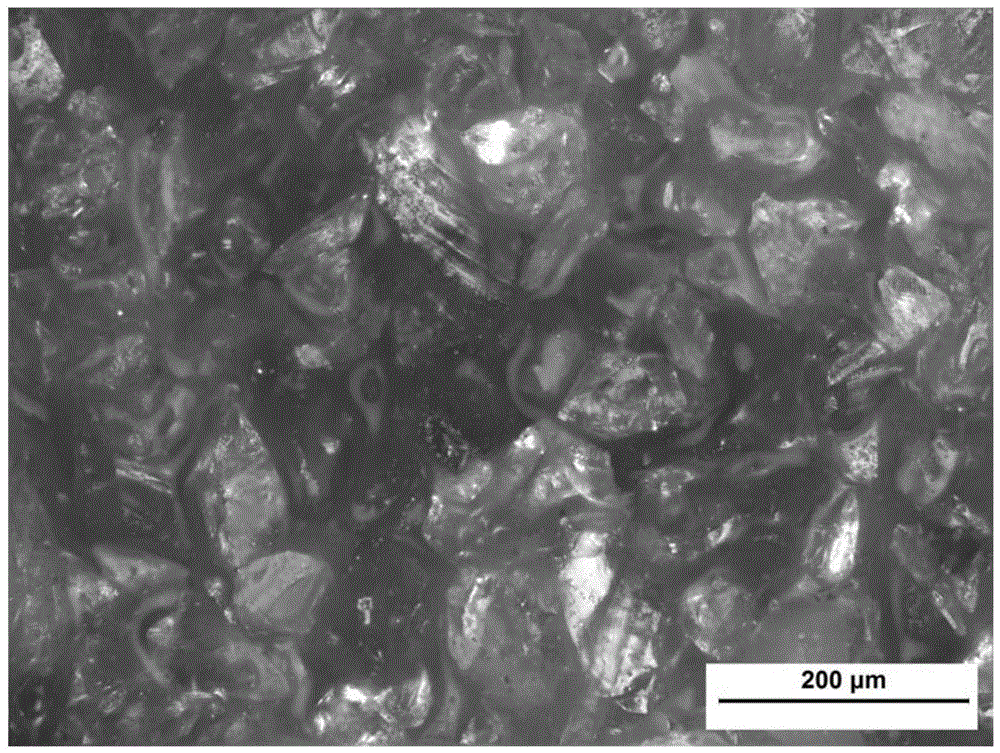
本发明涉及电子封装件的制备方法,特别涉及一种含高体积分数SiC的金属基复合电子封装件的制备方法。
背景技术:随着微电子器件向高性能、轻量化和小型化方向发展,对封装材料提出越来越苛刻的要求。传统的电子封装材料主要有塑料、金属及其合金、陶瓷,塑料具有密度小、绝缘性能好、成本低等优点,但存在热导率低、热膨胀系数大、强度低、耐湿性差等缺点,金属及其合金的机械性能好、散热性能好,但是其热膨胀系数高、密度大,陶瓷的热膨胀系数低、密度小,但是其热导率低,后续加工性能差、焊接性差,成本较高。SiC/Al复合材料具有强度高、热膨胀系数低、热导率高、密度低、成本低等优点,可广泛应用于航空航天、军事、电子信息等领域的电子封装,是目前电子封装材料的最佳选择。传统含SiC的金属基电子封装件的制备方法,首先通过混料、模压成型、烧结工艺得到SiC颗粒增强金属基复合材料,然后通过加工、焊接组装成所需形状,由于高体积分数SiC的金属基电子封装材料的可焊接性能、后续加工性能均很差,导致很难得到高体积分数SiC的电子封装材料,难以制备形状和结构复杂的电子封装件。因此,目前亟需探索一种含高体积分数SiC的金属基复合电子封装件的制备方法,以便通过较短的制备流程,能够得到含高体积分数SiC、结构和形状复杂的金属基复合电子封装件。3D打印技术被广泛应用于各个领域,也可以用来制备SiC预制体,但是,3D打印过程中无法加压,只是通过激光融化粘结剂把SiC颗粒粘结在一起,因此,相比利用高温高压烧结制备的SiC预制体,采用3D打印制备的SiC预制体的强度较低,必须通过后续的低温多段烧结来增强3D打印坯体的力学性能。
技术实现要素:本发明针对现有技术不足,提供一种结合3D打印技术制备含高体积分数SiC、结构形状复杂的金属基复合电子封装件的方法。本发明一种含高体积分数SiC的金属基复合电子封装件的制备方法,包括以下步骤:步骤一按质量比,粘接剂:SiC颗粒=1:3~5,配取粘接剂和SiC颗粒并混合均匀,得到SiC预制体备用料,所述SiC颗粒的粒径≤160μm;步骤二将步骤一所得SiC预制体备用料装入3D打印设备中,通过3D打印,得到设定形状、尺寸的SiC坯体;步骤三将步骤二所得SiC坯体进行低温多段烧结,得到SiC多孔预制体;所述低温多段烧结的工艺参数为:先升温至220-280℃,保温1-2h后再升温至380-420℃,保温1-2h,然后再继续升温至480-520℃,保温1-2h,随炉冷却至室温;步骤四对步骤三所得SiC多孔预制体进行金属合金熔液浸渗处理,得到成品。本发明涉及一种含高体积分数SiC的金属基复合电子封装件的制备方法,步骤一中所述SiC颗粒由粒径为5~15μm的SiC颗粒、55~85μm的SiC颗粒、140~160μm的SiC颗粒按质量比,5~15μm的SiC颗粒:55~85μm的SiC颗粒:140~160μm的SiC颗粒=1:1.5~2.5:8~10组成。本发明涉及一种含高体积分数SiC的金属基复合电子封装件的制备方法,步骤一中所述粘接剂为尼龙粉末、石蜡、有机硅树脂中的至少一种。本发明涉及一种含高体积分数SiC的金属基复合电子封装件的制备方法,所述尼龙粉末的粒径为25-75μm。本发明涉及一种含高体积分数SiC的金属基复合电子封装件的制备方法,步骤二中,所述3D打印的控制激光功率为20~200w,切片厚度为0.08mm~0.15mm,送料方式为单缸下送粉、双向铺粉方式,激光扫描速率为50-100mm/s。本发明涉及一种含高体积分数SiC的金属基复合电子封装件的制备方法,步骤二中所述设定尺寸、形状的SiC预制体,其尺寸和空间形状通过三维设计软件设定,所述三维设计软件优选为CAD三维设计软件。本发明涉及一种含高体积分数SiC的金属基复合电子封装件的制备方法,步骤二中,从室温加热至220-280℃时,控制升温速率为3-5℃/min;从220-280℃升温至380-420℃时,控制升温速率为1-3℃/min;从380-420℃升温至480-520℃时,控制升温速率为1.5-2℃/min。本发明涉及一种含高体积分数SiC的金属基复合电子封装件的制备方法,步骤三所得SiC多孔预制体中的SiC体积分数为60%~75%。本发明涉及一种含高体积分数SiC的金属基复合电子封装件的制备方法,步骤四中所述金属合金溶液浸渗处理方式为无压浸渗、气压浸渗、真空浸渗中的一种。本发明涉及一种含高体积分数SiC的金属基复合电子封装件的制备方法,步骤四中,进行合金溶液浸渗处理时,所述合金成分可按性能要求进行自主设计。原理和优势本发明可制备任意复杂形状的电子封装件,成型过程可实现高精度控制,能够精确控制SiC体积分数、孔隙率、预制体孔径和孔长,可精确控制材料的力学性能和热物理性能。本发明可直接按照设计图纸制备产品,无需设计制造模具,不受SiC预制体结构复杂程度的影响。本发明无需后续机械加工和连接组装,避免了高体积分数的SiC复合材料焊接性能差的缺点,封装结构整体性的提高使其力学性能和热物理性能进一步提高,还能缩短生产周期。本发明所用SiC颗粒由粒径为5~15μm的SiC颗粒、55~85μm的SiC颗粒、140~160μm的SiC颗粒按质量比,5~15μm的SiC颗粒:55~85μm的SiC颗粒:140~160μm的SiC颗粒=1:1.5~2.5:8~10组成。单一粒径的SiC颗粒间会存在无法填充SiC的铝带,一定质量比的多峰分布的SiC颗粒经过均匀混合后,小颗粒SiC很好地分布在大颗粒SiC空隙处,可以明显提高金属基复合材料的强度。本发明在3D打印时严格限定激光功率为20~200w,因为功率过低会导致粘接剂不能熔化而达不到粘结SiC颗粒的效果,进而使得SiC预制体的形状和尺寸难以控制,严重时,甚至会出现SiC预制体坍塌(这一现象在制备空间结构复杂、大尺寸SiC预制体的移样进烧结炉时尤为突出);而功率过高会导致粘接剂出现过烧现象,达不到粘结作用,进而也会导致上述情况的出现。本发明在3D打印时严格限定切片厚度为0.08mm~0.15mm,因为层厚过小会导致送料推盖触动已烧结部分,层厚过大会导致激光烧结不完全,部分区域仍为粉末态。本发明在得到设定形状、尺寸的SiC坯体后,采用多段低温烧结的方式进行后续烧结。常规制备SiC多孔预制体的烧结温度为1000℃-1500℃,时间为2h~5h不等,本发明对3D打印的预制体进行后续低温多段烧结,在稍微延长烧结时间的前提下可以大幅降低烧结温度,节省能源成本。同时可避免常规高温直接烧结法因为升温过快导致SiC预制体低温下内部脱脂不完全和高温下产生大量气泡,从而避免SiC致密度和强度较低等情况的出现。本发明首先以3-5℃/min的速率升温至220-280℃并保温1-2h,该阶段主要是将温度升至尼龙脱脂温度,然后按1-3℃/min的速率升温至380-420℃并保温1-2h,该阶段主要是尼龙分解阶段,再以1.5-2℃/min速率升温至480-520℃保温1-2h,该阶段主要是SiC烧结粘合阶段。粘接剂分解均匀是得到高质量复合材料的前提,不同阶段选取不同的升温速率,是因为要在缩短烧结总时间的同时保证粘接剂在升温过程中能够以合理的速度分解。若升温速率过快,粘结剂分解速率快,会产生大气泡,从而导致坯体出现大孔隙,进而导致坯体出现孔隙不均的情况;此外,升温速率过快会导致温度不均匀,也会导致坯体出现孔隙不均的情况。SiC预制体孔隙分布不均会严重影响坯体的强度和整体质量,还会导致浸渗金属分布不均匀,从而影响复合材料的性能。另外,升温速率过快导致的坯件局部温度不均匀,可能引起坯件局部应力分布不均,导致坯件开裂现象。总之,本发明引入3D打印技术制备结构及形状尺寸可设计、组织性能可控、含高体积分数SiC的金属基复合电子封装件,通过多工艺的协同作用,规避了传统连接组装成型工艺的连接处力学性能差、整体力学性能不均匀等情况的出现,也避免了3D打印技术制备含高体积分数SiC的金属基复合电子封装件极易出现坯体开裂、浸渗金属分布不均匀等情况。附图说明附图1为3D打印技术原理示意图;附图2为实施例1中3D打印技术制备预制体的金相照片;附图3为实施例2中3D打印所制备铝基复合材料的金相照片;附图4为实施例4中3D打印所制备尼龙SiC预制体断口形貌。从图1可以看出3D打印技术的基本原理与打印过程。从附图2可以看出实施例1中预制体SiC均匀分布,尼龙作为中间相粘结SiC。从附图3可以看出实施例2中,高体积分数SiC铝基复合材料结合紧密,材料组织分布均匀。从附图4可以看出SiC预制体的断裂是尼龙的断裂,SiC与尼龙的粘结十分紧密,断裂过程中界面没有变化。具体实施方式下面结合实施例对本发明作进一步说明。对比例1按照质量配比1:2:7称量粒径分别为10μm、85μm、145μm的SiC颗粒,粘结剂和SiC颗粒总质量之比为1:5,将粒径多峰分布的SiC颗粒和粘结剂进行混料、干燥,所得混合粉末作为制备SiC预制体的原材料;所述粘接剂是由石蜡与有机硅树脂按质量比1:1组成。将混合物导入模具中压制成型,采取低温多段烧结方法进行脱脂、二次烧结后续处理,其具体烧结方式为室温~250℃升温1h,250℃保温2h,250℃~400℃升温1h,400℃保温2h,400℃~500℃升温30min,500℃保温2h,烧结完毕随炉冷却。SiC预制体实测体积分数和抗弯强度如表1所示。对多孔SiC预制体进行Al合金溶液浸渗处理,制备出的SiC颗粒增强Al基复合材料封装件的力学性能和热物理性能如表2所示。对比例2按照质量配比1:2:7称量粒径分别为10μm、85μm、145μm的SiC颗粒,用50μm的尼龙3200粉作为粘结剂,粘结剂与SiC颗粒总质量之比为1:5,将粒径多峰分布的SiC颗粒和尼龙粉进行混料、干燥,所得混合粉末作为制备SiC预制体的原材料。设计SiC体积分数为60%,采用通用的三维设计软件CAD设计待制备SiC预制体文件,将文件导入选择性激光烧结设备中,排在立体不重复的空间内,并确定切片厚度为0.05mm、扫描间距为0.05mm、激光功率为200W、扫描速率为100mm/s。采用SLS设备对所制备的材料进行逐层选择性激光烧结,直至打印出完整的SiC预制体。对所制备的SiC预制体以10℃/min,升温至1200℃并保温3小时,烧结完毕随炉冷却。实测SiC预制体的体积分数和抗弯强度如表1对比例2所示,体积分数误差为17.8%,其SiC预制体的抗弯强度为9.8MPa。对多孔SiC预制体进行Al合金溶液浸渗处理,SiC颗粒增强Al基复合材料的封装件的力学性能和热物理性能如表2所示,热导率为220W/mk,热膨胀系数为13.4×10-6/℃,抗弯强度为375MPa。实施例1按照质量配比1:2:7称量粒径分别为10μm、85μm、145μm的SiC颗粒,用50μm的尼龙3200粉作为粘结剂,粘结剂与SiC颗粒总质量之比为1:5,将粒径多峰分布的SiC颗粒和粘结剂进行混料、干燥,所得混合粉末作为制备SiC预制体的原材料。设计SiC体积分数为60%,采用通用的三维设计软件CAD设计待制备SiC预制体文件,将文件导入选择性激光烧结设备中,排在立体不重复的空间内,并确定切片厚度为0.05mm、扫描间距为0.05mm、激光功率为200W、扫描速率为100mm/s。采用SLS设备对所制备的材料进行逐层选择性激光烧结,直至打印出完整的SiC预制体。对所制备的SiC预制体采取低温多段烧结方法进行脱脂、二次烧结后续处理,其具体烧结方式为室温~250℃升温1h,250℃保温2h,250℃~400℃升温1h,400℃保温2h,400℃~500℃升温30min,500℃保温2h,烧结完毕随炉冷却。实测SiC预制体的体积分数和抗弯强度如表1实施例1所示,体积分数误差只有0.8%,相对于对比例1,SiC预制体的抗弯强度提高31%。相对于对比例2,SiC预制体的抗弯强度提高33%。对多孔SiC预制体进行Al合金溶液浸渗处理,SiC颗粒增强Al基复合材料的封装件的力学性能和热物理性能如表2所示,相对于对比例1,热导率提高67.6%,热膨胀系数降低29.6%,抗弯强度提高12.8%。相对于对比例2,热导率提高60%,热膨胀系数降低29.1%,抗弯强度提高17.3%。实施例2按照质量配比1:2:7称量粒径分别为10μm、85μm、145μm的SiC颗粒,用25μm的尼龙3200粉作为粘结剂;粘结剂与SiC颗粒总质量之比为1:5,将粒径多峰分布的SiC颗粒和粘结剂进行混料、干燥,所得混合粉末作为制备SiC预制体的原材料。设计SiC体积分数为65%,采用通用的三维设计软件CAD设计待制备SiC预制体文件,将文件导入选择性激光烧结设备中,排在立体不重复的空间内,并确定切片厚度为0.1mm、扫描间度为0.1mm、激光功率为200W、扫描速率为100mm/s。采用SLS设备对所制备的材料进行逐层选择性激光烧结,直至打印出完整的SiC预制体。对所制备的SiC预制体采取低温多段烧结方法进行脱脂、二次烧结后续处理,其具体烧结方式为室温~250℃升温1.5h,250℃保温1.5h,250℃~400℃升温1h,400℃保温1.5h,400℃~500℃升温1h,500℃保温1.5h,烧结完毕随炉冷却。多孔SiC预制体实测体积分数和抗弯强度如表1所示,SiC体积分数误差仅为0.1%,相比对比例1,SiC预制体的强度提高了34%。相对于对比例2,SiC预制体的抗弯强度提高36.7%。对SiC多孔预制体进行Al合金溶液浸渗处理,实测的SiC颗粒增强Al基复合封装件的力学性能和热物理性能如表2所示,相对于对比例1,热导率提高61.9%,热膨胀系数降低34.1%,抗弯强度提高23.1%。相对于对比例2,热导率提高54.5%,热膨胀系数降低33.5%,抗弯强度提高28%。实施例3按照质量配比1:1:8称量粒径分别为5μm、60μm、145μm的SiC颗粒,用粒径50μm的尼龙3200粉作为粘结剂,粘结剂与SiC颗粒总质量之比为1:4,将粒径多峰分布的SiC颗粒和粘结剂进行混料、干燥,所得混合粉末作为制备SiC预制体的原材料。设计SiC多孔预制体体积分数为70%,采用通用的三维设计软件CAD设计待制备SiC预制体文件,将文件导入选择性激光烧结设备中,排在立体不重复的空间内,切片厚度、送料速度、激光功率、扫描速率等参数与实施例1相同,初始化FDM(熔融沉积造型)技术参数设置。采用FDM(熔融沉积造型)技术对所制备的材料逐层堆积,直至制成完整的SiC预制体。对所制备的SiC预制体采取低温多段烧结方法进行脱脂、二次烧结后续处理,其具体烧结方式为室温~250℃升温时间1.5h,250℃保温2h,250℃~400℃升温时间1h,400℃保温1.5h,400℃~500℃升温时间1h,500℃保温2h,烧结完毕随炉冷却。实测多孔SiC预制体体积分数和抗弯强度如表1实施例3所示,体积分数误差仅有0.0%,相对于对比实施例1强度提高35%。相对于对比例2,SiC预制体的抗弯强度提高37.8%。对多孔SiC预制体进行Al合金溶液浸渗处理,实测SiC颗粒增强Al基复合材料的力学性能和热物理性能如表2实施3所示,相对于对比例1,热导率提高45.2%,热膨胀系数降低40.0%,抗弯强度提高35.9%。相对于对比例2,热导率提高38.6%,热膨胀系数降低39.6%,抗弯强度提高41.3%。实施例4按照质量配比1:1:8称量粒径分别为5μm、60μm、145μm的SiC颗粒,用75μm的尼龙3200粉作为粘结剂,粘结剂与SiC颗粒总质量之比为1:4,将粒径多峰分布的SiC颗粒和粘结剂进行混料、干燥,所得混合粉末作为制备SiC预制体的原材料。设计SiC多孔预制体体积分数为75%,采用通用的三维设计软件CAD设计待制备SiC预制体文件,将文件导入选择性激光烧结设备中,排在立体不重复的空间内,并确定切片厚度、送料速度、激光功率、扫描速率等参数与实施例2相同,初始化FDM(熔融沉积造型)技术参数设置。采用FDM(熔融沉积造型)技术对所制备的材料逐层进行堆积,直至制成完整SiC预制体。对所制备的SiC预制体采取低温多段烧结方法进行脱脂、二次烧结后续处理,其具体烧结方式为室温~250℃升温时间1.5h,250℃保温2h,250℃~400℃升温时间1h,400℃保温2h,400℃~500℃升温时间1h,500℃保温2h,烧结完毕随炉冷却。实测多孔SiC预制体体积分数和抗弯强度如表1实施例4所示,体积分数误差仅有0.1%,相对于对比例,强度提高35%。相对于对比例2,SiC预制体的抗弯强度提高37.8%。对多孔SiC预制体进行Al合金溶液浸渗处理,实测SiC颗粒增强Al基复合材料的力学性能和热物理性能如表2实施例4所示,相对于对比例1,热导率提高30.5%,热膨胀系数降低44%,抗弯强度提高43.6%。相对于对比例2,热导率提高37.3%,热膨胀系数降低44.0%,抗弯强度提高49.9%。表1本发明实施例以及对比例所制备SiC预制体的相关性能表2本发明实施例以及对比例所制备SiC颗粒增强Al基体复合材料相关性能本发明的实施方式并不受所述实施例的限制,其他的任何未背离本发明的精神实质与原理下所作的改变、修饰、替代、组合、简化,均应为等效的置换方式,都包含在本发明的保护范围之内。