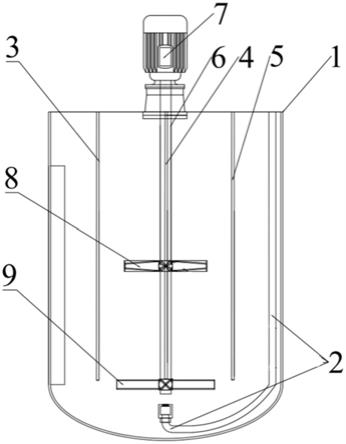
1.本实用新型涉及锂电池材料领域,具体涉及一种高镍正极前驱体材料的制备装置。
背景技术:2.随着锂离子电池向无钴、高镍方向发展,采用价格较为低廉的锰和镍取代资源缺乏和价格较高的钴,在降低成本的同时,更好的满足电子产品日益小型化和多功能化的要求。高镍前驱体材料是正极材料的关键,很大程度上决定了正极材料的结构及性能,大颗粒高镍前驱体材料在共沉淀法制备过程中,受工艺及材料特性影响,局部过饱和度偏高或者偏低,在反应中后期材料内部的残余应力、应变增大以及颗粒碰撞等原因,容易出现裂纹甚至开裂问题。一般通过缩短反应时间可以改善材料的开裂现象,公布号为cn 110611097 a的专利,采用有机絮凝剂添加的方式,通过形成絮凝形成的网状保护结构,在颗粒之间形成保护网,金属离子可顺利通过保护网,而颗粒与颗粒之间的碰撞由之前的刚性碰撞转变为柔性碰撞,从而杜绝颗粒开裂现象。
3.缩短反应时间虽然可以改善材料的开裂现象,但是反应时间短,材料的球形度及振实密度较低,进而影响正极材料的性能,且前驱体材料的生产效率降低。采用有机絮凝剂添加的方式,通过形成絮凝形成的网状保护结构,杜绝颗粒开裂现象,但是有机絮凝剂添加会加大洗涤及后处理成本,并且容易造成杂质引进及碳含量增大等问题,影响材料性能。
技术实现要素:4.针对上述已有技术存在的不足,本实用新型提供一种高镍正极前驱体材料的制备装置。
5.本实用新型是通过以下技术方案实现的。
6.一种高镍正极前驱体材料的制备装置,其特征在于,所述装置包括:反应釜、搅拌装置、进气管、第一进料管、第二进料管、第三进料管;所述搅拌装置包括搅拌轴、搅拌桨,所述搅拌轴的下端从反应釜的上端伸入釜内,所述搅拌轴的上端连接有电机;所述搅拌桨包括套装在搅拌轴上的上层桨叶和下层桨叶,所述上层桨叶包括折叶式叶片以及套装在折叶式叶片外部的圆环,所述下层浆叶为折叶式叶片或者圆盘式叶片;所述进气管从反应釜的上端伸入釜底,并且所述进气管的出气端对准下层浆叶;所述第一进料管、第二进料管、第三进料管均从反应釜的上端伸入釜内,所述第一进料管、第二进料管、第三进料管均匀分布在以搅拌桨为中心的圆周上,并且,所述第一进料管、第二进料管、第三进料管的下端与下层浆叶平齐。
7.进一步地,所述进气管包括管体、喷嘴,所述管体包括竖直管段和弧形管段,所述竖直管段的下端与弧形管段的一端连接,所述弧形管段的另一端与喷嘴连接,所述喷嘴上设有多个圆形喷孔。
8.进一步地,所述喷孔的直径小于等于0.5mm。
9.进一步地,所述第一进料管、第二进料管、第三进料管的下端与下层浆叶的水平距离均为50
‑
150mm。
10.进一步地,所述折叶式叶片的边角圆滑。
11.一种采用上述装置制备高镍正极前驱体材料的方法,其特征在于,所述方法包括:
12.(1)配制混合硫酸盐溶液,所述混合硫酸盐溶液中ni、co、mn离子摩尔比为x:y:(100
‑
x
‑
y),其中80≤x≤98,0≤y≤10,且总金属离子浓度为1
‑
3mol/l;
13.(2)向含有底液的反应釜中通过进气管通入氮气作为保护气,氮气通过进气管的喷嘴喷出后形成直径小于等于1mm的气泡;
14.(3)将经步骤(1)得到的混合硫酸盐溶液、液碱(作为沉淀剂)和氨水(作为络合剂)分别通过第一进料管、第二进料管、第三进料管加入到反应釜中,搅拌桨转速保持在100~300rpm下进行共沉淀反应;
15.(4)当共沉淀反应生成的前驱体颗粒生长到粒径d50为5
‑
10μm时,将混合硫酸盐溶液、液碱和氨水的流量增大,增大的幅度为当前流量的10~20%,此后每隔8小时按照当前流量的10~20%的幅度增大,持续进行到前驱体颗粒生长到目标粒径d50为10
‑
20μm,停止反应,经过陈化后得到球形前驱体,并进行离心、洗涤、干燥、除磁性异物处理后,得到高镍正极前驱体材料成品。
16.进一步地,所述底液包括液碱和氨水,所述底液的ph为10
‑
12,氨水浓度6
‑
24g/l,温度为40~60℃。
17.进一步地,所述液碱浓度为8
‑
12mol/l(工业液碱),所述氨水浓度为0.5
‑
2mol/l。
18.进一步地,所述步骤(2)中氮气的流量为0.1
‑
5m3/h。
19.进一步地,所述步骤(3)混合硫酸盐溶液流量为200
‑
400l/h,液碱流量为40
‑
100l/h,氨水流量为10
‑
40l/h。
20.本实用新型的有益技术效果,本实用新型通过优选的搅拌桨及搅拌、反应工艺,改善了物料在反应釜内部的整体轴向循环,以及因搅拌转速降低后的局部饱和度过高和过低问题,并尽可能的保证前驱体颗粒的生长速率一致,加强反应均一性,降低大颗粒高镍前驱体材料内部的残余应力、应变;反应釜底部通过喷嘴通入的保护气,形成毫米级的气泡,在搅拌的作用下均匀的分布在反应釜内部,可以减少大颗粒前驱体相互之间的碰撞,进一步提高反应均一性,解决大颗粒开裂等问题。
附图说明
21.图1为本实用新型的结构示意图。
22.图2为本实用新型的搅拌桨的结构示意图。
23.图3为本实用新型的进气管的结构示意图。
24.图4前驱体颗粒与气体气泡碰撞示意图。
25.图5为对比例1制备的高镍正极前驱体材料表面形貌图。
26.图6实施例1制备的高镍正极前驱体材料表面形貌图。
27.图7实施例2制备的高镍正极前驱体材料表面形貌图。
具体实施方式
28.下面结合附图和具体实施方式对本实用新型进行详细说明。
29.如图1
‑
3所示,一种高镍正极前驱体材料的制备装置,包括:反应釜1、搅拌装置、进气管2、第一进料管3、第二进料管4、第三进料管5。
30.搅拌装置包括搅拌轴6、搅拌桨,搅拌轴6的下端从反应釜1的上端伸入釜内,搅拌轴6的上端连接有电机7;搅拌桨包括套装在搅拌轴6上的上层桨叶8和下层桨叶9,上层桨叶8包括折叶式叶片10以及焊接在折叶式叶片外部的圆环11,圆环的直径以及高度与折叶式叶片10适配,下层浆叶9为折叶式叶片或者圆盘式叶片;折叶式叶片的边角打磨圆滑。
31.进气管2从反应釜1的上端伸入釜底,并且进气管2的出气端对准下层浆叶9,具体地,进气管2包括管体12、喷嘴13,管体12包括竖直管段和弧形管段,竖直管段的下端与弧形管段的一端连接,弧形管段的另一端与喷嘴13连接,喷嘴上设有多个圆形喷孔,喷孔的直径小于等于0.5mm,喷嘴13对准下层浆叶9。
32.第一进料管3、第二进料管4、第三进料管5均为竖直管道,均从反应釜1的上端伸入釜内,第一进料管3、第二进料管4、第三进料管5均匀分布在以搅拌桨为中心的圆周上,并且,第一进料管3、第二进料管4、第三进料管5的下端与搅拌桨的下层浆叶9平齐,第一进料管3、第二进料管4、第三进料管5的下端与下层浆叶的水平距离均为50
‑
150mm。
33.对比例1:
34.步骤1、将含有一定镍离子以及钴离子、锰离子的硫酸盐原料,配制成ni:co:mn=96:2:2,且总金属离子浓度为2mol/l混合盐溶液a,采用浓度范围为8mol/l的工业液碱作为沉淀剂溶液b,采用浓度范围为1mol/l的氨水作为络合剂溶液c;
35.步骤2、在反应釜1中配置含有一定沉淀剂溶液和络合剂溶液的底液d,并在反应釜通入氮气作为保护气,底液d的ph在11.4
‑
11.6,氨水浓度6
‑
8g/l,温度在45~50℃;
36.步骤3将混合盐溶液a、沉淀剂溶液b和络合剂溶液c按照混合盐溶液200l/h,工业液碱50l/h,氨水流量15l/h,加入到反应釜下层桨叶水平位置100mm的正三角位置,搅拌桨转速保持在160~240rpm下进行共沉淀反应,所述的搅拌桨包含上层桨叶和下层桨叶,桨叶为折叶式式搅拌桨;
37.步骤4、反应物料超过反应釜溢流口后,开始浓密工艺,反应持续到前驱体颗粒生长到18μm,停止反应,经过陈化后得到球形前驱体,并进行离心、洗涤、干燥、除磁性异物等处理后,得到大颗粒高镍正极前驱体成品材料。
38.对比例1制备的高镍正极前驱体材料表面形貌如图5所示。
39.实施例1
40.步骤1、将含有一定镍离子以及钴离子、锰离子的硫酸盐原料,配制成ni:co:mn=96:2:2,且总金属离子浓度为2mol/l混合硫酸盐溶液a,采用浓度为8mol/l的工业液碱作为沉淀剂溶液b,采用浓度为1mol/l的氨水作为络合剂溶液c;
41.步骤2、在反应釜1中配置含有一定沉淀剂溶液(液碱)和络合剂溶液(氨水)的底液d,并在反应釜底部通过进气管2通入直径小于等于1mm的氮气作为保护气,氮气流量为1m3/h,底液d的ph在11.4,氨水浓度9g/l,温度在45℃;
42.步骤3将混合盐溶液a、沉淀剂溶液b和络合剂溶液c按照混合盐溶液流量200l/h,工业液碱流量50l/h,氨水流量15l/h,分别通过第一进料管3、第二进料管4、第三进料管5加
入到距反应釜下层桨叶9水平距离100mm的正三角位置(即均匀分布在以下层浆叶为中心的圆周上),搅拌桨转速保持在160rpm下进行共沉淀反应,
43.步骤4、反应物料超过反应釜溢流口后,开始浓密工艺,前驱体颗粒生长到9μm时,将混合盐溶液、工业液碱、氨水流量等比例增大15%至230l/h、57.5l/h、17.25l/h,此后每隔8小时,按照当前混合盐溶液、工业液碱和氨水流量等比例增大15%,一直持续进行到前驱体颗粒生长到18μm,停止反应,经过陈化后得到球形前驱体,并进行离心、洗涤、干燥、除磁性异物等处理后,得到无开裂的大颗粒高镍正极前驱体成品材料。
44.实施例1制备的高镍正极前驱体材料表面形貌如图6所示。
45.实施例2
46.步骤1、将含有一定镍离子以及钴离子、锰离子的硫酸盐原料,配制成ni:co:mn=90:5:5,且总金属离子浓度为3mol/l混合硫酸盐溶液a,采用浓度为12mol/l的工业液碱作为沉淀剂溶液b,采用浓度为0.5mol/l的氨水作为络合剂溶液c;
47.步骤2、在反应釜1中配置含有一定沉淀剂溶液和络合剂溶液的底液d,并在反应釜底部通入直径小于等于1mm的氮气作为保护气,氮气流量为2m3/h,底液d的ph在12,氨水浓度23g/l,温度在60℃;
48.步骤3将混合盐溶液a、沉淀剂溶液b和络合剂溶液c按照混合盐溶液流量300l/h,工业液碱流量75l/h,氨水流量22l/h,分别通过第一进料管3、第二进料管4、第三进料管5加入到距离反应釜下层桨叶水平位置50mm的正三角位置,搅拌桨转速保持在120rpm下进行共沉淀反应;
49.步骤4、反应物料超过反应釜溢流口后,开始浓密工艺,前驱体颗粒生长到8μm时,将混合盐溶液、工业液碱、氨水流量等比例增大20%至360l/h、90l/h、26.4l/h,此后每隔8小时,按照当前混合盐溶液、工业液碱和氨水流量等比例增大20%,一直持续进行到前驱体颗粒生长到16μm,停止反应,经过陈化后得到球形前驱体,并进行离心、洗涤、干燥、除磁性异物等处理后,得到无开裂的大颗粒高镍正极前驱体成品材料。
50.实施例2制备的高镍正极前驱体材料表面形貌如图7所示。
51.实施例3
52.步骤1、将含有一定镍离子以及钴离子、锰离子的硫酸盐原料,配制成ni:co:mn=85:10:5,且总金属离子浓度为1mol/l混合硫酸盐溶液a,采用浓度为10mol/l的工业液碱作为沉淀剂溶液b,采用浓度为2mol/l的氨水作为络合剂溶液c;
53.步骤2、在反应釜1中配置含有一定沉淀剂溶液和络合剂溶液的底液d,并在反应釜底部通入直径小于等于1mm的氮气作为保护气,氮气流量为0.5m3/h,底液d的ph在10,氨水浓度15g/l,温度在50℃;
54.步骤3将混合盐溶液a、沉淀剂溶液b和络合剂溶液c按照混合盐溶液流量400l/h,工业液碱流量100l/h,氨水流量40l/h,分别通过第一进料管3、第二进料管4、第三进料管5加入到距离反应釜下层桨叶水平位置150mm的正三角位置,搅拌桨转速保持在280rpm下进行共沉淀反应;
55.步骤4、反应物料超过反应釜溢流口后,开始浓密工艺,前驱体颗粒生长到6μm时,将混合盐溶液、工业液碱、氨水流量等比例增大10%至440l/h、110l/h、44l/h,此后每隔8小时,按照当前混合盐溶液、工业液碱和氨水流量等比例增大10%,一直持续进行到前驱体颗
粒生长到11μm,停止反应,经过陈化后得到球形前驱体,并进行离心、洗涤、干燥、除磁性异物等处理后,得到无开裂的大颗粒高镍正极前驱体成品材料。
56.实施例4
57.步骤1、将含有一定镍离子以及钴离子、锰离子的硫酸盐原料,配制成ni:mn=80:20,且总金属离子浓度为3mol/l混合硫酸盐溶液a,采用浓度为11mol/l的工业液碱作为沉淀剂溶液b,采用浓度为0.5mol/l的氨水作为络合剂溶液c;
58.步骤2、在反应釜1中配置含有一定沉淀剂溶液和络合剂溶液的底液d,并在反应釜底部通入直径小于等于1mm的氮气作为保护气,氮气流量为3m3/h,底液d的ph在10,氨水浓度7g/l,温度在40℃;
59.步骤3将混合盐溶液a、沉淀剂溶液b和络合剂溶液c按照混合盐溶液流量400l/h,工业液碱流量40l/h,氨水流量30l/h,分别通过第一进料管3、第二进料管4、第三进料管5加入到距离反应釜下层桨叶水平位置75mm的正三角位置,搅拌桨转速保持在200rpm下进行共沉淀反应;
60.步骤4、反应物料超过反应釜溢流口后,开始浓密工艺,前驱体颗粒生长到10μm时,将混合盐溶液、工业液碱、氨水流量等比例增大17%至468l/h、46.8l/h、35.1l/h,此后每隔8小时,按照当前混合盐溶液、工业液碱和氨水流量等比例增大17%,一直持续进行到前驱体颗粒生长到20μm,停止反应,经过陈化后得到球形前驱体,并进行离心、洗涤、干燥、除磁性异物等处理后,得到无开裂的大颗粒高镍正极前驱体成品材料。
61.以上所述的仅是本实用新型的较佳实施例,并不局限发明。应当指出对于本领域的普通技术人员来说,在本实用新型所提供的技术启示下,还可以做出其它等同改进,均可以实现本实用新型的目的,都应视为本实用新型的保护范围。