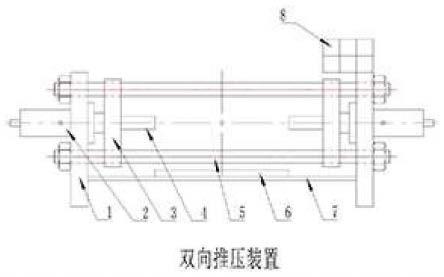
8min/mm。
10.所述双向推压阶段包括:关闭卸去加热元件,塑化完成;开始升压,进行推压,推压压力30-32 mpa/cm2,升压时间5-10min。
11.所述保压冷却阶段包括:推压完成,开始保压冷却,保压压力30-32 mpa/cm2,冷却方式为自然冷却。
12.聚三氟氯乙烯棒材卧式双向推压成型操作规程与成型工艺参数。
13.工艺参数表带压力的塑化工艺可以提高塑化效率,缩短塑化时间。
14.原料受热塑化时,熔体在不断膨胀,可将原材料中的低分子化合物受热分解产生的气体不断向外释放排泄,减少了立式模压成型塑化过程中排气操作工序。
15.聚三氟氯乙烯材料加工温度范围较窄,易引起变色,且对成型压力极为敏感,操作难度大,不易控制,成型压力低会导致制品密度不够,容易产生气孔,成型压力过高,产品卸模难,压力传递不均匀,会导致制品密度不一致,发生弯曲变形;保压冷却过程中,失压冷却,产品易开裂,因此模压成型过程中,必须要求模具的两端上下压杆同时推动滑块,在受力均匀的前提下,压制和保压冷却制品。
16.在保压冷却过程中,成型模具内制品受压一致,同步冷却,克服立式模压成型过程压力传递不均、散热不均的问题,保证了产品密度一致,色泽均一,避免了产品弯曲变形,有效提高了产品质量。
17.所述卧式双向推压成型设备包括卧式双向推压装置和专用模具。
18.所述卧式双向推压装置包括自支撑结构单元、运动结构单元、模具支撑结构单元和控制箱(8)。
19.所述自支撑结构单元包括墙板(1)、螺柱(5);所述运动结构单元包括双油缸(2)、推板(3)、推杆(4);所述模具支撑结构单元包括底板(7)、导轨(6);所述控制箱设有控制系统。
20.两端墙板(1)与四根螺柱(5)组成了机座架。
21.所述底板(7)安装于墙板下檐,以中心线为基准等距安装两根导轨(6)。
22.所述双油缸选用两套最大压力为50t油缸,分别安装于两端墙板,并保持中心在同一轴线,活塞一端与滑动模板中心连接,活塞最大行程为350mm。
23.所述推杆(4)通过螺纹连接于推板中心,为推压成型传递压力。
24.所述控制箱(8)安装于座机架上部,设有启动、作业、运行、压力调节、保压、卸压、计时功能按钮,用于控制卧式双向推压成型装置的运行与成型过程中的压力控制等控制程序。
25.所述双油缸,分别安装在同一机座架的两端墙板相对位置,且分别配置滑动模板。
26.所述卧式双向推压成型设备底板左侧的一端设有激光水平仪,用于监测托架上棒材模具中心与两滑动模板推杆是否处于同一水平线,用于模具定位。
27.与立式液压设备相比,本发明采用卧式双向推压成型装置替代单向油缸立式液压装置,利用卧式双向推压成型装置的油缸活塞推动推板前移,使安装在推板中心的推杆前伸,推动安装于托架上的模具模腔内压块,使模腔内粉料压密,通过控制塑化温度、塑化时间、塑化压力、成型压力,经保压冷却、卸模后制得合格的制品,也就是原来棒材成型模具直立在单油缸立式液压设备模块中的单向受压的成型模式转换为卧式双向成型模式。
28.所述专用模具包括锁紧结构单元与模具结构单元,所述锁紧结构单元包括压环(18)、螺杆(19)、螺母(20),所述模具结构单元包括型腔(15)、压块(16)、料腔(17)。
29.所述模具配置了加热元件(21)。
30.所述加热元件(21)是根据棒材模具规格及聚三氟氯乙烯原料成型塑化工艺温度、设定功率制作的,方便拆卸的铸铜加热圈。
31.所述模具采用通用压模所配备的型腔(15)、压块(16)、料腔的模具单元,增加了压环(18),配备了螺杆(9)与螺母(20),模具锁紧后使之成为一体,并配置了特制加热元件(21)及控制系统(8),设有加温、作业、保温、计时功能按钮,控制卧式双向推压成型设备成型过程中的塑化温度、保温时间等工艺参数。
32.所述模具配有托架。
33.所述托架包括框架结构单元、支撑块结构单元、调节结构单元。
34.所述框架结构单元由方形钢管制作成框架(9)。
35.所述支撑块结构单元为v形块(10),用于支撑棒材模具。
36.所述调节结构单元为调节螺母(11),用于调整支撑块单元高度。
37.所述托架还设有滚轴机构,滚轴机构装配有v形滚轮(12)与轮轴(13),通过支座(14)固定于框架下端,滚轮间距离与底板上的导轨相配合,确保托架能够平行运动。
38.本发明的有益效果在于:1. 改善了液压成型设备结构,改变了单油缸立式液压设备上下单向运动模式,设置了卧式双油缸双向推压横向运动方式,增加了滑动模板间距离,适用于超长棒材的成型制作。
39.2.在设备底板处设置托架,采用v形块支撑模具,螺母调节高度,解决了超长棒材模具在棒材制品成型过程中模具定位难的问题由原来立式模压时靠模具扶正优化为托架支撑,降低了操作人员的劳动强度,有利于安全生产。
40.3.采用激光水平仪监测装置,通过光线扫描校正超长棒材成型模具的定位坐标,改变了棒材模压成型时模具靠人工校正的低效不安全方式,有利于安全生产。
41.4.精确控制成型工艺参数,实现了半自动化操作,提高了生产效率。
附图说明
42.图1为双向推压装置,其中,1:墙板,2:油缸,3:推板,4:推杆,5:螺柱,6:导轨,7:底板,8:控制箱。
43.图2为专用模具,其中,15:型腔,16:压块,17:料腔,18:压环,19:螺杆,20:螺母,
21:加热元件。
44.图3为专用模具托架,其中,9:框架,10:v形块,11:调整螺母,12:v形滚轮,13:轮轴,14:支座。图4为操作流程图。
具体实施方式
[0045] 结合附图与实施例进一步说明本发明。
[0046]
实施例1选用m-300h作为原材料,选用φ30
×
800棒模;称取1290g的粉料,填入棒模料腔。开启设备,调节两推杆间距离至1960mm,以托架为中心安放模具,通过激光水平仪扫描校正,使模具中心与推杆中心同一轴线。采用32mpa预压力压紧原材料粉料,安装加热元件,设置加热温度为250℃,开始升温,达到250℃后开始计时,塑化压力1.5mpa/m2,塑化时间7min/mm。塑化结束,关闭并卸去加热元件。开始推压,推压压力32mpa/m2,升压时间7min。开始保压与冷却,保压压力32mpa/m2,自然冷却。当模具温度降至65℃,冷却结束,将推杆退出至料腔外。卸模取出制品。
[0047]
制得棒材直径为30
+0.1 mm,长度800
+0.1 mm;表面光滑,色泽一致,无杂质、气泡,无弯曲变形。
[0048]
实施例2选用m-300h作为原材料,选用φ40
×
800棒模;称取2255g的粉料,填入棒模料腔。开启设备,调节两推杆间距离至1950mm,以托架为中心安放模具,通过激光水平仪扫描校正,使模具中心与推杆中心同一轴线。采用30mpa预压力压紧原材料粉料,安装加热元件,设置加热温度为260℃,开始升温,达到260℃后开始计时,塑化压力1.0mpa/m2,塑化时间6min/mm。塑化结束,关闭并卸去加热元件。开始推压,推压压力30mpa/m2,升压时间8min。开始保压与冷却,保压压力30mpa/m2,自然冷却。当模具温度降至70℃,冷却结束,将推杆退出至料腔外。卸模取出制品。
[0049]
制得棒材直径为40
+0.2 mm,长度800
+0.2 mm;表面光滑,色泽一致,无杂质、气泡,无弯曲变形。
[0050]
前述实施例中涉及的塑化时间是指根据制品的厚度确定时间。