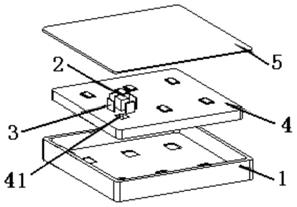
一种大功率ltcc微波组件散热结构及制造工艺
技术领域
[0001]
本发明涉及一种大功率ltcc微波组件散热结构及制造工艺。
背景技术:[0002]
射频电路散热问题一直是射电路工艺制造中必须要解决的主要问题。影响散热主要因素有:电路外壳材料、基板材料、功率芯片散热片材料、功率芯与散热片及其安装工艺、以及电路基板与外壳的装配结构等等。
[0003]
目前用于射频电路的ltcc基板导热系数为2.0w/mk~2.5 w/mk,外壳材料有:硅铝合金(100 w/mk~180 w/mk)、钼铜合金(150 w/mk~200 w/mk)、钨铜合金(180 w/mk~260 w/mk)、不锈钢(10 w/mk~30 w/mk)。
[0004]
通常大功率射频电路散热结构是:散热外壳与散热凸台一体结构,功率芯片贴装在散热凸台上,外围电路用高频电路板(罗杰斯板)拼接而成。这种结构,设计简单,散热性能好,适用于简单射频电路结构散热设计。但对于复杂多通道大功率射频电路,这种简单结构不能满足散热结构设计要求。
技术实现要素:[0005]
本发明所要解决的技术问题是克服现有技术的缺陷,提供一种大功率ltcc微波组件散热结构及制造工艺,可满足大功率射频电路的散热要求。
[0006]
为解决上述技术问题,本发明采用的技术方案如下:一种大功率ltcc微波组件散热结构,包括散热底座、散热凸台、片材、开有直通孔的ltcc基板和金属盖板;至少一个散热凸台焊接在散热底座内;ltcc基板装配在与散热外壳内,且散热凸台对应地从ltcc基板上的直通孔内穿过,形成一暴露于ltcc基板外的上表面,可用于承载功率裸芯;散热凸台与直通孔之间形成的缝隙中由片材填充。
[0007]
进一步地,所述ltcc基板上集成有微波元器件和非微波元器件。
[0008]
进一步地,采用焊接或粘接方法将ltcc基板装配到散热外壳内。
[0009]
进一步地,所述片材采用导热导电胶半烧结方法填充至散热凸台周围的缝隙。
[0010]
进一步地,所述功率裸芯通过散热载片安装在散热凸台上表面。
[0011]
进一步地,所述功率裸芯采用au80sn20焊料焊接在散热载片上。
[0012]
进一步地,所述散热载片采用钼铜或钨铜材料。
[0013]
进一步地,所述散热载片采用焊料共晶点≤183℃的焊料或导热导电胶半烧结到散热凸台。
[0014]
进一步地,所述ltcc基板上通过smt焊接工艺或导电胶粘片/键合工艺组装有非功率元器件。
[0015]
一种大功率ltcc微波组件散热结构制造工艺,
将散热凸台焊接在散热底座内的底面上;开有直通孔的ltcc基板装配在散热外壳内,且散热凸台对应地从ltcc基板上的直通孔内穿过,形成一暴露于ltcc基板外的上表面;将片材填充在散热凸台与直通孔之间形成的缝隙中;功率裸芯焊接在散热载片上,散热载片焊接或烧结到散热凸台的上表面;通过smt焊接工艺或导电胶粘片/键合工艺将非功率元器件组装到ltcc基板上;通过粘接胶粘接工艺、平行缝焊或激光焊工艺将金属盖板封盖在散热底座上。
[0016]
本发明所达到的有益效果:1) 有效提高大功率微波组件散热性能;2)大幅度减小射频组件的集成体积,降低微波信号传输寄生参数;3)大大提高ltcc基板利用率,降低生产制造成本。
附图说明
[0017]
图1a散热底座示意图;图1b散热凸台示意图;图1c薄片示意图;图1dltcc基板示意图;图1e金属盖板示意图;图2散热外壳示意图;图3微波芯组一示意图;图4微波芯组二示意图;图5功率器件示意图;图6微波芯组三示意图;图7大功率ltcc微波组件爆炸图;图8制造工艺流程图。
具体实施方式
[0018]
下面结合附图对本发明作进一步描述。以下实施例仅用于更加清楚地说明本发明的技术方案,而不能以此来限制本发明的保护范围。
[0019]
本实施例中的大功率ltcc微波组件散热结构及制造工艺,包括:散热结构设计、关键工艺及材料选用要求等信息。
[0020]
1、大功率ltcc微波组件散热结构及制造工艺特点1) 散热凸台与散热底座采用高温(焊料共晶点≥218℃)焊料焊接;2)ltcc 基板上大功率芯片安装区开有直通孔,ltcc基板与底座安装时,散热凸台从直通孔中穿过;3)功率芯片用au80sn20焊料焊接在用于散热的钼铜或钨铜载片上;4)带载片的功率芯片用低温焊料(焊料共晶点≤183℃)或导热导电胶半烧结到散热凸台上。
[0021]
5)其它非功率元器件集成在ltcc基板正背面。
[0022]
1.1 技术方案大功率微波组件散热结构包括:散热底座1、散热凸台2、薄片3、开有直通孔41的ltcc基板4和金属盖板5,见图1(微波组件爆炸图见图7);散热凸台2与散热底座1采用高温焊料焊接(焊料共晶点≥218℃),形成散热外壳1-2,如图2所示;开有直通孔41的ltcc基板4上集成有小功率元件(包括微波元器件和非微波元器件);采用焊接或粘接办法将ltcc基板4与散热外壳1-2装配到一起形成微波芯组一1-2-4,ltcc基板4上的直通孔大小位置与散热凸台2相配合,装配时,散热凸台2通过直通孔贯穿ltcc基板4,如图3所示;采用导热导电胶半烧结方法将微波芯组一1-2-4中散热凸台四周缝隙用薄片3填充,形成微波芯组二1-2-4-3,如图4所示;功率裸芯6用au80sn20焊料焊接在散热的钼铜或钨铜载片7上形成功率器件6-7,如图5所示;功率器件6-7用低温焊料(焊料共晶点≤183℃)或导热导电胶半烧结到微波芯组二1-2-4-3的散热凸台2上,形成微波芯组三,图6 所示;通过smt焊接工艺或导电胶粘片/键合工艺将非功率元器件组装到ltcc基板4上;通过粘接胶粘接工艺或平行缝焊(或激光焊)等工艺将金属盖板5最后封盖在微波芯组三上。
[0023]
如图8所示,本实施例中大功率ltcc微波组件散热结构制造工艺流程为:将散热凸台焊接在散热底座内的底面上;开有直通孔的ltcc基板装配在散热外壳内,且散热凸台对应地从ltcc基板上的直通孔内穿过,形成一暴露于ltcc基板外的上表面;将片材填充在散热凸台与直通孔之间形成的缝隙中;功率裸芯焊接在散热载片上,散热载片焊接或烧结到散热凸台的上表面;通过smt焊接工艺或导电胶粘片/键合工艺将非功率元器件组装到ltcc基板上;通过粘接胶粘接工艺、平行缝焊或激光焊工艺将金属盖板封盖在散热底座上。
[0024]
2、关键材料选用2.1 零部件材料选用1)散热底座:ce11(si50%-al50%,硅铝合金)或钼铜(mocu)或钨铜(wcu)。
[0025]
2)散热凸台:紫铜或钼铜(mocu)或钨铜(wcu)。
[0026]
3)功率裸芯、载片:钼铜(mocu)或钨铜(wcu)。
[0027]
4)ltcc基板:dupont951或ferro-a6或相当性能生瓷材料。
[0028]
5)散热凸台周围填缝用的薄片3材料:厚度10μm~15μm紫铜片;6)盖板:铝4047或可伐 4j29。
[0029]
2.2 关键工艺材料选用1)散热凸台与散热底座焊接材料:sac305焊膏(sn96.5ag3.0cu0.5)或sn96.5ag3.5焊膏。
[0030]
2)功率裸芯与载片焊接材料:25μm~30μm厚度au80sn20焊片或相当性能的半烧结银导热导电胶。
[0031]
3)ltcc基板与散热底座的装配材料:63sn37pb焊膏或相当性能导电环氧胶。
[0032]
4)功率器件与散热凸台的装配材料:63sn37pb焊膏或半烧结银导热导电胶。
[0033]
5)散热凸台四周缝隙填充粘接材料:半烧结银导热导电胶。
[0034]
3、关键工艺方法及参数控制3.1 散热凸台与散热底座焊接1)工艺方法:采用热板或者真空再流焊炉焊接;2)焊接峰值温度:焊料共晶点+(20℃~40℃);3)合金焊层厚度:5μm~15μm;4)焊透率:≥90%。
[0035]
3.2 功率裸芯与载片装配方法1:ausn共晶焊接1)工艺方法:采用热板或者真空共晶焊炉焊接;2)焊接峰值温度:焊料共晶点+(15℃~25℃);3)合金焊层厚度:5μm~15μm;4)焊透率:≥90%。
[0036]
方法2:半烧结银导热导电胶粘接1)工艺方法:点胶
→
粘片
→
固化(半烧结);2)点胶厚度:5μm~15μm,均匀无空洞;3)固化温度:保证导热导电胶充分固化(半烧结)且低于功率芯片耐受温度;3.3 ltcc基板与散热外壳装配方法1:sn63pb37焊膏红外再流焊接 1)工艺方法:采用sn63pb37焊膏红外再流焊接,焊接过程中,采用长尾镂空金属夹夹持焊件,保持两个焊接面可靠接触;2)焊接峰值温度:焊料共晶点+(15℃~25℃);3)合金焊层厚度:10μm~20μm;4)焊透率:≥75%。
[0037]
方法2:导电环氧胶粘接1)工艺方法:点胶
→
粘片
→
固化,固化过程中,采用长尾镂空金属夹夹持焊件,保持两个粘接面可靠接触;2)点胶厚度:15μm~25μm,均匀无空洞;;3)固化温度:温度低于组件上所有元器件耐受温度同时,保证导热导电胶充分固化;3.4 微波芯组一的散热凸台四周缝隙填充1)工艺方法:点胶
→
填铜片
→
固化。
[0038]
2)点胶厚度:30μm~50μm,四周缝隙一次性填上薄铜片,粘接胶不要污染薄铜片上侧表面;3)固化温度:温度低于组件上所有元器件耐受温度同时,保证导热导电胶充分固化;3.5 功率器件与散热凸台装配方法1:sn63pb37焊膏焊接1)工艺方法:采用sn63pb37焊膏红外再流焊接或者热板焊接;
2)焊接峰值温度:焊料共晶点+(15℃~25℃);3)合金焊层厚度:10μm~20μm;4)焊透率:≥90%。
[0039]
方法2:半烧结银导热导电胶粘接1)工艺方法:点胶
→
粘片
→
固化(半烧结);2)点胶厚度:5μm~15μm,均匀无空洞;3)固化温度:保证导热导电胶充分固化(半烧结)且低于组件上所有元器件耐受温度。
[0040]
以上所述仅是本发明的优选实施方式,应当指出,对于本技术领域的普通技术人员来说,在不脱离本发明技术原理的前提下,还可以做出若干改进和变形,这些改进和变形也应视为本发明的保护范围。