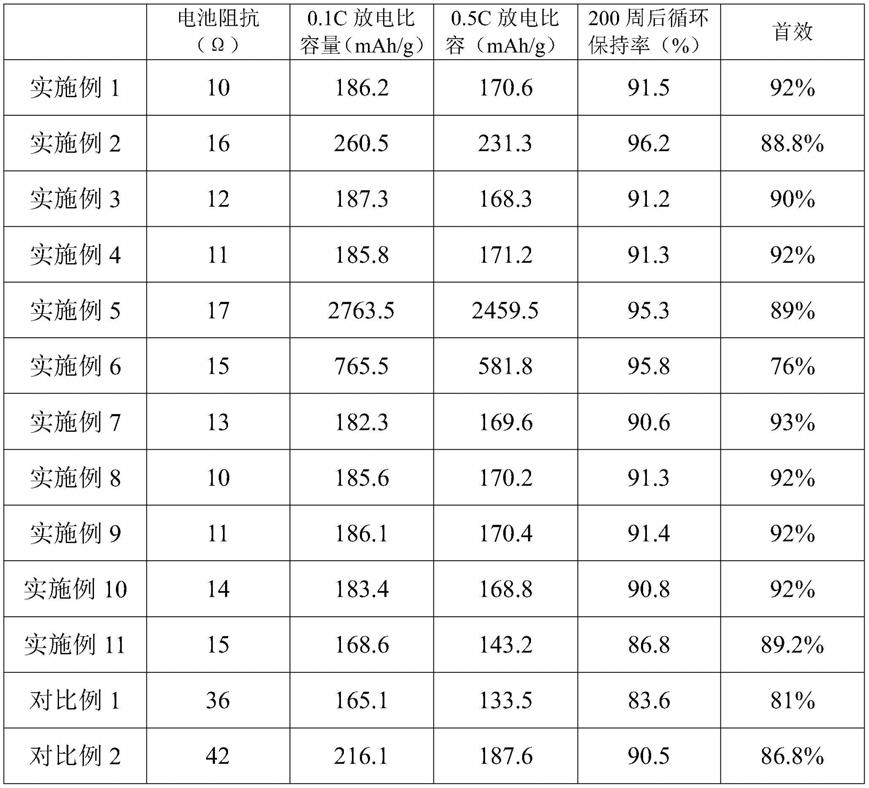
1.本发明属于电池技术领域,尤其涉及一种固态电池极片、其制备方法及应用。
背景技术:2.随着电子产品以及新能源汽车的大量普及,作为其电源的锂电池,因具有质量轻、体积小、工作电压高、能量密度高、输出功率大、充电效率高和无记忆效应等优点,越来越受到重视,从而不可避免的对锂电池的安全性、能量密度等要求也有越来越高。
3.目前市场广泛使用的锂离子电池所用的电解质为有机液态电解质,这也带来了一系列问题。液体电解质一般由锂盐、有机溶剂及添加剂组成,其室温下为易于流动的液体状态。在电池受到强烈碰撞或电池内部膨胀等作用后,电池包装很容易发生破损,液体电解质会泄漏出来。由于液体电解质含有大量易燃、易爆的有机溶剂,存在极大的安全隐患。另外在液态锂离子电池中所使用的液态电解质的量难以再降低,这对于提高锂离子电池的质量能量密度和体积能量密度都存在较大困难。
4.与传统的液态锂离子电池相比较,固态电池有很多优势,发展前景值得期待。其采用不燃的固态无机物作为电解质,不但具有较高的能量密度,且同时具有良好的安全性。
5.全固态电池技术目前仍处于研发阶段,目前主要通过两种方法制备固态电池的极片:1、应用湿法匀浆涂布的方式进行极片的制备,但固态电解质与大部分溶剂不稳定,即使稳定的溶剂,在球磨过程中也会有所反应,使得固态电解质的离子电导率有所下降,从而增加极片以及电池的阻抗,使得电池倍率性能下降,影响电池的循环性能。另外溶剂的添加增加了烘干、溶剂回收处理等工序,增加了成本且可能造成环境污染。2、全固态电池的制备极片的另一种方法为:将可纤维化聚合物通过高速剪切纤维化拉丝,形成网状结构,将其他组分颗粒包裹粘结到一起,进行热辊压后成为自支撑膜,再次通过热辊压将自支撑膜片与集流体复合后制成电池极片。但极片中粘结剂本身是离子与电子的绝缘体,粘结剂的引入会造成极片之中离子传导不顺畅,从而增加极片以及电池的阻抗。
6.cn112803064a公开了一种硫化物复合固态电解质膜、制备方法及在全固态电池中的应用。电解质原料由按重量份数计,80
‑
97份的硫化物固态电解质,3
‑
20份的低玻璃化转变温度的聚合物;其中,聚合物数均分子量范围为4000
‑
30000,玻璃化转变温度为
‑
70~
‑
50℃。该发明提供的硫化物复合固态电解质,由于采用低玻璃化转变温度的粘结剂具有较高的机械柔性,简化了硫化物复合固态电解质膜的制备工艺。其中用该方法制备出的固体电解质具有高离子电导率(≥10
‑4)和匹配高载量正极循环的优良特点。
7.cn108878960a公开了一种固态电解质正极和固态电池。所述固态电解质正极包括:涂覆有正极活性物质层的正极片,和在正极活性物质层外表面上涂覆的导电陶瓷复合涂层,其中,所述导电陶瓷复合涂层厚度为1~50μm;所述导电陶瓷复合涂层包括有机聚合物、锂盐、纳米无机固态电解质、高分子接枝改性陶瓷、粘结剂和润湿剂,其中,基于所述导电陶瓷复合涂层的总重量,所述有机聚合物的含量为5~80wt%,所述锂盐含量为5~50wt%,所述纳米无机固态电解质的含量为10~85wt%,所述高分子接枝改性陶瓷的含量
为1~20wt%,所述粘结剂的含量为1~12wt%,所述润湿剂的含量为0.1~0.5wt%。
8.现有固态电池在极片制备过程中,均需要使用粘结剂,存在离子传导不顺畅,而且粘结剂多为有机聚合物,在高电压的正极侧及低压的负极侧长时间循环后,会发生分解,进而造成极片之中颗粒的黏结性变差,从而增加极片以及电池的阻抗,导致循环性能变差,因此,如何在保证电池性能的情况下,还能够避免粘结剂的使用,成为目前迫切需要解决的问题。
技术实现要素:9.针对现有技术存在的不足,本发明的目的在于提供一种固态电池极片、其制备方法及应用,通过采用粘性固态电解质,使固态电池在制备的过程中不使用有机聚合物作为粘结剂,省去了烘干工序,避免有机溶剂后处理等问题。
10.为达此目的,本发明采用以下技术方案:
11.第一方面,本发明提供了一种固态电池极片,所述固态电池极片包括集流体,以及设置于集流体表面的活性物质层,所述活性物质层包括活性物质、粘性固态电解质和导电剂。
12.本发明中采用粘性固态电解质,具有离子导电能力、粘性、低储能模量与低损耗模量的性能,同时起到离子导体与粘结剂的作用,避免了极片制作过程中有机聚合物粘结剂及溶剂的使用,省去烘干工序,而且避免有机溶剂后处理及回收等问题,有效节约生产成本,避免环境污染,此外,由于电池极片中不存在有机聚合物,从而避免了聚合物在高、低电压下的分解造成的阻抗增大的问题,相对于传统锂离子电池,具有离子传导能力与粘结力,避免了电解液的加入,提升电池安全性能。
13.作为本发明的一个优选技术方案,所述粘性固态电解质包括li
x
ma3d
x
,其中,m为al、ga、in或tl中的一种或至少两种的组合,a和d分别为f、cl、br、i中的一种,1≤x≤8,例如x为1、2、3、4、5、6、7或8。
14.优选地,所述a和d的元素不同。
15.作为本发明的一个优选技术方案,所述粘性固态电解质包括li3ini3br3。
16.示例性地,提供一种li3ini3br3的制备方法:将libr与ini3按照摩尔比为3:1的比例在氩气氛围内放置于氧化锆球磨罐中,加入氧化锆球磨珠;球料比为5:1。将罐体密封后,使用高能球磨机在500rpm的转速下球磨40h后分离球磨珠与粉体,即制得li3ini3br3。
17.需要说明的是,本发明中其他通式的粘性固态电解质也可根据上述方法,按照摩尔比进行配制。
18.优选地,所述粘性固态电解质的电导率≥0.1ms/cm,例如为0.1ms/cm、0.5ms/cm、1ms/cm、2ms/cm、3ms/cm、4ms/cm、5ms/cm、6ms/cm、7ms/cm、8ms/cm、9ms/cm或10ms/cm。
19.优选地,所述粘性固态电解质的损耗模量≤5mpa,例如为0.5mpa、1.0mpa、1.5mpa、2.0mpa、2.5mpa、3.0mpa、3.5mpa、4.0mpa、4.5mpa或5.0mpa。
20.优选地,所述粘性固态电解质的储能模量≤5mpa,例如为0.5mpa、1.0mpa、1.5mpa、2.0mpa、2.5mpa、3.0mpa、3.5mpa、4.0mpa、4.5mpa或5.0mpa。
21.作为本发明的一个优选技术方案,所述活性物质为正极活性物质,所述固态电池极片为固态电池正极极片。
22.需要说明的是,本发明中正极活性物质可以是li
1+a
ni
b
co
c
mn
d
m
e
o2‑
f
,0≤a≤1,0≤b≤1,0≤c≤1,0≤d≤1,0≤e≤1,0≤f≤0.2、lim
g
mn2‑
g
o4,0≤g≤0.5、life1‑
h
m
h
po4,其中0≤h≤1、li2fe1‑
i
m
i
sio4,其中0≤i≤1、以及life1‑
j
m
j
so4f,其中0≤j≤1,m选自li、na、k、mg、ca、sr、ba、al、ga、in、si、ge、sn、pb、sc、v、cr、mn、fe、co、ni、cu、zn、y、zr、nb、mo、ru、rh、pd、ag、cd、la、ce、pr、nd、sm、eu、gd、er、tm、yb、lu、w、pt或au中的一种或至少两种的组合。
23.优选地,所述固态电池正极极片中活性物质层的厚度为30~200μm,例如为30μm、50μm、70μm、90μm、110μm、130μm、150μm、170μm、190μm或200μm。
24.优选地,所述集流体的厚度≤20μm,例如为1μm、2μm、4μm、6μm、8μm、10μm、12μm、14μm、16μm、18μm或20μm。
25.需要说明的是,集流体的材质应根据极片的种类进行选择,例如负极的集流体可选为铜箔,正极的集流体可选为铝箔。
26.优选地,所述固态电池正极极片中,所述正极活性物质的质量占活性物质层的25~90%,例如为25%、35%、40%、45%、50%、55%、60%、65%、70%、75%、80%、85%或90%,进一步优选为52~85%。
27.优选地,所述固态电池正极极片中,所述导电剂的质量占活性物质层的0.1~5%,例如为0.1%、0.5%、1.0%、1.5%、2.0%、2.5%、3.0%、3.5%、4.0%、4.5%或5.0%,进一步优选为1~2.5%。
28.需要说明的是,在制备过程中,若添加导电剂,可以相应降低粘性固态电解质的质量占比,从而能够提高活性物质的质量占比。
29.优选地,所述固态电池正极极片中,所述粘性固态电解质的质量占活性物质层的9~40%,例如为9%、12%、14%、16%、18%、20%、22%、24%、26%、28%、30%、32%、34%、36%、38%或40%,进一步优选为25~35%。
30.本发明通过控制粘性固态电解质的质量占活性物质层的9~40%,进一步优选为25~35%,从而在保证极片的延展性,并且具有可塑性和高压实密度,保证极片的离子电导率,提升电池的倍率性能,若占比低于9%,存在离子电导率低和粘结性差等问题,导致极片稳定性差;随着粘性电解质含量的提升,能够使极片具有更好的机械性能与延展性,更有利于极片的成型与制备;且正极活性层内的离子导电网络更为优化;但若占比高于40%,则存在活性物质占比低,影响电池能量密度的问题。
31.需要说明的是,当固态电解质、活性物质和导电剂,质量占比加和不够100%时,使用常规固态电解质作为补充,例如为硫化物电解质lipscl、lisipscl、lisnpscl或ligeps中的一种或至少两种的组合。
32.作为本发明的一个优选技术方案,所述活性物质为负极活性物质,所述固态电池极片为固态电池负极极片。
33.优选地,所述固态电池负极极片中活性物质层的厚度为30~300μm,30μm、60μm、90μm、120μm、150μm、180μm、210μm、240μm、270μm或300μm。
34.优选地,所述固态电池负极极片中,所述负极活性物质的质量占活性物质层的25~89.4%,例如为25%、30%、35%、40%、45%、50%、55%、60%、65%、70%、75%、80%、85%或89.4%,进一步优选为52.5~71%。
35.优选地,所述固态电池负极极片中,所述导电剂的质量占活性物质层的0.5~5%,
例如为0.5%、1.0%、1.5%、2.0%、2.5%、3.0%、3.5%、4.0%、4.5%或5.0%,进一步优选为1~2.5%。
36.优选地,所述固态电池负极极片中,所述粘性固态电解质的质量占活性物质层的10~40%,例如为10%、15%、20%、25%、30%、35%或40%,进一步优选为25~35%。
37.作为本发明的一个优选技术方案,所述正极活性物质包括licoo2、linio2、lifepo4、lini
0.5
mn
0.5
o2、li(nicomn)
1/3
o2、li
1.2
ni
0.13
mn
0.54
co
0.13
o2或limn2o4中的一种或至少两种的组合。
38.优选地,优选地,所述负极活性物质的材质包括石墨、硅或氧化亚硅中的一种或至少两种的组合。
39.优选地,所述导电剂包括乙炔黑、super
‑
p、碳纳米管、碳纤维、科琴黑、石墨导电剂或石墨烯中的一种或至少两种的组合。
40.第二方面,本发明提供了一种权利要求如第一方面所述的固态电池极片的制备方法,所述的制备方法包括:
41.将活性物质、粘性固态电解质和导电剂混合制备活性物质层,活性物质层与集流体制备成固态电池极片。
42.本发明在制备极片过程中没有有机溶剂的添加,省去烘干工序,避免有机溶剂后处理及回收等问题,有效节约生产成本,避免环境污染。此外,由于固态电解质与大部分溶剂不稳定,即使稳定的溶剂,在球磨过程中也会有所反应,使得电解质离子电导率下降,从而增加极片以及电池的阻抗,使得电池倍率性能下降,应用该方法制备极片避免硫化物电解质与溶剂的接触,提高极片的离子电导率,是电池的阻抗降低,提升电池的倍率性能。进一步地,本发明中无粘结剂的加入,避免了有机聚合物在高电压、低电压下的分解,从而延长了电池的循环寿命。且避免本身为电子绝缘体的粘结剂的加入,降低了极片内部阻抗,提升活性物质的容量发挥。
43.作为本发明的一个优选技术方案,所述混合的方式为搅拌。
44.需要说明的是,本发明对搅拌的方式不做具体要求和特殊限定,能够达到混合目的即可,例如可以采用高速搅拌、螺杆挤出或气流破碎等方式进行混合。
45.优选地,所述活性物质层的形成方式包括辊压,所述辊压的温度为70~90℃,例如为70℃、72℃、74℃、76℃、78℃、80℃、82℃、84℃、86℃、88℃或90℃。
46.优选地,所述活性物质层与集流体辊压制备成固态电池极片。
47.作为本发明的一个优选技术方案,所述制备方法具体包括以下步骤:
48.将活性物质、粘性固态电解质和导电剂搅拌混合后,在70~90℃下辊压制备成活性物质层,活性物质层与集流体辊压后形成固态电池极片。
49.本发明制备的极片延展性好,可塑性强,经过反复辊压能够达到较高的压实密度,能有效提升电池的能量密度。
50.第三方面,本发明还提供了一种如第一方面所述的固态电池极片的应用,所述固态电池极片用于固态电池。
51.本发明所述的数值范围不仅包括上述例举的点值,还包括没有例举出的上述数值范围之间的任意的点值,限于篇幅及出于简明的考虑,本发明不再穷尽列举所述范围包括的具体点值。
52.与现有技术相比,本发明的有益效果为:
53.本发明中采用粘性固态电解质,具有离子导电能力、粘性、低储能模量与低损耗模量的性能,同时起到离子导体与粘结剂的作用,避免了极片制作过程中有机聚合物粘结剂及溶剂的使用,省去烘干工序,而且避免有机溶剂后处理及回收等问题,有效节约生产成本,避免环境污染,此外,由于电池极片中不存在有机聚合物,从而避免了聚合物在高、低电压下的分解造成的阻抗增大的问题,相对于传统锂离子电池,具有离子传导能力与粘结力,避免了电解液的加入,提升电池安全性能。
具体实施方式
54.为更好地说明本发明,便于理解本发明的技术方案,下面对本发明进一步详细说明。但下述的实施例仅是本发明的简易例子,并不代表或限制本发明的权利保护范围,本发明保护范围以权利要求书为准。
55.以下实施例中,固态电池正极极片中集流体是厚度为16μm的铝箔,固态电池负极极片中集流体是厚度为12μm的铜箔。
56.实施例1
57.本实施例提供了一种固态电池极片,为固态电池正极极片,厚度为70μm,包括集流体,以及设置于集流体表面的活性物质层,活性物质层包括lini
0.8
co
0.1
mn
0.1
o2、碳纳米管和li3ini3br3,活性物质层中,lini
0.8
co
0.1
mn
0.1
o2质量占比为65.2%,碳纳米管质量占比为2.2%,li3ini3br3质量占比为32.6%。
58.本实施例还提供了一种上述固态电池极片的制备方法,所述制备方法具体包括以下步骤:
59.将6g lini
0.8
co
0.1
mn
0.1
o2、0.2g碳纳米管、3g li3ini3br3搅拌混合后,在80℃下辊压制备成活性物质层,活性物质层与集流体辊压后形成固态电池极片。
60.实施例2
61.本实施例提供了一种固态电池极片,为固态电池负极极片,厚度为120μm,包括集流体,以及设置于集流体表面的活性物质层,活性物质层包括石墨、碳纳米管和li3ini3br3,活性物质层中,石墨质量占比为66.3%,碳纳米管质量占比为2.1%,li3ini3br3质量占比为31.6%。
62.本实施例还提供了一种上述固态电池极片的制备方法,所述制备方法具体包括以下步骤:
63.将6.3g石墨、0.2g碳纳米管、3g li3ini3br3搅拌混合后,在80℃下辊压制备成活性物质层,活性物质层与集流体辊压后形成固态电池极片。
64.实施例3
65.本实施例提供了一种固态电池极片,与实施例1相比,其区别在于,活性物质层包括lini
0.8
co
0.1
mn
0.1
o2、乙炔黑和li3gacl3f3,活性物质层中,lini
0.8
co
0.1
mn
0.1
o2质量占比为52%,乙炔黑质量占比为1%,li3gacl3f3质量占比为35%,其余组分为li6sp5cl固态电解质。
66.实施例4
67.本实施例提供了一种固态电池极片,与实施例1相比,其区别在于,活性物质层包括lini
0.8
co
0.1
mn
0.1
o2、碳纤维和li3gabr3f3,活性物质层中,lini
0.8
co
0.1
mn
0.1
o2质量占比为
52%,碳纤维质量占比为1%,li3gabr3f3质量占比为25%,其余组分为li6sp5cl固态电解质。
68.实施例5
69.本实施例提供了一种固态电池极片,与实施例2相比,其区别在于,活性物质层包括硅、科琴黑和li2gaf3cl2,活性物质层中,硅质量占比为89.4%,科琴黑质量占比为0.6%,li4tli3f4质量占比为10%。
70.实施例6
71.本实施例提供了一种固态电池极片,与实施例2相比,其区别在于,活性物质层包括氧化亚硅、石墨烯和li4gaf3cl4,活性物质层中,氧化亚硅质量占比为25%,石墨烯质量占比为5%,li6tlf3cl6质量占比为35%,其余组分为li6sp5cl固态电解质。
72.实施例7
73.本实施例提供了一种固态电池极片,与实施例1相比,其区别在于,li3ini3br3质量占比为5%,多余部分由li6sp5cl取代,其余含量和组成与实施例1完全相同。
74.实施例8
75.本实施例提供了一种固态电池极片,与实施例1相比,其区别在于,li3ini3br3质量占比为10%,多余部分由li6sp5cl取代,其余含量和组成与实施例1完全相同。
76.实施例9
77.本实施例提供了一种固态电池极片,与实施例1相比,其区别在于,li3ini3br3质量占比为25%,多余部分由li6sp5cl取代,其余含量和组成与实施例1完全相同。
78.实施例10
79.本实施例提供了一种固态电池极片,与实施例1相比,其区别在于,li3ini3br3质量占比为35%,多余部分由li6sp5cl取代,其余含量和组成与实施例1完全相同。
80.实施例11
81.本实施例提供了一种固态电池极片,与实施例1相比,其区别在于,li3ini3br3的加入量为7.6g,碳纳米管和lini
0.8
co
0.1
mn
0.1
o2的加入量不变,使li3ini3br3质量占比为55%,lini
0.8
co
0.1
mn
0.1
o2质量占比为43.5%,碳纳米管质量占比为1.5%。
82.对比例1
83.本对比例提供了一种固态电池极片的制备方法,与实施例1相比,其区别在于,搅拌混合过程中还加入了0.2g的pvdf作为粘结剂,其余操作与步骤与实施例1完全相同。
84.本对比例还提供了一种上述制备方法制备得到的固态电池极片。
85.对比例2
86.本对比例提供了一种固态电池极片的制备方法,与实施例2相比,其区别在于,搅拌混合过程中还加入了0.2g的苯乙烯
‑
丁二烯
‑
苯乙烯嵌段共聚物作为粘结剂,其余操作与步骤与实施例1完全相同。
87.本对比例还提供了一种上述制备方法制备得到的固态电池极片。
88.本发明还提供了一种包括上述固态电池极片的电池。
89.将上述实施例和对比例中的固态电池极片组装对锂
‑
铟合金为对电极的扣电,隔膜为湿法涂布硫化物电解质膜,并在0.1c、0.5c下进行充放电,测试结果如表1所示。
90.表1
[0091][0092]
通过上表可知:
[0093]
(1)实施例1与实施例7
‑
11可以看出,虽然实施例7、8的性能与实施例1相当,但是其粘结稳定性比实施例1差,此外,本发明通过控制粘性固态电解质的质量占活性物质层的9~40%,进一步优选为25~35%,从而在保证极片的延展性,并且具有可塑性和高压实密度,保证极片的离子电导率,提升电池的倍率性能,若占比低于9%,存在离子电导率低和粘结性差等问题,导致极片稳定性差;随着粘性电解质含量的提升,能够使极片具有更好的机械性能与延展性,更有利于极片的成型与制备;且正极活性层内的离子导电网络更为优化;但若占比高于40%,则存在活性物质占比低,影响电池能量密度的问题。
[0094]
(2)实施例1与对比例1相比,实施例1的性能数据优于对比例1,实施例2与对比例2相比,实施例2的性能数据优于对比例2,由此可以看出,本发明中采用粘性固态电解质,具有离子导电能力、粘性、低储能模量与低损耗模量的性能,同时起到离子导体与粘结剂的作用,避免了极片制作过程中有机聚合物粘结剂及溶剂的使用,省去烘干工序,而且避免有机溶剂后处理及回收等问题,有效节约生产成本,避免环境污染,此外,由于电池极片中不存在有机聚合物,从而避免了聚合物在高、低电压下的分解造成的阻抗增大的问题,相对于传统锂离子电池,具有离子传导能力与粘结力,避免了电解液的加入,提升电池安全性能。
[0095]
申请人声明,以上所述仅为本发明的具体实施方式,但本发明的保护范围并不局限于此,所属技术领域的技术人员应该明了,任何属于本技术领域的技术人员在本发明揭
露的技术范围内,可轻易想到的变化或替换,均落在本发明的保护范围和公开范围之内。