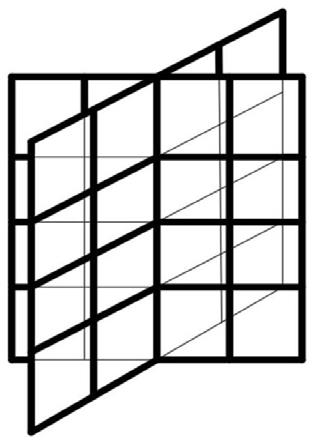
1.本发明属于化工分离技术领域,具体涉及一种填料塔用玄武岩格栅网布规整填料及制作 工艺。
背景技术:2.规整填料应用于填料塔,填料塔分离技术发展特征有四点:第一点,应用范围从一般化 工发展到炼油、石油化工、精细化工、医药及环保等行业;第二点,操作单元从蒸馏扩大到 吸收、萃取、洗涤、传热和生化处理等;第三点,装置趋向大型化及精细化;第四点,设计 及制作过程可用计算机设计和控制操作。
3.在工业上应用的规整填料绝大部分为波纹填料,波纹填料按结构可分为网波纹填料和板 波纹填料两大类,其材质又有金属、塑料和陶瓷等之分。上述各种材质存在耐腐蚀性能差、 分离效率低、耐温性差、制作成本高、使用周期短等一个或多个缺点,且容易造成资源浪费, 同时,也既会增加能耗,又会增加产品加工成本。
技术实现要素:4.有鉴于此,本发明的目的是提供一种料塔用玄武岩格栅网布规整填料及制作工艺,具有 耐腐蚀性能好、分离效率较高、耐温性好、制作成本较低、使用周期长等诸多性能,不会造 成资源浪费,节约能耗及降低产品加工成本。
5.一种玄武岩格栅网布规整填料,所述填料采用格栅网布基材拼插而成;所述格栅网布基 材采用玄武岩连续纤维粗丝编制而成;所述玄武岩连续纤维粗丝采用玄武岩连续纤维单丝合 并而成。
6.较佳的,所述格栅网布基材的一侧间隔加工有豁口,栅网布基材横纵交错的通过豁口拼 插在一起,形成填料块体。
7.较佳的,填料块体外围采用固定箍固定。
8.较佳的,玄武岩连续纤维粗丝丝径为0.10~0.50mm。
9.较佳的,填料块体高度50mm~300mm,每盘填料直径100mm~2000mm。
10.较佳的,固定箍为丝径9μm~24μm的玄武岩连续纤维布。
11.一种玄武岩格栅网布规整填料的制作工艺,包括:
12.步骤一、由玄武岩连续纤维单丝,合并成玄武岩连续纤维粗丝;
13.步骤二、将步骤一所得玄武岩连续纤维粗丝通过经编机加工成玄武岩格栅网布基材;
14.步骤三、将步骤二所得格栅网布基材裁剪成所需构造,并在基材的一侧等间隔加工豁口;
15.步骤四、将步骤三所得基材采用化学方法进行固化塑形处理;
16.步骤五、格栅网布基材横纵交错的通过豁口拼插在一起,形成填料块体。
17.较佳的,所述步骤四中,所述化学方法为:采用将间苯二胺与二氨基二苯基甲烷以
质量 比为45:55~65:35的比例混合,每100g标准树脂用15g~30g前述混合物,将剪裁后的玄武岩 格栅网布基材进行浸渍,浸渍完成后充分沥干,然后在35℃~50℃经5~7小时固化成型。
18.较佳的,所述步骤四中,所述化学方法为:将间苯二胺、二氨基二苯基甲烷、磷酸三苯 酯与苯酚以质量比为38:32:12:18~5:35:8:12的比例混合,每100g标准树脂用15g~32g前述混 合物,将剪裁后的玄武岩格栅网布基材进行浸渍,浸渍完成后充分沥干,然后在19℃~40℃ 经9~11小时固化成型。
19.较佳的,所述步骤四中,所述化学方法为:将间苯二胺、二氨基二苯基甲烷、甲苯二胺 以质量比为48:32:20~55:28:17的比例混合,每100g标准树脂用16g~35g前述混合物,将剪 裁后的玄武岩格栅网布基材进行浸渍,浸渍完成后充分沥干,然后在125℃~150℃经4~6小 时固化成型。
20.本发明具有如下有益效果:
21.本发明公开了一种填料塔用玄武岩格栅网布规整填料及工艺方法,该填料由玄武岩连续 纤维单丝,合并成玄武岩连续纤维粗丝;再由玄武岩连续纤维粗丝通过经编机加工成玄武岩 格栅网布基材,该基材采用经编定向结构,充分利用织物中纱线强力,改善其力学性能,使 其具有良好的抗拉强度,抗撕裂强度和耐蠕变性能;由于玄武岩格栅网布柔性较大、不易成 型,故格栅网布基材需通过剪切机裁剪成所需构造后,再使用间苯二胺与二氨基二苯基甲烷 混合物对其进行浸渍,浸渍完成后充分沥干,之后对其进行固化塑形,以增加其刚性以利于 后续拼插成型;将固化塑形后的基材,组装成规整填料块体。本发明有点在于:与现有金属 类规整填料相比,其耐腐蚀性能更好,造价更低;与现有陶瓷、玻璃、碳化硅类防腐规整填 料相比,其分离效率高,可使填料塔设备占用空间更小,更加节能;与现有聚乙烯、聚氯乙 烯、聚丙烯及尼龙等塑料类规整填料相比,其耐温性更好。以上优点可使该发明的应用范围 更加广泛。
附图说明
22.图1为本发明采用的经编玄武岩格栅网布示意图。
23.图2为本发明采用的经编玄武岩格栅网布剪裁示意图。
24.图3为本发明采用的经编玄武岩格栅网布拼插示意图。
25.图4为本实用新型玄武岩格栅网布规整填料示意图。图5为本实用新型玄武岩格栅网布的编织实物图。
26.其中,41-填料块拼插角度、42-填料固定箍。
具体实施方式
27.下面结合附图并举实施例,对本发明进行详细描述。
28.本发明的目的在于提供一种填料塔用玄武岩格栅网布规整填料及制作工艺,克服现有规 整填料的一些不足之处,该规整填料可用于强耐腐蚀性、温度高的场合。且与陶瓷填料相比, 在同样比表面积下,该新型玄武岩格栅网布规整填料的孔隙率更高、单位高度下的理论板数 更多,因此其分离效率比陶瓷填料更高;与金属丝网填料相比,其耐腐蚀性更好、造价更低; 与常用塑料类填料相比,其耐温可更高。综上所述,如果采用该新型玄武
岩格栅网布制作规 整填料可作为现有规整填料在分离领域的一个很好的补充。
29.其中,玄武岩连续纤维单丝是玄武岩石料在1450℃~1500℃熔融后,通过铂铑合金拉丝 漏板高速拉制而成的连续纤维。纯天然玄武岩纤维的颜色一般为褐色,有金属光泽,单丝直 径一般9μm~17μm,本发明采用玄武岩连续纤维粗丝经编成玄武岩格栅网布基材,经固化 后再拼插制作成整块填料,具体步骤为:
30.步骤一、由玄武岩连续纤维单丝,合并成玄武岩连续纤维粗丝;
31.步骤二、将步骤一所得玄武岩连续纤维粗丝通过经编机加工成玄武岩格栅网布基材,如 图1所示,该基材采用经编定向结构,织物中的经纬向纱线相互间无弯曲状态,如图5所示, 交叉点用高强纤维长丝捆绑结合起来,形成牢固的结合点,充分发挥其力学性能。
32.步骤三、将步骤二所得格栅网布基材需通过剪切机裁剪成所需构造;如图2所示,本发 明在基材的一侧等间隔开有豁口,便于后续拼插;
33.步骤四、将步骤三所得材料用间苯二胺与二氨基二苯基甲烷混合物进行浸渍,浸渍完成 后充分沥干,再对其进行固化塑形,以增加其刚性以利于后续拼插成型;
34.步骤五、如图3所示,格栅网布基材横纵交错的通过豁口拼插在一起,形成填料块体。 其中,根据所需填料直径加工出相应尺寸和数量的格栅网布基材,在预先制作好的固定模具 内进行拼插,组装成规整的填料块体,最后在填料块体外围采用固定箍固定。
35.其中,步骤一中的玄武岩连续纤维粗丝丝径为0.10~0.50mm。
36.步骤四中用间苯二胺与二氨基二苯基甲烷混合物进行浸渍,在浸渍过程中,除了可直接 用间苯二胺与二氨基二苯基甲烷混合物外,也可添加其他化合物,如磷酸三苯酯和苯酚混合 物、甲苯二胺等,但不局限于此两种,也可以包括其他类环氧树脂,以调解固化效果。
37.步骤五中所组装成规整填料块体,填料块拼插角度为0~180
°
,每盘填料高度50~300mm, 每盘填料直径100~2000mm,固定箍为丝径9μm~24μm的玄武岩连续纤维布。
38.实施例1:
39.选取丝径为0.10mm~0.50mm的玄武岩连续纤维粗丝,编织丝网目数为40目-80目,采 用经编定向结构将其编织成玄武岩格栅网布基材。将格栅网布基材通过剪切机裁剪成所需构 造,然后采用化学工艺进行固化,将固化成型后的基材进行拼插,最后组装成规整填料块体, 填料块拼插角度为30
°
(拼插角度0~180
°
可选),固定箍为丝径9μm的~24μm玄武岩连续 纤维布。
40.如图1所示,本实施例在横向排列的多个基材上插入多个纵向排列的基材,最后形成圆 柱状的填料块体,块体外围用固定箍固定。
41.实施例2:在实施例1中,采用化学工艺固化的方法为:将间苯二胺与二氨基二苯基甲 烷以质量比为45:55的比例混合,每100g标准树脂用15g前述混合物,将剪裁后的玄武岩格 栅网布基材进行浸渍,浸渍完成后充分沥干,然后在35℃~50℃经5~7小时固化成型。
42.实施例3:在实施例1中,采用化学工艺固化的方法为:将间苯二胺与二氨基二苯基甲 烷以质量比为55:45的比例混合,每100g标准树脂用23g前述混合物,将剪裁后的玄武岩格 栅网布基材进行浸渍,浸渍完成后充分沥干,然后在35℃~50℃经5~7小时固化成型。
43.实施例4:在实施例1中,采用化学工艺固化的方法为:将间苯二胺与二氨基二苯基甲 烷以质量比为65:35的比例混合,每100g标准树脂用30g前述混合物,将剪裁后的玄武岩
格 栅网布基材进行浸渍,浸渍完成后充分沥干,然后在35℃~50℃经5~7小时固化成型。
44.实施例5:
45.在实施例1中,采用化学工艺固化的方法为:将间苯二胺、二氨基二苯基甲烷、磷酸三 苯酯与苯酚以质量比为38:32:12:18的比例混合,每100g标准树脂用15g前述混合物,将剪 裁后的玄武岩格栅网布基材进行浸渍,浸渍完成后充分沥干,然后在19℃~40℃经9~11小时 固化成型。
46.实施例6:在实施例1中,采用化学工艺固化的方法为:将间苯二胺、二氨基二苯基甲 烷、磷酸三苯酯与苯酚以质量比为45:35:10:15的比例混合,每100g标准树脂用23g前述混 合物,将剪裁后的玄武岩格栅网布基材进行浸渍,浸渍完成后充分沥干,然后在19℃~40℃ 经9~11小时固化成型。
47.实施例7:在实施例1中,采用化学工艺固化的方法为:将间苯二胺、二氨基二苯基甲 烷、磷酸三苯酯与苯酚以质量比为45:35:8:12的比例混合,每100g标准树脂用32g前述混合 物,将剪裁后的玄武岩格栅网布基材进行浸渍,浸渍完成后充分沥干,然后在19℃~40℃经 9~11小时固化成型。
48.实施例8:
49.在实施例1中,采用化学工艺固化的方法为:将间苯二胺、二氨基二苯基甲烷、甲苯二 胺以质量比为48:32:20的比例混合,每100g标准树脂用16g前述混合物,将剪裁后的玄武岩 格栅网布基材进行浸渍,浸渍完成后充分沥干,然后在125℃~150℃经4~6小时固化成型。
50.实施例9:在实施例1中,采用化学工艺固化的方法为:将间苯二胺、二氨基二苯基甲 烷、甲苯二胺以质量比为14:8:5的比例混合,每100g标准树脂用26g前述混合物,将剪裁后 的玄武岩格栅网布基材进行浸渍,浸渍完成后充分沥干,然后在125℃~150℃经4~6小时固 化成型。
51.实施例10:在实施例1中,采用化学工艺固化的方法为:将间苯二胺、二氨基二苯基甲 烷、甲苯二胺以质量比为55:28:17的比例混合,每100g标准树脂用35g前述混合物,将剪裁 后的玄武岩格栅网布基材进行浸渍,浸渍完成后充分沥干,然后在125℃~150℃经4~6小时 固化成型。
52.综上所述,以上仅为本发明的较佳实施例而已,并非用于限定本发明的保护范围。凡在 本发明的精神和原则之内,所作的任何修改、等同替换、改进等,均应包含在本发明的保护 范围之内。