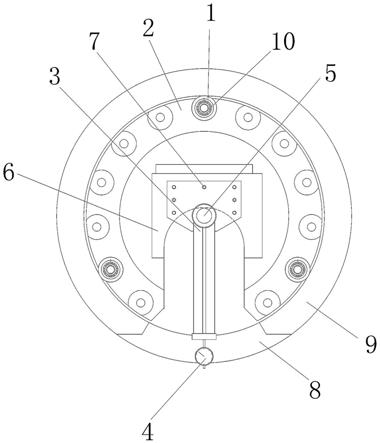
1.本发明涉及一种带有检测装配的行星中心架及检测方法。
背景技术:2.数控曲轴车床中心架回转精度的高低直接影响着机床车削曲轴的工作精度。行星中心架其结构由回转体2、滚轮10、v型块、滚道体8、滚道体盖9等组成,回转体2本身有带有u型缺口,且无中心定位孔,v型块用螺钉固定在回转体2上,其位置根据曲轴偏心位置可进行微调。其中装配难点在于如何保证固定在回转体2上滚轮10的安装精度,即:要求所有滚轮10外圆最高点位于同一圆周上(滚道体8内径),其同心度不大于0.015mm。因为零件尺寸较大,测量不便,装配、检测的难度都很大。
技术实现要素:3.本发明提供了一种带有检测装配的行星中心架及检测方法,用来解决上述背景技术中出现的技术问题。
4.带有检测装配的行星中心架,包括偏心轴、回转体、回转测量支架、千分表,其特征在于偏心轴排列设置在回转体的周围,锥度芯轴设置在回转体的中部,回转测量支架设置在锥度芯轴上,并且位于回转体的前部,回转测量支架向下延伸,延伸端部设有千分表。
5.优选的,带有检测装配的行星中心架,其特征在于所述回转体的前方下部设有缺口,所述回转测量支架的延伸部设置在缺口的前方。
6.优选的,带有检测装配的行星中心架,其特征在于所述回转体的中部设有中心定位板,定位板与回转测量支架同轴设置。
7.优选的,带有检测装配的行星中心架,其特征在于所述回转体定位盘与中心定位板通过定位销固定。
8.优选的,带有检测装配的行星中心架,其特征在于所述回转体转动设置在滚道体内,滚道体后部设有滚道体盖。
9.优选的,带有检测装配的行星中心架,其特征在于所述偏心轴设有至少十三个,偏心轴中转动设有滚轮行星中心架检测方法,其特征在于包括以下步骤:
①ꢀ
.将中心定位板通过定位销先固定于回转体上。
10.②
.将回转体滚轮轴孔与中心定位板的工艺孔一次装夹镗成。
11.③
.首先在三个偏心轴中装入滚轮,回转体组件装入滚道体内,旋转回转测量支架,回转测量支架上的千分表测量偏心轴滚轮的外径最高点,调整偏心轴,使滚轮的外圆与滚道体的内孔紧密接触并且间隙。
12.④
.移除滚道体、滚道体盖,依次将剩余的滚轮装入回转体上偏心轴内,分别用回转测量支架上的千分表测量各滚轮外径的最高点,计算该点与已定好的零点的差值。
13.⑤
.测量完毕,按此差值配磨所有滚轮外圆,去除量即为此差值的两倍。将滚轮拆
下后按实测数据进行磨削外圆、磨削后重新装好各滚轮。
14.优选的,行星中心架检测方法,其特征在于所述首先在三个偏心轴中装入滚轮为均匀三角式排列。
15.优选的,行星中心架检测方法,其特征在于所述中心定位板的工艺孔的规格为φ50h6。
16.有益效果:本方案技术降低了装配难度,提高了装配精度,缩短了装配时间,降低了生产成本,对于φ1100直径的行星中心架,用此方法装配及检测其精度可达到0.015mm以内,保证了曲轴的加工精度。
附图说明
17.图1为本实发明结构示意图;图2为本实发明侧视图;图3为最终步骤回转体示意图;图中:偏心轴1、回转体2、回转测量支架3、千分表4、锥度芯轴5、中心定位板6、定位销7、滚道体8、滚道体盖9、滚轮10。
具体实施方式
18.下面结合附图对本发明实施过程进行详细描述,所描述的实施例是本发明一部分实施例,而不是全部的实施例。基于本发明中的实施例,本领域普通技术人员在没有做出创造性劳动前提下所获得的所有其他实施例,都属于本发明保护的范围。
19.在本发明的描述中,还需要说明的是,除非另有明确的规定和限定,术语“设置”、“安装”、“相连”、“连接”应做广义理解,例如,可以是固定连接,可以是螺栓连接,也可以是可拆卸连接,或一体地连接;可以是机械连接,也可以是电连接;可以是直接相连,也可以通过中间媒介间接相连,可以是两个元件内部的连通,对于本领域的普通技术人员而言,可以具体情况理解上述术语在本发明中的具体含义。
20.带有检测装配的行星中心架,包括偏心轴1、回转体2、回转测量支架3、千分表4,其特征在于偏心轴1排列设置在回转体2的周围,锥度芯轴5设置在回转体2的中部,回转测量支架3设置在锥度芯轴5上,并且位于回转体2的前部,回转测量支架3向下延伸,延伸端部设有千分表4。
21.进一步的,回转体2的前方下部设有缺口,所述回转测量支架3的延伸部设置在缺口的前方。
22.进一步的,回转体2的中部设有中心定位板6,定位板与回转测量支架3同轴设置。
23.进一步的,回转体2定位盘与中心定位板6通过定位销7固定。
24.进一步的,回转体2转动设置在滚道体8内,滚道体8后部设有滚道体盖9。
25.进一步的,偏心轴1设有至少十三个,偏心轴1中转动设有滚轮10行星中心架检测方法,其特征在于包括以下步骤:
①ꢀ
.将中心定位板6通过定位销7先固定于回转体2上。
26.②
.将回转体2滚轮10轴孔与中心定位板6的工艺孔一次装夹镗成。
27.③
.首先在三个偏心轴1中装入滚轮10,回转体2组件装入滚道体8内,旋转回转测
量支架3,回转测量支架3上的千分表4测量偏心轴1滚轮10的外径最高点,调整偏心轴1,使滚轮10的外圆与滚道体8的内孔紧密接触并且间隙。
28.④
.移除滚道体8、滚道体盖9,依次将剩余的滚轮10装入回转体2上偏心轴1内,分别用回转测量支架3上的千分表4测量各滚轮10外径的最高点,计算该点与已定好的零点的差值。
29.⑤
.测量完毕,按此差值配磨所有滚轮10外圆,去除量即为此差值的两倍。将滚轮10拆下后按实测数据进行磨削外圆、磨削后重新装好各滚轮10。
30.进一步的,首先在三个偏心轴1中装入滚轮10为均匀三角式排列。
31.进一步的,中心定位板6的工艺孔的规格为φ50h6。
32.回转体2镗周边滚轮10孔之前,先将中心定位板6用定位销7固定在回转体2上,并配做定位销7防止移动。然后将回转体2上的十三个滚轮10轴孔与中心定位板6上的φ50h6工艺孔一次装夹镗成。
33.装配时,按附图所示,在回转体2上装入三个偏心轴1及滚轮10,三个偏心轴1的滚轮10围绕中心内呈均匀三角式分布,中心定位板6内装入配磨好的锥度芯轴5,以配磨芯轴上的外圆与回转测量支架3内孔定位装入回转测量支架3。
34.再将回转体2组件装入滚道体8内。旋转回转测量支架3,用回转测量支架3上的千分表4测量个偏心滚轮10的外径最高点,调整个偏心轴1,使滚轮10的外圆与滚道体8的内孔紧密接触,无间隙,且滚轮10外径最高点的千分表4测量值相等,此时百分表调零。这样就保证了回转体2的中心与滚道体8的内径中心同轴。
35.移除滚道体8、滚道体盖9,依次将剩余的十个滚轮10装入回转体2上的偏心轴1内,分别用回转测量支架3上的千分表4测量各滚轮10外径的最高点,计算该点与已定好的零点的差值。测量完毕,按此差值配磨所有滚轮10外圆,去除量即为此差值的两倍。将滚轮10拆下后按实测数据进行磨削外圆。磨削后重新装好各滚轮10。
36.同理,将开始安装的三偏心轴1更换成正常的滚轮10轴按上述流程配磨即可。
37.通过以上装配和检验方法,降低了装配难度,提高了装配精度,缩短了装配时间,降低了生产成本。对于φ1100直径的行星中心架,用此方法装配及检测其精度可达到0.015mm以内,保证了曲轴的加工精度。
38.以上所述的本发明实施方式,并不构成对本发明保护范围的限定,任何在本发明的精神和原则之内所作的修改、等同替换和改进等,均应包含在本发明的权利要求保护范围之内。