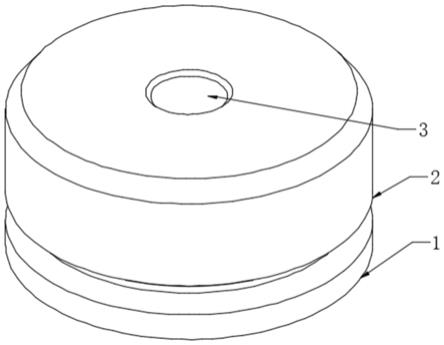
1.本发明涉及缓冲部件技术领域,具体涉及一种合成聚氨酯缓冲器及其加工工艺。
背景技术:2.缓冲器在电梯、起重机等行业有着重要作用,其极大程度减小设备的损伤,使得设备可以长期安全运行。现有的电梯行业中一般采用质轻、耐腐蚀、耐老化、电绝缘及防爆性能良好的聚氨酯缓冲器或者机械油压式缓冲器。
3.2020年12月14日国家市场监督管理总局、国家标准化管理委员会发布了新的电梯制造与安装安全规范gb/t 7588
‑
2020代替gb7588
‑
2003,于2022年7月1日实施,对比新国标的非线性缓冲器型式试验要求部分与欧洲标准en81
‑
20/50的非线性缓冲器要求部分,要求基本一致,这意味着新国标对聚氨酯缓冲器的性能提出了更高的要求。需要升级聚氨酯缓冲器的配方以满足更高性能的要求。
4.目前,用于速度为1.0m/s以下电梯的缓冲器采用的是普通的微孔型聚氨酯缓冲器,大于1.0m/s的电梯采用的都是液压缓冲器。普通的微孔型聚氨酯缓冲器,是由一块4~8mm厚的钢板做底板与微孔型聚氨酯弹性体通过一次成型技术并借助于胶黏剂实现一体化的,其反弹速度比较大,不能用于1.0m/s以上的电梯。液压缓冲器是由缸体、活塞、芯棒、密封圈、复位弹簧、撞头、复位开关以及符合规定要求的液压油等组成,当轿厢下梁缓冲板撞击活塞时,活塞迫使缸体内的液压油经过芯棒与活塞间的圆环形阻尼孔流入储油室中。
5.因为环形孔的阻尼作用,一方面使流体发生湍流,产生热量消耗轿厢一部分动能,另一方面延缓轿厢的冲击力,产生缓冲作用。复位弹簧的作用是使活塞完成缓冲作用后复位,同时也起一定的缓冲加速作用。复位开关与安全电路相连,用来验证缓冲器恢复到位。液压缓冲器虽然在速度和承载上都很理想,但成本高,维保麻烦,存在安全隐患,主要体现在:
①
漏油现象比较严重而且普遍,致使油量变化;
②
因油质的时效变化导致是否能满足要求,无法检测;
③
加入的液压油是不是符合要求,不可控;
④
定期检查、维保有可能不到位;
⑤
密封圈的老化;
⑥
时间长了,滑动副有可能锈死,等等。另外因漏油现象,对环境的污染较严重。
技术实现要素:6.本发明针对现有技术存在的上述问题,提供了一种合成聚氨酯缓冲器,该产品可直接安装在电梯井道底坑水泥地面上,不需要另配固定底座连接,且具有良好的缓冲效果,在达到国标对聚氨酯缓冲器的性能要求的前提下,起到更好的缓冲效果,且便于更换和拆卸。
7.本发明的基本方案为:一种合成聚氨酯缓冲器,该合成聚氨酯缓冲器包括缓冲体,缓冲体采用合成聚氨酯材料,所述合成聚氨酯材料包括二苯基甲烷二异氰酸酯、聚酯多元醇、3,3'
‑
二氯
‑
4,4'
‑
二氨基二苯基甲烷moca、聚四氢呋喃醚二醇、有机硅泡沫稳定剂、1,4—丁二醇、碳化二亚胺、二月桂酸二丁基锡和三亚乙基二胺。
8.优选地,所述合成聚氨酯材料中各个成分的质量配比为:二苯基甲烷二异氰酸酯为20
‑
30份、聚酯多元醇为0.1
‑
1份、3,3'
‑
二氯
‑
4,4'
‑
二氨基二苯基甲烷moca为1
‑
10份、、聚四氢呋喃醚二醇为0.01
‑
0.1份、有机硅泡沫稳定剂为58
‑
70份、1,4—丁二醇为0.01
‑
0.1份、碳化二亚胺为0.01
‑
0.1份、二月桂酸二丁基锡为0.1
‑
1份,三亚乙基二胺为0.1
‑
1份。
9.优选地,所述缓冲体包括一体成型的第一缓冲体和第二缓冲体,且所述第一缓冲体设于第二缓冲体上方;
10.所述缓冲体内开设有安装孔,所述安装孔自上而下垂直贯穿第一缓冲体及第二缓冲体;
11.所述安装孔包括一体成型的第一安装孔与第二安装孔,所述第一安装孔为锥形孔,且所述第一安装孔的直径自上而下逐渐减小,且所述第一安装孔的斜度为α,α的范围为5
‑
15度;
12.所述第一缓冲体与第二缓冲体连接处为一圈缓冲凹槽。
13.优选地,所述第二安装孔为t形孔,所述第二安装孔顶部的直径大于所述第一安装孔底部的直径,且所述第二安装孔内设有安装件,该合成聚氨酯缓冲器通过安装件安装于机架上。
14.优选地,所述缓冲凹槽由第一缓冲面和第二缓冲面连接构成;
15.所述第一缓冲面设于第一缓冲体底端,所述第二缓冲面设于第二缓冲体顶端;
16.且所述第一缓冲面与第二缓冲面形成的夹角为β,所述β的范围45
‑
60度。
17.优选地,还包括内置缓冲体;
18.所述第一缓冲体自上而下开有内置缓冲孔,内置缓冲体设于内置缓冲孔内。
19.优选地,所述内置缓冲体包括第一磁石、第二磁石、缓冲弹性件和伸缩杆;
20.所述第一磁石通第一弹性支撑杆设于内置缓冲孔中部;所述第二磁石通过第二弹性支撑杆设于内置缓冲孔底部;
21.所述第一磁石上方设有空隙,且该空隙内填充有缓冲橡胶;
22.所述第一磁石与第二磁石通过多个伸缩杆连接,且每个伸缩杆上均设有缓冲弹性件,且所述缓冲弹性件的顶部与第一磁石下表面接触,缓冲弹性件的底部与第二磁石的上表面接触;
23.所述第一磁石与第二磁石的磁性相同。
24.优选地,所述内置缓冲孔设有多个,多个内置缓冲孔呈环形且间隔均匀的分布,每个内置缓冲孔内均设有内置缓冲体。
25.进一步地,本发明还提供了一种合成聚氨酯缓冲器的缓冲体的加工工艺,其特征在于:包括以下步骤:
26.(1)检查浇注机设备情况,确保无故障、钢桶内清洁,准备好a桶、b桶,a桶和b桶禁止混用,且保证浇注机上方的a桶、b桶能够同时出料;
27.(2)将合成聚氨酯材料按照、聚酯多元醇为0.1
‑
1份、3,3'
‑
二氯
‑
4,4'
‑
二氨基二苯基甲烷moca为1
‑
10份、聚四氢呋喃醚二醇为0.01
‑
0.1份、有机硅泡沫稳定剂为58
‑
70份、1,4—丁二醇为0.01
‑
0.1份、碳化二亚胺为0.01
‑
0.1份、二月桂酸二丁基锡为0.1
‑
1份,三亚乙基二胺为0.1
‑
1份准备好;
28.(3)取3,3'
‑
二氯
‑
4,4'
‑
二氨基二苯基甲烷moca、聚酯多元醇与二分之一的聚四氢
呋喃醚二醇混合为a料;
29.取二苯基甲烷二异氰酸酯和剩下的聚四氢呋喃醚二醇混合为b料;
30.有机硅泡沫稳定剂、1,4—丁二醇、碳化二亚胺、二月桂酸二丁基锡和三亚乙基二胺混合为辅料;
31.(4)并将配好的a料和辅料投放进a桶,b料投放进b桶,启动电源和报警转换开关,然后启动加热转换开关,并启动a桶和b桶搅拌的电机,启动a桶和b桶调频的电机;
32.(5)在浇注机操作枪面板上设定工位及浇注时间(试样:工浇注时间0.06s);
33.(6)将试杯放在距浇注机枪嘴正下方合适距离的位置,按下注射按钮开始浇注,浇注完毕后,得到小样,并将枪嘴对准废料袋立即按下清洗按钮;
34.(7)待小样发泡完毕,用工具刀切开小样,通过剖面观察内部质地,质地细腻均匀则合格,质地不均匀、分层、孔隙则不合格。
35.优选地,上述步骤(1)中a桶、b桶的出料比为1:1.45。
36.本发明的工作原理及优点在于:
37.(1)其中缓冲体以合成聚氨酯为原材料制备而成,具有良好的耐油性、韧性、耐磨性、耐老化性和粘合性,抗压能力更好;
38.(2)该缓冲器底部设有安装件,不需要另外设置底座进行安装,节约成本;且该安装件在安装过程中也能起到卡接、防止位移与提升整体固定性的作用,提升缓冲器的抗压能力,避免使用中产生凹陷,破裂等现象,有效的延长了其使用寿命;
39.(3)第一缓冲体与第二缓冲体的连接处设有缓冲凹槽,利用增大受力面积来分散压力的原理达到缓冲的作用;
40.(4)充分利用了磁石的同性相斥的原理,利用第一磁石和第二磁石之间的磁性关系,当第一磁石上方受到作用力向下运动时,会对缓冲弹性件进行挤压作用,此时,第二磁石固定在内置缓冲孔底部,第一磁石和第二磁石的距离靠近时,由于同性相斥的作用,第一磁石与会恢复到原有位置,再一次起到缓冲作用;
41.(5)第一磁石与第二磁石之间设有缓冲弹性件,能够进一步起到缓冲作用,且便于第一磁石与第二磁石的恢复运动;
42.(6)内置缓冲孔内设有缓冲橡胶,能够进一步起到缓冲的作用。
附图说明
43.图1为本发明一种合成聚氨酯缓冲器的立体结构;
44.图2为本发明一种合成聚氨酯缓冲器的剖视图(实施例一);
45.图3为本发明一种合成聚氨酯缓冲器的俯视图(实施例一);
46.图4为本发明一种合成聚氨酯缓冲器的剖视图(实施例二);
47.图5为图4中a部的局部放大图;
48.图6为本发明一种合成聚氨酯缓冲器的俯视图(实施例二);
49.附图中涉及到的附图标记有:第二缓冲体1,第一缓冲体2;第一安装孔3,第二安装孔4,安装件5,缓冲凹槽6,第一磁石7,内置缓冲孔8,缓冲橡胶9,第一弹性支撑杆10,伸缩杆12,缓冲弹性件13,第二弹性支撑杆14,第二磁石15。
具体实施方式
50.下面通过具体实施方式进一步详细的说明:
51.2020年12月14日国家市场监督管理总局、国家标准化管理委员会发布了新的电梯制造与安装安全规范gb/t 7588
‑
2020代替gb7588
‑
2003,于2022年7月1日实施,对比新国标的非线性缓冲器型式试验要求部分与欧洲标准en81
‑
20/50的非线性缓冲器要求部分,要求基本一致,这意味着新国标对聚氨酯缓冲器的性能提出了更高的要求。需要升级聚氨酯缓冲器的配方以满足更高性能的要求。
52.实施例一:
53.如图1至3所示,一种合成聚氨酯缓冲器,该合成聚氨酯缓冲器包括缓冲体,缓冲体采用合成聚氨酯材料,合成聚氨酯材料包括二苯基甲烷二异氰酸酯、聚酯多元醇、3,3'
‑
二氯
‑
4,4'
‑
二氨基二苯基甲烷moca、聚四氢呋喃醚二醇、有机硅泡沫稳定剂、1,4—丁二醇、碳化二亚胺、二月桂酸二丁基锡和三亚乙基二胺,其中,合成聚氨酯材料中各个成分的质量配比为:二苯基甲烷二异氰酸酯为20
‑
30份、聚酯多元醇为0.1
‑
1份、3,3'
‑
二氯
‑
4,4'
‑
二氨基二苯基甲烷moca为1
‑
10份、、聚四氢呋喃醚二醇为0.01
‑
0.1份、有机硅泡沫稳定剂为58
‑
70份、1,4—丁二醇为0.01
‑
0.1份、碳化二亚胺为0.01
‑
0.1份、二月桂酸二丁基锡为0.1
‑
1份,三亚乙基二胺为0.1
‑
1份。
54.合成聚氨酯弹性体是一种密实制品,其性能介于橡胶与塑料之间,具有高回弹性、吸震性、耐磨性、耐油、耐撕裂、耐化学腐蚀及耐辐射等性能。
55.端羟基聚四氢呋喃的制备:四氢呋喃为五元环单体,环张力较小,聚合活性较低,反应速度较慢,在较强的含氢酸高氯酸催化作用下,用醋酸酐作载体,进行阳离子开环聚合,可以合成相对分子质量为1000~3000的端羟基聚四氢呋喃。
56.缓冲体包括一体成型的第一缓冲体2和第二缓冲体1,且第一缓冲体2设于第二缓冲体1上方;缓冲体内开设有安装孔,安装孔自上而下垂直贯穿第一缓冲体2及第二缓冲体1;安装孔包括一体成型的第一安装孔3与第二安装孔4,第一安装孔3为锥形孔,且第一安装孔3的直径自上而下逐渐减小,且第一安装孔3的斜度为α,α的范围为5
‑
15度;第一缓冲体2与第二缓冲体1连接处为一圈缓冲凹槽6。
57.第二安装孔4为t形孔,第二安装孔4顶部的直径大于第一安装孔3底部的直径,且第二安装孔4内设有安装件5,该合成聚氨酯缓冲器通过安装件5安装于机架上。
58.缓冲凹槽6由第一缓冲面和第二缓冲面连接构成;
59.第一缓冲面设于第一缓冲体2底端,第二缓冲面设于第二缓冲体1顶端;且第一缓冲面与第二缓冲面形成的夹角为β,β的范围45
‑
60度。
60.上述中的的缓冲体的加工工艺,其特征在于:包括以下步骤:
61.(1)检查浇注机设备情况,确保无故障、钢桶内清洁,准备好a桶、b桶,a桶和b桶禁止混用,且保证浇注机上方的a桶、b桶能够同时出料;
62.(2)将合成聚氨酯材料按照、聚酯多元醇为0.1
‑
1份、3,3'
‑
二氯
‑
4,4'
‑
二氨基二苯基甲烷moca为1
‑
10份、聚四氢呋喃醚二醇为0.01
‑
0.1份、有机硅泡沫稳定剂为58
‑
70份、1,4—丁二醇为0.01
‑
0.1份、碳化二亚胺为0.01
‑
0.1份、二月桂酸二丁基锡为0.1
‑
1份,三亚乙基二胺为0.1
‑
1份准备好;
63.(3)取3,3'
‑
二氯
‑
4,4'
‑
二氨基二苯基甲烷moca、聚酯多元醇与二分之一的聚四氢
呋喃醚二醇混合为a料;
64.取二苯基甲烷二异氰酸酯和剩下的聚四氢呋喃醚二醇混合为b料;
65.有机硅泡沫稳定剂、1,4—丁二醇、碳化二亚胺、二月桂酸二丁基锡和三亚乙基二胺混合为辅料;
66.(4)并将配好的a料和辅料投放进a桶,b料投放进b桶,启动电源和报警转换开关,然后启动加热转换开关,并启动a桶和b桶搅拌的电机,启动a桶和b桶调频的电机;
67.(5)在浇注机操作枪面板上设定工位及浇注时间(试样:工浇注时间0.06s);
68.(6)将试杯放在距浇注机枪嘴正下方合适距离的位置,按下注射按钮开始浇注,浇注完毕后,得到小样,并将枪嘴对准废料袋立即按下清洗按钮;
69.(7)待小样发泡完毕,用工具刀切开小样,通过剖面观察内部质地,质地细腻均匀则合格,质地不均匀、分层、孔隙则不合格。
70.上述步骤(1)中a桶、b桶的出料比为1:1.45。
71.完成的缓冲器需要经过以下实验:
72.一、根据欧标要求:非线性缓冲器应进行撞击实验,即借助重物模拟装有额定载重量的轿厢对非线性缓冲器进行冲击实验。记录设备系统频率不小于1000hz,按最大允许质量和最小允许质量分别进行10次撞击试验。
73.①
在撞击瞬间达到要求的最大速度不得小于0.8m/s
74.②
应该保证撞击瞬间的加速度至少为0.9gn
75.③
每次实验间隔为5min
‑
30min,进行最大允许质量实验时,当缓冲行程等于缓冲器实际高度的50%时,对应3次测得的缓冲力坐标值之间的偏差不大于5%;在进行最小允许质量实验时也应该满足这一要求。
76.④
实验环境温度在15℃到25℃之间
77.非线性蓄能型缓冲器应符合下列要求:
78.①
当装有额定载重量的轿厢或对重自由落体并以115%额定速度撞击轿厢缓冲器时,缓冲器的作用期间的平均减速度不应大于1.0gn;
79.②
减速度峰值超过2.5gn的时间不应大于0.04s
80.③
重物反弹的速度不应超过1.0m/s
81.④
最大减速度峰值不超过6gn
82.⑤
撞击试验后,缓冲器应无永久变形;
83.根据新国标要求:
84.当载有额定载重量的轿厢或对重自由下落并以115%额定速度撞击缓冲器时,非线性蓄能型缓冲器应符合下列要求:
85.按照cb/t 7588.2
‑
2020的5.5.3.2.6.1a)确定的减速度不应大于1.0gn;
86.2.5gn以上的减速度时间不应大于0.04s;
87.轿厢或对重反弹的速度不应超过1.0m/s;
88.缓冲器动作后,应无永久变形;
89.减速度最大峰值不应大于6.0gn。
90.应使用重块对缓冲器进行撞击试验。通过自由落体,在撞击瞬间达到所要求的最大速度,且不低于0.8m/s。
91.重块的质量应对应最大和最小质量。应在摩擦力尽可能小的情况下,沿铅锤方向导引重块,以便撞击瞬间加速度至少达到0.9gn,环境温度应为+15℃—+25℃。
92.应以下列质量分别进行三次试验:
93.a)最大质量
94.b)最小质量
95.两次试验的间隔为5min
‑
30min。
96.对于最大质量试验,当缓冲行程等于申请方给出的缓冲器实际高度50%时,对应三次测得的缓冲力值的偏差不大于5%。对于最小质量试验,三次缓冲力值的偏差也应类似。
97.实施例二:
98.如图1、3
‑
6所示,一种合成聚氨酯缓冲器,该合成聚氨酯缓冲器采用合成聚氨酯材料,合成聚氨酯材料包括二苯基甲烷二异氰酸酯、聚酯多元醇、3,3'
‑
二氯
‑
4,4'
‑
二氨基二苯基甲烷moca、聚四氢呋喃醚二醇、有机硅泡沫稳定剂、1,4—丁二醇、碳化二亚胺、二月桂酸二丁基锡和三亚乙基二胺,其中,合成聚氨酯材料中各个成分的质量配比为:二苯基甲烷二异氰酸酯为20
‑
30份、聚酯多元醇为0.1
‑
1份、3,3'
‑
二氯
‑
4,4'
‑
二氨基二苯基甲烷moca为1
‑
10份、、聚四氢呋喃醚二醇为0.01
‑
0.1份、有机硅泡沫稳定剂为58
‑
70份、1,4—丁二醇为0.01
‑
0.1份、碳化二亚胺为0.01
‑
0.1份、二月桂酸二丁基锡为0.1
‑
1份,三亚乙基二胺为0.1
‑
1份。
99.合成聚氨酯弹性体是一种密实制品,其性能介于橡胶与塑料之间,具有高回弹性、吸震性、耐磨性、耐油、耐撕裂、耐化学腐蚀及耐辐射等性能。
100.端羟基聚四氢呋喃的制备:四氢呋喃为五元环单体,环张力较小,聚合活性较低,反应速度较慢,在较强的含氢酸高氯酸催化作用下,用醋酸酐作载体,进行阳离子开环聚合,可以合成相对分子质量为1000~3000的端羟基聚四氢呋喃。
101.缓冲体包括一体成型的第一缓冲体2和第二缓冲体1,且第一缓冲体2设于第二缓冲体1上方;缓冲体内开设有安装孔,安装孔自上而下垂直贯穿第一缓冲体2及第二缓冲体1;安装孔包括一体成型的第一安装孔3与第二安装孔4,第一安装孔3为锥形孔,且第一安装孔3的直径自上而下逐渐减小,且第一安装孔3的斜度为α,α的范围为5
‑
15度;第一缓冲体2与第二缓冲体1连接处为一圈缓冲凹槽6。
102.第二安装孔4为t形孔,第二安装孔4顶部的直径大于第一安装孔3底部的直径,且第二安装孔4内设有安装件5,该合成聚氨酯缓冲器通过安装件5安装于机架上。
103.缓冲凹槽6由第一缓冲面和第二缓冲面连接构成;
104.第一缓冲面设于第一缓冲体2底端,第二缓冲面设于第二缓冲体1顶端;且第一缓冲面与第二缓冲面形成的夹角为β,β的范围45
‑
60度。
105.还包括内置缓冲体;第一缓冲体2自上而下开有内置缓冲孔8,内置缓冲体设于内置缓冲孔8内,内置缓冲体包括第一磁石7、第二磁石15、缓冲弹性件13和伸缩杆12;第一磁石7通第一弹性支撑杆10设于内置缓冲孔8中部;第二磁石15通过第二弹性支撑杆14设于内置缓冲孔8底部;第一磁石7上方设有空隙,且该空隙内填充有缓冲橡胶9;第一磁石7与第二磁石15通过多个伸缩杆12连接,且每个伸缩杆12上均设有缓冲弹性件13,且缓冲弹性件13的顶部与第一磁石7下表面接触,缓冲弹性件13的底部与第二磁石15的上表面接触;第一磁
石7与第二磁石15的磁性相同。内置缓冲孔8设有4个,4个内置缓冲孔8呈环形且间隔均匀的分布,每个内置缓冲孔8内均设有内置缓冲体。
106.充分利用了磁石的同性相斥的原理,利用第一磁石7和第二磁石15之间的磁性关系,当第一磁石7上方受到作用力向下运动时,会对缓冲弹性件13进行挤压作用,此时,第二磁石15固定在内置缓冲孔8底部,第一磁石7和第二磁石15的距离靠近时,由于同性相斥的作用,第一磁石7与会恢复到原有位置,再一次起到缓冲作用。
107.以上所述的仅是本发明的实施例,方案中公知的具体结构及特性等常识在此未作过多描述,所属领域普通技术人员知晓申请日或者优先权日之前发明所属技术领域所有的普通技术知识,能够获知该领域中所有的现有技术,并且具有应用该日期之前常规实验手段的能力,所属领域普通技术人员可以在本技术给出的启示下,结合自身能力完善并实施本方案,一些典型的公知结构或者公知方法不应当成为所属领域普通技术人员实施本技术的障碍。应当指出,对于本领域的技术人员来说,在不脱离本发明结构的前提下,还可以作出若干变形和改进,这些也应该视为本发明的保护范围,这些都不会影响本发明实施的效果和专利的实用性。