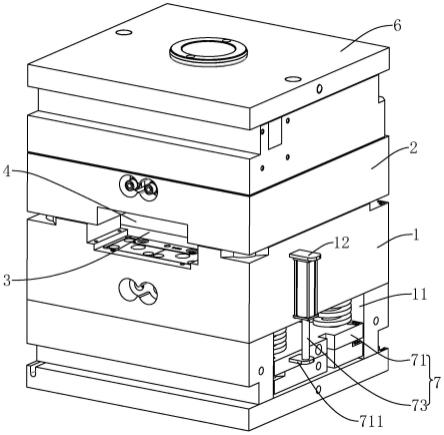
1.本技术涉及注塑模具技术领域,尤其是涉及一种天窗机械组总成前举臂注塑模具及其注塑工艺。
背景技术:2.注塑成型又称注射模塑成型,它是一种注射兼模塑的成型方法。注塑成型方法的优点是生产速度快、效率高,操作可实现自动化,花色品种多,形状可以由简到繁,尺寸可以由大到小,而且制品尺寸精确,产品易更新换代,能成形状复杂的制件,注塑成型适用于大量生产与形状复杂产品等成型加工领域。
3.注塑模具是注塑成型所需的工具,它将受热融化的材料由高压射入模腔,经冷却固化后,得到成形品。随着塑料制品的构造越来越复杂,在注塑成型过程中经常性需要用到嵌件,例如,汽车天窗机械组总成上的前举臂,如图11所示,前举臂包括嵌件本体5和塑料外包件50,嵌件本体5为金属制品。对嵌件本体5进行注塑时,需要先将嵌件本体5放置于模具的成型腔内,合模后再进行注塑作业,最后进行脱模得到嵌件成品(前举臂)。
4.针对上述中的相关技术,发明人认为存在有以下缺陷:然而,嵌件本体在注塑过程中经常性发生位移,影响注塑产品的注塑良率及注塑产品的品质问题,因此需要进一步改进。
技术实现要素:5.为了减少嵌件本体发生位移的可能,本技术的目的之一是提供一种天窗机械组总成前举臂注塑模具。
6.本技术提供的一种天窗机械组总成前举臂注塑模具采用如下的技术方案:一种天窗机械组总成前举臂注塑模具,包括定模具、位于定模具上方的动模具、安装于定模具的下模仁以及安装于动模具的上模仁,上模仁位于下模仁的上方,所述下模仁的上端面开设有供嵌件本体放置的嵌件放置槽,所述下模仁的上端面开设有连通于嵌件放置槽的下成型腔,所述上模仁的下端面开设有与下成型腔位置相对应的上成型腔,嵌件本体的下端面抵接于嵌件放置槽的内底壁,嵌件本体部分延伸至下成型腔以形成包覆部,上模仁的下端面抵接于嵌件本体和下模仁的上端面,上成型腔和下成型腔形成封闭的注塑型腔,所述上模仁/下模仁开设有连通于注塑型腔的注塑孔,嵌件本体的外侧壁和注塑型腔的内侧壁之间具有流液间隙,所述嵌件放置槽的底部内壁凸出设置有定位柱,所述嵌件本体开设有供定位柱插设的第一定位孔。
7.通过采用上述技术方案,注塑前,将嵌件本体放置于下模仁的嵌件放置槽内,并使得定位柱插设于第一定位孔,实现对嵌件本体在嵌件放置槽的定位,减少嵌件本体在注塑成型过程中发生位移的可能,保证了嵌件成品的尺寸精度和合格率,另外,上模仁和下模仁合模后,上模仁的下端面抵接于嵌件本体的上端面,实现了上模仁对嵌件本体的竖向滑移自由度进行约束的目的,从而减少嵌件本体在注塑过程中发生上浮的可能性,进一步减少
嵌件本体在注塑成型过程中发生位移的可能,保证了嵌件成品的尺寸精度和合格率。
8.优选的,所述包覆部贯穿开设有流液孔,所述流液孔设置有多个。
9.通过采用上述技术方案,在嵌件本体上开设有流液孔,一方面,在进行注塑时,注塑液从注塑孔进入注塑型腔内,部分注塑液从流液间隙进入上成型腔/下成型腔,部分注塑液从流液孔进入上成型腔/下成型腔,提高注塑液充满注塑型腔的效率,一方面,减少嵌件本体在注塑过程中受到注塑液的冲击力而发生上浮的可能性,另一方面,成型后的塑料外包件形成插设于流液孔的柱芯,提高塑料外包件和嵌件本体的连接结构稳定性,减少塑料外包件和嵌件本体发生脱离的可能。
10.优选的,所述第一定位孔和定位柱间隙配合,所述下模仁设置有凸出有嵌件放置槽内侧壁以供嵌件本体外侧壁抵接的限位台,所述下模仁的上端面开设有第一安装槽,第一安装槽连通于嵌件放置槽远离限位台一侧的内侧壁,下模仁设置有内置于第一安装槽的第一增阻镶块,第一增阻镶块具有弹性,所述第一增阻镶块的下部铰接于第一安装槽的内壁,第一增阻镶块的上部具有抵接于嵌件本体侧壁的第一抵推部,所述上模仁设置有迫使第一增阻镶块的第一抵推部抵紧于嵌件本体侧壁使得嵌件本体沿宽度方向移动并抵接于限位台的第一联动块。
11.通过采用上述技术方案,第一定位孔和定位柱间隙配合,方便工作人员将嵌件本体放置于嵌件放置槽内,实现嵌件本体和嵌件放置槽的预定位后,在上模仁和下模仁合模过程中,第一联动块迫使第一增阻镶块的自由端朝靠近限位台方向转动,第一增阻镶块的自由端转动过程中,第一抵推部抵接于嵌件本体外侧壁使得嵌件本体沿自身宽度方向滑移且抵接于限位台,以阻尼方式对嵌件本体在嵌件放置槽内的位置进行固定,同时对嵌件本体沿自身宽度方向滑移的自由度进行约束,从而减少嵌件本体在注塑成型过程中发生位移的可能。
12.优选的,所述第一联动块凸出固定于上模仁的下端面,下模仁的上端面开设有连通于第一安装槽远离嵌件放置槽一侧内壁的第一插接槽,第一联动块具有抵接于第一增阻镶块上部侧壁后迫使第一抵推部抵紧于嵌件本体侧壁的第一导向斜面,上模仁和下模仁合模后,第一联动块插设于第一插接槽,所述下模仁和第一增阻镶块之间设置有在常态下迫使第一增阻镶块的自由端朝远离嵌件放置槽方向转动的第一复位弹件。
13.通过采用上述技术方案,嵌件本体预定位后,进行合模时,在下模仁下降过程中,第一联动块的第一导向斜面抵接于第一增阻镶块的上部侧壁,下模仁继续下降,第一导向斜面迫使第一增阻镶块的自由端朝靠近限位台方向转动,使得第一抵推部推动嵌件本体沿自身宽度方向滑移且抵接于限位台,此时,第一复位弹件具有弹性势能,注塑完成后进行开模时,在下模仁上升且与第一增阻镶块脱离后,第一复位弹件迫使第一增阻镶块的自由端朝远离嵌件放置槽方向转动,使得第一增阻镶块的第一抵推部脱离于嵌件本体外侧壁,自动解除对嵌件本体的阻尼固定约束,便于后续对嵌件成品的脱模作业。
14.优选的,所述下模仁的上端面开设有第二安装槽,第二安装槽具有连通于嵌件放置槽的内侧壁的缺口,下模仁设置有内置于第二安装槽的第二增阻镶块,第二增阻镶块具有弹性,所述第二增阻镶块的下部铰接于第二安装槽的内壁,第二增阻镶块的上部具有穿过缺口且抵接于嵌件本体侧壁的第二抵推部,所述上模仁设置有迫使第二增阻镶块的第二抵推部抵紧于嵌件本体侧壁使得嵌件本体沿长度方向移动的第二联动块。
15.通过采用上述技术方案,在上模仁和下模仁合模过程中,第二联动块迫使第二增阻镶块的自由端朝靠近嵌件放置槽方向转动,第二增阻镶块的自由端转动过程中,第二抵推部穿过缺口且抵紧于嵌件本体侧壁使得嵌件本体沿自身长度方向滑移至设定位置处,以阻尼方式对嵌件本体在嵌件放置槽内的位置进行固定,同时对嵌件本体沿自身长度方向滑移的自由度进行约束,从而减少嵌件本体在注塑成型过程中发生位移的可能。
16.优选的,所述第二联动块凸出固定于上模仁的下端面,下模仁的上端面开设有连通于第二安装槽远离嵌件放置槽一侧内壁的第二插接槽,第二联动块具有抵接于第二增阻镶块上部侧壁后迫使第二抵推部抵紧于嵌件本体侧壁的第二导向斜面,上模仁和下模仁合模后,第二联动块插设于第二插接槽,所述下模仁和第二增阻镶块之间设置有在常态下迫使第二增阻镶块的自由端朝远离嵌件放置槽方向转动的第二复位弹件。
17.通过采用上述技术方案,嵌件本体预定位后,进行合模时,在下模仁下降过程中,第二联动块的第二导向斜面抵接于第二增阻镶块的上部侧壁,下模仁继续下降,第二导向斜面迫使第二增阻镶块的自由端朝靠近缺口方向转动,使得第二抵推部推动嵌件本体沿自身长度方向滑移,使得定位柱外周壁与第一定位孔的内侧壁抵接,此时,第二复位弹件具有弹性势能,注塑完成后进行开模时,在下模仁上升且与第二增阻镶块脱离后,第二复位弹件迫使第二增阻镶块的自由端朝远离缺口方向转动,使得第二增阻镶块的第二抵推部脱离于嵌件本体外侧壁,自动解除对嵌件本体的阻尼固定约束,便于后续对嵌件成品的脱模作业。
18.优选的,所述定模具开设有位于下模仁下方的安装腔,定模具设置有脱模机构,所述脱模机构包括沿竖向滑移连接于安装腔的顶针板、若干个固定连接于顶针板的顶针杆以及驱动顶针板滑移升降的顶针驱动件,嵌件放置槽的底部内壁贯穿开设有供顶针杆滑移穿设的顶针孔,顶针杆的轴向平行于定位柱的轴向。
19.通过采用上述技术方案,下模仁和上模仁开模后,对嵌件成品进行脱模时,顶针驱动件驱动顶针板上升,顶针板上升带动顶针杆穿过顶针孔抵接于嵌件本体下端面,顶针板继续上升,将嵌件成品顶出嵌件放置槽,使得嵌件成品的外周壁与下成型腔内侧壁、嵌件放置槽内侧壁分离,便于人工对嵌件成品进行拿取。
20.优选的,所述下模仁的上端面转动连接有位于嵌件放置槽一侧的转动轴,转动轴固定连接有限位板,下模仁设置有驱动转动轴转动的驱动部件,限位板自由端的下端面抵接于嵌件本体的上端面,所述上模仁的下端面开设有供限位板插设的避让槽。
21.通过采用上述技术方案,注塑前,通过驱动部件控制转动轴旋转,从而使得限位板转动至不干涉放置嵌件本体的位置处后,接着将嵌件本体放置于下模仁的嵌件放置槽内,并使得定位柱插设于第一定位孔,实现对嵌件本体在嵌件放置槽的定位,减少嵌件本体在注塑成型过程中发生位移的可能,接着通过驱动部件控制转动轴转动复位,使得限位板自由端的下端面抵接于嵌件本体的上端面,一方面,起到对嵌件本体是否完全放入嵌件放置槽进行检测,减少嵌件本体没有完全放入嵌件放置槽的可能,另一方面,通过限位板对嵌件本体的竖向滑移自由度进行约束,从而减少嵌件本体在注塑过程中发生上浮的可能性,进一步减少嵌件本体在注塑成型过程中发生位移的可能,保证了嵌件成品的尺寸精度和合格率;在完成注塑后,对嵌件成品进行脱模时,通过驱动部件控制转动轴旋转,从而使得限位板转动至不干涉放置嵌件本体的位置处后,再对嵌件成品进行拿取。
22.优选的,常态下,顶针杆下沉于嵌件放置槽的底部内壁,所述下模仁、定模具均具
有穿绳通道,定模具转动连接有位于安装腔下方的换向轮,所述驱动部件包括连接绳以及限位扭簧,连接绳的一端固定连接于限位板的自由端侧壁,连接绳的另一端依次穿过下模仁、定模具的穿绳通道且绕设于换向轮下周壁并固定于顶针板,限位扭簧迫使转动轴转动使得限位板的自由端在常态下延伸至嵌件放置槽上方。
23.通过采用上述技术方案,常态下,限位板的自由端延伸至嵌件放置槽上方,注塑前,顶针驱动件驱动顶针板上升一段距离且顶针杆仍未凸出于嵌件放置槽,通过连接绳拉动限位板的自由端绕转动轴的轴线转动,此时,限位扭簧具有弹性势能,从而使得限位板转动至不干涉放置嵌件本体的位置处后,接着将嵌件本体放置于下模仁的嵌件放置槽内,并使得定位柱插设于第一定位孔,接着顶针驱动件驱动顶针板下降复位,限位扭簧迫使限位板转动复位,使得限位板自由端的下端面抵接于嵌件本体的上端面;下模仁和上模仁开模后,对嵌件成品进行脱模时,顶针驱动件驱动顶针板上升一段距离,限位板转动至不干涉放置嵌件本体的位置处后,顶针驱动件继续驱动顶针板上升一段距离,顶针杆凸出于嵌件放置槽底部内壁,将嵌件成品顶出嵌件放置槽,再对嵌件成品进行拿取。
24.为了减少嵌件本体发生位移的可能,本技术的目的之二是提供一种应用于天窗机械组总成前举臂注塑模具的注塑工艺。
25.一种应用于天窗机械组总成前举臂注塑模具的注塑工艺,包括以下步骤:步骤s1、注塑准备,在上模仁的上成型腔以及下模仁的下成型腔内涂抹脱模剂,且对嵌件本体表面进行清理;步骤s2、将嵌件本体放置于嵌件放置槽,定位柱插设于第一定位孔,实现嵌件本体和嵌件放置槽的预定位;步骤s3、对上模仁和下模仁进行合模,在下模仁下降过程中,第一联动块的第一导向斜面抵接于第一增阻镶块的上部侧壁,下模仁继续下降,第一导向斜面迫使第一增阻镶块的自由端朝靠近限位台方向转动,使得第一抵推部推动嵌件本体沿自身宽度方向滑移且抵接于限位台;第二联动块的第二导向斜面抵接于第二增阻镶块的上部侧壁,下模仁继续下降,第二导向斜面迫使第二增阻镶块的自由端朝靠近缺口方向转动,使得第二抵推部推动嵌件本体沿自身长度方向滑移,使得定位柱外周壁与第一定位孔的内侧壁抵接,此时,第一复位弹件和第二复位弹件均具有弹性势能;步骤s4、注塑作业,通过热集流管系统对注塑孔进行注塑作业;步骤s5、冷却开模,在下模仁上升且与第一增阻镶块脱离后,第一复位弹件迫使第一增阻镶块的自由端朝远离嵌件放置槽方向转动,使得第一增阻镶块的第一抵推部脱离于嵌件本体外侧壁,自动解除对嵌件本体的阻尼固定约束;在下模仁上升且与第二增阻镶块脱离后,第二复位弹件迫使第二增阻镶块的自由端朝远离缺口方向转动,使得第二增阻镶块的第二抵推部脱离于嵌件本体外侧壁,自动解除对嵌件本体的阻尼固定约束,便于后续对嵌件成品的脱模作业;步骤s6、脱模作业 。
26.综上所述,本技术包括以下至少一种有益技术效果:1.注塑前,将嵌件本体放置于下模仁的嵌件放置槽内,并使得定位柱插设于第一定位孔,实现对嵌件本体在嵌件放置槽的定位,减少嵌件本体在注塑成型过程中发生位移的可能,保证了嵌件成品的尺寸精度和合格率,另外,上模仁和下模仁合模后,上模仁的下
端面抵接于嵌件本体的上端面,实现了上模仁对嵌件本体的竖向滑移自由度进行约束的目的,从而减少嵌件本体在注塑过程中发生上浮的可能性,进一步减少嵌件本体在注塑成型过程中发生位移的可能,保证了嵌件成品的尺寸精度和合格率;2.嵌件本体预定位后,进行合模时,在下模仁下降过程中,第一联动块的第一导向斜面抵接于第一增阻镶块的上部侧壁,下模仁继续下降,第一导向斜面迫使第一增阻镶块的自由端朝靠近限位台方向转动,使得第一抵推部推动嵌件本体沿自身宽度方向滑移且抵接于限位台,此时,第一复位弹件具有弹性势能,注塑完成后进行开模时,在下模仁上升且与第一增阻镶块脱离后,第一复位弹件迫使第一增阻镶块的自由端朝远离嵌件放置槽方向转动,使得第一增阻镶块的第一抵推部脱离于嵌件本体外侧壁,自动解除对嵌件本体的阻尼固定约束,便于后续对嵌件成品的脱模作业;3.注塑前,通过驱动部件控制转动轴旋转,从而使得限位板转动至不干涉放置嵌件本体的位置处后,接着将嵌件本体放置于下模仁的嵌件放置槽内,并使得定位柱插设于第一定位孔,实现对嵌件本体在嵌件放置槽的定位,减少嵌件本体在注塑成型过程中发生位移的可能,接着通过驱动部件控制转动轴转动复位,使得限位板自由端的下端面抵接于嵌件本体的上端面,一方面,起到对嵌件本体是否完全放入嵌件放置槽进行检测,减少嵌件本体没有完全放入嵌件放置槽的可能,另一方面,通过限位板对嵌件本体的竖向滑移自由度进行约束,从而减少嵌件本体在注塑过程中发生上浮的可能性,进一步减少嵌件本体在注塑成型过程中发生位移的可能,保证了嵌件成品的尺寸精度和合格率;在完成注塑后,对嵌件成品进行脱模时,通过驱动部件控制转动轴旋转,从而使得限位板转动至不干涉放置嵌件本体的位置处后,再对嵌件成品进行拿取。
附图说明
27.图1是实施例1中一种天窗机械组总成前举臂注塑模具的整体结构示意图。
28.图2是实施例1中下模仁和嵌件本体的结构示意图。
29.图3是实施例1中上模仁的结构示意图。
30.图4是实施例1中第一增阻镶块和第二增阻镶的结构示意图。
31.图5是图4在a处的局部放大示意图。
32.图6是实施例1中顶针板的结构示意图。
33.图7是实施例2中定模具的结构示意图。
34.图8是实施例2中下模仁的结构示意图。
35.图9是图8在b处的局部放大示意图。
36.图10是实施例2中上模仁的结构示意图。
37.图11是背景技术中前举臂的注塑成品结构示意图。
38.附图标记说明:1、定模具;11、安装腔;12、第二固定板;13、换向轮;2、动模具;3、下模仁;31、定位凹槽;32、嵌件放置腔;321、定位柱;322、顶针孔;33、下成型腔;34、限位台;35、第一安装槽;36、第一增阻镶块;361、第一抵推部;362、第一复位弹件;37、第一插接槽;38、第二安装槽;381、缺口;39、第二增阻镶块;391、第二抵推部;392、第二复位弹件;30、第二插接槽;301、固定槽;302、转动轴;303、限位板;4、上模仁;41、定位凸块;42、上成型腔;43、第二定位孔;44、注塑孔;45、第一联动块;451、第一导向斜面;46、第二联动块;461、第二
导向斜面;47、避让槽;5、嵌件本体;51、包覆部;52、外露部;53、第一定位孔;54、流液孔;50、塑料件;6、热流道模板;7、脱模机构;71、顶针板;711、第一固定板;72、顶针杆;73、液压油缸;8、驱动部件;81、限位扭簧;82、连接绳。
具体实施方式
39.以下结合附图1-11对本技术作进一步详细说明。
40.实施例1:参照图1,本技术实施例公开一种天窗机械组总成前举臂注塑模具,参照图1、图2,包括定模具1、位于定模具1上方的动模具2、通过螺栓安装于定模具1的下模仁3以及通过螺栓安装于动模具2的上模仁4,上模仁4位于下模仁3的上方,下模仁3放置有嵌件本体5,嵌件本体5呈条状设置,嵌件本体5具有包覆部51和外露部52。
41.参照图2、图3,下模仁3上端面的四个顶角处开设有定位凹槽31,上模仁4下端面的四个顶角处凸出有插设于定位凹槽31的定位凸块41。下模仁3的上端面开设有供嵌件本体5的外露部52放置的嵌件放置槽,本实施例中,嵌件放置槽设置有两个且沿下模仁3的宽度方向对称分布,下模仁3的上端面开设有连通于嵌件放置槽的下成型腔33,下成型腔33的深度大于嵌件放置槽的深度。上模仁4的下端面开设有与下成型腔33位置相对应的上成型腔42,嵌件本体5位于外露部52的下端面抵接于嵌件放置槽的底部内壁,嵌件本体5的上端面与下模仁3的上端面平齐。
42.嵌件放置槽的底部内壁凸出设置有定位柱321,定位柱321的轴向呈竖向设置,本实施例中,定位柱321设置有两个且沿嵌件放置槽的长度方向分布。定位柱321的上部呈锥形设置,嵌件本体5位于外露部52的上端面相对应贯穿开设有供定位柱321插设的第一定位孔53,第一定位孔53的直径大于定位柱321的最大直径使得第一定位孔53和定位柱321呈间隙配合。定位柱321的上端面凸出于下模仁3的上端面,上模仁4的下端面相对应开设有供定位柱321插设的第二定位孔43。
43.工作人员将嵌件本体5放置于嵌件放置槽时,定位柱321插设于第一定位孔53,实现嵌件本体5和嵌件放置槽的预定位后,嵌件本体5的包覆部51延伸至下成型腔33的上方,嵌件本体5位于包覆部51的外侧壁和注塑型腔的内侧壁之间具有流液间隙,嵌件本体5位于包覆部51的上端面贯穿开设有流液孔54,流液孔54设置有多个。上模仁4和下模仁3合模后,上模仁4的下端面抵接于嵌件本体5的上端面和下模仁3的上端面,上成型腔42和下成型腔33形成封闭的注塑型腔以用于对嵌件本体5的包覆部51进行注塑作业。
44.参照图1、图3,上模仁4开设有连通于注塑型腔的注塑孔44,动模具2的上端面安装有热流道模板6,热流道模板6设置有对注塑孔44进行注塑作业的热集流管系统,热集流管系统为现有技术,在此不做赘述。
45.参照图2、图3、图4,下模仁3设置有凸出于两个嵌件放置槽相互靠近的内侧壁以供嵌件本体5位于外露部52的外侧壁抵接的限位台34,限位台34的上端面与下模仁3的上端面平齐。下模仁3的上端面开设有第一安装槽35,第一安装槽35连通于嵌件放置槽远离限位台34一侧的内侧壁,下模仁3设置有内置于第一安装槽35的第一增阻镶块36,第一增阻镶块36为橡胶制品具有弹性。第一增阻镶块36的下部通过转轴销钉铰接于第一安装槽35的内壁,第一增阻镶块36的上部具有抵接于嵌件本体5位于外露部52侧壁的第一抵推部361。第一增
阻镶块36设置有在常态下迫使第一增阻镶块36的自由端朝远离嵌件放置槽方向转动的第一复位弹件362,第一复位弹件362可以采用扭簧,也可以采用玻珠螺丝,本实施例中,第一复位弹件362为第一玻珠螺丝,第一玻珠螺丝固定于第一增阻镶块36的中部,第一玻珠螺丝的玻珠端抵接于第一安装槽35靠近嵌件放置槽的内侧壁。
46.上模仁4设置有迫使第一增阻镶块36的第一抵推部361抵紧于嵌件本体5侧壁使得嵌件本体5沿宽度方向移动并抵接于限位台34的第一联动块45,第一联动块45凸出固定于上模仁4的下端面,第一联动块45具有抵接于第一增阻镶块36上部侧壁后迫使第一抵推部361抵紧于嵌件本体5位于外露部52侧壁的第一导向斜面451。下模仁3的上端面开设有连通于第一安装槽35远离嵌件放置槽一侧内壁的第一插接槽37,上模仁4和下模仁3合模后,第一联动块45插设于第一插接槽37,第一导向斜面451迫使第一增阻镶块36的自由端朝靠近限位台34方向转动,使得第一抵推部361推动嵌件本体5沿自身宽度方向滑移且抵接于限位台34侧壁,以阻尼形式对嵌件本体5进行固定。
47.参照图3、图4、图5,下模仁3的上端面开设有第二安装槽38,第二安装槽38设置有两个,第二安装槽38具有连通于嵌件放置槽的内侧壁的缺口381,下模仁3设置有内置于第二安装槽38的第二增阻镶块39,第二增阻镶块39相对应设置有两个,第二增阻镶块39为橡胶制品具有弹性,第二增阻镶块39的下部通过转轴销钉铰接于第二安装槽38的内壁,第二增阻镶块39的上部具有穿过缺口381且用于抵接于嵌件本体5侧壁的第二抵推部391。下模仁3设置有在常态下迫使第二增阻镶块39的自由端朝远离嵌件放置槽方向转动的第二复位弹件392,第二复位弹件392可以采用扭簧,也可以采用玻珠螺丝,本实施例中,第二复位弹件392为第二玻珠螺丝,第二玻珠螺丝固定于第二增阻镶块39的中部,第二玻珠螺丝的玻珠端抵接于第二安装槽38靠近嵌件放置槽的内侧壁。
48.上模仁4设置有迫使第二增阻镶块39的第二抵推部391抵紧于嵌件本体5位于外露部52侧壁使得嵌件本体5沿长度方向移动的第二联动块46。第二联动块46凸出固定于上模仁4的下端面,下模仁3的上端面开设有连通于第二安装槽38远离嵌件放置槽一侧内壁的第二插接槽30,第二联动块46具有抵接于第二增阻镶块39上部侧壁后迫使第二抵推部391抵紧于嵌件本体5侧壁的第二导向斜面461,第二导向斜面461设置有两个以用于同时控制两个第二增阻镶块39转动。上模仁4和下模仁3合模时,第二联动块46插设于第二插接槽30,第二联动块46的第二导向斜面461抵接于第二增阻镶块39的上部侧壁,下模仁3继续下降,第二导向斜面461迫使第二增阻镶块39的自由端朝靠近缺口381方向转动,使得第二抵推部391推动嵌件本体5沿自身长度方向滑移,使得定位柱321外周壁与第一定位孔53的内侧壁抵接,以阻尼形式对嵌件本体5进行固定。
49.参照图1、图6,定模具1开设有位于下模仁3下方的安装腔11,定模具1设置有脱模机构7,脱模机构7包括沿竖向滑移连接于安装腔11的顶针板71、若干个固定连接于顶针板71上端面的顶针杆72以及驱动顶针板71滑移升降的顶针驱动件。嵌件放置槽的底部内壁贯穿开设有供顶针杆72滑移穿设的顶针孔322,顶针杆72的轴向平行于定位柱321的轴向,顶针板71的侧壁固定连接有外置于安装腔11的第一固定板711,定模具1的外侧壁固定连接有第二固定板12,顶针驱动件为液压油缸73,液压油缸73的缸体固定连接于第二固定板12,液压油缸73的活塞杆固定连接于第一固定板711。
50.一种应用于天窗机械组总成前举臂注塑模具的注塑工艺:包括以下步骤:
步骤s1、注塑准备,在上模仁4的上成型腔42以及下模仁3的下成型腔33内涂抹脱模剂,且对嵌件本体5表面进行清理。
51.步骤s2、将嵌件本体5放置于嵌件放置槽,定位柱321插设于第一定位孔53,实现嵌件本体5和嵌件放置槽的预定位。
52.步骤s3、对上模仁4和下模仁3进行合模,在下模仁3下降过程中,第一联动块45的第一导向斜面451抵接于第一增阻镶块36的上部侧壁,下模仁3继续下降,第一导向斜面451迫使第一增阻镶块36的自由端朝靠近限位台34方向转动,使得第一抵推部361推动嵌件本体5沿自身宽度方向滑移且抵接于限位台34;第二联动块46的第二导向斜面461抵接于第二增阻镶块39的上部侧壁,下模仁3继续下降,第二导向斜面461迫使第二增阻镶块39的自由端朝靠近缺口381方向转动,使得第二抵推部391推动嵌件本体5沿自身长度方向滑移,使得定位柱321外周壁与第一定位孔53的内侧壁抵接,此时,第一复位弹件362和第二复位弹件392均具有弹性势能。
53.步骤s4、注塑作业,通过热集流管系统对注塑孔44进行注塑作业。
54.步骤s5、冷却开模,在下模仁3上升且与第一增阻镶块36脱离后,第一复位弹件362迫使第一增阻镶块36的自由端朝远离嵌件放置槽方向转动,使得第一增阻镶块36的第一抵推部361脱离于嵌件本体5外侧壁,自动解除对嵌件本体5的阻尼固定约束;在下模仁3上升且与第二增阻镶块39脱离后,第二复位弹件392迫使第二增阻镶块39的自由端朝远离缺口381方向转动,使得第二增阻镶块39的第二抵推部391脱离于嵌件本体5外侧壁,自动解除对嵌件本体5的阻尼固定约束,便于后续对嵌件成品的脱模作业。
55.步骤s6、脱模作业,对嵌件成品进行脱模时,液压油缸73的活塞杆收缩驱动顶针板71上升,顶针板71上升带动顶针杆72穿过顶针孔322抵接于嵌件本体5下端面,顶针板71继续上升,将嵌件成品顶出嵌件放置槽,使得嵌件成品的外周壁与下成型腔33内侧壁、嵌件放置槽内侧壁分离,通过人工对嵌件成品进行拿取。
56.实施例2:参照图7,本实施例与实施例1的不同之处在于,非工作状态下,顶针杆72下沉于嵌件放置槽的底部内壁,下模仁3和定模具1均具有穿绳通道,下模仁3的穿绳通道连通于固定槽301,定模具1的穿绳通道连通于定模具1的外侧壁,定模具1的外侧壁转动连接有位于安装腔11下方的换向轮13。
57.参照图8、图9,下模仁3的上端面开设有位于两个嵌件放置槽之间的固定槽301,固定槽301连通于嵌件放置槽,第一固定槽301的底部内壁转动连接有转动轴302,转动轴302的轴向呈竖向设置,转动轴302的上部外周壁固定连接有限位板303,限位板303凸出于下模仁3的上端面。下模仁3设置有驱动转动轴302转动的驱动部件8,限位板303自由端的下端面抵接于嵌件本体5位于外露部52的上端面,上模仁4下端面开设有供限位板303插设的避让槽47。
58.参照图7、图8、图9,驱动部件8包括连接绳82以及限位扭簧81,连接绳82为钢丝绳,连接绳82的一端固定连接于限位板303的自由端侧壁,连接绳82的另一端依次穿过下模仁3、定模具1的穿绳通道且绕设于换向轮13下周壁并固定于顶针板71,连接绳82部分外露于定模具1。限位扭簧81套设于转动轴302,限位扭簧81的一端固定连接于固定槽301底部内壁,限位扭簧81的另一端固定连接于转动轴302外周壁,限位扭簧81迫使转动轴302转动使
得限位板303的自由端在常态下延伸至嵌件放置槽上方。
59.实施例2的实施原理为:常态下,限位板303的自由端延伸至嵌件放置槽上方,注塑前,液压油缸73驱动顶针板71上升一段距离且顶针杆72仍未凸出于嵌件放置槽,通过连接绳82拉动限位板303的自由端绕转动轴302的轴线转动,此时,限位扭簧81具有弹性势能,从而使得限位板303转动至不干涉放置嵌件本体5的位置处后,接着将嵌件本体5放置于下模仁3的嵌件放置槽内,并使得定位柱321插设于第一定位孔53,接着液压油缸73驱动顶针板71下降复位,限位扭簧81迫使限位板303转动复位,使得限位板303自由端的下端面抵接于嵌件本体5的上端面;下模仁3和上模仁4开模后,对嵌件成品进行脱模时,液压油缸73驱动顶针板71上升一段距离,限位板303转动至不干涉放置嵌件本体5的位置处后,顶针驱动件继续驱动顶针板71上升一段距离,顶针杆72凸出于嵌件放置槽底部内壁,将嵌件成品顶出嵌件放置槽,再对嵌件成品进行拿取。
60.以上均为本技术的较佳实施例,并非依此限制本技术的保护范围,故:凡依本技术的结构、形状、原理所做的等效变化,均应涵盖于本技术的保护范围之内。