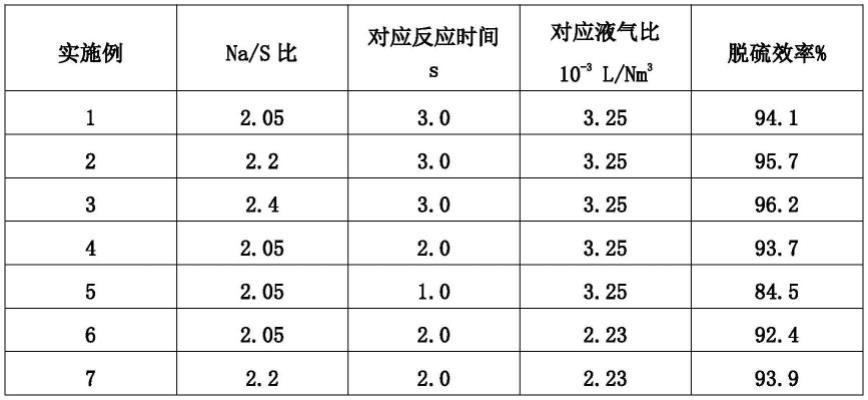
1.本实用新型涉及烟气处理技术领域,更具体地说它是一种基于超声波雾化的烟气脱酸系统。
背景技术:2.随着社会发展,大气污染问题带来的社会矛盾日益凸显,政府与时俱进,积极调整产业结构,推动绿色、循环、低碳发展,同时不断补充完善并修订相关环保法规,提升排放要求,加强环保监管力度,鼓励技术创新,着力改善大气污染问题。超低乃至超净排放已逐渐成为各行业大气污染物排放新一轮追求,在未来是大势所趋。
3.以常见脱硫工艺说明,按脱硫方式和产物状态,可分为湿法、干法、半干法三类。单从脱硫效率来看,干法脱硫一般稳定运行脱硫效率只能达到70%左右;半干法介于湿法和干法之间,一般稳定运行脱硫效率80%~85%(对于cfb半干法,脱硫效率达90%以上,最高达99.7%)。湿法脱硫一般稳定运行脱硫效率95%以上。因此为满足超低排放要求,常采用组合形式,如生活垃圾焚烧烟气净化脱酸工艺为“半干法+干法+湿法”三级脱酸,危废焚烧烟气净化脱酸工艺为“干法+两级湿法”脱酸。
4.针对部分行业待净化烟气或经初步净化后烟气中so2质量含量较低(对应折算质量浓度为50~500mg/nm3),但仍需进一步降低排放酸性气体浓度的情形,若采用干法或半干法脱酸技术,受脱酸效率制约,需要喷入更多的吸收剂物料,同时需配置更大的除尘装置,整体经济性较差;若采用湿法脱酸技术,造成烟气温降大,为避免冒白烟以及后端可能存在scr脱硝烟气温度要求,通常需配置换热设备等,同时产生大量脱酸废水需要处理,整体系统投资大、能耗高;因此针对低含量so2烟气的进一步脱酸需要寻求一种新型脱酸技术。
5.因此,有必要开发一种适用于低质量浓度酸性气体(so2、hcl、hf)脱除的高效低耗脱酸系统。
技术实现要素:6.本实用新型的目的是为了提供一种基于超声波雾化的烟气脱酸系统,为一种适用于低质量浓度酸性气体(so2、hcl、hf)脱除的高效低耗脱酸系统,脱酸效率高,投资成本低,且反应产物为干态,处理方便,满足质量含量较低的so2烟气的进一步脱酸需要;克服了烟气超低排放实施过程中针对低质量浓度酸性气体(so2、hcl、hf)烟气采用传统干法、半干法、湿法脱酸各自所存在的弊端。
7.为了实现上述目的,本实用新型的技术方案为:一种基于超声波雾化的烟气脱酸系统,其特征在于:包括碱液制备和供应系统、超声波雾化系统、脱酸反应器、除尘系统;
8.脱酸反应器、除尘系统、引风机依次连接;超声波雾化脱酸反应产生的副产物,由于粒径很小,质量较轻,在由下而上烟气夹带作用下,绝大部分随烟气排出,后经袋式除尘器脱除后排出;少部分在塔内烟气作用下形成悬浮态,可进一步增加干燥未反应的naoh与
酸性气体反应机会,提升脱酸效率,充分反应后的副产物落入脱酸反应器的底部灰斗后排出;
9.脱酸反应器内沿着烟气流向依次设置单气旋耦合器、气雾投加区管道;
10.碱液制备和供应系统、超声波雾化系统、气雾投加区管道依次连接;碱液在超声波雾化模块产生的高频振动形成的空化作用下形成粒径小于5~10um的naoh气雾,后进入脱酸反应器内naoh气雾投加区管道,与烟气混合完成脱酸反应;
11.气雾投加区管道为树形结构;保证气雾投加均匀性,提升超声波雾化的吸收剂气雾与烟气充分接触混合反应,实现深层脱酸目的,
12.在上述技术方案中,气雾投加区管道有多个;防止单个吸收塔气雾投加区管道截面局部漏烟导致脱硫不达标,实现整体深层脱酸目的;气雾投加区管道上设置多个喷嘴。
13.在上述技术方案中,气雾投加区管道按坡度0.005~0.01进行安装,避免主管和支管内集液。
14.在上述技术方案中,气雾投加区管道包括主管、支管和气雾出口;
15.主管沿脱酸反应器内截面中线设置;
16.支管根据脱酸反应器内截面布置,支管有多个,多个支管的长度不等;
17.多个气雾出口分别设置在主管和支管上。
18.在上述技术方案中,支管与主管采用切向过渡方式连接;
19.气雾出口与烟气流向一致,便于气雾输出;
20.在上述技术方案中,支管上设置多个分支管;分支管与支管采用切向过渡方式连接;
21.分支管上设置气雾出口;
22.多个分支管呈交错布置。
23.在上述技术方案中,超声波雾化系统包括雾化箱、雾化模块以及与雾化模块对应的控制系统;由超声波雾化器产生的吸收剂气雾,在塔内负压以及雾化箱自带鼓风机作用下由气雾投加区管道的气雾出口冒出,与烟气混合完成脱酸反应;
24.雾化模块位于雾化箱内;
25.雾化模块有多块;
26.多块雾化模块分别与控制系统连接;根据单个雾化模块的雾化量及雾化系统雾化出力设计要求,雾化箱底部集成布置大量雾化模块,通过对应的控制系统控制雾化模块启停个数进而调节雾化器总雾化量,达到雾化器出力可随烟气酸性气体浓度波动而快速调节的效果。本实用新型通过一定的控制逻辑实现雾化模块的分区、分块控制。
27.在上述技术方案中,溢流管设置在雾化箱侧面一定高度;根据雾化碱液浓度不同适当控制雾化箱内碱液淹没雾化模块高度;
28.溢流管与溢流槽连接;溢流槽与碱液制备和供应系统连接;当雾化箱内碱液供给量过大,超过最佳淹没高度时,雾化箱内碱液经溢流管流至溢流槽,溢流槽内碱液汇集一定量时返回至碱液稀释罐内;
29.碱液电伴热装置安装在雾化箱上;根据雾化碱液浓度不同适当控制雾化箱内碱液温度,确保雾化模块的雾化效果、雾化量处于最佳工作状态。
30.在上述技术方案中,脱酸反应器至少选自烟道、脱酸反应塔,脱酸反应器可根据项
目安装/改造空间情况,选用烟道替代,或者选用脱酸反应塔,对于改造空间受限项目具有良好的兼容性,可在原脱酸工艺基础上进行升级扩容以达到新的脱硫预期,避免重复投资,节省成本;
31.超声波雾化的吸收剂气雾出口方向与烟气流向一致,吸收剂气雾依靠吸收塔内/烟道内的负压以及雾化器自带鼓风机产生的微正压作用下喷入;
32.当脱酸反应器选用脱酸反应塔时,该塔为空塔结构,脱酸反应器包括单气旋耦合器、气雾投加区管道、烟气进口、烟气出口和锥形灰斗结构;
33.烟气进口、单气旋耦合器、气雾投加区管道、烟气出口由下至上依次设置;
34.锥形灰斗结构位于烟气进口下方;
35.气雾投加区管道包括第一气雾投加区管道、第二气雾投加区管道;第一气雾投加区管道与第二气雾投加区管道呈间隔设置,第一气雾投加区管道位于第二气雾投加区管道的烟气上游;
36.初步处理后含低质量浓度酸性气体的烟气,由塔下方烟气进口进入,向上经多气旋耦合器(含多个单元体)作用,形成多股旋转气流,加强了塔内烟气的均布和湍流,便于烟气与碱液超声波雾化气雾充分混合,有效提升脱酸效率,降低吸收剂物耗。
37.在上述技术方案中,碱液制备和供应系统包括碱液储存箱、碱液稀释泵、碱液稀释罐、碱液输送泵;
38.碱液储存箱、碱液稀释泵、碱液稀释罐、碱液输送泵依次连接;
39.溢流槽、工艺水系统分别与碱液稀释罐液体入口端连接;
40.碱液稀释罐的液体出口端通过碱液输送泵与送液管连通;送液管位于雾化箱内,一端位于雾化箱侧面、另一端伸至雾化箱底部;
41.碱液稀释罐内设置搅拌器;
42.外购袋装naoh经水解制备成高浓度naoh溶液储存至碱液储存箱内,并经碱液稀释泵泵入碱液稀释罐,添加工艺水,在碱液稀释罐搅拌器作用下稀释至质量浓度为10%~30%的naoh溶液,后经碱液输送泵泵入超声波雾化系统,为便于精准调控碱液供给量,减少超声波雾化器溢流量过大造成能耗浪费,碱液输送泵选用计量泵。
43.锥形灰斗结构和除尘系统下方均设置旋转卸灰阀。
44.本实用新型所述的基于超声波雾化的烟气脱酸系统的烟气脱酸方法,包括如下步骤,
45.步骤一:外购袋装naoh经碱液制备和供应系统水解、稀释制备成质量浓度为10%~30%的naoh溶液,由碱液制备和供应系统的碱液输送泵泵入超声波雾化系统的雾化箱中;
46.步骤二:步骤一中的naoh溶液在超声波雾化系统的雾化模块作用下产生naoh气雾,通过气雾投加管路送入脱酸反应器;
47.为保证气雾投加均匀性,提升吸收剂气雾与烟气酸性气体接触机会,实现深层脱酸目的,气雾投加区管道设计为树形结构,同时在塔内布置两层或其他数量的气雾投加区管道;
48.步骤三:来自初步处理后含低质量浓度酸性气体的烟气进入脱酸反应器,由下向上运动,首先在单气旋耦合器作用下均布形成多束单气旋气流,然后与气雾投加区管道鼓
出的naoh气雾充分接触并反应脱酸,形成脱酸烟气;
49.步骤四:步骤三产生的脱酸烟气排至除尘系统(如,袋式除尘器)中进一步除尘净化;脱酸反应产生的绝大部分脱酸副产物na2so3、nacl、naf等随烟气一起经袋式除尘器过滤后由底部灰斗排出;极少量部分脱酸副产物落入吸收塔底部锥形灰斗排出;
50.经除尘系统(如,袋式除尘器)净化后的烟气在引风机作用下通往烟囱排出。
51.本实用新型所述的基于超声波雾化的烟气脱酸系统,利用超声波空化作用改变了传统吸收剂雾化方式,针对低质量浓度酸性气体(so2、hcl、hf)脱除,实现高效低耗效果。本实用新型中的超声波雾化利用超声波高频振荡吸收剂溶液,在正负压交替作用下产生空化、撕裂、爆破等现象最终将溶液雾化成粒径在5~10um左右的气雾;气雾粒径小比表面积大,有利于烟气中酸性气体与吸收剂气雾的脱酸反应。
52.本实用新型中的超声雾化原理是:运用电子高频振荡原理,在超声波发生器上通上高频率的振荡电流,产生高频电能信号,通过换能器将其转换为超声机械振动(即超声波),超声波通过雾化介质传播,在气液界面处形成表面张力波,由于超声空化作用而使液体分子作用力破坏,从液体表面脱出形成雾滴,从而实现液体的雾化。
53.本实用新型具有以下优势:
54.(1)采用超声波雾化吸收剂溶液,产生的气雾粒径可低至5~10um左右,吸收剂粒径比表面积更大,结合底部旋流耦合器对流场的均布作用以及气雾投加区管道结构设计,进一步增强与烟气中低质量浓度酸性气体接触机会,保证高效脱硫,满足质量含量较低的so2烟气的进一步脱酸需要;同时缩短了反应时间,可进一步缩小反应所需空间,有效降低投资成本;
55.(2)采用湿法naoh脱酸,液气比较高(数量级为l/nm3),而采用超声波雾化脱酸工艺,液气比可低至10-3
l/nm3数量级,因此吸收剂利用率高,投加量少,配置碱液输送泵功耗减小,降低整体运行费用。
56.(3)超声波雾化脱酸反应产物为干态,无废水排放,脱酸副产物处置方便,降低系统脱酸废水处理成本;
57.(4)超净排放是大势所趋,由于超声雾化脱酸系统占地面积小,对于改造空间受限项目具有良好的兼容性,可在原脱酸工艺基础上进行升级扩容以达到新的脱硫预期,避免重复投资。
附图说明
58.图1为本实用新型基于超声波雾化的烟气脱酸系统的结构示意图。
59.图2为图1的a处放大图。
60.图3为本实用新型中的气雾投加区管道平面结构示意图。
61.图4为本实用新型中的气雾投加区管道立体结构示意图。
62.图1中,g表示工艺水系统;j1表示碱液储存箱;j2表示碱液稀释泵;j3表示碱液稀释罐;j4表示碱液输送泵;c1表示旋转卸灰阀;y表示待处理的初步处理后含低质量浓度酸性气体的烟气;q表示净烟气去烟囱的流向。
63.图1中的箭头表示烟气流向。
64.图2中,b表示雾化箱内的送液管。
65.图中1-碱液制备和供应系统,2-超声波雾化系统,2.1-雾化箱,2.11-溢流管,2.2-雾化模块,2.3-控制系统,2a-溢流槽,2b-碱液电伴热装置,3-脱酸反应器,3.1-单气旋耦合器,3.2-气雾投加区管道,3.2a-第一气雾投加区管道,3.2b-第二气雾投加区管道,3.21-主管,3.22-支管,3.221-分支管,3.23-气雾出口,3.3-烟气进口,3.4-烟气出口,3.5-锥形灰斗结构,4-除尘系统,5-引风机。
具体实施方式
66.下面结合附图详细说明本实用新型的实施情况,但它们并不构成对本实用新型的限定,仅作举例而已。同时通过说明使本实用新型的优点更加清楚和容易理解。
67.现以本实用新型试用于某行业中经初步净化后so2质量浓度较低烟气的脱酸对本实用新型进行详细说明,对本实用新型应用于其他so2质量浓度较低烟气的脱酸同样具有指导作用。
68.实施例:
69.某行业中经初步净化后so2质量浓度较低烟气。
70.某行业中经初步净化后so2质量浓度较低烟气的脱酸采用本实用新型所述基于超声波雾化脱酸系统,包括naoh溶液雾化系统、气雾投加、so2脱除等。
71.采用本实用新型对某行业中经初步净化后so2质量浓度较低烟气的脱酸方法,具体为:
72.将质量分数10%的naoh溶液输送到超声波雾化器中,雾化模块的振荡频率设置为1.7mhz,产生气雾粒径为5~10um,雾化后的naoh气雾利用超声波雾化器配置的鼓风机送入吸收塔内气雾投加区管道参与脱酸反应。其中气雾投加区管道设计为树形结构,在主管和支管上布置多个出雾口,且保证出雾口沿吸收塔截面均匀布置;从下至上设置2层气雾投加区管道。
73.气雾投加区管道1对应雾化器雾化量与烟气中so2含量的n(naoh):n(so2)约为(1~1.5):1;气雾投加区管道2对应雾化器雾化量与烟气中so2含量的n(naoh):n(so2)约为1:1;整体气雾投加区管道可调na/s满足(2~2.5):1。
74.烟气中so2与naoh气雾反应产生的副产物,绝大部分随烟气进入袋式除尘器进行脱除,少量落入吸收塔底部灰斗。
75.各实施例中各变量取值及相应的试验结果如下表1所示:
76.表1各实施例中各变量取值及相应的试验结果
[0077][0078]
从表1可以看出:本实用新型一种基于超声波雾化的烟气脱酸系统,随na/s、反应时间、液气比的升高脱酸能力逐步增强,最高脱酸效率>96%;系统设计时,na/s取值2.05~2.2、反应时间取值2s左右,可实现脱酸效率>90%的效果。
[0079]
鉴于本实用新型的反应时间短,所需反应空间就相应缩小,无论借用烟道或者专门设计吸收塔作为脱酸反应器,均可降低投资成本,且满足质量含量较低的so2烟气的进一步脱酸需要;另外鉴于较低的液气比(10-3
l/nm3量级),可降低碱液输送泵功率配置,进一步减少运行费用,因此本实用新型具有良好的经济效益。
[0080]
实施例1:以某500t/d处理量生活垃圾烟气治理项目为例,烟气量约为13万nm3/h,净化系统采用“半干法+干法+湿法”脱酸系统,其中半干法+干法脱酸效率高,可达到90%以上的脱酸效率(初步脱酸后,so2浓度约为80mg/nm3,hcl+hf浓度约为100mg/nm3),但要实现酸性气体的超低排放(so2浓度降至35mg/nm3以下,hcl+hf浓度降到10mg/nm3以下),需要配合使用湿法脱酸技术。结合本实用新型,在sda塔后添加超声波雾化脱酸系统,替代原湿法塔脱酸系统,相关经济性对比如下表2所示:
[0081]
表2经济性对比
[0082][0083][0084]
由上表2可知:对于同等脱酸要求,相较于现有的湿法脱酸系统,虽然本实用新型所述超声波雾化脱酸系统的声波雾化设备多投资约80万元,但配套的反应器结构更简单,碱液输送设备(泵+箱罐等)所需功耗、容积更小,投资成本降低,同时无废水处理成本,节约了废水处理设备投资及运行成本。按10年的运行期来计算,采用本实用新型所述超声波雾化脱酸系统,投资运营总成本约1476万元,远低于湿法脱酸系统,可见通过本实用新型的工艺改进及结构优化,可大幅降低质量含量较低的酸性气体进一步脱酸的成本,取得了商业上的成功。
[0085]
其它未说明的部分均属于现有技术。