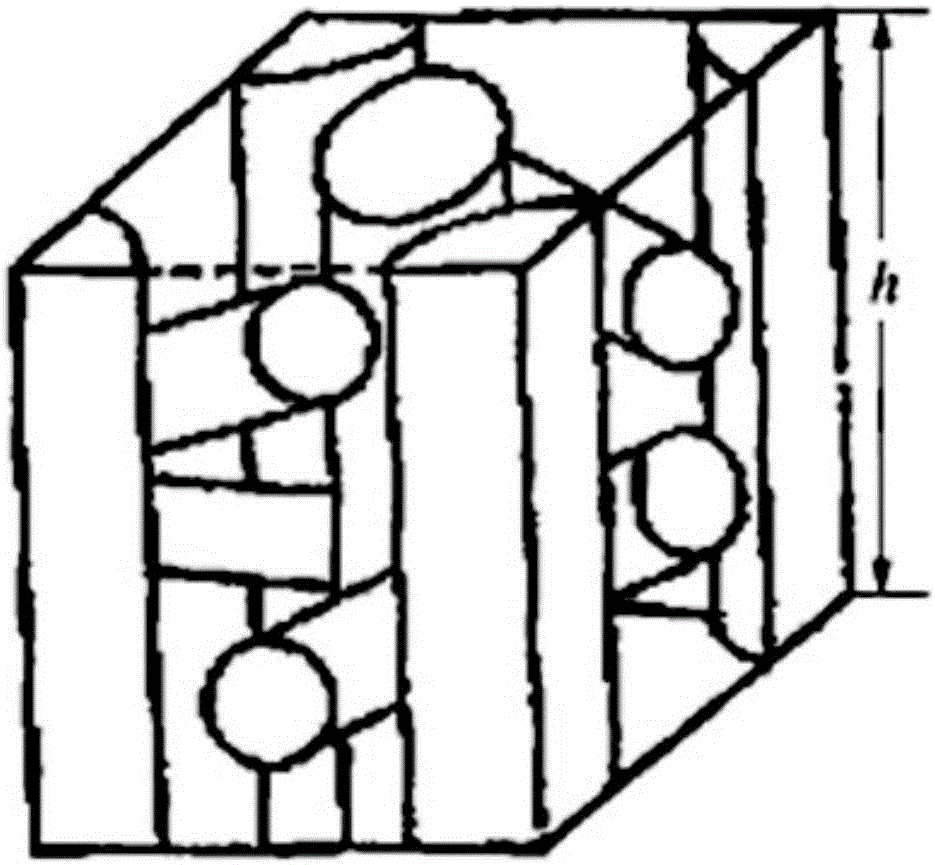
本发明涉及一种电力行业输变电用的实心柱体,尤其涉及一种大直径实心柱体的制造方法。
背景技术:
:随着特高压线路在我国逐年的增多,输变电用支柱绝缘子的用量也随之增加。全瓷支柱绝缘子存在重量重,容易出现断裂和脆断,电压等级提高后长度加大等缺陷。瓷芯加硅橡胶伞裙型支柱绝缘子存在外伞裙硅橡胶材料与陶瓷芯粘接不牢,产生气泡的现象,影响产品的电气性能及寿命。随着输变电电压等级的提高,复合材料内芯外加硅橡胶伞裙型支柱绝缘子的用量占比随之增大。复合材料内芯外加硅橡胶伞裙型支柱绝缘子的芯棒采用复合材料制成,由于直径较大,对于拉挤工艺很难一次拉挤成型。目前支柱绝缘子的芯棒采用的成型方式多为各种规格的小拉挤棒捆绑在一起进行整体灌注,但是此种工艺由于较细的多只内芯棒结构存在粘接层过多,在芯棒的横截面积中占据了较大的面积比例,固化过程中内部产生较大的内应力,应力不均导致内部产生裂纹等缺陷,在实际使用过程中很难达到理想使用效果。支柱绝缘子的芯棒还可以采用如下方式成型:内部为拉挤芯棒,外层分多次进行缠绕。这种成型方式虽然可以满足实际使用要求,但是生产效率较低,外层需进行多次缠绕即需多次固化,对于缠绕过程中的工序要求较多,且耗能较大,大大提高了产品的制造成本。此外,纤维在缠绕过程中有一定的磨损会大大降低芯棒的力学性能。CN101740185A公开了大直径复合绝缘子内芯棒的制备方法:选取实心拉挤绝缘芯棒直径≤130mm;芯棒外表面加工粗糙,外表面用丙酮擦洗干净,放入烘箱中恒温;棒外表面再涂覆2%的无水酒精溶液,再放入烘箱中恒温1小时;树脂胶的配置按比例称重并倒入真空搅拌器内真空搅拌20分钟,静置50分钟;将处理的内芯棒安装到数控缠绕机上开始缠绕,待缠绕机缠绕到设计尺寸;然后抽真空注入树脂胶;注胶完毕关闭两端阀门放入固化炉中加温阶梯固化。上述方法仍然采用缠绕方式进行制备芯棒,使得玻璃纤维与内芯棒轴向存在较大夹角,最终产品的强度和刚度不高。此外,上述方法的表面处理工序冗长、固化工序不合理,仍然有进一步改进的空间。此外,传统的复合支柱绝缘子芯棒通常包括多个纤维层,内芯棒与纤维层之间、各个纤维层之间通过环氧树脂固化结合在一起,但是内芯棒与纤维层之间、各个纤维层之间均存在界面,导致内芯棒与纤维层之间、各个纤维层之间容易发生滑移,从而影响绝缘子芯棒的弯曲性能。因此,迫切需要一种实心柱体的制造方法,其可以用于生产出弯曲性能得到显著提高的复合支柱绝缘子。技术实现要素:本发明的目的在于提供一种实心柱体的制造方法,其获得的实心柱体的强度相对比较高。本发明进一步的目的在于提供一种实心柱体的制造方法,其工序合理,并能够避免材料浪费现象,从而能够降低生产成本。本申请采用如下技术方案实现了上述目的。本发明提供一种实心柱体的制造方法,包括如下步骤:1)将纤维织物形成棒状物,将该棒状物作为内芯棒;2)采用三维编织法在所述内芯棒上形成三维编织层,从而得到预制体;所述三维编织层主要由玻璃纤维编织而成,表面编织角α为1~90°,且花节长度h为0.1~50mm;所述的表面编织角α是指玻璃纤维在三维编织层表面与三维编织层纵向之间的夹角,所述的花节长度h是指一个编织循环所编织出的三维编织层的长度;3)将所述预制体置于成型模具中,利用真空注射成型工艺将树脂注入所述的成型模具中以逐渐浸渍所述预制体,从而得到浸渍体;所述成型模具的相对真空度保持在-0.08~-0.1MPa,树脂的注入速度为250~650g/min,树脂的注入与回流时间为3~8h;4)将含所述浸渍体的成型模具封闭,并置于固化装置进行固化过程。在本发明中,所述实心柱体可以为绝缘子芯棒。在本发明的步骤1)中,将纤维织物形成棒状物。例如,将纤维织物折叠、并绕卷成棒状物。本发明的纤维织物包含单向玻璃纤维织物、双轴向玻璃纤维织物和/或多轴向玻璃纤维织物;优选为单向玻璃纤维织物。根据本发明的制造方法,优选地,在步骤1)中,所述内芯棒的直径为60~180mm;在步骤2)中,所述的三维编织层的厚度为80~120mm。根据本发明的一个实施方式,在步骤1)中,所述内芯棒的直径为70~150mm;优选为80~100mm。根据本发明的一个实施方式,所述的三维编织层的厚度为85~110mm,优选为90~100mm。本发明的三维编织层主要由玻璃纤维编织而成,还可以含有其他高强度纤维,例如芳纶纤维、碳纤维、超高强聚乙烯纤维、碳化硅纤维等。根据本发明的一个具体实施方式,在步骤2)中,所述三维编织层仅由玻璃纤维编织而成。本发明的三维编织法可以为两步法或四步法,可以形成三维四向或三维五向等编织结构。在本发明中,α为表面编织角,h为花节长度。表面编织角是指纱线(例如玻璃纤维)在编织物表面与编织物纵向或编织物的成型方向之间的夹角;花节长度是指一个编织循环所编织出的编织物的长度(参见图1和2)。表面编织角和花节长度是两个重要的参数,它们可以控制三维编织物的内部编织角,从而控制纱线的走向,控制编织物和复合材料的纤维体积含量和复合材料不同方向的性能。在本发明中,表面编织角α为1~90°,花节长度α为0.1~50mm;优选地,所述的表面编织角α为15~60°,花节长度h为1~5mm;更优选地,所述的表面编织角α为20~45°,花节长度h为2~5mm。将表面编织角和花节长度限制在上述范围内,可以有效地提高绝缘子芯棒的弯曲性能。根据本发明的一个具体实施方式,在步骤2)中,所述的表面编织角α为15~60°,且花节长度h为1~5mm。根据本发明的制造方法,优选地,在步骤2)中,所述三维编织层包括玻璃纤维经纱,所述玻璃纤维经纱与所述内芯棒的中心轴之间的夹角为0~3°。本发明的经纱具有通常的含义,但不包括接结纱线或固接纱线。在本发明中,所述玻璃纤维经纱与所述内芯棒的中心轴之间的夹角优选为0~1°。根据本发明的制造方法,优选地,在步骤2)中,以所述预制体的重量为基准,所述三维编织层占65wt%~80wt%,更优选为70wt%~75wt%。根据本发明的制造方法,优选地,在步骤2)中,所述的玻璃纤维的纤度可以为500~9600tex;优选地,所述的玻璃纤维的纤度为1000~2000tex;更优选地,所述的玻璃纤维的纤度为1100~1800tex。在本发明的步骤3)中,将所述预制体置于成型模具中,然后将成型模具合模。随后利用真空注射成型工艺将树脂注入所述的成型模具中。树脂从成型模具的进胶口注入,逐渐浸渍所述预制体,从而得到浸渍体;多余的树脂则从成型模具的出胶口流出。根据本发明的一个具体实施方式,所述成型模具的相对真空度保持在-0.08~-0.1MPa,树脂的注入速度为250~650g/min,树脂的注入与回流时间为1.5~8h;作为优选,所述成型模具的相对真空度保持在-0.085~-0.095MPa,树脂的注入速度为350~450g/min,树脂的注入与回流时间为2~6h。在本发明的步骤3)中,优选地,所述的树脂为在25℃的粘度小于700厘泊,优选为小于500厘泊的环氧树脂。本发明的环氧树脂可以选自以下树脂中的一种或多种:双酚A型环氧树脂、双酚F型环氧树脂、多酚型缩水甘油醚环氧树脂、脂肪族缩水甘油醚环氧树脂。本发明的双酚A型环氧树脂就是二酚基丙烷缩水甘油醚。本发明的双酚F型环氧树脂通常为双酚F与环氧氯丙烷在NaOH作用下反应而得的液态双酚F型环氧树脂。多酚型缩水甘油醚环氧树脂是一类多官能团环氧树脂,在其分子中有两个以上的环氧基。脂肪族缩水甘油醚环氧树脂是是由二个或二个以上环氧基与脂肪链直接相连而成的缩水甘油醚。本发明的环氧树脂优选为双酚A型环氧树脂,例如CYD-128环氧树脂(湖南省岳阳巴陵石化化工公司)。根据本发明的制造方法,优选地,在步骤3)中,所述的树脂包括100重量份的双酚A型环氧树脂、60~100重量份的固化剂、0.5~2.5重量份的有机胺促进剂、0.1~0.5重量份的有机硅消泡剂。优选地,所述的环氧树脂可以包括100重量份的双酚A型环氧树脂、70~80重量份的固化剂、0.8~1.0重量份的有机胺促进剂、0.2~0.3重量份的有机硅消泡剂。本发明的固化剂、促进剂、消泡剂可以采用本领域已知的那些。作为优选,固化剂选自酸酐固化剂,促进剂可以选自胺基苯酚类促进剂、消泡剂选自有机硅聚合物消泡剂。本发明的一个具体实施方案,所述的环氧树脂包括100重量份的湖南省岳阳巴陵石化化工公司生产的CYD-128环氧树脂、60~100重量份的甲基四氢苯酐固化剂、0.5~2.5重量份的嘉兴联兴化工新材料有限公司生产的DMP-30促进剂、0.1~0.5重量份的BYK-A530消泡剂。根据本发明的一个优选实施方案,所述的环氧树脂包括100重量份的湖南省岳阳巴陵石化化工公司生产的CYD-128环氧树脂、70~80重量份的甲基四氢苯酐固化剂、0.8~1.0重量份的嘉兴联兴化工新材料有限公司生产的DMP-30促进剂、0.2~0.3重量份的BYK-A530消泡剂(德国毕克化学公司生产)。注胶完毕后,封闭成型模具的出胶口与进胶口,然后放入固化炉中进行固化。为了防止树脂在固化时放出大量的热而造成产品开裂,固化方式采用低温长时固化。根据本发明的一个实施方式,在步骤4)中,所述的固化过程分为三个阶段,第一阶段为在50~63℃下固化4~6h,第二阶段为在65~73℃下固化4~6h,第三阶段为在75~85℃下固化3~6h。根据本发明的优选实施方式,在步骤4)中,所述的固化过程分为三个阶段,第一阶段为在57~60℃下固化4~5h,第二阶段为在67~70℃下固化5~6h,第三阶段为在77~80℃下固化5~6h。根据本发明的进一步优选实施方式,第一阶段为在60℃下固化4~4.5h,第二阶段为在70℃下固化5~5.5h,第三阶段为在80℃下固化5~5.5h。在上述固化步骤完毕后,可以对固化后的实心柱体进行脱模、表面加工等后处理,从而形成复合支柱绝缘子实心芯棒产品。本发明采用纤维织物形成内芯棒,然后在其外表面形成三维编织层,这样可以非常有效地防止传统实心柱体中的内芯棒与纤维层之间、各个纤维层之间的滑移,从而显著提高绝缘子芯棒的弯曲性能。本发明将经纱与内芯棒的中心轴之间的夹角控制在合适范围,这样进一步提高了绝缘子芯棒的弯曲性能。此外,本发明的方法工序合理,生产效率高。本发明的方法可以快速生产大直径的绝缘子芯棒。附图说明图1为编织物纱线在表面的交织示意图;图2为编织物纱线在内部的交织示意图;图3为本发明的实施例1的绝缘子芯棒的结构示意图。具体实施方式下面结合具体实施例对本发明作进一步的说明,但本发明的保护范围并不限于此。下面对以下实施例和对比例中使用的原料进行详细说明:拉挤芯棒:西安高强绝缘电气有限责任公司生产,直径为110mm,耐酸耐高温拉挤棒。单向玻璃纤维布:泰山玻璃纤维有限公司。环氧树脂配方:CYD-128环氧树脂甲基四氢苯酐DMP-30促进剂BYK-A530消泡剂100重量份80重量份1.0重量份0.2重量份环氧树脂的性能:在25℃的粘度小于500厘泊。环氧树脂原料说明如下:编号名称生产厂家1CYD-128环氧树脂湖南省岳阳巴陵石化化工公司2甲基四氢苯酐北京前门化工原料有限公司3DMP-30促进剂嘉兴联兴化工新材料有限公司4BYK-A530消泡剂德国毕克化学公司实施例11)采用纤维织物折叠、并绕卷成棒状物作为内芯棒,其直径为80mm、长度为2100mm,纤维织物为单向玻璃纤维布。2)采用三维编织法在步骤1)得到的内芯棒上形成三维编织层,从而得到预制体(参见图3)。三维编织层的厚度为100mm,幅宽为2100m。表面编织角α为45°,花节长度h为3mm。玻璃纤维的纤度为1000tex。三维编织层包括玻璃纤维经纱,玻璃纤维经纱与内芯棒的中心轴之间的夹角为0°,以所述预制体的重量为基准,三维编织层的重量占68wt%。3)将步骤2)得到预制体置于成型模具中,合模后采用树脂传递模塑成型工艺(RTM)进行注胶成型,成型过程中模具内相对真空度保持在-0.09MPa以下,注胶所用树脂为环氧树脂,注入速度为400g/min,注入与回流时间为5h。4)注胶完毕后,将模具的出胶口与进胶口封闭,放入固化炉中进行固化;固化制度为60℃固化4h,70℃固化5h,然后80℃固化5h。5)固化完毕后,进行脱模、表面加工形成绝缘子产品。将所得产品进行性能测试,结果参见表1。比较例11)选取直径为105mm、长2100mm实心拉挤绝缘芯棒;将其外表面进行喷砂处理,去除外表面的富树脂层;并用酒精擦洗外表面,除去其表面杂质。2)第一次缠绕:缠绕前,用毛滚蘸缠绕用环氧树脂在实心拉挤绝缘芯棒表面涂刷环氧树脂。开始缠绕玻璃纤维,缠绕角度分为两种:5°、85°,两种角度的缠绕厚度占比为7:1。第一次缠绕至芯棒直径为220mm,停止缠绕。3)第一次固化处理:70℃固化2h,90℃固化2h,然后120℃固化3h。4)第二次缠绕:将第一次固化处理后的芯棒外表面进行喷砂处理,去除外表面的富树脂层;并用酒精擦洗外表面,除去其表面杂质。开始第二次缠绕,缠绕角度分为两种:5°、85°,两种角度的缠绕厚度占比为7:1。第二次缠绕至芯棒直径为305mm,停止缠绕。5)第二次固化处理:70℃固化2h,90℃固化2h,然后120℃固化3h。6)将第二次固化处理后的芯棒进行车加工,将芯棒直径车加工为305mm。将所得产品进行性能测试,结果参见表1。表1本发明并不限于上述实施方式,在不背离本发明的实质内容的情况下,本领域技术人员可以想到的任何变形、改进、替换均落入本发明的范围。当前第1页1 2 3