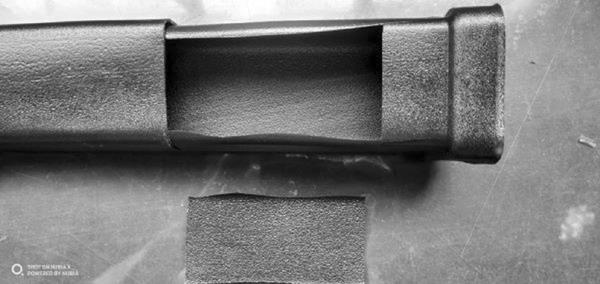
1.本发明涉及一种塑料微发泡吹塑成型方法,尤其涉及一种与智能化生产相适应的风道微发泡吹塑工艺方法。
背景技术:2.微发泡材料因其性能优异和成本经济而备受推崇,以惰性气体为物理发泡介质的微发泡注塑/吹塑工艺目前已广泛应用。在更快的工业发展速度和更高的产品质量要求下,微发泡注塑/吹塑技术工艺的进步和完善,依旧刻不容缓而且永无止尽。
3.目前,国外微孔发泡的工业化进程远远快于国内,除了mucell工艺外,瑞士的sulzer公司也已经开发出商业化的“optifoam”注塑成型工艺。此外,高压气体连续挤出的发泡工艺,也基本上实现了工业化。在国内,微孔发泡的研究仍然处于起步阶段,泡沫塑料生产企业大多引进国外成套设备,自身缺乏技术力量。因此微孔发泡的研究具有较强的实际意义。近年来,汽车轻量化、高速列车、国产大飞机等项目的全面启动和实施给高性能轻质材料—微孔材料带来了良好的发展机遇。微孔发泡技术的研究仅仅停留在泡孔结构的调控上是远远不够的。一般来说,只有具备一定形状的微孔材料才有使用价值,这就涉及到微孔材料的成型。普通的泡沫塑料通常采用发泡母粒二次发泡的方式成型。与普通的泡沫塑料不同,微孔材料的优势在于数量多孔径小的泡孔。这些泡孔在进行二次发泡成型时,会发生膨胀和融合,成为孔少而大的普通泡沫塑料,丧失了原有的优势。因此微孔材料大多在发泡的过程中同时进行成型。微孔材料的形状通常包含薄膜、片材、管材、型材以及其他复杂结构,相应的制备方法包括微孔吹塑、微孔挤出、微孔模压和微孔注塑等方法。这些方法中包含着一个普遍存在的科学问题,即受限发泡。受限发泡是相对自由发泡而言的,是指对材料在微孔发泡过程中的膨胀行为进行约束,使其成为目标形状的一种发泡成型方式。
4.因此,市面上需要一种适用于微发泡吹塑、风道稳定、可智能化控制、可连续自适应生产的与智能化生产相适应的风道微发泡吹塑工艺方法。
技术实现要素:5.本发明旨在提供一种适用于微发泡吹塑、风道稳定、可智能化控制、可连续自适应生产的与智能化生产相适应的风道微发泡吹塑工艺方法。
6.为了实现上述目的,本发明采用以下技术方案:一种与智能化生产相适应的风道微发泡吹塑工艺方法,包括以下阶段:s1:原料准备
①
原材料准备:准备cs002塑料母料370份-400份,碳酸氢钠发泡剂母粒5.8份-7份;
②
辅材及设备准备:准备额定功率70kw-80kw集成有控制中心、料筒、与产品模具对应的程序数据库和模具抓取固定装置的挤出吹塑成型机,该挤出吹塑成型机内还集成有气源、增压设备、储气设备、限流元件、气体注入装置按照注气原理组合,通过高压不锈钢卡
套管有序连接并配合气压传感器、气体流量计、压力显示表所形成的注气系统;模具抓取固定装置内部,还设置有内置于模具抓取固定装置、设置于模具抓取固定装置与模具浇道转弯处匹配区域正下方位置对应的呈正方形及其中心点等距均布的9个区域电加热装置;准备各型对应模具;s2:原料预处理破碎与预混
①
将阶段s1步骤
①
准备的cs002塑料母料、碳酸氢钠发泡剂母粒除尘、除水、除油、破碎,然后将cs002塑料母料、碳酸氢钠发泡剂母粒按质量比97.9:(1.9-2.1)预混均匀,获得洁净混合原料;s3:预准备
①
将阶段s2步骤
①
获得的洁净混合原料装入挤出吹塑成型机的料筒中,预热至185℃
±
5℃;
②
通过控制中心操作挤出吹塑成型机的模具抓取固定装置选定目标模具,装配并固定好;
③
通过控制中心操作挤出吹塑成型机的模具抓取固定装置中的区域电加热装置,使与选定模具转弯处对应的区域加热至模具转弯处温度升至90℃
±
15℃;
④
通过控制中心从产品模具对应的程序数据库调用对应的生产程序,基础参数为:合模压力为450mpa-550mpa、模头位移压力280mpa-320mpa、塑化百分比54%-58%、射出延时0.4s-0.6s、循环周期40s-80s;s4:吹塑工艺及参数智能化控制
①
设置料筒温度185℃
±
5℃,设置模头温度190℃
±
5℃,气针气压0.2mpa
±
0.01mpa,进行吹塑;
②
吹塑完成之后脱模,开模压力为450mpa-550mpa,然后将零件气冷至不高于100℃,取下产品,获得所需毛坯吹塑产品;
③
重复阶段s3、阶段s4,重复生产,获得批量毛坯吹塑产品;s5:剪边及检测
①
按设计需求机械加工去除阶段s4步骤
③
获得的批量毛坯吹塑产品的毛边多余余量,获得成品吹塑件;
②
在成品吹塑造件中抽样进行机械性能检测,要求所有尺寸均符合设计要求,减重率不低于10%、不高于25%,同一表面最高点与最低点厚度差不大于0.2mm,机械性能满足以下条件:拉伸强度25mpa-28mpa、弯曲强度22mpa-24mpa、维卡软化温度不低于125℃、冲击强度不低于50kj/m2。
7.与现有技术相比,本发明由于采用了以上技术方案,具有以下优点:(1)申请人以自身长期与各汽车企业合作研发获得的试验数据为样本数据,构建局部寻优网络多指标预测模型、然后通过交叉验证模拟改进,再利用遗传算法,得到产品质量指标与各成型工艺参数之间的非线性映射关系。研究结果表明:通过基础数据模拟寻优得到的最优工艺参数,也因此发现了对于薄壁、转弯和吹塑管道,随着弯道的增多和吹塑距离的加长,其料筒温度、模头温度均应高于180℃,远高于现有技术中的150℃-160℃,否则会出现发泡不充分、不均匀、脱模困难、成型后表面粗糙的问题。
8.(2)根据本发明的工艺方法,可以使泡孔更细小和均匀,尤其在相对现有技术高
温、低压、低降压速率的条件下,能显著减小泡孔孔径,并且这种作用不会因材料厚度的增加而失效。将根据本发明的发泡方法,对泡孔微观形态的影响,结合高温、长时的方式,通过控制模具温度和发泡条件,成功得到了密集的、均匀的、微小的、稳定的泡孔结构。
9.(3)本发明实行的是全自动化控制,对于本发明的配料适用的管道而言,只需选用对应程序,就可以实现投料到成型的全过程,可以智能化控制和学习,收集数据并不断迭代、优化参数,获得更优的与产品形制相匹配的工艺参数,也更加可以适应连续自适应生产。
10.综上所述,本发明适用于微发泡吹塑、风道稳定、可智能化控制、可连续自适应生产。
附图说明
11.图1为本发明实施例1处理后与阴性对照组及阳性对照组对比的弯曲强度应力-应变数据图;图2为本发明实施例1处理后与阴性对照组及阳性对照组对比的拉伸强度应力-应变数据图;图3为本发明实施例1处理后与阴性对照组及阳性对照组对比的维卡软化温度-位移量数据图;图4为本发明实施例1处理后与阴性对照组及阳性对照组对比的抗冲击性能数据表;图5为本发明实施例1处理后从前到后依次测量的各区域实际密度乘以整体体积的减重点阵图;图6为本发明实施例1选取的市售阳性对照实物解剖图;图7为不发泡情况下的产品实物解剖图;图8为本发明实施例1处理后实物解剖图;图9为本发明实施例1处理后实物截面sem形貌;图10为本发明实施例1风道模拟图。
具体实施方式
12.实施例1:如图8所示实物和图1-4所示性能参数,一种与智能化生产相适应的风道微发泡吹塑工艺方法,用于制造吉利汽车空调风道管的vf12微发泡吹塑管,包括以下阶段:s1:原料准备
①
原材料准备:准备cs002塑料母料370份-400份,碳酸氢钠发泡剂母粒5.8份-7份;
②
辅材及设备准备:准备额定功率70kw-80kw集成有控制中心、料筒、与产品模具对应的程序数据库和模具抓取固定装置的挤出吹塑成型机,该挤出吹塑成型机内还集成有气源、增压设备、储气设备、限流元件、气体注入装置按照注气原理组合,通过高压不锈钢卡套管有序连接并配合气压传感器、气体流量计、压力显示表所形成的注气系统;模具抓取固定装置内部,还设置有内置于模具抓取固定装置、设置于模具抓取固定装置与模具浇道转
弯处匹配区域正下方位置对应的呈正方形及其中心点等距均布的9个区域电加热装置;准备各型对应模具;s2:原料预处理破碎与预混
①
将阶段s1步骤
①
准备的cs002塑料母料、碳酸氢钠发泡剂母粒除尘、除水、除油、破碎,然后将cs002塑料母料、碳酸氢钠发泡剂母粒按质量比97.9:(1.9-2.1)预混均匀,获得洁净混合原料;s3:预准备
①
将阶段s2步骤
①
获得的洁净混合原料装入挤出吹塑成型机的料筒中,预热至185℃
±
5℃;
②
通过控制中心操作挤出吹塑成型机的模具抓取产品截面为方管、有两个直角弯道的目标模具,装配并固定好;
③
通过控制中心操作挤出吹塑成型机的模具抓取固定装置中的区域电加热装置,使与选定模具转弯处对应的区域加热至模具转弯处温度升至90℃
±
15℃;
④
通过控制中心从产品模具对应的程序数据库调用对应的生产程序,基础参数为:合模压力为500mpa、模头位移压力280mpa-320mpa、塑化百分比55%、射出延时0.5s、循环周期65s;s4:吹塑工艺及参数智能化控制
①
设置料筒温度185℃
±
5℃,设置模头温度190℃
±
5℃,气针气压0.2mpa
±
0.01mpa,进行吹塑;
②
吹塑完成之后脱模,开模压力为500mpa,然后将零件气冷至不高于100℃,取下产品,获得所需毛坯吹塑产品;
③
重复阶段s3、阶段s4,重复生产,获得批量毛坯吹塑产品;s5:剪边及检测
①
按设计需求机械加工去除阶段s4步骤
③
获得的批量毛坯吹塑产品的毛边多余余量,获得成品吹塑件;
②
在成品吹塑造件中抽样进行机械性能检测,要求所有尺寸均符合设计要求,减重率不低于10%、不高于25%,同一表面最高点与最低点厚度差不大于0.2mm,机械性能满足以下条件:拉伸强度25mpa-28mpa、弯曲强度22mpa-24mpa、维卡软化温度不低于125℃、冲击强度不低于50kj/m2。
13.根据本实施例方法制造的吹塑品,其外观和解剖图所图8所示,以南京聚隆提供的微发泡样品为阳性对照,以目前吉利所用市售竞品为阴性对照,性能对比结果如图1-4所示,本实施例拉伸强度25.34mpa、弯曲强度22.83、维卡软化温度128.82℃、冲击吸收功1.94kj、冲击强度60.46kj/m2,同一表面最高点与最低点厚度差0.13mm,发泡后减重情况如图5所示,发泡最不充分处减重率10.63%,最充分处减重率24.05%,由于弯角处模具温度补偿机制,与图10对比说明风道的影响被模具升温所补偿,发泡情况在设计要求之内,优于如图6、图7所示现有技术;本实施例产品截面的sem微观形貌图如图9所示,可见发泡细小、均匀、稳定。下同。
14.实施例2:整体与实施例1相同,差异之处在于:
s3:预准备
②
通过控制中心操作挤出吹塑成型机的模具抓取产品截面为圆管、有4个直角弯道的目标模具,装配并固定好;
④
合模压力为450mpa、模头位移压力280mpa-320mpa、塑化百分比58%、射出延时0.6s、循环周期80s;s4:吹塑工艺及参数智能化控制
②
开模压力为450mpa;根据本实施例方法制造的吹塑品,拉伸强度27.71mpa、弯曲强度22.14、维卡软化温度125.81℃、冲击强度52.44kj/m2。
15.实施例3:整体与实施例1相同,差异之处在于:s3:预准备
②
通过控制中心操作挤出吹塑成型机的模具抓取产品为直通方管的目标模具,装配并固定好;
④
合模压力为550mpa、模头位移压力280mpa-320mpa、塑化百分比54%、射出延时0.4s、循环周期40s;s4:吹塑工艺及参数智能化控制
②
开模压力为450mpa;根据本实施例方法制造的吹塑品,拉伸强度26.28mpa、弯曲强度23.32、维卡软化温度131.02℃、冲击强度62.35kj/m2。
16.对所公开的实施例的上述说明,仅为了使本领域专业技术人员能够实现或使用本发明。对这些实施例的多种修改对本领域的专业技术人员来说将是显而易见的,本文中所定义的一般原理可以在不脱离本发明的精神或范围的情况下,在其它实施例中实现。因此,本发明将不会被限制于本文所示的这些实施例,而是要符合与本文所公开的原理和新颖特点相一致的最宽的范围。