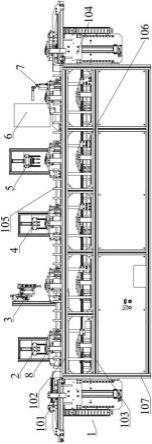
1.本发明属于机械制造装备技术领域,具体地,涉及一种具有连续搬运结构的金属件粘结组装机。
背景技术:2.如图1-3所示,其为一种工业用零部件的仰视图和主视图,工业用零部件9包括圆筒形筒体部分901和两个对称设置的弧形连接部902,两个对称设置的弧形连接部902处于同一圆周上,并且两个对称设置的弧形连接部902之间设有间隙,与此工业用零部件向连接的是如图3所示的底座903,在企业生产过程中,需要将两个对称设置的弧形连接部902粘结到底座903上,在现有申请号为:201810976442.8的圆柱体金属件上料装置及其组装设备的专利申请中,主要的技术方案集中在金属件的上料上,实现了此部分的自动化,但是上述的专利申请并不适用于本专利申请的工业用零部件和底座的组装。并且,本专利工业用零部件和底座组装的设备为整体生产线的一部分分支结构,需要将在整体生产线上输送的底座在此部分只进行工业用零部件的粘结,然后再将粘结好工业用零部件的底座输送回整体生产线上,如何完善与整体生产线的匹配是本专利申请解决的问题。
技术实现要素:3.发明目的:本发明的目的是提供一种具有连续搬运结构的金属件粘结组装机,解决了现有技术中对于非标零部件的组装存在很大的局限性,以及现有的生产设备中,如何与整体生产线良好匹配完全实现自动化生产的问题。
4.技术方案:本发明提供了一种具有连续搬运结构的金属件粘结组装机,包括底座搬运单元、底座吹风清扫单元、底座去油污单元、底座干燥单元、底座点胶单元、零部件上料组装单元、固化单元和若干底座夹具,所述底座搬运单元与主生产线呈分支结构设置,并且底座搬运单元的一端靠近主生产线,所述底座搬运单元和主生产线上均设有底座搬运单元,所述底座吹风清扫单元、底座去油污单元、底座干燥单元、底座点胶单元、零部件上料组装单元和固化单元均设置在底座搬运单元上,并且底座吹风清扫单元、底座去油污单元、底座干燥单元、底座点胶单元和零部件上料组装单元沿底座搬运单元远离主生产线的方向依次设置,所述底座夹具上设有底座,并且底座夹具依次进过底座吹风清扫单元、底座去油污单元、底座干燥单元、底座点胶单元和零部件上料组装单元。本发明具有连续搬运结构的金属件粘结组装机,能够与全自动生产线匹配,实现零部件的组装,并且零部件的组装为连续,自动的循环工作过程,能够保证生产的自动化水平。
5.进一步的,上述的具有连续搬运结构的金属件粘结组装机,所述底座搬运单元包括初始端升降输送装置、上水平支撑板、下水平支撑板、末端升降输送装置、上输送装置、下输送装置和搬运机台,所述搬运机台为矩形体结构,所述上水平支撑板和下水平支撑板平行设置在搬运机台上,并且上水平支撑板位于下水平支撑板的正上方,所述上水平支撑板和下水平支撑板均为矩形平板状,所述初始端升降输送装置和末端升降输送装置分别设置
在搬运机台长度方向的两端,所述初始端升降输送装置位于搬运机台靠近主生产线的一端,所述末端升降输送装置位于搬运机台远离主生产线的一端,所述上输送装置设置在上水平支撑板上,所述下输送装置设置在下水平支撑板上,所述上输送装置和下输送装置的两端分别与初始端升降输送装置和末端升降输送装置连接,并且上输送装置和下输送装置的输送方向反向设置。初始端升降输送装置用实现底座搬运单元与主生产线之间底座夹具的转运,末端升降输送装置在上输送装置、下输送装置之间转运底座夹具,从而保证底座在完成组装后自动进行输送。上输送装置和下输送装的折返设置,使得底座夹具能够输送回主生产线。
6.进一步的,上述的具有连续搬运结构的金属件粘结组装机,所述初始端升降输送装置包括初始端升降竖直支撑板、初始端竖直升降直线模组、两条平行设置的竖直导轨一、初始端竖直滑板、水平支撑板一、无杆气缸一、推杆一、推块一、水平导轨一、转接导轨一、转接导轨驱动气缸一、初始到位传感器和底座夹具定位装置一,所述初始端升降竖直支撑板和搬运机台靠近主生产线的一端固定连接,所述底座夹具定位装置一固定设置在初始端升降竖直支撑板的上端部上,所述初始端竖直升降直线模组和两条平行设置的竖直导轨一均沿竖直方向设置在初始端升降竖直支撑板上,所述初始端竖直滑板和初始端竖直升降直线模组的滑块连接,并且初始端竖直滑板和两条平行设置的竖直导轨一滑动连接,所述水平支撑板一和初始端竖直滑板固定连接,并且水平支撑板一水平设置,所述无杆气缸一设置在水平支撑板一的下端面上,并且无杆气缸一和推杆一的一端连接,所述推块一和推杆一的另一端连接,并且推块一位于水平支撑板一上方,所述水平导轨一设置在水平支撑板一的上端面上,所述推杆一和水平导轨一滑动连接,所述转接导轨驱动气缸一和初始到位传感器均设置在水平支撑板一的上端面上,所述转接导轨一和转接导轨驱动气缸一连接,所述转接导轨一上设有底座夹具,所述推块一与底座夹具相接触。初始端升降输送装在上下位置处的切换,能够将底座夹具转运至组装线上,再将下输送装置上的底座夹具送回主生产线。
7.进一步的,上述的具有连续搬运结构的金属件粘结组装机,所述末端升降输送装置包括末端升降竖直支撑板、末端竖直线性模组、两条平行设置的末端竖直导轨一、末端竖直滑板、水平支撑板二、无杆气缸二、推杆二、推块二、水平导轨二、转接导轨二、转接导轨驱动气缸二、末端到位传感器和底座夹具定位装置二,所述末端升降竖直支撑板和搬运机台远离主生产线的一端固定连接,所述底座夹具定位装置二固定设置在末端升降竖直支撑板的上端部上,所述末端竖直线性模组和两条平行设置的末端竖直导轨一均沿竖直方向设置在末端升降竖直支撑板的竖直面上,所述末端竖直滑板和末端竖直线性模组连接,并且末端竖直滑板和两条平行设置的末端竖直导轨一滑动连接,所述水平支撑板二和末端竖直滑板固定连接,并且水平支撑板二水平设置,所述无杆气缸二设置在水平支撑板二的下端面上,所述推杆二的一端和无杆气缸二连接,并且推杆二的另一端位于水平支撑板二的水平位置以上,所述推块二和推杆二的上端部连接,所述水平导轨二和转接导轨驱动气缸二均设置在水平支撑板二的上端面上,所述推杆二和水平导轨二滑动连接,所述转接导轨二与转接导轨驱动气缸二连接,所述转接导轨二上设有底座夹具,所述推块二与底座夹具相接触。末端升降输送装置实现上输送装置和下输送装之间底座夹具的转运,工作稳定可靠,能够改变底座夹具的输送方向,形成回流。
8.进一步的,上述的具有连续搬运结构的金属件粘结组装机,所述底座吹风清扫单元和底座干燥单元的结构相同,并且底座吹风清扫单元和底座干燥单元均包括竖直支撑架一、竖直驱动气缸一、两条平行设置的竖直导轨二、竖直滑板二、若干气嘴和气嘴安装板,所述竖直支撑架一固定设置在搬运机台上,所述竖直驱动气缸一和两条平行设置的竖直导轨二均设置在竖直支撑架一上,所述竖直驱动气缸一的活塞杆和竖直滑板二连接,所述竖直滑板二和两条平行设置的竖直导轨二滑动连接,所述气嘴安装板和竖直滑板二固定连接,并且气嘴安装板上设有若干气嘴。设置的底座吹风清扫单元在进行组装前去除底座上的灰尘,底座干燥单元能够将清洁过后的底座进行干燥,避免潮湿的底座造成打胶不牢固。
9.进一步的,上述的具有连续搬运结构的金属件粘结组装机,所述底座去油污单元包括竖直支撑架二、竖直驱动气缸二、竖直升降架二、清洁头、清洁剂存储桶、清洁剂存储桶安装架和清洁头旋转驱动组件,所述竖直支撑架二和搬运机台固定连接,所述竖直驱动气缸二固定设置在竖直支撑架二上,所述竖直升降架二和竖直驱动气缸二的活塞杆连接,所述清洁头旋转驱动组件设置在竖直升降架二上,并且清洁头旋转驱动组件和清洁剂存储桶安装架连接,所述清洁剂存储桶设置在清洁剂存储桶安装架上,所述清洁头和清洁剂存储桶连接,所述清洁头与底座夹具上的底座相接触。清洁头旋转驱动能够带动清洁剂存储桶安装架摇动,从而使得清洁头摩擦底座待打胶的面,进行油污的清除。
10.进一步的,上述的具有连续搬运结构的金属件粘结组装机,所述清洁头旋转驱动组件包括旋转驱动气缸、旋转驱动齿条、旋转驱动主动轮、两个旋转驱动从动齿轮和两个旋转轴,所述旋转驱动气缸设置在竖直升降架二上,所述旋转驱动齿条的一端和旋转驱动气缸的活塞杆连接,所述旋转驱动齿条和竖直升降架二滑动连接,所述旋转驱动齿条和旋转驱动主动轮啮合,所述旋转驱动主动轮和两个旋转驱动从动齿轮啮合,所述两个旋转驱动从动齿轮和两个旋转轴一一对应设置,所述旋转驱动从动齿轮和旋转轴的上端部通过键连接,所述清洁剂存储桶安装架和两个旋转轴连接。
11.进一步的,上述的具有连续搬运结构的金属件粘结组装机,所述底座点胶单元包括支撑架三、升降驱动气缸三、升降滑板三、两条平行设置的竖直导轨三、旋转滑台、旋转滑台安装板、旋转盘、打胶枪一和打胶枪二,所述支撑架三和搬运机台固定连接,所述升降驱动气缸三和两条平行设置的竖直导轨三设置在支撑架三上,并且升降驱动气缸三的活塞杆和升降滑板三连接,所述升降滑板三和两条平行设置的竖直导轨三和升降滑板三固定连接,所述旋转滑台设置在旋转滑台安装板上,所述旋转盘和旋转滑台连接,所述打胶枪一和打胶枪二均设置在旋转盘上,并且打胶枪一和打胶枪二相对交错设置。打胶枪一和打胶枪二在旋转滑台的旋转作用下,分别形成两段弧形胶带部分,能够与零部件的两个对称设置的弧形连接部想配合进行粘结组装。
12.进一步的,上述的具有连续搬运结构的金属件粘结组装机,所述零部件上料组装单元包括零部件振动盘、零部件切料盘、接料通道、零部件接料气缸、零部件接料吸盘、零部件上料机器人、零部件上料夹爪气缸和切料盘旋转滑台,所述零部件振动盘内设有若干零部件,所述切料盘旋转滑台和零部件切料盘连接,所述零部件切料盘上设有一组零部件接料槽一,所述一组零部件接料槽一按照环形阵列的方式设置,并且零部件接料槽一与零部件振动盘的出料通道连通,所述零部件接料槽一与接料通道连通,所述接料通道上设有零部件接料槽二,所述零部件接料槽二和零部件接料槽一连通,所述零部件接料气缸设置在
接料通道上,并且零部件接料气缸的活塞杆和零部件接料吸盘连接,所述零部件接料吸盘位于零部件接料槽二内,所述零部件上料机器人和零部件上料夹爪气缸连接,所述零部件上料夹爪气缸可夹持零部件接料槽二内的零部件。在实现自动上料零部件的同时,通过机械手将零部件夹持至底座组装位置实现自动粘结。
13.进一步的,上述的具有连续搬运结构的金属件粘结组装机,所述固化单元包括支撑架四、直线模组四、直线导轨四、水平滑板四、环形uv固化灯、固化灯翻转油缸、翻转固定座和翻转支架,所述支撑架四固定设置在搬运机台上,所述水平滑板四与直线模组四的滑块连接,并且水平滑板四和直线导轨四滑动连接,所述固化灯翻转油缸和水平滑板四铰接,并且固化灯翻转油缸的活塞杆和翻转支架铰接,所述翻转支架和翻转固定座铰接,所述翻转固定座固定设置在水平滑板四上,所述环形uv固化灯和翻转支架连接,所述环形uv固化灯套设在零部件的外部。环形uv固化灯的罩设能够进行点胶位置的固化。
14.上述技术方案可以看出,本发明具有如下有益效果:本发明所述的具有连续搬运结构的金属件粘结组装机,通过设置能够具有折返功能的底座搬运单元,从而实现了夹具底座在滑移进入支路进行组装后,在返回主生产线进行其余的组装,通过合理布置的底座吹风清扫单元、底座去油污单元、底座干燥单元、底座点胶单元、零部件上料组装单元、固化单元,能够实现零部件与底座之间的较黏组装,并且上述过程循环进行,实现了自动化的生产。
附图说明
15.图1为本发明所述零部件的主视图;图2为本发明所述零部件的仰视图;图3为本发明所述底座和底座夹具的结构示意图;图4为本发明所述具有连续搬运结构的金属件粘结组装机的主视图;图5为本发明所述具有连续搬运结构的金属件粘结组装机的俯视图;图6为本发明所底座搬运单元的结构示意图;图7为本发明所述初始端升降输送装置的结构示意图;图8为本发明所述末端升降输送装置的结构示意图;图9为本发明所述底座搬运单元的局部结构示意图一;图10为本发明所述底座搬运单元的局部结构示意图二;图11为本发明所述清扫工位定位组件、清洁工位定位组件、干燥工位定位组件、点胶工位定位组件、组装工位定位组件、回程输送定位组件一、回程输送定位组件二、回程输送定位组件三、回程输送定位组件四或回程输送定位组件五的结构示意图;图12为本发明所述推块一、推块二或夹具推块的结构示意图;图13为本发明所述底座吹风清扫单元或底座干燥单元的结构示意图;图14为本发明所述底座去油污单元的主视图;图15为本发明所述底座去油污单元的俯视图;图16为本发明所述底座点胶单元的结构示意图;图17为本发明所述零部件上料组装单元的结构示意图;图18为本发明图17中c处的局部放大图;
图19为本发明所述固化单元的结构示意图。
具体实施方式实施例
16.如图4、5所示的具有连续搬运结构的金属件粘结组装机,包括底座搬运单元1、底座吹风清扫单元2、底座去油污单元3、底座干燥单元4、底座点胶单元5、零部件上料组装单元6、固化单元7和若干底座夹具8,所述底座搬运单元1与主生产线呈分支结构设置,并且底座搬运单元1的一端靠近主生产线,所述底座搬运单元1和主生产线上均设有底座搬运单元1,所述底座吹风清扫单元2、底座去油污单元3、底座干燥单元4、底座点胶单元5、零部件上料组装单元6和固化单元7均设置在底座搬运单元1上,并且底座吹风清扫单元2、底座去油污单元3、底座干燥单元4、底座点胶单元5和零部件上料组装单元6沿底座搬运单元1远离主生产线的方向依次设置,所述底座夹具8上设有底座,并且底座夹具8依次进过底座吹风清扫单元2、底座去油污单元3、底座干燥单元4、底座点胶单元5和零部件上料组装单元6。
17.上述具有连续搬运结构的金属件粘结组装机的总体原理为:底座搬运单元1与主生产线上的分支结构,将主生产线上流转的若干底座夹具8通过底座搬运单元1转运到底座搬运单元1上,在底座搬运单元1上先正向流转分别依次经过底座吹风清扫单元2、底座去油污单元3、底座干燥单元4、底座点胶单元5、零部件上料组装单元6、固化单元7各个工作单元,完成零部件和底座的组装,然后底座搬运单元1再将组装完成的底座夹具8反向流转,从而将组装完成的底座夹具8重新输送回主生产线上。
18.如图6所示的底座搬运单元1包括初始端升降输送装置101、上水平支撑板102、下水平支撑板103、末端升降输送装置104、上输送装置105、下输送装置106和搬运机台107,所述搬运机台107为矩形体结构,所述上水平支撑板102和下水平支撑板103平行设置在搬运机台107上,并且上水平支撑板102位于下水平支撑板103的正上方,所述上水平支撑板102和下水平支撑板103均为矩形平板状,所述初始端升降输送装置101和末端升降输送装置104分别设置在搬运机台107长度方向的两端,所述初始端升降输送装置101位于搬运机台107靠近主生产线的一端,所述末端升降输送装置104位于搬运机台107远离主生产线的一端,所述上输送装置105设置在上水平支撑板102上,所述下输送装置106设置在下水平支撑板103上,所述上输送装置105和下输送装置106的两端分别与初始端升降输送装置101和末端升降输送装置104连接,并且上输送装置105和下输送装置106的输送方向反向设置。
19.初始端升降输送装置101作为主生产线与上输送装置105和下输送装置106之间的输送单元,将主生产线上的底座夹具8输送至上输送装置105上,上输送装置105上沿着初始端升降输送装置101至末端升降输送装置104放置流转底座夹具8完成零部件与底座的组装,然后末端升降输送装置104实现上输送装置105至下输送装置106之间的输送,组装完成的底座夹具8在下输送装置106上输送,沿着末端升降输送装置104至初始端升降输送装置101方向,在通过初始端升降输送装置101将组装完成的底座夹具8输送回主生产线上。
20.如图7所示的初始端升降输送装置101包括初始端升降竖直支撑板108、初始端竖直升降直线模组109、两条平行设置的竖直导轨一110、初始端竖直滑板111、水平支撑板一112、无杆气缸一113、推杆一114、推块一115、水平导轨一116、转接导轨一117、转接导轨驱
动气缸一118、初始到位传感器119和底座夹具定位装置一120,所述初始端升降竖直支撑板108和搬运机台107靠近主生产线的一端固定连接,所述底座夹具定位装置一120固定设置在初始端升降竖直支撑板108的上端部上,所述初始端竖直升降直线模组109和两条平行设置的竖直导轨一110均沿竖直方向设置在初始端升降竖直支撑板108上,所述初始端竖直滑板111和初始端竖直升降直线模组109的滑块连接,并且初始端竖直滑板111和两条平行设置的竖直导轨一110滑动连接,所述水平支撑板一112和初始端竖直滑板111固定连接,并且水平支撑板一112水平设置,所述无杆气缸一113设置在水平支撑板一112的下端面上,并且无杆气缸一113和推杆一114的一端连接,所述推块一115和推杆一114的另一端连接,并且推块一115位于水平支撑板一112上方,所述水平导轨一116设置在水平支撑板一112的上端面上,所述推杆一114和水平导轨一116滑动连接,所述转接导轨驱动气缸一118和初始到位传感器119均设置在水平支撑板一112的上端面上,所述转接导轨一117和转接导轨驱动气缸一118连接,所述转接导轨一117上设有底座夹具8,所述推块一115与底座夹具8相接触。
21.初始端升降输送装置101工作:初始端竖直升降直线模组109带动水平支撑板一112上的底座夹具8下降到位,使得转接导轨一117与主生产线上的导轨对接,将待组装的底座夹具8从主生产线上的导轨推到转接导轨一117上,初始端竖直升降直线模组109带动水平支撑板一112上的底座夹具8上升到位,使得转接导轨一117与上输送导轨135处于同一直线上,转接导轨驱动气缸一118驱动转接导轨一117与上输送导轨135接通,无杆气缸一113带动推块一115移动,使得底座夹具8从转接导轨一117滑移到上输送导轨135上。
22.如图8所示的末端升降输送装置104包括末端升降竖直支撑板121、末端竖直线性模组122、两条平行设置的末端竖直导轨一123、末端竖直滑板124、水平支撑板二125、无杆气缸二126、推杆二127、推块二128、水平导轨二129、转接导轨二130、转接导轨驱动气缸二131、末端到位传感器132和底座夹具定位装置二133,所述末端升降竖直支撑板121和搬运机台107远离主生产线的一端固定连接,所述底座夹具定位装置二133固定设置在末端升降竖直支撑板121的上端部上,所述末端竖直线性模组122和两条平行设置的末端竖直导轨一123均沿竖直方向设置在末端升降竖直支撑板121的竖直面上,所述末端竖直滑板124和末端竖直线性模组122连接,并且末端竖直滑板124和两条平行设置的末端竖直导轨一123滑动连接,所述水平支撑板二125和末端竖直滑板124固定连接,并且水平支撑板二125水平设置,所述无杆气缸二126设置在水平支撑板二125的下端面上,所述推杆二127的一端和无杆气缸二126连接,并且推杆二127的另一端位于水平支撑板二125的水平位置以上,所述推块二128和推杆二127的上端部连接,所述水平导轨二129和转接导轨驱动气缸二131均设置在水平支撑板二125的上端面上,所述推杆二127和水平导轨二129滑动连接,所述转接导轨二130与转接导轨驱动气缸二131连接,所述转接导轨二130上设有底座夹具8,所述推块二128与底座夹具8相接触。
23.上述末端升降输送装置104的工作原理为:末端竖直线性模组122驱动水平支撑板二125上升到位,使得转接导轨二130与上输送导轨135处于同一水平高度,转接导轨驱动气缸二131驱动转接导轨二130与上输送导轨135接通,过渡输送气缸一136驱动组装工位定位组件142中的夹具推块155推动上输送导轨135上的组装完成的底座夹具8滑移至转接导轨二130上,转接导轨驱动气缸二131带动转接导轨二130复位,末端竖直线性模组122驱动水平支撑板二125下降到位,使得转接导轨二
130与下输送导轨146处于同一水平高度,转接导轨驱动气缸二131驱动转接导轨二130与下输送导轨146接通,无杆气缸二126驱动推块二128,使得推块二128推动组装完成的底座夹具8移动,将转接导轨二130上的组装完成的底座夹具8滑移至回程输送定位组件一149位置处。
24.如图9和10所示的上输送装置105包括主输送气缸一134、上输送导轨135、过渡输送气缸一136、推板三137、清扫工位定位组件138、清洁工位定位组件139、干燥工位定位组件140、点胶工位定位组件141、组装工位定位组件142和推板四143,所述主输送气缸一134和过渡输送气缸一136均设置在上水平支撑板102的下端面上,并且主输送气缸一134和过渡输送气缸一136均为无杆气缸,所述上输送导轨135设置在上水平支撑板102的上端面上,所述清扫工位定位组件138通过推板三137和主输送气缸一134连接,所述组装工位定位组件142通过推板四143和过渡输送气缸一136连接,所述清扫工位定位组件138、清洁工位定位组件139、干燥工位定位组件140、点胶工位定位组件141和组装工位定位组件142沿初始端升降输送装置101至末端升降输送装置104的方向依次设置,并且清扫工位定位组件138、清洁工位定位组件139、干燥工位定位组件140、点胶工位定位组件141和组装工位定位组件142处于同一直线上,所述清扫工位定位组件138、清洁工位定位组件139、干燥工位定位组件140、点胶工位定位组件141和组装工位定位组件142间隔均匀设置,所述上输送导轨135的两端分别与水平导轨一116和水平导轨二129连接,并且上输送导轨135、水平导轨一116和水平导轨二129呈一条直线设置,所述底座夹具8和上输送导轨135滑动连接,所述清扫工位定位组件138和清洁工位定位组件139之间、清洁工位定位组件139和干燥工位定位组件140之间、干燥工位定位组件140和点胶工位定位组件141之间均设有连接杆144。
25.上述上输送装置105的工作原理为:无杆气缸一113推动底座夹具8沿着转接导轨一117和上输送导轨135移动,当底座夹具8与清扫工位定位组件138中的夹具推块155接触,在无杆气缸一113的推动力作用下,底座夹具8下压倾斜凸面171,使得倾斜凸面171压入矩形凹槽170,此时推块复位弹簧168被压缩,底座夹具8能够移动经过夹具推块155,底座夹具8到达夹具接近传感器156位置,夹具接近传感器156感应到底座夹具8,夹具定位气缸157驱动夹具定位板158上升,使得夹具定位板158进行底座夹具8的限定,夹具锁定凸轮159卡入定位槽一164内,锁定块驱动气缸161驱动夹具锁定块160移动,使得夹具锁定块160的锥形头伸入定位槽二165内,从而使得底座夹具8被限定在清扫工位定位组件138、清洁工位定位组件139、干燥工位定位组件140、点胶工位定位组件141、组装工位定位组件142、回程输送定位组件一149、回程输送定位组件二150、回程输送定位组件三151、回程输送定位组件四152和回程输送定位组件五153位置处。
26.清扫工位定位组件138、清洁工位定位组件139、干燥工位定位组件140、点胶工位定位组件141和组装工位定位组件142之间进行底座夹具8的输送时,主输送气缸一134驱动推板三137移动,推板三137上设有夹具推块155,在清扫工位定位组件138、清洁工位定位组件139、干燥工位定位组件140和点胶工位定位组件141上的夹具推块155之间通过连接杆144连接,因此主输送气缸一134同时带动清扫工位定位组件138、清洁工位定位组件139、干燥工位定位组件140和点胶工位定位组件141上的夹具推块155同步移动,因此根据夹具推块155的工作原理,能够将清扫工位定位组件138上的底座夹具8推动到清洁工位定位组件139上,将清洁工位定位组件139上的底座夹具8推动到干燥工位定位组件140上,将干燥工
位定位组件140上的底座夹具8推动到点胶工位定位组件141上,将点胶工位定位组件141上的底座夹具8推动到组装工位定位组件142上,组装工位定位组件142通过过渡输送气缸一136推动推板三137带动夹具推块155移动,将组装工位定位组件142上的底座夹具8推动到末端升降输送装置104上。
27.本专利申请中的组装工位定位组件142、回程输送定位组件一149、回程输送定位组件二150、回程输送定位组件三151、回程输送定位组件四152和回程输送定位组件五153的工作原理与上述上输送装置105的输送原理同理。
28.主输送气缸二145带动推板五148移动,由于回程输送定位组件一149、回程输送定位组件二150、回程输送定位组件三151和回程输送定位组件四152之间的夹具推块155通过连接杆144连接,因此在主输送气缸二145启动时,回程输送定位组件一149、回程输送定位组件二150、回程输送定位组件三151和回程输送定位组件四152上的夹具推块155同步移动,将回程输送定位组件一149上的底座夹具8推动到回程输送定位组件二150上,将回程输送定位组件二150上的底座夹具8推动到回程输送定位组件三151上,将回程输送定位组件三151上的底座夹具8推动到回程输送定位组件四152上,将回程输送定位组件四152上的底座夹具8推动到回程输送定位组件五153上,回程输送定位组件五153上的底座夹具8在过渡输送气缸二147推动到初始端升降输送装置101上,完成一个循环。
29.上述结构中,下输送装置106包括主输送气缸二145、下输送导轨146、过渡输送气缸二147、推板五148、回程输送定位组件一149、回程输送定位组件二150、回程输送定位组件三151、回程输送定位组件四152、回程输送定位组件五153和推板六154,所述主输送气缸二145和过渡输送气缸二147均设置在下水平支撑板103的下端面上,并且主输送气缸二145和过渡输送气缸二147均为无杆气缸,所述下输送导轨146设置在下水平支撑板103的上端面上,所述回程输送定位组件一149通过推板五148和主输送气缸二145连接,所述回程输送定位组件五153通过推板六154和过渡输送气缸二147连接,所述回程输送定位组件一149、回程输送定位组件二150、回程输送定位组件三151、回程输送定位组件四152和回程输送定位组件五153沿末端升降输送装置104至初始端升降输送装置101的方向依次设置,并且回程输送定位组件一149、回程输送定位组件二150、回程输送定位组件三151、回程输送定位组件四152和回程输送定位组件五153处于同一直线上,所述回程输送定位组件一149、回程输送定位组件二150、回程输送定位组件三151、回程输送定位组件四152和回程输送定位组件五153间隔均匀设置,所述下输送导轨146的两端分别与水平导轨一116和水平导轨二129连接,并且下输送导轨146、水平导轨一116和水平导轨二129呈一条直线设置,所述底座夹具8和下输送导轨146滑动连接,所述回程输送定位组件一149和回程输送定位组件二150之间、回程输送定位组件二150和回程输送定位组件三151之间、回程输送定位组件三151和回程输送定位组件四152之间均设有连接杆144。
30.上述下输送装置106的工作原理与上输送装置105的工作原理相同。
31.如图11所示的清扫工位定位组件138、清洁工位定位组件139、干燥工位定位组件140、点胶工位定位组件141、组装工位定位组件142、回程输送定位组件一149、回程输送定位组件二150、回程输送定位组件三151、回程输送定位组件四152和回程输送定位组件五153的结构均相同,并且清扫工位定位组件138、清洁工位定位组件139、干燥工位定位组件140、点胶工位定位组件141、组装工位定位组件142、回程输送定位组件一149、回程输送定
位组件二150、回程输送定位组件三151、回程输送定位组件四152和回程输送定位组件五153均包括夹具推块155、夹具接近传感器156、夹具定位气缸157、夹具定位板158、夹具锁定凸轮159、夹具锁定块160、锁定块驱动气缸161、夹具推块安装板162和推块直线导轨163,所述夹具推块155固定设置在夹具推块安装板162上,所述夹具推块安装板162和推块直线导轨163滑动连接,所述推块直线导轨163固定设置在上水平支撑板102和下水平支撑板103上,所述夹具推块155与底座夹具8相接触,所述夹具接近传感器156、夹具定位气缸157、夹具锁定凸轮159和锁定块驱动气缸161设置在上水平支撑板102和下水平支撑板103上,所述夹具定位气缸157的活塞杆和夹具定位板158连接,所述夹具锁定块160和锁定块驱动气缸161的活塞杆连接,所述底座夹具8上设有定位槽一164和定位槽二165,所述夹具锁定凸轮159设置在定位槽一164内,所述夹具锁定块160靠近底座夹具8的一端呈锥形头设置,并且锥形头设置在定位槽二165内。
32.上述结构中,底座夹具定位装置一120和底座夹具定位装置二133由夹具锁定块160和锁定块驱动气缸161两部分构成。
33.如图12所示的推块一115、推块二128和夹具推块155的结构相同,并且推块一115、推块二128和夹具推块155均包括矩形块166、推块本体167、推块复位弹簧168和推块转轴169,所述矩形块166的上端部设有矩形凹槽170,所述推块本体167通过推块转轴169设置在矩形凹槽170内,所述推块复位弹簧168设置在推块本体167和矩形凹槽170的底面之间,所述推块本体167的上端部设有倾斜凸面171,所述倾斜凸面171与底座夹具8相接触,所述推块转轴169至推块复位弹簧168的方向与底座夹具8的输送方向相同。
34.输送方向前端的底座夹具8能够压缩推块复位弹簧168,从而使得倾斜凸面171收回矩形凹槽170内,底座夹具8能够顺利通过推块一115、推块二128和夹具推块155,在推块一115、推块二128和夹具推块155实现底座夹具8推动作用时,倾斜凸面171靠近推块复位弹簧168的端部与底座夹具8的边缘相接触,在推块复位弹簧168的拉力的作用下,倾斜凸面171能够推动底座夹具8滑移,因此推块一115、推块二128和夹具推块155只能实现推动的作用。
35.如图13所示的底座吹风清扫单元2和底座干燥单元4的结构相同,并且底座吹风清扫单元2和底座干燥单元4均包括竖直支撑架一201、竖直驱动气缸一202、两条平行设置的竖直导轨二203、竖直滑板二204、若干气嘴205和气嘴安装板206,所述竖直支撑架一201固定设置在搬运机台107上,所述竖直驱动气缸一202和两条平行设置的竖直导轨二203均设置在竖直支撑架一201上,所述竖直驱动气缸一202的活塞杆和竖直滑板二204连接,所述竖直滑板二204和两条平行设置的竖直导轨二203滑动连接,所述气嘴安装板206和竖直滑板二204固定连接,并且气嘴安装板206上设有若干气嘴205。底座夹具8移动到位后,竖直驱动气缸一202驱动若干气嘴205下降到位,若干气嘴205启动,喷出高压气体,进行底座夹具8上底座的灰尘去除。
36.如图14、15所示的底座去油污单元3包括竖直支撑架二301、竖直驱动气缸二302、竖直升降架二303、清洁头304、清洁剂存储桶305、清洁剂存储桶安装架306和清洁头旋转驱动组件307,所述竖直支撑架二301和搬运机台107固定连接,所述竖直驱动气缸二302固定设置在竖直支撑架二301上,所述竖直升降架二303和竖直驱动气缸二302的活塞杆连接,所述清洁头旋转驱动组件307设置在竖直升降架二303上,并且清洁头旋转驱动组件307和清
洁剂存储桶安装架306连接,所述清洁剂存储桶305设置在清洁剂存储桶安装架306上,所述清洁头304和清洁剂存储桶305连接,所述清洁头304与底座夹具8上的底座相接触。所述清洁头旋转驱动组件307包括旋转驱动气缸308、旋转驱动齿条309、旋转驱动主动轮310、两个旋转驱动从动齿轮311和两个旋转轴312,所述旋转驱动气缸308设置在竖直升降架二303上,所述旋转驱动齿条309的一端和旋转驱动气缸308的活塞杆连接,所述旋转驱动齿条309和竖直升降架二303滑动连接,所述旋转驱动齿条309和旋转驱动主动轮310啮合,所述旋转驱动主动轮310和两个旋转驱动从动齿轮311啮合,所述两个旋转驱动从动齿轮311和两个旋转轴312一一对应设置,所述旋转驱动从动齿轮311和旋转轴312的上端部通过键连接,所述清洁剂存储桶安装架306和两个旋转轴312连接。底座夹具8移动到位后,竖直驱动气缸二302驱动清洁头304下降使得清洁头304与底座夹具8内的底座相接触,然后旋转驱动气缸308启动,带动旋转驱动齿条309移动,从而带动旋转驱动主动轮310转动,两个旋转驱动从动齿轮311同步转动,两个旋转轴312转动,清洁剂存储桶安装架306和两个旋转轴312之间偏心设置,这样能够形成清洁剂存储桶安装架306在底座绕动的动作,进行点胶面的清洁。
37.如图16所示的底座点胶单元5包括支撑架三501、升降驱动气缸三502、升降滑板三503、两条平行设置的竖直导轨三504、旋转滑台505、旋转滑台安装板506、旋转盘507、打胶枪一508和打胶枪二509,所述支撑架三501和搬运机台107固定连接,所述升降驱动气缸三502和两条平行设置的竖直导轨三504设置在支撑架三501上,并且升降驱动气缸三502的活塞杆和升降滑板三503连接,所述升降滑板三503和两条平行设置的竖直导轨三504滑动连接,所述旋转滑台安装板506和升降滑板三503固定连接,所述旋转滑台505设置在旋转滑台安装板506上,所述旋转盘507和旋转滑台505连接,所述打胶枪一508和打胶枪二509均设置在旋转盘507上,并且打胶枪一508和打胶枪二509相对交错设置。打胶枪一508和打胶枪二509的打胶起始点分别位于图3中所示的a和b两个点位置处,底座夹具8移动到位后,升降驱动气缸三502驱动打胶枪一508和打胶枪二509下降到位,旋转滑台505驱动旋转盘507转动,从而使得打胶枪一508和打胶枪二509沿着两个近似半圆形的轨迹进行打胶,并且两条打胶轨迹之间具有间隙。
38.如图17、18所示的零部件上料组装单元6包括零部件振动盘601、零部件切料盘602、接料通道603、零部件接料气缸604、零部件接料吸盘605、零部件上料机器人606、零部件上料夹爪气缸607和切料盘旋转滑台608,所述零部件振动盘601内设有若干零部件,所述切料盘旋转滑台608和零部件切料盘602连接,所述零部件切料盘602上设有一组零部件接料槽一609,所述一组零部件接料槽一609按照环形阵列的方式设置,并且零部件接料槽一609与零部件振动盘601的出料通道连通,所述零部件接料槽一609与接料通道603连通,所述接料通道603上设有零部件接料槽二610,所述零部件接料槽二610和零部件接料槽一609连通,所述零部件接料气缸604设置在接料通道603上,并且零部件接料气缸604的活塞杆和零部件接料吸盘605连接,所述零部件接料吸盘605位于零部件接料槽二610内,所述零部件上料机器人606和零部件上料夹爪气缸607连接,所述零部件上料夹爪气缸607可夹持零部件接料槽二610内的零部件。零部件振动盘601将零部件筛选至出料通道上,在直振的作用下,零部件振动盘601上的零件不断向零部件切料盘602上移动,切料盘旋转滑台608驱动零部件切料盘602上的一组零部件接料槽一609其中之一与零部件振动盘601的出料口连通,零部件输送进入零部件接料槽一609内,当零部件所在的零部件接料槽一609旋转至与零部
件接料槽二610连通后,零部件接料气缸604的活塞杆伸出驱动零部件接料吸盘605吸附住零部件接料槽一609内的零部件,然后零部件接料气缸604的活塞杆收回,将零部件拉入零部件接料槽二610内,零部件上料机器人606驱动零部件上料夹爪气缸607夹持住零部件接料槽二610内的零部件放置到底座的打胶位置处。
39.如图19所示的固化单元7包括支撑架四701、直线模组四702、直线导轨四703、水平滑板四704、环形uv固化灯705、固化灯翻转油缸706、翻转固定座707和翻转支架708,所述支撑架四701固定设置在搬运机台107上,所述水平滑板四704与直线模组四702的滑块连接,并且水平滑板四704和直线导轨四703滑动连接,所述固化灯翻转油缸706和水平滑板四704铰接,并且固化灯翻转油缸706的活塞杆和翻转支架708铰接,所述翻转支架708和翻转固定座707铰接,所述翻转固定座707固定设置在水平滑板四704上,所述环形uv固化灯705和翻转支架708连接,所述环形uv固化灯705套设在零部件的外部。零部件上料夹爪气缸607夹持住零部件在底座的打胶位置处,直线模组四702驱动环形uv固化灯705移动到底座位置处,固化灯翻转油缸706将竖直状态的环形uv固化灯705翻转至水平,此时环形uv固化灯705罩设在组装在一起的零部件和底座上方,进行固化。
40.本发明具有连续搬运结构的金属件粘结组装机的工作原理,包括如下步骤:s1、初始端升降输送装置101先使得水平支撑板一112下降到位,从主生产线上接收底座夹具8,然后初始端升降输送装置101带动水平支撑板一112上升,使得初始端升降输送装置101与上输送装置105的起始端相接;s2、底座夹具8从初始端升降输送装置101输送到上输送装置105上;s3、上输送装置105使得底座夹具8沿着直线进行输送,底座夹具8输送过程中,依次经过底座吹风清扫单元2、底座去油污单元3、底座干燥单元4、底座点胶单元5、零部件上料组装单元6和固化单元7;s4、在底座吹风清扫单元2工位处,进行底座的清扫,去除底座上的灰尘;s5、在底座去油污单元3工位处,去除待黏胶位置的油污;s6、在底座干燥单元4工位处,将底座进行干燥;s7、在底座点胶单元5工位处,在底座上进行点胶,形成处于同一圆周的两段对称结构的黏胶轨迹;s8、在零部件上料组装单元6工位处,进行零部件的上料,将零部件粘结在底座的黏胶位置处;s9、保持在零部件上料组装单元6位置处不动,固化单元7启动,进行黏胶位置处的固化,从而使得零部件和底座粘结在一起;s10、上输送装置105将组装完成的底座所在的底座夹具8输送至末端升降输送装置104上;s11、末端升降输送装置104初始时,与上输送装置105处于相同的水平高度,末端升降输送装置104接收底座夹具8后,末端升降输送装置104下降,使得末端升降输送装置104下降到下输送装置106位置处;s12、末端升降输送装置104上的底座夹具8输送至下输送装置106上,下输送装置106在回程输送定位组件一149、回程输送定位组件二150、回程输送定位组件三151、回程输送定位组件四152和回程输送定位组件五153之间依次输送,从而使得底座夹具8重新回到
初始端升降输送装置101位置处;s13、初始端升降输送装置101下降到位,使得初始端升降输送装置101与下输送装置106处于同一水平位置,下输送装置106上的底座夹具8输送至初始端升降输送装置101上,s14、初始端升降输送装置101上的底座夹具8重新输送至主生产线上,从而完成支路的组装。
41.以上所述仅是本发明的优选实施方式,应当指出,对于本技术领域的普通技术人员来说,在不脱离本发明原理的前提下,还可以做出若干改进,这些改进也应视为本发明的保护范围。