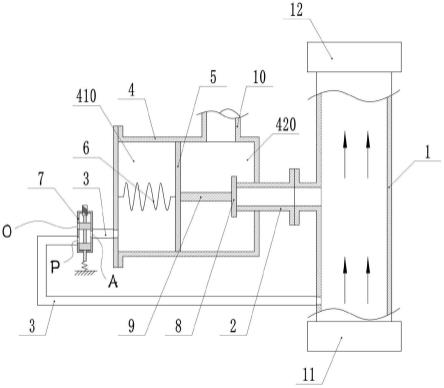
1.本实用新型属于风机排空系统技术领域,具体涉及一种应用于鼓风机的气动放空系统。
背景技术:2.鼓风机是广泛应用于各个工业领域的一类通用设备,无论是螺杆式鼓风机还是离心式鼓风机,都会遇到开机加载时因为背压太高而转速不够的问题,这将造成加载阶段主机喘振或者驱动电机扭矩过大的情况;或者遇到在设备正常运行过程中后端排气压力突然上升(例如后端阀门开度突然变小或管网堵塞等情况发生),造成主机喘振、驱动电机超功率或者主机咬死等情况。为了避免上述有害设备安全的情况出现,当开机加载或者运行超压时,需要在排气管路上设置放空系统,从而泄放管路中的气体压力。
3.目前,通常是在排气管路上连通排空管,排空管上安装放空阀,放空阀的阀盖上开设两个气孔,一个作为进气孔,另一个作为出气孔,两个气孔各连接安装一个二位二通电磁阀,通过plc板指令控制上述两个二位二通电磁阀的开闭,以实现放空阀的开闭功能。但是这样的问题是,放空阀的阀盖上需要加工两个气孔,加工用时较长,而且,使用两个二位二通电磁阀的成本较高,出现故障的概率也较高。
技术实现要素:4.本实用新型意在提供一种应用于鼓风机的气动放空系统,以解决放空阀使用两个电磁阀时存在成本较高、故障率较高的问题。
5.为了达到上述目的,本实用新型的方案为:一种应用于鼓风机的气动放空系统,包括与主排气管连通的排空管和旁支管,排空管上安装有放空阀,所述放空阀包括阀体,阀体内水平滑动连接有左挡板,所述左挡板的面积大于排空管的径向截面面积,左挡板将阀体分隔为独立的左腔室和右腔室,所述左腔室内设有弹性件,弹性件的一端与左腔室的侧壁相连,弹性件的另一端与左挡板相连,所述旁支管远离主排气管的一端与左腔室连通,旁支管上安装有二位三通电磁阀;所述右腔室与排空管连通,右腔室内设有用于封堵排空管的右挡板,右挡板通过连杆与左挡板相连,右腔室连通有泄气管。
6.本方案的工作原理及有益效果在于:本方案中,采用一个两位三通电磁阀即可控制气路走向,即控制左腔室是否通过旁支管与主排气管连通,从而实现对左腔室内压的调整,进而使得左挡板受到的压力发生改变,带动右挡板移动,实现放空阀的打开/关闭,如此,仅需在阀体上开设一个气孔即可,减少加工工序,降低加工成本,同时降低放空系统的故障率。
7.可选地,所述弹性件为弹簧或弹性膜片。
8.本方案中,弹簧或弹性膜片均具有良好的拉伸/压缩形变性。
9.可选地,所述泄气管远离右腔室的一端安装有消音器。
10.本方案中,放空阀放空时,高速气流会产生噪音,因此,利用消音器降低放空时产
生的噪音。
11.可选地,所述消音器包括圆筒,圆筒内设有第一导流筒和第二导流筒,第一导流筒和第二导流筒的侧壁开设有若干通孔,第二导流筒的两端封口,第二导流筒内形成第一消音室,第一导流筒和圆筒之间形成第二消音室,第二消音室的两端封口,所述第一消音室和第二消音室内均填充有消音材料;所述第一导流筒和第二导流筒之间形成环形气路通道,所述环形气路通道沿气流的流向具有向外倾斜段和渐扩段。
12.本方案中,改进消音器结构,高速气流在环形气路通道内流动,在向外倾斜段中,内外圆直径之差保持不变,通流面积增大,气体流速降低;在渐扩段内,内外圆直径之差逐渐增大,通流面积增大程度变大,气体流速进一步降低,从而使得高速气流的速度显著降低,进而降低噪音。并且,本方案将传统消音器的通流截面由圆形改为环形,在保证通流面积不变甚至增大的前提下,通流截面处的宽度d由传统的通流截面圆直径变成环形截面的内外圆半径差,d值减小,则l值也减小,因此消音器总长度减小,后期所需的轴向安装空间更小,制造成本得以降低。
13.可选地,所述第二导流筒的底端设有锥形分流筒,所述锥形分流筒的锥角朝向远离第二导流筒的一侧。
14.本方案中,锥形分流筒能够分流由泄气管进入圆筒内的高速气流,避免高速气流直接撞上第二导流筒的封口端,即避免90
°
流向突变,以便气流可以在圆筒内平顺流动,降低气流在圆筒入口处的压损。
15.可选地,所述第一导流筒内设有与所述泄气管连接的连接筒,所述连接筒固定于第一导流筒内,连接筒的周壁上开设有若干过气孔,所述锥形分流筒位于所述连接筒内。
16.本方案中,高速气流进入连接筒内后,再经过气孔流入连接筒与第一导流筒之间的空间内,避免高速气流直接进入第一导流筒内产生突扩,从而进一步降低气流在圆筒入口端的压损。
17.可选地,所述过气孔为条形孔,且过气孔为斜孔,斜孔的进气口低于斜孔的出气口。
18.本方案中,过气孔为斜孔时,能够导向气流的流向,以便气流能够更平顺地流入环形气路通道的向外倾斜段内。
19.可选地,所述向外倾斜段与竖向面之间的夹角为12
°
~26
°
。
20.本方案中,向外倾斜段与竖向面之间的夹角为12
°
~26
°
时,能够有效避免向外倾斜段的倾斜度过大或者过小。当向外倾斜段与竖向面之间的夹角小于12
°
时,向外倾斜段的通流面积虽然在增大,但增大的程度过低,气体流速的降低程度很低;当向外倾斜段与竖向面之间的夹角大于26
°
时,向外倾斜段的通流面积虽然增大的程度较高,但环形气路通道的外圆直径过大,导致消音器的直径过大,不利于安装。
21.可选地,所述第二导流筒的顶端采用带孔球形板封口。
22.本方案中,第二导流筒的顶端采用带孔球形板封口,相较于采用带孔平直板封口,前者能够减小尾迹涡流,从而降低气流与环境大气的摩擦。
23.可选地,所述第一消音室和第二消音室的内侧壁上设有不锈钢网。
24.本方案中,不锈钢网用于防止第一消音室和第二消音室内的消音材料经通孔被高速气流卷走。
附图说明
25.图1为本实用新型实施例一中应用于鼓风机的气动放空系统的剖视图(箭头表示气流流向);
26.图2为本实用新型实施例一中放空阀打开时的剖视图(箭头表示气流流向);
27.图3为本实用新型实施例二中应用于鼓风机的气动放空系统的剖视图;
28.图4为本实用新型实施例二中消音器的轴向局剖图(箭头表示气流流向);
29.图5为图4中a的放大示意图;
30.图6为本实用新型实施例二中连接筒的立体图(带锥形分流筒);
31.图7为本实用新型实施例三中连接筒的轴向剖视图。
具体实施方式
32.下面通过具体实施方式进一步详细说明:
33.说明书附图中的标记包括:主排气管1、排空管2、旁支管3、阀体4、左腔室410、右腔室420、左挡板5、弹性件6、二位三通电磁阀7、右挡板8、连杆9、泄气管10、产气端11、用气端12、圆筒13、第一导流筒14、第二导流筒15、连接筒16、吊装板17、吊装孔18、通孔19、带孔球形板20、平直板21、消音材料22、不锈钢网23、锥形分流筒24、隔板25、环形气路通道26、向外倾斜段261、渐扩段262、过气孔27。
34.实施例一
35.本实施例基本如图1所示:一种应用于鼓风机的气动放空系统,包括与主排气管1连通的排空管2和旁支管3,排空管2上安装有放空阀,放空阀包括阀体4,阀体4内水平滑动连接有左挡板5,左挡板5的面积大于排空管2的径向截面面积,左挡板5将阀体4分隔为独立的左腔室410和右腔室420,左腔室410内设有弹性件6,弹性件6的左端与左腔室410的左侧壁相连,弹性件6的右端与左挡板5相连,弹性件6为弹簧或弹性膜片,本实施例中,弹性件6为弹簧。
36.旁支管3远离主排气管1的一端与左腔室410连通,具体地,在左腔室410的左侧壁上开孔,旁支管3通过该孔与左腔室410连通(需要说明的是,左腔室410的左侧壁即为放空阀的阀盖),旁支管3上安装有二位三通电磁阀7。
37.右腔室420与排空管2远离主排气管1的一端连通,右腔室420内设有用于封堵排空管2的右挡板8,右挡板8通过连杆9与左挡板5相连,且右挡板8的面积小于左挡板5的面积,右腔室420连通有泄气管10。
38.另外,主排气管1的底端连接鼓风机的产气端11,主排气管1的顶端连接鼓风机的用气端12,即,主排气管1内压缩气体的流向为从下往上。旁支管3与主排气管1的连通处位于排空管2与主排气管1的连通处和产气端11之间。
39.具体使用时,在鼓风机运行过程中,向用气端12鼓风出现喘振或超载时,plc控制二位三通电磁阀7失电,此时二位三通电磁阀7的p口关闭(p口通过旁支管3与主排气管1连接),a口与o口连通(a口通过旁支管3与左腔室410连接,o口与外界大气连接),于是,左腔室410与外界大气连通,左腔室410内的表压为0;同时,主排气管1内的压缩气体的压强p2(表压)作用在右挡板8的右表面上,从而推动右挡板8克服摩擦力以及弹性件6的弹力向左移动,右挡板8不再封堵排空管2,放空阀打开,如图2所示,主排气管1内的压缩气体经排放管
进入右腔室420内,再经泄气管10泄放,从而降低主排气管1内的气压。
40.当鼓风机正常运行向用气端12供气时,plc控制二位三通电磁阀7得电,此时二位三通电磁阀7的o口关闭,p口与a口连通,即旁支管3连通了主排气管1和左腔室410,左腔室410内的气压与主排气管1内的气压相同,即左腔室410内的气压为p2,此时,由于左挡板5的右侧面面积大于排空管2的径向截面面积,也大于右挡板8的右侧面面积,因此,左挡板5受到的、向右的压力大于右挡板8受到的、向左的压力,且弹性件6对左挡板5还施加向右的推力,如此,左挡板5、连杆9和右挡板8向右移动,右挡板8重新封堵排空管2,放空阀关闭,主排气管1向用气端12正常供气。
41.综上所述,本实施例中,只需要一个二位三通电磁阀7就可以控制气路走向,并且只需在阀盖上开设一个气孔即可,降低系统成本和故障率,减少阀体4加工工序,降低阀体4加工成本,实现降本增效的目的。
42.实施例二
43.本实施例与实施例一的区别之处在于:如图3所示,本实施例中的气动放空系统还包括消音器,消音器安装在泄气管10远离右腔室420的一端。结合图4和图5所示,消音器包括圆筒13,圆筒13内设有第一导流筒14、第二导流筒15和用于与泄气管10相连的连接筒16。圆筒13的顶端焊接有吊装板17,吊装板17的数量为两个,且两个吊装板17相对设置,吊装板17上开设有吊装孔18。消音器的整体重量较重,因此,本实施例中,通过吊装板17和吊装孔18即可将消音器吊装至安装位点,避免工人手动搬运、安装,降低工人劳累程度。
44.第一导流筒14和第二导流筒15的侧壁开设有若干通孔19,第二导流筒15的两端封口,且第二导流筒15的顶端采用带孔球形板20封口,第二导流筒15的底端采用平直板21封口。第二导流筒15内形成第一消音室,第一导流筒14和圆筒13之间形成第二消音室,第二消音室的两端封口,且第二消音室的两端均采用平直板21封口,第一消音室和第二消音室内均填充有消音材料22,消音材料22为离心玻璃棉或不锈钢纤维棉。第一消音室和第二消音室的内侧壁上设有不锈钢网23,用于防止消音材料22经通孔19被高速气流卷走。
45.第二导流筒15的底端设有锥形分流筒24,锥形分流筒24的锥角朝下,锥形分流筒24位于连接筒16内。本实施例中,锥形分流筒24焊接在第二导流筒15的底端。第二导流筒15内焊接有隔板25,利用隔板25支撑消音材料22。
46.第一导流筒14和第二导流筒15之间形成环形气路通道26,环形气路通道26沿气流的流向具有向外倾斜段261和渐扩段262,向外倾斜段261与竖向面之间的夹角θ为12
°
~26
°
,并且,向外倾斜段261顶端的外圆直径大于向外倾斜段261底端的外圆直径,向外倾斜段261的内外圆直径之差处处相等。本实施例中,向外倾斜段261与竖向面之间的夹角θ为15
°
。
47.连接筒16固定于第一导流筒14内,连接筒16可以与第二导流筒15的底端焊接,也可以与第一导流筒14的底端焊接。结合图6所示,连接筒16的周壁上开设有若干过气孔27,过气孔27为条形孔。另外,连接筒16与泄气管10的连接可以采用螺栓连接、卡扣连接、螺纹连接等能够将连接筒16与泄气管10密封连接在一起的方式。
48.目前,圆筒13式消音器一般采用圆筒13作为主体,在圆筒13内侧壁上固定消音材料22,中部留出气流通道,如此,气流通道的直径与泄气管10的内径基本一致,导致气流流至消音器出口时,流速基本不变,消音器出口处高速气流与环境大气摩擦依旧会产生较大
的气动噪音。另外,为了满足消音器气流通道截面宽度d和消音段长度l有效消音比例(l/d>6),消音器的长度通常都比较长,需要的轴向安装空间较大,同时制造成本也较高。
49.而本实施例中的消音器,利用连接筒16和锥形分流筒24分流高速气流,避免高速气流在进入圆筒13内后产生突扩以及90
°
流向突变,有效减小压损,从而降低放空阀出口处的背压,提高放空系统性能。并且,利用第一导流筒14和第二导流筒15,在圆筒13内形成了第一消音室和第二消音室以及环形气路通道26,中低频噪音声波发生反射和干涉,降低了中低频噪音,并通过消音材料22吸收声能,降低了中高频噪音。而环形气路通道26的通流面积逐渐增大,气体流速降低,从而降低了圆筒13出口处的气动噪音,即,本实施例的消音器兼具集合阻抗式消音特性和环形渐扩式降速效果。并且,环形气路通道26的设计,将传统消音器的通流截面由圆形改为环形,在保证通流面积不变甚至增大的前提下,通流截面宽度d由传统的通流截面圆直径变成了环形截面的内外圆半径差,d值减小,l值也可减小,从而减小消音器的总长,后期所需的轴向安装空间更小,降低了制造成本。
50.具体地,高速气流经泄气管10进入连接筒16内,从而避免高速气流直接进入第一导流筒14内,即避免了突扩。进入连接筒16内的高速气流在锥形分流筒24的作用下,经过气孔27流入连接筒16与第一导向筒之间的空间内,继而流入环形气路通道26的向外倾斜段261。此过程中,锥形分流筒24的设计避免了高速气流直接与第二导流筒15的底端相撞而产生90
°
流向突变。
51.高速气流在环形气路通道26内流动的过程中,向外倾斜段261的内外圆直径之差保持不变,通流面积增大,因此气体流速降低,而渐扩段262的内外圆直径之差逐渐增大,通流面积增大程度变大,气体流速进一步降低。如此,高速气流从连接筒16流入直至从渐扩段262顶端流出,气流的通流直径可扩大约3~4倍,通流面积可扩大9~16倍,因此,本实施例中,经渐扩段262顶端流出的气体流速约为流入连接筒16时的气体流速的1/9~1/16,气体流速显著降低,圆筒13出口处的气动噪音得以显著降低。
52.此外,高速气流产生的噪音是中低频和高频的混合噪音,高速气流经在圆筒13内流动的过程中,中低频噪音的声波在圆筒13内的各种壁(包括连接筒16壁、第一导流筒14壁、第二导流筒15壁、圆筒13壁等)上反射、相互干涉,降低了中低频声波能量,从而降低中低频噪音;并且,第一消音室和第二消音室内的消音材料22能够通过通孔19吸收声能,对中高频噪音有明显的吸音降噪作用。
53.因此,本实施例中,对中、低、高频噪音都具有有效的降噪作用,并显著降低了气体流速,从而有效降低消音器出口处的气动噪音。此外,本实施例还减小了消音器总长,所需的轴向安装空间更小,降低了制造成本。另外,本实施例使得气体流经消音器的压损更小,降低了放空阀出口的背压,提高了放空系统的性能。
54.实施例三
55.本实施例与实施例二的区别之处在于:如图7所示,过气孔27为斜孔,斜孔的进气口低于斜孔的出气口。本实施例中,过气孔27为斜孔时,能够导向气体的流向,使得连接筒16内的气体流出时向上流出,从而更好地流入环形气路通道26。
56.以上所述的仅是本实用新型的实施例,方案中公知的具体结构及特性等常识在此未作过多描述。应当指出,对于本领域的技术人员来说,在不脱离本实用新型结构的前提下,还可以作出若干变形和改进,这些也应该视为本实用新型的保护范围,这些都不会影响
本实用新型实施的效果和本实用新型的实用性。说明书中的具体实施方式等记载可以用于解释权利要求的内容。