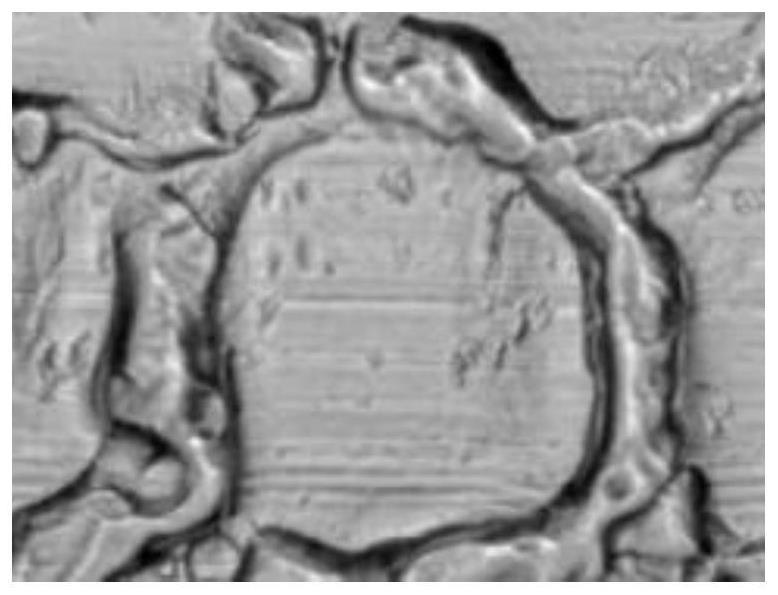
1.本发明涉及表面高清洁高毛化的锂电池正极集电体用铝箔的制备方法,属于铝箔压延加工及材料表面处理技术领域。
背景技术:2.随着国家倡导大力发展新能源汽车行业,市场对汽车动力锂离子电池的需求日益旺盛,动力电池正极集电体铝箔材料作为汽车动力锂离子电池的关键材料,对电池性能的稳定应、一致性、安全性有着重要影响。同时,续航里程作为终端汽车使用客户最关切的一项参数,也对电池的能量密度提升提出了更高的要求和挑战,动力电池正极集电体铝箔材料作为电池活性物质磷酸铁锂等的依附载体,其铝箔的表面质量好坏直接影响了与活性物质的粘结性强度和粘结密度大小,也直接对应了电池极片及电池的性能稳定一致性和能量密度。
3.目前,主流电池生产厂家在正极极片的生产环节,在涂布辊压之前工艺环节并不会对铝箔表面进行专门的处理,常常会出现锂电池用正极集电体铝箔表面质量差,表面清洁度差带油多且表面粗糙度不够,导致与磷酸铁锂等活性物质涂层粘结性差并导致易于掉粉或者甚至局部漏涂等问题,会对电池使用带来不稳定的安全隐患,同时也降低了电池的能量密度。针对以上问题,大量研究者研究通过在铝箔表面涂碳或者表面多孔化等方式来增加铝箔表面活性物质的粘结性,但为了提高锂离子电池的能量密度,集流体铝箔的厚度已经减薄到9~13μm,表面多孔化会造成铝箔力学性能下降,无法满足极片制作工艺要求,涂碳铝箔表面涂层的厚度通常为微米级,已经达到集流体厚度的10%左右,涂层厚度较大而且涂碳工艺大大增加了材料的生产成本也降低了成品率。因此需要探究其他低成本且生产使用可行性高的替代新技术以解决目前问题。
技术实现要素:4.针对现有技术的不足,本发明的目的在于提供表面高清洁高毛化的锂电池正极集电体用铝箔的制备方法,解决了锂电池用正极集电体铝箔表面质量差,与磷酸铁锂等活性涂层粘结性差导致的易于掉粉甚至漏涂的问题,提高活性物质粘结强度,最终有利于提高成品电池的能量密度和一致性、安全性。
5.为解决上述技术问题,本发明所提出的新技术方案是:
6.表面高清洁高毛化的锂电池正极集电体用铝箔的制备方法,按照上述1060锂电池用铝箔进行组分及加工工艺控制,所述方法包括如下步骤:
7.(1)熔炼;(2)铸轧;(3)冷轧开坯;(4)中间退火;(5)冷轧中轧;(6)切边;(7)箔轧;(8)分切;(9)倒卷电晕;(10)表面预处理;(11)表面辊压粗化处理,等主要工序。
8.优选地,所述熔炼工序熔炼1070或1060或1235d或1100铝合金,采用纯铝锭配料生产,废料比控制≤0%,进行两次精炼处理,精炼气体采用ar气。
9.优选地,所述铸轧工序采用在线除气箱除气,经过二级板式过滤加管式过滤器进
行组合式熔体过滤。
10.优选地,所述铸轧工序铸轧成品坯料厚度5.5~7.0mm,晶粒度要求1级。
11.优选地,所述箔轧成品铝箔厚度为10~15μm规格,双面光材质。
12.优选地,所述倒卷电晕工序采用1~2次电晕,电晕功率12~19kw,线速度150~250m/min,开卷轴张力12~28n/mm2。
13.优选地,所述表面预处理工序包括表面酸碱溶液浸润、水清洗、烘干三步骤,其中酸碱液为naoh和hcl等酸或者碱性物质溶液,酸碱洗需要流转浸润一段时间。
14.优选地,所述表面辊压粗化处理工序采用激光毛化机对轧辊进行表面毛化并对双面光铝箔进行毛化轧制,铝箔表面粗糙度ra控制0.5~0.9μm,环状毛化坑宽度5~15μm左右,表面毛化坑的直径在50~100μm,要求铝箔表面进行双面毛化且环状毛化坑要求不重叠。
15.进一步优选地,所述铸轧工序除气箱温度控制705~725℃,采用二级板式过滤采用50目及60目过滤片,管式过滤器为ra级,过滤箱温度控制700~720℃,氢含量≤0.12ml/100gal。
16.进一步优选地,所述电晕工序倒卷机胶辊每卷需要采用干净地无尘布清理一次,确保无铝屑无灰尘无油污,电晕后铝箔表面达因值要求不低于32dyn。
17.进一步优选地,所述表面预处理工序中酸碱洗需要流转浸润5~10s,以显微镜观察下完全去除表面氧油脂及粉末残留物为准。
18.进一步优选地,所述表面辊压粗化处理工序铝箔表面粗糙度控制0.5~0.6μm,表面粗化后显微最大厚度减薄量要求<35%,粗化后铝箔强度和延伸率降低<10%。
19.与现有技术相比,本发明所达到的有益效果:
20.本发明通过优化铝箔生产关键工序技术方法及参数要求,同时结合新型地铝箔表面预处理及毛化轧制工艺,显著提高了动力电池正极集流体铝箔表面洁净度及粗糙度,提高了铝箔与磷酸铁锂等活性涂层物质地粘结性、粘结强度和均匀性,极大改善了粘结性差导致的易于掉粉甚至漏涂的问题,最终有利于电池极片量产稳定化并提高成品电池的能量密度和一致性、安全性。本发明制备的铝箔表面无油脂等残留,表面粗糙度ra测试值为0.5~0.9μm,达到常规铝箔地5~10倍,同时活性涂层剥离强度达到常规铝箔极片的1.5~2倍,该发明方法生产的铝箔特别适合于生产磷酸铁锂、钛酸锂等动力锂电池极片,生产成本低应用前景广阔。
附图说明
21.图1是实施例1的表面形貌图;
22.图2是实施例2的表面形貌图;
23.图3是对比例1的表面形貌图;
24.图4是对比例2的表面形貌图;
具体实施方式
25.本发明的目的在于提供表面高清洁高毛化的锂电池正极集电体用铝箔的制备方法,解决了锂电池用正极集电体铝箔表面质量差,与磷酸铁锂等活性涂层粘结性差导致的
易于掉粉甚至漏涂的问题,提高活性物质粘结强度,最终有利于提高成品电池的能量密度和一致性、安全性。
26.所述方法包括如下步骤:
27.(1)熔炼:采用1070或1060或1235d或1100铝合金,采用纯铝锭配料生产,废料比控制≤0%,进行两次精炼处理,精炼气体采用ar气。
28.(2)铸轧:铸轧工序采用在线除气箱除气,除气箱温度控制705~725℃,氢含量≤0.12ml/100gal;经过二级板式过滤加管式过滤器进行组合式熔体过滤,二级板式过滤采用50目及60目过滤片,管式过滤器为ra级,过滤箱温度控制700~720℃;铸轧工序铸轧成品坯料厚度5.5~7.0mm,晶粒度要求1级。
29.(3)冷轧开坯:将铸轧坯料经开坯冷轧机2~4道次轧至退火道次厚度4.8~5.2mm(1100合金)或者3.8~4.0mm(1235d合金)或者1.8~2.0mm(1060,1070合金)厚度。
30.(4)中间退火:将开坯轧至退火厚度的铝卷进行中间退火;
31.(5)冷轧中轧:将退火后铝卷上中轧轧机经3~4道次轧至0.24~0.26mm厚度;
32.(6)切边:将中轧后铝卷上纵剪机进行纵剪切边,裂边切尽。
33.(7)箔轧:中轧切边后半成品基材经4~5道次箔轧成成品厚度为10~15μm规格地双面光铝箔。
34.(8)分切:将箔轧后铝箔母卷宽度方向一剖二进行初步一次定长度分切。
35.(9)倒卷电晕:倒卷时采用双面刃圆盘刀将分切后铝卷继续精切至成品窄幅宽度规格,采用1~2次电晕,电晕功率12~19kw,线速度150~250m/min,开卷轴张力12~28n/mm2,倒卷机胶辊每卷需要采用干净地无尘布清理一次,确保无铝屑无灰尘无油污,电晕后铝箔表面达因值要求不低于32dyn。
36.(10)表面预处理:经过表面酸碱溶液浸润、水清洗、烘干三步骤处理,其中酸碱液为naoh和hcl等酸或者碱性物质溶液,酸碱洗需要流转浸润5~10s,以显微镜观察下完全去除表面氧油脂及粉末残留物为准。
37.(11)表面辊压粗化处理:采用激光毛化机对轧辊进行表面毛化并对双面光铝箔进行毛化轧制,环状毛化坑宽度控制5~15μm左右,表面毛化坑的直径控制50~100μm,要求铝箔表面进行双面毛化且环状毛化坑要求不重叠,要求表面粗化后显微最大厚度减薄量要求<35%,粗化后铝箔强度和延伸率降低<10%。
38.本发明方法制备得到的动力锂电池正极集电体用铝箔产品,表面高清洁无铝粉及油脂残留,表面高毛化,铝箔表面粗糙度ra控制0.5~0.9μm,活性涂层剥离强度达到常规铝箔极片的1.5~2倍,该发明方法生产的铝箔各项基础性能指标稳定,特别适合于生产磷酸铁锂等动力锂电池正极极片,活性物质涂敷工序无明显漏涂、掉粉等现象,压实工序无脆断问题。
39.下面结合实施例对本发明作进一步描述。以下实施例仅用于更加清楚地说明本发明的技术方案,而不能以此来限制本发明的保护范围。
40.实施例1:
41.本发明实施例涉及表面高清洁高毛化的锂电池正极集电体用铝箔的制备方法。具体生产方法如下:
42.(1)熔炼:采用aa1060国标铝合金成分要求进行配料熔炼,采用纯铝锭配料生产,
废料比控制≤0%,进行两次精炼处理,精炼气体采用ar气。
43.(2)铸轧:铸轧工序采用在线除气箱除气,除气箱温度控制719℃,氢含量0.05ml/100gal;采用板式过滤50目及60目过滤片,配合ra级管式过滤器使用,过滤箱温度控制716℃;铸轧成品坯料厚度6.6mm,晶粒度检测为1级。
44.(3)冷轧开坯:经两道次6.6mm
→
3.5mm
→
2.0mm开坯轧至退火道次厚度;
45.(4)中间退火:将0.20mm厚度铝卷进行中间退火,工艺采用4h炉气温度升温至550℃,保温5h后转炉气温度360℃保温3h;
46.(5)冷轧中轧:将退火后铝卷上中轧轧机经3道次2.0mm
→
0.95mm
→
0.45mm
→
0.26mm轧至0.26mm厚度;
47.(6)切边:将中轧后铝卷上纵剪机进行纵剪切边,单边切3cm。
48.(7)箔轧:中轧切边后半成品基材经4道次0.26mm
→
0.134mm
→
0.072mm
→
0.03mm
→
0.012mm箔轧成成品厚度为12μm规格地双面光铝箔。
49.(8)分切:将箔轧后铝箔母卷宽度方向一剖二进行初步一次定长度分切。
50.(9)倒卷电晕:倒卷时采用双面刃圆盘刀将分切后铝卷继续精切至成品窄幅宽度规格,采用1次电晕,电晕功率16kw,线速度145m/min,开卷轴张力21n/mm2,倒卷机胶辊每卷需要采用干净地无尘布清理一次,确保无铝屑无灰尘无油污,电晕后铝箔表面达因值要求32dyn。
51.(10)表面预处理:经过表面酸碱溶液浸润、水清洗、烘干三步骤处理,其中酸碱液为naoh和hcl等酸或者碱性物质溶液,酸碱洗需要流转浸润8s,以显微镜观察下完全去除表面氧油脂及粉末残留物为准。
52.(11)表面辊压粗化处理:采用激光毛化机对轧辊进行表面毛化并对双面光铝箔进行毛化轧制,环状毛化坑宽度控制9μm,表面毛化坑的直径控制70μm。
53.本发明方法制备得到的动力锂电池正极集电体用铝箔产品,表面高清洁无铝粉及油脂残留,表面高毛化,铝箔表面粗糙度ra0.722μm,活性涂层剥离强度达到常规铝箔极片的1.71倍,表面粗化后显微最大厚度减薄量32%,粗化后铝箔强度和延伸率仅降低8.5%;实际使用验证活性物质涂敷工序对比常规表面质量铝箔无明显漏涂、掉粉等现象,压实工序无脆断问题。
54.实施例2:
55.本发明实施例涉及表面高清洁高毛化的锂电池正极集电体用铝箔的制备方法。具体生产方法如下:
56.(1)熔炼:采用aa1070国标铝合金成分要求进行配料熔炼,采用纯铝锭配料生产,废料比控制≤0%,进行两次精炼处理,精炼气体采用ar气。
57.(2)铸轧:铸轧工序采用在线除气箱除气,除气箱温度控制724℃,氢含量0.03ml/100gal;采用板式过滤50目及60目过滤片,配合ra级管式过滤器使用,过滤箱温度控制719℃;铸轧成品坯料厚度7.0mm,晶粒度检测为1级。
58.(3)冷轧开坯:经两道次6.6mm
→
3.5mm
→
2.0mm开坯轧至退火道次厚度;
59.(4)中间退火:将0.20mm厚度铝卷进行中间退火,工艺采用4h炉气温度升温至550℃,保温5h后转炉气温度360℃保温3h;
60.(5)冷轧中轧:将退火后铝卷上中轧轧机经3道次2.0mm
→
0.95mm
→
0.45mm
→
0.24mm轧至0.24mm厚度;
61.(6)切边:将中轧后铝卷上纵剪机进行纵剪切边,单边切3cm。
62.(7)箔轧:中轧切边后半成品基材经4道次0.24mm
→
0.115mm
→
0.054mm
→
0.023mm
→
0.013mm箔轧成成品厚度为13μm规格地双面光铝箔。
63.(8)分切:将箔轧后铝箔母卷宽度方向一剖二进行初步一次定长度分切。
64.(9)倒卷电晕:倒卷时采用双面刃圆盘刀将分切后铝卷继续精切至成品窄幅宽度规格,采用2次电晕,电晕功率15kw,线速度150m/min,开卷轴张力2n/mm2,倒卷机胶辊每卷需要采用干净地无尘布清理一次,确保无铝屑无灰尘无油污,电晕后铝箔表面达因值要求33dyn。
65.(10)表面预处理:经过表面酸碱溶液浸润、水清洗、烘干三步骤处理,其中酸碱液为naoh和hcl等酸或者碱性物质溶液,酸碱洗需要流转浸润5s,以显微镜观察下完全去除表面氧油脂及粉末残留物为准。
66.(11)表面辊压粗化处理:采用激光毛化机对轧辊进行表面毛化并对双面光铝箔进行毛化轧制,环状毛化坑宽度控制12μm,表面毛化坑的直径控制90μm。
67.本发明方法制备得到的动力锂电池正极集电体用铝箔产品,表面高清洁无铝粉及油脂残留,表面高毛化,铝箔表面粗糙度ra0.623μm,活性涂层剥离强度达到常规铝箔极片的1.82倍,表面粗化后显微最大厚度减薄量30%,粗化后铝箔强度和延伸率仅降低9.2%;实际极片生产使用验证活性物质涂敷工序对比常规表面质量铝箔无明显漏涂、掉粉等现象,压实工序无脆断问题。
68.对比例1:
69.本发明对比例其他过程同实施例一,去除案例一中9~11工序,经箔轧后不经电晕、表面预处理、表面粗化工序处理直接作为成品使用。
70.本对比例制备得到的动力锂电池正极集电体用铝箔产品,表面有明显铝粉及油脂残留,表面粗糙度ra 0.092μm,实际极片生产使用验证生产过程不稳定,存在常发性漏涂、掉粉等现象问题投诉。
71.对比例2:
72.本发明对比例其他过程同实施例二,去除案例二中11工序,经箔轧后不经表面粗化工序处理直接作为成品使用。
73.本对比例制备得到的动力锂电池正极集电体用铝箔产品,表面有明显铝粉及油脂残留,表面粗糙度ra 0.153μm,实际极片生产使用验证生产过程不稳定,存在间或性漏涂、掉粉等现象问题投诉。
74.实施案例产品表面形貌及参数对比表:
[0075] 表面形貌图表面粗糙度表面清洁度使用效果实施案例1见图10.722μm无残留无漏涂、掉粉实施案例2见图20.623μm无残留无漏涂、掉粉对比案例1见图30.092μm有油脂铝粉等常发性漏涂、掉粉对比案例1见图40.153μm无残留间或性漏涂、掉粉
[0076]
以上所述仅为本发明的具体实施方式而已,并不用于限定本发明的保护范围,凡在本发明的精神和原则之内,所做的任何修改、等同替换、改进等,均应包含在本发明的保
护范围之内。