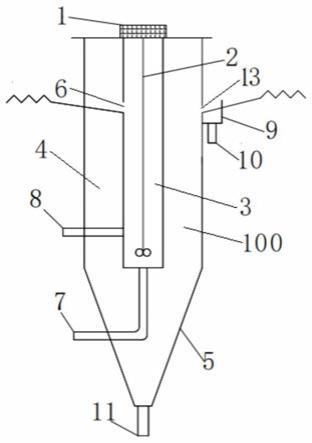
1.本发明涉及废水处理技术领域,具体而言,涉及利用剩余污泥吸附预处理煤气化废水的装置、方法及用途。
背景技术:2.煤气化技术是在气化剂的作用下将煤炭转化为气态清洁能源的技术,该技术广泛应用于现代煤化工清洁发展。然而煤气化过程中因高温煤气的冷却和洗涤等生产过程产生大量高浓度有机废水,成为阻碍现代煤化工发展的重要环保难题之一。
3.煤气化废水的种类繁多,由于废水产生的工艺类型不同,废水处理的难易程度也有所不同,其中最难处理的是固定床鲁奇气化炉工艺产生的废水,其不仅有机污染物浓度高,经酚氨回收预处理后的废水cod仍达到3000-6000mg/l,而且有机物污染物成分复杂,含有大量酚类化合物、苯系物、含氮杂环、多环芳烃和长链烷烃等;此外,废水的可生化性也较差,可生化指标(bod5/cod)仅为0.3-0.4,属于难降解废水,单纯依靠传统厌氧-好氧生化工艺难以稳定高效处理该废水。因而,处理煤气化废水的工艺仍有待进一步改善。
技术实现要素:4.本技术主要是基于以下问题和发现提出的:
5.为了降低有机污染物浓度并提高可生化性,保证生化工艺段高效运行,可以采用对煤气化废水进行预处理的方式。发明人发现,煤气化废水生化处理过程中,好氧段每日可以产生大量剩余污泥,剩余污泥主要是由微生物细胞体构成的,其代谢过程中分泌的包裹在细胞壁外的多聚物(extracellular polymeric substances,eps)主要由蛋白质、多糖、腐殖质、核酸等高分子聚合物构成,其中含有的氨基、羧基、羟基及疏水基团等官能团,可以为煤气化废水中难降解有机污染物提供大量的吸附位点,通过分子力、静电力、离子交换、络合、螯合、微沉淀等物理、化学过程吸附去除废水中的有机物;同时,剩余污泥作为吸附剂预处理煤气化废水,还可以实现剩余污泥的再利用,降低煤气化废水的处理成本。然而,能够实施利用剩余污泥吸附预处理煤气化废水的装置较少,且现有的装置难以高效、简捷的降低废水的有机物浓度,提高废水的可生化性。
6.本发明旨在至少在一定程度上解决相关技术中的技术问题之一。为此,本发明的一个目的在于提出一种利用剩余污泥吸附预处理煤气化废水的装置,以降低废水的有机物浓度,提高废水的可生化性。
7.在本发明的一个方面,本发明提出了一种利用剩余污泥吸附预处理煤气化废水的装置。根据本发明的实施例,该装置包括:壳体,所述壳体内限定出有上下布置的吸附沉降区和污泥浓缩区,所述污泥浓缩区为倒锥体结构,所述污泥浓缩区底部设有排泥口;吸附反应器,所述吸附反应器设在所述壳体内,所述吸附反应器顶部与所述壳体顶壁相连,所述吸附反应器内设有搅拌装置,所述吸附反应器的上部设有泥水出口、下部设有进水进泥口,所述吸附反应器将所述吸附沉降区分隔为吸附区和沉降区,所述吸附反应器内为吸附区,所
述吸附反应器外为沉降区,所述吸附区和所述沉降区通过所述泥水出口连通;沉降区出水堰,所述出水堰设在所述壳体上部,所述壳体通过出水口与所述出水堰连通,所述出水口位置不高于所述泥水出口,所述出水堰底部设有排水口;隔板,所述隔板设在所述吸附沉降区内,所述隔板止抵于所述壳体的顶壁、所述壳体的侧壁和所述吸附反应器外壁,并将所述沉降区分隔为仅底部连通的第一沉降区和第二沉降区,所述泥水出口位于所述第一沉降区,所述出水口位于所述第二沉降区。
8.发明人发现,一方面,该装置是利用废水生化净化系统中废弃的剩余污泥吸附煤气化废水中的有机物,未增加新的吸附介质,其中剩余污泥中含有的氨基、羧基、羟基及疏水基团等官能团,为煤气化废水中难降解有机污染物提供大量的吸附位点,通过分子力、静电力、离子交换、络合、螯合、微沉淀等物理、化学过程吸附去除废水中的有机物,从而既能大幅降低废水的有机物浓度,又能提高废水的可生化性,使预处理废水后续的生化处理工艺高效稳定地运行,同时可以有效实现剩余污泥的再利用,降低废水的处理成本;另一方面,本发明将吸附区、沉降区和污泥浓缩区有效地融合在该装置中,设备整体结构简单,操作方便,便于使用,避免了多个设备串联的冗杂结构,降低了废水处理的原料成本、设备成本和占地面积;再一方面,该装置通过隔板将沉降区分隔为仅底部连通的第一沉降区和第二沉降区,使得吸附反应器中吸附反应后的泥水混合物通过泥水出口流至第一沉降区进行沉降,沉降后的水和少量污泥通过隔板底部流向第二沉降区继续沉降,增加了泥水混合物的出水路径和沉降时间,使得污泥的沉降效果佳,进而有利于提高废水的预处理效率,且隔板与壳体、吸附反应器相连,还可以提高对吸附反应器的固定效果,保证设备的结构稳定性。由此,该装置不仅可以大幅降低废水中的有机物浓度,提高废水的可生化性和处理效率,还能实现废弃的剩余污泥的再利用,降低废水的处理成本,此外,该装置还具有结构简单、处理高效和易操作等的优点。
9.另外,根据本发明上述实施例的利用剩余污泥吸附预处理煤气化废水的装置还可以具有如下附加的技术特征:
10.根据本发明的实施例,所述泥水出口和所述吸附反应器顶部之间的距离与所述吸附反应器高度的比值为(0.2~0.3):1。
11.根据本发明的实施例,所述出水口和所述壳体顶壁之间的距离与所述沉降区高度的比值为(0.2~0.3):1。
12.根据本发明的实施例,所述出水口位置低于所述泥水出口。
13.根据本发明的实施例,所述吸附区与所述沉降区的体积比为1:(4~6)。
14.根据本发明的实施例,所述进水进泥口与煤气化废水供给装置和生化池好氧段剩余污泥出口相连,所述排水口与后续废水生化工艺相连。
15.根据本发明的实施例,所述出水堰外堰壁的顶部高于所述出水口。
16.根据本发明的实施例,所述隔板的底部不高于所述吸附反应器的底部。
17.根据本发明的实施例,所述吸附反应器的下部设有取样口,所述取样口位置高于所述进水进泥口。
18.根据本发明的实施例,利用剩余污泥吸附预处理煤气化废水的装置还包括:搅拌电机,所述搅拌电机设在所述壳体顶部且与所述搅拌装置相连。
19.根据本发明的实施例,所述隔板与所述壳体的顶壁和/或所述壳体的侧壁固定相
连。
20.根据本发明的实施例,所述出水堰沿所述第二沉降区壳体外周壁周向的至少一部分布置。
21.在本发明的另一个方面,本发明提出了一种采用前面所述的装置实施利用剩余污泥吸附预处理煤气化废水的方法,根据本发明的实施例,该方法包括:(1)将剩余污泥和煤气化废水供给至吸附反应器内,在搅拌条件下进行吸附反应;(2)吸附反应后的泥水混合物通过泥水出口流至第一沉降区进行沉降,沉降后的水和少量污泥通过隔板底部流向第二沉降区继续沉降;(3)通过沉降区出水堰回收所述第二沉降区沉降后的水,通过排泥口回收所述第一沉降区和所述第二沉降区沉降形成的浓缩污泥,实现泥水分离。
22.发明人发现,该方法是利用废水生化净化系统中废弃的剩余污泥吸附煤气化废水中的有机物,未增加新的吸附介质,其中剩余污泥中含有的氨基、羧基、羟基及疏水基团等官能团,为煤气化废水中难降解有机污染物提供大量的吸附位点,通过分子力、静电力、离子交换、络合、螯合、微沉淀等物理、化学过程吸附去除废水中的有机物,从而既能大幅降低废水的有机物浓度,又能提高废水的可生化性,使预处理废水后续的生化处理工艺高效稳定地运行,同时可以有效实现剩余污泥的再利用,降低废水的处理成本;另一方面,该方法将吸附区、沉降区和污泥浓缩区有效地融合在该装置中,设备整体结构简单,操作方便,便于使用,避免了多个设备串联的冗杂结构,降低了废水处理的原料成本、设备成本和占地面积;再一方面,该方法通过隔板将沉降区分隔为仅底部连通的第一沉降区和第二沉降区,使得吸附反应器中吸附反应后的泥水混合物通过泥水出口流至第一沉降区进行沉降,沉降后的水和少量污泥通过隔板底部流向第二沉降区继续沉降,增加了泥水混合物的出水路径和沉降时间,使得污泥的沉降效果佳,进而有利于提高废水的预处理效率,且隔板与壳体、吸附反应器相连,还可以提高对吸附反应器的固定效果,保证设备的结构稳定性。由此,该方法操作简单、方便,可重复,易于实现和规模化生产,不仅可以大幅降低废水中的有机物浓度,提高废水的可生化性和处理效率,还能实现废弃的剩余污泥的再利用,降低废水的处理成本。具体地,与未进行预处理的煤气化废水相比,采用该方法获得的预处理废水的cod含量可降低20%-40%,废水的可生化指标可提高20%左右。
23.根据本发明的实施例,所述剩余污泥和所述煤气化废水在所述吸附反应器内的停留时间不大于2h。
24.根据本发明的实施例,供给至所述吸附反应器内的剩余污泥和煤气化废水与流出的泥水混合物保持动态平衡,任选地,所述剩余污泥和所述煤气化废水的固液比为0.5~1g/l。
25.根据本发明的实施例,所述剩余污泥为生化池好氧段的剩余污泥,所述剩余污泥的单日供给量不大于生化池好氧段单日产生的剩余污泥;
26.根据本发明的实施例,所述吸附反应器内的温度为30~35℃;任选地,在200-300转/分的搅拌速率下进行所述吸附反应。
27.根据本发明的实施例,所述污泥浓缩区内的浓缩污泥高度不高于所述污泥浓缩区高度的2/3,优选不高于1/3。
28.根据本发明的实施例,在吸附反应器下部取样,并对取得的样品进行检测,根据检测结果控制所述剩余污泥和所述煤气化废水的固液比。
29.在本发明的又一个方面,本发明提出了一种前面所述的装置和前面所述的方法在煤气化废水处理和/或剩余污泥处理中的用途。与现有技术相比,该装置不仅可以应用于煤气化废水处理中,还可以应用于剩余污泥处理中,应用范围广,实用性强。
30.本发明的附加方面和优点将在下面的描述中部分给出,部分将从下面的描述中变得明显,或通过本发明的实践了解到。
附图说明
31.本发明的上述和/或附加的方面和优点从结合下面附图对实施例的描述中将变得明显和容易理解,其中:
32.图1是根据本发明一个实施例的预处理煤气化废水的装置的截面正视图。
33.图2是根据本发明一个实施例的预处理煤气化废水的装置的截面俯视图。
34.图3是根据本发明再一个实施例的预处理煤气化废水的方法的流程示意图。
35.图4是根据本发明实施例1的煤气化废水进水和沉降区出水堰出水的cod含量的对比示意图。
36.图5是根据本发明实施例1的煤气化废水和沉降区出水堰出水的生化性指标的对比示意图。
37.附图标记:1:搅拌电机
ꢀꢀ
2:搅拌装置
ꢀꢀ
3:吸附反应器
ꢀꢀ
4:吸附沉降区
ꢀꢀ
5:污泥浓缩区
ꢀꢀ
6:泥水出口
ꢀꢀ
7:进水进泥口
ꢀꢀ
8:取样口
ꢀꢀ
9:沉降区出水堰
ꢀꢀ
10:排水口
ꢀꢀ
11:排泥口
ꢀꢀ
12:隔板
ꢀꢀ
13:出水口
ꢀꢀ
100:壳体
ꢀꢀ
41:第一沉降区
ꢀꢀ
42:第二沉降区。
具体实施方式
38.下面详细描述本发明的实施例。下面描述的实施例是示例性的,仅用于解释本发明,而不能理解为对本发明的限制。实施例中未注明具体技术或条件的,按照本领域内的文献所描述的技术或条件或者按照产品说明书进行。所用试剂或仪器未注明生产厂商者,均为可以通过市购获得的常规产品。
39.在本发明的一个方面,本发明提出了一种利用剩余污泥吸附预处理煤气化废水的装置。根据本发明的实施例,参照图1、图2理解,该装置包括:壳体100,所述壳体100内限定出有上下布置的吸附沉降区4和污泥浓缩区5,所述污泥浓缩区5为倒锥体结构,以保证污泥浓缩区中的污泥浓缩效果并方便底部排泥,所述污泥浓缩区5底部设有排泥口11,用以排净污泥浓缩区中的污泥;吸附反应器3,所述吸附反应器3设在所述壳体100内,优选地,壳体100和吸附反应器3可以均为筒体,吸附反应器3和壳体100同轴设置,由此可以进一步保证整个设备的结构稳定性;所述吸附反应器3顶部与所述壳体100顶壁相连,所述吸附反应器3内设有搅拌装置2,以便使吸附反应器中的剩余污泥和煤气化废水能够充分混合,提高对废水的预处理效率及效果,所述吸附反应器3的上部设有泥水出口6、下部设有进水进泥口7,进水进泥口7直接或间接贯穿壳体100的外壁与煤气化废水供给装置及剩余污泥出口相连,所述吸附反应器3将所述吸附沉降区4分隔为吸附区和沉降区,所述吸附反应器3内为吸附区,所述吸附反应器3外为沉降区,所述吸附区和所述沉降区通过所述泥水出口6连通;沉降区出水堰9,所述出水堰9设在所述壳体100上部,所述壳体100通过出水口13与所述出水堰9连通,所述出水口13位置不高于所述泥水出口6,由此不仅有利于沉降区的废水从出水口流
出,还能调节沉降区的液面高度,防止废水从泥水出口倒流入吸附反应器中,所述出水堰9底部设有排水口10;隔板12,所述隔板12设在所述吸附沉降区4内,所述隔板12止抵于所述壳体100的顶壁、所述壳体100的侧壁和所述吸附反应器3外壁,并将所述沉降区分隔为仅底部连通的第一沉降区41和第二沉降区42,所述泥水出口6位于所述第一沉降区41,所述出水口13位于所述第二沉降区42,由此既可以改善吸附反应器流出的泥水混合物的沉降效果,还能提高整个设备的结构稳定性。
40.根据本发明的实施例,发明人发现,一方面,该装置是利用废水生化净化系统中废弃的剩余污泥吸附煤气化废水中的有机物,未增加新的吸附介质,其中剩余污泥中含有的氨基、羧基、羟基及疏水基团等官能团,为煤气化废水中难降解有机污染物提供大量的吸附位点,通过分子力、静电力、离子交换、络合、螯合、微沉淀等物理、化学过程吸附去除废水中的有机物,从而既能大幅降低废水的有机物浓度,又能提高废水的可生化性,使预处理废水后续的生化处理工艺高效稳定地运行,同时可以有效实现剩余污泥的再利用,降低废水的处理成本;另一方面,本发明将吸附区、沉降区和污泥浓缩区有效地融合在该装置中,设备整体结构简单,操作方便,便于使用,避免了多个设备串联的冗杂结构,降低了废水处理的原料成本、设备成本和占地面积;再一方面,该装置通过隔板将沉降区分隔为仅底部连通的第一沉降区和第二沉降区,使得吸附反应器中吸附反应后的泥水混合物通过泥水出口流至第一沉降区进行沉降,沉降后的水和少量污泥通过隔板底部流向第二沉降区继续沉降,增加了泥水混合物的出水路径和沉降时间,使得污泥的沉降效果佳,进而有利于提高废水的预处理效率,且隔板与壳体、吸附反应器相连,还可以提高对吸附反应器的固定效果,保证设备的结构稳定性。由此,该装置不仅可以大幅降低废水中的有机物浓度,提高废水的可生化性和处理效率,还能实现废弃的剩余污泥的再利用,降低废水的处理成本,此外,该装置还具有结构简单、处理高效和易操作等的优点。
41.下面参考图1~2对本发明上述实施例的利用剩余污泥吸附预处理煤气化废水的装置进行详细描述。
42.根据本发明的实施例,所述泥水出口6和所述吸附反应器3顶部之间的距离与所述吸附反应器3高度的比值可以为(0.2~0.3):1,具体可以是0.2/1、0.22/1、0.25/1、0.3/1等;若泥水出口和所述吸附反应器顶部之间的距离与所述吸附反应器高度的比值过小,当泥水出口发生堵塞时,吸附反应器中的泥水混合物无法流出,会导致吸附反应器中的水位有明显的提升,尤其是连续进水进泥过程中,水位过高极有可能出现泥水混合物溢出壳体的问题,具有一定的安全隐患;若泥水出口和所述吸附反应器顶部之间的距离与所述吸附反应器高度的比值过大,吸附反应器内的空气过多,又会使过多的氧溶解到废水中,导致废水氧含量过高,影响剩余污泥的吸附效果;通过控制泥水出口和所述吸附反应器顶部之间的距离与所述吸附反应器高度的比值为(0.2~0.3):1,不仅可以保证泥水混合物流通时的安全性,即便吸附反应器堵塞,也能及时发现并预留出反应时间,还有利于提高剩余污泥的吸附效果,同时,还能使剩余污泥与废水具有合理的吸附反应时间,提高对难降解的有机物的吸附效果,并避免废水中可生化降解的有机物过度降解,保证吸附效果并改善废水的可生化性。
43.根据本发明的实施例,所述出水口13和所述壳体100顶壁之间的距离与所述沉降区高度的比值可以为(0.2~0.3):1,具体可以是0.2/1、0.22/1、0.25/1、0.3/1等,由此,更
有利于调节沉降区的液面在适宜高度范围,既能延长沉降路径和沉降时间,保证沉降效果,还有利于沉降区中的废水通过出水口顺利流出,有效防止废水回流至吸附反应器内影响废水的处理效率及效果。
44.根据本发明的实施例,所述出水口13位置可以低于所述泥水出口6,由此不仅更有利于吸附反应器泥水混合物和设备最终出水的顺利流出,还能进一步调节沉降区的液面高度,有效防止废水从泥水出口倒流入吸附反应器中。
45.根据本发明的实施例,所述吸附反应器3的高度可以不大于所述吸附沉降区4的高度,若所述吸附反应器的高度大于所述吸附沉降区的高度,吸附反应器会伸入到污泥浓缩区内,导致第一沉降区与第二沉降区之间的连通处过窄,吸附反应器内的泥水混合物流至第一沉降区进行沉降后会在污泥浓缩区产生大量的剩余污泥,使得第一沉降区与第二沉降区之间的连通易发生堵塞,沉降后的水难以通过连通处流向第二沉降区中,不仅影响废水的处理效率,还可能导致第一沉降区内液面高于泥水出口,从而出现沉降后的水倒流至吸附反应器中以及进而导致的吸附反应器内液面升高等问题;而通过控制吸附反应器的高度不大于吸附沉降区的高度,可以使得沉降后的水和少量的污泥更好地通过第一沉降区与第二沉降区之间的连通处流向第二沉降区中,既能保证沉积效果,并有效提高废水的处理效率,还有利于避免吸附反应器内液面溢出。
46.根据本发明的实施例,所述吸附区与所述沉降区的体积比可以为1:(4~6),具体可以为1/4、1/5、1/6等,若吸附区与沉降区的体积比过大,说明沉降区的体积过小,会导致泥水混合物的出水路径缩短,沉降时间减少,从而影响泥水混合物的沉降效果;若吸附区与沉降区的体积比过小,说明沉降区过大,容易造成投资浪费,通过控制吸附区与沉降区的体积比为1:(4~6),可以在节省设备投资的前提下保证剩余污泥的吸附效率的前提下有效实现泥水混合物的分离,使得污泥的沉降效果佳。
47.根据本发明的实施例,所述进水进泥口7可以与煤气化废水供给装置、生化池好氧段剩余污泥出口相连,所述排水口10可以与后续废水生化工艺相连,由此,可实现废水预处理和废水生化工艺的连续化处理,达到节能降耗和提高废水处理效率的目的。
48.根据本发明的实施例,沉降区出水堰外堰壁的顶部可以高于出水口13,由此,不仅能避免出水堰内废水溢出,还能调节沉降区的液位高度。
49.根据本发明的实施例,所述隔板12的底部可以不高于所述吸附反应器3的底部,由于吸附反应器中的泥水混合物先流至第一沉降区进行沉降,沉降后的水和少量污泥通过隔板底部流向第二沉降区继续沉降,若隔板的底部高于所述吸附反应器的底部,会导致泥水混合物的出水路径缩短,沉降时间减少,从而影响泥水混合物的沉降效果,而通过控制隔板的底部不高于吸附反应器的底部,可以进一步增加泥水混合物的出水路径和沉降时间,使得污泥的沉降效果更佳,进而使得废水的处理效率更好。
50.根据本发明的实施例,参照图1,所述吸附反应器3的下部可以设有取样口8,所述取样口8位置可以高于所述进水进泥口7,参照图2,取样口8在水平方向上的投影可以与进水进泥口重合或位于进水进泥口的投影区域内,通过在取样口取样并进行检测可以更好的控制剩余污泥和煤气化废水的固液比,提高对废水进行处理的效率及效果,其中,从该取样口取得的样品更贴合剩余污泥和煤气化废水的实际情况,更有利于调控剩余污泥和煤气化废水的固液比并预测最佳的吸附时间及吸附效果,提高对废水的预处理效果,可靠性更佳。
51.根据本发明的实施例,参照图1,利用剩余污泥吸附预处理煤气化废水的装置还可以包括:搅拌电机1,所述搅拌电机1可以设在所述壳体100顶部且与所述搅拌装置2相连,由此,可以实现自动化搅拌操作,更有利于实际生产应用。可以理解的是,所述搅拌装置的类型不受特别限制,本领域技术人员可以根据实际需要灵活选择,例如可以是桨式搅拌器、涡轮式搅拌器、螺带式搅拌器等。
52.根据本发明的实施例,所述隔板12可以与所述壳体100的顶壁和/或所述壳体100的侧壁固定相连,且参照图2,隔板12可以将沉降区分隔为对称布置的第一沉降区41和第二沉降区42,由此,隔板可以更好地与壳体固定在一起,不仅能防止隔板发生掉落影响废水的处理效果,还能进一步保证隔板对吸附反应器的固定效果,提高整个设备的结构稳定性。可以理解的,固定相连的类型不受特别限制,本领域技术人员可以根据实际需要灵活选择,只要能实现固定连接即可,例如可以是一体成型,也可以是可拆卸连接。
53.根据本发明的实施例,参照图2,所述出水堰9可以沿所述第二沉降区42壳体外周壁周向的至少一部分布置,例如可以沿第二沉降区壳体外周壁周向布置并以壳体作为出水堰的内堰壁,由此,出水堰与壳体可以更好地结合在一起,更有利于沉降区的水流入出水堰中。
54.在本发明的另一个方面,本发明提出了一种采用前面所述的装置实施利用剩余污泥吸附预处理煤气化废水的方法,根据本发明的实施例,该方法包括:
55.(1)将剩余污泥和煤气化废水供给至吸附反应器内,在搅拌条件下进行吸附反应
56.根据本发明的实施例,该步骤中,所述剩余污泥和所述煤气化废水在所述吸附反应器内的停留时间可以不大于2h,具体可以是1h、1.5h、2h等,其中,将剩余污泥与煤气化废水混合的目的是为了吸附废水中不易降解的有机物,若剩余污泥和所述煤气化废水在所述吸附反应器内的停留时间过长,剩余污泥的微生物会导致废水中易降解的有机物也发生过度降解,影响预处理废水后续进行生化净化的效果,而通过控制剩余污泥和煤气化废水在吸附反应器内的停留时间不大于2h,更有利于促进剩余污泥有效吸附废水中的难降解的有机物,使可生化降解的有机物保留在废水中,从而能够大幅降低废水的有机物浓度,提高废水的可生化性,使预处理废水后的生化处理工艺更加高效稳定地运行。
57.根据本发明的实施例,所述剩余污泥可以为生化池好氧段的剩余污泥,所述剩余污泥的单日供给量可以不大于生化池好氧段单日产生的剩余污泥;由此,可以利用生化池好氧段的剩余污泥实现对煤气化废水的连续化预处理,不需要增加新的吸附介质,更有利于提高剩余污泥的再利用效率,降低废水的处理成本。
58.根据本发明的实施例,供给至所述吸附反应器内的剩余污泥和煤气化废水与流出的泥水混合物可以保持动态平衡,由此,可以保证剩余污泥吸附效果的稳定性。根据本发明的一些示例,可以根据生化池好氧段每日生产的剩余污泥量来控制剩余污泥的使用量,优选地,根据生化池好氧段每日产生的剩余污泥量,所述剩余污泥和所述煤气化废水的固液比可以为0.5~1g/l,具体可以为0.5g/l、0.7g/l、0.9g/l、1g/l等,由此,有利于实现剩余污泥的有效利用并根据单日产生的剩余污泥量实现与煤气化废水较佳的配比,有效去除废水中的有机物。
59.根据本发明的实施例,所述吸附反应器内的温度可以为30~35℃,具体可以为30℃、31℃、32℃、33℃、34℃、35℃;由此,该温度更贴近于煤气化废水和剩余污泥的实际温
度,不仅无需采用多余的保温措施,还有利于提高剩余污泥的吸附效果,进而可以更有效地降低废水的有机物浓度,提高废水的可生化性,使后续废水生化处理工艺更加高效稳定地运行。另外,可以在200-300转/分(例如可以为200转/分、230转/分、250转/分、270转/分、300转/分等)的搅拌速率下进行所述吸附反应,若搅拌速率过慢,吸附反应器中的剩余污泥与废水不能完全混合,使得剩余污泥发生沉降,易于导致吸附反应器易发生堵塞,而通过控制搅拌速率为200-300转/分,可以使得剩余污泥与废水混合地更均匀,更有利于提高剩余污泥的吸附效果。
60.(2)吸附反应后的泥水混合物通过泥水出口流至第一沉降区进行沉降,沉降后的水和少量污泥通过隔板底部流向第二沉降区继续沉降
61.根据本发明的实施例,该步骤中,通过上述沉降方式可以增加泥水混合物的出水路径和沉降时间,使得污泥的沉降效果佳,进而有利于提高废水的处理效率及效果。
62.(3)通过沉降区出水堰回收所述第二沉降区沉降后的水,通过排泥口回收所述第一沉降区和所述第二沉降区沉降形成的浓缩污泥,实现泥水分离
63.根据本发明的实施例,所述污泥浓缩区内的浓缩污泥高度可以不高于所述污泥浓缩区高度的2/3,若污泥浓缩区内的浓缩污泥高度过高,一方面可能会影响第一沉降区和第二沉降区的流通效果和沉降区的沉降效果,更重要的是,会导致浓缩污泥在污泥浓缩区中停留时间过长,导致废水中容易降解的有机物发生过度降解,影响废水后续生化净化阶段中有机物的生物净化效果,通过控制污泥浓缩区内的浓缩污泥高度不高于所述污泥浓缩区高度的2/3,可及时对污泥浓缩区内的污泥进行排泥,优选每日排净污泥浓缩区内的污泥。更优选地,所述污泥浓缩区内的浓缩污泥高度可以不高于所述污泥浓缩区高度的不高于1/3,一旦污泥浓缩区内有机污泥的高度达到上述界限,可以及时排泥,保证沉降区的流通并避免废水中易生物降解的有机物过度降解,提高预处理废水的可生化性并提高后续对废水的生化净化效果。
64.根据本发明的实施例,可以在吸附反应器下部取样,并对取得的样品进行检测,根据检测结果控制所述剩余污泥和所述煤气化废水的固液比,提高对废水进行处理的效率及效果,其中,从该取样口取得的样品更贴合剩余污泥和煤气化废水的实际情况,更有利于调控剩余污泥和煤气化废水的固液比并预测最佳的吸附时间及吸附效果,提高对废水的预处理效果,可靠性更佳。根据本发明的一些示例,可以对取得的样品进行cod
cr
、bod5等检测,以进一步优化剩余污泥和煤气化废水的固液比,改善废水的可生化性。
65.综上,根据本发明前面所述的实施利用剩余污泥吸附预处理煤气化废水的方法,该方法是利用废水生化净化系统中废弃的剩余污泥吸附煤气化废水中的有机物,未增加新的吸附介质,其中剩余污泥中含有的氨基、羧基、羟基及疏水基团等官能团,为煤气化废水中难降解有机污染物提供大量的吸附位点,通过分子力、静电力、离子交换、络合、螯合、微沉淀等物理、化学过程吸附去除废水中的有机物,从而既能大幅降低废水的有机物浓度,又能提高废水的可生化性,使预处理废水后续的生化处理工艺高效稳定地运行,同时可以有效实现剩余污泥的再利用,降低废水的处理成本;另一方面,该方法将吸附区、沉降区和污泥浓缩区有效地融合在该装置中,设备整体结构简单,操作方便,便于使用,避免了多个设备串联的冗杂结构,降低了废水处理的原料成本、设备成本和占地面积;再一方面,该方法通过隔板将沉降区分隔为仅底部连通的第一沉降区和第二沉降区,使得吸附反应器中吸附
反应后的泥水混合物通过泥水出口流至第一沉降区进行沉降,沉降后的水和少量污泥通过隔板底部流向第二沉降区继续沉降,增加了泥水混合物的出水路径和沉降时间,使得污泥的沉降效果佳,进而有利于提高废水的预处理效率,且隔板与壳体、吸附反应器相连,还可以提高对吸附反应器的固定效果,保证设备的结构稳定性。由此,该方法操作简单、方便,可重复,易于实现和规模化生产,不仅可以大幅降低废水中的有机物浓度,提高废水的可生化性和处理效率,还能实现废弃的剩余污泥的再利用,降低废水的处理成本。具体地,与未进行预处理的煤气化废水相比,采用该方法获得的预处理废水的cod含量可降低20%-40%,废水的可生化指标可提高20%左右。需要说明的是,针对上述利用剩余污泥吸附预处理煤气化废水的装置所描述的特征及效果同样适用于方法,此处不再一一赘述。
66.在本发明的又一个方面,本发明提出了一种前面所述的装置和前面所述的方法在煤气化废水处理和/或剩余污泥处理中的用途。与现有技术相比,该装置不仅可以应用于煤气化废水处理中,还可以应用于剩余污泥处理中,应用范围广,实用性强。需要说明的是,针对上述利用剩余污泥吸附预处理煤气化废水的装置和采用上述装置实施利用剩余污泥吸附预处理煤气化废水的方法所描述的特征及效果同样适用于该用途,此处不再一一赘述。
67.下面参考具体实施例,对本发明进行描述,需要说明的是,这些实施例仅仅是描述性的,而不以任何方式限制本发明。
68.实施例1
69.该装置由有机玻璃制成,吸附反应器的有效容积为105ml,沉降区的有效容积为470ml。将生化池好氧段的剩余污泥和煤气化废水通过进水进泥口流至吸附反应器内,使剩余污泥和煤气化废水的固液比为0.5-1g/l,打开搅拌装置,污泥吸附区机械搅拌,在200-300转/分的搅拌速率下进行所述吸附反应;保持吸附反应器内的温度为30-35℃,剩余污泥和煤气化废水在吸附反应器内的停留时间为2h;吸附反应后的泥水混合物通过泥水出口流至第一沉降区进行沉降,沉降后的水和少量污泥通过隔板底部流向第二沉降区继续沉降,通过沉降区出水堰回收第二沉降区沉降后的水,完成剩余污泥吸附预处理煤气化废水过程。
70.图4为实施例1中煤气化废水进水和沉降区出水堰出水的cod含量的对比示意图。图5为实施例1中煤气化废水和沉降区出水堰出水的生化性指标(bod5/cod)的对比示意图。由图4可知,煤气化废水中的cod含量为3250
±
250mg/l,沉降区出水堰出水的cod含量为2000
±
250mg/l,可见,煤气化废水吸附预处理后,cod含量降低了30%-40%;由图5可知,煤气化废水中的生化性指标为0.36,沉降区出水堰出水的生化性指标为0.43,可见,煤气化废水吸附预处理后,可生化性指标提高了20%左右,由此,该装置利用废水生化净化系统中的剩余污泥可以有效吸附煤气化废水中的有机物,进而降低废水的有机物浓度,提高废水的可生化性。
71.在本发明的描述中,需要理解的是,术语“纵向”、“轴向”、“上”、“下”、“顶”、“底”、“内”、“外”、“顺时针”、“径向”、“周向”等指示的方位或位置关系为基于附图所示的方位或位置关系,仅是为了便于描述本发明和简化描述,而不是指示或暗示所指的装置或元件必须具有特定的方位、以特定的方位构造和操作,因此不能理解为对本发明的限制。
72.此外,术语“第一”、“第二”仅用于描述目的,而不能理解为指示或暗示相对重要性或者隐含指明所指示的技术特征的数量。由此,限定有“第一”、“第二”的特征可以明示或者
隐含地包括至少一个该特征。在本发明的描述中,“多个”的含义是至少两个,例如两个,三个等,除非另有明确具体的限定。
73.在本说明书的描述中,参考术语“一个实施例”、“一些实施例”、“示例”、“具体示例”、或“一些示例”等的描述意指结合该实施例或示例描述的具体特征、结构、材料或者特点包含于本发明的至少一个实施例或示例中。在本说明书中,对上述术语的示意性表述不必须针对的是相同的实施例或示例。而且,描述的具体特征、结构、材料或者特点可以在任一个或多个实施例或示例中以合适的方式结合。此外,在不相互矛盾的情况下,本领域的技术人员可以将本说明书中描述的不同实施例或示例以及不同实施例或示例的特征进行结合和组合。
74.尽管上面已经示出和描述了本发明的实施例,可以理解的是,上述实施例是示例性的,不能理解为对本发明的限制,本领域的普通技术人员在本发明的范围内可以对上述实施例进行变化、修改、替换和变型。