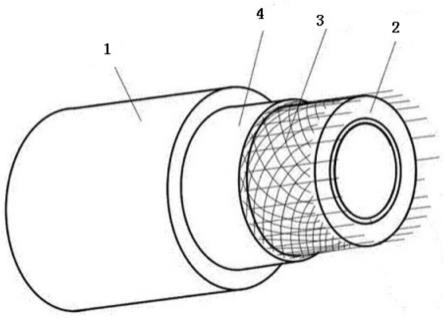
1.本发明涉及复合管技术领域,特别是涉及一种钢丝网骨架复合管及其生产方法。
背景技术:2.钢丝网骨架塑料复合管是一款改良过的新型的钢骨架塑料复合管。这种管材又称为srtp管。这种新型管道是用高强度过塑钢丝网骨架和热塑性塑料聚乙烯为原材料,钢丝缠绕网作为聚乙烯塑料管的骨架增强体,以高密度聚乙烯(hdpe)为基体,采用高性能的hdpe改性粘结树脂将钢丝骨架与内、外层高密度聚乙烯紧密地连接在一起,使之具有优良的复合效果。因为有了高强度钢丝增强体被包覆在连续热塑性塑料之中,因此这种复合管克服了钢管和塑料管各自的缺点,而又保持了钢管和塑料管各自的优点。
3.然而目前的复合管在生产过程中由于钢丝网和塑料原材之间的结合紧密度不够高,导致钢丝网骨架塑料复合管的强度较差,不能满足某些高作用力环境下的作业需求。
技术实现要素:4.本发明的目的在于提供一种钢丝网骨架复合管,以解决上述问题。
5.为实现上述目的,本发明提供如下技术方案:一种钢丝网骨架复合管,包括外聚乙烯层、内聚乙烯层以及设置于外聚乙烯层、内聚乙烯层之间的钢丝网层,所述外聚乙烯层和钢丝网层还设置有热熔胶层;
6.所述外聚乙烯层、内聚乙烯层、热熔胶层均呈中空管状结构。
7.作为本发明的一种改进,所述钢丝网层为表面镀有铜层的钢丝网。
8.作为本发明的一种改进,所述外聚乙烯层、内聚乙烯层的原料包括聚乙烯、抗氧化剂、增塑剂。
9.作为本发明的一种改进,所述热熔胶层的原料包括共聚酰胺树脂30-50份、乙酰丙酮锌1-3份、抗氧剂1-3份、增粘树脂15-35份、粘度调节剂3-6份、apao5-15份、填料10-20份。
10.一种钢丝网骨架复合管生产方法,包括以下步骤:
11.步骤s10、将聚乙烯、抗氧化剂、增塑剂混合均匀后加入挤出机中熔融挤出,经过模具定型后形成内聚乙烯层;
12.步骤s20、内聚乙烯层在牵引机作用下送入钢丝缠绕机,在内聚乙烯层表面将钢丝缠绕编织成网状,形成钢丝网层;
13.步骤s30、将共聚酰胺树脂、乙酰丙酮锌、抗氧剂、增粘树脂、粘度调节剂、apao份、填料混合均匀送入挤出机中熔融后挤出包覆在钢丝网层,形成热熔胶层;
14.步骤s40、将聚乙烯、抗氧化剂、增塑剂混合均匀后加入挤出机中熔融挤出,在钢丝网层外表面成型,形成外聚乙烯层,冷却完毕后获得钢丝网骨架复合管。
15.作为本发明的一种改进,在步骤s20中,钢丝缠绕呈网状前还经过涂塑工艺,涂塑工艺包括以下步骤:
16.s21、将钢丝从放线机上放线后经过矫正机校正,对其自身应力以及走线方向进行
调整;
17.s22、将校正后的钢丝进行高频预热,随后将共聚酰胺树脂原料放入挤出机中熔融,并在成型模具中均匀涂覆于在成型模孔中运行的钢丝;
18.s23、涂塑完毕的钢丝最终收线成卷。
19.作为本发明的一种改进,在步骤s22中,还包括钢丝涂覆层检测工艺,包括以下步骤:
20.s221、在挤出机的机身上设置两个同轴固定环,在固定环之间设置中心固定板,中心固定板所在平面穿过挤出机的机身的中轴线,在中心固定板上设置钢丝涂覆层表面轮廓转化装置,将钢丝涂覆层表面的轮廓形状转化为指针走向;
21.s222、布置阵列式探测极板用于实时追踪指针的运动轨迹,阵列式探测极板包括两对相互垂直的极板,极板获取指针运动时产生的电感应信号,将检测到电感应信号峰值的相对极板的连线与指针端头运动轨迹的夹角设定为指针走向a,指针走向的运动速度为v;
22.s223、采集并记录阵列式探测极板的探测范围内电感应信号波峰值,并且读取波峰处的过零点时刻,获取每个极板采集到的波峰后的过零点时刻并记为t1、t2、t3、t4,则根据公式(1)确认指针走向,根据公式(2)确认指针运动速度,
[0023][0024][0025]
其中d为极板之间的间距;
[0026]
s224、根据步骤s223能够获得指针在不同位置处的走向和运动速度,据此即可实时追踪指针的运动轨迹,当其轨迹超过预设的边界时,发出警报,并停止钢丝涂覆动作。
[0027]
作为本发明的一种改进,在步骤s221中,钢丝涂覆层表面轮廓转化装置的使用方法为:
[0028]
在挤出机的机身外周设置有两个定位环,定位环与挤出机的机身同轴而设,在两个定位环之间设置两个安装基板,两个安装基板在同一水平面上且挤出机的机身中轴线在该水平面上;
[0029]
在安装基板上设置架体,架体上转动设置一校准头和一指针转头,左侧的校准头和一自重件通过皮带相连,自重件自由垂落从而与安装基板之间垂直,采用螺杆顶头将自重件固定在架体上;
[0030]
铰接杆和自重件的下端铰接且二者之间设置确保铰接杆和自重件相互垂直的挡块,铰接杆另一端和皮带固定连接,自重件固定完毕后旋转铰接杆直至挡块处,此时铰接杆和自重件相互垂直,铰接杆旋转小角度后带动皮带工作,皮带轮再带动校准头旋转一定的微小角度,此时校准头达到校准位;
[0031]
钢丝滚轮在涂覆完毕后的钢丝表面滚动,并随其表面轮廓上下移动,通过放大齿轮箱带动指针转头转动,固定在指针转头上的指针则显示在校准头上,通过阵列式探测极板对指针的运动轨迹进行捕捉。
[0032]
本发明的其它特征和优点将在随后的说明书中阐述,并且,部分地从说明书中变得显而易见,或者通过实施本发明而了解。本发明的目的和其他优点可通过在所写的说明书、权利要求书、以及附图中所特别指出的结构来实现和获得。
[0033]
下面通过附图和实施例,对本发明的技术方案做进一步的详细描述。
附图说明
[0034]
图1为本发明钢丝网骨架复合管的结构示意图;
[0035]
图2为本发明钢丝涂覆层表面轮廓转化装置的结构示意图。
[0036]
图中各构件为:
[0037]
1、外聚乙烯层,
[0038]
2、内聚乙烯层,
[0039]
3、钢丝网层,
[0040]
4、热熔胶层,
[0041]
5、阵列式探测极板,
[0042]
6、挤出机,61、定位环,62、安装基板,63、架体,64、校准头,65、指针转头,66、皮带,67、自重件,68、螺杆顶头,69、铰接杆,
[0043]
7、钢丝,71、钢丝滚轮,72、放大齿轮箱,73、指针。
具体实施方式
[0044]
以下结合附图对本发明的优选实施例进行说明,应当理解,此处所描述的优选实施例仅用于说明和解释本发明,并不用于限定本发明。
[0045]
请参阅图1,一种钢丝网骨架复合管,其特征在于,包括外聚乙烯层1、内聚乙烯层2以及设置于外聚乙烯层1、内聚乙烯层2之间的钢丝网层3,所述外聚乙烯层1和钢丝网层3还设置有热熔胶层4;
[0046]
所述外聚乙烯层1、内聚乙烯层2、热熔胶层4均呈中空管状结构。
[0047]
所述钢丝网层3为表面镀有铜层的钢丝网。
[0048]
所述外聚乙烯层1、内聚乙烯层2的原料包括聚乙烯、抗氧化剂、增塑剂。
[0049]
所述热熔胶层4的原料包括共聚酰胺树脂30-50份、乙酰丙酮锌1-3份、抗氧剂1-3份、增粘树脂15-35份、粘度调节剂3-6份、apao5-15份、填料10-20份。
[0050]
上述技术方案的工作原理及有益效果:本发明采用特定比例的热熔胶层,从而增强钢丝网层和外聚乙烯层、内聚乙烯层之间的粘接紧密性,从而确保了钢丝网骨架复合管的整体强度,保证其适应高作用力的作业环境。
[0051]
为保证复合管粘合强度和增强层中钢丝强度,钢丝涂塑作为复合管生产的第一道工序尤为重要。粘接是复合管材的制造工艺的重点,复合粘接有以下三层含义:即镀层钢丝与粘合剂的粘接;中间层与pe芯管层的粘接;中间层与外pe层的粘接。复合管增强层所使用的材料一般为高强度的镀铜钢丝。管材中增强层是钢丝与热熔胶直接粘合,以及中间层与内外层的粘都是通过热熔胶来实现粘合和缝隙钢丝涂胶是钢丝在复合模具中通过挤出机共挤复合完成该工序。钢丝进挤出前,进行高频预热处理。生产时,加热熔化的热熔胶在挤出机螺杆旋转的推动下向前移动,并经历温度、压力等变化,热熔胶达到熔融状态时到成型
模具,均匀地涂覆于在成型模孔中运行的钢丝,经冷却成型后收卷机收线成品。镀层钢丝与粘合剂的粘接即钢丝涂塑工艺包括:钢丝放线、应力校正、钢丝高频预热、挤出复合、冷却成型、收线、检验等流程。
[0052]
钢丝涂塑中热熔胶需要均匀的涂覆在钢丝上,以确保钢丝网的结构强度。由于钢丝在涂覆时是采用成卷作业的,因此需要在涂覆过程中实时监测其涂覆的均匀性,防止成型模具或者挤出机出现损坏而无法及时得知,造成整卷的钢丝无法使用,为此提供以下生产方法。
[0053]
一种钢丝网骨架复合管生产方法,包括以下步骤:
[0054]
步骤s10、将聚乙烯、抗氧化剂、增塑剂混合均匀后加入挤出机6中熔融挤出,经过模具定型后形成内聚乙烯层2;
[0055]
步骤s20、内聚乙烯层2在牵引机作用下送入钢丝缠绕机,在内聚乙烯层2表面将钢丝缠绕编织成网状,形成钢丝网层3;
[0056]
步骤s30、将共聚酰胺树脂、乙酰丙酮锌、抗氧剂、增粘树脂、粘度调节剂、apao份、填料混合均匀送入挤出机6中熔融后挤出包覆在钢丝网层3,形成热熔胶层4;
[0057]
步骤s40、将聚乙烯、抗氧化剂、增塑剂混合均匀后加入挤出机6中熔融挤出,在钢丝网层3外表面成型,形成外聚乙烯层1,冷却完毕后获得钢丝网骨架复合管。
[0058]
在步骤s20中,钢丝缠绕呈网状前还经过涂塑工艺,涂塑工艺包括以下步骤:
[0059]
s21、将钢丝从放线机上放线后经过矫正机校正,对其自身应力以及走线方向进行调整;
[0060]
s22、将校正后的钢丝进行高频预热,随后将共聚酰胺树脂原料放入挤出机6中熔融,并在成型模具中均匀涂覆于在成型模孔中运行的钢丝7;
[0061]
s23、涂塑完毕的钢丝最终收线成卷。
[0062]
在步骤s22中,还包括钢丝涂覆层检测工艺,包括以下步骤:
[0063]
s221、在挤出机6的机身上设置两个同轴固定环,在固定环之间设置中心固定板,中心固定板所在平面穿过挤出机6的机身的中轴线,在中心固定板上设置钢丝涂覆层表面轮廓转化装置,将钢丝涂覆层表面的轮廓形状转化为指针73走向;
[0064]
s222、布置阵列式探测极板5用于实时追踪指针73的运动轨迹,阵列式探测极板5包括两对相互垂直的极板,极板获取指针73运动时产生的电感应信号,将检测到电感应信号峰值的相对极板的连线与指针73端头运动轨迹的夹角设定为指针73走向a,指针73走向的运动速度为v;
[0065]
s223、采集并记录阵列式探测极板5的探测范围内电感应信号波峰值,并且读取波峰处的过零点时刻,获取每个极板采集到的波峰后的过零点时刻并记为t1、t2、t3、t4,则根据公式(1)确认指针73走向,根据公式(2)确认指针73运动速度,
[0066][0067][0068]
其中d为极板之间的间距;
[0069]
s224、根据步骤s223能够获得指针73在不同位置处的走向和运动速度,据此即可实时追踪指针73的运动轨迹,当其轨迹超过预设的边界时,发出警报,并停止钢丝7涂覆动作。
[0070]
在步骤s221中,钢丝涂覆层表面轮廓转化装置的使用方法为:
[0071]
在挤出机6的机身外周设置有两个定位环61,定位环61与挤出机6的机身同轴而设,在两个定位环61之间设置两个安装基板62,两个安装基板62在同一水平面上且挤出机6的机身中轴线在该水平面上;
[0072]
在安装基板62上设置架体63,架体63上转动设置一校准头64和一指针73转头65,左侧的校准头64和一自重件67通过皮带66相连,自重件67自由垂落从而与安装基板62之间垂直,采用螺杆顶头68将自重件67固定在架体63上;
[0073]
铰接杆69和自重件67的下端铰接且二者之间设置确保铰接杆69和自重件67相互垂直的挡块,铰接杆69另一端和皮带66固定连接,自重件67固定完毕后旋转铰接杆69直至挡块处,此时铰接杆69和自重件67相互垂直,铰接杆69旋转小角度后带动皮带66工作,皮带66轮再带动校准头64旋转一定的微小角度,此时校准头64达到校准位;
[0074]
钢丝滚轮在涂覆完毕后的钢丝7表面滚动,并随其表面轮廓上下移动,通过放大齿轮箱72带动指针73转头65转动,固定在指针73转头65上的指针73则显示在校准头64上,通过阵列式探测极板5对指针73的运动轨迹进行捕捉。
[0075]
最后应说明的是:以上所述仅为本发明的优选实施例而已,并不用于限制本发明,尽管参照前述实施例对本发明进行了详细的说明,对于本领域的技术人员来说,其依然可以对前述各实施例所记载的技术方案进行修改,或者对其中部分技术特征进行等同替换,凡在本发明的精神和原则之内,所作的任何修改、等同替换、改进等,均应包含在本发明的保护范围之内中。