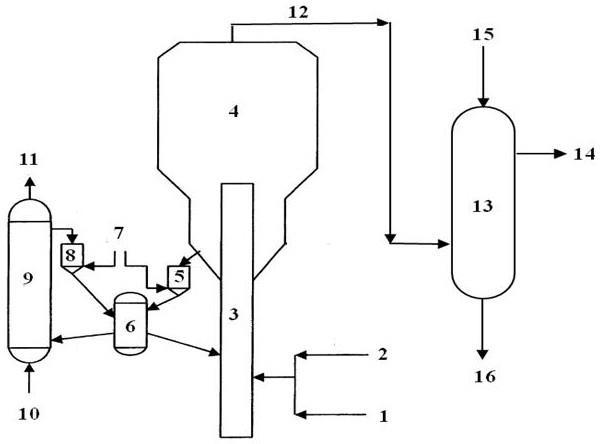
1.本发明涉及一种液化气深度脱硫方法,特别是应用于催化裂化液化气原料的低烯烃饱和率下深度脱硫处理。
背景技术:2.催化裂化液化气是丙烯、异构丁烯的主要来源,一般组成为:丙烷(12.8v%)、丁烷(26.1v%)、丙烯(38.0v%)、丁烯(21.0v%)等,同时含有高达4264mg/m3的含硫化合物,含硫化合物主要以硫化氢和有机硫化物如硫醇的形式存在。据统计,2018年中国石化的催化裂化液化气处理量高达1430万吨/年。丙烯作为下游聚合、异构丁烯作为mtbe原料需要脱硫(硫化氢和硫醇),精制才能满足下游总硫含量≯10mg/m3的要求。
3.传统的液化气双脱硫工艺多为merox脱臭(sweeten)工艺,其主要原理见如下:可以看出,双脱(脱h2s和脱硫醇)其缺点之一是:硫醇(rsh)仅仅氧化转化为二硫化物(rssr),并不降低总硫含量或有限度降低总硫含量;缺点之二脱硫装置产生的再生有机废气和碱渣都是环保难以处理的污染物,存在环保或安全方面的隐患。
4.cn200910233505.1公开了一种高酸性石油天然气的高效脱硫剂。该发明是在纤维膜式反应器中加入一种水溶性含氮有机溶剂(碱性氮含量≥100g/l)来脱硫,比传统烷醇胺法(如n-甲基二乙醇胺,mdea)脱硫率高,但是含氮有机溶剂需要反复再生、换热,流程复杂、能耗较高。
5.cn104194833a公开了一种液化气深度脱硫工艺,改工艺是液化气先通过胺液抽提脱h2s,并进行水洗脱除携带的胺液;然后在硫化态mo-ni/γ-al2o3催化剂上加氢转化将液化气中的硫化物转化为高沸点的硫化物;加氢产物进入稳定塔,采用低硫碳五以上馏分进行精馏分离,得到超低硫液化气产物,可以作为生产mtbe或烷基化低硫原料。
6.cn103965984a介绍了一种液化石油气催化脱硫醇方法,该方法中液化石油气与氢气混合后进入一个固定床反应器,与其中装填的ni-mo/γ-al2o3催化剂或ni-mo/γ-al2o3催化剂进行硫醚化反应,将低沸点硫醇转化为高沸点的硫醚化合物;然后硫醚化反应产物再在蒸馏塔中进行蒸馏处理,得到不含硫醇的液化气产品。其缺点是液化气含有0.03%(v/v)~0.03%(v/v)的1,3-丁二烯容易造成催化剂积碳失活,100h左右,硫醇含量就超过10
µ
g/g;另外,蒸馏塔需要再沸器,能耗较高。
7.us7270737b2介绍了一种烃类原料脱硫工艺,其特点是烃类,如催化裂化汽油,采用含有viii族金属元素的催化剂(商品名称hr845催化剂,硫化态)先进行选择性加氢脱硫,将汽油中低沸点的硫醇硫与二烯烃反应转化为高沸点的硫化物,然后通过抽提塔得到低硫含量抽余油,与原料相比,脱硫率可以达到97.9%,同时在降低二烯烃含量的情况下,烯烃饱和率也较低。但是该工艺采用环丁砜作为溶剂,需要反复再生、流程复杂,同时具有燃爆危险、腐蚀性、水危害级别1(德国规例)易污染周围环境等缺点。
8.加氢脱硫技术在催化裂化汽油脱硫方面都取得了良好的成果,但加氢脱硫技术于液化气脱硫方面的工业应用相对较少,因此为弥补目前液化气脱硫过程的不足。
技术实现要素:9.针对现有技术中的不足之处,本发明提供了一种液化气深度脱硫方法。该脱硫方法可以在较低温度下进行液化气深度脱硫,在烯烃饱和率≯1.0%下,满足产物总硫含量≯5.0mg/m3、硫醇硫含量≯1.0mg/m3的要求。
10.本发明的液化气深度脱硫方法,包括如下内容:液化气原料和氢气从流化床反应器下部进入,与进入反应器中的微球形脱硫催化剂接触,以流化床状态进行选择性脱硫反应;然后,含有硫化氢的反应产物与催化剂在反应器上部进行气固分离,气相从反应器顶部排出进入醇胺吸收塔脱除硫化氢,得到液化气脱硫产物,待再生催化剂从反应器下部排出。本发明方法中,步骤(1)所述的液化气原料为催化裂化(fcc)液化气、焦化液化气、天然液化气等中的一种或多种。其中优选催化裂化(fcc)液化气,其中丙烯含量为20.0v%~40.0v%、丁烯含量为10.0v%~30v%;总硫含量为100~5000mg/m3,硫醇硫含量为50~200mg/m3。
11.本发明方法中,步骤(1)所述的流化床反应器中的操作条件如下:反应压力为0.3mpa~2.0mpa、反应温度50℃~150℃、液化气进料体积空速5.0h-1
~20.0h-1
、氢气与液化气体积比10:1~100:1;优选的操作条件如下:反应压力为0.5~1.5mpa、反应温度80~120℃、进料体积空速10.0~17.0h-1
、氢气与液化气体积比20:1~50:1。
12.本发明方法中,所述的气固分离可采用本领域所用的可分离固体和气体的任何装置,比如旋风分离装置、沉降分离等。
13.本发明方法中,从反应器排出的待再生催化剂经气提后输送到再生器,在空气存在下烧炭再生,所得的再生催化剂返回流化床反应器循环使用。所述的再生器中的再生条件如下:再生压力为0.5mpa~1.5mpa,气剂体积比200:1~500:1,在400℃~500℃下恒温0.2~1.0小时,再生气为空气。
14.本发明方法中,所述的硫化氢醇胺吸收过程采用工业上常用、成熟的工艺。醇胺吸收塔内使用的醇胺液为一乙醇胺、二乙醇胺、二异丙醇胺中的至少一种。
15.本发明方法中,所述的微球形脱硫催化剂包括载体和活性金属组分;所述的载体为氧化锌和氧化铝复合球形载体,以载体质量为基准,氧化锌为20.0%~90.0%,优选为50.0%~70.0%;所述的活性金属组分为ni和mo;以催化剂的重量为基准,nio的含量为5.0wt%~20.0wt%,moo3含量为1.0wt%~8.0wt%,优选地,nio含量为8.0wt%~15.0wt%,moo3含量含量为2.0wt%~5.0wt%。所述的微球形催化剂直径为10~60
µ
m,其中直径为20~40
µ
m的微球占总颗粒物的60wt%~95wt%,优选80wt%~95wt%。
16.所述的微球形脱硫催化剂的制备方法,包括以下步骤:将氧化锌和氧化铝混合研
磨均匀,加入硝酸水溶液形成浆液,经喷雾干燥成型、焙烧后,制备出微球形载体;然后将含有ni和mo的浸渍液喷浸到上述载体中,干燥焙烧后,得到微球形脱硫催化剂。
17.其中,所述的浆液的固液质量比为0.250g/ml~0.650g/ml,优选地,为0.300g/ml~0.500g/ml。
18.其中,喷雾干燥成型过程中在喷雾干燥塔内进行,所述的喷雾干燥塔热空气入口温度为300~400℃、出口温度为120~200℃,经过旋风分离器得到的微球,在400~600℃下焙烧3.0~10.0小时。
19.其中,浸渍过程后的干燥条件为:150~200℃干燥4~6小时,焙烧条件为:400~500℃焙烧4~6小时。
20.与现有技术相比,本发明的方法具有以下特点;(1)与传统固定床液化气加氢脱硫醇方法(如cn104194833a)一般采用液化气先通过胺液抽提脱h2s,然后在硫化态mo-ni/γ-al2o3催化剂上加氢转化将液化气中的硫化物转化为高沸点的硫化物;加氢产物进入稳定塔,采用低硫碳五以上馏分进行精馏分离,得到超低硫液化气产物相比。本发明方法在一个反应器中、同时在一个催化剂的不同活性中心进行加氢脱硫和吸附h2s的反应,反应原理如下:有机硫化物加氢脱硫反应:来自原料的硫醇、硫醚、二硫化物及碳基硫化物转化为h2s:h2s吸附反应:包括主要来自液化气原料及加氢脱硫生成的h2s,h2s从液化气相分离、并吸附到固体催化剂上,得到脱硫液化气产物:(2)与传统固定床液化气加氢脱硫醇方法(如cn103965984a)一般采用380~830
µ
m(20~40目)大粒度催化剂,本发明采用特殊制备的微球形脱硫催化剂,该催化剂具有适宜的颗粒尺寸分布,其中20~40
µ
m占60wt%~95wt%,调控氧化锌在载体中的占比,配合适宜的催化剂活性组分,极大地提高了该微球形脱硫催化剂上的活性中心的分散度,提高了反应原料与活性中心的接触面积,加快了反应速率,同时该颗粒尺寸的催化剂更有利于提高液化气反应物及产物在催化剂内外扩散速率,可以实现在高空速下加氢脱硫,减少了停留时间,实现了低温下加氢脱硫、降低烯烃饱和率的效果;(3)本发明采用加氢反应产物后胺液吸收硫化氢,可以彻底脱除液化气中硫醇等硫化物后生成的硫化氢,达到深度脱硫的效果。
21.(4)与传统固定床选择性加氢脱硫方法相比,本发明采用流化床加氢工艺可以避
免因液化气原料中二烯烃造成的在催化剂上聚合结焦、以及反应器产生压降,影响催化剂使用寿命及装置长周期运行。
附图说明
22.图1为本发明的流程示意图。
23.图2为对比例1微球催化剂扫描电镜图(sem)。
24.图3为实施例1微球催化剂扫描电镜图(sem)。
25.图4为实施例2微球催化剂扫描电镜图(sem)。
26.图5为实施例3微球催化剂扫描电镜图(sem)。
27.图6为实施例4微球催化剂扫描电镜图(sem)。
具体实施方式
28.下面结合附图和实施例进一步说明本发明方法及效果,但并不因此限制本发明的保护范围。本发明中,比表面积和孔容是采用低温液氮吸附bet法测得。
29.根据图1中的流程示意图:液化气原料1与氢气2从底部进入提升管3,并被提升到流化床反应器4内,在一定条件下进行加氢脱硫反应;反应产物12从反应器4顶部排出进入胺液吸收塔13脱硫化氢,贫胺液5从胺液吸收塔顶进入,与反应产物逆流接触后富胺液6从胺液吸收塔底流出,得到脱硫产物14;积硫、积碳失活的催化剂进入待生催化剂收集器5,用氮气7将氢气置换净后进入闭锁料斗6,进入再生器9,用空气10进行烧硫、烧炭再生,排出含硫烟气11去回收硫磺;再生后催化剂进入再生后催化剂收集器8,经管线进入闭锁料斗6,经管线进入提升管3,循环使用。
30.特别是,提升管中主要发生h2对催化剂进行还原,反应如下:特别是,流化床反应器主要发生的硫醇、硫醚、二硫醚和羰基硫等在催化剂加氢脱硫,如下:特别是,再生器主要发生的烧碳、烧硫反应如下:
。
31.对比例1本实例制备13.0wt%nio-4.0wt%moo3/γ-al2o3微球催化剂。
32.称取含有83.0g干基al2o3粉,并研磨混合均匀,加入100ml浓度为10g/100ml的稀硝酸溶液和去离子水,配制成200ml的浆液。将上述浆液进行喷雾干燥,干燥塔进风温度为350℃,出风温度为150℃。经过旋风分离器得到的微球在550℃下焙烧5小时,制成微球载体。
33.称取上述微球载体50g放入喷浸罐中,开动旋转泵。在30分钟内将37.5ml含有6.5g nio的硝酸镍、2.0g moo3的四钼酸铵溶液喷淋到催化剂载体中。室温下晾干后,在120℃下干燥6小时,在500℃下焙烧4小时,制成微球催化剂,编号为r催化剂。该r催化剂物性列于表1中,图2为r催化剂扫描电镜图(sem)。
34.实施例1本实例制备13.0wt%nio-4.0wt%moo3/zno-al2o3微球催化剂。
35.称取含有41.5g干基zno和41.5g干基al2o3粉,并研磨混合均匀,加入100ml浓度为10g/100ml的稀硝酸溶液和去离子水,配制成200ml的浆液。将上述浆液进行喷雾干燥,干燥塔进风温度为350℃,出风温度为150℃。经过旋风分离器得到的微球在550℃下焙烧5小时,制成微球载体。
36.称取上述微球载体50g放入喷浸罐中,开动旋转泵。在30分钟内将35.0ml含有6.5g nio的硝酸镍、2.0g moo3的四钼酸铵溶液喷淋到催化剂载体中。室温下晾干后,在120℃下干燥6小时,在500℃下焙烧4小时,制成微球催化剂,编号为lds-1催化剂。该lds-1催化剂物性列于表1中,图3为lds-1催化剂扫描电镜图(sem)。
37.实施例2本实例制备10.0wt%nio-2.0wt%moo3/zno-al2o3微球催化剂。
38.称取含有61.6g干基zno和26.4g干基al2o3粉,并研磨混合均匀,加入100ml浓度为10g/100ml的稀硝酸溶液和去离子水,配制成200ml的浆液。将上述浆液进行喷雾干燥,干燥塔进风温度为370℃,出风温度为170℃。经过旋风分离器得到的微球在500℃下焙烧4小时,制成微球载体。
39.称取上述微球载体50g放入喷浸罐中,开动旋转泵。在30分钟内将35.0ml含有5.0g nio的碱式碳酸镍、1.0g moo3的四钼酸铵溶液喷淋到催化剂载体中。室温下晾干后,在120℃下干燥6小时,在480℃下焙烧5小时,制成微球催化剂,编号为lds-2催化剂。该lds-2催化剂物性列于表1中,图4为lds-2催化剂扫描电镜图(sem)。
40.实施例3本实例采取与实施例1的相同的条件方法制备13.0wt%nio-4.0wt%moo3/zno-al2o3微球催化剂。其中zno占催化剂的质量比例为10.0%。
41.编号为lds-3催化剂,该lds-3催化剂物性列于表1中,图5为lds-3催化剂扫描电镜图(sem)。结果表明,低zno占催化剂的质量比例,喷雾干燥成球颗粒成球性差,颗粒直径差
别较大,不均匀。
42.实施例4本实例采取与实施例1的相同的条件方法制备13.0wt%nio-4.0wt%moo3/zno-al2o3微球催化剂。主要区别在于喷雾干燥成球过程中zno和al2o3浆液固液比由实施例1的0.415g/ml降低为0.277g/ml。
43.制成微球催化剂,编号为lds-4催化剂。该lds-4催化剂物性列于表1中,图6为lds-4催化剂扫描电镜图(sem)。结果表明,低浓度浆液固液比喷雾干燥成球颗粒更小,特别是颗粒直径差别更大,不均匀。
44.对比例2本对比例考察对比例1催化剂的性能。
45.将10ml 新r催化剂装入图1流化床反应器内。首先,引入氢气升压,新r催化剂在氢气压力为0.8mpa、温度300℃、氢剂体积比20:1下条件预还原1h;然后,维持反应压力为0.8mpa、氢剂体积比20:1、降低温度至120℃、在体积空速8.0h-1
下进液化气原料进行脱硫反应;反应产物经胺液吸收塔脱硫化氢得到脱硫产物,采用二乙醇胺为吸收溶剂,二乙醇胺:反应产物体积比为3:1;失活(积硫、积碳)催化剂用氮气置换、经闭锁漏斗输送到再生器,在空气压力0.8mpa、气剂体积比300:1、480℃下,烧硫、烧碳0.5h再生;再生催化剂用氮气置换再经闭锁漏斗输送到流化床反应器进行循环脱硫反应;脱硫产物采样分析。
46.表2列出了液化气原料和脱硫产物分析结果。
47.实施例3本实施例考察实施1催化剂的性能。
48.将10ml 新lds-1催化剂装入图1流化床反应器内。首先,引入氢气升压,新lds-1催化剂在氢气压力为0.8mpa、温度300℃、氢剂体积比20:1下条件还原1h;然后维持反应压力为0.8mpa、氢剂体积比20:1、降低温度至120℃、在体积空速8.0h-1
下进液化气原料进行脱硫反应;反应产物经胺液吸收塔脱硫化氢得到脱硫产物,采用二乙醇胺为吸收溶剂,二乙醇胺:反应产物体积比为3:1;失活(积硫、积碳)催化剂用氮气置换、经闭锁漏斗输送到再生器,在空气压力0.8mpa、气剂体积比300:1、480℃下,烧硫、烧碳0.5h再生;再生催化剂用氮气置换再经闭锁漏斗输送到流化床反应器进行循环脱硫反应;脱硫产物采样分析。
49.表2列出了液化气原料和脱硫产物分析结果。
50.实施例4本实施例考察实施2催化剂的性能。
51.将10ml 新lds-2催化剂装入图1流化床反应器内。首先,引入氢气升压,新lds-2催化剂在氢气压力为1.2mpa、温度280℃、氢剂体积比20:1下条件还原1h;然后维持反应压力为1.2mpa、氢剂体积比20:1、降低温度至80℃、在体积空速16.0h-1
下进液化气原料进行脱硫反应;反应产物经胺液吸收塔脱硫化氢得到脱硫产物,采用二乙醇胺为吸收溶剂,二乙醇胺:反应产物体积比为3:1;失活(积硫、积碳)催化剂用氮气置换、经闭锁漏斗输送到再生器,在空气压力1.2mpa、气剂体积比300:1、460℃下,烧硫、烧碳0.5h再生;再生催化剂用氮气置换再经闭锁漏斗输送到流化床反应器进行循环脱硫反应;脱硫产物采样分析。
52.表2列出了液化气原料和脱硫产物分析结果。
53.实施例5
本实施例按照实施例3的条件,考察实施3中lds-3催化剂的性能。
54.表2列出了液化气原料和脱硫产物分析结果。
55.实施例6本实施例按照实施例3的条件,考察实施4中lds-4催化剂的性能。
56.表2列出了液化气原料和脱硫产物分析结果。
57.表1 催化剂性质表2 液化气原料及脱硫产物性质