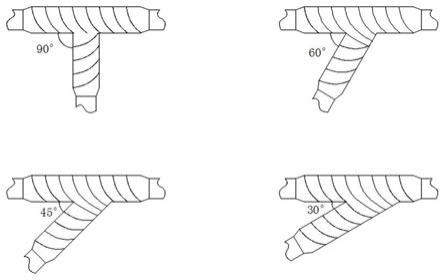
一种免维护高压电缆热熔t型接头的制造方法
技术领域
1.本发明涉及电缆连接技术领域,具体是指一种免维护高压电缆热熔t型接头的制造方法。
背景技术:2.随着城市电力需求的不断增加,以及城市电网入地改造不断进行,电力电缆的用量越来越大。但是,电缆线路的故障次数也在节节攀升,国内某城市2010年对10kv配网电力电缆故障率调查报告指出,电缆中间接头故障率为45.3%,终端头故障率为6.6%,电缆本体故障率为4.4%。因此,传统的中压电缆附件在使用过程中仍然存在部分问题,尤其是南方地区6~35kv中压电力电缆线路,由于电缆沿线环境复杂,雨水较多,很多电缆线路都长期浸泡在水中,传统的中压电缆接头由于缺乏可靠的防水防潮保护,水分或潮气侵入电缆,导致中压电力电缆线路接头位置故障率较高,因此,熔融接头技术开始被应用于南方雨水较多的地区陆地电力线路使用。但由于熔融只是近几年才在陆地电缆中使用,只存在两端电缆的熔融接头,由于熔融接头在陆地电缆的制备工艺相当不成熟,其制备的熔融接头需要定期检查和维护,为陆地使用熔融接头的使用带来的极大的不便,而三根电缆熔融接头通过现有的熔融接头技术则根本无法成功制得,即使将三根电缆硬性焊接在一起,其稳定性,电阻大小均为无法达到正常电缆接头的实际使用标准,因此现目前还未发现能够将三根电缆熔融焊接在一起的制备工艺。
技术实现要素:3.针对现有技术的不足,本发明的目的在于提供一种适用于陆地电缆使用,且工艺新颖,能够对三根电缆进行焊接的免维护高压电缆热熔t型接头的制造方法。
4.为了实现上述目的,本发明通过下述技术方案实现:一种免维护高压电缆热熔t型接头的制造方法,包括以下步骤:
5.(1)电缆焊接:将三根电缆的线芯呈t形以银基钎焊的方式焊接;
6.(2)导体屏蔽恢复:在电缆线芯表面绕包半导电热熔带;
7.(3)绝缘恢复:在半导电热熔带外层绕包主绝缘层,进行加热熔接,并急速冷却,冷却时间不大于2h;
8.(4)绝缘屏蔽恢复:冷却主绝缘层后,在其表面绕包半导电自粘胶带;
9.(5)金属屏蔽及隔离套恢复;接着以铜箔带粘贴搭接两端铜屏蔽层;
10.(6)铠装及外护套恢复:绕包第一层防水复合带,完全搭接电缆各端口外护套;地线搭接各端口的钢铠:绕包第二层防水复合带,完全搭接电缆端口外护套层。
11.本技术方案首创了三根电缆的焊接方法,由于三根电缆的焊接在一起,其焊点相较于两根电缆焊接的焊点更为复杂,且具有更大的电阻,因此,采用传统两根电缆使用放热焊焊接的接头,其电阻过大,无法达到国家标准(gb/t1270),且由于电阻过大,通电后产生的电热较高,两根电缆的绝缘保护方法也无法适用,点着火的风险极高。因此,本技术方案
的主要技术点如下:
12.第一,三根电缆接头的焊接角度,经过大量实验,最终测得,三根电缆接头处呈t型的方式焊接在一起,其在保证稳固性的情况下,焊点处电阻最小,且焊接难度相对较低;
13.第二,三根电缆接头的焊接方式,采用分层银基钎焊的方式焊接,相较于一般导体的放热焊、分层氩弧焊、分层银钎焊、铜焊的焊方式,其焊接处的焊点电阻最低,基本能够满足国家标准;
14.第三,焊接完成后,三根电阻的焊点处结构较为复杂,且焊点处电阻还是略高于两根电缆的焊接方式,因此在绝缘恢复过程中,采用急速冷却的方式,加强绝缘层的固化效果,提高绝缘层的密度、拉伸轻度、断裂拉升应变百分比,以满足三根电缆焊接处焊点的绝缘要求。
15.为了更好地实现本发明的方法,进一步地,所述步骤(1)中,电缆焊接的具体过程为:
16.(1.1)对需要进行接头的三根电缆的线芯进行预处理,并定制t形石墨模具;
17.(1.2)将三根电缆的线芯置于定制的t形石墨模具内,加入含银量为25~35%的钎料,以及用于钎焊的焊粉;所述焊粉型号为qj101;
18.(1.3)采用电阻焊机通过分层焊接的方式熔接线芯,并处理线芯熔接点至光滑无凸起无毛刺。
19.为了更好地实现本发明的方法,进一步地,所述步骤(1.1)中,所述电缆的线芯预处理的过程为:将线芯的主绝缘消出50~~60mm的铅笔头,并打磨漏出内半导电层10~20mm。
20.为了更好地实现本发明的方法,进一步地,所述(1.2)中,将三根电缆的线芯置于定制的t形石墨模具内之前,需要对石墨模具和需要焊接的电缆线芯分别加热除潮,石墨加热除潮的时间为5分钟,电缆线芯加热除潮的时间为1分钟。
21.为了更好地实现本发明的方法,进一步地,所述步骤(2)中,所述导体屏蔽恢复的具体过程为:在电缆线芯表面绕包两层半导电热熔带,并完全搭接线芯打磨出的内半导电层5~8mm。
22.为了更好地实现本发明的方法,进一步地,所述步骤(3)中,所述绝缘恢复过程中的主绝缘层主要由最内部的聚乙烯热融带、中间的硅橡胶自融带,外部的铝箔带构成,主绝缘层缠绕力度为280n/
㎝2,绕包过程无气隙产生。
23.为了更好地实现本发明的方法,进一步地,所述聚乙烯热融带的绕包厚度为2~3mm,所述硅橡胶自融带的宽度为100mm,所述铝箔带的厚度为0.5mm。
24.为了更好地实现本发明的方法,进一步地,所述步骤(3)中,所述绝缘恢复过程中,对主绝缘层加热熔接的温度为160~200℃。
25.为了更好地实现本发明的方法,进一步地,所述步骤(3)中,所述绝缘恢复过程中,急速冷却的方式为,在主绝缘层外部套设冷却水袋,所述冷却水袋内设置有进水口和出水口,通过冷却水袋内不断流动的冷却水对主绝缘层进行冷却。
26.为了更好地实现本发明的方法,进一步地,所述步骤(5)中,所述金属屏蔽及隔离套恢复过程中,所述铜箔带的厚度为0.5mm。
27.本发明与现有技术相比,具有以下优点及有益效果:
28.(1)本发明提供了三根电缆的熔融接头的焊接方法,从焊接角度、焊接方式两个方面综合考量,使得三根电缆的熔融接头的稳定性,电阻大小均符合国家标准,实现三根电缆的熔融焊接;
29.(2)本发明的方法在绝缘恢复过程中,急速冷却主绝缘层,使得主绝缘层的物理性质得到显著提升,使得该绝缘屏蔽的主绝缘层能够满足三根电缆熔融接头的绝缘防护工作,另外,急速冷却主绝缘层,还能缩短电缆焊接作业的整体时间,为两根电缆熔融接头的焊接也提供了积极的借鉴意义;
30.(3)本发明首创三根电缆接头的焊接方法,该方法制备得到的三电缆熔融接头符合国家标准,能够极大程度减少两根电缆中间接头的使用,减低电缆线路的复杂性,间接减低电缆中间接头的故障率,为电力电缆线路的铺设提供了新的发展方向。
附图说明
31.通过阅读参照以下附图对非限制性实施例所作的详细描述,本发明的其他特征、目的和优点将会变得更为明显:
32.图1为本发明中三根电缆接头不同焊接角度的示意图;
33.图2为本发明中三根电缆接头不同焊接角度与熔融接头电阻线性关系;
具体实施方式
34.为使本发明的目的、工艺条件及优点作用更加清楚明白,结合以下实施实例,对本发明作进一步详细说明,但本发明的实施方式不限于此,在不脱离本发明上述技术思想情况下,根据本领域普通技术知识和惯用手段,做出各种替换和变更,均应包括在本发明的范围内,此处所描述的具体实施实例仅用以解释本发明,并不用于限定本发明。
35.实施例1:
36.本实施例提供了一种免维护高压电缆热熔t型接头的制造方法,具体包括以下步骤:
37.(1)电缆焊接:将三根电缆的线芯呈t形以银基钎焊的方式焊接;
38.(2)导体屏蔽恢复:在电缆线芯表面绕包半导电热熔带;
39.(3)绝缘恢复:在半导电热熔带外层绕包主绝缘层,进行加热熔接,并急速冷却,冷却时间不大于2h;
40.(4)绝缘屏蔽恢复:冷却主绝缘层后,在其表面绕包半导电自粘胶带;
41.(5)金属屏蔽及隔离套恢复:接着以铜箔带粘贴搭接两端铜屏蔽层;
42.(6)铠装及外护套恢复:绕包第一层防水复合带,完全搭接电缆各端口外护套;地线搭接各端口的钢铠;绕包第二层防水复合带,完全搭接电缆端口外护套层。
43.实施例2:
44.本实施例在上述实施例的基础上,进一步限定步骤(1)中,电缆焊接的具体过程,具体为:
45.(1.1)对需要进行接头的三根电缆的线芯进行预处理,并定制t形石墨模具;
46.(1.2)将三根电缆的线芯置于定制的t形石墨模具内,加入含银量为25~35%的钎料,以及用于钎焊的焊粉;所述焊粉型号为qj101;
47.(1.3)采用电阻焊机通过分层焊接的方式熔接线芯,并处理线芯熔接点至光滑无凸起无毛刺。
48.其中,所述步骤(1.1)中,所述电缆的线芯预处理的过程为:将线芯的主绝缘消出50~~60mm的铅笔头,并打磨漏出内半导电层10~20mm;所述(1.2)中,将三根电缆的线芯置于定制的t形石墨模具内之前,需要对石墨模具和需要焊接的电缆线芯分别加热除潮,石墨加热除潮的时间为5分钟,电缆线芯加热除潮的时间为1分钟。本实施例其他部分与上述实施例相同,这里不在赘述。
49.实施例3:
50.本实施例在上述实施例的基础上,进一步限定步骤(2)中,导体屏蔽恢复的具体过程,具体为:在电缆线芯表面绕包两层半导电热熔带,并完全搭接线芯打磨出的内半导电层5~8mm。本实施例其他部分与上述实施例相同,这里不在赘述。
51.实施例4:
52.本实施例在上述实施例的基础上,进一步限定步骤(3)的具体内容,其中,所述绝缘恢复过程中的主绝缘层主要由最内部的聚乙烯热融带、中间的硅橡胶自融带,外部的铝箔带构成,主绝缘层缠绕力度为280n/
㎝2,绕包过程无气隙产生;所述聚乙烯热融带的绕包厚度为2~3mm,所述硅橡胶自融带的宽度为100mm,所述铝箔带的厚度为0.5mm;所述绝缘恢复过程中,对主绝缘层加热熔接的温度为160~200℃。本实施例其他部分与上述实施例相同,这里不在赘述。
53.实施例5:
54.本实施例在上述实施例的基础上,进一步限定步骤(3)中,绝缘恢复过程中,急速冷却的方式为水冷却,具体为:在主绝缘层外部套设冷却水袋,所述冷却水袋内设置有进水口和出水口,通过冷却水袋内不断流动的冷却水对主绝缘层进行冷却。本实施例其他部分与上述实施例相同,这里不在赘述。
55.实施例6:
56.本实施例在上述实施例的基础上,进一步限定步骤(5)的具体内容,所述金属屏蔽及隔离套恢复过程中,所述铜箔带的厚度为0.5mm。本实施例其他部分与上述实施例相同,这里不在赘述。
57.实施例7:
58.本实施例为了验证三根电缆接头的焊接角度对焊点电阻的影响,特别做如下实验:
59.以30
°
、45
°
、60
°
、90
°
进行三根电缆接头的焊接,如图1所示,导体直流电阻试验按照gb/t 12706进行,分别测量了不同焊接角度熔融接头电阻,焊接的方式为传统的放热焊,并进行了拓展试验,即验证各种不同的焊接角度对导体电阻的影响。试验结果见表1:
60.表一 熔融接头电阻试验结果表(单位:ω/km)
[0061][0062]
根据表一内容可知,焊接角度对熔融接头电阻的影响较为明显,但是熔融接头电阻与焊接角度的大小并不呈现明显的规律线性关系,为了探寻最佳焊接角度,实际操作过程中,试验了30个焊接角度(即3
°
、6
°……
90
°
),其实验结果图2所示。
[0063]
根据图2可知,以目前试验结果最优的焊接角度为90
°
,且以90
°
焊接熔融接头的电阻无法满足国家标准,不能作为常规电缆接头进行使用。
[0064]
实施例8:
[0065]
本实施例为了验证三根电缆接头的焊接方式,根据上述实施例可知,其三根电缆接头以90
°
焊接时,熔融接头的电阻最小,因此,本实施例中,三根电缆接头均以90
°
焊接,分别采用放热焊、分层氩弧焊、分层银钎焊、铜焊的焊方式进行分组焊接,然后分别测量了电缆本体导体以及熔融接头电阻,并进行了拓展试验,即验证各种不同的焊接方式对熔融接头电阻的影响。试验结果如表2所示:
[0066]
表二 熔融接头电阻试验结果表(单位:ω/km)
[0067][0068]
根据表二内容可知,导体焊接后,导体直流电阻均有不同程度的增加现象,其中以分层银钎焊最好,其熔融接头的电阻基本满足国家标准,可以作为电缆接头的实际操作使用。另外,放热焊效果最差,究其原因是焊药中有大量的杂质引入焊接后的导体,导致电阻增加。
[0069]
实施例9:
[0070]
由于三根电阻的焊点处结构较为复杂,且焊点处电阻还是略高于两根电缆的焊接方式,因此在绝缘恢复过程中,对绝缘层的物理参数要求相对较高,本实施例利用高热聚乙烯冷却后,密度和拉升强度会提高的技术原理,分别使用水冷、风冷、自然冷却三种方式,探究三种冷却方式对聚乙烯密度和拉升强度的影响。
[0071]
试验情况具体如下:
[0072]
(1)实验材料:
[0073]
采用交联聚乙烯制备成柱形条(仿绝缘恢复过程中的绝缘层),热压温度为180℃,
预测10分钟,施压(压力10mpa)5分钟。
[0074]
(2)实验分组
[0075]
第一组:自然冷却(空气缓冷);
[0076]
第二组:风冷(空气急冷);
[0077]
第三组:水冷(水急冷)。
[0078]
(3)实验过程:
[0079]
自然冷却(空气缓冷):保压10mpa的情况下,让物料缓慢冷却,冷却至25℃,冷却时间为3小时;
[0080]
风冷(空气急冷):保压10mpa的情况下,对物料外部进行风力吹拂,风速为5~10m/s,加速冷却,冷却至25℃,冷却时间为2小时;
[0081]
自然冷却(空气缓冷):保压10mpa的情况下,在物料外部套设冷却水袋,通过冷却水袋内不断流动的冷却水对物料进行急速冷却,冷却至25℃,冷却时间为1小时;
[0082]
(4)实验结果:
[0083]
结果如表三所示:
[0084]
表三 冷却方式对绝缘层材质(交联聚乙烯)物理性质影响
[0085]
冷却方式密度(g/cm3)拉升强度(mpa)断裂拉升应变(%)自然冷却(空气缓冷)0.93533.1861.8风冷(空气急冷)0.95735.9908.8水冷(水急冷)0.97938.4967.4
[0086]
通过表三内的数据可知:急冷时试样拉伸强度、断裂拉伸应变、密度明显强于缓冷的试样,说明在绝缘恢复过程中,对绝缘层进行急速冷却,能够显著提高绝缘层的物理性质,使其对内部电缆进行更好的防护。
[0087]
尽管已经示出和描述了本发明的实施例,本领域的普通技术人员可以理解:在不脱离本发明的原理和宗旨下可以对这些实施例进行多种变化、修改、替换和变型,本发明的范围由权利要求及其等同物限定。