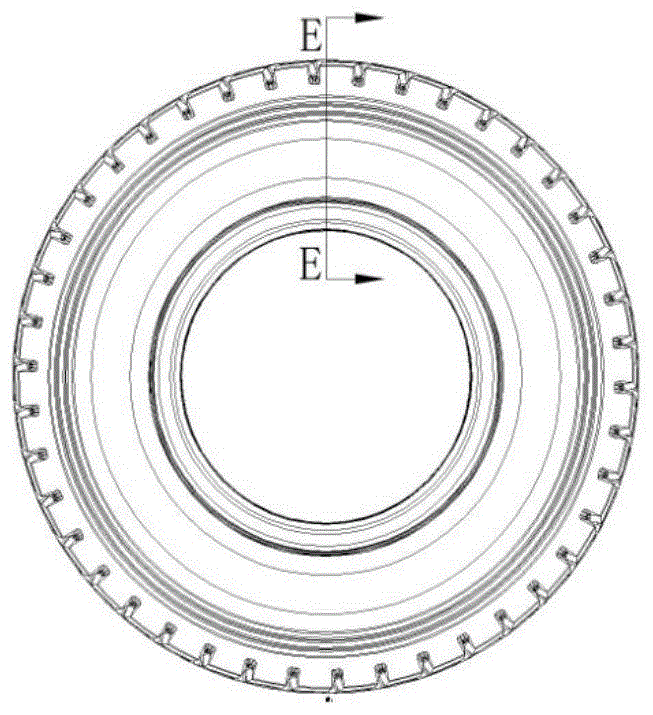
本发明涉及轮胎
技术领域:
,具体涉及一种全钢丝子午线轮胎胎体帘线伸张率弯曲度的测量控制方法。
背景技术:
:在全钢丝子午线轮胎市场反馈出现u爆、侧脱问题。市场反馈的u爆或侧脱胎,针对此问题进行原因分析。u爆等发生发生原因主要有气密性不好、胎体帘线伸张率不合适导致。帘线伸张通过胎体帘线弯曲控制。一般认为胎体帘线弯曲度通过调整平宽或调整材料分布,属于工厂工艺控制范畴。随着研究的深入和管控的加强,不断出现新问题,如原先认为由于胎体帘线伸张大,导致帘线弯曲小,容易出现肩部过渡层厚度小,内衬层过薄导致u爆。但有的规格发现在胎侧部位出现,过渡层渗胶严重的情况。目前,对帘线胎体帘线弯曲度和伸张率通过经验性进行评价有一定局限性,对胎体帘线伸张率和弯曲度的测量控制没有形成标准性的测量和控制方法。技术实现要素:为解决
背景技术:
中提到的缺陷,本发明展示了一种全钢丝子午线轮胎胎体帘线伸张率弯曲度的测量控制方法。为实现上述目的,现提供技术方案如下:一种全钢丝子午线轮胎胎体帘线伸张率弯曲度的测量控制方法,包括胎体帘线伸张率和胎体帘线弯曲度的测量和控制;所述胎体帘线伸张率的测量和控制包括以下步骤:步骤一:渗胶情况判定;步骤二:如胎侧渗胶在判定标准内,判定合格;如果超出判定标准,判定不合格,需要调整工艺平宽和材料分布,如果通过施工调整不过来,需要修改模具,重新确定断面宽的设计参数,通过平衡轮廓理论修正;在保证胎体帘线伸张率合格的情况下,所述胎体帘线弯曲度的测量和控制方法如下:步骤三:避开部件接头处,取30mm厚的轮胎断面;步骤四:把内衬层与胎体间扒开,内衬层和胎体间剥开后,拓印胎体帘线,并直线连接两钢丝圈;步骤五:用钢直尺连接两钢丝圈b-b’直线(如图6),测量肩部、胎侧部位胎体曲线峰值到b-b’(两胎圈帘线)直线的垂直距离,来判定肩部、胎侧部位的弯曲度。步骤六:如果胎体帘线弯曲度超出标准,判定不合格,首先对平宽进行修订,减小平宽,再次判定胎体帘线弯曲度,同时减小平宽可能导致渗胶严重,需要重新判定渗胶情况,执行步骤一。进一步的,渗胶情况判定中分别在断面a点胎肩处,b分型线处,c胎侧处三点处切断,在20倍电子显微镜下测量白胶的渗胶情况,测量白胶渗透到胎体帘线中的最高峰到两钢丝帘线的垂直距离h;a点胎肩处,b分型线处渗胶评定小于f,c胎侧渗胶小于e,则在判定标准内,判定合格;如果超出判定标准,判定不合格。本发明的有益效果:1、本发明对胎体帘线伸张率和弯曲度的测量控制没有形成标准性的测量和控制方法,有效避免u爆、侧脱问题的出现。2、本发明从设计机理分析产生原因解释,并规范结构设计。根据不同的设计理念,容易出现的工艺问题,做出相应的施工调整。3、本发明针对全钢不同设计理论特点,针对控制不同部位胎体帘线伸张,制定相应检验方法,控制帘线弯曲度,避免轮胎在使用中出现u爆、侧脱等批量质量问题,全钢胎体帘线弯曲度的控制方法将填补国内全钢丝子午线轮胎胎体帘线弯曲度的空白。附图说明图1为轮胎断面图;图2为图1中e-e处的剖面图;图3为p部放大图;图4为胎侧部位过渡层渗胶;图5为肩部过渡层渗胶;图6为胎体帘线弯曲示意图;图7为胎体胶渗透测量图;图8为调整后的胎体帘线弯曲示意图;图9为调整后的肩部渗胶,即图5中f-f的截面图;图10为胎体胶截面位置示意图;图11为胎体充气后,达到平衡轮廓的模型。其中:1、气密层胶;2、过渡层胶;3、胎体;31、钢丝帘线;311、轮胎胎里钢丝帘线展开线;312、参照线;32、胎体胶;4、垫胶;5、从胎肩点到胎体的垂线辅助线;6、u型爆裂开面;7、辅助线:相邻钢丝帘线靠近气密层胶侧底部切线连线。具体实施方式为使本领域技术人员更加清楚和明确本发明技术方案,下面结合附图1-10对本发明技术方案进行详细描述,但本发明的实施方式不限于此。全钢丝子午线轮胎市场反馈出现u爆、侧脱问题,如图1-3,一般主要胎体帘线伸张有过大或过小两种情况。帘线伸张过大情况包括三个现象1、帘线弯曲度过直,容易导致胎里露线。2、如图5,肩部渗胶严重:一般胎体帘线伸张过大,一般容易导致肩部内衬层中的过渡层胶2向胎体帘线渗透,在肩部形成眼镜效果,如果伸张严重的甚至造成成品内衬层薄,在使用中出现u爆问题。3、如图4,胎侧渗胶严重:有个别规格或花纹,出现渗胶严重的部位在胎侧,在胎侧部位出现眼镜现象。胶料的渗透与胎体帘线伸张有关,胎体帘线弯曲度反应胎体帘线伸张率,工厂控制胎体帘线弯曲度指标一般是x光判定。国内各个工厂工艺胎体帘线弯曲度的控制,没有具体规定。一般根据x光检验来控制,标准一般控制帘线弯曲度控制在3根胎体帘线以内。但是实际显示,弯曲度按x光标准控制,范围过宽。有的规格轮胎胎体最大伸张在肩部,而有的在侧部。这两种不同的现象,是不同轮胎结构设计导致的。轮胎结构设计导致渗胶分析:1、肩部渗胶,胎是胎胚装锅后,模具轮廓比胎胚轮廓大,胎侧部位模具向胎体有压情况。胎体的伸张主要是x方向的伸张。2、胎侧渗胶,这种情况是胎胚比模具轮廓周长小,胎体帘线不仅有x方向,还有y方向的伸张,现在统计的结果看,英制规格即h/b=1的规格,这种现象较多,如11r22.5,10.00r20,11r24.5等规格。针对以上两种情况,我们针对胎胚与模具的关系进行研究发现,有以下现象:模具内周长-胎胚外周长肩部-15mm胎侧15mm下面进行硫化时胎受力分析。肩部硫化过程中,胎胚外直径处、胎侧处先与模具接触,最后是肩部胶料流动填满模具。这时的胎体受力不是自然平充气衡下的受力,受到的力包括硫胎体化胶囊的压力、模具外压力,还有胎体受到的张力,这时的胎体帘线弯曲主要集中在胎冠部。胎侧部硫化开始与第一种情况相同即硫化过程中,胎胚外直径处、胎侧处先与模具接触,最后是肩部胶料流动填满模具。但是这种情况,肩部胎体帘线伸张正常,但是胎侧部位伸张大。导致胎侧部位内衬层和过渡层胶2向胎体渗胶严重。胎体在这种状态下的伸张形式,假定如果在模具中的胎体在假设充气后,胎体达到受力平衡。如图11是胎体充气后,达到平衡轮廓的模型:胎体平衡轮廓公式:下表是胎体内轮廓设计表单纯考虑轮胎充气状态下,胎体平衡轮廓关系,可以得出轮胎的外直径和零点半径的选取直接影响轮胎充气后断面宽。从上表中可以看出,如果计算得出断面宽过小,胎体在硫化过程中胎体受力,使断面宽有减小的趋势,但是硫化胶囊压力,导致胎体向外,即在最宽点处,胎体向里,过渡层胶2在硫化胶囊压力的作用下,向外渗透。一般轮胎设计原理的发展从自然平衡轮廓理论到非自然平衡轮廓理论,没有考虑硫化过程中胎体受力的变化,没有考虑硫化过程中胎体帘线受力,导致帘线伸张部位的不同,导致胶料渗透的现象。总之,在硫化模具中胎体受力:受到的力包括硫胎体化胶囊的压力、模具外压力,张力。如果在硫化模具中胎体帘线受力后,断面宽较小,即胎体轮廓有收的趋势,而过渡层受硫化胶囊压力向外,导致过渡层胶2向胎体帘线渗透。从下表中可以看出不同的轮廓参数,轮胎充气达到平衡时的断面宽与轮胎轮廓参数和结构参数有效带束层有关。如果轮胎轮廓设计出现rm1这种情况,将考虑胎侧渗胶问题。在硫化时,断面宽本来是减小的,但是硫化胶囊压力导致过渡层胶2向胎体渗透。这时胎侧部位胎体较直,如果胎侧部位渗胶现象严重,只能调整胎侧或胎面等本成品尺寸,通过增加材料减小胎侧部位胎体伸张。名称rm1下胎侧高(mm)136零点半径rb(mm)446.5胎里半径ra(mm)535.25断面宽度b(mm)274(标准279)有效带束层端点坐标3/84经过平衡轮廓计算可以看出,轮胎轮廓的主要参数,胎里直径、零点半径、有效带束层宽度等关系到断面宽b。如果零点半径增加,断面宽有减小趋势。如零点半径较高的轮廓,轮胎的断面宽是减小的,下胎侧较直。在硫化的过程中胎体受力,胎体断面宽由减小的趋势,导致在胎侧最宽点处帘线伸张最大,帘线过直,出现渗胶的情况。反应出来的是胎侧部位的胎体帘线伸张比肩部伸张大胎侧部位胎体帘线直。最直观的感觉是胎侧部位内衬层过渡层渗胶比肩部严重。如果胎体帘线伸张过小容易导致胎体帘线弯曲度过大。而胎体帘线弯曲度在国内没有具体规定。如果弯曲度过大容易造成肩部帘线弯曲等质量问题,即使x光合格,帘线弯曲度也可能存在过大的问题。胎体帘线弯曲度在3根帘线以内,检验合格。图6是该胎体帘线的实际弯曲度示意图,表明胎体帘线在胎肩部弯曲较大。但是肩部帘线弯曲距离达到h为25mm,这种弯曲度的帘线对产品质量有什么影响,没有定性,更没有量化。针对不同部位,胎体帘线角度不同,对轮胎性能的影响,进行如下有限元分析。不同胎体帘线弯曲度对应剪切应变、应变能表结论:静态下,实测胎体帘线角度应变能密度增加7.3%,说明胎体帘线弯曲过大,在使用中造成生热过大,导致早期损坏的现象。经过有限元分析结论,胎体帘线弯曲度控制标准采用方案2,轮胎性能能够保证。根据渗胶的研究和有限元分析对胎体帘线弯曲的分析,得出渗胶控制标准和胎体帘线弯曲标准,根据标准进行胎体帘线伸张率的控制。本专利是根据帘线伸张过大和过小的不同情况,分别制定控制方法。保证产品质量,避免使用中出现早期u爆等质量问题针对胎体帘线伸张国内现有技术和资料显示胎体帘线伸张为一个范围,如胎体伸张率小于1.2%-1.8%,在此范围内计算工艺平宽。但实际帘线弯曲度没有具体规定,在此伸张率范围内计算平宽出现一些问题,不能用工艺现象解释。一般遇到的主要问题是肩部帘线弯曲或露线问题。但是胎侧严重渗胶,x光显示合格,实际帘线弯曲度较大问题没有进行深入研究和测量控制。现阶段多是对轮胎肩部帘线弯曲的分析,对策原因一般如下:成型参数、挤出半成品尺寸、胎坯外周长和定型压力不当以及生产过程中的压延、挤出、成型、硫化工序出现偏差均会造成肩部帘线弯曲质量缺陷.控制钢丝帘线31假定伸张值为1.2%~1.8%,准确制定半成品尺寸和胎坯外周长,一次定型压力设置为0.02~0.04mpa,严格控制压延张力、成型及硫化工艺等措施均可有效避免肩部帘线弯曲缺陷的产生。下面针对胎体帘线伸张的研究制定检验方法和控制标准。经过有限元分析,胎体帘线弯曲度控制标准采用方案2,其剪切应变0.27%,应变能密度变化在4.88%,轮胎性能能够保证。以此为制定胎体帘线弯曲度制定标准的依据。例如:胎体帘线角度超出范围,静态下,实测胎体帘线角度应变能密度增加7.3%,说明胎体帘线弯曲过大,在使用中造成生热过大,导致早期损坏的现象。胎体渗胶实验方法,能够验证轮胎结构力学的内轮廓设计理念,并且检验工艺及施工设计是否合理。通过统计各个规格渗胶情况,制定渗胶标准。一种全钢丝子午线轮胎胎体帘线伸张率弯曲度的测量控制方法,包括胎体帘线伸张率和胎体帘线弯曲度的测量和控制;所述胎体帘线伸张率的测量和控制包括以下步骤:步骤一:渗胶情况判定,在内衬层上贴一层0.7mm厚白胶,轮胎硫化后取断面,如图10断面的位置,分别在断面a点胎肩处,b分型线处,c胎侧处三点处切断,在20倍电子显微镜下测量白胶的渗胶情况,测量白胶渗透到胎体帘线中的最高峰到两钢丝帘线31的垂直距离h;步骤二:a、b处肩部渗胶评定小于f,c处胎侧渗胶小于e,则在判定标准内,判定合格;如果超出判定标准,判定不合格,需要调整工艺平宽和材料分布,如果通过施工调整不过来,需要修改模具,重新确定断面宽的设计参数,通过平衡轮廓理论修正;在保证胎体帘线伸张率合格的情况下,所述胎体帘线弯曲度的测量和控制方法如下:步骤三:避开部件接头处,取30mm厚的轮胎断面;步骤四:把内衬层与胎体间扒开,内衬层和胎体间剥开后,拓印胎体帘线,并直线连接两钢丝圈;步骤五:用钢直尺连接两钢丝圈b-b’直线,如图6测量肩部胎侧部位胎体曲线峰值到b-b’(两胎圈帘线)直线的垂直距离,来判定肩部、胎侧部位的弯曲度,胎体帘线弯曲度判定分为两部分:带束层区域为胎肩,断面最宽部位为胎侧部位。通过渗胶和胎体帘线弯曲度的测量和判定合格为帘线伸张率合格,产品判定合格,一项出现问题判定为不合格。胎体帘线如果伸张过小,胎体帘线弯曲度超出标准,判定不合格,首先对平宽进行修订,减小平宽,再次判定胎体帘线弯曲度。同时减小平宽可能导致渗胶严重,需要重新判定渗胶情况,如果渗胶不合格需要调整材料分布,保证渗胶合格。全面控制了帘线伸张过大或过小的问题,也避免了因为设计不当导致问题出现。根据以上结论,针对市场中出现的u爆进行调整,符合胎体伸张和渗胶控制标准,经过调整由于帘线伸张过大过过小导致的u爆,得到有效控制,图8为调整后胎体帘线弯曲示意图。以上所述,仅是本发明的最佳实施例而已,并非对本发明的任何形式的限制,任何熟悉本领域的技术人员,在不脱离本发明技术方案范围的情况下利用上述揭示的方法和内容对本发明做出的许多可能的变动和修饰,均属于权利要求书保护的范围。当前第1页12