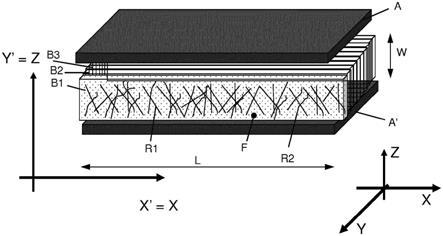
1.本发明涉及一种制造具有改进的压缩强度的片状复合部件的新颖方法。
背景技术:2.由纤维增强的热塑性材料制造的复合部件已在许多技术领域中得到广泛使用。
3.例如,wo 2015/117799a1公开了一种包含泡沫芯的复合部件,其具有第一和第二表皮层,所述第一和第二表皮层与所述泡沫芯分别在其第一表面和第二表面上结合。类似地,wo 2006/133586公开了一种抗挠刚性复合片材,其包括:由玻璃含量为20至60重量%且空隙含量小于5体积%的玻璃纤维增强的聚丙烯制成的厚度为0.5至5mm的一个或两个表皮层、和由玻璃含量为35至80重量%且空隙含量为20至80体积%的玻璃纤维增强的聚丙烯制成的厚度为2至40mm的芯层。如在wo 2006/105682 a1中大量描述的,这样的多孔芯片材可通过将聚丙烯纤维和玻璃纤维干混、将共混的非织造材料针刺(针入,needling)以及热压来而形成。
4.一个长久以来的挑战在于寻求在保持重量尽可能小的同时优化机械性质。在许多情况下,用比较厚的芯层进行制造过程将是期望的。单纯地将芯层厚度按比例放大会导致如下缺点:最初软的芯层当在热压步骤中施加表皮层时提供不了足够的压缩强度。因此,提供一种涉及具有改进的压缩强度的芯层的改进的制造方法将是期望的。
技术实现要素:5.根据本发明,提供了一种制造片状复合部件的方法,其包括以下工艺步骤:
6.a)提供基本上平面的布置体(arrangement)(a,b,a'),其包括夹在一对表皮层(a,a')之间的芯层(b),芯层的第一面与所述表皮层中的第一个(a)相邻并且基本上平行,并且芯层的第二面与所述表皮层中的另一个(a')相邻并且基本上平行,表皮层(a,a')各自包含表皮热塑性材料和任选的增强纤维,芯层(b)包含由起绒热塑性纤维和增强纤维制成的起绒材料,
7.b)加热并且加压夹层布置体(a,b,a'),随后冷却,从而获得复合部件。
8.术语“表皮层”应以其最宽泛的含义理解为是指附接至内部或芯结构的表面层。上表皮层和下表皮层可具有或不具有相等的厚度。表皮层中的每个都包含热塑性材料,为了清楚起见在此称为“表皮热塑性材料”。此外,每个表皮层任选地包含增强纤维。
9.芯层由通过热塑性纤维和增强纤维制成的起绒材料形成。为了清楚起见,构成热塑性纤维的材料在本文被称为“起绒(绒面,绒毛,fleece)热塑性材料”。
10.作为构成芯层的一种材料的纤维增强热塑性起绒材料被广泛用在许多技术领域中,特别地用于生产具有有利结构性质的轻型部件。它们典型地用完善的梳理(carding)或气流成网(air
‑
laying)技术生产,并且基本上形成为片材。作为生产过程的结果,这样的起绒材料的纤维主要在片材平面内(即在可定义为“x
‑
y
‑
平面”的平面内)取向。虽然所知晓的是,在垂直于片材平面的方向上针刺起绒材料略微增加在z
‑
方向上取向的增强纤维的量,
但是再取向效果相对较小,因此x
‑
y
‑
取向仍然占主导。
11.然而,根据本发明,芯层b是具有主要在垂直于第一和第二面的取向方向z上取向的增强纤维的z
‑
取向芯层。以这种方式,获得显著改进的压缩强度。
12.应强调,上述特征“主要的z
‑
取向”(即垂直于由所述第一和第二面限定的x
‑
y参考平面)并不排除第二方向(即一个特定的平面内方向例如y)的优先取向。但是,毫无疑问地,这意味着与各向同性的情况相比在z
‑
方向上的主要性。
13.根据一个有利的实施方案(权利要求2),z
‑
取向芯层(b)通过以下形成:
14.i)提供至少一个具有上面、下面和片材厚度(t)的预固结的轻型增强热塑性材料的片材;
15.ii)将片材切割成多个基本一致的芯带,每个芯带具有带长度(l)和带宽度(w),每个芯带包括以对应于所述片材厚度(t)的带厚度间隔开的上面部分和下面部分;
16.iii)将所述芯带以面对面的方式、任选地在其间具有分隔层的情况下布置,从而形成芯堆叠体,所述芯堆叠体具有对应于所述带长度(l)的堆叠长度(l
堆叠
)、具有对应于所述带宽度(w)的堆叠高度(h
堆叠
)和具有对应于所述带厚度(t)的倍数的堆叠宽度(w
堆叠
);
17.任选地重复进行步骤i)至iii)以形成另外的芯堆叠体;
18.其中所述至少一个芯堆叠体形成如下的所述z
‑
取向芯层:具有将表面层(a)和(a')施加到其以形成用于后续工艺步骤b)的所述夹层布置体(a,b,a')的暴露的第一和第二面。
19.简而言之,芯带的旋转导致几何学上的再取向,从而得到所述期望的主要的z
‑
取向。
20.术语“基本一致(大致相等,substantially congruent)”应在如下意义上理解:彼此相邻布置的每对芯带具有彼此匹配的实质表面部分。其应包括一个构件或一对构件具有比其他构件更大的表面、因此留下非接触部分的可能性。这允许形成具有非恒定厚度的夹层布置体。
21.根据一个实施方案(权利要求3),在步骤iii)中施加分隔层,特别是增强织物。
22.根据一个实施方案(权利要求4),z
‑
取向芯层包含单一芯堆叠体。
23.根据另一个实施方案(权利要求5),z
‑
取向芯层包含至少两个芯堆叠体,任选地具有不同的堆叠高度(h
堆叠1
,h
堆叠2
)。
24.根据又一个实施方案(权利要求6),至少一个芯堆叠体包含具有不同组成的芯带。
25.根据一个特别有利的实施方案(权利要求7),预固结的轻型增强热塑性材料具有35至80重量%的增强纤维含量和20至80体积%的空隙含量。
26.根据一个实施方案(权利要求8),所述芯带在将布置成芯堆叠体以随后施加表皮层(a,a')和进行工艺步骤b)之前加热。
27.根据一个替代实施方案(权利要求9),将未加热的芯带布置成芯堆叠体,随后施加表皮层(a,a')和进行工艺步骤b)。
28.如在纤维增强的热塑性材料的领域中所知晓的(权利要求10),增强纤维可选自各种各样的,包括但不限于玻璃纤维、碳纤维、芳族聚酰胺纤维、玄武岩纤维和天然纤维。替代地,增强纤维可由高熔点热塑性材料制造,即由在热压步骤的处理温度下不熔化的材料制造。根据一个有利的实施方案,增强纤维是玻璃纤维。
29.起绒热塑性材料和表皮热塑性材料可独立地选自各种已知的聚合物,例如聚丙烯(pp)、聚醚酰亚胺(pei)、聚砜(psu)、聚醚砜(pes)、聚苯砜(ppsu)、聚邻苯二甲酰胺(ppa)、聚苯醚(ppo)、聚醚醚酮(peek)聚苯硫醚(pps)、聚酰胺(pa)、聚芳基醚酮(paek)、聚醚酮酮(pekk)和聚碳酸酯(pc)(权利要求11)。有利地,起绒热塑性材料和表皮热塑性材料是相同或相互相容的热塑性聚合物。
30.在许多有利的实施方案中,增强纤维是碳纤维,并且起绒热塑性材料和表皮热塑性材料是pp,优选熔体流动指数mfi(230℃,2.16kg)为5至500、优选为10至200g/10min的聚丙烯。
31.在某些实施方案(权利要求12)中,至少一种表皮层(a,a')包含增强片材,所述增强片材由织造织物、非卷曲织物或单向纤维布置体组成。
32.取决于应用,在工艺步骤b)之前提供的芯层(b)的面积重量为250至10'000g/m2(权利要求13)。
附图说明
33.通过参考以下结合附图对本发明的各种实施方案的描述,本发明的上述和其他特征和目的以及实现它们的方式将变得更加明显,并且将更好地理解本发明本身,在所述附图中:
34.图1以透视图示出根据现有技术的待处理的布置体;
35.图2也以透视图示出图1的布置体的芯层;
36.图3以侧透视图示出根据第一实施方案的待处理的布置体;
37.图4以纵向透视图示出与图3相似的但仅具有三个芯带的布置体;
38.图5以纵向透视图示出根据第二实施方案的具有不同芯带的待处理的布置体;
39.图6以纵向透视图示出根据第三实施方案的在芯带之间具有分隔层的待处理的布置体;和
40.图7以纵向透视图示出根据第四实施方案的具有不同芯带高度的待处理的布置体。
具体实施方式
41.将理解,附图不一定按比例绘制。在某些情况下,相对尺寸是明显变形的,以便于可视化。在各个附图中,相同或相应的特征通常用相同的符号表示。
42.图1和图2中示出根据现有技术的制造片状复合部件的方法。如图1中笼统地显示,该方法开始于提供基本上平面的布置体(a,b,a'),其包括夹在一对表皮层(即上表皮层a和下表皮层a')之间的芯层b。在所示的实例中,芯层b由在彼此上面堆叠的两个单独层b1和b2构成。
43.芯层b的第一面与上表皮层a相邻并且基本上平行,而芯层的第二面与下表皮层a'相邻并且基本上平行。
44.两个表皮层a、a'各自包含表皮热塑性材料和任选地增强纤维。芯层b(即单独层b1和b2中的每个)包含由起绒热塑性纤维制成的起绒材料f,并且进一步包含增强纤维r1、r2等。
45.如图2所示,在每个芯层中的增强纤维r1、r2等的取向主要在层平面上,即在由方向矢量x和y所跨越(延伸)的平面上。更准确地,增强纤维以这样的方式取向:其纵向纤维方向在面外方向z上不具有实质性的分量。应指出,这也适用于弯曲的纤维,在该情况下必须考虑沿纤维的任何点处的局部纤维方向。
46.现在,在图3和图4中说明本发明的基本构思。与图1和图2所示的情况形成对比,现在大量的增强纤维r1、r2等具有垂直于芯层的面的方向分量(即沿着面外方向z)。在图3和图4所示的示例中,这是通过使芯层b由多个基本一致的芯带b1、b2、b3等构成而实现的,所述芯带b1、b2、b3等全部均由与对于图2中所例举的芯层所使用的材料相同或相似的材料组成。但是与图1所示的布置体形成对比,芯带以其平面垂直于表皮层a和a'而取向。这是通过将每个芯带翻转90
°
来实现的。
47.更具体地,可通过以下方法形成图3和图4所示的布置体的z
‑
取向芯层b。首先,提供具有上面、下面和片材厚度t的预固结的轻型增强热塑性材料(也称为“lwrt”)。随后,将该片材切割成多个基本一致的芯带,每个芯带具有带长度l和带宽度w,并且进一步包括以对应于片材厚度t的带厚度间隔开的上面部分和下面部分。然后,以面对面的方式布置芯带,从而形成芯堆叠体,其具有对应于带长度l的堆叠长度l
堆叠
和具有对应于带宽度w的堆叠高度h
堆叠
。显然,堆叠体具有对应于单独带厚度t的倍数的堆叠宽度w
堆叠
。如此获得的芯堆叠体形成具有暴露的第一和第二面的z
‑
取向芯层,以向其施加表面层a和a'。
48.然后,可使如此获得的夹层布置体a,b,a'经历加热和加压步骤,随后冷却,从而获得具有优异的压缩强度性质的片状复合部件。
49.在图5中示例了第二实施方案。在这种情况下,使用具有不同的lwrt芯带b1、b2、b3的布置体。这些芯带具有基本上相同的几何形状,但是它们并不都具有相同的组成。例如,各种芯带可具有些许不同的纤维含量和/或些许不同的孔隙率。也可使用具有不同类型的增强纤维的芯带,例如一些带具有碳纤维而另一些带具有玻璃纤维。
50.在图6中示例了第三实施方案。在这种情况下,使用具有基本上相同的lwrt芯带b1、b2、b3的布置体。然而,该布置体进一步包含布置在芯带之间的分隔层s,特别是织物层。
51.在图7中示出了第四实施方案。在这种情况下,使用具有三个具有不同带高度的lwrt芯带b1、b2、b3的布置体。芯带大致上、但并非严格地一致。在所示的特定实例中,带高度逐渐增加,从而形成阶梯状配置,导致夹层布置体的厚度逐渐增加。其他几何配置当然是可能的并且有用的。