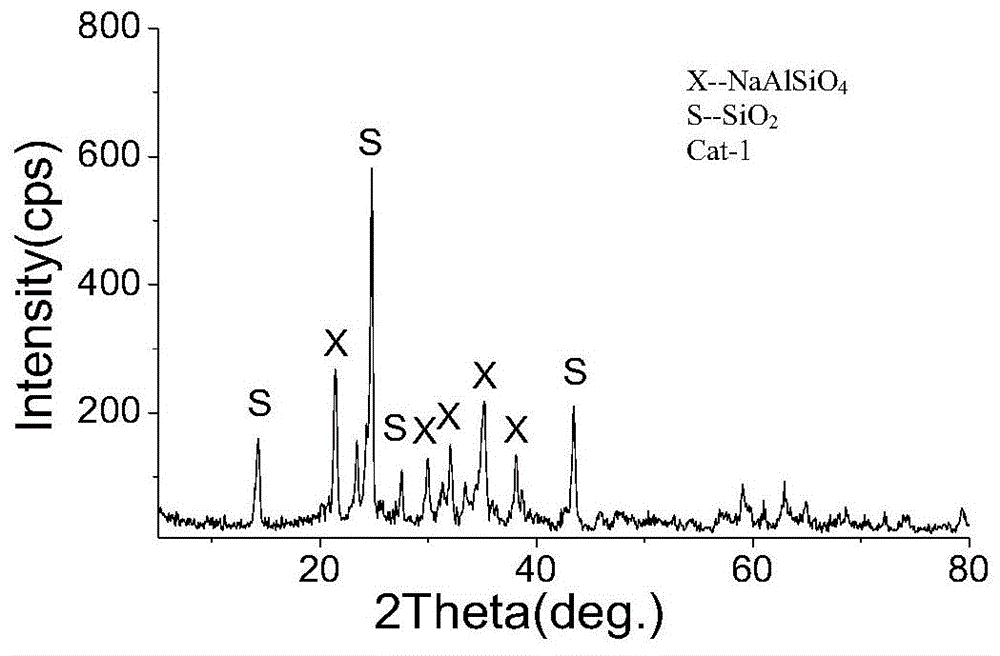
本发明涉及固废处理
技术领域:
,尤其是涉及一种高铝粉煤灰的改性方法。
背景技术:
:粉煤灰是一种工业废渣,我国历年累积堆放总量已达10亿吨以上,目前对粉煤灰的利用率只有40%左右,大部分仍占用大量土地堆存起来,污染了环境,破坏了生态平衡。高铝粉煤灰是我国所特有的一种新型铝资源,其远景资源量约100亿吨氧化铝。而我国现已查明的铝土矿资源储量仅有32亿吨,按目前的开采规模估算,资源保障年限仅约20年,铝资源当前的对外依存度高达55%。因此,高铝粉煤灰的开发利用对于缓解我国铝土矿资源短缺、保障我国铝产业安全和增强铝产业可持续发展能力具有现实意义。粉煤灰中大部分铝以莫来石相存在,常压条件下无法直接酸浸提取,需添加活化剂经过焙烧活化使莫来石相转变为可溶于酸的含铝物相后再进行酸浸。现有技术从粉煤灰中提取铝的方法主要采用回转窑焙烧活化-酸浸工艺,其存在温度高、时间长、能耗大及铝提取率低等问题。技术实现要素:本发明的目的是提供一种高铝粉煤灰的改性方法,解决现有高铝粉煤灰提铝工艺中温度高、时间长、能耗大及铝提取率低等问题技术问题。为了达到上述目的,本发明提供如下技术方案:高铝粉煤灰的改性方法,包括:(1)将将高铝粉煤灰粗粉与碳酸钠按照1:0.3-0.5比例混合置于高压反应釜中,向釜内通入氟气与氮气的混合气体,进行高温氟化处理后得到氟化后的粉煤灰;(2)取步骤(1)中的氟化后的粉煤灰进行球磨粉碎,过筛,得到粉煤灰细粉;(4)将步骤(2)所获粉煤灰细粉与表面活性剂混合,之后加入碱性溶液,再将形成的混合物转移到高温反应釜中,在高温下反应后出料干燥,即得改性高铝粉煤灰。在一种优选的实施方式中,步骤(1)中,所述氟气与氮气的混合气体中的氟气与氮气的体积之比为3~5:1,通入釜内的氟气与氮气的混合气体的压强为10~100kpa。在一种优选的实施方式中,步骤(1)中,高温氟化处理的温度为200~300℃,反应时间为2~8小时。在一种优选的实施方式中,步骤(3)中,所述表面活性剂包括硬脂酸、十二烷基硫酸钠、十二烷基苯磺酸钠、甘胆酸钠中的任意一种或多种的组合。在一种优选的实施方式中,所述碱性溶液包括氢氧化钠溶液、氢氧化钾溶液和氨水溶液中的一种。在一种优选的实施方式中,步骤(3)中,高温反应釜中的反应温度为200~300℃,反应时间为2~3小时。常规的高铝粉煤灰提铝工艺中,需要先将粉煤灰与碳酸钠混合后于800-1300℃的高温下煅烧,才能使粉煤灰中的莫来石相转化为玻璃相,便于后续的酸法工艺溶出铝,能耗大,时间长。本发明的高铝粉煤灰的改性方法针对高铝粉煤灰的酸法提铝工艺,将粉煤灰做改性处理,经过多次实验研究发现,先将粉煤灰粗粉与碳酸钠在氟气与氮气的混合气体环境下进行高温氟化预活化处理,后再进行物理粉磨,能够将粉煤灰中的大部分莫来石相转化为玻璃相,有效提高粉煤灰的活性,同时该预处理的过程对于温度的没有过高的需求,避免了常规的高温煅烧的活化处理工艺,节省了能耗。另外,再将经过物理活化后的粉煤灰细粉加入表面活性剂处理后,在后续的酸性提铝工艺中,能够有效果提高铝的溶出率。附图说明为了更清楚地说明本发明实施例或现有技术中的技术方案,下面将对实施例或现有技术描述中所需要使用的附图作简单地介绍,显而易见地,下面描述中的附图仅仅是本发明的一些实施例,对于本领域普通技术人员来讲,在不付出创造性劳动的前提下,还可以根据这些附图获得其他的附图。图1是本发明实施例1中得到改性后的粉煤灰的x射线衍射图谱;图2是本发明实施例2中得到改性后的粉煤灰的x射线衍射图谱;图3是本发明实施例3中得到改性后的粉煤灰的x射线衍射图谱;图4是本发明实施例4中得到改性后的粉煤灰的x射线衍射图谱;图5是本发明实施例5中得到改性后的粉煤灰的x射线衍射图谱;图6是本发明对比例1中得到改性后的粉煤灰的x射线衍射图谱;图7是本发明对比例2中得到改性后的粉煤灰的x射线衍射图谱;图8是本发明对比例3中得到改性后的粉煤灰的x射线衍射图谱。具体实施方式下面将结合本发明的附图,对本发明的技术方案进行清楚、完整地描述,显然,所描述的实施例仅仅是本发明一部分实施例,而不是全部的实施例。基于本发明中的实施例,本领域普通技术人员在没有作出创造性劳动前提下所获得的所有其他实施例,都属于本发明保护的范围。在本发明的一较为典型的具体实施方案之中,高铝粉煤灰的改性方法,包括:(1)将高铝粉煤灰粗粉与碳酸钠按照1:0.3-0.5的比例混合置于高压反应釜中,向釜内通入氟气与氮气的混合气体,进行高温氟化处理后得到预处理后的粉煤灰;所述氟气与氮气的混合气体中的氟气与氮气的体积之比为3~5:1,通入釜内的氟气与氮气的混合气体的压强为10~100kpa;高温氟化处理的温度为200~300℃,反应时间为2~8小时。(2)取步骤(1)中的氟化后的粉煤灰进行球磨粉碎,过筛,得到粉煤灰细粉;(3)将步骤(2)所获粉煤灰细粉与表面活性剂混合,之后加入碱性溶液,再将形成的混合物转移到高温反应釜中,在高温下反应后出料干燥,即得改性高铝粉煤灰。所述表面活性剂包括硬脂酸、十二烷基硫酸钠、十二烷基苯磺酸钠、甘胆酸钠中的任意一种或多种的组合;所述碱性溶液包括氢氧化钠溶液、氢氧化钾溶液和氨水溶液中的一种;高温反应釜中的反应温度为200~300℃,反应时间为2~3小时。以下结合若干实施例及相应附图对本发明的技术方案作进一步的解释说明。在如下实施例中,所用试剂均优选为分析纯。以下实施例选取某电厂粉煤灰作为样品,该试样中除了含有一定比例的玻璃相外,还有莫来石(al6si2o13)、石英(sio2)和一些微量的赤铁矿(fe2o3)、石灰石(caco3)等矿物。实施例1包括如下步骤:(1)将高铝粉煤灰粗粉与碳酸钠按照1:0.3的比例混合置于高压反应釜中,向釜内通入氟气与氮气的混合气体,进行高温氟化处理后得到预处理后的粉煤灰;所述氟气与氮气的混合气体中的氟气与氮气的体积之比为3:1,通入釜内的氟气与氮气的混合气体的压强为50kpa;高温氟化处理的温度为200℃,反应时间为4小时。(2)取步骤(1)中的氟化后的粉煤灰进行球磨粉碎,过100目筛,得到粉煤灰细粉;(3)将步骤(2)所获粉煤灰细粉与表面活性剂混合,之后加入碱性溶液,再将形成的混合物转移到高温反应釜中,在高温下反应后出料干燥,即得改性高铝粉煤灰。所述表面活性剂为十二烷基硫酸钠;所述碱性溶液为氢氧化钠溶液;高温反应釜中的反应温度为200℃,反应时间为2小时;编号为cat-1。实施例2包括如下步骤:(1)将高铝粉煤灰粗粉与碳酸钠按照1:0.3的比例混合置于高压反应釜中,向釜内通入氟气与氮气的混合气体,进行高温氟化处理后得到预处理后的粉煤灰;所述氟气与氮气的混合气体中的氟气与氮气的体积之比为3:1,通入釜内的氟气与氮气的混合气体的压强为80kpa;高温氟化处理的温度为250℃,反应时间为4小时。(2)取步骤(1)中的氟化后的粉煤灰进行球磨粉碎,过100目筛,得到粉煤灰细粉;(3)将步骤(2)所获粉煤灰细粉与表面活性剂混合,之后加入碱性溶液,再将形成的混合物转移到高温反应釜中,在高温下反应后出料干燥,即得改性高铝粉煤灰。所述表面活性剂包括硬脂酸和十二烷基硫酸钠;所述碱性溶液为括氢氧化钾溶液;高温反应釜中的反应温度为300℃,反应时间为2小时;编号为cat-2。实施例3包括如下步骤:(1)将高铝粉煤灰粗粉与碳酸钠按照1:0.4的比例混合置于高压反应釜中,向釜内通入氟气与氮气的混合气体,进行高温氟化处理后得到预处理后的粉煤灰;所述氟气与氮气的混合气体中的氟气与氮气的体积之比为4:1,通入釜内的氟气与氮气的混合气体的压强为60kpa;高温氟化处理的温度为200℃,反应时间为4小时。(2)取步骤(1)中的氟化后的粉煤灰进行球磨粉碎,过150目筛,得到粉煤灰细粉;(3)将步骤(2)所获粉煤灰细粉与表面活性剂混合,之后加入碱性溶液,再将形成的混合物转移到高温反应釜中,在高温下反应后出料干燥,即得改性高铝粉煤灰。所述表面活性剂包括硬脂酸和十二烷基苯磺酸钠;所述碱性溶液包括氢氧化钠溶液;高温反应釜中的反应温度为200℃,反应时间为3小时;编号为cat-3。实施例4包括如下步骤:(1)将高铝粉煤灰粗粉与碳酸钠按照1:0.4的比例混合置于高压反应釜中,向釜内通入氟气与氮气的混合气体,进行高温氟化处理后得到预处理后的粉煤灰;所述氟气与氮气的混合气体中的氟气与氮气的体积之比为5:1,通入釜内的氟气与氮气的混合气体的压强为80kpa;高温氟化处理的温度为300℃,反应时间为3小时。(2)取步骤(1)中的氟化后的粉煤灰进行球磨粉碎,过100目筛,得到粉煤灰细粉;(3)将步骤(2)所获粉煤灰细粉与表面活性剂混合,之后加入碱性溶液,再将形成的混合物转移到高温反应釜中,在高温下反应后出料干燥,即得改性高铝粉煤灰。所述表面活性剂为十二烷基硫酸钠和十二烷基苯磺酸钠;所述碱性溶液为氢氧化钠溶液;高温反应釜中的反应温度为300℃,反应时间为2小时;编号为cat-4。实施例5包括如下步骤:(1)将高铝粉煤灰粗粉与碳酸钠按照1:0.5的比例混合置于高压反应釜中,向釜内通入氟气与氮气的混合气体,进行高温氟化处理后得到预处理后的粉煤灰;所述氟气与氮气的混合气体中的氟气与氮气的体积之比为4:1,通入釜内的氟气与氮气的混合气体的压强为60kpa;高温氟化处理的温度为300℃,反应时间为4小时。(2)取步骤(1)中的氟化后的粉煤灰进行球磨粉碎,过100目筛,得到粉煤灰细粉;(3)将步骤(2)所获粉煤灰细粉与表面活性剂混合,之后加入碱性溶液,再将形成的混合物转移到高温反应釜中,在高温下反应后出料干燥,即得改性高铝粉煤灰。所述表面活性剂为硬脂酸;所述碱性溶液为氢氧化钠溶液;高温反应釜中的反应温度为250℃,反应时间为2小时;编号为cat-5。对照例1本对照例与实施例1的不同之处在于:不对粉煤灰粗粉进行高压氟化处理,直接进行物理球磨。具体制备方法包括:(1)将粉煤灰粗粉与碳酸钠按照1:0.3的比例混合,进行球磨粉碎,过100目筛,得到粉煤灰细粉;(2)将步骤(1)所获粉煤灰细粉与表面活性剂混合,之后加入碱性溶液,再将形成的混合物转移到高温反应釜中,在高温下反应后出料干燥,即得改性高铝粉煤灰。所述表面活性剂为十二烷基硫酸钠;所述碱性溶液为氢氧化钠溶液;高温反应釜中的反应温度为200℃,反应时间为2小时;编号为cat-1a。对照例2本对照例与实施例2的不同之处在于:对经过高压氟化后的粉煤灰粗粉不进行物理球磨,直接与表面活性剂进行高温反应。具体制备方法包括:(1)将高铝粉煤灰粗粉置于高压反应釜中,向釜内通入氟气与氮气的混合气体,进行高温氟化处理后得到预处理后的粉煤灰;所述氟气与氮气的混合气体中的氟气与氮气的体积之比为3:1,通入釜内的氟气与氮气的混合气体的压强为80kpa;高温氟化处理的温度为250℃,反应时间为4小时。(2)将步骤(1)所获粉煤灰粗粉与表面活性剂混合,之后加入碱性溶液,再将形成的混合物转移到高温反应釜中,在高温下反应后出料干燥,即得改性高铝粉煤灰。所述表面活性剂包括硬脂酸和十二烷基硫酸钠;所述碱性溶液为括氢氧化钾溶液;高温反应釜中的反应温度为300℃,反应时间为2小时;编号为cat-2a。对照例3本对照例与实施例3的不同之处在于:对经过物理球磨后的粉煤灰细粉直接进行后续的酸法提铝工艺。具体制备方法包括:包括如下步骤:(1)将高铝粉煤灰粗粉置于高压反应釜中,向釜内通入氟气与氮气的混合气体,进行高温氟化处理后得到预处理后的粉煤灰;所述氟气与氮气的混合气体中的氟气与氮气的体积之比为4:1,通入釜内的氟气与氮气的混合气体的压强为60kpa;高温氟化处理的温度为200℃,反应时间为4小时。(2)取步骤(1)中的预处理后的粉煤灰进行球磨粉碎,过150目筛,得到粉煤灰细粉;编号为cat-3a。将以上实施例1-5与对比例1-3中得到的粉煤灰样品进行x射线衍射分析对比,对比结果如图1-8所示;并将得到的粉煤灰样品采用相同的酸法浸出工艺提取铝,其中的工艺参数均相同,对比铝的溶出率,结果如下表1。表1:编号溶出率%(铝)备注cat-194.2%实施例1cat-293.7%实施例2cat-392.8%实施例3cat-492.5%实施例4cat-592.3%实施例5cat-1a78.1%对照例1cat-2a89.5%对照例2cat-3a81.3%对照例3由表1可以看出,经过本发明的方法将粉煤灰改性后,经过酸法溶出,其中铝的溶出率较高,其明显优于对比例。由图1至5可以看出,实施例1至5的得到的改性后的粉煤灰样品经过x射线衍射后,其衍射图谱中几乎所有的莫来石已经完全反应,都转为了可溶出的铝盐,而对比例1与实施例1相比,其衍射图谱中还存在较多的莫来石相,对比例2与实施例2相比,其衍射图谱中区别较小,因此在未将粉煤灰经过物理研磨过程后,并没有明显的莫来石相的区别;对比例3与实施例3相比,其衍射图谱中还存在较多的莫来石相。因此,由本发明的改性方法将粉煤灰改性处理后,能够有效降低粉煤灰中的莫来石相,提高粉煤灰的活性。以上所述,仅为本发明的具体实施方式,但本发明的保护范围并不局限于此,任何熟悉本
技术领域:
的技术人员在本发明揭露的技术范围内,可轻易想到变化或替换,都应涵盖在本发明的保护范围之内。因此,本发明的保护范围应所述以权利要求的保护范围为准。当前第1页1 2 3