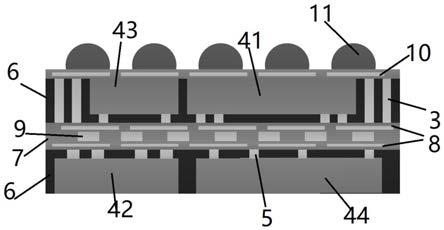
1.本发明涉及集成电路封装技术领域,特别涉及一种模块化封装结构及方法。
背景技术:2.现有的异质基板集成结构的制备方法,一般通过多层异质基板和有机金属布线层进行线路布置和信号互连,然后将多个功能芯片贴于一面,通过空间折叠的形式实现立体式的三维集成。该方法由于采用多层异质基板和有机金属布线层,所以在三维折叠后z方向上的尺寸会很大,这对当前需要的小尺寸来说,缩小x、y方向的同时大大增加z方向上的尺寸厚度,这无法有效的减小结构件的封装体积,提高微系统集成度。而且在工作时,由于多芯片导致发热量较大,因此,其折叠弯曲处的多层异质基板和有机布线层容易因此而老化损坏。
3.pip(package in package,堆叠封装)一般称堆叠封装,又称封装内的封装,还称器件内置器件。封装内芯片通过金线键合堆叠到基板上,同样的堆叠,通过金线再将两个堆叠之间的基板键合,然后整个封装成一个元件便是pip(器件内置器件)。pip封装的优点:外形高度较低、可以采用标准的smt电路板装配工艺、单个器件的装配成本较低。pip封装的局限性:由于在封装之前单个芯片不可以单独测试,所以总成本会高(封装良率问题);事先需要确定存储器结构,器件只能有设计服务公司决定,没有终端使用者选择的自由。
4.pop(package on package,堆叠组装)一般称堆叠组装,又称封装上的封装,还称元件堆叠装配。在底部元器件上面再放置元器件,逻辑加存储通常为2~4层,存储型pop可达8层。pop封装的优点:由于装配前各个器件可以单独测试,保障了更高的良品率,总的堆叠装配成本可降至最低;器件的组合可以由终端使用者自由选择,便于产品的灵活设计和升级、有不同的供应商可以选择。pop与pip相比,外形高度会稍微高些、需要额外的堆叠工艺。总之,如图1所示,现有的pop/pip结构中,模块1与模块2之间通过锡球21实现上下层的连接,其芯片塑封在塑封层中,使用倒贴方式实现上下层堆叠,但虽然pop性能优越,但外形高度相对于pip较高。
技术实现要素:5.本发明的目的在于提供一种模块化封装结构及方法,以解决现有的pop虽然性能优越但外形高度相对较高的问题。
6.为解决上述技术问题,本发明提供一种模块化封装结构,包括:
7.堆叠布置的多个重构晶圆模块,每个重构晶圆模块与其他重构晶圆模块的相对面中至少一面具有光刻胶导电连接体;
8.所述光刻胶导电连接体包括最外侧的光刻胶层及第一重新布线层;
9.所述第一重新布线层将各个重构晶圆模块的电性引出至与光刻胶层位于同一平面的凸点;
10.各个重构晶圆模块的光刻胶层通过晶圆级键合融合为一体,各个重构晶圆模块的
凸点通过晶圆级键合形成电连接;
11.至少一个重构晶圆模块的电性通过第三重新布线层引出。
12.本发明还提供一种模块化封装方法,包括:
13.将多个重构晶圆模块堆叠布置,其中,每个重构晶圆模块之间通过光刻胶导电连接体进行电连接;
14.所述光刻胶导电连接体包括光刻胶层及第一重新布线层;
15.将所述第一重新布线层将各个重构晶圆模块的电性引出至与光刻胶层位于同一平面的凸点;
16.将各个重构晶圆模块的光刻胶层通过晶圆级键合融合为一体,将各个重构晶圆模块的凸点通过晶圆级键合形成电连接;
17.将至少一个重构晶圆模块的电性通过第三重新布线层引出。
18.可选的,在所述的模块化封装方法中,每个重构晶圆模块的制作包括:
19.在基板上形成释放层,在释放层上形成金属连接柱和第一芯片,
20.形成塑封层,所述塑封层覆盖所述第一芯片和金属连接柱;
21.对所述塑封层进行加热,然后对所述塑封层进行减薄,直至暴露出第一芯片的ubump和金属连接柱;
22.在塑封层上形成光刻胶导电连接体;
23.将该重构晶圆模块通过其光刻胶导电连接体与其他重构晶圆模块的光刻胶导电连接体进行电连接;
24.去除释放层及基板;
25.在第一芯片被暴露出的表面上形成第三重新布线层、焊盘、焊点及焊球中的一种或多种。
26.可选的,在所述的模块化封装方法中,在塑封层上形成光刻胶导电连接体包括:
27.在塑封层上沉积第一介质层,在第一介质层上形成第一金属层,在第一金属层上形成第二介质层,在第二介质层上刻蚀,暴露出第一金属层,在第二介质层上形成第二金属层,在第二金属层上形成光刻胶层;
28.对光刻胶层进行抛光。
29.可选的,在所述的模块化封装方法中,将该重构晶圆模块通过其光刻胶导电连接体与其他重构晶圆模块的光刻胶导电连接体进行电连接包括:
30.采用键合机工艺,所述键合机工艺的上下级具有真空吸附功能,使重构晶圆模块键合时保持水平。
31.可选的,在所述的模块化封装方法中,所述第一重新布线层的金属线宽度小于2微米,所述第二重新布线层的金属线宽度为2~10微米,所述第三重新布线层的金属线宽度为2~10微米。
32.在本发明提供的模块化封装结构及方法中,通过将多个重构晶圆模块堆叠布置,其中,每个重构晶圆模块之间通过包括光刻胶层及第一重新布线层的光刻胶导电连接体进行电连接,实现了重构晶圆模块通过小尺寸的光刻胶导电连接体以及第一重新布线层连接,避免了现有的pop/pip结构中通过锡球实现上下层的连接,避免了pop贴片厚度以及尺寸的限制,可以实现更薄芯片,更大尺寸芯片的封装,其封装产品相比于pop结构可以更薄
更大,集成具有多样性。
33.另外,多个重构晶圆模块通过晶圆级键合方式,实现上下层的i/o传输,避免了现有的pop/pip结构中通过锡球实现上下层的连接,满足重构晶圆模块之间的高速传播,能够满足部分产品的高速传播要求。
34.另外,第一重新布线层的金属线宽度小于2微米,可代替部分pop/pip产品,封装产品相比于pop结构可以更薄更大,集成更具有多样性。
附图说明
35.图1是现有的块化封装结构示意图;
36.图2是本发明一实施例模块化封装结构示意图;
37.图3是本发明一实施例模块化封装结构示意图;
38.图4是本发明一实施例模块化封装方法的流程示意图;
39.图中所示:1
‑
基板;2
‑
释放层;3
‑
金属连接柱;4
‑
芯片;5
‑
ubump;6
‑
塑封层;7
‑
第一介质层/第二介质层/光刻胶层;8
‑
第一金属层;9
‑
第二金属层;10
‑
第二重新布线层/第三重新布线层;11
‑
焊球。
具体实施方式
40.以下结合附图和具体实施例对本发明提出的模块化封装结构及方法作进一步详细说明。根据下面说明和权利要求书,本发明的优点和特征将更清楚。需说明的是,附图均采用非常简化的形式且均使用非精准的比例,仅用以方便、明晰地辅助说明本发明实施例的目的。
41.另外,除非另行说明,本发明的不同实施例中的特征可以相互组合。例如,可以用第二实施例中的某特征替换第一实施例中相对应或功能相同或相似的特征,所得到的实施例同样落入本申请的公开范围或记载范围。
42.本发明的核心思想在于提供一种模块化封装结构及方法,以解决现有的pop虽然性能优越但外形高度相对较高的问题。
43.为实现上述思想,本发明提供了一种模块化封装结构及方法,封装结构包括:堆叠布置的多个重构晶圆模块,每个重构晶圆模块与其他重构晶圆模块的相对面中至少一面具有光刻胶导电连接体;所述光刻胶导电连接体包括最外侧的光刻胶层及第一重新布线层;所述第一重新布线层将各个重构晶圆模块的电性引出至与光刻胶层位于同一平面的凸点;各个重构晶圆模块的光刻胶层通过晶圆级键合融合为一体,各个重构晶圆模块的凸点通过晶圆级键合形成电连接;至少一个重构晶圆模块的电性通过第三重新布线层引出。
44.本发明提供一种模块化封装结构,包括:堆叠布置的多个重构晶圆模块,每个重构晶圆模块与其他重构晶圆模块的相对面中至少一面具有光刻胶导电连接体;所述光刻胶导电连接体包括最外侧的光刻胶层7及第一重新布线层10;所述第一重新布线层10将各个重构晶圆模块的电性引出至与光刻胶层7位于同一平面的凸点;各个重构晶圆模块的光刻胶层7通过晶圆级键合融合为一体,各个重构晶圆模块的凸点通过晶圆级键合形成电连接;至少一个重构晶圆模块的电性通过第三重新布线层10引出。
45.本发明还提供一种模块化封装方法,包括:将多个重构晶圆模块堆叠布置,其中,
每个重构晶圆模块之间通过光刻胶导电连接体进行电连接;所述光刻胶导电连接体包括光刻胶层7及第一重新布线层10;将所述第一重新布线层10将各个重构晶圆模块的电性引出至与光刻胶层7位于同一平面的凸点;将各个重构晶圆模块的光刻胶层7通过晶圆级键合融合为一体,将各个重构晶圆模块的凸点通过晶圆级键合形成电连接;将至少一个重构晶圆模块的电性通过第三重新布线层10引出。
46.在本发明的一个实施例中,在所述的模块化封装方法中,每个重构晶圆模块的制作包括:在基板1上形成释放层2,在释放层2上形成金属连接柱3和第一芯片4,形成塑封层6,所述塑封层6覆盖所述第一芯片4和金属连接柱3;对所述塑封层6进行加热,然后对所述塑封层6进行减薄,直至暴露出第一芯片4的ubump 5和金属连接柱3;在塑封层6上形成光刻胶导电连接体;将该重构晶圆模块通过其光刻胶导电连接体与其他重构晶圆模块的光刻胶导电连接体进行电连接;去除释放层2及基板1;在第一芯片4被暴露出的表面上形成第三重新布线层10、焊盘、焊点及焊球11中的一种或多种。
47.在本发明的一个实施例中,在所述的模块化封装方法中,在塑封层6上形成光刻胶导电连接体包括:在塑封层6上沉积第一介质层7,在第一介质层7上形成第一金属层8,在第一金属层8上形成第二介质层7,在第二介质层7上刻蚀,暴露出第一金属层8,在第二介质层7上形成第二金属层9,在第二金属层9上形成光刻胶层7;对光刻胶层7进行抛光。
48.在本发明的一个实施例中,在所述的模块化封装方法中,将该重构晶圆模块通过其光刻胶导电连接体与其他重构晶圆模块的光刻胶导电连接体进行电连接包括:采用键合机工艺,所述键合机工艺的上下级具有真空吸附功能,使重构晶圆模块键合时保持水平。可选的,在所述的模块化封装方法中,所述第一重新布线层10的金属线宽度小于2微米,所述第二重新布线层10的金属线宽度为2~10微米,所述第三重新布线层10的金属线宽度为2~10微米。
49.本发明提供一种模块化封装结构的实施例,包括:堆叠布置的多个重构晶圆模块,每个重构晶圆模块与其他重构晶圆模块的相对面中至少一面具有光刻胶导电连接体;所述光刻胶导电连接体包括光刻胶层及第一重新布线层。
50.本发明还提供一种模块化封装方法的实施例,包括:将多个重构晶圆模块堆叠布置,其中,每个重构晶圆模块之间通过光刻胶导电连接体进行电连接;所述光刻胶导电连接体包括光刻胶层7及第一重新布线层(包括第一介质层、第一金属层8、第二介质层及第二金属层9)。
51.在本发明的一个实施例中,在所述的模块化封装方法中,每个重构晶圆模块的制作包括:在基板1上形成释放层(也可以称为临时键合层)2,在释放层2上形成第一有源结构;在第一有源结构上形成光刻胶导电连接体;将该重构晶圆模块通过其光刻胶导电连接体与其他重构晶圆模块的光刻胶导电连接体进行电连接;去除释放层2及基板1。
52.在本发明的一个实施例中,在所述的模块化封装方法中,所述第一有源结构包括金属连接柱3、芯片4、第二重新布线层10、焊盘及焊点中的一种或多种。
53.在本发明的一个实施例中,在所述的模块化封装方法中,还包括:在释放层上形成第一有源结构后,还包括:形成塑封层6,所述塑封层6覆盖所述第一有源结构;对所述塑封层6进行加热,然后对所述塑封层6进行减薄,直至暴露出能够将第一有源结构的电性引出的部件,例如金属连接柱3及ubump 5。
54.在本发明的一个实施例中,在所述的模块化封装方法中,还包括:在去除释放层2及基板1后,在第一有源结构被暴露出的表面上形成第二有源结构或光刻胶导电连接体,所述第二有源结构包括第三重新布线层10、焊盘、焊点及焊球11中的一种或多种。
55.在本发明的一个实施例中,在所述的模块化封装方法中,在第一有源结构上形成光刻胶导电连接体包括:在第一有源结构上沉积第一介质层7,在第一介质层7上形成第一金属层8,在第一金属层8上形成第二介质层7,在第二介质层7上刻蚀,暴露出第一金属层8,在第二介质层7上形成第二金属层9,在第二金属层9上形成光刻胶层7;对光刻胶层7进行抛光。
56.在本发明的一个实施例中,在所述的模块化封装方法中,将该重构晶圆模块通过其光刻胶导电连接体与其他重构晶圆模块的光刻胶导电连接体进行电连接包括:将该重构晶圆模块通过其光刻胶导电连接体与其他重构晶圆模块的光刻胶导电连接体进行晶圆级键合,采用键合机工艺,所述键合机工艺的上下级具有真空吸附功能,使重构晶圆模块键合时保持水平。
57.在本发明的一个实施例中,在所述的模块化封装方法中,所述第一重新布线层(第一金属层8和/或第二金属层9)的金属线宽度小于2微米,所述第二重新布线层10的金属线宽度为2~10微米,所述第三重新布线层10的金属线宽度为2~10微米。
58.在本发明提供的模块化封装结构及方法中,通过将多个重构晶圆模块堆叠布置,其中,每个重构晶圆模块之间通过包括光刻胶导电连接体及第一重新布线层的光刻胶导电连接体进行电连接,实现了重构晶圆模块通过小尺寸的光刻胶导电连接体以及第一重新布线层连接,避免了现有的pop/pip结构中通过锡球实现上下层的连接,避免了pop贴片厚度以及尺寸的限制,可以实现更薄芯片,更大尺寸芯片的封装,其封装产品相比于pop结构可以更薄更大,集成具有多样性。
59.另外,多个重构晶圆模块通过晶圆级键合方式,实现上下层的i/o传输,避免了现有的pop/pip结构中通过锡球实现上下层的连接,满足重构晶圆模块之间的高速传播,能够满足部分产品的高速传播要求。
60.另外,第一重新布线层的金属线宽度小于2微米,可代替部分pop/pip产品,封装产品相比于pop结构可以更薄更大,集成更具有多样性。
61.如图2所示,其为重构晶圆模块键合产品一集成方案:上下模块通过扇出工艺进行晶圆重构,后续使用光刻胶导电连接体(bcb/cu)工艺实现实现上下重构晶圆的键合,其中扇出重构晶圆时使用info工艺,表面可以形成2/2um线宽线距的重新布线层,满足芯片间高速信号传播;多芯片重构晶圆模块也可以与si wafer键合,如图3所示。
62.如图4所示,工艺路线可简单归纳如下:取一载玻璃作为基板1,涂覆释放层2,释放层2满足高温工艺,并且最终释放无残留;制作金属连接柱3(mega pillar),金属连接柱3高度高于后续所贴芯片4的ubump 5高度;使用正贴工艺,贴好带有ubump 5的芯片4;对前述已贴芯片的重构晶圆模块进行塑封形成塑封层6,并且烘烤后进行塑封层6的减薄工艺,露出金属连接柱3以及ubump 5;形成第一介质层7、第一金属层8、第二介质层7和第二金属层9,另外最外层使用光刻胶层7(bcb)作为第三介质层,通过抛光(cmp)工艺进行光刻胶导电连接体(bcb/cu)的表面抛光,满足bcb/cu键合需求;取另外一重构晶圆模块进行晶圆级键合,其中,键合机工艺时其上下模块具有真空吸附功能,使重构晶圆模块键合时保持水平;键合
片两端基板1进行激光解键合,金属连接柱3处无胶残留;金属连接柱3面形成第三重新布线层10,植球形成焊球11;将模块化封装结构进行切割,分选。
63.重构晶圆模块的预清洁和干燥,应用在重构晶圆模块上的聚合物,处理重构晶圆模块表面,粘附启动剂(ap3000),光刻胶旋转、涂层和软化、在流动的氮气中烘烤1~5分钟,烘烤温度170℃。在250℃下对光刻胶进行60秒或以上的部分固化,图案金属/聚合物粘结接口抛光,光刻胶导电连接体抛光、清洁、重构晶圆模块对齐,然后进行重构晶圆模块粘结工艺,工艺条件如下:真空泵至0.1mtor、温度升至250℃、施加大于0.3mpa的粘结压力、保持不超过60分钟、然后温度升至350℃、保持不超过60分钟、释放粘结压力、冷却重构晶圆模块和卸载,进行重构晶圆模块减薄工艺,工艺条件如下:顶部重构晶圆模块背面研磨,抛光和使用四甲酰胺氢氧化物进行蚀刻,形成tsv。重复上述步骤。
64.去除重构晶圆模块表面的颗粒、污染和水分,均匀地应用光刻胶(<2%则不均匀),粘附促进剂可增强重构晶圆模块表面与聚合物粘合剂之间的粘附性,软化烘烤去除溶剂和挥发性物质,硬化表面,使表面在重构晶圆模块对齐过程中允许表面接触,部分固化结果>55%则光刻胶相融连接,光刻胶导电连接体抛光工艺,形成或暴露金属粘结垫、金属连接柱和光刻胶导电连接体的粘合表面,抛光和清洁,以形成在模块上的清洁表面,模块与预图案对齐标记对齐,能够在所需位置形成tsv,无缝粘合两个重构晶圆模块,真空防止金属和粘合剂氧化,可使光刻胶聚合(交联或固化),强制粘合表面的亲密接触,将光刻胶处理到几乎达到100%的相融,能够使铜在粘结接口上进行插液和颗粒生长,并消除粘结接口上的小空隙。可选的退火工艺能够缩短粘合时间,能够形成具有微米直径和相对低高度
‑
直径长宽比的高密度tsv,将模块中的有源结构连接到下一层和/或从模块中带出能够将电性引出的部件,形成三维结构的多个层。
65.综上,上述实施例对模块化封装结构及方法的不同构型进行了详细说明,当然,本发明包括但不局限于上述实施中所列举的构型,任何在上述实施例提供的构型基础上进行变换的内容,均属于本发明所保护的范围。本领域技术人员可以根据上述实施例的内容举一反三。
66.本说明书中各个实施例采用递进的方式描述,每个实施例重点说明的都是与其他实施例的不同之处,各个实施例之间相同相似部分互相参见即可。对于实施例公开的系统而言,由于与实施例公开的方法相对应,所以描述的比较简单,相关之处参见方法部分说明即可。
67.上述描述仅是对本发明较佳实施例的描述,并非对本发明范围的任何限定,本发明领域的普通技术人员根据上述揭示内容做的任何变更、修饰,均属于权利要求书的保护范围。