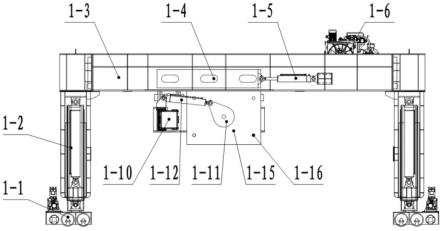
1.本实用新型属于盾构隧道中隔施工技术领域,具体涉及一种盾构隧道预制中隔墙安装机。
背景技术:2.截至2020年底,国内投入运营的铁路隧道16798座,总长19630km。铁路隧道衬砌结构通常采用混凝土现浇工艺施做,部分区段存在衬砌空洞、衬砌厚度不足等质量缺陷,经过运营期列车荷载作用,极易引发各类病害,给铁路行车带来极大安全隐患。隧道结构预制化可有效解决现浇工艺的质量缺陷,同时也是提高隧道修建速度、降低施工成本的重要途径。隧道结构预制拼装技术是隧道施工专业化、工厂化、机械化发展的方向之一。近些年,随着地下工程预制拼装技术的发展,大直径盾构隧道内部结构的预制拼装受到了越来越多的关注。
3.在施工的隧道中,隧道区间采用单洞双线布置,内部结构为全预制结构,共分为五部分,分别为下部结构(弧形件)、中隔墙、横向牛腿、两侧电缆槽、疏散平台。弧形件为底部支撑构件。中隔墙安装在弧形件上表面的中线位置,将隧道分为左线、右线通道。
4.由于隧道内施工空间狭小,预制件中隔墙尺寸大、自重大,且拼装精度和工效要求高,需要采用全自动、信息化拼装工艺。
技术实现要素:5.本实用新型的目的是提供一种盾构隧道预制中隔墙安装机,实现待安装中隔墙从抓举状态,行走至姿态调整工位,完成中隔墙空间姿态调整和就位拼装全过程的精确控制,提高中隔墙拼装的自动化、精准化水平,加快中隔墙拼装效率,降低施工风险。
6.本实用新型采用以下技术方案:一种盾构隧道预制中隔墙安装机,其特征在于,该中隔墙安装机用于设置于隧道内,且位于隧道内的以中线为分割线的左或右侧;其为空间矩形架体结构,其可在竖直方向上升或下降;设定横向为x向,纵向为y向,竖向为z向。
7.该中隔墙安装机包括:抓盘、作动装置、矩形架和智能控制系统,其中:
8.抓盘设置在靠近中线侧,为一板体,且竖直设置,其外侧朝向中线侧,外侧用于承接待安装中隔墙,且在初始时,待安装中隔墙处于纵向卧式状态;
9.作动装置设置于矩形架上,用于:推动抓盘纵向和横向移动,以带动待安装中隔墙纵向和横向移动,沿移动至待安装位置;推动抓盘在竖直面内旋转90
°
,将待安装中隔墙由卧式状态旋转至立式状态;用于推动抓盘转动,直至消除待安装中隔墙与已安装中隔墙在x向,y向和z向的转角偏差;
10.智能控制系统用于控制作动装置作动。
11.进一步地,该作动装置包括:
12.安装小车纵移滑块,设置于矩形架上方纵梁上,可沿矩形架纵向往复滑动;
13.纵移油缸,纵向设置,一端连接安装小车纵移滑块,另一端连接矩形架;纵移油缸
用于驱动安装小车纵移滑块纵向往复滑动;
14.安装小车横移外滑套,为一壳体,其横向设置,开口端朝向隧道中线侧;设置于安装小车纵移滑块下方,且两者通过摆动铰接相连接;
15.安装小车横移内滑套,同轴承插在安装小车横移外滑套内,且通过横移油缸与安装小车横移外滑套相连接,安装小车横移内滑套可在所安装小车横移外滑套内左右往复滑动;
16.翻转主轴,为一轴体,同轴设置于安装小车横移内滑套的靠近中线侧的外端部,且可在安装小车横移内滑套内转动;翻转主轴的外端与抓盘铰接连接;
17.横移油缸用于推动安装小车横移内滑套在横向上往复滑动,以推动抓盘在横向上往复移。
18.进一步地,该作动装置还包括:
19.翻转曲柄,为一端大一端小的板体,其小端与翻转主轴相连接,大端与抓盘内侧面的中心处铰接连接;
20.翻转油缸,纵向设置,其两端分别与安装小车横移外滑套和翻转曲柄相连接,用于推动翻转曲柄带动抓盘翻转;
21.扭转油缸,横向设置,两端分别与抓盘和小车横移内滑套相连接,用于驱动抓盘以铰接点为圆心转动。
22.进一步地,该矩形架包括:
23.四个竖直设置的伸缩支腿,设置于矩形的四个顶点处,可在竖直方向上升或下降;在各伸缩支腿的下端均设置有行走机构,用于在隧道内纵向移动;
24.架体纵向梁,为两根纵向走向的槽钢,左右间隔设置,位于左右侧的伸缩支腿顶部,槽钢的开口侧朝向对侧;槽钢的开口内用作安装小车纵移滑块的滑动轨道。
25.进一步地,在矩形架的纵梁的上方和下方均设置有一套中隔墙姿态视觉识别系统,用于获取待安装中隔墙相对已安装中隔墙的空间位置姿态信息。
26.进一步地,该中隔墙安装机还包括:
27.定位激光传感器,为两套,各一套安装于位于隧道5中线一侧的两个伸缩支腿的下方,用于探测x向距离;
28.顶升测距激光传感器,为两套,分别设置在中隔墙安装机1前端、后端的伸缩支腿上,通过检测伸缩支腿竖直方向的位移量;
29.底部间隙激光传感器,为两套,分别布置在中隔墙安装机靠近隧道中线一侧的行走机构箱体上,通过向待安装中隔墙底部激光测距;
30.定位激光传感器、顶升测距激光传感器和底部间隙激光传感器均与智能控制系统相连接。
31.本实用新型的有益效果是:在采用作动装置对待安装中隔墙在x向、y向和 z向进行精准调整,实现了盾构隧道受限空间内中隔墙构件全过程自动精准拼装,可有效提高中隔墙拼装精度和效率,减少人工干预,降低施工风险。
附图说明
32.图1是本实用新型盾构隧道中隔墙拼装示意图;
33.图2是一种中隔墙安装机纵向面的结构图;
34.图3是本实用新型实施所需的一种中隔墙安装机横向面的结构图;
35.图4是本实用新型实施所需的中隔墙安装机测控传感器布置图;
36.图5是待安装中隔墙托举抓取姿态及横移示意图;
37.图6是待安装中隔墙托举抓取姿态的横向视图;
38.图7是待安装中隔墙顶升示意图;
39.图8是待安装中隔墙翻转示意图;
40.图9是待安装中隔墙纵向移动示意图;
41.图10是待安装中隔墙转角偏差识别示意图;
42.图11是待安装中隔墙绕y轴转角偏差精调示意图;
43.图12是待安装中隔墙绕z轴转角偏差精调示意图;
44.图13是待安装中隔墙绕x轴转角偏差精调示意图;
45.图14是待安装中隔墙z向位移精调示意图;
46.图15是待安装中隔墙y向位移精调示意图;
47.图16是待安装中隔墙x向位移精调示意图;
48.其中:1.中隔墙安装机;2.中隔墙;2-1.待安装中隔墙;2-2.已安装中隔墙; 2-3.中隔墙抓取孔;3.汽车运载平台;4.弧形件;5.隧道;
49.1-1.行走机构;1-2.伸缩支腿;1-3.架体纵向梁;1-4.安装小车纵移滑块;1-5. 纵移油缸;1-6.智能控制系统;1-7.摆动铰接;1-8.摆动油缸;1-9.安装小车横移外滑套;1-10.安装小车横移内滑套;1-11.翻转曲柄;1-12.翻转油缸;1-13.翻转主轴;1-14.扭转油缸;1-15.抓盘;1-16.托举销轴;1-17.横移油缸;1-18.定位激光传感器;1-19.顶升测距激光传感器;1-20.中隔墙姿态视觉识别系统;1-21.底部间隙激光传感器。
具体实施方式
50.下面结合附图和具体实施方式对本实用新型进行详细说明。
51.本实用新型一种盾构隧道预制中隔墙安装机,如图1、2和3所示,该中隔墙安装机1用于设置于隧道内,且位于隧道5内的以中线为分割线的左或右侧;其为空间矩形架体结构,其可在竖直方向上升或下降;设定横向为x向,纵向为 y向,竖向为z向。
52.该中隔墙安装机1包括抓盘1-15、作动装置、矩形架和智能控制系统1-6,其中:抓盘1-15设置在靠近中线侧,为一板体,且竖直设置,其外侧朝向中线侧,外侧用于承接待安装中隔墙2-1,其在初始时,待安装中隔墙2-1处于纵向卧式状态。
53.作动装置设置于矩形架上,用于:推动抓盘1-15纵向和横向移动,以带动待安装中隔墙2-1纵向和横向移动,沿移动至待安装位置;推动抓盘1-15在竖直面内旋转90
°
,将待安装中隔墙2-1由卧式状态旋转至立式状态;用于推动抓盘1-15 转动,直至消除待安装中隔墙2-1与已安装中隔墙2-2在x向,y向和z向的转角偏差。
54.智能控制系统1-6用于控制作动装置作动。
55.上述作动装置包括:安装小车纵移滑块1-4,设置于矩形架上方纵梁上,可沿矩形架纵向往复滑动;
56.纵移油缸1-5,纵向设置,一端连接安装小车纵移滑块1-4,另一端连接矩形架;纵
移油缸1-5用于驱动安装小车纵移滑块1-4纵向往复滑动;
57.安装小车横移外滑套1-9,为一壳体,其横向设置,开口端朝向隧道5中线侧;设置于安装小车纵移滑块1-4下方,且两者通过摆动铰接1-7相连接;摆动油缸1-8竖直设置,其两端分别与安装小车纵移滑块1-4和安装小车横移外滑套 1-9相连接,且摆动油缸1-8位于靠近安装小车横移外滑套1-9的末端,摆动油缸 1-8用于推动安装小车横移外滑套1-9的末端向下运动,以带动前端的抓盘1-15 绕y轴摆动。
58.安装小车横移内滑套1-10,同轴承插在安装小车横移外滑套1-9内,且通过横移油缸1-17与安装小车横移外滑套1-9相连接,安装小车横移内滑套1-10可在所安装小车横移外滑套1-9内左右往复滑动;
59.翻转主轴1-13,为一轴体,同轴设置于安装小车横移内滑套1-10的靠近中线侧的外端部,且可在安装小车横移内滑套1-10内转动;翻转主轴1-13的外端与抓盘1-15铰接连接;
60.横移油缸1-17用于推动安装小车横移内滑套1-10在横向上往复滑动,以推动抓盘1-15在横向上往复移。
61.作动装置还包括:
62.翻转曲柄1-11,为一端大一端小的板体,其小端与翻转主轴1-13相连接,大端与抓盘1-15内侧面的中心处铰接连接;
63.翻转油缸1-12,纵向设置,其两端分别与安装小车横移外滑套1-9和翻转曲柄1-11相连接,用于推动翻转曲柄1-11带动抓盘1-15翻转;
64.扭转油缸1-14,横向设置,两端分别与抓盘1-15和小车横移内滑套1-10相连接,用于驱动抓盘1-15以铰接点为圆心转动。
65.矩形架包括:
66.四个竖直设置的伸缩支腿1-2,设置于矩形的四个顶点处,可在竖直方向上升或下降;在各伸缩支腿1-2的下端均设置有行走机构1-1,用于在隧道内纵向移动;
67.架体纵向梁1-3,为两根纵向走向的槽钢,左右间隔设置,位于左右侧的伸缩支腿1-2顶部,槽钢的开口侧朝向对侧;槽钢的开口内用作安装小车纵移滑块 1-4的滑动轨道。
68.矩形架纵梁的上方和下方各设置有一套中隔墙姿态视觉识别系统1-20。
69.如图4、5、6和7所示,该中隔墙安装机1还包括:
70.定位激光传感器1-18,为两套,各一套安装于位于隧道5中线一侧的两个伸缩支腿1-2的下方,用于探测x向距离;识别已安装中隔墙2-2的边沿,从而确定中隔墙安装机1的纵向(y向)位置。
71.顶升测距激光传感器1-19,为两套,分别设置在中隔墙安装机1前端、后端的伸缩支腿1-2上,通过检测伸缩支腿1-2竖直方向的位移量,判断中隔墙安装机1的顶升距离。
72.底部间隙激光传感器1-21,为两套,分别布置在中隔墙安装机1靠近隧道5 中线一侧的行走机构1-1箱体上,通过向待安装中隔墙2-1底部激光测距,感知设定范围内有无障碍物可确定待安装中隔墙2-1与地面(弧形件4上表面)之间的安全距离。所述底部间隙激光传感器1-21主要用于探测待安装中隔墙2-1翻转90
°
过程中距离地面的距离,可防止两者碰撞。
73.定位激光传感器1-18、顶升测距激光传感器1-19和底部间隙激光传感器1-21 均
与智能控制系统1-6相连接。
74.中隔墙姿态视觉识别系统1-20用于获取待安装中隔墙2-1相对已安装中隔墙 2-2的空间位置姿态信息。两套所述中隔墙姿态视觉识别系统1-20通过两套独立的机械手分别设置在中隔墙安装机1的上方和下方,可用于探测待安装中隔墙 2-1、已安装中隔墙2-2的空间姿态信息。采用双目识别系统识别待安装中隔墙 2-1与已安装中隔墙2-2的表面三维信息,从而获取两者的空间姿态、结构边沿位置,通过对比分析,可得出待安装中隔墙2-1与已安装中隔墙2-2之间的空间位置和姿态偏差,为智能控制系统1-6提供操控参数。
75.上述的一种盾构隧道预制中隔墙安装机用于中隔墙空间姿态自动定位控制的方法,包括以下步骤:
76.步骤a、待安装中隔墙2-1翻转,具体为:
77.步骤a.1、待安装中隔墙2-1横移:待安装中隔墙2-1固定于抓盘1-15上,且待安装中隔墙2-1处于纵向卧式状态,横移油缸1-17在横向上驱动抓盘1-15,抓盘1-15向隧道5中线处移动,直至到达设定位置,减小待安装中隔墙2-1自重产生的力矩。
78.步骤a.2、待安装中隔墙2-1顶升:启动中隔墙安装机1的伸缩支腿1-2,伸缩支腿1-2上升,带动待安装中隔墙2-1顶升,为待安装中隔墙2-1翻转预留足够的顶部和底部空间。顶升测距激光传感器1-19测量顶升距离,待安装中隔墙 2-1顶升到位后,并传输至智能控制系统1-6,且在顶升到位后,停止顶升;
79.步骤a.3、待安装中隔墙2-1旋转障碍检测:底部间隙激光传感器1-21探测待安装中隔墙2-1底部翻转范围内是否有障碍物,如果检测到有障碍物,则智能控制系统1-6发出警报,并停止动作;如果未检测到障碍物,执行下一步;如图 7所示。
80.步骤b、待安装中隔墙2-1翻转90
°
,如图8所示,具体为:
81.步骤b.1、在待安装中隔墙2-1翻转90
°
的过程中,底部间隙激光传感器1-21 检测待安装中隔墙2-1翻转范围下方的空间距离,如果下方的空间距离不满足待安装中隔墙2-1翻转空间需求,则智能控制系统1-6发出报警信息,并停止翻转动作,同时驱动伸缩支腿1-2,使待安装中隔墙2-1顶升,至满足翻转的空间需求,并执行下步;如果下方的空间距离满足待安装中隔墙2-1翻转空间需求,执行下步;
82.步骤b.2、翻转油缸1-12驱动翻转主轴1-13转动,带动抓盘1-15由纵向设置状态旋转至竖直设置状态,以同步带动待安装中隔墙2-1由纵向卧式状态旋转至立式状态;
83.步骤c、待安装中隔墙2-1姿态调整,如图9~16所示,具体如下:
84.步骤c.1、待安装中隔墙2-1纵向移动:启动中隔墙安装机1的行走机构1-1 纵向行走,带动待安装中隔墙2-1向已安装中隔墙2-2方向移动,且定位激光传感器1-18横向探测已安装中隔墙2-2的边沿,当检测到已安装中隔墙2-2的边沿时,行走机构1-1继续行走一设定距离后停止;上述移动距离应确保待安装中隔墙2-1与已安装中隔墙2-2较为接近,满足两套中隔墙姿态视觉识别系统1-20工作距离要求,同时又保留足够的姿态调整空间;
85.步骤c.2、采用两套中隔墙姿态视觉识别系统1-20分别测量待安装中隔墙2-1 与已安装中隔墙2-2纵向相邻边沿的平行度,通过智能控制系统1-6获取待安装中隔墙2-1与已安装中隔墙2-2的绕x轴的转角偏差;根据上述待安装中隔墙2-1 与已安装中隔墙2-2的绕x轴的转角偏差,智能控制系统1-6给出翻转油缸1-12 驱动控制指令,使待安装中隔墙2-1绕x轴摆动,消除绕x轴的转角偏差;
86.步骤c.3、采用两套中隔墙姿态视觉识别系统1-20分别测量待安装中隔墙2-1 与已安装中隔墙2-2的表面信息,通过智能控制系统1-6获取待安装中隔墙2-1 与已安装中隔墙2-2的绕y轴的转角偏差,智能控制系统1-6给出摆动油缸1-8 驱动控制指令,使待安装中隔墙2-1绕y轴摆动,消除绕y轴的转角偏差;
87.步骤c.4、采用两套中隔墙姿态视觉识别系统1-20分别测量待安装中隔墙2-1 与已安装中隔墙2-2的表面信息,通过智能控制系统1-6获取待安装中隔墙2-1 与已安装中隔墙2-2的绕z轴的转角偏差,智能控制系统1-6给出扭转油缸1-14 驱动控制指令,使待安装中隔墙2-1绕z轴摆动,消除绕z轴的转角偏差;
88.步骤c.5、采用两套中隔墙姿态视觉识别系统1-20,分别按照c.1、c.2、c.3 步骤,精确复测待安装中隔墙2-1与已安装中隔墙2-2在绕x轴、y轴、z轴方向的转角偏差,如果上述转角偏差不满足精度控制要求,则重新执行步骤c.1、 c.2、或c.3,直至满足精度控制要求,进行下一步操作;
89.上述步骤c.1、c.2、c.3可调换顺序。
90.步骤d、待安装中隔墙2-1位置精调,具体如下:
91.步骤d.1、待安装中隔墙2-1下移到位:顶升测距激光传感器1-19识别中隔墙安装机1伸缩支腿1-2顶升位置,得到待安装中隔墙2-1与地面的距离,智能控制系统1-6控制伸缩支腿1-2下降,使待安装中隔墙2-1精准下降到设计安装位置;
92.步骤d.2、待安装中隔墙2-1纵移到位:两套中隔墙姿态视觉识别系统1-20 分别测量待安装中隔墙2-1与已安装中隔墙2-2相邻边沿的距离,获得待安装中隔墙2-1纵向位移参数,智能控制系统1-6控制纵移油缸1-5纵向伸缩,带动待安装中隔墙2-1纵向移动,将待安装中隔墙2-1纵向精准移动到设计安装位置;
93.步骤d.3、待安装中隔墙2-1横移到位:两套中隔墙姿态视觉识别系统1-20 分别测量待安装中隔墙2-1与已安装中隔墙2-2横向表面距离,获得待安装中隔墙2-1横向位移参数,智能控制系统1-6控制横移油缸1-17横向伸缩,带动待安装中隔墙2-1移动,将待安装中隔墙2-1横向移动到设计安装位置。
94.在步骤d后还包括步骤e:
95.步骤e、中隔墙安装机1复位,具体包括:
96.步骤e.1、使用临时垫块、螺栓,将待安装中隔墙2-1与地面、相邻已安装中隔墙2-2固定;
97.步骤e.2、横移油缸1-17收缩,缩回托举销轴1-16,使中隔墙安装机1脱离待安装中隔墙2-1;
98.步骤e.3、中隔墙安装机1复位,各液压油缸、智能控制系统1-6恢复到初始状态,等待下一次拼装。
99.至此,一块待安装中隔墙2-1完成空间姿态高精度定位,完成由卧式抓举状态到立式精准拼装状态。
100.在上述安装过程中,实现了重型、大尺寸中隔墙构件在隧道空间内六自由度姿态高精度定位,全过程实现了信息化、自动化、无人化拼装,显著降低施工风险,保证了待安装中隔墙的拼装精度和工效。