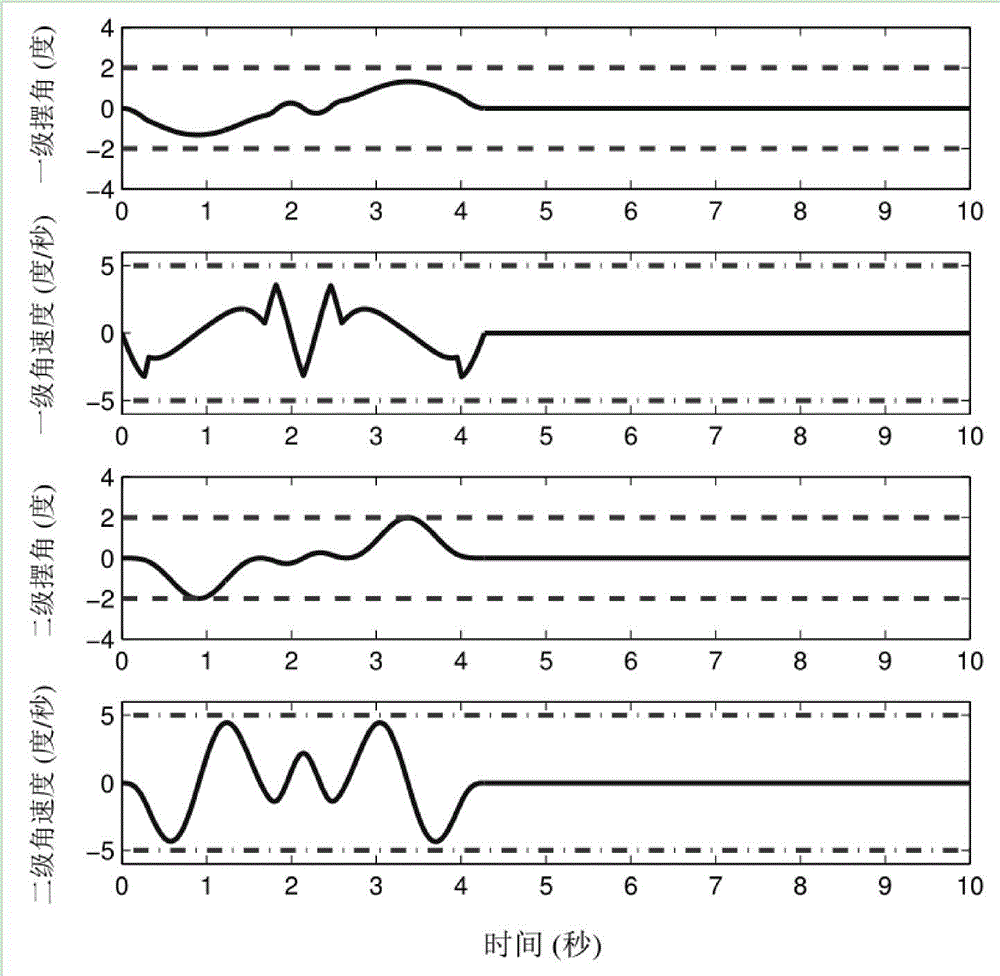
本发明属于非线性欠驱动机电系统自动控制的技术领域,特别是涉及一种基于伪谱法的双摆吊车全局时间最优轨迹规划方法。
背景技术:在工业生产过程中,为运送负载到所期望的位置,包括桥式吊车、悬臂式吊车、塔式吊车、船用吊车在内的各类吊车系统,有着非常广泛的应用。为了简化吊车系统的机械结构,往往不直接控制负载,而是通过台车的运动,间接地拖动负载至目标位置。这种结构带来的结果是,吊车系统的控制输入维数小于待控自由度维数。具有该特性的系统即所谓的欠驱动系统[1]。相比全驱动系统,由于欠驱动特性的存在,欠驱动系统往往更难控制,而在实际生产中,吊车系统往往是由经验丰富的工人操作。如果发生误操作,可能引起负载剧烈摆动导致碰撞,甚至发生安全事故。因此,对吊车系统自动控制方法的研究具有现实意义与广泛应用价值,得到了广大学者的关注。对于桥式吊车系统,主要的控制目标包括两个方面,即快速且精确的台车定位与负载摆动的抑制与消除。然而,这两方面通常是互相矛盾的,即过快的台车运动往往导致较大的负载摆动。因此,同时实现这两方面的控制目标具有较高的难度。为了获得较好的控制效果,目前国内外学者已经提出了很多吊车系统自动控制方法。Tuan等提出了基于部分反馈线性化的控制方法[2-3],可以简化桥式吊车系统的控制算法设计。在文献[4],[5]中,Singhose等利用输入整形的思想对吊车系统进行控制,可有效地抑制负载残余摆动。为处理不确定的外界干扰,研究人员利用滑模算法控制吊车系统[6-7],可以获得很好的鲁棒性。胡洲等提出了一种非线性信息融合控制方法[8],可以处理控制器输入饱和的问题,实现对吊车系统的高性能控制。文献[9],[10]提出了基于能量与无源性的控制策略,可获得较好的效果。除此之外,近年来,包括遗传算法[11]、模糊控制[12]等一些智能控制方法同样在吊车控制领域有着一定的应用。众所周知,吊车系统的负载摆动由台车的加减速运动引起,在台车运动与负载摆动之间存在着较强的耦合。基于此,可以为台车规划一条合适的轨迹,当台车按照该轨迹运动时,即可实现对其快速精确定位的目标。同时,考虑到摆角抑制与消除的要求,在轨迹规划过程中,通过深入分析与合理利用台车运动与负载摆动之间的耦合关系,可以规划出一条具有消摆能力的台车轨迹。这样即可完成台车快速精确定位与负载消摆的双重目标。基于该思想,研究人员已提出了很多吊车轨迹规划方法[13-17]。例如,在文献[13]中,Uchiyama等提出了一种针对悬臂吊车的开环控制策略,为了消除残余摆动,他们为悬臂的水平运动规划了一条S型轨迹。文献[14]则提出了一种基于相平面分析的轨迹规划方法,它可以较好地抑制负载摆动,并消除了残余摆动。对于吊车系统,虽然上述各种方法在理想情况下可以得到较好的控制效果,但是这些方法均假设吊钩的质量可以忽略且负载可看作质点,并将吊车系统的负载摆动视为单摆系统。若吊钩的质量较大,无法忽略,或者负载形状很大,不能简单看作质点,在这种情况下,吊车系统的摆动将会呈现出双摆现象,即吊钩绕台车进行一级摆动,同时负载绕吊钩发生二级摆动。此时,上述的单摆吊车控制方法无法取得令人满意的控制性能,目前仅存在极少考虑双摆效应的吊车系统控制策略。文献[18-20]通过分析双摆吊车系统的固有频率,将输入整形的方法成功地扩展到双摆吊车系统。孙宁等在考虑系统摆角约束、台车速度约束等一系列约束的前提下,提出了一种基于微分平坦理论的双摆吊车最优轨迹规划方法[21]。郭卫平等通过分析吊车系统的能量,提出了一种基于无源性的双摆吊车控制策略[22]。尽管上述控制策略可以实现对双摆吊车系统的控制,它们均无法实现全局时间最优的控制效果,即无法保证吊车系统运行效率的最大化。因此需要设计合适的控制方法,以提高吊车系统的工作效率。
技术实现要素:本发明的目的是解决现有双摆效应桥式吊车系统轨迹规划方法存在的上述不足,提供一种基于伪谱法的双摆吊车全局时间最优轨迹规划方法。本发明致力于通过分析具有双摆效应的桥式吊车系统的运动学模型,提出了一种基于伪谱法的双摆吊车全局时间最优轨迹规划方法,得到了一条全局时间最优的台车轨迹,在完成台车精确定位的同时,实现了两级负载摆动的快速抑制与消除,并将其应用于实际吊车平台进行实验,可极大地提高吊车系统的工作效率。本发明提供的基于伪谱法的双摆吊车全局时间最优轨迹规划方法包括:第1、分析轨迹约束并构造相应的优化问题分析吊车系统的控制目标,考虑包括两级摆角及台车速度和加速度上限值在内的多种约束,得出如下的以运送时间为代价函数的优化问题:其中,x(t)代表台车的位置,xf表示台车的目标位置,括号中的t表示时间,变量后面(t)表示该变量为关于时间的变量,为简明起见,在公式中略去大部分变量中的(t),T表示完成运送的总时间,min表示最小,s.t.后面接表示需要考虑的约束条件;分别表示台车位置x(t)关于时间的一阶导数和二阶导数,即台车速度与加速度;vmax,amax分别代表所允许的台车最大速度与最大加速度;θ1(t),θ2(t)分别表示一级与二级摆角,表示一级与二级角速度;θ1max,θ2max表示运送过程中允许的一级与二级最大摆角,ω1max,ω2max表示所允许的一级与二级最大角速度。第2、加速度驱动模型建立与优化问题转化分析与利用双摆桥式吊车系统,得到如下的加速度驱动系统模型:其中,ζ表示系统的全状态向量,具体定义如下:其中,x(t),分别表示台车位置与速度,θ1(t),表示一级摆角及角速度,θ2(t),表示二级摆角及角速度,括号的上标T代表矩阵的转置运算;u(t)代表该系统的系统输入,且为台车加速度;f(ζ),h(ζ)均代表以系统的全状态向量ζ为自变量的函数,由吊车系统运动学方程得到,具体形式见(7);为系统的全状态向量关于时间的导数。利用上述加速度驱动系统模型,原优化问题转化为如下的形式:其中,ζ表示系统的全状态向量,u(t)代表该系统的系统输入,且为台车加速度;括号中的t表示时间,变量后面(t)表示该变量为关于时间的变量,为简明起见,在公式中略去大部分变量中的(t),T表示完成运送的总时间,min表示最小,s.t.后面接表示需要考虑的约束条件;向量的上标T代表矩阵的转置运算;xf表示给定的台车目标位置,表示台车速度,vmax,amax分别代表所允许的台车最大速度与最大加速度;θ1(t),θ2(t)分别表示一级与二级摆角,表示一级与二级角速度;θ1max,θ2max表示运送过程中允许的一级与二级最大摆角,ω1max,ω2max表示所允许的一级与二级最大角速度。第3、基于高斯伪谱法的轨迹规划利用高斯伪谱法的思想对第2步中的优化问题进行处理与求解,具体步骤如下:第3.1、首先利用拉格朗日插值方法,选择勒让德-高斯(Legendre-Gauss,LG)点处的离散系统状态轨迹以及输入轨迹,通过离散轨迹与拉格朗日插值多项式,表示相应的近似轨迹模型。第3.2、接着,通过对近似后的轨迹模型进行求导,将系统状态的导数用拉格朗日多项式导数表示。第3.3、随后,利用离散的轨迹模型及其导数,将原系统运动学模型转化为一系列多项式方程;利用高斯积分,第2步中优化问题里的边界条件同样表示成多项式方程的形式。第3.4、最后,时间最优轨迹规划问题即转化为一种具有代数约束的非线性规划问题,通过求解即得到全局最优时间及最优轨迹。第4、轨迹跟踪通过码盘或激光传感器,测量台车位置与速度信号x(t),利用第3.4步所得待跟踪台车时间最优参考轨迹以及对应的速度轨迹,选择比例微分(proportional-derivative,PD)控制器如下:其中,F(t)代表作用在台车上的驱动力,xr(t),分别表示参考位移轨迹以及速度轨迹,kp,kd是需要调整的正的控制增益。利用该控制器,能够计算得到相应的实时控制信号,驱动吊车运动,完成控制目标。本发明方法的理论依据及推导过程第1、分析轨迹约束并构造相应的优化问题具有双摆效应的桥式吊车,其运动学模型如下所示:其中,m1,m2分别表示吊钩和负载的质量,M表示台车的质量;x(t)表示台车位移,表示x(t)关于时间的二阶导数,即台车加速度;t表示时间,变量后面(t)表示该变量为关于时间的变量,为简明起见,在公式中略去大部分变量中的(t);θ1(t),θ2(t)表示一级与二级摆角(吊钩摆角与负载绕吊钩的摆角),为相应的角速度,为角加速度;l1表示吊绳的长度,l2为等效绳长,即负载质心与吊钩质心之间的距离;g为重力加速度。对于式(1)、(2),分别两边同除以(m1+m2)l1与m2l2,并化简得:式(3)、(4)描述了台车位移x(t)与系统两级摆角θ1(t),θ2(t)之间的耦合关系,即台车的运动对负载摆动的影响。通过深入分析该耦合关系,规划一条具有消摆能力的台车轨迹,是本发明的基础。为完成时间最优轨迹规划,考虑到吊车系统在实际工作时的目标、物理约束及安全性,本发明将系统地考虑如下几个方面的轨迹约束[21]:1)为实现快速而精确的台车定位,台车从初始位置x0开始运动,经过时间T达到目标位置xf,且开始时刻与结束时刻的台车速度、加速度均为0,即其中,T表示运送过程所需要时间;对于初始位置,不失一般性,这里选取x0=0。2)考虑到实际电机的输出有界,在运送过程中,台车的速度、加速度均应保持在适当的范围内,即其中,vmax,amax分别表示允许的台车最大速度和加速度,代表台车速度与加速度的绝对值。3)为保证在运送结束时可直接对负载进行下一步的处理,台车达到目标位置后应无残余摆动且角速度也均为0,即4)为避免由于负载的剧烈摆动引起的碰撞,在运送过程中,两级摆动的摆角及角速度都应保持在允许的范围内,即其中,θ1max,θ1max分别表示一级与二级摆角允许的最大角度;ω1max,ω2max代表允许的一级与二级最大角速度。综上,构造出如下的优化问题:其中,min表示最小,s.t.后面接表示需要考虑的约束条件。接下来,将通过伪谱法求解该优化问题,并为台车规划出一条时间最优轨迹。第2、加速度驱动模型建立与优化问题转化为方便后续的轨迹规划,这里首先对双摆吊车系统模型以及优化问题(5)进行转化。为此定义系统全状态向量ζ(t)如下:其中,x(t),分别表示台车位置与速度,θ1(t),表示一级摆角及角速度,θ2(t),表示二级摆角及角速度,括号的上标T代表矩阵的转置运算。根据式(3)、(4),将台车的加速度作为系统的输入。此时,运动学模型转化为如下形式:其中,表示ζ(t)关于时间的导数;u(t)为台车加速度f(ζ),h(ζ)表示关于ζ(t)的辅助函数,具体形式如下:其中,为方便描述,定义了如下的辅助变量A,B,C,D:上式中,使用了如下的简化形式:S1=sinθ1,S2=sinθ2,C1=cosθ1,C2=cosθ2,S1-2=sin(θ1-θ2),C1-2=cos(θ1-θ2).利用所得的加速度驱动系统模型(6),原优化问题(5)以转化为:其中,ζ表示系统的全状态向量,u(t)代表该系统的系统输入,且为台车加速度;括号中的t表示时间,变量后面(t)表示该变量为关于时间的变量,为简明起见,在公式中略去大部分变量中的(t),T表示完成运送的总时间,min表示最小,s.t.后面接表示需要考虑的约束条件;向量的上标T代表矩阵的转置运算;xf表示给定的台车目标位置,表示台车速度,vmax,amax分别代表所允许的台车最大速度与最大加速度;θ1(t),θ2(t)分别表示一级与二级摆角,表示一级与二级角速度;θ1max,θ2max表示运送过程中允许的一级与二级最大摆角,ω1max,ω2max表示所允许的一级与二级最大角速度。接下来,将通过伪谱法求解该优化问题,并为台车规划出一条时间最优轨迹。第3、基于高斯伪谱法的轨迹规划为适应高斯伪谱法的要求,首先需要利用坐标变换,将轨迹对应的时间区间由t∈[0,T]转化到区间τ∈[-1,1]上,即这里的τ表示类似时间的辅助变量。随后选取K个勒让德-高斯(Legendre-Gauss,LG)点{τ1,τ2,...,τK}∈(-1,1)组成点列。这里的τ1,τ2,...,τK即代表所选取的LG点,下标表示该点的序号为1,2,...,K;K为选择的LG点的数目。LG点的选取通过求解K阶的勒让德多项式的零点获得。同时,把τ0=-1加到点列的首位,待规划的系统状态量及输入量离散表示成如下的形式:ζ(τ0),ζ(τ1),ζ(τ2),...,ζ(τK),u(τ0),u(τ1),u(τ2),...,u(τK),利用该K+1个节点,构造出K+1个拉格朗日插值多项式,具体形式如下:其中,代表序号为i的拉格朗日差值多项式,i∈{0,1,...,K};这里,τ∈[-1,1];表示连乘符号,即从序号j=0的项开始,一直乘到j=K的项,且过程中跳过j=i的项。利用式(11)以及LG点处的系统状态量和输入量的值,系统的状态量轨迹以及输入量轨迹通过下面的方式近似表出:其中,ζ(τi),u(τi)分别表示τ=τi处的系统状态量以及输入量;表示累加符号,即从序号i=0的项开始累加到i=K的项。对式(12)求导,并利用式(11)中插值函数的具体形式,计算并化简,得到状态量轨迹的导数如下:其中,表示τ=τk处的状态轨迹导数值;代表τ=τk处,拉格朗日多项式的导数值,具体形式如下:利用式(13)、(14)以及LG点处的轨迹值,对优化问题(9)中的微分方程约束进行离散化与近似化处理,具体结果如下:其中,k∈{0,1,2,...,K}。式(15)具有代数约束的形式。接下来,优化问题中的边界条件约束也需要转化成代数约束的形式,其中0时刻边界约束直接改写如下:ζ(0)=[000000]T.为表示运送过程结束时刻的边界约束,定义τK+1=1。由式(10)可知,τK+1=1即对应运送结束时刻t=T。利用高斯积分,该边界约束条件表示为:其中,ζ(τ0)即上述的系统初始状态向量;wk表示第k个勒让德权值(Legendreweight),具体值在求解LG点时一并求得。综上,优化问题中所有的约束都可以通过代数约束的形式表出,基于此,原优化问题转化成一种具有代数约束的非线性规划问题,具体如下所示:minTs.t.ζ(0)=[000000]T,ζ(τ)-χ≤0,-ζ(τ)-χ≤0,u(τ)-amax≤0,-u(τ)-amax≤0其中,向量χ的定义如下:χ=[∞vmaxθ1maxω1maxθ2maxω2max]T其中,∞代表无穷大。对于上述带约束非线性规划问题,这里选择连续二次型规划方法(sequentialquadraticprogramming,SQP)求解,得到如下的时间最优状态向量序列:ζ(τ0),ζ(τ1),ζ(τ2),...,ζ(τK),ζ(τK+1),上式即时间离散的最优状态向量序列。取每个向量的前两项(台车位移与台车速度),并进行插值,即得到相应的全局时间最优的台车位移与速度轨迹。第4、轨迹跟踪通过码盘或激光传感器,测量台车位置与速度信号x(t),利用第3步所得待跟踪台车时间最优参考轨迹以及对应的速度轨迹,选择比例微分(proportional-derivative,PD)控制器如下:其中,F(t)代表作用在台车上的驱动力,xr(t),分别表示参考位移轨迹以及速度轨迹,kp,kd是需要调整的正的控制增益。利用该控制器,能够计算得到相应的实时控制信号,驱动吊车运动,完成控制目标。本发明的优点和有益效果本发明针对具有双摆效应的桥式吊车,提出了一种基于伪谱法的双摆吊车全局时间最优轨迹规划方法。具体而言,首先将吊车系统的运动学模型转化为一种加速度驱动模型,并基于此模型,考虑各种约束,构造出带约束的优化问题;随后,利用高斯伪谱法对所得优化问题进行处理,将其转化为更方便求解的非线性规划问题。在此基础上,即可得到时间最优台车轨迹。本发明提出的这种轨迹规划方法除了考虑消摆的目标之外,还可以非常方便地处理摆角约束、角速度约束、台车速度约束、加速度约束等实际物理约束。与现有方法不同的是,本发明提出的方法可获得全局时间最优解,极大地提高了吊车系统的工作效率。最后,通过仿真与实验,验证了本发明的有效性。附图说明:图1表示本发明中轨迹规划仿真结果1(台车位移与速度曲线);图2表示本发明中轨迹规划仿真结果2(两级摆角及角速度曲线);图3表示本发明中轨迹规划实验结果;图4表示线性二次型控制器实验结果;图5表示多项式轨迹规划实验结果。具体实施方式:实施例1:分析吊车系统的控制目标,考虑包括两级摆角及台车速度和加速度上限值在内的多种约束,得到如下的以运送时间为代价函数的优化问题:这里,选择台车的目标位置为xf=0.6m,轨迹约束如下:θ1max=θ2max=2deg,vmax=0.3m/s,ω1max=ω2max=5deg/s,amax=0.15m/s2第2、加速度驱动模型建立与优化问题转化分析与利用双摆桥式吊车系统,建立如下的加速度驱动系统模型:由于该模型具体表达式过于复杂,这里不再赘述,仅给出吊车系统的相应物理参数,如下所示:M=6.5kg,m1=2.003kg,m2=0.559kg,g=9.8m/s2,l1=0.53m,l2=0.4m.接着优化问题转化为如下的形式:第3、基于高斯伪谱法的轨迹规划为实现本发明所提出的基于伪谱法的轨迹规划方法,这里使用GPOPS软件工具箱[23]以及SNOPT工具箱[24]离线求解第2步中的优化问题并得到相应的时间最优轨迹。其中,选取勒让德-高斯点参数K=750。具体的结果参见仿真实验描述部分。第4、仿真实验效果描述第4.1、仿真结果为验证本发明提出轨迹规划算法的可行性,首先在MATLAB/Simulink环境中进行数值仿真。仿真过程分为两步。第一步,按照本方法为台车规划一条时间最优的参考轨迹;第二步,假定台车按照该参考轨迹运行,得到台车及摆角的轨迹。仿真的结果如附图1、附图2所示。附图1中,虚线代表台车目标位置,点画线代表台车速度约束,实线代表仿真结果。附图2中,虚线代表角度约束,点画线代表角速度约束,实线代表仿真结果。从附图1中可以看出,当台车沿参考轨迹运行时,台车快速且精确地收敛到目标位置xf=0.6m;同时,在整个过程中,台车的速度满足所设定约束。从附图2中可以看出,台车运送过程中,两级摆角均小于所给约束值2deg;同时,角速度也在所约束范围内;且在运送结束时,两级摆角均不存在残余摆动,即快速消摆的目标也可实现。第4.2、实验结果通过码盘或激光传感器,测量台车位置与速度信号x(t),利用第3步所得待跟踪台车时间最优参考轨迹以及对应的速度轨迹,选择比例微分(proportional-derivative,PD)控制器如下:其中,F(t)代表作用在台车上的驱动力,xr(t),分别表示参考位移轨迹以及速度轨迹,kp,kd是需要调整的正的控制增益。利用该控制器,能够计算得到相应的实时控制信号,驱动吊车运动,完成控制目标。在实验中,选取的跟踪控制器控制增益为:kp=750,kd=150实验结果如附图3所示。其中,点画线代表摆角约束,实线表示实际的台车运动轨迹以及摆角轨迹。从图中可以看出,在PD控制器作用下,台车可以较好地跟踪该参考轨迹,实现快速精确台车定位的控制目标。两级摆角在整个运送过程中均保持在给定的范围内,且运送结束时,几乎没有残余摆动。该实验结果验证了本发明可以实现较好的效果。为进一步体现本发明的有效性,作为对比,这里给出了文献[21]的最优轨迹规划方法,以及线性二次型调节器(linearquadraticregulator,LQR)方法的实验结果。其中,文献[21]中轨迹规划方法的约束选取与本发明所提方法的约束一致;而对于LQR方法,其控制器表达式如下:其中,F(t)代表作用在台车上的驱动力;x(t),表示实时测量的台车位置与速度;xf即给定的目标位置,设为xf=0.6m;θ1(t),表示一级摆角及其角速度;θ2(t),表示二级摆角及其角速度,k1,k2,k3,k4,k5,k6均为相应的控制增益,具体取值见下文。同时,该方法代价函数选取如下:其中,X定义如下e(t)代表台车定位误差,e(t)=x(t)-xf;矩阵Q,R的选择如下:Q=diag{200,1,200,1,200,1},R=0.05计算得到控制器增益如下:k1=63.2456,k2=50.7765,k3=-129.3086,k4=-6.9634,k5=19.9137,k6=-6.7856.LQR方法以及文献[21]中方法,实验结果如附图4、附图5所示。其中,附图5为利用文献[21]中方法的实验结果,实线代表实验结果,点画线代表摆角约束。从附图3中可以看出,当台车跟踪所规划最优轨迹运行时,完成运送过程仅需4.095s,且整个过程中两级摆动均保持在给定约束2deg以内,运送完成时基本无残余摆动。而对于文献[21]所提方法,完成运送过程需要5.445s;对于LQR方法,完成运送过程需要7.425s。同时,LQR方法导致的一级摆动最大摆角达到6.5deg,二级摆动最大摆角达到11.5deg,远大于本发明所提方法的摆角。综上可知,本发明所设计的方法可以实现台车的精确定位以及系统两级摆动的快速消除,获得良好的控制性能。参考文献[1]LiuY,YuH.Asurveyofunderactuatedmechanicalsystems.IETControlTheory&Applications.2013,7(7):921-935[2]TuanLA,LeeSG,DangVH,MoonS,KimB.Partialfeedbacklinearizationcontrolofathree-dimensionaloverheadcrane.InternationalJournalofControl,AutomationandSystems,2013,11(4):718-727[3]TuanLA,KimGH,KimMY,LeeSG.Partialfeedbacklinearizationcontrolofoverheadcraneswithvaryingcablelengths.InternationalJournalofPrecisionEngineeringandManufacturing,2012,13(4):501-507[4]SinghoseW,KimD,KenisonM.Inputshapingcontrolofdouble-pendulumbridgecraneoscillations.ASMEJournalofDynamicSystems,Measurement,andControl,2008,130(3):034504.1-034504.7[5]BlackburnD,SinghoseW,KitchenJ,PatrangenaruV,LawrenceJ,KamoiT,TauraA.Commandshapingfornonlinearcranedynamics.JournalofVibrationandControl,2010,16(4):477-501[6]王伟,易建强,赵冬斌,刘殿通.桥式吊车系统的分级滑模控制方法.自动化学报,2004,30(5):784-788[7]XiZ,HeskethT.Discretetimeintegralslidingmodecontrolforoverheadcranewithuncertainties.IETControlTheory&Applications,2010,4(10):2071-2081[8]胡洲,王志胜,甄子洋.带输入饱和的欠驱动吊车非线性信息融合控制.自动化学报,2014,40(7):1522-1527[9]SunN,FangY,ZhangX.Energycouplingoutputfeedbackcontrolof4-DOFunderactuatedcraneswithsaturatedinputs.Automatica,2013,49(5):1318-1325[10]SunN,FangY.Newenergyanalyticalresultsfortheregulationofunderactuatedoverheadcranes:Anend-effectormotion-basedapproach.IEEETransactionsonIndustrialElectronics,2012,59(12):4723-4734[11]NakazonoK,OhnishiK,KinjoH,YamamotoT.Loadswingsuppressionforrotarycranesystemusingdirectgradientdescentcontrolleroptimizedbygeneticalgorithm.TransactionsoftheInstituteofSystems,ControlandInformationEngineers,2011,22(8):303-310[12]ZhaoY,GaoH.Fuzzy-model-basedcontrolofanoverheadcranewithinputdelayandactuatorsaturation.IEEETransactionsonFuzzySystems,2012,20(1):181-186[13]UchiyamaN,OuyangH,SanoS.Simplerotarycranedynamicsmodelingandopen-loopcontrolforresidualloadswaysuppressionbyonlyhorizontalboommotion.Mechatronics,2013,23(8):1223-1236[14]SunN,FangY,ZhangX,YuanY.Transportationtask-orientedtrajectoryplanningforunderactuatedoverheadcranesusinggeometricanalysis.IETControlTheory&Applications,2012,6(10):1410-1423[15]孙宁,方勇纯,王鹏程,张雪波.欠驱动三维桥式吊车系统自适应跟踪控制器设计.自动化学报,2010,36(9):1287-1294[16]SunN,FangY,ZhangX,MaB.Anovelkinematiccoupling-basedtrajectoryplanningmethodforoverheadcranes.IEEE/ASMETransactionsonMechatronics,2012,20(1):241-248[17]WangPeng-Cheng,FangYong-Chun,JiangZi-Ya.Adirectswingconstraint-basedtrajectoryplanningmethodforunderactuatedoverheadcranes.ActaAutomaticaSinica,2014,40(11):2414-2419[18]VaughanJ,KimD,SinghoseW.Controloftowercraneswithdouble-pendulumpayloaddynamics.IEEETransactionsonControlSystemsTechnology,2010,18(6):1345-1358[19]SinghoseW,KimD.Manipulationwithtowercranesexhibitingdouble-pendulumoscillations.In:Proceedingsof2007IEEEInternationalConferenceonRoboticsandAutomation.Roma,Italy:IEEE,2007.4550-4555[20]MasoudZ,AlhazzaK,Abu-NadaE,MajeedM.Ahybridcommand-shaperfordouble-pendulumoverheadcranes.JournalofVibrationandControl,2014,20(1):24-37[21]孙宁,方勇纯,钱彧哲.带有状态约束的双摆效应吊车轨迹规划.控制理论与应用,2014,31(7):974-980[22]郭卫平,刘殿通.二级摆型吊车系统动态及基于无源的控制.系统仿真学报,2008,20(18):4945-4948[23]GargD,PattersonM,HagerW,RaoA,BensonD,HuntingtonG.Aunifiedframeworkforthenumericalsolutionofoptimalcontrolproblemsusingpseudospectralmethods.Automatica,2010,46(11):1843-1851[24]GillP,MurrayW,SaundersM.SNOPT:AnSQPalgorithmforlarge-scaleconstrainedoptimization.SIAMReview,2005,47:99-131。