由纤维板材料制成。由此,受力线可以缝合在基板本体上,基板本体不需要通过双料注塑工艺成型,降低了生产成本。
36.本发明的第二方面提供一种汽车内饰件基板的制备方法,包括以下步骤:将基板本体定位,在基板本体上开设弱化槽,弱化槽构成气囊门的边缘,弱化槽两端之间的连线构成气囊门的转轴;在基板本体上缝合受力线,受力线的位置与转轴对应;将基板本体移动至热压机中热压成型,制得汽车内饰件基板。
37.相对于现有技术,该制备方法工艺步骤少,生产方法简单,能提高生产效率,降低生产成本。
38.本发明的第三方面提供一种汽车内饰件,包括上述的汽车内饰件基板。
39.相对于现有技术,该汽车内饰件采用了一种全新结构的基板,由受力线来固定住气囊门,不需要设置特殊工艺处理的网格布,因此能降低其制备成本,提高生产效率。
附图说明
40.图1为本发明实施例中汽车内饰件的剖视图;
41.图2为图1中a处的局部放大图;
42.图3为本发明实施例中汽车内饰件的后视图;
43.图4为本发明实施例中基板的结构图;
44.图5为本发明实施例中基板本体上受力线和固定线的布置图;
45.图6为本发明实施例中受力线和固定线的尺寸标示图。
46.附图标记说明:
[0047]1‑
基板本体,11
‑
气囊门,12
‑
弱化槽,13
‑
转轴,14
‑
缝线区,2
‑
受力线,21
‑
拉伸部,22
‑
弯折部,23
‑
连接部,3
‑
固定线,31
‑
固定部,32
‑
转折部,4
‑
表皮,5
‑
气囊框。
具体实施方式
[0048]
为使本发明实施例的目的、技术方案和优点更加清楚,下面将结合本发明实施例中的附图,对本发明实施例中的技术方案进行清楚、完整地描述,显然,所描述的实施例是本发明一部分实施例,而不是全部的实施例。通常在此处附图中描述和示出的本发明实施例的组件可以以各种不同的配置来布置和设计。
[0049]
因此,以下对在附图中提供的本发明的实施例的详细描述并非旨在限制要求保护的本发明的范围,而是仅仅表示本发明的选定实施例。基于本发明中的实施例,本领域普通技术人员在没有作出创造性劳动前提下所获得的所有其他实施例,都属于本发明保护的范围。
[0050]
应注意到:相似的标记和字母在下面的附图中表示类似项,因此,一旦某一项在一个附图中被定义,则在随后的附图中不需要对其进行进一步定义和解释。
[0051]
在本发明的描述中,需要说明的是,除非另有明确的规定和限定,术语“安装”、“设置”、“连接”等,应做广义理解,例如“连接”,可以是固定连接,也可以是可拆卸连接,或一体地连接;可以是机械连接,也可以是电连接;可以是直接相连,也可以通过中间媒介间接相连,可以是两个元件内部的连通。对于本领域的普通技术人员而言,可以具体情况理解上述术语在本发明中的具体含义。
[0052]
以下结合附图对本发明的优选实施例进行说明,应当理解,此处所描述的优选实施例仅用于说明和解释本发明,并不用于限定本发明。
[0053]
结合图1至图4所示,本发明的实施例提供一种汽车内饰件,其包括依次设置的表皮4、基板和气囊框5,表皮4贴在基板的表面,气囊框5设置在基板的背面,汽车的安全气囊适于设置在气囊框5中。基板包括基板本体1,基板本体1包括气囊门11,基板本体1上设有凹陷的弱化槽12,弱化槽12构成了气囊门11的边缘,弱化槽12两端之间的连线构成气囊门11的转轴13,如图3中点划线所示。安全气囊打开时产生爆破力,气囊门11沿弱化槽12撕裂并沿转轴13翻转,由于爆破力较大,气囊门11的转轴13处会发生撕裂。
[0054]
本实施例的基板包括受力线2,在转轴13对应部位划定缝线区14,即图3中虚线包围部位,受力线2设置在缝线区14内,并与基板本体1缝合连接。当转轴13被撕裂时,受力线2会拉住气囊门11,防止气囊门11与基板本体1完全分离,避免气囊门11飞出损伤车内人员,提高安全性。
[0055]
本实施例将受力线2直接固定在基板本体1上,与现有技术单独设置网格布的结构相比,固定气囊门11效果更好,且生产工艺更加简单,可以提高生产效率,降低生产成本,具有很高的经济价值。
[0056]
本实施例中基板本体1的材料为nfpp板材,在其他实施方式中,基板本体1可以选用其他材质的纤维板,如ppgf等。相较于注塑件,纤维板更加环保耐用,也便于受力线2与基板本体1缝合连接。同时基板本体1不需要如现有技术一样通过双料注塑工艺成型,可以减少生产设备的使用,降低了生产成本。
[0057]
结合图5和图6所示,受力线2包括多个拉伸部21和多个弯折部22,拉伸部21用于拉住气囊门11,拉伸部21穿过转轴13;弯折部22用于连接各拉伸部21,各弯折部22设置在转轴13的两侧。多个拉伸部21可以分摊安全气囊打开时的爆破力,降低对于受力线2本身性能的要求,弯折部22除了具有连接拉伸部21的作用,还能够增加受力线2与基板本体1之间的摩
擦力,分摊部分施加在拉伸部21上的力。受力线2的两端和设有连接部23,连接部23与基板本体1缝合连接,将受力线2的两端缝合在基板本体1上,连接可靠,加工方便。
[0058]
进一步地,对受力线2各部位的形状进行限制,可以提高其抗冲击能力和连接可靠性。本实施例中,拉伸部21为直线形,由此拉伸部21能发挥最大的性能,且便于拉伸部21布置。弯折部22为u形,u形的弯折部22易于设置,且能使受力线2与基板本体1之间的摩擦力较大。在其他的实施方式中,弯折部22也可以为v形或]形。连接部23的形状为折线形,可以制约受力线2的大幅度位移,避免受力线2两端与基板本体1脱离。
[0059]
进一步地,受力线2主要由拉伸部21来拉住气囊门11,通过对拉伸部21的结构进行设计,可以分摊每个拉伸部21受到的力,以此提高其承受能力,防止拉伸部21断裂。本实施例中,各拉伸部21之间相互平行,各拉伸部21之间的间距相等,且各拉伸部21的长度相等,这样有利于各拉伸部21之间均匀分摊受力,提高受力线2整体的承受能力。
[0060]
本实施例中,转轴13的长度l
y
为25cm,拉伸部21的数量x为20个,l
y
/x=1.25cm。在其他实施方式中,对拉伸部21的数量进行限定,满足10cm≥l
y
/x≥0.5cm,,通过控制拉伸部21的数量,可以调整受力线2整体的承受冲击能力,由此保证汽车内饰件的安全性。
[0061]
本实施例中,拉伸部21与转轴13之间的夹角α为90
°
,在其他实施方式中,90
°
≥α>0
°
,优选90
°
≥α≥60
°
。限定拉伸部21与转轴13之间的夹角,使转轴13撕裂时拉伸部21可以发挥其拉伸性能,一般情况下转轴13垂直方向上受力最大,因此90
°
≥α≥60
°
时,受力线2可以更好地发挥性能。
[0062]
本实施例中,拉伸部21的长度为l
s
为60mm,拉伸部21与转轴13垂直方向上的延伸长度为2l
s
*sinα=60mm。在其他实施方式中,限定拉伸部21沿转轴13垂直方向上的延伸长度,100mm≥2ls*sinα≥1mm,保证其拉伸效果,避免拉伸撕裂,优选为70mm≥2ls*sinα≥30mm,进一步地提升其拉伸能力。
[0063]
本实施例中,各拉伸部21的长度和与各弯折部22的长度和的比例为5:1,在其他实施方式中,各拉伸部21的长度和与各弯折部22的长度和的比例为1:10
‑
10:1。可以根据需要承受的拉力设计拉伸部21与弯折部22的长度和比例,以此调整受力线2能承受的总爆破力。
[0064]
由于本实施例中受力线2的各拉伸部21之间均匀分摊受力,整体的承受能力大幅提高,对于受力线2本身性能要求降低。受力线2可以由一种或多种材料的纱线编织而成,如芳纶线、pet线、pp线等,相较于现有的网格布,材料成本大幅降低。受力线2也可以由一根或多根纱线编织而成,可以通过增加纱线数量来调整性能,而不需要采用特殊工艺或材料,生产成本较低。
[0065]
进一步地,限定述受力线2的性能,时其延伸率为10%
‑
100%,受力线2的断裂强度为500
‑
50000n/cm,保证受力线2整体的承受冲击能力。
[0066]
本实施例中,连接部23为折线形,连接部23中相邻折线的夹角为β为45
°
,在其他实施方式中,89
°
≥β≥1
°
,优选45
°
≥β≥15
°
,通过调整β可以提高连接部23的连接可靠度,避免其与基板本体1脱离。
[0067]
进一步地,连接部23缝合的针脚密度为1
‑
10个/cm2,可以根据所需承受的力调整针脚密度,保证连接部23与基板本体1连接可靠。
[0068]
结合图5和图6所示,基板本体1上还设有固定线3,其与基板本体1缝合连接,固定线3沿受力线2延伸方向设置,用于将受力线2固定在基板本体1上。本实施例通过固定线3将
受力线2固定在基板本体1上,加工简便,固定可靠,受力线2不会与基板本体1脱离。
[0069]
固定线3为折线形,其包括固定部31和转折部32,各固定部31之间通过转折部32连接,各转折部32分布在受力线2两侧,各固定部31压住受力线2。转折部32与基板本体1缝合连接,由此将固定线3多点缝合在基板本体1上,连接可靠,加工方便。
[0070]
进一步地,限定转折部32缝合的针脚密度为1
‑
10个/cm 2
,保证固定线3与基板本体1连接可靠,不会脱离。
[0071]
安全气囊爆破时受力线2在固定线3的挤压下可以获得更大摩擦力,分摊部分施加于受力线2上的拉力,各固定部31之间也可以分摊受力,防止固定线3断裂。
[0072]
本实施例中,各固定部31之间相互分摊受力,降低了对固定线3本身性能的要求,可以由一种或多种材料的纱线编织而成,生产成本较低。也可以由一根或多根纱线编织而成,通过增加纱线数量来调整性能,不需要采用特殊工艺或材料,生产成本较低。
[0073]
进一步地,对固定线3的结构进行限定,可以提高其受力能力。相邻固定部31之间的夹角γ相等,本实施例中γ为45
°
。在其他实施方式中89
°
≥γ≥1
°
,优选45
°
≥γ≥15
°
,通过调整相邻固定部31的夹角,可以提高固定部31的固定效果,防止受力线2与基板本体1脱离。
[0074]
在本实施例中,受力线2的总长度l
x
为1152mm,固定部31的数量为y为160个,l
x
/y=7.2mm。在其他实施方式中,限定10mm≥l
x
/y≥0.5mm,固定部31的数量可以根据所需承受的冲击力进行调整,保证固定部31不会拉断。
[0075]
本发明的另一实施例提供一种汽车内饰件基板的制备方法,包括以下步骤:
[0076]
s1、将基板本体1定位,在基板本体1上开设弱化槽12,弱化槽12构成气囊门11的边缘,弱化槽12两端之间的连线构成气囊门11的转轴13;
[0077]
s2、在基板本体1上缝合受力线2,受力线2的位置与转轴13对应,位于缝线区14内;
[0078]
s3、将基板本体1移动至热压机中热压成型,制得汽车内饰件基板。
[0079]
本实施例的制备方法工艺步骤少,生产方法简单,能提高生产效率,减少生产设备使用,降低生产成本,具有很高的经济价值。
[0080]
进一步地,步骤s2中受力线2的布置结构与参见上述实施例中受力的布局结构,s2还包括缝合固定线3,将受力线2固定在基板本体1上,保证受力线2能承受安全气囊爆破时产生的冲击力。
[0081]
最后应说明的是,以上各实施例仅用以说明本发明的技术方案,而非对其限制;尽管参照前述各实施例对本发明进行了详细的说明,本领域的普通技术人员应当理解:其依然可以对前述各实施例所记载的技术方案进行修改,或者对其中部分或者全部技术特征进行等同替换;而这些修改或者替换,并不使相应技术方案的本质脱离本发明各实施例技术方案的范围。