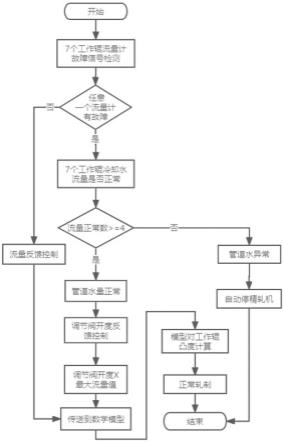
1.本发明涉及一种精轧机工作辊冷却水调节阀开度反馈控制方法,属于热连轧板材生产方法技术领域。
背景技术:2.热连轧高速生产过程中,工作辊冷却水对精轧机工作辊进行冷却以避免轧辊表面温度过高造成损伤。精轧设定数学模型(fsu模型)根据不同钢族对七架精轧机工作辊冷却水调节阀的开度进行设定并下发一级可编程控制器(plc)执行。在带钢轧制过程中,一级可编程控制器(plc)采集现场七个工作辊流量计实测冷却水流量,根据系统中设定的每个工作辊冷却水最大流量值计算得出开启冷却水流量百分比, 一级介质自动控制系统cpu在每个扫描周期采集流量计测量冷却水流量,并实时反馈到控制系统。热连轧高速生产中现场设备震动较大、环境比较恶劣,安装在管道上的工作辊冷却水流量计经常发生故障,显示检测流量为0,此时系统判断认为管道没有冷却水,为保护轧机设备一级可编程控制器(plc)发出精轧机快停命令,造成精轧机堆钢事故的发生。流量计故障显示水流量为0时,实际管道水量没有发生变化,理论上满足带钢轧制条件。目前同类型产线对精轧机工作辊冷却水的自动控制均采用单一的现场流量反馈到自动控制系统进行控制,在流量计故障时都会造成停机、堆钢事故的发生。在带钢轧制过程中精轧机工作辊冷却水不参与带钢终轧温度、卷取温度等动态调整,冷却水量设定值保持不变,根据现场调节阀开度与冷却水流量线性对应关系,现场流量计检测流量理论上保持恒定值,可应用调节阀开度对应计算出冷却水流量。
技术实现要素:3.本发明目的是提供一种精轧机工作辊冷却水调节阀开度反馈控制方法,通过在一级可编程控制器(plc)中编写控制程序实现对流量计故障信号的采集,增加应用工作辊冷却水调节阀开度反馈计算功能,流量计故障发生后,可快速诊断设备故障,并及时切换到调节阀开度反馈控制模式中,该过程无需人工干预,系统对故障处理更加快速、可靠;在相关区域人机操作界面(hmi)弹出自动报警画面,可提示相应技术人员及时处理设备故障;流量计运行正常、故障信号消失后系统自动切换到流量计反馈控制模式,系统运行的可靠性及稳定性较强,杜绝了工作辊冷却水流量计故障造成的堆钢事故发生,有效地解决了背景技术中存在的上述问题。
4.本发明的技术方案是:一种精轧机工作辊冷却水调节阀开度反馈控制方法,包含以下步骤:(1)一级可编程控制器对七架精轧机工作辊流量计故障信号在每个扫面周期内进行采集;(2)任意一个机架冷却水发出故障信号时,应用其它机架流量计水量对发生故障流量计管道冷却水流量进行判断;(3)一级可编程控制器采集冷却水调节阀实际开度,故障发生时应用调节阀开度代替流量计流量进行数据传输;(4)增加流量计故障发生时自动切换
到调节阀开度控制功能,同时自动屏蔽故障信号的发出;(5)工作辊冷却水管道调节阀实际开度传送到自动控制系统,根据调节阀开度与冷却水流量的线性对应关系,转换为流量值;(6)一级可编程控制器采集故障流量计报警信号,并根据该故障报警信号在一级主画面中编写程序,故障发生时弹出报警画面,提示相应机架冷却水流量计发生故障及时处理。
5.所述步骤(1)中,在一级可编程控制器中对精轧机七个工作辊冷却水流量计工作状态进行检测,对流量计的故障信号err进行采集;正常情况下,流量计故障信号置位为0;在流量计发生短路或断路故障时,此时该信号置位为1,自控系统报出流量计故障信号。
6.所述步骤(2)中,在一级可编程控制器中增加总管道冷却水是否正常判断功能块;在某个机架工作辊冷却水流量计发生故障时,系统对其它六个工作辊冷却水流量进行监测并对冷却水流量是否正常进行判断;编写控制程序,一级可编程控制器中累加功能块对六个冷却水管道水量是否正常信号进行累加,当四个以上的流量计水量检测正常时,一级可编程控制器自动判断认为管道供水正常。
7.所述步骤(3)中,一级可编程控制器采集每架精轧机工作辊冷却水控制系统中工作辊冷却水调节阀实际开度,二级数学模型下发工作辊冷却水调节阀开度设定值,调节阀开度在带钢轧制过程中为模型设定值,实际开度在轧制过程中有轻微波动,冷却水水量基本为固定值;应用调节阀实际开度值与管道最大流量值的线性对应关系,在流量计故障替代流量进行带钢轧制过程的自动控制。
8.所述步骤(4)中,在一级可编程控制器程序中增加精轧机工作辊冷却水控制模式自动选择功能块,选择条件为流量计故障信号,当对应流量计故障信号为0即流量计运行正常时,系统选用流量计作为反馈数据进行自动控制;当流量计故障信号为1即系统检测流量计故障时,选择调节阀实际开度进行数据反馈。对停轧机信号进行屏蔽,在故障发生时自动实现控制方式的切换。
9.所述步骤(5)中,7架精轧机工作辊冷却水最大流量不同,其中f1-f5最大流量为1400m3/h,f6-f7最大流量为1000m3/h,二级数学模型对轧制过程中每个机架冷却水调节阀开度进行设定;该设定在数学模型中分为四个钢族对应于一级控制系统中的所有钢种,在模型参数表中根据不同钢种实际控制情况灵活设定f1-f7机架冷却水的调节阀开度值以获得不同的工作辊冷却能力及工作辊合理的凸度计算;一级自控系统接收二级模型下发设定值,在轧制时冷却水调节阀打开到相应开度,并把实际开度值反馈回控制系统,新增控制功能根据调节阀开度和冷却水流量的一元线性关系,应用实际开度乘以最大流量得出工作辊冷却水流量,在流量计故障时替代实测流量进行控制。
10.所述步骤(6)中,任意一架精轧机的工作辊冷却水流量计出现故障时,一级可编程控制器对相应流量计故障信号err进行采集,在数据包中增加每个流量计故障信号与hmi的通讯,实时传送到hmi(人机操作界面)中,编写程序实现流量计故障时在hmi中自动弹出报警画面控制功能,对流量计故障进行重点报警;在hmi中设定报警画面弹出的区域,精轧机工作辊流量计故障设定在精轧操作台和精轧工程师站进行报警,对其他区域报警画面进行屏蔽。
11.本发明的有益效果是:通过在一级可编程控制器中编写控制程序实现对流量计故障信号的采集,增加应用工作辊冷却水调节阀开度反馈计算功能,流量计故障发生后,可快速诊断设备故障,并及时切换到调节阀开度反馈控制模式中,该过程无需人工干预,系统对
故障处理更加快速、可靠;在相关区域人机操作界面(hmi)弹出自动报警画面,可提示相应技术人员及时处理设备故障;流量计运行正常、故障信号消失后系统自动切换到流量计反馈控制模式,系统运行的可靠性及稳定性较强,杜绝了工作辊冷却水流量计故障造成的堆钢事故发生。
附图说明
12.图1是本发明的工作流程图。
具体实施方式
13.为了使发明实施案例的目的、技术方案和优点更加清楚,下面将结合实施案例中的附图,对本发明实施案例中的技术方案进行清晰的、完整的描述,显然,所表述的实施案例是本发明一小部分实施案例,而不是全部的实施案例,基于本发明中的实施案例,本领域普通技术人员在没有做出创造性劳动前提下所获得的所有其他实施案例,都属于本发明保护范围。
14.一种精轧机工作辊冷却水调节阀开度反馈控制方法,包含以下步骤:(1)一级可编程控制器对七架精轧机工作辊流量计故障信号在每个扫面周期内进行采集;(2)任意一个机架冷却水发出故障信号时,应用其它机架流量计水量对发生故障流量计管道冷却水流量进行判断;(3)一级可编程控制器采集冷却水调节阀实际开度,故障发生时应用调节阀开度代替流量计流量进行数据传输;(4)增加流量计故障发生时自动切换到调节阀开度控制功能,同时自动屏蔽故障信号的发出;(5)工作辊冷却水管道调节阀实际开度传送到自动控制系统,根据调节阀开度与冷却水流量的线性对应关系,转换为流量值;(6)一级可编程控制器采集故障流量计报警信号,并根据该故障报警信号在一级主画面中编写程序,故障发生时弹出报警画面,提示相应机架冷却水流量计发生故障及时处理。
15.所述步骤(1)中,在一级可编程控制器中对精轧机七个工作辊冷却水流量计工作状态进行检测,对流量计的故障信号err进行采集;正常情况下,流量计故障信号置位为0;在流量计发生短路或断路故障时,此时该信号置位为1,自控系统报出流量计故障信号。
16.所述步骤(2)中,在任意一个机架冷却水流量计故障时,系统对其它机架冷却水实际流量进行检测,在四架以上冷却水流量正常时判定认为该管道冷却水流量计故障,实际管道冷却水流量正常,切换到调节阀开度反馈控制模式。在一级可编程控制器中增加总管道冷却水是否正常判断功能块;在某个机架工作辊冷却水流量计发生故障时,系统对其它六个工作辊冷却水流量进行监测并对冷却水流量是否正常进行判断;编写控制程序,一级可编程控制器中累加功能块对六个冷却水管道水量是否正常信号进行累加,当四个以上的流量计水量检测正常时,一级可编程控制器自动判断认为管道供水正常。
17.所述步骤(3)中,一级可编程控制器采集每架精轧机工作辊冷却水控制系统中工作辊冷却水调节阀实际开度,二级数学模型下发工作辊冷却水调节阀开度设定值,调节阀开度在带钢轧制过程中为模型设定值,实际开度在轧制过程中有轻微波动,冷却水水量基本为固定值;应用调节阀实际开度值与管道最大流量值的线性对应关系,在流量计故障替代流量进行带钢轧制过程的自动控制。
18.所述步骤(4)中,在一级可编程控制器程序中增加精轧机工作辊冷却水控制模式
自动选择功能块,选择条件为流量计故障信号,当对应流量计故障信号为0即流量计运行正常时,系统选用流量计作为反馈数据进行自动控制;当流量计故障信号为1即系统检测流量计故障时,选择调节阀实际开度进行数据反馈。对停轧机信号进行屏蔽,在故障发生时自动实现控制方式的切换。
19.所述步骤(5)中,7架精轧机工作辊冷却水最大流量不同,其中f1-f5最大流量为1400m3/h,f6-f7最大流量为1000m3/h,二级数学模型对轧制过程中每个机架冷却水调节阀开度进行设定;该设定在数学模型中分为四个钢族对应于一级控制系统中的所有钢种,在模型参数表中根据不同钢种实际控制情况灵活设定f1-f7机架冷却水的调节阀开度值以获得不同的工作辊冷却能力及工作辊合理的凸度计算;一级自控系统接收二级模型下发设定值,在轧制时冷却水调节阀打开到相应开度,并把实际开度值反馈回控制系统,新增控制功能根据调节阀开度和冷却水流量的一元线性关系,应用实际开度乘以最大流量得出工作辊冷却水流量,在流量计故障时替代实测流量进行控制。
20.所述步骤(6)中,任意一架精轧机的工作辊冷却水流量计出现故障时,一级可编程控制器对相应流量计故障信号err进行采集,在数据包中增加每个流量计故障信号与hmi的通讯,实时传送到hmi(人机操作界面)中,编写程序实现流量计故障时在hmi中自动弹出报警画面控制功能,对流量计故障进行重点报警;在hmi中设定报警画面弹出的区域,精轧机工作辊流量计故障设定在精轧操作台和精轧工程师站进行报警,对其他区域报警画面进行屏蔽。
21.在实际应用中,本发明通过编制plc控制程序及在人机操作界面(hmi)中增加自动弹出报警画面等控制功能,包括如下控制过程:1、一级可编程控制器中增加7架精轧机工作辊冷却水流量计故障检索功能。在plc控制系统中添加现场电磁流量计故障报警信号,用cm_b_scl2_71功能块中故障信号err实现生产过程中对电磁流量计的诊断。正常轧制情况下,工作辊流量在800m3/h波动,当流量计流量在plc连续扫描周期内固定在最小值0或者最大值时,控制功能块置位故障信号err为1,系统报出该流量计发生故障。
22.2、一级可编程控制器报出某个流量计故障时,新增控制程序对其它六个精轧机工作辊冷却水流量进行检测,累加控制功能块对水量正常机架个数进行累加,累加输出结果大于4即四架以上精轧机工作辊冷却水流量正常时,plc判断认为冷却水管道水量正常,故障原因为现场设备冷却水流量计故障,实际精轧机工作辊冷却水流量及压力能满足正常生产。
23.3、在一级可编程控制器系统中增加控制程序,对7个精轧机工作辊调节阀在轧制过程中的实际开度进行采集。调节阀开度由二级数学模型根据轧制钢种不同进行不同的设定,同时流量值反馈给数学模型进行工作辊凸度计算以实现带钢板形的良好控制。在一块带钢轧制过程中模型设定调节阀开度为定值,实际反馈开度值由于现场管道震动等原因会出现微量变化,该变化不会对模型计算产生影响。
24.4、一级可编程控制器系统中增加工作辊冷却水调节阀开度控制与流量反馈控制自动切换功能。应用新增流量计故障时管道水量正常信号及流量计故障err信号输出工作辊冷却水控制功能选择信号,在管道水量正常及流量计正常(err信号为0)时系统应用流量反馈控制;在管道水量正常及流量计故障(err信号为1)时系统应用调节阀开度反馈控制。
在流量计故障时系统应用水量判断信号自动屏蔽流量计故障信号的发出,避免精轧机停机堆钢事故的发生。
25.5、实现与二级数学模型通讯的自动完成。在工作辊流量计发生故障时,plc系统传送给二级fsu数学模型的控制值为0,二级模型无法计算轧辊凸度,从而无法对带钢板形等进行实时调整。应用odg数据分析及计算得出开度与实际流量的对应曲线,在系统中根据计算公式及每个精轧机工作辊冷却水的最大流量值自动计算该块带钢轧制时的冷却水流量值,plc把计算流量值发送给数学模型。在生产时对实际流量与计算流量观察,计算流量与实际流量误差在每小时10m3左右,此误差与流量计正常时产生的误差基本相同,对带钢生产没有影响。
26.6、一级可编程控制器采集故障流量计报警信号,并根据该故障报警信号在一级主画面中编写脚本程序,在hmi软件intouch中编写脚本文件对每个流量计故障信号err状态进行扫描,一旦前后两个扫描周期err值不等(由0变为1),系统立即触发报警;hmi中增加7个工作辊冷却水流量计报警画面,某个流量计故障时在全线hmi运行画面最前端自动弹出相应的画面进行重点报警,及时提醒相关人员进行处理,流量计故障消失后系统自动切换到冷却水流量反馈控制模式。