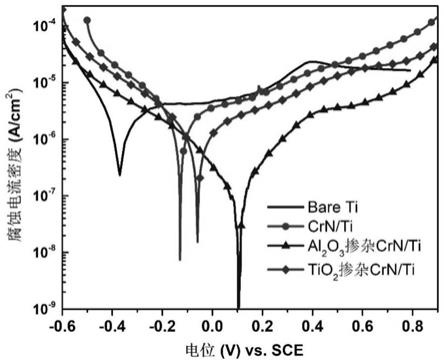
1.本发明属于燃料电池技术领域,尤其涉及一种用于燃料电池金属双极板的薄膜及其制备方法。
背景技术:2.面对日益严峻的环境污染和能源危机问题,发展一种无污染可再生的新型能源越来越受到人们的重视。氢能由于反应效率高,反应副产物无污染,被认为是最有潜力代替化石燃料可再生的新型能源之一。质子交换膜燃料电池作为一种新型动力电池,是以氢能为燃料将氢能直接转化为电能的新型能量转化装置,具有有碳排放量低、能量转换效率高、工作温度低(<100摄氏度)、启动速度快等优点,被认为是用于车载能源和分布式发电站的理想装置。
3.双极板是质子交换膜燃料电池核心组件之一,它起到将燃料电池中的阳极燃料和阴极氧分开以提供流场并为电堆传导电流的作用。为实现上述功能,双极板应具有良好的导电性和导热性、高耐腐蚀性和抗气体渗透性、良好的机械性能和低成本等特性。
4.在众多双极板材料中,金属双极板凭借优异的导电、导热,阻气及机械加工性能,越来越受到人们的青睐,丰田mirai、本田clarity和现代nexo等乘用车均采用金属双极板。然而,未经处理的金属双极板在燃料电池工作时容易腐蚀,从而严重影响燃料电池的输出功率和使用寿命,目前最常用的改进策略是在金属双极板表面镀制一层既耐蚀又导电的薄膜,但一般情况下薄膜的导电性越优异,耐腐蚀性越差,这是限制金属双极板表面改性薄膜发展的最大瓶颈所在。
5.因此,开发一种兼具高耐腐蚀性、高导电性、寿命长且制备简单的一种pemfc金属双极板表面改性薄膜,是目前燃料电池领域丞待解决的难题。目前pemfc金属双极板表面改性薄膜的研究方向主要分为两大类:一是金属基薄膜,例如贵金属涂层(au、pt、ag等)、金属化合物涂层(tin、ticn、crn);二是碳基涂层,如石墨涂层、导电聚合物涂层、类金刚石涂层等。
技术实现要素:6.鉴于上述的分析,本发明通过磁控共溅射的方式,调节基底偏压和掺杂氧化物种类,旨在提供一种氧化物掺杂改性的过渡金属氮化物薄膜,其兼具高耐腐蚀、高导电及长寿命的特性。本发明的目的主要是通过以下技术方案实现的:
7.本发明提供了一种用于燃料电池金属双极板的薄膜,该薄膜由氧化物掺杂氮化物组成,氧化物为al2o3、tio2、zro2、sio2中一种或两种以上物质混合而成,氮化物为crn、tin、nbn、zrn中的一种;
8.该薄膜中氧化物的百分含量为1
‑
5at%,其余为氮化物。
9.进一步地,所述薄膜的厚度为100
‑
500nm。
10.本发明还提供了用于燃料电池金属双极板的薄膜的制备方法,该方法包括如下步
骤:
11.步骤一:清洗金属衬底,打磨金属单质靶材;
12.步骤二:将金属衬底、金属单质靶材和氧化物靶材安装于磁控溅射镀膜机内,进行预溅射;
13.步骤三:将金属衬底接入负偏压,通入氮气和氩气;
14.步骤四:进行磁控溅射,金属衬底表面沉积氧化物和氮化物,形成薄膜。
15.进一步地,所述步骤一中,金属衬底的材质为不锈钢、钛、镍、铝中的一种;金属单质靶材为cr、ti、nb、zr中的一种。
16.进一步地,所述步骤一中,所述清洗金属衬底的过程包括:依次用去离子水、丙酮溶液超声清洗,再经化学抛光,乙醇清洗。
17.进一步地,所述步骤二中,氧化物靶材为al2o3、tio2、zro2、sio2中的一种或两种以上物质的混合。
18.进一步地,所述预溅射包括:调节氧化物靶材和金属单质靶材的射频功率,关闭靶材挡板,通入氩气,进行预溅射。
19.进一步地,所述步骤三中,负偏压为
‑
140~
‑
60v。
20.进一步地,所述步骤三中,氮气和氩气的流量比为(40~60):20sccm。
21.进一步地,所述步骤四中,磁控溅射过程中,金属氧化物靶材的射频功率为5~30w,金属单质靶材的射频功率为60~100w。
22.与现有技术相比,本发明至少具有如下实用效果之一:
23.1、本发明的用于燃料电池金属双极板的薄膜,质子交换膜燃料电池金属双极板表面改性薄膜具备优异的耐腐蚀性和导电性并且寿命长,疏水性佳,各项指标均满足doe标准,具有很大的应用前景,薄膜制备方法,操作简单,条件易控,易于大规模生产;
24.2、本发明的用于燃料电池金属双极板的薄膜,微量的al2o3等金属氧化物掺入,可以显著提高过渡金属氮化物的耐腐蚀性、导电性、稳定性及疏水性;
25.3、本发明的用于燃料电池金属双极板的薄膜,磁控溅射时基底施加一定的负偏压,有助于改善薄膜成分、提高薄膜膜基结合力,有利于薄膜综合性能提高。
26.本发明的其他特征和优点将在随后的说明书中阐述,并且,部分的特征和优点从说明书中变得显而易见,或者通过实施本发明而了解。本发明的目的和其他优点可通过在所写的说明书以及附图中所特别指出的结构来实现和获得。
附图说明
27.附图仅用于示出具体实施例的目的,而并不认为是对本发明的限制,在整个附图中,相同的参考符号表示相同的部件。
28.图1为不同金属氧化物(al2o3、tio2)掺杂改性crn薄膜的动电位曲线;
29.图2为不同金属氧化物(al2o3、tio2)掺杂改性crn薄膜的接触电阻变化曲线;
30.图3为al2o3不同溅射功率掺杂后crn薄膜的动电位曲线;
31.图4为al2o3不同溅射功率掺杂后crn薄膜的接触电阻变化曲线;
32.图5为al2o3不同溅射功率掺杂后crn薄膜的静电位曲线;
33.图6为al2o3不同溅射功率掺杂后crn薄膜的xrd谱图;
34.图7为不同基底偏压制备的crn薄膜的动电位曲线;
35.图8为不同基底偏压制备的crn薄膜的接触电阻变化曲线;
36.图9为0v、
‑
100v偏压制备的crn薄膜和
‑
100v偏压制备的al2o3掺杂的crn薄膜的接触角图像。
具体实施方式
37.下面结合附图来具体描述本发明的优选实施例,其中,附图构成本发明一部分,并与本发明的实施例一起用于阐释本发明的原理,并非用于限定本发明的范围。
38.一种用于燃料电池金属双极板的薄膜,如图1
‑
9所示,该薄膜由氧化物掺杂氮化物组成,氧化物为al2o3、tio2、zro2、sio2中一种或两种以上物质混合而成,氮化物为crn、tin、nbn、zrn中的一种。
39.薄膜由金属氧化物靶材和过渡金属靶材在含氮气体中反应溅射得到,薄膜中,氧化物的掺杂量为≤5at%,优选为1~2at%,其余为氮化物。
40.薄膜的厚度为100
‑
500nm,优选为150
‑
350nm,更优选为200nm。
41.本发明的薄膜用于质子交换膜燃料电池金属双极板表面,具有良好的耐腐蚀性和导电性能。
42.一种用于燃料电池金属双极板的薄膜的制备方法,该方法包括如下步骤:
43.步骤一:清洗金属衬底,打磨金属单质靶材;
44.步骤二:将金属衬底、金属单质靶材和氧化物靶材安装于磁控溅射镀膜机内,进行预溅射;
45.步骤三:将金属衬底接入负偏压,通入氮气和氩气;
46.步骤四:进行磁控溅射,金属衬底表面沉积氧化物和氮化物,形成薄膜。
47.具体的,所述步骤一中,金属衬底的材质为不锈钢、钛、镍、铝中的一种;其中,所述不锈钢包括304、316、316l、310、904l,金属衬底的材质也可以为钛基合金、镍基合金、铝基合金板,金属衬底优选为钛片,金属衬底厚度为0.05~0.2mm,优选为0.1mm
‑
0.2mm。示例性的,钛片尺寸为50mm
×
50mm。
48.金属单质靶材为cr、ti、nb、zr中的一种。优选为cr、ti、nb中的一种,更优选为cr。
49.为了获得优质的复合薄膜,首先要清洗钛片衬底,除去钛片衬底表面的天然氧化层,得到清洁、平整的钛表面。
50.所述步骤一中,所述清洗金属衬底的过程包括:依次用去离子水、丙酮溶液超声清洗,再经化学抛光,乙醇清洗。
51.示例性的,按照如下步骤清洗金属衬底:
52.(1)将钛片置于去离子水中进行超声处理20min;
53.(2)在丙酮溶液中进行超声清洗20min;
54.(3)用去离子水冲洗后,使用化学抛光的方式,在10%稀盐酸或者草酸溶液中浸泡6~8小时,然后超声去掉钛片表面钝化层;
55.(4)用去离子水冲洗后,采用乙醇溶液清洗20min。
56.为了去除金属单质靶材表面的氧化物,用细砂纸细致打磨金属单质靶材表面。
57.由于氧化物靶材的主要成分为陶瓷,在空气中很稳定,并且陶瓷材料容易开裂,所
以不需要砂纸打磨预处理。
58.所述步骤二中,将氧化物靶材和金属单质靶材安装在磁控溅射镀膜设备腔室的靶位上,将金属衬底安装在腔室的基底上,所述靶位与金属衬底的距离为60~80mm,优选为70mm,且在安装完毕后需要用万用表检查,以防短路,再进行抽真空处理,进行预溅射。
59.氧化物靶材为al2o3、tio2、zro2、sio2中的一种或多种。优选为al2o3、tio2中一种或者两种,更优选为al2o3。
60.所述预溅射包括:调节氧化物靶材和金属单质靶材的射频功率,关闭靶材挡板,通入氩气,进行预溅射。以进一步清洁靶材表面,清洁完毕后关闭射频电源。
61.具体的,进行预溅射时,金属单质靶材和氧化物靶材的射频功率均为50~100w,优选为80w,溅射时间为15~25min,优选为20min。氩气用量优选为40sccm。
62.所述步骤三中,在磁控溅射时,基底辅助一定负偏压,有助于改善薄膜成分、提高薄膜膜基结合力,有利于薄膜综合性能提高,负偏压为
‑
140~
‑
60v,优选为
‑
120~
‑
80v,更优选为
‑
100v。负偏压的占空比优选为50~70%,优选为60%。
63.需要说明的是,在溅射过程中,金属衬底的负偏压全程处于打开状态。
64.所述步骤三中,氮气和氩气的流量比为(40~60):20sccm,优选为(45~55):20sccm,更优选为50:20sccm。
65.所述步骤四中,磁控溅射过程中,两个溅射靶材均采用射频电源进行溅射,可以预防溅射过程中靶中毒现象。具体的,金属氧化物靶材的射频功率为5~30w,优选为10~25w,更优选为20w;金属单质靶材的射频功率为60~100w,优选为70~90w,更优选为80w。
66.控制薄膜溅射时间为90min。
67.薄膜的形成过程为:
68.一方面,电离后的氩正离子轰击靶材,将氧化物击落,沉积在金属衬底上;另一方面,氩正离子冲击金属单质靶材,将金属单质击落,击落的金属单质与氮气结合形成氮化物,氮化物沉积在金属衬底上。氧化物和氮化物沉积在金属衬底上,形成改性薄膜,正离子冲击改性薄膜,将薄膜表面与金属衬底结合不牢固的物质冲走。
69.需要说明的是,施加偏压时,正离子轰击,其中,正离子绝大部分是氩正离子,也存在少量金属正离子。
70.测试薄膜的耐腐蚀、导电性、稳定性及疏水性能。
71.具体的,耐腐蚀和稳定性分别通过测试金属极板的动电位和静电位曲线得到,使用上海辰华公司生产的电化学工作站chi660e进行测试,其中,动电位曲线的测试电位为
‑
0.6~0.9v,扫速为2mv/s。静电位曲线主要测试在
‑
0.1v和0.6v的电位下,腐蚀电流密度随时间的变化。电解池及三电极购买于天津艾达恒晟有限公司。腐蚀液为0.5m的h2so4溶液。
72.导电性测试是通过施加压力下极板与碳纸接触电阻来反映,接触电阻测试仪器由本组自主搭建而成,主要由贝奇直流低电阻测试仪ch2516b和智取电动压力试验机zq
‑
990b配合使用。
73.疏水性能由东莞市晟鼎精密仪器有限公司生产的接触角测量仪sdc
‑
100s测试水与薄膜的接触角得到。
74.实施例1
75.一种用于燃料电池金属双极板的薄膜的制备方法,该方法包括如下步骤:
76.(1)切取尺寸为50mm
×
50mm
×
0.1mm的钛片进行清洗,氮气吹干后迅速放进磁控溅射镀膜设备(北京泰科诺科技公司生产的jcp500高真空多靶磁控溅射镀膜设备)腔室的基底盘上并进行固定;取al2o3靶和细砂纸打磨过的cr靶,安装在靶位上,使得靶位与基底的距离为70mm,抽真空至5
×
10
‑4pa以下,调节基底的转速为15r/min;
77.(2)调节两靶的射频电源功率为80w,在关闭靶材挡板的情况下,通入氩气40sccm,进行预溅射,进一步清洁靶材表面,20min后关闭射频电源;
78.(3)设置基底偏压为
‑
100v,占空比为60%,并启动;
79.(4)调节cr靶材所在射频电源功率为80w,al2o3靶材所在射频电源功率为20w,通入氩气和氮气的比例为50:20(sccm),调节限流阀为15,确保工作气压是0.6pa,打开靶材挡板,正式进行薄膜溅射,溅射90min后,得到厚度约为200nm的薄膜。
80.实施例2
81.本实施例采用tio2靶材替换al2o3靶材,其余步骤及工艺参数均与实施例1相同。
82.实施例3
83.本实施例采用zro2靶材替换al2o3靶材,其余步骤及工艺参数均与实施例1相同。
84.实施例4
85.本实施例采用ti靶材替换cr靶材,其余步骤及工艺参数均与实施例1相同。
86.实施例5
87.本实施例采用nb靶材替换cr靶材,其余步骤及工艺参数均与实施例1相同。
88.实施例6
89.本实施例中,未开启al2o3靶,只制备单一的crn薄膜,其余步骤及工艺参数均与实施例1相同。
90.对比例1
‑491.本对比例所用方法与实施例1相似,区别在于,al2o3的功率分别为10、15、25、30w。
92.对比例5
‑793.本对比例所用方法与实施例6相似,区别仅在于,基底施加偏压分别为0、
‑
60、
‑
140v。
94.效果实施例1
95.由图1的al2o3与tio2掺杂的crn薄膜动电位曲线,拟合得到两者的腐蚀电流密度为0.084、0.98μa/cm2,均小于doe标准中要求的1μa/cm2,且低于纯ti片(2.9μa/cm2)和单一crn(2.31μa/cm2)的腐蚀电流密度。
96.需要说明的是,doe标准为美国能源部提出的2020年燃料电池双极板的指标要求,如表1所示。
97.表1美国能源部提出的2020年燃料电池双极板的指标要求
[0098][0099]
图2中的al2o3与tio2掺杂的crn薄膜接触电阻变化曲线,可以得到在150n/cm2的压力下,al2o3掺杂的crn薄膜的接触电阻为3.09mω
·
cm2,tio2掺杂的crn薄膜的接触电阻为7.34mω
·
cm2,均满足doe标准中≤10mω
·
cm2,且低于crn薄膜(12.46mω
·
cm2)的接触电
阻。
[0100]
效果实验例2
[0101]
图3
‑
图6为al2o3不同溅射功率掺杂后crn薄膜的性能测试曲线。由图3可知,随着al2o3的功率从0w升高到20w,薄膜的耐腐蚀性变好,这是由于随着al2o3掺入量增多,薄膜柱状晶消失,逐渐非晶化,而晶界往往是载流子的快速通道,缺陷多发之处,所以非晶化有利于薄膜耐腐蚀性能提高。但是随着al2o3掺入量继续增大,薄膜的耐腐蚀性能反而有所降低。
[0102]
图4可知,随着al2o3的功率从0w升高到20w,接触电阻有所降低,这可能是由于适当的al2o3加入改变了crn表面的形貌,使得薄膜表面更加平整,从而实际接触面积增大,接触电阻变小,而随着al2o3的功率进一步提高后,由于al2o3本身的导电性非常差,它的存在会拉低薄膜整体的导电性。综合耐腐蚀性能和导电性可以发现,在al2o3的功率为20w时,al2o3掺杂的crn薄膜的综合性能最优,各指标均满足doe标准,其中腐蚀电流密度达到0.084μa/cm2,接触电阻(3.09mω
·
cm2)也低于纯ti(3.89mω
·
cm2)。
[0103]
图5测试了
‑
0.1v的静电位曲线,发现性能最优异的样品,即al2o320w时,连续运行了10个小时,电流依然稳定,说明薄膜的耐久性较好,而al2o3的功率为15w和25w时,曲线运行过程中电流转正,而al2o3的功率为30w时,电流难以平稳,都表明耐腐蚀性不佳。
[0104]
从图6的xrd图看到只有一个crn(111)的衍射峰,并未观察到al2o3峰,说明al2o3可能以非晶化的形式存在,并且随着al2o3量增多,crn(111)峰强度降低,峰逐渐宽化,说明随着al2o3量增多,薄膜的结晶性逐渐变差,这势必对其耐腐蚀性和导电性造成影响。但是crn峰的位置并没有移动,说明al2o3与crn只是混合状态,没有掺入晶格,但是al2o3的存在影响了crn的结晶状态。
[0105]
效果实施例3
[0106]
图7、8测试了不同偏压下crn薄膜的动电位和接触电阻变化曲线,未施加偏压的crn样品,经过几次lsv测试后发现薄膜脱落,说明膜基结合力较差,而施加偏压的crn样品,经过多次lsv测试未见脱落,说明薄膜膜基结合力增大了。随着溅射偏压的增大,腐蚀电位先右移再左移,在
‑
110v时达到最大,为
‑
0.13v,腐蚀电流密度也呈现先降低后增大的趋势,同样在
‑
110v时达到最小值,说明施加偏压后,薄膜的耐腐蚀性增强,所以综合来看,施加负偏压是本发明al2o3(tio2)掺杂crn性能优势的关键因素之一。
[0107]
实验例4
[0108]
图9为0v、
‑
100v偏压制备的crn薄膜和
‑
100v偏压制备的al2o3掺杂的crn薄膜与水的湿润性。由于在燃料电池阴极会生成水,需要及时把反应生成的水排出,因为水会阻碍反应气体进入电极,同时水附着在双极板上会加快双极板的腐蚀,所以燃料电池金属双极板的应用需要有一定的疏水性。未施加偏压得到的crn薄膜的接触角最小,为38.82
°
,施加
‑
100v偏压后,crn薄膜与水的接触角增大至76.92
°
,而掺入al2o3后,薄膜与水的接触角进一步增大至91.54
°
。表明与单一的crn涂层相比,
‑
100v偏压制备的al2o3掺杂的crn薄膜的与水具有更好的疏水性能,有助于燃料电池内部水管理。
[0109]
以上所述,仅为本发明较佳的具体实施方式,但本发明的保护范围并不局限于此,任何熟悉本技术领域的技术人员在本发明揭露的技术范围内,可轻易想到的变化或替换,都应涵盖在本发明的保护范围之内。