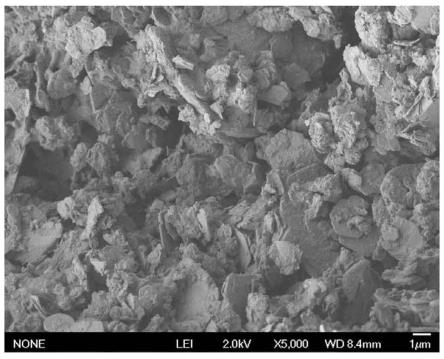
1.本发明涉及一种用于烯烃氢甲酰化反应的催化剂及其制备方法和应用,尤其涉及一种利用烯烃氢甲酰化反应制备醛类香料的方法,属于有机合成领域。
背景技术:2.氢甲酰化反应(hydroformylation),又称羰基合成反应(oxo process),是在适当的催化剂的存在下把h2和co加到烯烃分子上生成高经济附加值的醛的反应,产物醛可以通过进一步的反应得到醇、胺、羧酸、酯等化学化工产品,被广泛应用于香料、医药等领域。1938年,德国otto roelen首次报道了氢甲酰化反应,现在每年大约有700万吨的羰基产品都是利用这种方法生产的。氢甲酰化反应将廉价烯烃转化为醛,反应的原子利用率可达100%,符合绿色化学和产业升级的要求,是一类非常重要的化学反应。
3.1970年之前,大部分的氢甲酰化反应是通过co催化剂来完成的,后来rh催化剂逐渐占据主导。目前工业上,大约75%的氢甲酰化反应是用rh催化剂来完成的,广泛使用rh和有机膦配体合成的均相催化剂,具有催化活性高、反应条件温和的特点,但是存在铑金属价格昂贵且易流失、膦配体易氧化失活、含膦废水难处理、催化剂和反应物料难分离等问题,不利于其在大规模工业化中的应用。
4.专利cn111822045a公开了在氢甲酰化反应中使用离子液体将铑膦均相催化剂固载在sio2表面得到的催化剂,在最佳实施例中,烯烃的转化率为51.7%,产物醛的选择性为86.0%,计算收率为44.5%。该方法使用的铑膦催化剂价格昂贵,使用过程中也无法避免金属铑的流失,且反应的转化率和选择性均存在较大的提升空间。
5.专利cn104710288a公开了一种利用烯烃氢甲酰化反应生产高碳醛的方法,使用有机聚合物骨架载体负载活性金属如rh、ir或co制备得到非均相催化剂,醛收率最高为89.71%,产物的正异比最高为6.9,收率和正异比均有较大的提升空间,而且也存在常规负载型铑活性组分的流失问题。
6.专利cn109876847b公布了一种直接将均相催化剂包裹在s-1分子筛中的方法。这些方法都需要使用膦配体,制备方法较为复杂,且膦配体对空气敏感,在空气中极易被氧化。
7.专利cn109847741a公开了使用不同载体负载单原子铑制备的催化剂,摆脱了膦配体的限制,但是时空产率较低。因此,非均相催化剂同均相催化体系相比,存在金属流失严重,催化活性差等问题。
8.专利cn113385205a公开了一种应用于氢甲酰化反应的rh基无机金属磷化物催化剂,该催化剂将铑和过渡金属、磷源负载于氧化物或分子筛上,再经过氢气还原得到负载型金属磷化物固体催化剂,虽然解决了均相催化剂难分离的难题,但是反应的转化率不高;另外,催化剂中仍然大量使用铑、钯、钌等贵金属,导致催化剂的成本较高。
9.在氢甲酰化反应过程中,反应底物中的双键会同时发生多种反应类型,如加氢反应、聚合反应等,且反应温度越高,副反应越明显。因此,如何控制副反应发生,提高反应选
择性和收率是氢甲酰化反应的重点和难点。因此,开发一种廉价、实用、活性高、选择性高、催化性能稳定、环境友好的氢甲酰化催化剂体系具有重要工业意义和经济价值。
技术实现要素:10.要解决的技术问题为了解决现有技术中烯烃氢甲酰化反应制备醛过程中的存在的收率低、选择性差等问题,本发明提供一种用于烯烃氢甲酰化反应的催化剂及其制备方法,利用该催化剂可以有效提高现有工艺中产物醛的收率;同时氢甲酰化反应条件温和,可有效降低反应原料的聚合和醛产物的进一步氢化,提高总选择性。
11.用于解决问题的方案为达到以上目的,本发明采用如下技术方案:本发明第一方面提供一种用于烯烃氢甲酰化反应的催化剂的制备方法,包括以下步骤:(1)采用含氮化合物对干燥的载体进行改性处理得到改性载体;(2)将步骤(1)得到的改性载体浸渍在含钴源的溶液中,进行搅拌吸附,得到催化剂前驱体;(3)将贵金属的盐加入步骤(2)得到催化剂前驱体中进行进一步的吸附,然后经过过滤和烘干得到所述的催化剂;所述载体为金属硫化合物或金属硒化合物;所述金属硫化合物或金属硒化合物中的金属为w、mo、bi、nb、zr、ti、ni中的一种、两种或者多种;所述催化剂中含有的活性组分包括钴元素和贵金属元素;所述贵金属元素为rh、ru、pd、ir、pt中的一种、两种或者多种;所述的含氮化合物为取代或者未取代的含氮芳杂环化合物、取代或者未取代的含氮脂杂环化合物、r1r2nh、r3r4r5n、h2n-r
6-nh2中的一种或者多种;所述的含氮芳杂环化合物和含氮脂杂环化合物为5~12元环化合物;所述含氮芳杂环化合物和含氮脂杂环化合物上的取代基为c1~c6烷基;r1为c1~c6烷基;r2为c1~c6烷基;r3为c1~c6烷基;r4为c1~c6烷基;r5为c1~c6烷基;r6为c1~c6亚烷基本发明中,如无特别说明,后文提到“改性载体”指的是改性后的载体,“载体”指的是改性之前的载体。
12.本发明的催化剂先采用含氮化合物对载体进行处理得到改性载体,然后再负载活性组分。反应时,活性金属可能起到降低反应活化能的作用;所用载体为金属硫化物或硒化物,可能增大了反应的空间和催化活性。不同温度和压力下,载体的电子通量不同,可有效调节反应产物的正异比;含氮化合物在氢甲酰化反应过程中克服底物烯烃中的空间位阻,
起到调节区域选择性的作用。另外,还可进一步激活催化剂中的活性位点,缩短反应时间,提高转化率。在反应中调节反应体系的酸碱性,抑制产物醛的过度反应,提高反应的总收率。
13.上述“改性处理”指的是在一定温度和一定时间下搅拌处理,所述一定温度一般指的是20~30℃,一定时间一般指的是2~4小时。
14.所述的含氮芳杂环化合物和含氮脂杂环化合物为5~12元环化合物;所述的含氮芳杂环化合物优选为吡啶或者联吡啶,所述的含氮脂杂环化合物优选为哌啶、吗啉、二氮杂二环或者1,5,7-三氮杂二环[4.4.0]癸-5-烯。作为进一步的优选,所述含氮化合物为二氮杂二环(dbu)、二乙胺(dea)、乙二胺(eda)、三乙胺(et3n)、吡啶(py)、吗啉(mor)、6,6'-二甲基-3,3'-联吡啶(cas号:85484-42-0)、4-二甲氨基吡啶(dmap)、四甲基哌啶(htmp)、1,5,7-三氮杂二环[4.4.0]癸-5-烯(tbd,cas号:5807-14-7)、哌啶(pi) 中的一种、两种或者多种。
[0015]
上述“烷基”指的是烷烃失去一个h后形成的基团,“亚烷基”指的是烷烃失去两个h后形成的基团。
[0016]
作为优选,所述载体为ws2、mos2、bi2s3、nbs2、zrs2、tis2、nbse2、wse2、mose2、zrse2、nise2、bi2se3中的一种、两种或者多种,可直接从市场上购买得到。
[0017]
作为优选,钴元素的负载量(以金属计)和所述载体的质量比为0.001~0.1:1;优选0.005~0.07:1;更优选0.01~0.07:1。
[0018]
作为优选,所述贵金属元素和所述钴元素的质量比为0.05~0.2:1(以金属计)。
[0019]
步骤(1)中,作为优选,所述含氮化合物和所述载体的质量比为1~20:1;优选为2~10:1;更优选为2~4:1;作为优选,改性处理的温度为50~60℃,改性处理的时间为2~4小时。
[0020]
作为优选,改性处理在c1~c4烷基醇中进行,优选为甲醇或者乙醇。
[0021]
步骤(2)中,所述钴源为含钴的氯化物、硝酸盐、硫酸盐、乙酰丙酮盐、羰基化合物、氢氧化物或其水合物中的任意一种或其组合,优选为co(no3)2·
6h2o、coso4·
7h2o、coso4、cocl2、cocl2·
6h2o、co(oac)2·
4h2o、co(oac)2、naco(co)4、na3co(no2)6、co2(co)8、co(acac)3、co(acac)2、hco(co)4、co(oh)2中的任意一种或其组合;作为优选,所述钴源的溶液为水溶液,吸附的同时还加入正丁醇;作为优选,吸附的温度为45~55℃,吸附的时间为4~8小时。
[0022]
步骤(3)中,作为优选,贵金属的盐为金属氯化物、硝酸盐、乙酰丙酮盐或其水合物中的任一种或其组合;作为优选,进一步吸附的温度为45~55℃,吸附的时间为2~10小时。
[0023]
本发明还提供了上述方法制备得到的催化剂。
[0024]
本发明还进一步提供了一种醛的制备方法,在上述的催化剂的作用下,烯烃与合成气在溶剂中进行氢甲酰化反应,得到所述的醛;所述烯烃为端位烯烃或共轭烯烃。
[0025]
在醛的制备方法中,当所述烯烃为端位烯烃时,反应示例如下:
当所述烯烃为共轭烯烃时,反应(1,4-加成)示例如下:r为烃基。
[0026]
优选的,所述烯烃选自丙烯、1-丁烯、2-丁烯、异丁烯、1-戊烯、2-戊烯、1-辛烯、1,3-丁二烯、1,3-戊二烯、异戊二烯、2,6-二甲基-1,5-庚二烯、5-甲基-1,4-己二烯中的任意一种。
[0027]
共轭二烯发生氢甲酰化反应时,会同时发生1,2-加成和1,4-加成,但以1,4-加成为主。因此,区域选择性的调控在该反应中非常重要。
[0028]
发明人尝试将该催化剂用于其他含碳碳双键的非烯烃底物的氢甲酰化反应,取得了一定的效果。所述非烯烃底物选自2,5-二氢呋喃、1,4-二乙酰氧基-2-丁烯中的任意一种。
[0029]
所述合成气为主要包含h2和co的混合气体,h2和co的摩尔比为1:0.5~2.0,优选为1:1。
[0030]
所述的溶剂为水、异丙醇、乙醇、甲醇、甲苯中的一种或其组合。
[0031]
所述催化剂和所述烯烃的质量比为0.005~0.1:1;所述烯烃和所述溶剂的质量比为1:1~5。
[0032]
所述氢甲酰化反应的温度60~100℃,h2/co合成气总压力为1.0~5.0mpa;优选1.0~3.0mpa。
[0033]
本发明的有益效果如下:本发明的催化剂催化活性高,用于氢甲酰化反应时可以有效提高烯烃的转化率,同时可有效降低反应原料的聚合和醛产物的进一步氢化,选择性更高。
附图说明
[0034]
图1为催化剂性能测试实施例13的香茅醛的核磁共振氢谱;图2为催化剂性能测试实施例13的香茅醛的核磁共振碳谱;图3为催化剂制备实施例1的催化剂的sem照片;图4为催化剂制备实施例1的催化剂的x射线衍射图谱。
具体实施方式
[0035]
为了更好的理解本发明的技术方案,下面结合实施例进一步阐述本发明的内容,但本发明的内容并不仅仅局限于以下实施例。
[0036]
催化剂制备实施例金属质量=金属盐质量*金属元素质量/金属盐分子量*100%;理论负载量=金属质量/载体质量*100%。
[0037]
实施例1室温下,在100ml的乙醇中,加入10.0g干燥的ws2、30.0g的4-二甲氨基吡啶(dmap)
开启搅拌使其均匀分散,水浴加热,将温度升高至50℃,2小时后,滤出固体,置于60℃的真空干燥箱中,烘干,得到改性载体。室温时,将3.46g的co(no3)2·
6h2o溶解于10ml的去离子水中,然后加入制得的改性载体,温度升至45℃,搅拌吸附4小时。然后,滴加1.0ml溶解了0.142g rhcl3的水溶液,继续搅拌吸附2小时。吸附结束后,过滤,将得到的固体置于60℃真空干燥箱中烘干,得到催化剂,记为0.7%rh-7.0%co/ws
2-dmap(其中的0.7%和7.0%仅表示理论负载量),得到的催化剂的sem照片见图3,x射线衍射图谱见图4。
[0038]
实施例2~43改变钴源、贵金属、载体、氮化物的种类和比例等参数,按照实施例1 的方法,分别得到如下催化剂,具体如表1所示。
[0039]
表1 催化剂及制备参数a贵金属和钴的质量都以金属计,不包含阴离子。
[0040]
“‑”
表示不添加。
[0041]
注:实施例41*、42*、43*为催化剂对比实施例,仅改变了载体的种类、氮化物的含量,其他条件和制备方法同实施例1。
[0042]
实施例44室温下,在100ml的乙醇中,加入10.0g干燥的ws2、30.0g的4-二甲氨基吡啶(dmap)开启搅拌使其均匀分散,水浴加热,将温度升高至60℃,4小时后,滤出固体,置于60℃的真空干燥箱中,烘干,得到改性载体。室温下,将4.77g的coso4·
7h2o溶解于20ml的去离子水中,然后加入制得的改性载体,温度升至55℃,搅拌吸附8小时。然后,滴加5.0ml溶解了0.117氯化钯的水溶液,继续搅拌吸附2小时。吸附结束后,过滤,将得到的固体置于60℃真空干燥箱中烘干,得到催化剂,记为0.7%pd-10.0%co/ws
2-dmap。
[0043]
实施例45
室温下,在100ml的乙醇中,加入10.0g干燥的ws2、30.0g的4-二甲氨基吡啶(dmap)开启搅拌使其均匀分散,水浴加热,将温度升高至60℃,4小时后,滤出固体,置于60℃的真空干燥箱中,烘干,得到改性载体。室温下,将4.77g的coso4·
7h2o溶解于20ml的去离子水中,然后加入制得的改性载体,温度升至50℃,搅拌吸附8小时。然后,滴加5.0ml溶解了0.08g硝酸钯的水溶液,继续搅拌吸附2小时。吸附结束后,过滤,将得到的固体置于60℃真空干燥箱中烘干,得到催化剂,记为0.5%pd-10.0%co/ws
2-dmap。
[0044]
催化剂性能测试实施例1室温下,将6.8g0.7%rh-7.0%co/ws
2-dmap催化剂均匀分散于100g甲苯中,得到催化剂悬浮液。
[0045]
将高压釜分别用氮气和合成气(co/h2=1:1,摩尔比)置换3次后,使釜内充满合成气。将催化剂悬浮液、2mol(136.2g)1,3-戊二烯泵入高压釜,再通合成气至压力为3mpa,升温至80℃。加热搅拌3h后,降温至室温后泄压,并使用气相色谱检测反应液。结果显示:1,3-戊二烯转化率为99.6%,3-己烯醛选择性为99.8%。
[0046]
实施例2改变催化剂和溶剂的种类、用量,反应温度、时间等参数,其余操作同催化剂性能测试实施例1,反应结果汇总于下表,见表2。
[0047]
表2 反应结果汇总
注:对比例4中催化剂为发明人参照专利文献cn113385205a的实施例7在实验室制备。
[0048]
实施例3丙烯氢甲酰化反应室温下,将4.2g0.7%rh-7.0%co/ws
2-dmap催化剂均匀分散于100g甲苯中,得到催化剂悬浮液。
[0049]
将高压釜分别用氮气和合成气(co/h2=1:1,摩尔比)置换3次后,使釜内充满合成气。将催化剂悬浮液、2mol(84.0g)丙烯泵入高压釜,再通合成气至压力为3mpa,升温至80℃。加热搅拌3.5h后,降温至室温后泄压,并使用气相色谱检测反应液。结果显示:丙烯转化率为98.4%,正丁醛择性为99.2%。
[0050]
实施例41-丁烯氢甲酰化反应室温下,将5.6g0.7%rh-7.0%co/ws
2-dmap催化剂均匀分散于100g甲苯中,得到催化剂悬浮液。
[0051]
将高压釜分别用氮气和合成气(co/h2=1:1,摩尔比)置换3次后,使釜内充满合成气。将催化剂悬浮液、2mol(112.2g)1-丁烯泵入高压釜,再通合成气至压力为3mpa,升温至80℃。加热搅拌3.8h后,降温至室温后泄压,并使用气相色谱检测反应液。结果显示:1-丁烯转化率为98.7%,正戊醛择性为99.2%。
[0052]
实施例52-丁烯氢甲酰化反应室温下,将5.6g0.7%rh-7.0%co/ws
2-dmap催化剂均匀分散于100g甲苯中,得到催化剂悬浮液。
[0053]
将高压釜分别用氮气和合成气(co/h2=1:1,摩尔比)置换3次后,使釜内充满合成气。将催化剂悬浮液、2mol(112.2g)2-丁烯泵入高压釜,再通合成气至压力为3mpa,升温至80℃。加热搅拌3.8h后,降温至室温后泄压,并使用气相色谱检测反应液。结果显示:2-丁烯转化率为97.7%,2-甲基丁醛择性为98.6%。
[0054]
实施例6异丁烯氢甲酰化反应室温下,将5.6g0.7%rh-7.0%co/ws
2-dmap催化剂均匀分散于100g甲苯中,得到催化剂悬浮液。
[0055]
将高压釜分别用氮气和合成气(co/h2=1:1,摩尔比)置换3次后,使釜内充满合成气。将催化剂悬浮液、2mol(112.2g)异丁烯泵入高压釜,再通合成气至压力为3mpa,升温至80℃。加热搅拌3.5h后,降温至室温后泄压,并使用气相色谱检测反应液。结果显示:异丁烯转化率为98.6%,异戊醛择性为99.1%。
[0056]
实施例71,3-丁二烯氢甲酰化反应室温下,将5.4g0.7%rh-7.0%co/ws
2-dmap催化剂均匀分散于100g甲苯中,得到催化剂悬浮液。
[0057]
将高压釜分别用氮气和合成气(co/h2=1:1,摩尔比)置换3次后,使釜内充满合成气。将催化剂悬浮液、2mol(108.2g)1,3-丁二烯泵入高压釜,再通合成气至压力为3mpa,升温至80℃。加热搅拌4.5h后,降温至室温后泄压,并使用气相色谱检测反应液。结果显示:1,3-丁二烯转化率为98.4%, 2-甲基-3-丁烯醛择性为89.8%。
[0058]
实施例81-戊烯氢甲酰化反应室温下,将7.0g0.7%rh-7.0%co/ws
2-dmap催化剂均匀分散于100g甲苯中,得到催化剂悬浮液。
[0059]
将高压釜分别用氮气和合成气(co/h2=1:1,摩尔比)置换3次后,使釜内充满合成气。将催化剂悬浮液、2mol(140.3g)1-戊烯泵入高压釜,再通合成气至压力为3mpa,升温至80℃。加热搅拌3.0h后,降温至室温后泄压,并使用气相色谱检测反应液。结果显示:1-戊烯转化率为99.2%,正己醛择性为98.3%。
[0060]
实施例92-戊烯氢甲酰化反应室温下,将7.0g0.7%rh-7.0%co/ws
2-dmap催化剂均匀分散于100g甲苯中,得到催化剂悬浮液。
[0061]
将高压釜分别用氮气和合成气(co/h2=1:1,摩尔比)置换3次后,使釜内充满合成气。将催化剂悬浮液、2mol(140.3g)2-戊烯泵入高压釜,再通合成气至压力为3mpa,升温至80℃。加热搅拌4.0h后,降温至室温后泄压,并使用气相色谱检测反应液。结果显示:2-戊烯
转化率为98.2%,2-甲基戊醛择性为79.6%,2-乙基丁醛选择性为19.8%。
[0062]
实施例101-辛烯氢甲酰化反应室温下,将5.61g0.7%rh-7.0%co/ws
2-dmap催化剂均匀分散于100g甲苯中,得到催化剂悬浮液。
[0063]
将高压釜分别用氮气和合成气(co/h2=1:1,摩尔比)置换3次后,使釜内充满合成气。将催化剂悬浮液、1mol(112.2g)1-辛烯泵入高压釜再通合成气至压力为3mpa,升温至100℃。加热搅拌4.0h后,降温至室温后泄压,并使用气相色谱检测反应液。结果显示:1-辛烯转化率为98.1%,正壬醛择性为98.6%。
[0064]
实施例11异戊二烯氢甲酰化反应室温下,将6.8g0.7%rh-7.0%co/ws
2-dmap催化剂均匀分散于100g甲苯中,得到催化剂悬浮液。
[0065]
将高压釜分别用氮气和合成气(co/h2=1:1,摩尔比)置换3次后,使釜内充满合成气。将催化剂悬浮液、2mol(136.2g)异戊二烯泵入高压釜,再通合成气至压力为3mpa,升温至80℃。加热搅拌4.0h后,降温至室温后泄压,并使用气相色谱检测反应液。结果显示:异戊二烯转化率为97.7%,3-甲基-3-戊烯醛择性为98.1%。
[0066]
实施例125-甲基-1,4-己二烯氢甲酰化反应室温下,将5.5g 0.7%rh-7.0%co/ws
2-dmap催化剂均匀分散于100g甲苯中,得到催化剂悬浮液。
[0067]
将高压釜分别用氮气和合成气(co/h2=1:1,摩尔比)置换3次后,使釜内充满合成气。将催化剂悬浮液、1mol(110.2g)5-甲基-1,4-己二烯泵入高压釜,再通合成气至压力为3mpa,升温至85℃。加热搅拌4.5h后,降温至室温后泄压,并使用气相色谱检测反应液。结果显示:5-甲基-1,4-己二烯转化率为98.6%,6-甲基-5-庚烯醛选择性为97.2%。实施例132,6-二甲基-1,5-庚二烯氢甲酰化反应室温下,将6.2g0.7%rh-7.0%co/ws
2-dmap催化剂均匀分散于100g甲苯中,得到催化剂悬浮液。
[0068]
将高压釜分别用氮气和合成气(co/h2=1:1,摩尔比)置换3次后,使釜内充满合成气。将催化剂悬浮液、1mol(124.4g)2,6-二甲基-1,5-庚二烯泵入高压釜,再通合成气至压力为3mpa升温至90℃。加热搅拌4h后,降温至室温后泄压,并使用气相色谱检测反应液。结果显示:2,6-二甲基-1,5-庚二烯转化率为98.6%,香茅醛选择性为98.4%。香茅醛经过减压蒸馏提纯,得到香茅醛纯品进行核磁检测,得到的氢谱如图1所示,碳谱如图2所示。
[0069]
核磁氢谱数据解析如下(上标代表h的位置):1h-nmr(400mhz,cd3oh):δ9.72~9.71ppm(=ch1)、5.15~5.10ppm(=ch
7-)、2.46~2.22 ppm(-ch
22-)、2.07~2.02 ppm(-ch
3-,-ch
62-,)、1.70ppm(-ch
83
)、1.63ppm(-ch
93
); 1.42~1.29ppm(-ch
52-)、0.99~0.93ppm(-ch
43
);各个h的位置如下:
核磁碳谱数据解析如下(上标代表c的位置)
13 c-nmr(100mhz,cd3oh):202.83ppm(c1)、131.02ppm(c8)、124.68ppm(c7)、50.65ppm(c2)、37.15ppm(c5)、28.73ppm(c9)、27.49ppm(c3)、25.21ppm(c6)、19.16ppm(c4)、16.74ppm(c
10
);各个c的位置如下:发明人尝试将本发明的催化剂用于非烯烃类的底物的氢甲酰化反应,反应结果如下:实施例142,5-二氢呋喃氢甲酰化反应室温下,将7.0g 0.7%rh-7.0%co/ws
2-dmap催化剂均匀分散于100g纯化中,得到催化剂悬浮液。
[0070]
将高压釜分别用氮气和合成气(co/h2=1:1,摩尔比)置换3次后,使釜内充满合成气。将催化剂悬浮液、2mol(140.2g)2,5-二氢呋喃依次泵入高压釜,再通合成气至压力为2mpa,升温至80℃,加热搅拌4.5h后,降温至室温后泄压,并使用气相色谱检测反应液。结果显示:2,5-二氢呋喃转化率为90.1%,四氢呋喃-3-甲醛选择性为94.2%。
[0071]
实施例151,4-二乙酰氧基-2-丁烯氢甲酰化反应室温下,将10.3g 0.7%rh-7.0%co/ws
2-dmap催化剂均匀分散于100g甲苯中,得到催化剂悬浮液。
[0072]
将高压釜分别用氮气和合成气(co/h2=1:1,摩尔比)置换3次后,使釜内充满合成气。将催化剂悬浮液、1mol(172.2g)1,4-二乙酰氧基-2-丁烯依次泵入高压釜,再通合成气至压力为3mpa,升温至100℃,加热搅拌5.0h后,降温至室温后泄压,并使用气相色谱检测反应液。结果显示:1,4-二乙酰氧基-2-丁烯转化率为91.6%,2-甲酰基-1,4-二乙酰氧基丁烷
选择性为93.1%。
[0073]
催化剂套用实施例反应结束后,将催化剂性能测试实施例1中的催化剂0.7%rh-7.0%co/ws
2-dmap过滤、干燥得到回收催化剂,在相同条件下进行循环套用,测试催化剂的稳定性,结果如表3所示。
[0074]
表3 催化剂套用数据除特殊说明的外,本发明所述的百分数均为质量百分数,所述的比值均为质量比。
[0075]
以上所述的具体实施方式对本发明的技术方案和有益效果进行了详细说明,应理解的是以上所述仅为本发明的最优选实施例,并不用于限制本发明,凡在本发明的原则范围内所做的任何修改、补充和等同替换等,均应包含在本发明的保护范围之内。