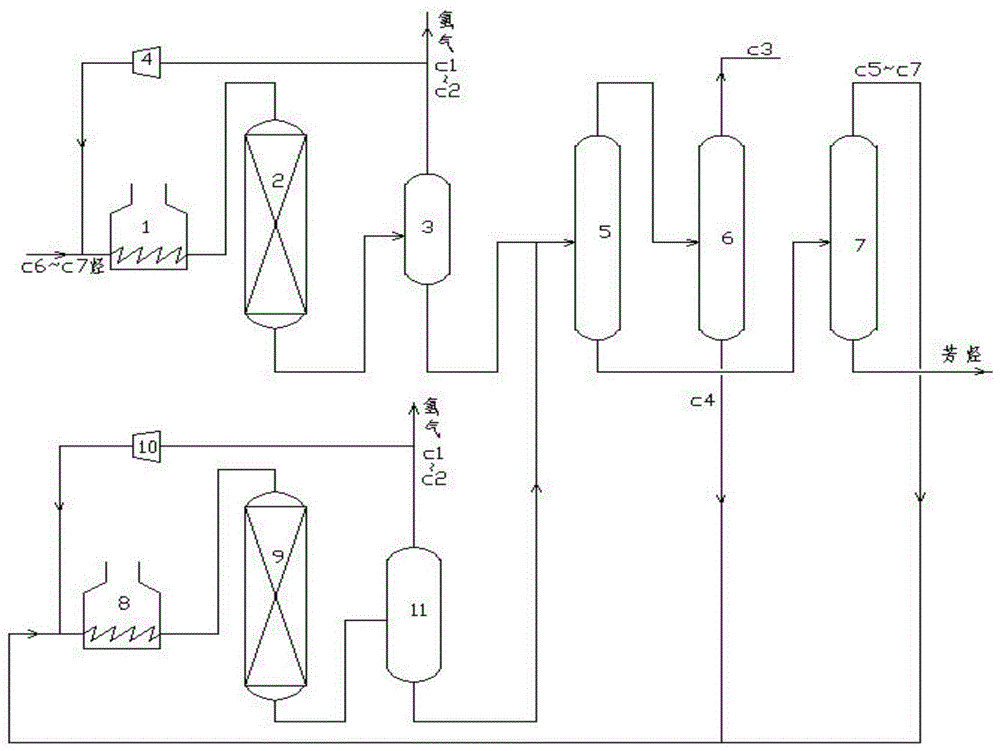
本发明涉及一种由c6~c7烷烃高产芳烃和氢气的方法,更具体地说,是通过两个不同催化反应区的反应,使烷烃最大量转化为芳烃和氢气,提高烷烃的目标产物收率。技术背景催化重整装置生产的抽余油主要为c6~c7的正构烷烃、异构烷烃和少量的环烷烃。目前其主要用作汽油调和组分或生产各类溶剂油。由于这些抽余油中正构烷烃的辛烷值低,使其直接作为汽油调和组分的加入量有限,而作为溶剂油使用附加值较低。通过pt/kl沸石基催化剂的转化反应,可高选择性地将正构烷烃转化为苯、甲苯等芳烃,分离芳烃后还可获得未反应的异构烷烃是较高辛烷值的汽油调和组分。然而,由于受反应平衡的限制,在一定的温度区间、反应压力和空速条件下,原料中的正构烷烃的转化率仍是一定的,未转化的烷烃仍然影响原料的有效利用率和汽油调和组分油的辛烷值。目前,为提高pt/kl沸石基催化反应产物中未转化烷烃的利用率,主要集中在组合pt/kl沸石基催化反应区和异构化反应区,将正构烷烃和单甲基烷烃通过pt/kl沸石基催化反应区生产芳烃,再将未反应完全而剩余的正构烷烃和单甲基烷烃通过异构化反应区异构化反应,反应产物与原料中二甲基烷烃一并成为高辛烷值汽油调和组分;或者是将pt/kl沸石基催化反应区产物中非芳烃部分中c6及以上正构烷烃和带一个支链的烷烃分离出来,再循环去芳构化反应区再转化,获得最大量芳烃,同时也得到支链更多、辛烷值更高的汽油调和组分油。cn106367112b公开了一种利用重整抽余油生产芳烃和提高副产品辛烷值的方法,该工艺将重整抽余油中的c6~c7馏分经金属改性的pt/kl分子筛催化剂芳构化反应后,产物进行芳烃与非芳烃分离,c5+非芳烃再进入有异构化催化剂的反应器进行异构化反应获得较高辛烷值的汽油组分;该工艺将芳构化和异构化反应组合,得到适当芳烃产物的同时,也可获得高辛烷值的汽油组分油。cn106367116b公开了一种利用重整抽余油制备轻质芳烃的方法,该工艺具体过程是将重整抽余油经干燥塔脱水,再经预热器加热到反应温度后进入装有pt/kl分子筛催化剂的芳构化反应器进行芳构化反应,芳构化反应产物经分离出c5+非芳烃和轻质芳烃,c5+非芳烃进入分馏塔分馏切割成c5~c6馏份和c6~c7馏份,c6~c7馏份返回芳构化反应器中继续进行芳构化;该工艺通过循环未反应物料的方式,获得最大量芳烃。cn107916134a公开了一种由轻烃生产高辛烷值汽油和芳烃的方法,该工艺将c5~c8的轻质芳烃通入异构化反应区进行异构化反应,再将液相异构化反应产物送入装有pt/kl分子筛催化剂的芳构化区进行芳构化反应,芳构化反应产物经气液分离后,将所得液相产物芳烃抽提,得到含芳烃组分的抽出油和含非芳烃组分的抽余油;该工艺将异构化和芳构化反应组合,可获得高辛烷值的汽油组分,并保持适当的芳烃产物。cn107916132a公开了一种由c6~c7烷烃生产芳烃和异构化汽油的方法,该工艺将正构烷烃和单甲基烷烃的c6~c7烷烃以装有pt/kl分子筛催化剂的芳构化区进行重整反应,然后将反应产物中的芳烃和非芳烃分离,非芳烃再经脱已烷塔分离,正构烷烃和单甲基烷烃再选择性循环回pt/kl分子筛催化剂的芳构化区重整反应;该工艺通过反应物料的选择性循环反应,芳构化反应效率高,并可获得高辛烷值的汽油组分。cn107955644a公开了一种非芳轻烃的高效芳构化方法,该方法是将非芳轻烃原料进入装有pt/kl分子筛催化剂的芳构化区进行芳构化反应,产物进行芳烃与非芳烃分离,c6非芳进入脱二甲基丁烷塔,脱二甲基丁烷塔塔顶和塔底物料作为高辛烷值汽油组分回收,脱二甲基丁烷塔侧线采出物料返回芳构化反应区;该方法大幅提高了轻烃原料的芳构化利用率,并解决了轻重组分在系统内的累积问题。cn108238838a公开了一种c6烷烃高产苯的方法,该方法是将c6烷烃原料依次通过吸附器脱除正已烷、通过脱异已烷塔脱除轻、重组分,脱异已烷塔的侧线组分和从吸附器来正已烷进入装有pt/kl分子筛催化剂的芳构化区进行芳构化反应,该方法大幅提高了c6烷烃中活性组分的利用率,脱除了原料中的大部分水,并解决了轻重组分在反应系统内的累积问题。综合已有专利的公开信息,为提高pt/kl沸石基催化反应产物中未转化烷烃的利用率,主要集中在组合pt/kl沸石基催化反应和异构化反应的两个反应区,或者是将pt/kl沸石基催化反应区产物中非芳烃部分中c6及以上正构烷烃和带一个支链的烷烃分离出来,再循环去芳构化反应区再转化,获得最大量芳烃,同时也得到支链更多、辛烷值更高的汽油调和组分油。这些技术的目的产物仍有大量的汽油调和组分油,不符合转型升级减少燃料汽油的时代发展要求。如果能够将pt/kl沸石基催化反应产物中的烷烃分离出来再有效地二次转化为芳烃,并最大量获得氢气,将是提高c6~c7抽余油烷烃利用率的有效途径之一。技术实现要素:本发明的目的是在于提供一种由c6~c7烷烃高产芳烃和氢气的方法,使原料c6~c7烷烃最大限度和高选择性地转化为苯、甲苯和二甲苯等芳烃,同时获得高产率氢气,且装置流程简单。为了实现上述技术目的,本发明采用如下技术方案:一种由c6~c7烷烃高产芳烃和氢气的方法,将c6~c7烷烃送入有金属改性的kl沸石型催化剂存在的第一反应器进行芳构化选择性和活性的脱氢反应,然后将反应产物送至分离系统实现氢气、芳烃与非芳烃分离,c4~c7非芳烃再进入有金属改性的hzsm-5沸石型催化剂存在的第二反应器进一步芳构化改质反应,所得液相反应产物返回分离系统实现循环。优选的方案,所述c6~c7烷烃为重整抽余油切割得到的c6~c7组分。优选的方案,所述第一反应器为列管式反应器、筒式的轴向、径向床反应器或流化床反应器,反应器个数为2~6,且每个反应器设有旁路;所述第一反应器的反应控制的工艺条件为:温度440~520℃,压力0.2~1.0mpa(g),氢油体积比400~1200:1,原料体积空速1.0~3.5h-1。优选的方案,所述金属改性的kl型沸石催化剂是pt/kl催化剂,所述催化剂包括沉积碱金属钾的l-沸石载体和金属催化剂活性组分,所述金属催化剂活性组分在载体上的负载量为1.0~3.0wt%;所述金属催化剂活性组分包括金属铂主催化剂,以及锡、锌、钡、铁中的至少一种改性金属。kl-沸石型载体的成型方法可为滚球成型、滴球成型、压片成型或挤条成型。所述pt/kl型属单功能催化剂,载体kl为碱性,没有酸性中心,反应物没有在酸性中心上裂解的机会;l沸石结构和分子筛静电场效应,使pt微粒高度分散,提供了足够的反应分子吸附、环化、脱氢所需的活性中心,烷烃分子(≥c6)主链的1,6位碳原子与pt粒作用生成1,6吸附态后、直接闭环脱氢为芳烃,具有较高的芳构化反应活性和芳烃选择性,裂解副反应少。进一步优选的方案,所述金属改性的pt/kl催化剂具体制备过程为:将al(oh)3加入到koh溶液中,加热溶解得到铝溶胶,将sncl4·5h2o溶于蒸馏水中,再与铝溶胶混合形成混合溶液,搅拌下将混合溶液加入到硅溶胶中,搅拌形成白色凝胶,再将白色凝胶移入晶化釜内晶化,然后迅速冷却,产物经离心分离、洗涤,所得固体经过干燥,得到含锡kl分子筛原粉;将含锡kl分子筛在zn、ba、fe中的一种或几种的盐溶液中浸渍、干燥、焙烧,然后在pt(nh3)2cl2溶液中浸渍、干燥、焙烧,或者将含锡kl分子筛直接在pt(nh3)2cl2溶液中浸渍、干燥、焙烧。优选的方案,所述第二反应器中的芳构化改质反应可以在固定床反应器或移动床反应器-连续再生反应系统中进行,反应器个数为一个或多个,两个或两个以上反应器采用串联或并联的操作方式。所述第二反应器的反应控制的工艺条件为:温度460~550℃,压力0.1~0.7mpa(g),原料体积空速0.5~2.5h-1。反应可在非临氢或临氢条件下进行,临氢条件下含氢载气在反应系统内可循环或一次通过,氢油体积比为100~1000:1。优选的方案,所述金属改性的hzsm-5沸石型催化剂可为任何具有芳构化活性的催化剂,催化剂上改性活性组分在载体上的负载量为0.1~5.0wt%。所述改性活性组分为锌、锑、铋、钼或镓中的至少一种金属的氧化物和混合稀土的氧化物,所述的混合稀土氧化物含30wt%的氧化镧、50wt%的氧化铈、15wt%的氧化镨和5wt%的氧化钕。所述载体由65.0wt%的hzsm-5和35.0wt%的γ-al2o3组成,所述的hzsm-5的氧化硅/氧化铝的摩尔比为30~100。进一步优选的方案,所述金属改性的hzsm-5沸石型催化剂具体制备过程为:将一定比例的氢氧化铝粉与氧化硅/氧化铝的hzsm-5沸石粉搅拌均匀,再加入一定浓度的硝酸,充分捏合、挤条、干燥、切粒、焙烧,制成催化剂载体;取一定量的上述载体在锌、锑、铋、钼或镓中的一种或几种的盐溶液中浸渍、干燥、焙烧,再与含氧化镧、氧化铈、氧化镨和氧化钕的混合氯化稀土的水溶液再浸渍、干燥、焙烧,制成催化剂。优先的方案,第一反应器的反应产物经过气液分离,将含氢气、c1~c2的气体分离出来,一部分作为反应的循环氢,另一部分排出反应系统,作为其它单元的氢气来源;分离出氢气的物料再进行液化气分离,将c4及c3分离出来,余下液相物料通过芳烃抽提分离出其中的芳烃与非芳烃,所得的芳烃为抽出油,非芳烃组分为抽余油;液化气分离得到的c4烃及抽余油得到c5~c7烃,即c4+烃类一并再进入第二反应器反应,将该反应产物含氢气、c1~c2的气体分离出来,一部分作为反应的循环氢(如需临氢环境时),另一部分排出反应系统,作为其它单元的氢气来源;分离出氢气后的物料返回与第一反应器后的分离出含氢气、c1~c2的气体的物料合并实现液化气分离、芳烃与非芳烃分离后循环利用。优先的方案,所述第一反应和第二反应共用一台循环压缩机或分别配置各自的循环压缩机。本发明优点:本发明的方法使得原料c6~c7烷烃最大限度和高选择性地转化为苯、甲苯和二甲苯等芳烃,同时获得高产率氢气,且装置流程简单。附图说明图1为本发明的工艺流程示意图;为了便于理解本发明,图中仅示出了主要设备,其它一些设备如换热器、冷却器、机泵和容器等未在示意图中给出;图中:1-第一加热炉,2-第一反应器,3-第一气液分离器,4-第一循环氢压缩机,5-稳定塔,6-c3、c4分离塔,7-芳烃抽提分离装置,8-第二加热炉,9-第二反应器,10-第二循环氢压缩机,11-第二气液分离器。具体实施方式下面结合附图和具体实施例对本发明作进一步说明,但本发明并不限于此。重整抽余油c6~c7烷烃与循环氢混合后经与第一反应器2的高温出料换热后,通过第一加热炉1加热后自第一反应器2上端进入并发生高选择性芳构化反应,反应生成物经与进料换热再经冷却器冷却后进入第一气液分离器3,顶部分离出的氢气及c1~c2一部分经第一循环氢压缩机4循环回第一反应器2入口,另一部分则外送作为其它氢源和燃料气,底部液相进入稳定塔5,稳定塔5顶物料再进入c3、c4分离塔6,使c3、c4分离,塔5底物料进入芳烃抽提装置7,芳烃经芳烃抽提蒸馏自芳烃抽提装置7底部作为产品外送,自芳烃抽提装置7顶部甩出c5~c7与c3、c4分离塔6底部甩出c4混合后一并与第二反应器9出料换热后进入第二加热炉8加热后自第二反应器9上端进入并进行烷烃芳构化改质反应,反应生成物经与进料换热再经冷却器冷却后进入第二气液分离器11,顶部分离出的氢气及c1~c2一部分经第二循环氢压缩机10循环回第二反应器9入口,另一部分则外送作为其它氢源和燃料气,底部液相进入稳定塔5。实施例1制备本发明所用的pt/kl催化剂。将43.5gal(oh)3加入到500ml含129gkoh的溶液中,加热溶解得到铝溶胶,将15.0gsncl4·5h2o溶于200ml蒸馏水中,再与铝溶胶混合形成混合溶液,搅拌下将混合溶液加入到783ml的硅溶胶中,搅拌形成白色凝胶。再将白色凝胶移入3l的晶化釜内150℃晶化2天,然后迅速冷却至40℃,产物经离心分离、洗涤至液相ph值为10~11,所得固体于120℃干燥10小时,得到含锡kl分子筛原粉。取100克上述含锡kl分子筛作为载体,以含5wt%的bacl2、5wt%的zncl2溶液在30℃浸渍24小时,将浸渍后固体于120℃干燥10小时,350℃焙烧4小时,再将固体用浓度为16mg/ml的pt(nh3)2cl2溶液过饱和浸渍,浸渍时液/固体积比为4∶1,温度30℃,浸渍时间6小时,将浸渍后固体于120℃干燥10小时,350℃焙烧4小时,制成含pt1.0wt%、sn1.0wt%、zn0.5wt%、ba0.5wt%的催化剂。实施例2制备本发明的hzsm-5型沸石催化剂。取氧化硅/氧化铝摩尔比为56的hzsm-5沸石粉120克,80克氢氧化铝粉,搅拌混合均匀,加入4毫升浓度为40wt%的硝酸和100毫升去离子水充分捏合,挤成直径为2毫米的条,110℃干燥8小时,切成长度为2~3毫米的颗粒,再于570℃焙烧4小时。取上述载体100克,以含3wt%的zncl2、3wt%的bicl3溶液在30℃浸渍24小时,将浸渍后固体于120℃干燥10小时,350℃焙烧4小时;再用100毫升含1.0克混合氯化稀土(约含30wt%氧化镧、50wt%的氧化铈、15wt%的氧化镨和5wt%的氧化钕)的水溶液在80℃浸渍2小时,120℃干燥8小时,550℃焙烧4小时;将制成的催化剂在密闭容器内在空气流中升温至580℃,然后以80克/小时的水蒸汽处理5小时,再用空气冷却至常温。对比例1按图1的流程由c6~c7烷烃生产芳烃和氢气,原料只经过装有实施例1的pt/kl催化剂的第一反应器,c4和c5~c7轻烃直接作为产品外送出。以表1所示混合原料进入第一反应器内。第一反应器控制的工艺条件为:温度为440~520℃,压力0.2~1.0mpa(g),氢油体积比400~1200:1,原料体积空速1.0~3.5h-1。反应产物经气液分离,得到h2和c1、c2、c3、c4烃类及c5~c7液相产物,液相产品全部去芳烃抽提蒸馏装置,芳烃抽提溶剂为环丁砜,抽出油为芳烃,抽余油为c5~c7烃类。反应结果见表2。表2数据表明,在催化剂作用下c6烷烃对苯的芳构化活性及选择性较高,产物中苯收率接近40%,氢气产率达3.58%,但c6烷烃仍有部分不能转化为其它芳烃,且总芳烃收率低。对比例2按图1的流程由c6烷烃生产芳烃和氢气,原料只经过装有实施例2的hzsm-5型沸石催化剂的第二反应器,c4和c5~c7轻烃直接作为产品外送出。以表1所示混合原料进入反应器内。第二反应器控制的工艺条件为:反应温度460~550℃,压力0.1~0.7mpa(g),原料体积空速0.5~2.5h-1;反应在非临氢条件下进行。反应产物经气液分离,得到h2和c1、c2、c3、c4烃类及c5~c7液相产物,液相产品全部去芳烃抽提蒸馏装置,芳烃抽提溶剂为环丁砜,抽出油为芳烃,抽余油为c5~c7烃类。反应结果见表2。表2数据表明,在催化剂作用下c6烷烃对苯的芳构化活性及选择性远不及对比例1,但芳烃的总收率接近60%,氢气产率达4%,c6烷烃转化较完全。实施例3按图1的流程由c6烷烃生产芳烃和氢气,以表1所示混合原料先经过装有实施例1的pt/kl催化剂的第一反应器,反应产物经气液分离,得到h2和c1、c2、c3、c4烃类及c5+液相产物,液相产品全部去芳烃抽提蒸馏装置,芳烃抽提溶剂为环丁砜,抽出油为芳烃,抽余油为c5~c7烃类;c4和c5~c7烃类再进入装有实施例2的hzsm-5型沸石催化剂的第二反应器,反应产物经气液分离后一并进入同一分离系统,抽出油为芳烃,抽余油c5~c7液相产物及c4再循环回hzsm-5型沸石催化剂的第二反应器。pt/kl催化剂第一反应器的控制工艺条件为:温度为440~520℃,压力为0.2~1.0mpa(g),氢油体积比400~1200:1,原料体积空速为1.0~3.5h-1。hzsm-5型沸石催化剂第二反应器的工艺条件为:反应温度460~550℃,压力0.1~0.7mpa(g),原料体积空速0.5~2.5h-1;反应在非临氢条件下进行。反应结果见表2。表2数据表明,c6烷烃在双反应区间的催化剂作用下,苯的收率接近47%,其它芳烃收率接近26%,芳烃的总收率达73%,氢气产率达5.17%,c6轻烃转化为高价值的氢气和苯及芳烃较完全。对比例3按图1的流程由重整抽余油c6~c7轻烃生产芳烃和氢气,原料只经过装有实施例1的pt/kl催化剂的第一反应器,c4和c5~c7轻烃直接作为产品外送出。以表3所示混合原料进入第一反应器内。第一反应器控制的工艺条件为:温度为440~520℃,压力0.2~0.5mpa(g),氢油体积比800~1200:1,原料体积空速1.5~3.5h-1。反应产物经气液分离,得到h2和c1、c2、c3、c4烃类及c5~c7液相产物,液相产品全部去芳烃抽提蒸馏装置,芳烃抽提溶剂为环丁砜,抽出油为芳烃,抽余油为c5~c7烃类。反应结果见表4。表4数据表明,催化剂作用下c6~c7轻烃对苯、甲苯的芳构化活性及选择性较高,产物中苯+甲苯的收率接近36%,氢气产率达2.85%,但c6、c7轻烃仍有大部分不能转化为芳烃。对比例4按图1的流程由重整抽余油c6~c7轻烃生产芳烃和氢气,原料只经过装有实施例2的hzsm-5型沸石催化剂的第二反应器,c4和c5~c7轻烃直接作为产品外送出。以表3所示混合原料进入第二反应器内。第二反应器控制的工艺条件为:反应温度480~550℃,压力0.4~0.7mpa(g),原料体积空速1.5~2.5h-1;反应在临氢条件下进行,氢油体积比为500~1000:1。反应产物经气液分离,得到h2和c1、c2、c3、c4烃类及c5~c7液相产物,液相产品全部去芳烃抽提蒸馏装置,芳烃抽提溶剂为环丁砜,抽出油为芳烃,抽余油为c5~c7烃类。反应结果见表4。表4数据表明,催化剂作用下c6~c7轻烃对苯、甲苯的芳构化活性及选择性与对比例3相当,但苯的选择性远不及对比例3,芳烃的总收率接近62%,氢气产率达4%,c6~c7轻烃转化较完全。实施例4按图1的流程由重整抽余油c6~c7轻烃生产芳烃和氢气,以表3所示混合原料先经过装有实施例1的pt/kl催化剂的第一反应器,反应产物经气液分离,得到h2和c1、c2、c3、c4烃类及c6~c7液相产物,液相产品全部去芳烃抽提蒸馏装置,芳烃抽提溶剂为环丁砜,抽出油为芳烃,抽余油为c5~c7烃类;c4和c5~c7烃类再进入装有实施例2的hzsm-5型沸石催化剂的第二反应器,反应产物经气液分离后一并进入同一分离系统,抽出油为芳烃,抽余油c5~c7液相产物及c4再循环回hzsm-5型沸石催化剂的第二反应器。pt/kl催化剂第一反应器的控制工艺条件为:温度为440~520℃,压力0.2~0.5mpa(g),氢油体积比800~1200:1,原料体积空速1.5~3.5h-1。hzsm-5型沸石催化剂的第二反应器的控制工艺条件为:反应温度480~550℃,压力0.4~0.7mpa(g),原料体积空速1.5~2.5h-1;反应在临氢条件下进行,氢油体积比为500~1000:1。反应结果见表4。表4数据表明,c6~c7轻烃在双反应区间的催化剂作用下对苯、甲苯的芳构化活性及选择性高,苯+甲苯的收率接近55%,其它芳烃收率接近17%,芳烃的总收率达72%,氢气产率达4.9%,c6~c7轻烃转化为高价值的氢气和苯+甲苯及芳烃较完全。表1轻烃c6原料项目原料c6,w%异戊烷0.01正戊烷0.04二甲基丁烷5.5甲基戊烷50.43正己烷39.67甲基环戊烷3.25二甲基戊烷0.55苯0.05c7+0.5合计100表2对比例1-2和实施例3的反应结果表3轻烃c6~c7原料项目原料c6/c7,w%正戊烷1.09二甲基丁烷7.95甲基戊烷31.78正己烷19.01甲基环戊烷1.85二甲基戊烷8.77甲基已烷22.55乙基戊烷1.26正庚烷4二甲基环戊烷0.65c8+1.09合计100表4对比例3-4和实施例4的反应结果当前第1页12